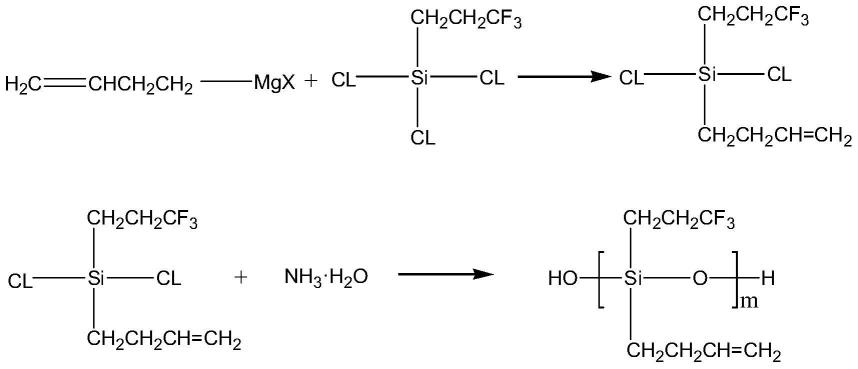
1.本发明涉及氟硅橡胶技术领域,具体的涉及一种高疲劳性氟硅混炼胶及其制备方法。
背景技术:2.氟硅橡胶的主链是由si-o链节组成,其侧链则由ch
3-和cf3ch2ch
2-组成。属于有机硅类橡胶。其具有性能优异,适用范围广的特点,可在-60℃~250℃耐介质油中使用,例如在汽油、柴油、机油、变压器油等工矿环境中使用,所以氟硅橡胶广泛地应用于汽车、轮船、航天航空、工程器械等方面。但是,氟硅橡胶存在耐疲劳性差的问题,导致使用寿命降低,抑制了使用范围。例如作为动态密封应用时,作为汽车发动机中由氟硅橡胶制做成的止逆阀,因其长期在油环境中反复动作,就极易损坏,更换起来也是非常麻烦,所以如何能大幅延长氟硅橡胶的耐疲劳使用寿命就成为必要迫切的工作。
3.中国专利cn113999532a一种抗疲劳硅橡胶及其制备方法中提供了通过在甲基乙基硅橡胶和天然胶中填充改性填料、复合硅油,使得甲基乙基硅橡胶和天然胶形成交联网络,并且利用对苯二胺改性的填料和复合硅油作为负载,促进在橡胶材料中的分散,达到增加耐疲劳性目的。上述方式虽然能够提升硅橡胶材料的抗疲劳性能,但是上述方法制得的抗疲劳橡胶,因其材料本身限制,其耐油性和耐高温性都比较差,无法满足一些耐油、耐高温的工矿环境使用,并且改性填料的制作过程也较繁琐,增加了人力物力,成本较高。
4.中国专利cn103665459a耐疲劳橡胶提供了一种通过使用防老剂来防止橡胶的老化从而增加橡胶的使用寿命。上述方式虽然能够起到耐热防老化、抗动态疲劳的作用,但是该专利中提到的方式以及使用的防老剂只能适用于天然胶、氢化丁腈等由碳碳链组成的橡胶,无法应用在由硅氧链组成的氟硅橡胶领域。并且由于该专利中防老化耐疲劳的原理决定了其在低温应用领域的耐疲劳效果较差,应用范围较小。
5.中国专利cn110628094a柔性渐变的耐疲劳橡胶及其制备方法提供了一种采用了空心蜜胺微球,利用微球表面的富胺基与硅69以及白炭黑一起参与橡胶的硫化交联,形成蜜胺-橡胶交联网络,增加交联密度。首先该方式适用于碳碳键链接的橡胶,其次上述方式在提高橡胶耐疲劳效果的同时,会因为过于密集的交联而导致物理机械性能的下降。
6.按照目前现有的提高橡胶耐疲劳的办法来看,要么是其应用范围受限制、要么是效果差强人意,成本也较高。针对目前这种情况,以及应用领域迫切的需求,故提出本发明。
技术实现要素:7.针对现有技术的不足,本发明提供了一种高疲劳性氟硅混炼胶、抗疲劳剂及其制备方法。因氟硅橡胶中含有三氟丙基,其空间位阻本就比较大,再加上受氟硅橡胶交联固化后各交联点比较致密的影响,导致氟硅橡胶在受到拉伸、曲挠等运动影响时,其内部分子间相对滑移困难,从而造成微观上分子间的撕裂,宏观上表现出橡胶制品的龟裂以及损坏。本发明主要是通过使用一种氟硅混炼胶抗疲劳剂,来大幅增加耐疲劳性。该抗疲劳剂同一个
硅原子上同时链接了三氟丙基和烯丁基,因为三氟丙基的存在能够使得其耐油性不受影响,同时因为烯丁基的存在,又使得氟硅橡胶硫化后各交联点之间能够充分的分散开,从而形成更加分散的交联网络,使得分子间滑移相对容易,进而增加氟硅橡胶的耐疲劳性。
8.为实现上述目的,本发明采用的技术方案如下:
9.一种高疲劳性氟硅混炼胶,按重量份计,包括组成如下:
10.氟硅生胶100份,白炭黑30~90份,分散剂0.1~30份,耐热添加剂1~15份,交联剂0.2~5份,抗疲劳剂0.5-10份;
11.所述的氟硅生胶化学结构如通式(i)所示:
12.r-(rfmesio)
n-(r
vi
mesio)
p-r
13.(i)
14.式(i)中,r为不饱和单价烯烃、羟基、甲基,rf为cf3ch2ch
2-,r
vi
