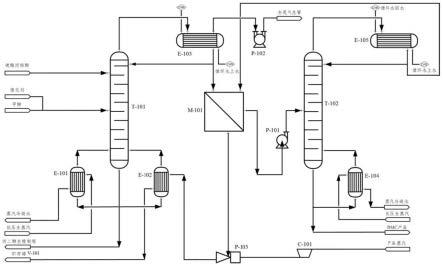
1.本发明涉及精馏分离技术领域,尤其涉及一种膜分离耦合精馏的甲醇和碳酸二甲酯共沸物的分离方法。
背景技术:2.碳酸二甲酯(dimethyl carbonate,dmc),是一种低毒、环保性能优异、用途广泛的化工原料,它是一种重要的有机合成中间体,分子结构中含有羰基、甲基和甲氧基等官能团,具有多种反应性能,在生产中具有使用安全、方便、污染少、容易运输等特点。由于碳酸二甲酯毒性较小,是一种具有发展前景的“绿色”化工产品。目前已经实现商业化的dmc生产工艺主要包含两种:一种是以cucl为催化剂的甲醇氧化羰基化路线;另外一种是甲醇酯交换路线。受制于热力学平衡限制,无论采取哪种生产工艺,最终的产物都包含有dmc和甲醇,需要进一步分离纯化得到符合标准的dmc。
3.在常压下,dmc和ch3oh会形成二元共沸物(dmc:30%,ch3oh:70%,温度63.5℃),难以通过常压精馏的方式得到高纯的dmc。工业上把甲醇与碳酸二甲酯的共沸物进行分离是生产高纯度碳酸二甲酯的关键环节,对于甲醇-dmc的分离方法主要有低温结晶法、吸附法、萃取精馏法、共沸精馏法和加压精馏法,以上几种分离方法都存在着较大的缺点和不足,如成本高、能耗大、操作难度大和安全性差等。目前主流的dmc/ch3oh分离工艺是变压精馏和萃取精馏:其中变压精馏能耗大、设备要求高、控制复杂;萃取蒸馏在得到dmc的同时可能会引入萃取剂,另外萃取剂普遍具有环境毒性。
4.目前工业上应用较多的方法是加压精馏,加压精馏利用的是甲醇-dmc共沸物随着压力不同,其共沸组成发生较大改变,从而利用压差变化实现二者的分离。加压精馏工艺系统通常包括反应精馏塔、加压塔和常压精馏塔,从反应精馏塔塔顶采出的甲醇-dmc共沸物,含甲醇约70%,在加压泵的输送下进入加压精馏塔,加压塔的压力控制在8-12bar,从加压塔顶采出的馏出物含甲醇>80%,经与反应精馏塔塔釜物料换热后,返回到反应精馏塔实现甲醇的循环,加压塔底部采出含dmc>99%的dmc粗品,再经dmc精制塔得到纯度>99.9%的产品。但是加压精馏工艺,需要加压操作,其能耗成本高,设备投资成本高,不符合节能减排的绿色生产要求。
5.膜分离法可以在常压或者微负压的条件下操作,能耗低,对分离设备的耐压性要求也较低;并且在分离的过程中不会引入任何杂质;膜组件占地面积小,可以节约土地使用成本。其中dmc为疏水分子,其动力学直径约为0.6nm,ch3oh为亲水分子,其动力学直径约为0.36nm。分子筛膜能利用dmc和ch3oh分子大小和亲疏水性质差异,将这两种物质进行分离。膜是膜分离法的核心,在dmc/ch3oh分离领域的膜,主要有有机膜、无机膜两种。
6.关于有机膜,例如:中国科学院大连化物所在2006年和2008年分别报道了壳聚糖中空纤维膜(cn 101020131 a)和壳聚糖zsm-5分子筛杂化膜(cn 101099924 a),在dmc/ch3oh共沸物体系中,甲醇的渗透通量为0.4kg
·
m-2
·
h-1
,并且渗透侧甲醇的含量为93%;清华大学在2006年报道了聚乙烯醇/聚丙烯酸膜(cn 101003002 a),在dmc/ch3oh共沸物体系
中,甲醇的渗透通量为0.8kg
·
m-2
·
h-1
,并且渗透侧甲醇的含量为96%;清华大学在2007年报道了分子筛填充聚二甲基硅氧烷均质膜(cn 101229491 a),该膜选择性透过dmc,在dmc/ch3oh共沸物体系中,dmc的渗透通量为1.3kg
·
m-2
·
h-1
左右,并且渗透侧dmc的含量为60%左右;上海师范大学在2012年报道了一种氯碱膜(cn 102989320 a),在dmc/ch3oh共沸物体系中,甲醇的渗透通量为3.4kg
·
m-2
·
h-1
,并且渗透侧甲醇的含量为84.5%。菲尔丁化学技术公司报道了一种壳聚糖中空纤维膜(doi:10.1016/s0376-7388(02)00367-8),在dmc/ch3oh共沸物体系中,甲醇的渗透通量为0.28kg
