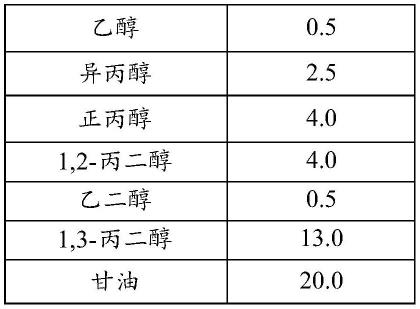
1.本发明涉及加氢反应技术领域,更具体地说,是涉及一种甘油加氢制备1,3-丙二醇的方法。
背景技术:2.1,3丙二醇是一种重要的有机化工原料,广泛应用于聚酯印染和纺织品、工程塑料、化妆品、聚氨酯、溶剂、医疗等领域。特别1,3-丙二醇可以替代乙二醇合成聚对苯二甲酸丙二酯(ptt),ptt是一种性能卓越的聚酯产品,一直领导着合成纤维的发展趋势,综合了尼龙的柔软性和更好的色牢度、腈纶的蓬松性、涤纶的抗污性,并具有高回弹性,具有非常好的市场前景。
3.1,3-丙二醇的合成方法主要有环氧乙烷法、生物发酵法、丙烯醛水合法、缩醛法、甘油加氢法等。已实现工业化主要为丙烯醛水合法、环氧乙烷法以及生物发酵法。其中丙烯醛水合法和环氧乙烷法操作条件苛刻,生产成本高和产品品质较差,逐渐被生物发酵法取代。但是生物发酵法生产效率低,后续分离能耗较高。甘油加氢法采用生产柴油副产甘油为原料,工艺简单,绿色环保和生产效率高,受到广泛关注。
4.公开号为cn103524302a的中国专利公开了一种甘油加氢制备1,3-丙二醇的工艺方法,液相产物全部经渗透汽化膜脱水并对脱水产物分离;但是该技术方案膜分离需要把反应产物全部汽化,并且要求水含量小于20%,其中产物1,3-丙二醇和原料甘油沸点高,汽化需要能量高,势必造成能耗非常高,同时无法适用不同甘油原料浓度。
5.公开号为cn111039756a及cn113527062a的中国专利分别公开了一种甘油制备1,3-丙二醇的方法及其系统,提供的方法集成了高效催化剂、反应器和分离系统;但是上述技术方案分离系统全部采用常规精馏系统,副产物异丙醇和正丙醇将和水容易产生共沸物,分离困难,如果采用共沸精馏,能耗会很高。
技术实现要素:6.有鉴于此,本发明的目的在于提供一种甘油加氢制备1,3-丙二醇的方法,集成高效催化剂和固定床加氢反应工艺,利用新型膜分离工艺,解决了醇水共沸物难分离问题,耦合分离热量,降低分离能耗,整个工艺适用性强,连续操作简单,生产效率高,生产成本低。
7.本发明提供了一种甘油加氢制备1,3-丙二醇的方法,包括以下步骤:
8.a)将甘油溶液和氢气在催化剂存在下进行加氢反应,得到反应混合物;再将所述反应混合物进行气液分离,分别得到液相产物和氢气,其中氢气循环使用;
9.b)将步骤a)得到的液相产物进行轻重分馏,分别得到轻组分和重组分;其中,所述轻馏分依次分离出甲醇、水、正丙醇、乙醇和异丙醇;所述重组分进行甘油回收耦合汽提,分别得到汽提轻组分和甘油,其中甘油循环使用;再将所述汽提轻组分依次分离出水、1,2-丙二醇、乙二醇和1,3丙二醇。
10.优选的,步骤a)中所述甘油溶液的质量浓度为10%~80%;所述甘油溶液由粗甘
油水溶液精制后与溶剂混合配制而成;所述溶剂选自水、甲醇、乙醇中的一种或多种。
11.优选的,步骤a)中所述催化剂选自pt-w系催化剂、ir-re系催化剂、pt-分子筛系催化剂中的一种或多种。
12.优选的,步骤a)中所述甘油溶液的进料量为20t/h~30t/h;所述氢气的流量为7000nm3/h~9000nm3/h;所述催化剂的用量为15t~25t。
13.优选的,步骤a)中所述加氢反应采用固定床反应器;
14.所述加氢反应的温度为120℃~200℃,压力为0.5mpa~10mpa。
15.优选的,步骤a)中所述气液分离的过程具体为:
16.将所述反应混合物先进行热高压气液分离,分别得到气相组分和第一液相组分,其中,气相组分再进行冷高压气液分离,分别得到氢气和第二液相组分;所述第一液相组分和第二液相组分作为液相产物进行后续轻重分馏;所述氢气循环使用。
17.优选的,步骤b)中所述依次分离出甲醇、水、正丙醇、乙醇和异丙醇的过程具体为:
18.所述轻组分进入甲醇分离塔,顶部分离出甲醇,塔底的含水物料经膜蒸发器汽化后,进入膜分离脱水器,分离出水,剩余物料进入正丙醇分离塔,塔底分离出正丙醇,塔顶物料进入异丙醇分离塔,塔顶分离出乙醇,塔底分离出异丙醇。
19.优选的,所述含水物料的含水量小于30wt%;
20.所述膜分离脱水器为a型分子筛膜分离脱水器、13x型分子筛膜分离脱水器或mofs分子筛膜反应器。
21.优选的,步骤b)中所述甘油回收耦合汽提采用甘油回收塔耦合汽提塔;所述甘油回收耦合汽提的过程具体为:
22.所述重组分进入甘油回收塔,塔顶水蒸气进入汽提塔,将丙二醇和乙二醇汽提出去,得到汽提轻组分,塔底得到甘油,循环使用。
23.优选的,步骤b)中所述依次分离出水、1,2-丙二醇、乙二醇和1,3丙二醇的过程具体为:
24.所述汽提轻组分依次进入第一脱水塔,塔顶分离出水,塔底物料进入第二脱水塔,塔顶分离出水,塔底物料进入1,2-丙二醇塔,塔顶分离出1,2-丙二醇,塔底物料进入1,3-丙二醇塔,塔顶分离出乙二醇,塔顶分离出1,3丙二醇。
25.本发明提供了一种甘油加氢制备1,3-丙二醇的方法,包括以下步骤:a)将甘油溶液和氢气在催化剂存在下进行加氢反应,得到反应混合物;再将所述反应混合物进行气液分离,分别得到液相产物和氢气,其中氢气循环使用;b)将步骤a)得到的液相产物进行轻重分馏,分别得到轻组分和重组分;其中,所述轻馏分依次分离出甲醇、水、正丙醇、乙醇和异丙醇;所述重组分进行甘油回收耦合汽提,分别得到汽提轻组分和甘油,其中甘油循环使用;再将所述汽提轻组分依次分离出水、1,2-丙二醇、乙二醇和1,3丙二醇。与现有技术相比,本发明提供的甘油加氢制备1,3-丙二醇的方法采用特定反应工艺和特定分离工艺相结合的方式,反应工艺通过高效催化剂和固定床连续操作,生产效率高,而分离工艺通过膜脱水和能量耦合,适用不同甘油原料浓度,可解决副产物共沸问题,运行能耗低,易于工业化推广;并且,本发明提供的方法能够得到高指标的1,3-丙二醇,同时能够分离异丙醇、正丙醇、1,2-丙二醇等产物,各分离产物的纯度均在99.95%以上。
附图说明
26.图1为本发明实施例提供的甘油加氢制备1,3-丙二醇的方法的工艺流程图。
具体实施方式
27.下面将结合本发明实施例,对本发明的技术方案进行清楚、完整地描述,显然,所描述的实施例仅仅是本发明一部分实施例,而不是全部的实施例。基于本发明中的实施例,本领域普通技术人员在没有做出创造性劳动前提下所获得的所有其他实施例,都属于本发明保护的范围。
28.本发明提供了一种甘油加氢制备1,3-丙二醇的方法,包括以下步骤:
29.a)将甘油溶液和氢气在催化剂存在下进行加氢反应,得到反应混合物;再将所述反应混合物进行气液分离,分别得到液相产物和氢气,其中氢气循环使用;
30.b)将步骤a)得到的液相产物进行轻重分馏,分别得到轻组分和重组分;其中,所述轻馏分依次分离出甲醇、水、正丙醇、乙醇和异丙醇;所述重组分进行甘油回收耦合汽提,分别得到汽提轻组分和甘油,其中甘油循环使用;再将所述汽提轻组分依次分离出水、1,2-丙二醇、乙二醇和1,3丙二醇。
31.本发明首先将甘油溶液和氢气在催化剂存在下进行加氢反应,得到反应混合物;再将所述反应混合物进行气液分离,分别得到液相产物和氢气,其中氢气循环使用。
32.在本发明中,所述甘油溶液的质量浓度优选为10%~80%,更优选为40%~60%;所述甘油溶液优选由粗甘油水溶液精制后与溶剂混合配制而成;所述溶剂优选选自水、甲醇、乙醇中的一种或多种,更优选为水;采用本领域技术人员熟知的去离子水即可。
33.本发明对所述粗甘油水溶液的来源没有特殊限制;所述粗甘油水溶液的质量浓度优选大于70%。
