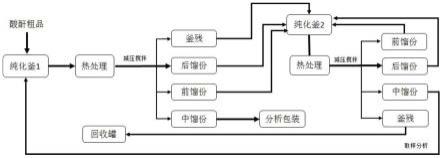
1.本发明属于精细化工技术领域,具体涉及一种间歇蒸馏釜制备高纯三氟甲磺酸酐的方法。
背景技术:2.三氟甲磺酸酐是药品合成的重要试剂,用于有机化学中的三氟甲磺酰化反应,一般用于氨基、羟基的保护或者合成偶联反应的前体。三氟甲磺酸酐作为中间体广泛应用在医药产业,如核苷、抗生素、类固醇、蛋白质、配糖类、维生素等,是一种新型高效friedel-crafts烷基化和环己烷化反应的催化剂,比如国家一类新药爱普列特类化合物即需要试剂三氟甲磺酸酐。
3.三氟甲磺酸酐有多种制备方法,三氟甲磺酸与磷的氯化物反应法、混合酸酐法、三氟甲磺酸与五氧化二磷反应法。
4.1)三氟甲磺酸与磷的氯化物反应法
5.三氟甲磺酸与五氯化磷反应,原料加入的温度不超过40℃,反应温度则控制在20~80℃,便可以得到含有三氟甲磺酸酐的混合物,进一步蒸馏便可以得到三氟甲磺酸酐,化学方程式为:2cf3so3h+pcl5→
(cf3so2)2o+pocl3+2hcl。
6.三氟甲磺酸与三氯化磷混合,接着加入与pcl3等量的cl2,此时的温度最好不超过40℃,反应温度为20~80℃,将生成物蒸馏便可以得到较高纯度三氟甲磺酸酐,化学方程式为:2cf3so3h+pcl5→
(cf3so2)2o+pocl3+2hcl。
7.2)混合酸酐法
8.三氟甲磺酸或者它的衍生物和乙烯酮、羰基酸以及它的衍生物等羰基化合物在一定条件下反应,可以产生含有三氟甲磺酰基和羰基的混合酸酐,分子式为cf3so
2-o-co-r。它在一定程度下分解便可以产生三氟甲磺酸酐。
9.三氟甲磺酰氯与三氟甲磺酸盐(cf3so3m,m=li,na,k)反应也可以制备三氟甲磺酸酐,化学方程式为:cf3so2cl+cf3so3m——
→
(cf3so2)2o+mcl。
10.3)三氟甲磺酸与五氧化二磷存在条件下,脱水生成三氟甲磺酸酐,化学方程式:6cf3so3h+p2o5——
→
3(cf3so2)2o+2h3po411.此方法制备三氟甲磺酸酐反应较为温和、收率高,成为目前工业上生产三氟甲磺酸酐的主要方法。
12.以上制备方法可得到粗品三氟甲磺酸酐,但主含量较低,杂质含量高,早已不能满足市场对高纯的要求,需要进一步纯化。
13.中国专利cn201310410410009.5公布了三氟甲磺酸酐的纯化方法,包括:1)三氟甲磺酸酐粗品导入蒸馏釜中,加热全回流1-5h;2)釜温达到50℃~65℃时调节回流比收集馏份;3)当蒸馏釜釜温大于120℃时蒸馏结束。该方法调节回流比控制不同出料馏份,控制难度大,间歇蒸馏釜无液体扰动装置,内部物料受热不均,导致产品纯度低于99.7%,且蒸馏过程中随着釜内物料剩余重量及组份变化,釜温上涨快,产品收率低。
14.中国专利cn202010672255.8公布了一种三氟甲磺酸酐制备工艺,包括:1)三氟甲磺酸与五氧化二磷混合搅拌,减压蒸馏出料;2)所得粗品投入蒸馏釜中抽真空,加热减压蒸馏,得到精品三氟甲磺酸酐。该工艺方法采用简单蒸馏手段提纯三氟甲磺酸酐纯度较低,蒸馏真空低,出料速度快,杂质含量高。