·
m-2
·
h-1
,并且渗透侧甲醇的含量为95%;德国多特蒙德大学发明了聚乙烯醇pervap
tm 1255(doi:10.1016/j.seppur.2013.08.025),,甲醇的渗透通量为0.5kg
·
m-2
·
h-1
,并且渗透侧甲醇的含量为96%。
7.而研究人员对应用于dmc/ch3oh分离的无机膜研究较少。中国科学院有机化学有限公司于2008年报道了一种nay分子筛膜,在dmc/ch3oh共沸物体系中,甲醇的渗透通量为0.5kg
·
m-2
·
h-1
,并且渗透侧甲醇的含量为98%。广岛大学于2011年报道了一种sio2膜,甲醇的通量为0.4kg
·
m-2
·
h-1
,渗透侧甲醇含量大概为98%。
8.通过比较无机膜和有机膜的结果可以发现,有机膜的通量较高但是选择性较差,而无机膜的选择性较高,但是通量较低,亟需开发同时具有高选择性和高通量分离膜。
技术实现要素:9.本发明的目的是针对上述传统分离方法难以分离或者不能分离近沸点、恒沸点有机混合物溶液的亟待解决的问题,提供一种整体运行不再需要中压蒸汽,能耗降低、运行成本大幅降低的膜分离耦合精馏的分离甲醇和碳酸二甲酯共沸物的方法。
10.为实现上述发明目的,本发明的技术方案如下:
11.一种膜分离耦合精馏的甲醇和碳酸二甲酯共沸物的分离方法,采用甲醇和碳酸二甲酯共沸物的分离装置,利用膜分离耦合精馏的方法分离甲醇和碳酸二甲酯;
12.所述分离装置包括反应精馏塔、第一换热器、第二换热器、第三换热器、第四换热器、第五换热器、膜分离器、蒸汽喷射真空系统、压缩机、进料泵、常压塔、贮存罐、dmc精制塔、丙二醇精制塔;
13.所述反应精馏塔的顶部与所述第三换热器、膜分离器通过管线依次连通,膜分离器的截留侧出口与所述进料泵的进口通过管线连通,进料泵的出口与所述常压塔的中部通过管线连通,常压塔的顶部与所述第五换热器、膜分离器的截留侧入口通过管线依次连通;反应精馏塔的底部与所述第一换热器的进口通过管线连通,第一换热器的出口与反应精馏塔通过管线连通;第五换热器的出口还通过管线与常压塔的上部连通,用于将常压塔的顶部采出的部分甲醇-dmc蒸汽冷凝,冷凝液回流到常压塔内;常压塔的底部与所述第四换热器的进口通过管线连通,第四换热器的出口与常压塔通过管线连通;膜分离器的渗透侧出口与所述蒸汽喷射真空系统的抽吸口通过管线连通,蒸汽喷射真空系统的排出口与所述第二换热器、反应精馏塔的中下部通过管线依次连通,所述贮存罐与第二换热器通过管线连通;常压塔的底部与所述dmc精制塔通过管线连通;反应精馏塔的底部与所述丙二醇精制塔通过管线连通;
14.所述膜分离器包括渗透汽化膜组件,所述渗透汽化膜为fau分子筛膜,膜分离器包
括串联设置的多级分子筛膜组,上一级分子筛膜组的截留侧出口与下一级分子筛膜组的截留侧入口连接,每一级分子筛膜组的渗透侧出口并联,并与蒸汽喷射真空系统的抽吸口连通;所述蒸汽喷射真空系统包括多级蒸汽喷射泵,所述压缩机与所述蒸汽喷射真空系统的入口通过管线连通,用于对产品蒸汽加压,加压后的产品蒸汽进入蒸汽喷射真空系统作为喷射介质;
15.操作方法为:开启反应精馏塔、第一换热器、第二换热器、第三换热器、第四换热器、第五换热器、膜分离器、蒸汽喷射真空系统、压缩机、进料泵、常压塔,向反应精馏塔中通入原料碳酸丙烯酯、催化剂、甲醇,进行反应,保持装置系统平稳运行,分别收集分离得到的dmc、甲醇和副产物丙二醇。
