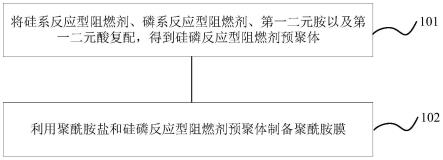
1.本发明涉及聚酰胺膜技术领域,尤其涉及一种聚酰胺膜及制备方法、电子器件。
背景技术:2.目前,聚酰胺树脂薄膜如双向拉伸尼龙薄膜(bopa)膜等具强度高,阻隔性好,透明性好等优点,被广泛用在电器、母线、磁盘驱动、显示器、开关接头、真空袋以及食品包装袋中。但是聚酰胺的氧指数为24,属于可燃材料,阻燃性差,这些缺点严重限制了其应用。
3.在共聚阻燃改性中发现磷系阻燃剂的加入能够较好的改善阻燃性能,但是加入反应型磷系阻燃剂后,由于磷反应阻燃剂本身的磷碳键不稳定,所以分解温度会低,当高温聚合生产聚酰胺膜时,磷反应阻燃剂容易发生副反应导致树脂变黄,使得黄色指数会变高,严重限制了其在颜色要求高的领域的应用。因此,需要开发一种白度高的阻燃聚酰胺膜。
技术实现要素:4.本发明的目的在于提供一种聚酰胺膜及制备方法、电子器件,该聚酰胺膜的白度较高,提高了聚酰胺膜的光学性能,从而提高了聚酰胺膜的光稳定性。
5.第一方面,本发明提供一种聚酰胺膜的制备方法,包括:将硅系反应阻燃剂、磷系反应阻燃剂、第一二元胺以及第一二元酸复配,得到硅磷反应型阻燃剂预聚体;
6.利用聚酰胺盐和硅磷反应型阻燃剂预聚体制备聚酰胺膜。
7.与现有技术相比,本发明提供的聚酰胺膜的制备方法具有以下优势:
8.本发明实施例提供的聚酰胺膜的制备方法中,首先将硅系反应阻燃剂、磷系反应阻燃剂、二元胺以及二元酸复配,得到硅磷反应型阻燃剂预聚体。由于硅系反应阻燃剂含有磷氧基团或芳基的有机酸基团,容易吸电子,在高温聚合过程中容易产生副产物环戊酮,导致阻燃聚酰胺变黄和发灰。当加入硅系反应阻燃剂时,由于硅系反应阻燃剂属于碱性阻燃剂,硅系反应型阻燃剂的引入会中和磷系反应型阻燃剂给聚酰胺带来的酸性,从而阻止聚酰胺变黄和发灰,使得聚酰胺的白度增高,从而可以制备出白度高的聚酰胺膜,提高了聚酰胺膜的光学性能,增强了聚酰胺膜的光稳定性。同时,将硅系反应阻燃剂、磷系反应阻燃剂、二元胺以及二元酸复配,可以使得磷系反应型阻燃剂和硅系反应型阻燃剂分布在二元胺以及二元酸分子链端部,避免了硅系反应阻燃剂高温聚合过程中产生副产物环戊酮,从而使得聚酰胺不易变黄和发灰。另外,由于硅系反应型阻燃剂是粘稠的聚硅氧烷聚合物,可以紧密的聚合在聚酰胺中,避免了迁移至聚酰胺表面。从而使得聚酰胺复合膜的阻燃效果提高,通过两种阻燃剂的协调作用,使得聚酰胺膜的光学性能和阻燃性能能大大提高。
9.另外,本发明实施例中,由于硅系反应型阻燃剂是粘稠的聚硅氧烷聚合物,可以与聚酰胺紧密连接,可以省略粘接剂等原料,简化了工艺步骤,节约了成本。
10.由上可见,本发明提供的聚酰胺膜的制备方法可以提高聚酰胺膜的白度,还能提高聚酰胺膜的光学性能,从而提高聚酰胺膜的光稳定性。
11.第二方面,本发明还提供一种聚酰胺膜,聚酰胺膜采用第一方面所述的聚酰胺膜
的制备方法制备而成。
12.与现有技术相比,本发明提供的聚酰胺膜的有益效果与第一方面提供的聚酰胺膜的制备方法的有益效果相同,此处不做赘述。
13.第三方面,本发明还提供一种电子器件,所述电子器件包括第二方面提供的聚酰胺膜。
14.与现有技术相比,本发明提供的电子器件的有益效果与第二方面聚酰胺膜的有益效果相同,此处不做赘述。