34.在本发明中,所述精制优选采用甘油净化设备/系统,目的是脱除甘油中的酯类、重金属、盐以及有色重组分;精制后的甘油进入甘油原料罐备用,进一步与溶剂混合配制成不同浓度的甘油溶液。
35.在本发明中,所述催化剂优选选自pt-w系催化剂、ir-re系催化剂、pt-分子筛系催化剂中的一种或多种,更优选为pt-w系催化剂。本发明对所述催化剂的来源没有特殊限制,采用本领域技术人员熟知的上述加氢催化剂的市售商品或自制品均可。
36.在本发明中,所述甘油溶液的进料量优选为20t/h~30t/h,更优选为25t/h;所述氢气的流量优选为7000nm3/h~9000nm3/h,更优选为8000nm3/h;所述催化剂的用量优选为15t~25t,更优选为20t。
37.在本发明中,所述加氢反应优选采用固定床反应器;所述加氢反应的温度优选为120℃~200℃,更优选为170℃~190℃,压力优选为0.5mpa~10mpa,更优选为4mpa~6mpa。
38.在本发明中,为充分利用热能,甘油溶液和氢气在进料过程中,优选先经原料和产品换热器,再经2mpa~4mpa蒸汽原料加热器,实现上述升温过程。
39.在本发明中,所述气液分离的过程优选具体为:
40.将所述反应混合物先进行热高压气液分离,分别得到气相组分和第一液相组分,其中,气相组分再进行冷高压气液分离,分别得到氢气和第二液相组分;所述第一液相组分和第二液相组分作为液相产物进行后续轻重分馏;所述氢气循环使用。
41.在此基础上,上述循环使用的氢气可以部分代替作为反应原料的新鲜氢气,同时,二者分别通过压缩机进行流量控制。
42.得到所述液相产物后,本发明将得到的液相产物进行轻重分馏,分别得到轻组分和重组分;其中,所述轻组分依次分离出甲醇、水、正丙醇、乙醇和异丙醇;所述重组分进行甘油回收耦合汽提,分别得到汽提轻组分和甘油,其中甘油循环使用;再将所述汽提轻组分依次分离出水、1,2-丙二醇、乙二醇和1,3丙二醇。
43.在本发明中,所述轻重分馏优选采用轻重分馏塔,所述第一液相组分进入轻重分馏塔中下部,所述第二液相组分进入轻重分馏塔中部,塔顶得到轻组分,塔底得到重组分。
44.在本发明中,所述轻组分依次分离出甲醇、水、正丙醇、乙醇和异丙醇;所述依次分离出甲醇、水、正丙醇、乙醇和异丙醇的过程优选具体为:
45.所述轻组分进入甲醇分离塔,顶部分离出甲醇,塔底的含水物料经膜蒸发器汽化后,进入膜分离脱水器,分离出水,剩余物料进入正丙醇分离塔,塔底分离出正丙醇,塔顶物料进入异丙醇分离塔,塔顶分离出乙醇,塔底分离出异丙醇。
46.在本发明中,所述含水物料的含水量优选小于30wt%;所述经膜蒸发器汽化的目的是保证后续进入膜分离脱水器的物料为气态。
47.在本发明中,所述膜分离脱水器优选为a型分子筛膜分离脱水器、13x型分子筛膜分离脱水器或mofs分子筛膜反应器,更优选为a型分子筛膜分离脱水器。
48.在本发明中,所述重组分进行甘油回收耦合汽提,分别得到汽提轻组分和甘油,其中甘油循环使用;再将所述汽提轻组分依次分离出水、1,2-丙二醇、乙二醇和1,3丙二醇。
49.在本发明中,所述甘油回收耦合汽提优选采用甘油回收塔耦合汽提塔;所述甘油回收耦合汽提的过程优选具体为:
50.所述重组分进入甘油回收塔,塔顶水蒸气进入汽提塔,将丙二醇和乙二醇汽提出去,得到汽提轻组分,塔底得到甘油,循环使用。
51.在本发明中,所述依次分离出水、1,2-丙二醇、乙二醇和1,3丙二醇的过程优选具体为:
52.所述汽提轻组分依次进入第一脱水塔,塔顶分离出水,塔底物料进入第二脱水塔,塔顶分离出水,塔底物料进入1,2-丙二醇塔,塔顶分离出1,2-丙二醇,塔底物料进入1,3-丙二醇塔,塔顶分离出乙二醇,塔顶分离出1,3丙二醇。
53.在本发明中,第一脱水塔塔顶分离出的水优选返回步骤a)作为溶剂循环使用;第二脱水塔塔顶分离出的水由于为高纯水,优选送至界外使用。