15.中国专利cn201910769924.0公布了一种三氟甲磺酸酐的制备方法,采用三氟甲磺酸盐与过量三氟甲磺酰氟在催化剂作用下反应制得酸酐方式,该工艺多了制备三氟甲磺酸盐的步骤,对三氟甲磺酰氟纯度要求高,且反应过程压力高、三氟甲磺酰氟容易汽化随真空损失,转化率低。所得三氟甲磺酸酐只进行一步简单减压蒸馏,最终产品纯度难以进一步提升。
16.涉及三氟甲磺酸酐的纯化工艺较少,现有生产工艺采用间歇蒸馏方式较为普遍,酸酐反应过程产生的三氟甲磺酸三氟甲酯、二氧化硫、氟化氢、硫酸、焦磷酸等杂质残留较多,仅仅靠单次的简单蒸馏难以制得较高纯度的三氟甲磺酸酐,且蒸馏所得前后馏份含有部分三氟甲磺酸酐产品未能得到有效提纯。
17.因此,我们提出了一种间歇蒸馏釜制备高纯三氟甲磺酸酐的方法来解决上述问题。
技术实现要素:18.本发明所要解决的技术问题在于针对上述现有技术的不足,提供一种间歇蒸馏釜制备高纯三氟甲磺酸酐的方法。该方法通过间歇减压蒸馏分组份多级提纯的方式,既解决了酸酐反应过程中副反应产生不同沸点杂质难以提纯的问题,大大提高了产品纯度,又解决其余组份含少量产品难以回收问题。
19.为解决上述技术问题,本发明采用的技术方案是:一种间歇蒸馏釜制备高纯三氟甲磺酸酐的方法,其特征在于,该方法包括以下步骤:
20.s1、将三氟甲磺酸酐粗品加入第一纯化釜中进行热处理,热处理的过程中进行搅拌,并通入氮气;所述热处理结束后进行减压蒸馏,调节所述第一纯化釜的压力为-0.06mpa,然后逐渐加热所述第一纯化釜,当所述第一纯化釜的温度<60℃时,出第一前馏分;当所述第一纯化釜的温度为60℃时,出第一中馏分;当所述第一纯化釜的温度为130℃时,出第一后馏分,当所述第一纯化釜的温度为160℃时停止出料,得到第一釜残、第一前馏分、第一中馏分和第一后馏分;
21.s2、将s1中得到的第一釜残、第一前馏分和第一后馏分通入第二纯化釜中进行热处理,所述热处理的过程中进行搅拌,并通入氮气;所述热处理结束后进行减压蒸馏,调节所述第二纯化釜的压力为-0.06mpa,然后逐渐加热所述第二纯化釜,当第二纯化釜的温度<60℃时,出第二前馏分;当所述第二纯化釜的温度为60℃时,出第二中馏分;当所述第二纯化釜的温度为130℃时,出第二后馏分,当所述第二纯化釜的温度为160℃时停止出料,得到第二釜残、第二前馏分、第二中馏分和第二后馏分;
22.s3、将s2中得到的第二中馏份回流到所述第一纯化釜中与重新加入的三氟甲磺酸酐粗品混合,再次进行热处理,热处理的过程中进行搅拌,并通入氮气;所述热处理结束后,进行减压蒸馏,得到釜残、前馏分、中馏分和后馏分,所述中馏分为三氟甲磺酸酐精品;
23.s2中得到的第二前馏分和第二后馏分均全部回流到所述第二纯化釜中循环反
应。。
24.优选地,s1中所述热处理的温度为25℃~30℃,时间8h~10h,压力-0.04mpa。
25.优选地,s1、s2和s3中所述氮气的纯度均为99.99%,流量均为0.8m3/h~1m3/h;所述搅拌的频率均为10hz。
26.优选地,s2中所述热处理的温度为25℃~35℃,时间为3h~8h,压力为-0.04mpa。
27.优选地,s3中所述第二中馏份和重新加入的三氟甲磺酸酐粗品的质量比为1:(1.5~2)。
28.优选地,s3中所述热处理和s1中所述热处理步骤相同,s3中所述减压蒸馏和s1中所述减压蒸馏步骤相同。