16.在上述技术方案中,向反应精馏塔中通入原料后,反应精馏塔内原料反应生成dmc和丙二醇,dmc和原料中的甲醇在反应精馏塔内形成甲醇-dmc共沸物,从反应精馏塔塔顶采出的甲醇-dmc共沸物经第三换热器降温冷凝后进入膜分离器,膜分离器中从截留侧出口出来的物料进入常压塔,常压塔塔顶采出的甲醇-dmc常压共沸物经第五换热器降温冷凝后,大部分返回膜分离器的截留侧入口再次进行dmc/甲醇膜分离,其余部分回流,经上部入口重回常压塔;常压塔底部采出的dmc中间产品大部分进入dmc精制塔精制进一步提高浓度,其余部分通过第四换热器加热再沸,dmc蒸汽经过下部入口返回常压塔内部;蒸汽喷射真空系统为膜的渗透汽化过程提供需要的真空度,在膜两侧压差驱动作用下,经过膜分离器的渗透侧出口出来的渗透物主要为负压甲醇蒸汽,从膜分离器渗透侧出来后进入蒸汽喷射真空系统,与进入蒸汽喷射真空系统的高压产品蒸汽混合得到排出的中低压蒸汽,回收甲醇蒸汽的潜热;蒸汽喷射真空系统排出口的中低压蒸汽通过第二换热器给反应精馏塔底部采出的部分丙二醇料液加热,使丙二醇再沸得到丙二醇蒸汽,对蒸汽喷射真空系统排出的中低压蒸汽的潜热进行回收;
17.反应精馏塔底部的丙二醇大部分直接进入丙二醇精制塔中进行精制,其余通过第一换热器和第二换热器进行加热,其中第一换热器利用水蒸汽对丙二醇进行加热,第二换热器利用蒸汽喷射真空系统排出口的中低压蒸汽对丙二醇加热,加热后的丙二醇以蒸汽形式重新进入反应精馏塔下部,与经由第三换热器冷凝后的甲醇-dmc混合液进行充分的汽、液两相接触传质,保证精馏过程稳定运行。
18.优选地,蒸汽喷射真空系统的产品蒸汽喷射介质采用甲醇或者碳酸丙烯酯;
19.当选用甲醇作为喷射介质时,该喷射介质与膜分离器中渗透过来的甲醇蒸汽混合后,喷射介质混合物料经第二换热器换热后一部分返回反应精馏塔,一部分进入贮存罐;
20.当选用碳酸丙烯酯作为喷射介质时,该喷射介质与甲醇蒸汽混合,得到的是甲醇-碳酸丙烯酯的混合物料,该混合物料经第二换热器换热后进入贮存罐内可用于其它需要将碳酸丙烯酯和甲醇预混的化工反应。
21.优选地,所述蒸汽喷射真空系统包括五级或六级蒸汽喷射泵联用;
22.所述膜分离器包括串联设置的三级分子筛膜组。
23.在上述技术方案中,所述第一、二、四换热器为再沸器,所述第三、五换热器为冷凝器。
24.优选地,所述第一换热器、第四换热器均为采用低压生蒸汽作为换热工质的换热器;第三换热器、第五换热器均采用循环冷却水作为换热工质;第二换热器采用由蒸汽喷射
真空系统排出的高压喷射介质蒸汽和膜组件渗透侧的甲醇蒸汽混合的中低压蒸汽作为换热介质。
25.优选地,所述分离装置还包括与所述第三换热器连接的真空泵,所述真空泵用于抽出第三换热器中在反应开始前产生的废气。
26.在上述技术方案中,所述第一换热器用于对从反应精馏塔的底部采出的丙二醇加热,加热后的丙二醇循环进入反应精馏塔,丙二醇蒸汽向上回流,经过第二换热器中的甲醇-dmc混合液冷凝后向下回流,汽、液两相接触传质,使精馏过程连续进行。
27.优选地,所述第四换热器用于对从常压塔采出的部分dmc重新加热,加热后的dmc蒸汽循环进入常压塔,与通过第五换热器冷凝下来的甲醇-dmc混合液进行汽、液两相接触传质,保证常压塔中的精馏过程连续稳定运行。
28.在上述技术方案中,常压塔采出的dmc进入dmc精制塔精制得到符合标准的dmc产品。
29.本发明的有益效果是:
30.相比原加压精馏工艺,本发明方法整体运行不再需要中压蒸汽,加压操作条件取消,能耗等运行成本大幅降低。本发明还针对膜分离过程中的真空系统做了创新性的改进,引入以碳酸丙烯酯或者甲醇为喷射动力源的蒸汽喷射真空系统,取代传统膜分离中的真空泵,不仅能够提供膜分离所需要的真空度,同时还能将喷射蒸汽与甲醇蒸汽混合,回收甲醇蒸汽的潜热,同时蒸汽喷射真空系统排出口的物料通过第二换热器给部分丙二醇料液提供热量,进一步进行蒸汽潜热的回收,降低能耗。
附图说明
31.为了更清楚地说明本发明实施例或现有技术中的技术方案,下面将对实施例或现有技术描述中所需要使用的附图作简单地介绍,显而易见地,下面描述中的附图仅仅是本发明的一些实施例,对于本领域普通技术人员来讲,在不付出创造性劳动的前提下,还可以根据这些附图获得其他的附图。
32.其中:
33.图1是实施例1中使用的渗透汽化实验室装置的结构示意图;
34.附图标记说明:
35.1.油浴锅、2.分子筛膜管、3.液氮罐、4.冷阱、5.真空表、6.真空泵、7.缓冲瓶、8.第一管线、9.第二管线、10.第三管线、11.第四管线、12.第五管线、13.三口烧瓶、14.第六管线。
36.图2是实施例1中渗透通量和渗透侧甲醇含量随着温度的变化结果。
37.图3是实施例1中渗透通量和渗透侧甲醇含量随着原料中dmc浓度的变化结果(60℃)。
38.图4是90℃时90% ch3oh/dmc混合液的甲醇渗透通量和渗透侧甲醇含量随着时间的变化结果。
39.图5是温度和压力对dmc/甲醇分离性能的影响结果。
40.图6是温度、浓度、渗透侧压力对dmc/甲醇分离性能的影响结果。
41.图7是5kpa下甲醇和dmc的分离性能随温度的变化结果。
42.图8是分子筛膜醇水分离和dmc/甲醇分离对比图。
43.图9是脱甲醇膜的工业放大结果。
44.图10是本发明方法使用的分离装置的结构示意图;
45.图11是图10的分离装置中的膜分离器的结构示意图;
46.附图标记说明:
47.t-101
ꢀꢀꢀꢀꢀ
反应精馏塔
48.t-102
ꢀꢀꢀꢀꢀ
常压塔
49.e-101
ꢀꢀꢀꢀꢀ
第一换热器
50.e-102
ꢀꢀꢀꢀꢀ
第二换热器
51.e-103
ꢀꢀꢀꢀꢀ
第三换热器
52.e-104
ꢀꢀꢀꢀꢀ
第四换热器
53.e-105
ꢀꢀꢀꢀꢀ
第五换热器
54.m-101
ꢀꢀꢀꢀꢀ
膜分离器
55.m-1011
ꢀꢀꢀꢀ
分子筛膜组
56.p-101
ꢀꢀꢀꢀꢀ
进料泵
57.p-102
ꢀꢀꢀꢀꢀ
抽气泵
58.p-103
ꢀꢀꢀꢀꢀ
蒸汽喷射泵
59.v-101
ꢀꢀꢀꢀꢀ
贮存罐
60.c-101
ꢀꢀꢀꢀꢀ
压缩机。
具体实施方式
61.下面将结合本发明实施例中的附图,对本发明实施例中的技术方案进行清楚、完整地描述,显然,所描述的实施例仅仅是本发明一部分实施例,而不是全部的实施例。基于本发明中的实施例,本领域普通技术人员在没有作出创造性劳动前提下所获得的所有其他实施例,都属于本发明保护的范围。
62.实施例1分子筛膜筛选基础实验
63.为了确定本发明工艺中采用哪种分子筛膜能够有效地分离甲醇和碳酸二甲酯共沸物,分别采用了fau分子筛膜(fau沸石膜)和lta分子筛膜进行实验。lta分子筛膜直接商购获得。
64.一、渗透汽化实验室装置和实验方法
65.首先构建了如图1所示的渗透汽化实验室装置:将真空泵6与缓冲瓶7通过第一管线8连通;设置两组液氮罐和冷阱,将冷阱4置于液氮罐3中,两组冷阱4之间设置有三根管线(第二管线9、第三管线10、第四管线11,第二管线9和第三管线10并联),第二、三、四管线上均设置有阀门,缓冲瓶7与第二管线9通过第五管线12连通,第五管线12设置有真空表5;将分子筛膜管2置于三口烧瓶13中,分子筛膜管2与第四管线11通过第六管线14连通,将三口烧瓶13置于油浴锅1中。分子筛膜管2是在陶瓷多孔支撑管上生长分子筛膜得到,甲醇和碳酸二甲酯共沸物在陶瓷多孔支撑管外部流通,经陶瓷多孔支撑管表面生长的分子筛膜后甲醇渗透进入支撑管内,而碳酸二甲酯则留在管外,实现甲醇和碳酸二甲酯的分离。本实施例比较了fau分子筛膜和lta分子筛膜的效果。
66.实验过程如下:向三口烧瓶中加入甲醇和碳酸二甲酯共沸物,水浴加热保持一定温度,将固定有分子筛膜管的组件浸入甲醇/dmc共沸物料液中。打开真空泵,关闭第二、三、四管线上的阀门,排净管路内残留的空气。向液氮罐中加入液氮。之后打开第四管线上的阀门,使分子筛膜组件与冷阱通过第四管线相连,在压力驱动下,甲醇渗透到膜管内,并在冷阱中冷凝得到渗透液。收集渗透液,称量渗透液质量,通过气相色谱测定渗透液的组成。
67.二、fau分子筛膜检测结果
68.1、极限真空数据(60pa)
69.图2反映出dmc/ch3oh(3/7)经分子筛膜筛分后的渗透通量和渗透侧甲醇含量随着温度的变化,从图中可以看出甲醇的渗透通量随着温度的升高而逐渐上升,并且其渗透侧的甲醇含量在60℃以上达到99%以上。在60℃时,分子筛膜的甲醇通量达到0.53kg