为ch2=ch-;2000≤n≤13000,0≤p≤1200。
15.所述的抗疲劳剂为羟基烯丁基三氟丙基硅氧烷,化学结构如通式(ii)所示:
[0016][0017]
式(ii)中,m表示平均聚合度,1≤m≤1000。
[0018]
根据本发明,优选的,所述的抗疲劳剂按如下方法制备得到:
[0019]
(1)对整个反应系统和所有用到的物料进行干燥处理,确保整个反应体系在无水化中进行;
[0020]
(2)将镁屑、促进剂1,2-二溴乙烷投入到thf,加入反应系统中,开启搅拌;
[0021]
(3)向反应系统中滴加卤丁烯和thf的混合液,控制滴加速度,使反应保持轻微沸腾状态,持续反应,制得烯丁基格利雅试剂;
[0022]
(4)将烯丁基格利雅试剂滴加入三氟丙基三氯硅烷和thf的混合物中,持续搅拌,至反应完成后,精馏得到烯丁基三氟丙基二氯硅烷;
[0023]
(5)将烯丁基三氟丙基二氯硅烷滴加到浓氨水中,控制滴加速度和温度,当ph达到10以下时,持续反应1~3h;
[0024]
(6)反应结束后通入水,将油相水洗至中性,后分离油相、水相,并将油相减压脱水,即得抗疲劳剂。
[0025]
根据本发明,优选的,步骤(2)中所述的促进剂1,2二溴乙烷与四氢呋喃(thf)的体积比为(0.1~1):100。
[0026]
根据本发明,优选的,步骤(2)中所述的镁屑和thf的质量比为1:(1.2~2)。
[0027]
根据本发明,优选的,步骤(3)中所述的卤丁烯为4-氯-1-丁烯或者4-溴-1-丁烯或4-碘-1-丁烯。
[0028]
根据本发明,优选的,步骤(3)中所述的卤丁烯与(thf)的质量比为:1:(1.1~2)。
[0029]
根据本发明,优选的,步骤(3)中所述的镁与卤丁烯的质量比为1:(3.1~3.7)。
[0030]
根据本发明,优选的,步骤(3)中所述的反应时间2~4h,反应温度控制在50~70℃。
[0031]
根据本发明,优选的,步骤(4)中所述的烯丁基格利雅试剂和三氟丙基三氯硅烷的摩尔比为(2~3):1。
[0032]
根据本发明,优选的,步骤(4)中所述的三氟丙基三氯硅烷和thf的质量比为1:(1.1~1.5)。
[0033]
根据本发明,优选的,步骤(4)中所述的反应时间为3-4h。若反应时间不足,三氟丙基三氯硅烷的含量较多,收率低,精馏困难。
[0034]
根据本发明,优选的,步骤(5)中所述的反应温度控制在20-50℃。
[0035]
根据本发明,优选的,步骤(5)中所述的ph值,控制在8-10之间,ph值过低会导致羟基烯丁基三氟丙基硅氧烷聚合度低,导致粘度过低。
[0036]
根据本发明,优选的,步骤(5)中所述的氨水的浓度为25wt%。
[0037]
根据本发明,优选的,步骤(6)中,油相减压脱水的条件为:-0.095~-0.1mpa,21~25℃。
[0038]
根据本发明,优选的,所述的白炭黑为沉淀或气相白炭黑,bet比表面积50-400m2/g。
[0039]
根据本发明,优选的,所述的分散剂为含羟基或甲氧基或乙氧基的硅烷或氟硅烷,或含饱和或不饱和烯烃的硅氮烷或氟硅氮烷,以上其中的一种或几种。
[0040]
根据本发明,优选的,所述的耐热添加剂为氧化铁、氢氧化铈、氧化铈等金属氧化物。
[0041]
根据本发明,优选的,所述的交联剂为过氧化物交联剂,如过氧化苯甲酰、2,5-二甲基-2.5-二叔丁基过氧化己烷等。
[0042]
根据本发明,上述高疲劳氟硅混炼胶的制备方法,包括如下步骤:
[0043]
(1)按照重量比例份数,称取氟硅生胶,白炭黑,分散剂,耐热添加剂,交联剂,抗疲劳剂;
[0044]
