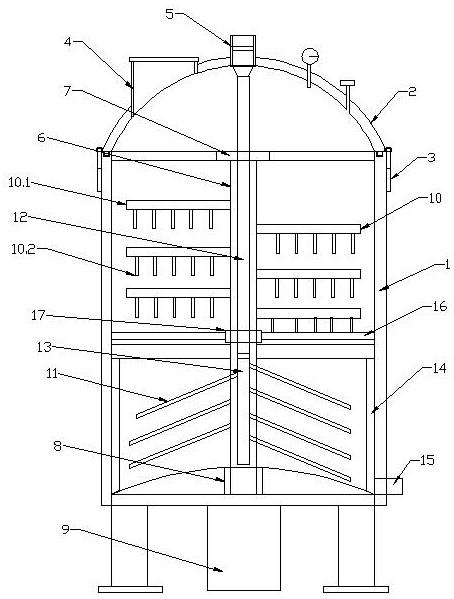
1.本发明涉及废旧塑料回收利用技术领域,具体涉及一种废聚丙烯塑料再利用生产工艺。
背景技术:2.现如今,废弃塑料回收问题已经成为重大的生态问题,有效实现废弃塑料的回收再利用不仅能够保护好生态环境,而且可以降低塑料相关企业的生产成本。废聚丙烯塑料(pp)的资源化再利用是将废聚丙烯酸塑料作为一种有效资源,再次加以利用的过程。对于成分单一、老化程度低的废聚丙烯塑料可通过如分类、清洗、破碎、熔融、造粒成型这类简单方式进行再利用;而对于那些老化程度相对较高、力学性质或/和机械性能跟新塑料相差较大的废聚丙烯塑料,需要对其进行改性再利用。常用的改性方法有填充改性、共混改性等,其中填充改性是通过往废聚丙烯塑料中加入一定量的无机或有机填料以提高制品的某些性能,如刚性、硬度等;而共混改性则是将废聚丙烯塑料与其他塑料和物质共混,以提高废聚丙烯塑料的力学性能。
3.实际中,很多pp塑料是经过两次、甚至是多次再利用的,加上回收前在使用过程中的紫外线老化,其性能都有明显下降,致使pp回收料的熔融指数随加工次数不断增加而上升,因此,在利用废旧pp料生产pp编织袋时,需要与新料混合搭配使用。在保证pp编织袋质量的前提下,废pp料用量及质量都是有限定的,而且还需对包括熔融温度、拉丝温度等在内的生产技术参数进行改变,这就严重影响了废pp的再利用价值。
技术实现要素:4.针对上述现有技术中存在的不足,本发明的目的是提供一种废聚丙烯塑料再利用生产工艺,通过茂金属聚丙烯等复合改性剂对废旧pp进行改性,使聚丙烯形成“海—岛”结构,有效增强了其抗冲击韧性和抗拉伸强度,且能够通过助剂来调节粒子的熔融指数,使塑化更为均匀,避免影响后续拉伸工序技术参数改变和扁丝质量。
5.为实现上述目的,本发明采用的技术方案是:一种废聚丙烯塑料再利用生产工艺,通过破碎、预清洗、浮选除杂、风干、混炼改性、塑化挤出、冷却造粒这些步骤来完成的,其特征在于,所述混炼改性步骤是将废旧聚丙烯塑料粒子、茂金属聚丙烯粒子、山梨醇类成核剂置于反应釜中,升温至210~230℃,在500~700r/min的转速下反应3h~6h;然后往反应釜中缓慢加入光稳定剂、抗氧化剂、分散剂,在转速为400~600r/min下,混炼15~30min;其中茂金属聚丙烯粒子、山梨醇类成核剂的添加量分别为废旧聚丙烯塑料粒子总重的10%~18%、0.1~0.4%;而稳定剂、抗氧化剂、分散剂的加入量分别为废旧聚丙烯塑料粒子总重的3~5%、0.3~0.6%、4~6%。
6.茂金属聚丙烯具有相对分子量分布窄、微晶较小、抗冲击强度和韧性极佳、透明性好、光泽度高、抗辐射性能好、绝缘性能优异等优点。采用茂金属聚丙烯对废旧聚丙烯进行改性,能够使废旧聚丙烯获得茂金属等相关功能,同时能够使加入的茂金属聚丙烯和山梨