附图说明
15.此处所说明的附图用来提供对本发明的进一步理解,构成本发明的一部分,本发明的示意性实施例及其说明用于解释本发明,并不构成对本发明的不当限定。在附图中:
16.图1为本发明实施例的聚酰胺膜的制备流程图;
17.图2为本发明实施例的硅磷反应型阻燃剂预聚体的制备流程图。
具体实施方式
18.为了使本发明所要解决的技术问题、技术方案及有益效果更加清楚明白,以下结合实施例,对本发明进行进一步详细说明。应当理解,此处所描述的具体实施例仅仅用以解释本发明,并不用于限定本发明。
19.此外,术语“第一”、“第二”仅用于描述目的,而不能理解为指示或暗示相对重要性或者隐含指明所指示的技术特征的数量。由此,限定有“第一”、“第二”的特征可以明示或者隐含地包括一个或者更多个该特征。在本发明的描述中,“多个”的含义是两个或两个以上,除非另有明确具体的限定。“若干”的含义是一个或一个以上,除非另有明确具体的限定。
20.目前聚酰胺因为性能优良,应用非常广泛。但是未经阻燃改性的聚酰胺,阻燃性能差,垂直燃烧水平只能达到ul94-2,氧指数为24%,并且燃烧过程中还会有熔滴现象。在共聚阻燃改性中发现磷系阻燃剂的加入能够较好的改善阻燃性能,但是加入反应型磷系阻燃剂后,磷系阻燃剂的热分解温度低,在高温聚合过程中容易发生副反应导致树脂变黄,黄色指数会变高,严重限制了其在白度要求高的领域的应用。
21.针对上述问题,本发明实施例提供一种电子器件,其可以包括本发明实施例的聚酰胺膜,以使得聚酰胺膜的白度较高,提高聚酰胺膜的光学性能,从而提高聚酰胺膜的光稳定性。在实际应用中,该电子器件可以包括电器、母线、磁盘驱动、显示器、开关接头,也可以包括其它电子器件,此处不做限定。
22.本发明实施例提供的一种聚酰胺膜,可以应用于上述电子器件。本发明实施例的聚酰胺膜的材料包括硅系反应型阻燃剂、磷系反应型阻燃剂、二元胺和二元酸。
23.应该说明的是,本发明实施例的第一二元胺、第一二元酸、第二二元胺和第二二元酸中的术语“第一”、“第二”仅用于区分二元胺和二元酸在不同的反应中的使用,“第一”、“第二”并不用于限定量的关系。例如:下文中第一二元胺以及第一二元酸是二元胺和二元酸在制备硅磷反应型阻燃剂预聚体中的使用,第二二元胺以及第二二元酸中是二元胺和二元酸在制备聚酰胺盐中的使用。第二二元胺和第一二元胺可以相同,也可以不同,第二二元酸和第一二元酸可以相同也可以不同。所述二元酸可以为选自脂肪族二元酸或芳香族二元
酸中的至少一种。所述二元胺可以为选自脂肪族二元胺或芳香族二元胺中的至少一种。
24.本发明实施例还提供一种聚酰胺膜的制备方法,其可以用于制备本发明实施例的聚酰胺膜。图1示出了本发明实施例的聚酰胺膜的制备流程图,如图1所示,本发明实施例的聚酰胺膜的制备方法包括:
25.步骤101:将硅系反应型阻燃剂、磷系反应型阻燃剂、第一二元胺以及第一二元酸复配,得到硅磷反应型阻燃剂预聚体。
26.示例性的,本发明实施例将硅系反应型阻燃剂、磷系反应型阻燃剂、第一二元胺以及第一二元酸复配,形成硅磷反应型阻燃剂预聚体盐溶液,反应温度为10~100℃,该盐溶液的质量浓度为10%~90%。