(2)使用捏合设备,按重量比例依次投入全部氟硅生胶,全部分散剂,以及全部耐热添加剂,1/4份的白炭黑以及全部的抗疲劳剂,常温常压开启搅拌,当本次釜中吃粉结束时,重新再添加1/4份的白炭黑,如此循环至白炭黑全部吃粉结束;
[0045]
(3)吃粉结束后,开始升温,温度控制在150~180℃,并在此温度下进行抽真空处理,真空度-0.09~-0.1mpa,持续2~4h;
[0046]
(4)待处理好的混炼胶冷却后,在开炼机按照重量份数加入交联剂,并进行多次薄通,得到高疲劳性氟硅混炼胶。
[0047]
本发明抗疲劳剂的合成路线如下:
[0048]
h2c=chch2ch
2-x+mg
→
h2c=chch2ch
2-mgx
[0049][0050]
本发明的技术特点及有益效果如下:
[0051]
1.本发明的抗疲劳效果主要来自抗疲劳剂的使用:
[0052]
(1)该抗疲劳剂分子内每一个硅原子上都含有三氟丙基,保证了氟硅橡胶的耐油性;
[0053]
(2)该抗疲劳剂以羟基封端,能够有效地提高白炭黑在氟硅橡胶中的分散效果;
[0054]
(3)该抗疲劳剂中烯丁基和三氟丙基是同时链接在同一个硅原子上,在保证了烯丁基三氟丙基的含量的同时,又可以保证在氟硅橡胶硫化后,可以获得更多的有效交联点,同时各交联点之间又能够充分的分散开,从而形成分散的交联网络,使得分子间滑移相对容易,进而增加氟硅橡胶的耐疲劳性。
[0055]
2.本发明中抗疲劳混炼胶制作容易,只要在混炼胶生产过程中,添加少量份数的本抗疲劳剂,就可以大幅提升抗疲劳效果,不会额外增加工序,不影响生产效率。
附图说明
[0056]
图1为实施例1制备的抗疲劳剂核磁氢谱谱图。
具体实施方式
[0057]
为了更好的理解和解释本发明,下面通过一些具体实施例来进一步阐述本发明,但本发明不仅限于以下实施例。
[0058]
实施例中所述的氟硅生胶化学结构如通式(i)所示:
[0059]
r-(rfmesio)
n-(r
vi
mesio)
p-r
[0060](i)[0061]
式(i)中,r为不饱和单价烯烃、羟基、甲基,rf为cf3ch2ch
2-,r
vi
为ch2=ch-;2000≤n≤13000,0≤p≤1200。
[0062]
实施例1
[0063]
1#抗疲劳剂的制备,包括如下步骤:
[0064]
(1)对整个反应系统和所有用到的物料进行干燥处理,确保整个反应体系在无水化中进行。将360g镁屑、3g促进剂1,2-二溴乙烷投入到540ml的thf中,开启搅拌,并向其中滴加由1260g的4-氯-1丁烯和1890ml的thf的混合液,控制滴加速度,使反应保持轻微沸腾状态,持续反应一段时间,制得烯丁基格利雅试剂1430g。
[0065]
(2)将制得的烯丁基格利雅试剂滴加入1166g的三氟丙基三氯硅烷和4720ml的thf的混合物中,持续搅拌,至反应完成后,精馏得到烯丁基三氟丙基二氯硅烷882g。
[0066]
(3)将制得的烯丁基三氟丙基二氯硅烷滴加到浓氨水中,控制滴加速度和温度,控制ph在8-9之间,持续反应2h。
[0067]
(4)反应结束后通入水,将油相水洗至中性,后分离油相、水相,并将油相减压脱水得羟基烯丁基三氟丙基硅氧烷452g。
[0068]
动力粘度为240cp,羟基含量7.1mol%。
[0069]
本实施例制备的抗疲劳剂的核磁氢谱谱图如图1所示,谱图中0.63ppm为烯丁基中与硅相连的-ch
2-中氢的化学位移,0.85ppm为三氟丙基中与硅相连的-ch
2-中氢的化学位移,2.06ppm为烯丁基中与碳碳双键相连的-ch
2-中氢的化学位移,2.12ppm为三氟丙基中中间-ch
2-中氢的化学位移,4.32ppm为硅羟基氢的化学位移,4.90ppm~5.94ppm为碳碳双键上氢的化学位移。
[0070]
核磁图谱表征合成的化合物为羟基烯丁基三氟丙基硅氧烷,具有式(ii)所示结构:
[0071][0072]
实施例2
[0073]
2#抗疲劳剂的制备,包括如下步骤:
[0074]
(1)对整个反应系统和所有用到的物料进行干燥处理,确保整个反应体系在无水化中进行。将320g镁屑、3g促进剂1,2-二溴乙烷投入到520ml的thf中,开启搅拌,并向其中滴加由1180g的4-氯-1丁烯和1920ml的thf的混合液,控制滴加速度,使反应保持轻微沸腾状态,持续反应一段时间,制得烯丁基格利雅试剂1320g。
[0075]
(2)将制得的烯丁基格利雅试剂滴加入1260g的三氟丙基三氯硅烷和4420ml的thf的混合物中,持续搅拌,至反应完成后,精馏得到烯丁基三氟丙基二氯硅烷814g。
[0076]
(3)将制得的烯丁基三氟丙基二氯硅烷滴加到浓氨水中,控制滴加速度和温度,控制ph在7-8之间,持续反应2h。
[0077]
(4)反应结束后通入水,将油相水洗至中性,后分离油相、水相,并将油相减压脱水得羟基烯丁基三氟丙基硅氧烷387g。
[0078]
动力粘度为150cp,羟基含量8.1mol%。
[0079]
实施例3
[0080]
取乙烯基含量0.2mol%的氟硅生胶100份,投入捏合机中,同时分批次加入预混的
气相白炭黑32份,羟基氟硅油6份,六甲基二硅氮烷1份,1#抗疲劳剂3份,氧化铈2份,待物料混合均匀后,持续搅拌并加热升温至175℃,-0.097mpa负压真空热处理3h。待热处理好的生胶冷却后,在开炼机上添加0.5份2,5-二甲基-2,5-双过氧化叔丁基己烷,薄通均匀,下片。
[0081]
在170℃*14min的条件下压制2mm厚试片,并在200℃*3h条件下二段硫化。测试物理性能和耐疲劳次数(疲劳测试标准:gbt 1688-2008,试样尺寸:1型;试验应变:50%;试验频率:5hz;试验温度:23
±
3℃;试验环境:空气)。
[0082]
实施例4
[0083]
取乙烯基含量0.3mol%的氟硅生胶100份,投入捏合机中,同时分批次加入预混的气相白炭黑40份,羟基氟硅油8份,六甲基二硅氮烷1.5份,1#抗疲劳剂4份,氧化铈2份,待物料混合均匀后,持续搅拌并加热升温至175℃,-0.097mpa负压真空热处理3h。待热处理好的生胶冷却后,在开炼机上添加0.5份2,5-二甲基-2,5-双过氧化叔丁基己烷,薄通均匀,下片。
[0084]
在170℃*14min的条件下压制2mm厚试片,并在200℃*3h条件下二段硫化。测试物理性能和耐疲劳次数(疲劳测试标准:gbt 1688-2008,试样尺寸:1型;试验应变:50%;试验频率:5hz;试验温度:23
±
3℃;试验环境:空气)。
[0085]
实施例5
[0086]
取乙烯基含量0.3mol%的氟硅生胶100份,投入捏合机中,同时分批次加入预混的气相白炭黑37份,羟基氟硅油7份,六甲基二硅氮烷2份,1#抗疲劳剂2.5份,氧化铈2份,待物料混合均匀后,持续搅拌并加热升温至175℃,-0.097mpa负压真空热处理3h。待热处理好的生胶冷却后,在开炼机上添加0.5份2,5-二甲基-2,5-双过氧化叔丁基己烷,薄通均匀,下片。
[0087]
在170℃*14min的条件下压制2mm厚试片,并在200℃*3h条件下二段硫化。测试物理性能和耐疲劳次数(疲劳测试标准:gbt 1688-2008,试样尺寸:1型;试验应变:50%;试验频率:5hz;试验温度:23
±
3℃;试验环境:空气)。
[0088]
实施例6
[0089]
取乙烯基含量0.3mol%的氟硅生胶100份,投入捏合机中,同时分批次加入预混的气相白炭黑42份,羟基氟硅油8份,六甲基二硅氮烷2份,1#抗疲劳剂3.5份,氧化铈2份,待物料混合均匀后,持续搅拌并加热升温至175℃,-0.097mpa负压真空热处理3h。待热处理好的生胶冷却后,在开炼机上添加0.5份2,5-二甲基-2,5-双过氧化叔丁基己烷,薄通均匀,下片。