29.本发明与现有技术相比具有以下优点:
30.1、本发明采用搅拌、鼓氮热处理、减压蒸馏方式,通过馏份分类进行两级热处理+减压蒸馏提纯方式,有效去除轻重组份杂质,得到较高纯度产品,蒸馏过程各组份采用不同处理方式,得到有效回收利用,产品收率可达到92%以上。优于行业同类指标,具有很好的经济价值和社会价值,易于在行业内推广。
31.2、本发明将三氟甲磺酸酐粗品进行两次热处理+两次减压蒸馏,主要将不同沸点组份进一步分离,通过实验摸索两次热处理即可将三氟甲磺酸酐酸酐以外其它组份与酸酐分离,且能达到较高的回收效果,降低损失,为提高酸酐纯度做准备。如果是一次热处理+一次蒸馏,三氟甲磺酸酐酸酐产品损失较大,纯度无法达到99.5%以上。
32.下面通过附图和实施例对本发明的技术方案作进一步的详细说明。
附图说明
33.图1是本发明的工艺流程图。
具体实施方式
34.实施例1
35.本实施例中间歇蒸馏釜制备高纯三氟甲磺酸酐的方法,包括以下步骤:
36.s1、将质量为2100kg的三氟甲磺酸酐粗品加入第一纯化釜中进行热处理,热处理的过程中进行搅拌,并通入氮气,所述氮气的流量为1m3/h;热处理结束后进行减压蒸馏,调节所述第一纯化釜的压力为-0.06mpa,逐渐加热所述第一纯化釜,当第一纯化釜的温度<60℃时,出第一前馏分;当所述第一纯化釜的温度为60℃时,出第一中馏分;当所述第一纯化釜的温度为130℃时,出第一后馏分,当所述第一纯化釜的温度为160℃时停止出料,得到第一釜残、第一前馏分、第一中馏分和第一后馏分;所述第一前馏份的出料比例为20%、所述第一中馏份的出料比例为65%、所述第一后馏份的出料比例为10%;
37.所述热处理的温度为30℃,时间8h,压力-0.04mpa;所述氮气的纯度为99.99%;所述搅拌的频率为10hz;所述第一釜残、第一前馏分和第一后馏分的总质量为630kg;
38.所述第一前馏分中含有50%三氟甲磺酸酐、35%三氟甲酯和15%其它杂质;所述第一釜残中含有35%三氟甲磺酸酐、55%硫酸、7%磷酸和3%氟磺酸;所述第一后馏分中含有85%三氟甲磺酸酐和15%硫酸;所述第一中馏分中含有三氟甲磺酸酐98%和2%其他杂质;
39.s1将三氟甲磺酸酐粗品中的三氟甲磺酸三氟甲酯、二氧化硫、氟化氢、二氧化碳等轻组份去除;
40.s2、将s1中得到的第一釜残、第一前馏分和第一后馏分通入第二纯化釜中进行热处理,所述热处理的过程中进行搅拌,并通入氮气,所述热处理的温度为30℃,时间为8h,压力-0.04mpa;热处理结束后,调节所述第二纯化釜的压力为-0.06mpa,出料速度为30kg/h,当所述第二纯化釜的温度为60℃时,出中馏分,当所述第二纯化釜的温度为130℃时,切换后馏分出料,当温度为160℃时停止出料,得到第二釜残、第二前馏分、第二中馏分和第二后馏分;
41.所述氮气的纯度为99.99%,流量为1m3/h;所述搅拌的频率为10hz;经检测:所述第二中馏分中三氟甲磺酸酐的含量为97.84%;
42.所述第二前馏分中含有20%三氟甲磺酸酐、75%三氟甲酯和5%其它杂质组份;所述第二釜残中含有5%三氟甲磺酸酐、85%硫酸和10%磷酸;所述第二后馏分中含有75%三氟甲磺酸酐和25%硫酸;