27.由上可见,由于硅系反应阻燃剂含有磷氧基团或芳基的有机酸基团,容易吸电子,在高温聚合过程中容易产生副产物环戊酮,导致阻燃聚酰胺变黄和发灰。当加入硅系反应阻燃剂时,由于硅系反应阻燃剂属于碱性阻燃剂,硅系反应型阻燃剂的引入会中和磷系反应型阻燃剂给聚酰胺带来的酸性,从而阻止聚酰胺变黄和发灰,使得聚酰胺的白度增高,从而可以制备出白度高的聚酰胺膜,提高了聚酰胺膜的光学性能,增强了聚酰胺膜的光稳定性。同时,将硅系反应阻燃剂、磷系反应阻燃剂、二元胺以及二元酸复配,可以使得磷系反应型阻燃剂和硅系反应型阻燃剂分布在二元胺以及二元酸分子链端部,避免了硅系反应阻燃剂高温聚合过程中产生副产物环戊酮,从而使得聚酰胺不易变黄和发灰。另外,由于硅系反应型阻燃剂是粘稠的聚硅氧烷聚合物,可以紧密的聚合在聚酰胺中,避免了迁移至聚酰胺表面。从而使得聚酰胺复合膜的阻燃效果提高,通过两种阻燃剂的协调作用,使得聚酰胺膜的光学性能和阻燃性能能大大提高。
28.另外,本发明实施例中,由于硅系反应型阻燃剂是粘稠的聚硅氧烷聚合物,可以与聚酰胺紧密连接,可以省略粘接剂等原料,简化了工艺步骤,节约了成本。
29.步骤102:利用聚酰胺盐和所述硅磷反应型阻燃剂预聚体制备聚酰胺膜。
30.示例性的,本发明实施例中将聚酰胺盐溶液加入高温高压反应釜,然后加入复配后的硅磷反应型阻燃剂预聚体盐溶液混合,经过三次正压和负压置换,使反应釜中含有0.04mpa的氮气,加热使温度达到230℃,压力达到2.5mpa.然后经过40分钟降至大气压,同时升温至275℃~280℃,抽真空,保持温度在275℃~280℃,抽真空至-0.06mpa,保持5分钟。接着通氮气使釜内压力达到0.1mpa,在200℃~350℃温度下,通过挤出机熔融后,统一经过模头流出,并在-200℃~100℃温度下在急冷辊上冷却,形成片材,即聚酰胺膜。该片材可以为拉伸片材或非拉伸片材,其相对粘度在1.8~2.7。
31.图2示出了本发明实施例的硅磷反应型阻燃剂预聚体的制备流程图,如图2所示,本发明实施例的硅磷反应型阻燃剂预聚体的制备方法包括:
32.步骤201:将第一二元胺与磷系反应阻燃剂混合,得到磷系反应型阻燃剂预聚体。
33.示例性的,本发明实施例将第一二元胺与磷系反应阻燃剂混合,形成磷系反应型阻燃剂预聚体盐溶液,反应温度为10℃~100℃,该盐溶液的质量浓度为10%~90%。
34.步骤202:将第一二元酸与硅系反应阻燃剂混合,得到硅系反应型阻燃剂预聚体。
35.示例性的,本发明实施例将第一二元酸与硅系反应阻燃剂混合,得到硅系反应型阻燃剂预聚体,形成硅系反应型阻燃剂预聚体盐溶液,反应温度为10℃~100℃,该盐溶液的质量浓度为10%~90%。
36.步骤203:将所述磷系反应阻燃剂预聚体和所述硅系反应阻燃剂预聚体混合反应,得到硅磷反应型阻燃剂预聚体。
37.示例性的,本发明实施例向磷系反应阻燃剂预聚体盐溶液中加入硅系反应阻燃剂预聚体盐溶液,形成混合盐溶液,然后继续反应3小时,得到硅磷反应型阻燃剂预聚体。
38.在一种可选方式中,本发明实施例的聚酰胺膜的制备方法,在利用聚酰胺盐和硅磷反应型阻燃剂预聚体制备聚酰胺膜前,该方法还包括:利用第二二元胺和第二二元酸制备聚酰胺盐。例如:将第二二元胺和第二二元酸加入去离子水中成盐,聚酰胺盐的质量浓度为50%。