醇成核剂与废聚丙烯形成“海—岛”结构,从而大大提高废旧聚丙烯的韧性。试验中,茂金属聚丙烯、山梨醇成核剂的加入量以及加入顺序,对最后的改性结构,具体是抗冲击韧性和拉伸强度有着显著区别,尤其是茂金属聚丙烯和山梨醇成核剂的加入顺序,只有茂金属聚丙烯、山梨醇成核剂的加入量分别为14%、0.25%,且控制加入顺序为先加入茂金属聚丙烯一段时间后再加入山梨醇成核剂后,才能使废旧聚丙烯塑料粒子与新pp粒子的加入量比为60:100时,复合粒子的抗冲击韧性、拉伸强度超过国家标准以上。
7.进一步,上述混炼改性中的废旧聚丙烯塑料粒子在混炼改性之前先用紫外线在密闭环境下照射1~3天,然后送去硫化15~25min。通过该步骤实现对废旧聚丙烯塑料粒子的抗拉伸强度的提升。
8.进一步,上述塑化挤出步骤是先将新聚丙烯塑料粒子、超支化聚合物按照100份、6~8份的重量份进行混合,然后送入塑化挤出机中,在常规的熔融温度下先融化,再加入50-60份经过混炼改性的废旧聚丙烯塑料溶液,混合均匀后,挤出。该步骤中废旧聚丙烯塑料粒子的添加量超过了常规的添加量(添加比例一般是低于40的),但是其制得的扁丝的抗拉伸强度和伸长率均在国家标准以上。而且本步骤添加助剂超支化聚合物,能够使新、旧粒子的熔融指数接近,不需要改变熔融挤出温度和后续的拉丝工序中相应技术参数。
9.山梨醇类成核剂能够有效改善聚丙烯塑料的透明性、热变形温度及刚性,其成核效果好,但是其加入到反应釜内容易被杂质固定,或粘附到反应釜内壁上,从而影响其效果。因此,上述混炼改性中,最好是在每次使用之前先将反应釜内清洗干净,然后将废旧聚丙烯塑料粒子与茂金属聚丙烯塑料粒子先加入到反应釜内,反应釜内升温至210~230℃,在搅拌作用下使两者进行融化及预混合均匀,再在搅拌作用下加入山梨醇类成核剂,在加入山梨醇类成核剂的同时,采用刮板对反应釜内壁进行刮扫并同时阻挡山梨醇类成核剂直接喷向反应釜内壁。
10.进一步,为不影响山梨醇类成核剂的成核效果,进一步对反应釜结构进行改进,具体是反应釜,包括反应釜体、釜盖,所述釜盖通过多个升降机构压在反应釜体顶部开口上且釜盖与反应釜体形成密封连接;在釜盖上固定连接有固体料进口、液体料进口,液体料进口位于釜盖的正中间位置,且在不进料的时候,固体料进口与液体料进口是属于封闭状态;在反应釜体内设置有搅拌轴,搅拌轴的顶部与通过支架固定在反应釜体内的上部轴承座旋转连接,搅拌轴底部与固定在反应釜体内底部的下部轴承座旋转连接且搅拌轴该端穿过该下部轴承座后固定在反应釜体外的伺服电机固定连接;所述搅拌轴为顶部开口且内空的空心轴,在搅拌轴的上段固定连接有第一搅拌叶,第一搅拌叶包括多根按不同高度位置设置的横向搅拌杆、固定在每根横向搅拌杆底部的多根纵向搅拌杆,搅拌轴的下端两侧固定连接有多个按不同高度位置分布的第二搅拌叶,第二搅拌叶末端封闭但内部空心;在液体料进口上且反应釜体内的端部固定连接有固定送料管,固定送料管伸进空芯的搅拌轴内且在固定送料管的底部通过旋转接头连接有旋转送料管,第二搅拌叶的内端伸进搅拌轴内固定连接在旋转送料管上且两者相连通;上述固定送料管是由上、下两端的硬质管和中间的波纹管构成,而旋转送料管为硬质管;在搅拌轴上还通过横向支架固定有至少两个刮板,刮板位于第二搅拌叶的外端且刮板与反应釜体内壁相贴合;反应釜体内底部为中间凸起、周边往外下斜状,且在反应釜体内底部一侧固定连接且连通有一耐高温抽吸管;在第一搅拌叶与第二搅拌叶之间的反应釜体内还固定连接有120目过滤网,在过滤网中间开设有穿孔且在