43.s3、将s2中得到的第二中馏份回流到所述第一纯化釜中,与重新加入的三氟甲磺酸酐粗品混合进行热处理,热处理的过程中进行搅拌,并通入氮气,所述热处理的温度为30℃,时间为8h,压力-0.04mpa;热处理结束后关闭氮气,进行减压蒸馏,所述减压蒸馏时所述第一纯化釜的压力为-0.06mpa,然后逐渐加热所述第一纯化釜,当第一纯化釜的温度<60℃时,出前馏分;当所述第一纯化釜的温度为60℃时,出中馏分;当所述第一纯化釜的温度为130℃时,出后馏分,当所述第一纯化釜的温度为160℃时停止出料,得到釜残、前馏分、中馏分和后馏分,控制所述前馏份的出料比例为10%、所述中馏份的出料比例为80%、所述后馏份的出料比例为5%,其余为釜残;所述中馏分为三氟甲磺酸酐精品;
44.所述第二中馏份和重新加入的三氟甲磺酸酐粗品的质量比为1:2;所述氮气的纯度为99.99%,流量为1m3/h;所述搅拌的频率为10hz;所述减压蒸馏和s1中所述减压蒸馏步骤相同;s2中得到的第二前馏分和第二后馏分回流到所述第二纯化釜中循环反应;
45.将s1、s2和s3中得到的第一釜残、第二釜残和釜残转入回收罐中储存,回收罐夹套冷冻液降温,罐内通过真空维持负压-0.04mpa,作为反应工序原料使用。
46.本实施例中采用的三氟甲磺酸酐粗品的成分含量包括90.5%的三氟甲磺酸酐、407ppm的f-、2467ppm的so
42-;本实施例中得到的三氟甲磺酸酐精品经检测的产品指标如表1所示;
47.表1:实施例1所得三氟甲磺酸酐产品指标
[0048][0049]
实施例2
[0050]
本实施例中间歇蒸馏釜制备高纯三氟甲磺酸酐的方法,包括以下步骤:
[0051]
s1、将质量为3000kg三氟甲磺酸酐粗品加入第一纯化釜中进行热处理,热处理的过程中进行搅拌,并通入氮气,所述氮气的流量为0.8m3/h;热处理结束后进行减压蒸馏,调节所述第一纯化釜的压力为-0.06mpa,逐渐加热所述第一纯化釜,当第一纯化釜的温度<60℃时,出第一前馏分;当所述第一纯化釜的温度为60℃时,出第一中馏分;当所述第一纯
化釜的温度为130℃时,出第一后馏分,当所述第一纯化釜的温度为160℃时停止出料,得到第一釜残、第一前馏分、第一中馏分和第一后馏分;所述第一前馏份的分馏比例为20%、所述第一中馏份的分馏比例为65%、所述第一后馏份的分馏比例为10%;
[0052]
所述热处理的温度为25℃,时间10h,压力-0.04mpa;所述氮气的纯度为99.99%;所述搅拌的频率为10hz;所述第一釜残、第一前馏分和第一后馏分的总质量为900kg;
[0053]
所述第一前馏分中含有三氟甲磺酸酐、三氟甲酯和杂质;所述第一釜残中含有三氟甲磺酸酐、硫酸、磷酸和氟磺酸;所述第一后馏分中含有三氟甲磺酸酐和硫酸;所述第一中馏分中含有三氟甲磺酸酐和其他杂质;
[0054]
s2、将s1中得到的第一釜残、第一前馏分和第一后馏分通入第二纯化釜中进行热处理,所述热处理的过程中进行搅拌,并通入氮气,所述热处理的温度为35℃,时间3h,压力-0.04mpa;热处理结束后,调节所述第二纯化釜的压力为-0.06mpa,控制出料速度为30kg/h,当所述第二纯化釜的温度为60℃时,出中馏分,当所述第二纯化釜的温度为130℃时,切换后馏分出料,当温度为160℃停止出料,得到第二釜残、第二前馏分、第二中馏分和第二后馏分;