39.在一种示例中,本发明实施例的第二二元胺和所述第二二元酸的摩尔比为1:(1~1.5)。在该摩尔比范围内,可以使得第二二元胺和第二二元酸形成聚酰胺盐时,反应的更完全,减少了原料的残留,使得在后续反应中的反应体系更干净。
40.在一种可选方式中,本发明实施例的硅系反应型阻燃剂、磷系反应型阻燃剂、第一二元胺以及第一二元酸的摩尔比为(10~25):(10~25):(10~25):(10~25),所述聚酰胺盐和所述硅磷反应型阻燃剂预聚体的质量比为100:(4~10)。其中,当硅系反应型阻燃剂、磷系反应型阻燃剂、第一二元胺以及第一二元酸的摩尔比为(10~25):(10~25):(10~25):(10~25)时,可以使得磷系反应型阻燃剂和硅系反应型阻燃剂均匀的分布在二元胺以及二元酸分子链端部,避免了硅系反应阻燃剂高温聚合过程中产生副产物环戊酮,从而使得聚酰胺不易变黄和发灰。通过磷系反应型阻燃剂和硅系阻燃剂的复配以及配方优化,使硅磷协同得到最大利用。另外,当聚酰胺盐和所述硅磷反应型阻燃剂预聚体的质量比为100:
41.(4~10)范围内时,通过使用少量的硅磷反应型阻燃剂预聚体,就可以使得聚酰胺盐与硅磷反应型阻燃剂预聚体完全发生反应,而且在该范围下,不仅可以使得聚酰胺不易变黄和发灰,还节约了硅磷反应型阻燃剂的使用量。同时,由于硅磷反应型阻燃剂与聚酰胺的分子链接枝,可以省略阻燃剂与聚酰胺的固相增粘等工艺步骤,简化了工艺步骤,节约了成本。
42.在一种示例中,本发明实施例的聚酰胺膜的材料还可以包括成核剂、消光剂、增塑剂、抗静电剂、耐热稳定剂、耐候剂、抗水解稳定剂、染料、阻燃剂、催化剂、消泡剂、偶联剂、增强剂、增韧剂、颜料、光泽增强剂、封端剂和抗uv剂中的至少一种。
43.在实际应用中,本发明实施例的磷系反应型阻燃剂包括磷酸酯类反应型阻燃剂、有机磷盐类反应型阻燃剂,磷杂环类反应型阻燃剂及聚合物磷酸酯类反应型阻燃剂中的至少一种,硅系反应型阻燃剂包括硅树脂反应型阻燃剂、含氮硅氧烷和聚硅氧烷反应型阻燃剂中的至少一种。其中,硅系反应型阻燃剂可以为1,3-双(3-氨基丙基)-1,1,3,3-四甲基二硅氧烷(gapd)或其衍生物、聚硅氧烷(如聚二苯基二甲基硅氧烷)。gapd的化学结构式为:聚硅氧烷如聚二甲基硅氧烷、聚二苯基二甲基硅氧烷等。
44.磷系反应型阻燃剂可以为2-羧乙基苯基次膦酸(ceppa)或其衍生物、[(6-氧-(6h)-二苯并-(ce)(1,2)-氧磷杂己环-6-酮)甲基]-丁二酸(ddp)或其衍生物。例如:ceppa
的化学结构式为:ddp的化学结构式为:
[0045]
示例性的,本发明实施例的聚酰胺盐包括单独单体均聚聚酰胺盐、单独双体均聚聚酰胺盐、共聚聚酰胺盐、共聚阻燃聚酰胺盐中的至少一种。例如:该聚酰胺盐中的聚酰胺包括聚酰胺6、聚酰胺66、聚酰胺46、聚酰胺56、聚酰胺10、聚酰胺12、聚酰胺610、聚酰胺612、共聚阻燃聚酰胺6、共聚阻燃聚酰胺66中的至少一种。
[0046]
本发明实施例通过在聚合前期引入硅系反应型阻燃剂,通过与磷系反应型阻燃剂和二胺进行复配得到硅磷复合型反应阻燃剂。将硅磷复合型阻燃剂引入到聚酰胺聚合过程中,既达到了阻燃效果也达到了树脂的白度要求。通过添加硅磷反应型阻燃剂制备出了无析霜的共聚阻燃尼龙,减少了其他助剂的添加,并且通过硅磷协同保证了阻燃性的同时,使白度增加,扩展了共聚阻燃尼龙在产品中的应用。