·
m-2
·
h-1
,渗透侧的甲醇含量99.8%;在90℃时,分子筛膜的甲醇通量达到1.3kg
·
m-2
·
h-1
,渗透侧的甲醇含量99.5%;在110℃时,分子筛膜的甲醇通量达到4.2kg
·
m-2
·
h-1
,渗透侧的甲醇含量99.3%。
70.图3是渗透通量和渗透侧甲醇含量随着原料中dmc浓度的变化图,从图中可以看出渗透侧甲醇浓度随着原料中dmc浓度的减少而逐渐增加,甲醇渗透通量随原料侧dmc浓度的增加而降低,渗透侧甲醇浓度在98.5%以上。当原料中dmc浓度在30%~70%范围内,甲醇的通量在0.41~0.53kg
·
m-2
·
h-1
,表现出优异的分离性能。
71.从图4中可以看出膜分离性质比较稳定,运行360分钟后膜性能几乎没有变化,其中甲醇的渗透通量基本在2.6kg
·
m-2
·
h-1
附近,渗透侧甲醇含量在99.7%以上。并且我们对该分离体系做了物料衡算:原液质量为52.421g,分离360分钟后,渗透液体的质量为21.261g,原料侧液体剩余31.15g,损失0.1g,原料损失低于0.2%。另外从色谱给出的浓度数据,分离前原料侧的dmc浓度为7.2%,分离后原料侧的dmc浓度为12.1%,和从质量推算的结果一致。说明dmc几乎没有分解。
72.2、非极限真空数据
73.图5是渗透通量和渗透侧甲醇含量随着温度和真空侧压力的变化图,从图中可以看出渗透侧甲醇浓度几乎没有变化,都在99.2%以上。甲醇的渗透通量随温度的增加而增加;另外甲醇通量随着真空侧压力的降低而急剧上升,在5kpa(大多数工业泵能达到的水准)压力和100℃及以上时,其甲醇的通量仍能达到1kg
·
m-2
·
h-1
以上,渗透侧甲醇浓度为99.2%以上,表现出优异的dmc/ch3oh分离性能。
74.从图6中可以看出,随着原料侧甲醇浓度的降低,甲醇的通量和选择性在逐渐降低,同样随着真空侧压力的降低,甲醇的通量急剧上升。在真空侧压力5kpa,温度100℃,原料中dmc浓度在30%~60%时,甲醇通量都在0.5kg
·
m-2
·
h-1
以上,渗透侧甲醇的浓度随着原料侧甲醇浓度的增加而增加,在真空侧压力5kpa,温度100℃,dmc浓度在30%~60%时,渗透侧甲醇浓度在96%~99%之间;在真空侧压力5kpa,温度120℃,dmc浓度在30%~60%时,甲醇通量都在1.3kg
·
m-2
·
h-1
以上,渗透侧甲醇的浓度随着原料侧甲醇浓度的增加而增加,在真空侧压力5kpa,温度120℃,原料中dmc浓度在30%~60%时,渗透侧甲醇浓度在96%~99%之间,表现出优异的dmc/ch3oh分离性能。
75.从图7中可以看出甲醇的通量和温度基本呈正相关,渗透侧甲醇浓度都大于99.2%。在100℃时,原料中dmc浓度在30~60%之间,甲醇通量都大于0.5kg/m2h;在120℃
时,原料中dmc浓度在30~60%之间,甲醇通量都大于1.2kg/m
2 h,表现出十分优异的dmc/ch3oh分离性能。
76.3、脱甲醇膜的放大
77.采用本实施例方法分别对乙醇/水和dmc/甲醇进行分离。从图8可以看出,当渗透液水含量高于90%时,分子筛膜对dmc中甲醇的分离选择性与乙醇中水的选择性相似。乙醇/水测试效率高,因此本实验通过评价乙醇/水分离,确定分子筛膜的性能。
78.我们对甲醇分离膜进行放大实验,制备了三批fau分子筛膜样品,三批样品的制备方法中,调整了老化时间和晶化温度(第一、二批样品的老化时间分别是6h、10h,晶化温度分别是90、95℃),得到长度为1.03m的膜管。从首次放大的结果看,膜通量较低,选择性不稳定;经过优化老化温度和晶化温度,得到第二批管(即图9中第一次改进放大对应的样品),第二批管的选择性进一步提升,但是通量依旧降低;因此我们在此基础上,改进原料配方和生产工艺,使得得到的第三批fau分子筛膜样品(即图9中第二次改进放大对应的样品)在膜的微观结构得到了优化,晶间缺陷减少、结构更密、更完整,通量和选择性较第一、二批样品更好。从图9的结果可以看出第三批样品的通量都在0.5kg