穿孔内固定有与搅拌轴旋转连接的中间轴承座。
11.本领域技术人员熟知,成核剂的添加方式主要有反应釜体外、反应釜体内,釜内添加成核剂可使成核剂充分分散并与pp混合均匀,提高成核效率和制品的均匀性,然而在釜内添加成核剂的难度较大,究其原因可能是添加后,成核剂被除pp料外的其他杂质固定,或是粘附到反应釜内壁上,这在生产透明pp塑料的工艺中往反应釜体内添加成核剂最后导致催化剂活性降低中得以证实。因此,本技术通过对改性反应釜的结构以及改性过程中各原料的添加顺序进行改进,从而有效保证改性效果,实现在反应釜内完成混炼改性。
附图说明
12.图1本发明涉及到的反应釜结构示意图;图2为本发明涉及到的120目过滤网等的俯视示意图;图3为本发明涉及到的刮板等结构俯视示意图;其中,1、反应釜体,2、釜盖,3、升降机构,4、固体料进口,5、液体料进口,6、搅拌轴,7、上部轴承座,8、下部轴承座,9、伺服电机,10、第一搅拌叶,10.1、横向搅拌杆,10.2、纵向搅拌杆,11、第二搅拌叶,12、固定送料管,13、旋转送料管,14、刮板,15、耐高温抽吸管,16、120目过滤网,17、中部轴承座。
具体实施方式
13.现结合具体实施例,来对本发明作进一步的阐述。以下仅为本发明的优选实施方式,并非限制本发明的保护范围。任何在不脱离本发明的构思前提下的等同或相似替换,均应落在本发明的保护范围内。下文未详述部分,均应参照现有技术进行。
14.实施例一本实施例的废聚丙烯塑料再利用生产工艺,通过如下步骤来实现:(1)破碎:将回收的废旧聚丙烯塑料送入破碎机中进行破碎至3~5cm见方大小,(2)预清洗:将经过破碎的废旧塑料粒子送入清洗池中进行常规清洗,主要是去掉泥沙和油剂;(3)浮选除杂:将经过预清洗的废旧塑料粒子送入浮选设备中,浮选池中事先加入有清洗使用后的水,按常规方式进行四级以上的浮选,去除残留的杂质;(4)风干:按常规方式将经过浮选的废旧塑料粒子进行风干;(5)混炼改性:将废旧聚丙烯塑料粒子、茂金属聚丙烯粒子、山梨醇类成核剂一起置于常规的反应釜中,升温至210~230℃,在500~700r/min的转速下反应6h;然后往反应釜中缓慢加入光稳定剂、抗氧化剂、分散剂,在转速为400~600r/min下,混炼30min;其中茂金属聚丙烯粒子、山梨醇类成核剂的添加量分别为废旧聚丙烯塑料粒子总重的14%、0.25%;而稳定剂、抗氧化剂、分散剂的加入量分别为废旧聚丙烯塑料粒子总重的5%、0.6%、6%;(6)塑化挤出:先将新聚丙烯塑料粒子、超支化聚合物按照100份、6份的重量份进行混合,然后送入塑化挤出机中,在常规的熔融温度下先融化,再加入60份经过步骤(5)混炼改性的废旧聚丙烯塑料溶液,混合均匀后,挤出;(7)冷却造粒:按常规方式对塑化挤出的粒子流进行冷却并切成粒子。
15.采用本实施例制得的的粒子进行拉伸出来的扁丝抗冲击强度达到12.5kj/m
²
,拉
伸强度为19.8mpa、断裂伸长率为25%。