[0090]
在170℃*14min的条件下压制2mm厚试片,并在200℃*3h条件下二段硫化。测试物理性能和耐疲劳次数(疲劳测试标准:gbt 1688-2008,试样尺寸:1型;试验应变:50%;试验频率:5hz;试验温度:23
±
3℃;试验环境:空气)。
[0091]
实施例7
[0092]
取乙烯基含量0.3mol%的氟硅生胶100份,投入捏合机中,同时分批次加入预混的气相白炭黑34份,羟基氟硅油6份,六甲基二硅氮烷2.5份,1#抗疲劳剂1.5份,2#抗疲劳剂1.5份,氧化铈2份,待物料混合均匀后,持续搅拌并加热升温至175℃,-0.097mpa负压真空热处理3h。待热处理好的生胶冷却后,在开炼机上添加0.5份2,5-二甲基-2,5-双过氧化叔丁基己烷,薄通均匀,下片。
[0093]
在170℃*14min的条件下压制2mm厚试片,并在200℃*3h条件下二段硫化。测试物理性能和耐疲劳次数(疲劳测试标准:gbt 1688-2008,试样尺寸:1型;试验应变:50%;试验频率:5hz;试验温度:23
±
3℃;试验环境:空气)。
[0094]
对比例1
[0095]
对比例1和实施例3相比,不同之处在于将抗疲劳剂去除,对比例1中没有添加抗疲劳剂,其他制备方式相同。
[0096]
对比例2
[0097]
对比例2和实施例3相比,不同之处在于将抗疲劳剂去除,同时添加结构为ch2=ch-[(ch2ch
2 cf3)mesio]
m-ch=ch2的乙烯基氟硅油3份替代抗疲劳剂,其他制备方式相同。
[0098]
对比例3
[0099]
对比例3和实施例3相比,不同之处在于将抗疲劳剂去除,同时添加结构为oh-[(ch2ch2cf3)mesio-(ch2ch)mesio]
m-h的乙烯基氟硅油3份替代抗疲劳剂,其他制备方式相同。
[0100]
对比例4
[0101]
对比例4和实施例3相比,不同之处在于将1#抗疲劳剂去除,同时添加结构为oh-[(ch2ch
2 cf3)mesio-(ch2chch2ch2)mesio]
m-h的乙烯基氟硅油3份替代抗疲劳剂,其他制备方式相同。
[0102]
试验例
[0103]
实施例及对比例测试数据如下表1所示:
[0104]
表1实施例与对比例测试数据
[0105][0106]
[0107]
从表1中数据来看,实施列3-7表明抗疲劳剂的添加极大的增加了耐疲劳次数,并且对回弹和压缩变形有所提升。
[0108]
对比例1和实施例3相比,对比例1比实施例3的耐疲劳次数少499万次。对比例1中没有添加抗疲劳剂,由此可见抗疲劳剂的作用非常大。
[0109]
对比例2和实施例3相比,对比例2比实施例3的耐疲劳次数少490万次。对比例2使用的是硅原子上直接链接三氟丙基和甲基的乙烯基封端的氟硅油,封端的乙烯基并不能形成更加分散的交联网络,使分子间相对滑移容易,从而增加耐疲劳次数。
[0110]
对比例3和实施例3相比,对比例3比实施例3的耐疲劳次数相少493万次。对比例3使用了共聚的羟基乙烯基氟硅油,同样的道理,其无法形成更加分散的交联网络,并且共聚氟硅油中含有的甲基、乙烯基硅氧链节会影响下氟硅橡胶的耐油性。
[0111]
对比例4和实施例3相比,对比例4比实施例3的耐疲劳次数相差379万次,对比例4虽然使用了含有烯丁基的共聚氟硅油,但是其烯丁基并非和三氟丙基链接在同一个si原子上,其烯丁基的摩尔含量无法和烯丁基直接和三幅丙基链接在同一个si原子上的均聚的氟硅油相比,所以效果较差,并且甲基烯丁基硅氧链节会影响氟硅橡胶耐油性。