[0055]
所述氮气的纯度为99.99%,流量为0.8m3/h;所述搅拌的频率为10hz;得到所述第二中馏分的质量为800kg;经检测:所述第二中馏分中三氟甲磺酸酐的含量为98.68%;所述第二前馏分中含有三氟甲磺酸酐、三氟甲酯和其它杂质;所述第二釜残中含有三氟甲磺酸酐、硫酸和磷酸;所述第二后馏分中含有三氟甲磺酸酐和硫酸;
[0056]
s3、将s2中得到的第二中馏份回流到所述第一纯化釜中,与重新加入的三氟甲磺酸酐粗品混合进行热处理,热处理的过程中进行搅拌,并通入氮气,所述热处理的温度为25℃,时间为10h,压力-0.04mpa;热处理结束后关闭氮气,进行减压蒸馏,所述减压蒸馏时所述第一纯化釜的压力为-0.06mpa,然后逐渐加热所述第一纯化釜,当第一纯化釜的温度<60℃时,出前馏分;当所述第一纯化釜的温度为60℃时,出中馏分;当所述第一纯化釜的温度为130℃时,出后馏分,当所述第一纯化釜的温度为160℃时停止出料,得到釜残、前馏分、中馏分和后馏分,控制所述前馏份的出料比例为5%、所述中馏份的出料比例为85%、所述后馏份的出料比例为5%,其余为釜残;所述中馏分为三氟甲磺酸酐精品;
[0057]
所述第一中馏份回流和重新加入的三氟甲磺酸酐粗品的质量比为1:1.5;所述氮气的纯度为99.99%,流量为0.8m3/h;所述搅拌的频率为10hz;所述减压蒸馏和s1中所述减压蒸馏步骤相同;s2中得到的第二前馏分和第二后馏分回流到所述第二纯化釜中循环反应;
[0058]
将s1、s2和s3中得到的第一釜残、第二釜残和釜残转入回收罐中储存,回收罐夹套冷冻液降温,罐内通过真空维持负压-0.04mpa,作为反应工序原料使用。
[0059]
本实施例中采用的三氟甲磺酸酐粗品的成分含量包括91.5%的三氟甲磺酸酐、358ppm的f-、3261ppm的so
42-);本实施例中得到的三氟甲磺酸酐精品经检测的产品指标如表2所示;
[0060]
表2:实施例2所得三氟甲磺酸酐产品指标
[0061]
[0062]
实施例3
[0063]
本实施例中间歇蒸馏釜制备高纯三氟甲磺酸酐的方法,包括以下步骤:
[0064]
s1、将质量为2100kg的三氟甲磺酸酐粗品加入第一纯化釜中进行热处理,热处理的过程中进行搅拌,并通入氮气,所述氮气的流量为0.9m3/h;热处理结束后进行减压蒸馏,调节所述第一纯化釜的压力为-0.06mpa,逐渐加热所述第一纯化釜,当第一纯化釜的温度<60℃时,出第一前馏分;当所述第一纯化釜的温度为60℃时,出第一中馏分;当所述第一纯化釜的温度为130℃时,出第一后馏分,当所述第一纯化釜的温度为160℃停止出料,得到第一釜残、第一前馏分、第一中馏分和第一后馏分;所述第一前馏份的分馏比例为20%、所述第一中馏份的分馏比例为65%、所述第一后馏份的分馏比例为10%;
[0065]
所述热处理的温度为27℃,时间9h,压力-0.04mpa;所述氮气的纯度为99.99%;所述搅拌的频率为10hz;所述第一釜残、第一前馏分和第一后馏分的总质量为630kg;