16.实施例二本实施例中的废聚丙烯塑料再利用生产工艺,通过如下步骤来实现:(1)破碎:将回收的废旧聚丙烯塑料送入破碎机中进行破碎至3~5cm见方大小,(2)预清洗:将经过破碎的废旧塑料粒子送入清洗池中进行常规清洗,主要是去掉泥沙和油剂;(3)浮选除杂:将经过预清洗的废旧塑料粒子送入浮选设备中,浮选池中事先加入有清洗使用后的水,按常规方式进行四级以上的浮选,去除残留的杂质;(4)风干:按常规方式将经过浮选的废旧塑料粒子进行风干;(5)混炼改性:在每次使用之前先将反应釜内清洗干净,然后将废旧聚丙烯塑料粒子与茂金属聚丙烯塑料粒子先加入到常规的反应釜内,反应釜内升温至210~230℃,在300~500r/min搅拌作用下使两者进行融化及预混合均匀1h,再在500~700r/min搅拌作用下加入山梨醇类成核剂搅拌反应5h后,往反应釜中缓慢加入光稳定剂、抗氧化剂、分散剂,在转速为400~600r/min下,混炼30min;其中茂金属聚丙烯粒子、山梨醇类成核剂的添加量分别为废旧聚丙烯塑料粒子总重的14%、0.25%;而稳定剂、抗氧化剂、分散剂的加入量分别为废旧聚丙烯塑料粒子总重的5%、0.6%、6%;(6)塑化挤出:先将新聚丙烯塑料粒子、超支化聚合物按照100份、6份的重量份进行混合,然后送入塑化挤出机中,在常规的熔融温度下先融化,再加入60份经过混炼改性的废旧聚丙烯塑料溶液,混合均匀后,挤出;(7)冷却造粒:按常规方式对塑化挤出的粒子流进行冷却并切成粒子。
17.采用本实施例制得的的粒子进行拉伸出来的扁丝抗冲击强度达到约15.1kj/m
²
,拉伸强度约为22.4mpa、断裂伸长率约为33%。
18.实施例三本实施例中的废聚丙烯塑料再利用生产工艺,通过如下步骤来实现:(1)破碎:将回收的废旧聚丙烯塑料送入破碎机中进行破碎至3~5cm见方大小,(2)预清洗:将经过破碎的废旧塑料粒子送入清洗池中进行常规清洗,主要是去掉泥沙和油剂;(3)浮选除杂:将经过预清洗的废旧塑料粒子送入浮选设备中,浮选池中事先加入有清洗使用后的水,按常规方式进行四级以上的浮选,去除残留的杂质;(4)风干:按常规方式将经过浮选的废旧塑料粒子进行风干;(5)混炼改性:在每次使用之前先将反应釜内清洗干净,然后将废旧聚丙烯塑料粒子与茂金属聚丙烯塑料粒子先加入到常规的反应釜内,反应釜内升温至210~230℃,在300~500r/min搅拌作用下使两者进行融化及预混合均匀1h,再在500~700r/min搅拌作用下加入山梨醇类成核剂搅拌反应5h后,往反应釜中缓慢加入光稳定剂、抗氧化剂、分散剂,在转速为400~600r/min下,混炼30min;其中茂金属聚丙烯粒子、山梨醇类成核剂的添加量分别为废旧聚丙烯塑料粒子总重的18%、0.4 %;而稳定剂、抗氧化剂、分散剂的加入量分别为废旧聚丙烯塑料粒子总重的5%、0.6%、6%;(6)塑化挤出:先将新聚丙烯塑料粒子、超支化聚合物按照100份、6份的重量份进行混合,然后送入塑化挤出机中,在常规的熔融温度下先融化,再加入60份经过混炼改性的
废旧聚丙烯塑料溶液,混合均匀后,挤出;(7)冷却造粒:按常规方式对塑化挤出的粒子流进行冷却并切成粒子。