·
m-2
·
h-1
左右,这些数据的测试是在静态环境下测试,实际情况会有液体剧烈流动,因此,我们将膜管截短,通过剧烈搅拌,去除浓差极化,测得实际通量约为1.8kg
·
m-2
·
h-1
,能满足生产需求。
79.fau分子筛膜在小试阶段,表现出优异的dmc/甲醇分离性能和稳定性。
80.第三批样品fau沸石膜的具体合成过程如下:
81.(1)按照如下方法配制合成液i:
82.制备溶液a1:15.11g naoh溶于180g去离子水中,然后加入1.82g偏铝酸钠,溶解即得溶液a1;
83.溶液b1:15.11g naoh溶于180g去离子水中,然后加入33.3g硅溶胶(其中含sio2的质量百分含量为40%),溶解即得溶液b1;
84.将溶液a1和溶液b1充分混合,得均匀澄清的合成液i。所得合成液i中,所含物质按照摩尔比折算70na2o:al2o3:20sio2:2000h2o。
85.(2)涂覆合成液并焙烧复合体
86.将圆柱形支撑体浸入合成液i中30s后,取出晾干,得到复合体f1(负载量为10mg/cm2,负载量在焙烧后通过质量变化得到)。接着将复合体f1置于马弗炉中,以5℃/min的升温速率升温至500℃,保持180min,然后自然冷却至室温备用。
87.(3)fau分子筛膜合成
88.将焙烧后的复合体f1用支架固定,分别垂直放置于聚四氟乙烯合成釜中,然后将合成液i转入合成釜之中;在微波合成之前,将合成釜置于70℃烘箱中,使得复合体f1在合成液i存在条件下老化18小时;之后将合成釜置于微波炉中,在4分钟内匀速升温至95℃;然后维持体系温度95℃(即晶化温度),反应30分钟。完成后分离膜管与液体,获得fau分子筛膜,表层分子筛膜组成为na1si
1.5
al1o5。
89.三、lta分子筛膜检测结果
90.将fau分子筛膜换为lta分子筛膜,对90℃、70%甲醇/30%dmc共沸物检测,结果显示lta分子筛的甲醇通量是0.05kg m-2
h-1
,渗透侧甲醇含量95%,效果明显差于fau分子筛膜。
91.实施例2甲醇和碳酸二甲酯共沸物的分离装置
92.本发明方法使用的甲醇和碳酸二甲酯共沸物的分离装置,其结构如图10所示,主要由反应精馏塔t-101、第一换热器e-101、第二换热器e-102、第三换热器e-103、第四换热器e-104、第五换热器e-105、膜分离器m-101、蒸汽喷射真空系统p-103、进料泵p-101、常压塔t-102、贮存罐v-101、丙二醇精制塔、dmc精制塔、压缩机c-101组成。
93.反应精馏塔t-101的顶部与第三换热器e-103、膜分离器m-101通过管线依次连通,膜分离器m-101的截留侧出口与进料泵p-101的进口通过管线连通,进料泵p-101的出口与常压塔t-102的中部通过管线连通,常压塔t-102的顶部与第五换热器e-105、膜分离器m-101的截留侧入口通过管线依次连通;第五换热器e-105的出口还通过管线与常压塔t-102的上部连通,用于常压塔t-102的顶部采出的部分甲醇-dmc蒸汽冷凝,冷凝液回流到常压塔t-102内,常压塔t-102的顶部采出的其余甲醇-dmc混合物则经过第五换热器e-105降温冷却后返回膜分离器m-101截留侧中再次进行分离;膜分离器m-101的渗透侧出口与蒸汽喷射真空系统p-103的抽吸口通过管线连通,蒸汽喷射真空系统p-103的排出口与第二换热器e-102、反应精馏塔t-101的中下部通过管线依次连通。贮存罐v-101与第二换热器e-102通过管线连通,膜分离器m-101包括渗透汽化膜组件。
94.膜分离器m-101的出口有渗透侧出口和截留侧出口,甲醇-dmc共沸物经第三换热器e-103降温冷凝后进入膜分离器m-101进行甲醇和dmc的分离,从渗透侧出口出来的物料中主要含有甲醇,从截留侧出口出来的物料为甲醇-dmc共混物,共混物中的dmc浓度高于膜分离器m-101的截留侧入口处的dmc浓度。