54.在本发明中,上述正丙醇塔、异丙醇塔、1,2-丙二醇塔、1,3-丙二醇塔等分离塔均为本领域技术人员熟知的负压操作,分离压力优选为-20kpa~-100kpa。
55.本发明提供的甘油加氢制备1,3-丙二醇的方法包括反应工艺和分离工艺,其中反应工艺主要通过甘油溶液和氢气在催化剂作用下进行加氢反应生成1,3-丙二醇的加氢混合产物;之后经分离工艺将1,3-丙二醇、加氢副产物、溶剂以及未循环甘油分离。所述的反应工艺包括:甘油净化系统、甘油和溶剂与氢气混合系统、加热和换热系统、加氢反应和气液分离系统、氢气循环和压缩系统等组成;所述分离工艺包括:轻重组分分离、甲醇分离、膜脱水分离、乙醇分离、异丙醇分离、正丙醇分离、未反应甘油分离、溶剂分离、1,3-丙二醇分离、乙二醇分离以及1,2-丙二醇分离等系统组成。
56.本发明采用特定反应工艺和特定分离工艺相结合的方式,反应工艺通过高效催化剂和固定床连续操作,生产效率高,而分离工艺通过膜脱水和能量耦合,适用不同甘油原料浓度,可解决副产物共沸问题,运行能耗低,易于工业化推广;并且,本发明提供的方法能够得到高指标的1,3-丙二醇,同时能够分离异丙醇、正丙醇、1,2-丙二醇等产物,各分离产物的纯度均在99.95%以上。
57.与现有技术相比,本发明侧重于工艺整体方案,包括反应和分离,一般情况反应工艺确定了才能有分离工艺,本发明将二者整合在一起更加合理;反应只是保护工艺条件(原料浓度、压力、温度、流量等),而实际上,这些会影响后续分离工艺,特别是分离工艺是和其他现有技术完全不同的,申请人研究发现,其他现有技术中的分离工艺过于模糊和简单,实际分离效果是不可能得到高指标的产品的,而本发明涉及到多种分离手段的耦合,不是简单的按照沸点分开那么容易,里面涉及多个醇水(正丙醇、异丙醇)共沸产物以及膜分离的实际应用条件,并且能耗问题一直是困扰,本技术也能够清楚说明,这通常情况是不容易想到的和做到的,需要技术摸索,仅仅依靠常识是做不到的。
58.本发明提供了一种甘油加氢制备1,3-丙二醇的方法,包括以下步骤:a)将甘油溶液和氢气在催化剂存在下进行加氢反应,得到反应混合物;再将所述反应混合物进行气液分离,分别得到液相产物和氢气,其中氢气循环使用;b)将步骤a)得到的液相产物进行轻重分馏,分别得到轻组分和重组分;其中,所述轻馏分依次分离出甲醇、水、正丙醇、乙醇和异丙醇;所述重组分进行甘油回收耦合汽提,分别得到汽提轻组分和甘油,其中甘油循环使用;再将所述汽提轻组分依次分离出水、1,2-丙二醇、乙二醇和1,3丙二醇。与现有技术相比,本发明提供的甘油加氢制备1,3-丙二醇的方法采用特定反应工艺和特定分离工艺相结合的方式,反应工艺通过高效催化剂和固定床连续操作,生产效率高,而分离工艺通过膜脱水和能量耦合,适用不同甘油原料浓度,可解决副产物共沸问题,运行能耗低,易于工业化推广;并且,本发明提供的方法能够得到高指标的1,3-丙二醇,同时能够分离异丙醇、正丙醇、1,2-丙二醇等产物,各分离产物的纯度均在99.95%以上。
59.为了进一步说明本发明,下面通过以下实施例进行详细说明。本发明以下实施例中所用的原料具体为质量50%甘油+50%去离子水,所用的催化剂为pt-w系。
60.实施例
61.参见图1所述,图1为本发明实施例提供的甘油加氢制备1,3-丙二醇的方法的工艺流程图;其中,1为甘油净化设备,2为甘油原料罐,3为溶剂原料罐,4为原料和产物换热器,5为原料加热器,6为固定床加氢反应器,7为热高压气液分离罐,8为冷高压气液分离罐,9为循环氢压缩机,10新鲜氢压缩机,11为轻重分馏塔,12为甲醇分离塔,13为膜蒸发器,14为膜分离脱水器,15为正丙醇分离塔,16为异丙醇分离塔,17为甘油回收塔,18为汽提塔,19为脱水塔i,20为脱水塔ii,21为1,2-丙二醇塔1,22为1,3-丙二醇塔。