[0066]
所述第一前馏分中含有三氟甲磺酸酐、三氟甲酯和杂质;所述第一釜残中含有三氟甲磺酸酐、硫酸、磷酸和氟磺酸;所述第一后馏分中含有三氟甲磺酸酐和硫酸;所述第一中馏分中含有三氟甲磺酸酐和其他杂质;
[0067]
s2、将s1中得到的第一釜残、第一前馏分和第一后馏分通入第二纯化釜中进行热处理,所述热处理的过程中进行搅拌,并通入氮气,所述热处理的温度为32℃,时间6h,压力-0.04mpa;热处理结束后,调节所述第二纯化釜的压力为-0.06mpa,控制出料速度为30kg/h,当所述第二纯化釜的温度为60℃时,出中馏分,当所述第二纯化釜的温度为130℃时,切换后馏分出料,当温度为160℃停止出料,得到第二釜残、第二前馏分、第二中馏分和第二后馏分;
[0068]
所述氮气的纯度为99.99%,流量为0.9m3/h;所述搅拌的频率为10hz;得到所述第二中馏分的质量为700kg;经检测:所述第二中馏分中三氟甲磺酸酐的含量为97.34%;所述第二前馏分中含有三氟甲磺酸酐、三氟甲酯和其它杂质;所述第二釜残中含有三氟甲磺酸酐、硫酸和磷酸;所述第二后馏分中含有三氟甲磺酸酐和硫酸;
[0069]
s3、将s2中得到的第二中馏份回流到所述第一纯化釜中,与重新加入的三氟甲磺酸酐粗品混合进行热处理,热处理的过程中进行搅拌,并通入氮气,所述热处理的温度为27℃,时间为9h,压力-0.04mpa;热处理结束后关闭氮气,进行减压蒸馏,所述减压蒸馏时所述第一纯化釜的压力为-0.06mpa,然后逐渐加热所述第一纯化釜,当第一纯化釜的温度<60℃时,出前馏分;当所述第一纯化釜的温度为60℃时,出中馏分;当所述第一纯化釜的温度为130℃时,出后馏分,当所述第一纯化釜的温度为160℃时停止出料,得到釜残、前馏分、中馏分和后馏分,控制所述前馏份的出料比例为10%、所述中馏份的出料比例为80%、所述后馏份的出料比例为5%,其余为釜残;所述中馏分为三氟甲磺酸酐精品;
[0070]
所述第一中馏份回流和重新加入的三氟甲磺酸酐粗品的质量比为1:1.7;所述氮气的纯度为99.99%,流量为0.9m3/h;所述搅拌的频率为10hz;所述减压蒸馏和s1中所述减压蒸馏步骤相同;s2中得到的第二前馏分和第二后馏分回流到所述第二纯化釜中循环反应;
[0071]
将s1、s2和s3中得到的第一釜残、第二釜残和釜残转入回收罐中储存,回收罐夹套冷冻液降温,罐内通过真空维持负压-0.04mpa,作为反应工序原料使用。
[0072]
本实施例中采用的三氟甲磺酸酐粗品的成分含量包括90.8%的三氟甲磺酸酐、
397ppm的f-、3164ppm的so
42-);本实施例中得到的三氟甲磺酸酐精品经检测的产品指标如表3所示;
[0073]
表3:实施例3所得三氟甲磺酸酐产品指标
[0074][0075]
目前,行业的三氟甲磺酸酐质量指标如表4所示;
[0076]
表4三氟甲磺酸酐质量指标(行业)
[0077][0078]
可见,实施例1-3中制得的三氟甲磺酸酐精品均符合上述质量指标。
[0079]
以上所述,仅是本发明的较佳实施例,并非对本发明作任何限制。凡是根据发明技术实质对以上实施例所作的任何简单修改、变更以及等效变化,均仍属于本发明技术方案的保护范围内。