95.渗透汽化膜为分子筛膜,如图11所示,膜分离器m-101包括串联设置的多级分子筛膜组m-1011,上一级分子筛膜组m-1011的截留侧出口与下一级分子筛膜组m-1011的截留侧入口连接,每一级分子筛膜组m-1011的渗透侧出口并联,并与蒸汽喷射真空系统p-103的抽吸口连通。多级分子筛膜组对甲醇-dmc共沸物进行分离,通过多级分子筛膜组的分离,甲醇和dmc分离更完全。
96.在一些实施方式中,蒸汽喷射真空系统包括五级或六级蒸汽喷射泵联用,从而达到所需要的真空度;如图2所示,膜分离器m-101包括串联设置的三级分子筛膜组m-1011,分子筛膜为fau分子筛膜,经实验验证,fau分子筛膜对甲醇-dmc共沸物的分离效果优良,小试和中试实验中其分离效果均达到工艺要求。
97.反应精馏塔t-101的底部与丙二醇精制塔通过管线连通。在反应精馏塔t-101中碳酸丙烯酯、甲醇的反应同时产生丙二醇与dmc,对丙二醇精制后得到纯度达标的丙二醇产品。
98.反应精馏塔t-101的底部与第一换热器e-101的进口通过管线连通,第一换热器e-101的出口与反应精馏塔t-101通过管线连通,第一换热器e-101用于对从反应精馏塔t-101的底部采出的部分丙二醇加热,加热再沸后的丙二醇蒸汽循环进入反应精馏塔t-101,丙二醇蒸汽向上回流,经过第二换热器中的甲醇-dmc混合液冷凝后向下回流,汽、液两相接触传质,使精馏过程连续进行;除第一换热器e-101与水蒸气换热循环和第二换热器e-102与中低压蒸汽换热循环后重新进入反应精馏塔的丙二醇外,其余反应精馏塔t-101的底部采出的大部分丙二醇进入丙二醇精制塔。
99.常压塔t-102的底部与dmc精制塔通过管线连通,常压塔t-102采出的大部分dmc进
入dmc精制塔精制得到符合标准的dmc产品。
100.常压塔t-102的底部与第四换热器e-104的进口通过管线连通,第四换热器e-104的出口与常压塔t-102的中下部通过管线连通,第四换热器e-104用于对从常压塔t-102采出的部分dmc重新加热,加热后的dmc蒸汽循环进入常压塔t-102,与通过第五换热器e-105冷凝下来的甲醇-dmc混合液进行汽、液两相接触传质,保证常压塔中的精馏过程连续稳定运行;常压塔t-102底部采出的其余部分dmc进入dmc精制塔。
101.压缩机c-101与蒸汽喷射真空系统p-103的入口通过管线连通,用于对产品蒸汽加压,加压后的产品蒸汽进入蒸汽喷射真空系统p-103的蒸汽入口作为喷射动力介质。
102.在一些实施方式中,本发明的分离装置还包括与第三换热器e-103连接的真空泵p-102,真空泵p-102用于抽出第三换热器e-103中在反应开始前装置中存留的废气。
103.在一些实施方式中,第一换热器e-101、第二换热器e-102、第四换热器e-104为再沸器,所述第三换热器e-103、第五换热器e-105为冷凝器,第一换热器、第四换热器均为采用低压生蒸汽(水蒸气)作为换热工质的换热器;所述第三换热器、第五换热器均采用循环冷却水作为换热工质;所述第二换热器采用由蒸汽喷射真空系统排出的高压喷射介质蒸汽和膜组件渗透侧的甲醇蒸汽混合的中低压蒸汽作为换热介质。
104.实施例3膜分离耦合精馏的甲醇和碳酸二甲酯共沸物的分离方法
105.经过实施例1的实验验证后,构建了实施例2的装置,采用实施例2的装置进行甲醇和碳酸二甲酯共沸物的分离,按照如下步骤操作:
106.开启反应精馏塔t-101、第一换热器e-101、第二换热器e-102、第三换热器e-103、第四换热器e-104、第五换热器e-105、膜分离器m-101、蒸汽喷射真空系统p-103、压缩机c-101、进料泵p-101、常压塔t-102、抽气泵p-102,向反应精馏塔t-101中通入原料碳酸丙烯酯、催化剂、甲醇,进行反应,保持装置系统平稳运行,分别收集分离得到的dmc、甲醇和副产物丙二醇。