62.具体过程如下:
63.在反应系统(1~10)中,外来80%粗甘油水溶液通过甘油净化设备(1)精制脱除甘油中的酯类、重金属、盐以及有色重组分,之后进入甘油原料罐(2);以水为溶剂从溶剂原料罐(3)输出,按照质量比例与甘油原料罐(2)输出的精制甘油混合,配制成50%质量浓度的甘油水溶液,以25t/h原料进料量与氢气充分混合后经原料和产品换热器(4)、3mpa蒸汽原料加热器(5)进入固定床加氢反应器(6)。
64.加热后的甘油水溶液和氢气从固定床加氢反应器(6)顶部进入催化剂床层,在催化剂和反应条件下加氢反应生成含有1,3-丙二醇的反应混合物,从固定床加氢反应器(6)底部流出,进入热高压气液分离罐(7);主要参数为:催化剂装填量20t,反应温度180℃、反应压力5mpa、氢气量8000nm3/h。
65.反应混合物组成如表1所示。
66.表1反应混合物组成
[0067][0068][0069]
反应后产物经热高压气液分离罐(7),顶部分离出氢气和轻组分,再经冷高压气液分离罐(8),顶部得到氢气,底部得到轻组分;其中氢气进入循环氢压缩机(9),并与经新鲜氢压缩机(10)后的新鲜氢气一起送至固定床加氢反应器(6);轻组分与热高压气液分离罐(7)底部物料(重组分)分别进入分离工艺系统(11~22)。
[0070]
反应系统中,冷高压气液分离罐(8)底部得到的轻组分和热高压气液分离罐(7)底部得到的重组分分别进入轻重分馏塔(11)的中部和中下部,塔顶物料进入甲醇分离塔(12),甲醇分离塔(12)顶部产出工业级甲醇,约含水25%的塔底物料经膜蒸发器(13)进入a型分子筛膜分离脱水器(14),将物料中水脱除后,进入正丙醇分离塔(15),塔底采出99.98%正丙醇,塔顶物料进入异丙醇分离塔(16)继续分离,异丙醇分离塔(16)塔顶采出98.6%乙醇,塔底采出99.95%异丙醇。
[0071]
上述各分离塔物料组成如表2所示。
[0072]
表2各分离塔物料组成
[0073][0074][0075]
轻重分馏塔(11)塔底物料进入甘油回收塔(17),其中甘油回收塔(17)耦合汽提塔(18),甘油回收塔(17)塔顶水蒸气进入汽提塔(18),将丙二醇和乙二醇一起汽提出,塔底未反应甘油送回反应系统的甘油原料罐(2),汽提出的轻组分依次进入脱水塔i(19)和脱水塔ii(20),其中脱水塔i(19)塔顶采出出水返回反应系统的溶剂原料罐(3)继续使用,脱水塔ii(20)的塔顶采出纯水送至界外使用;脱水塔ii(20)底部物料依次进入1,2-丙二醇塔(21)、1,3-丙二醇塔(22),将1,2-丙二醇、1,3丙二醇、乙二醇等产物分离出来;其中1,2-丙二醇塔(21)塔顶采出99.95%1,2-丙二醇,1,2-丙二醇塔(21)塔底物料进入1,3-丙二醇塔(22)继续分离,1,3-丙二醇塔(22)塔顶采出77.76%乙二醇,1,3-丙二醇塔(22)塔底采出99.95%1,3-丙二醇。
[0076]
各分离塔物料组成如表3所示。
[0077]
表3各分离塔物料组成
[0078][0079]
从表2、表3中可以看出,本发明所述甘油加氢制备1,3-丙二醇的反应和分离工艺,采用低能耗膜分离脱水和精馏系统可以分离产出高纯度醇产品,整个分离工艺没有高能耗共沸精馏系统,不受限加氢原料浓度要求,连续性好,生产效率高。
[0080]
所公开的实施例的上述说明,使本领域专业技术人员能够实现或使用本发明。对这些实施例的多种修改对本领域的专业技术人员来说将是显而易见的,本文中所定义的一般原理可以在不脱离本发明的精神或范围的情况下,在其它实施例中实现。因此,本发明将不会被限制于本文所示的这些实施例,而是要符合与本文所公开的原理和新颖特点相一致的最宽的范围。