19.采用本实施例制得的的粒子进行拉伸出来的扁丝抗冲击强度达到约13.9kj/m
²
,拉伸强度约为21.6mpa、断裂伸长率约为27%。
20.实施例四本实施例中的废聚丙烯塑料再利用生产工艺,通过如下步骤来实现:(1)破碎:将回收的废旧聚丙烯塑料送入破碎机中进行破碎至3~5cm见方大小,(2)预清洗:将经过破碎的废旧塑料粒子送入清洗池中进行常规清洗,主要是去掉泥沙和油剂;(3)浮选除杂:将经过预清洗的废旧塑料粒子送入浮选设备中,浮选池中事先加入有清洗使用后的水,按常规方式进行四级以上的浮选,去除残留的杂质;(4)风干:按常规方式将经过浮选的废旧塑料粒子进行风干;(5)混炼改性:在每次使用之前先将反应釜内清洗干净,然后将废旧聚丙烯塑料粒子与茂金属聚丙烯塑料粒子先加入到特制的反应釜内。如图1-3所示,这种特制的反应釜包括反应釜体1、釜盖2,釜盖2通过多个升降机构3压在反应釜体1顶部开口上且釜盖2与反应釜体1形成密封连接;在釜盖2上固定连接有固体料进口4、液体料进口5,液体料进口5位于釜盖2的正中间位置,且在不进料的时候,固体料进口4与液体料进口5是属于封闭状态;在反应釜体1内设置有搅拌轴6,搅拌轴6的顶部与通过支架固定在反应釜体1内的上部轴承座7旋转连接,搅拌轴6底部与固定在反应釜体1内底部的下部轴承座8旋转连接且搅拌轴6该端穿过该下部轴承座8后固定在反应釜体1外的伺服电机9固定连接;搅拌轴6为顶部开口且内空的空心轴,在搅拌轴6的上段固定连接有第一搅拌叶10,第一搅拌叶10包括多根按不同高度位置设置的横向搅拌杆10.1、固定在每根横向搅拌杆10.1底部的多根纵向搅拌杆10.2,搅拌轴6的下端两侧固定连接有多个按不同高度位置分布的第二搅拌叶11,第二搅拌叶11末端封闭但内部空心;在液体料进口5上且反应釜体1内的端部固定连接有固定送料管12,固定送料管12伸进空芯的搅拌轴6内且在固定送料管12的底部通过旋转接头连接有旋转送料管13,第二搅拌叶11的内端伸进搅拌轴6内并固定连接在旋转送料管13上且第二搅拌叶11与旋转送料管13相连通;固定送料管12是由上、下两端的硬质管和中间的波纹管构成,而旋转送料管13为硬质管,在搅拌轴6旋转下,带动第二搅拌叶11、旋转送料管13旋转;在搅拌轴6上还通过横向支架固定有至少两个刮板14,刮板14位于第二搅拌叶11的外端且刮板14与反应釜体1内壁相贴合;反应釜体1内底部为中间凸起、周边往外下斜状,且在反应釜体1内底部一侧固定连接且连通有一耐高温抽吸管15;在第一搅拌叶10与第二搅拌叶11之间的反应釜体1内还固定连接有120目过滤网16,在过滤网16中间开设有穿孔且在穿孔内固定有与搅拌轴6旋转连接的中间轴承座17;在将废旧聚丙烯塑料粒子与茂金属聚丙烯塑料粒子由固体料进口4加入到反应釜体1内后,加热使反应釜体1内升温至210~230℃,然后开启伺服电机9,带动搅拌轴6、主要是第一搅拌叶10在300~500r/min搅拌作用下使废旧聚丙烯塑料粒子与茂金属聚丙烯塑料粒子进行融化及预混合均匀1h,融化的混合液体经过滤后进入第二搅拌叶所在区域中,再在第二搅拌叶11、转速为500~700r/min的搅拌作用下由液体料进口5加入山梨醇类成核剂,山梨醇类成核剂直接进入第二搅拌叶11所在区域中,避免在杂质容易携带区域(因茂金属聚