107.反应精馏塔t-101内原料反应生成dmc和丙二醇,dmc和原料中的甲醇在反应精馏塔t-101内形成甲醇-dmc共沸物,从反应精馏塔t-101塔顶采出的甲醇-dmc共沸物,含甲醇约70%,经第三换热器e-103降温冷凝后进入膜分离器m-101,单程将甲醇含量降至40%左右,膜分离器m-101中从截留侧出口出来的物料(甲醇-dmc共混物)进入常压塔t-102,常压塔t-102塔顶采出的甲醇-dmc常压共沸物经第五换热器e-105降温冷凝后,大部分再返回膜分离器m-101的截留侧入口再次进行dmc/甲醇膜分离,其余部分回流,经上部入口重回常压塔t-102;常压塔t-102底部采出含dmc>99%的dmc中间产品大部分进入dmc精制塔,经后续dmc精制塔将其浓度提到99.9%以上,其余部分通过第四换热器e-104加热再沸,dmc蒸汽经过下部入口返回常压塔t-102内部。蒸汽喷射真空系统p-103为膜的渗透汽化过程提供需要的真空度,经过膜分离器m-101的渗透侧出口出来的渗透物主要为甲醇,甲醇含量>98%,为负压甲醇蒸汽状态,从膜分离器m-101渗透侧出来后进入蒸汽喷射真空系统p-103,与进入蒸汽喷射真空系统p-103的高压产品蒸汽混合得到排出的中低压蒸汽,充分回收了甲醇蒸汽的潜热;蒸汽喷射真空系统p-103排出口的中低压蒸汽通过第二换热器e-102给反应精馏塔t-101底部采出的部分丙二醇料液加热,使丙二醇再沸得到丙二醇蒸汽,对蒸汽喷射真空系统p-103排出的中低压蒸汽的潜热进行回收,进一步降低能耗。
108.反应精馏塔t-101底部的丙二醇大部分直接进入丙二醇精制塔中进行精制,其余
通过第一换热器e-101和第二换热器e-102进行加热,其中第一换热器e-101利用水蒸汽对丙二醇进行加热,第二换热器利用蒸汽喷射真空系统p-103排出口的中低压蒸汽对丙二醇加热,加热后的丙二醇以蒸汽形式重新进入反应精馏塔t-101下部,与经由第三换热器冷凝后的甲醇-dmc混合液进行充分的汽、液两相接触传质,保证精馏过程稳定运行。
109.蒸汽喷射真空系统p-103的产品蒸汽喷射介质既可以采用甲醇也可以采用碳酸丙烯酯。当选用甲醇作为喷射介质,那么该喷射介质与膜分离器m-101中渗透过来的甲醇蒸汽混合后,喷射介质混合物料经第二换热器e-102换热后一部分返回反应精馏塔t-101,一部分进入贮存罐v-101。当选用碳酸丙烯酯作为喷射介质,那么该喷射介质与甲醇蒸汽混合,得到的是甲醇-碳酸丙烯酯的混合物料,该喷射介质混合物料经第二换热器e-102换热后进入贮存罐v-101内可用于其它需要将碳酸丙烯酯和甲醇预混的化工反应。
110.相比原加压精馏工艺的装置,本发明工艺整体运行不再需要中压蒸汽,加压操作条件取消,能耗等运行成本大幅降低。本发明还针对膜分离过程中的真空系统做了创新性的改进,引入以碳酸丙烯酯或者甲醇为喷射动力源的蒸汽喷射真空系统,取代传统膜分离中的真空泵,不仅能够提供膜分离所需要的真空度,同时还能有效回收甲醇蒸汽的潜热,此外蒸汽喷射真空系统排出口的物料给反应精馏塔釜供热进行蒸汽潜热的回收,进一步降低能耗。
111.将本发明方法与现有加压精馏工艺进行了对比测算,以生产5万吨dmc/年为例,计算出出了两种工艺对应的物料衡算表,计算得到两种方法的运行成本对比结果如表1中所示:相比目前较为普遍采用的高能耗的加压精馏工艺,本发明的膜分离耦合精馏新工艺节省了约50%的运行成本,不再需要中压蒸汽,新工艺显示出了良好的节能效益和适应性。以年产5万吨dmc为例,按照目前的原料价格,每吨产品的运行成本较加压精馏减少739.5元/吨产品,每年节省的运行成本为3865.4万元。
112.表1新老工艺运行成本对比
[0113][0114]
以上所揭露的仅为本发明较佳实施例而已,当然不能以此来限定本发明之权利范围,因此依本发明权利要求所作的等同变化,仍属本发明所涵盖的范围。