丙烯塑料粒子和废旧聚丙烯塑料粒子为固体,杂质不易去除,故在过滤网16以上的部位为杂质容易携带的区域),采用刮板14对反应釜体1内壁进行刮扫并同时阻挡山梨醇类成核剂直接喷向反应釜体1内壁,搅拌反应5h后,由液体料进口5往反应釜体1中缓慢加入光稳定剂、抗氧化剂、分散剂,在转速为400~600r/min下,混炼30min;其中茂金属聚丙烯粒子、山梨醇类成核剂的添加量分别为废旧聚丙烯塑料粒子总重的14%、0.25%;而稳定剂、抗氧化剂、分散剂的加入量分别为废旧聚丙烯塑料粒子总重的5%、0.6%、6%;(6)塑化挤出:先将新聚丙烯塑料粒子、超支化聚合物按照100份、6份的重量份进行混合,然后送入塑化挤出机中,在常规的熔融温度下先融化,再加入60份经过混炼改性的废旧聚丙烯塑料溶液,混合均匀后,挤出;(7)冷却造粒:按常规方式对塑化挤出的粒子流进行冷却并切成粒子。
21.采用本实施例制得的的粒子进行拉伸出来的扁丝抗冲击强度达到约15.5kj/m
²
,拉伸强度约为22.7mpa、断裂伸长率约为36%。
22.实施例五本实施例中的废聚丙烯塑料再利用生产工艺,通过如下步骤来实现:(1)破碎:将回收的废旧聚丙烯塑料送入破碎机中进行破碎至3~5cm见方大小,(2)预清洗:将经过破碎的废旧塑料粒子送入清洗池中进行常规清洗,主要是去掉泥沙和油剂;(3)浮选除杂:将经过预清洗的废旧塑料粒子送入浮选设备中,浮选池中事先加入有清洗使用后的水,按常规方式进行四级以上的浮选,去除残留的杂质;(4)风干:按常规方式将经过浮选的废旧塑料粒子进行风干;(5)紫外线辐射:用紫外线在密闭环境下照射3天,然后送去硫化25min;(6)混炼改性:在每次使用之前先将反应釜内清洗干净,然后将废旧聚丙烯塑料粒子与茂金属聚丙烯塑料粒子先加入到特制反应釜内,特制的反应釜结构如图1-3所示,先加热使反应釜内升温至210~230℃,在300~500r/min搅拌作用下使两者进行融化及预混合均匀1h,再在500~700r/min搅拌作用下加入山梨醇类成核剂,在加入山梨醇类成核剂的同时,采用刮板对反应釜内壁进行刮扫并同时阻挡山梨醇类成核剂直接喷向反应釜内壁,搅拌反应5h后,往反应釜中缓慢加入光稳定剂、抗氧化剂、分散剂,在转速为400~600r/min下,混炼30min;其中茂金属聚丙烯粒子、山梨醇类成核剂的添加量分别为废旧聚丙烯塑料粒子总重的14%、0.25%;而稳定剂、抗氧化剂、分散剂的加入量分别为废旧聚丙烯塑料粒子总重的5%、0.6%、6%;(7)塑化挤出:先将新聚丙烯塑料粒子、超支化聚合物按照100份、6份的重量份进行混合,然后送入塑化挤出机中,在常规的熔融温度下先融化,再加入60份经过混炼改性的废旧聚丙烯塑料溶液,混合均匀后,挤出;(8)冷却造粒:按常规方式对塑化挤出的粒子流进行冷却并切成粒子。
23.采用本实施例制得的的粒子进行拉伸出来的扁丝抗冲击强度达到约15.6kj/m
²
,拉伸强度约为22.9mpa、断裂伸长率约为36%。