[0047]
为了验证本发明实施例提供的聚酰胺膜的效果,本发明实施例采用实施例与对比例对比的方式进行证明。
[0048]
实施例一
[0049]
本发明实施例提供一种聚酰胺膜,组分包括硅系反应型阻燃剂gapd、磷系反应型阻燃剂ceppa、己二胺和己二酸。
[0050]
本发明实施例一提供的聚酰胺膜的制备方法包括如下步骤:
[0051]
第一步,制备聚酰胺盐:将1393.3g的己二胺与1107g的己二酸加入50℃的去离子水中成盐,得到聚酰胺盐溶液,聚酰胺盐溶液的质量浓度为50%。
[0052]
第二步,制备磷系反应型阻燃剂预聚体:取50g己二胺与50g磷系反应型阻燃剂ceppa加入90℃的去离子水中成盐,得到磷系反应型阻燃剂预聚体,磷系反应型阻燃剂预聚体的质量浓度为50%。
[0053]
第三步,制备硅磷反应型阻燃剂预聚体:取10g的己二酸与10g的硅系反应型阻燃剂gapd加入90℃的去离子水中成盐,得到硅系反应型阻燃剂预聚体,硅系反应型阻燃剂预聚体质量浓度为50%,之后加入100g第二步制备的磷系反应型阻燃剂预聚体,继续反应3h,得到硅磷反应型阻燃剂预聚体。
[0054]
第四步,制备聚酰胺膜:将2000g聚酰胺盐溶液加入高温高压反应釜,再加入120g硅磷反应型阻燃剂预聚体。经过三次正压和负压置换,使反应釜中含有0.04mpa的氮气,加热使温度达到230℃,压力达到2.5mpa。再经过40分钟降至大气压,同时升温至280℃,抽真空,保持温度在275℃,抽真空至-0.06mpa,保持5分钟。然后通氮气使釜内压力达到0.1mpa,出料、切粒,得到聚酰胺66切片,其相对粘度在1.8~2.7。粒料在120℃真空干燥12h备用。
[0055]
实施例二
[0056]
本发明实施例提供一种聚酰胺膜,组分包括硅系反应型阻燃剂gapd、磷系反应型阻燃剂ceppa、己二胺和己二酸。
[0057]
本发明实施例二提供的聚酰胺膜的制备方法包括如下步骤:
[0058]
第一步,制备聚酰胺盐:将1393.3g的己二胺与1107g的己二酸加入50℃的去离子水中成盐,得到聚酰胺盐溶液,聚酰胺盐溶液的质量浓度为50%。
[0059]
第二步,制备磷系反应型阻燃剂预聚体:取50g己二胺与50g磷系反应型阻燃剂ceppa加入90℃的去离子水中成盐,得到磷系反应型阻燃剂预聚体,磷系反应型阻燃剂预聚体的质量浓度为50%。
[0060]
第三步,制备硅磷反应型阻燃剂预聚体:取30g的己二酸与30g的硅系反应型阻燃剂gapd加入90℃的去离子水中成盐,得到硅系反应型阻燃剂预聚体,硅系反应型阻燃剂预聚体质量浓度为50%,之后加入100g第二步制备的磷系反应型阻燃剂预聚体,继续反应3h,得到硅磷反应型阻燃剂预聚体。
[0061]
第四步,制备聚酰胺膜:将2000g聚酰胺盐溶液加入高温高压反应釜,再加入160g硅磷反应型阻燃剂预聚体。经过三次正压和负压置换,使反应釜中含有0.04mpa的氮气,加热使温度达到230℃,压力达到2.5mpa。再经过40分钟降至大气压,同时升温至280℃,抽真空,保持温度在275℃,抽真空至-0.06mpa,保持5分钟。然后通氮气使釜内压力达到0.1mpa,出料、切粒,得到聚酰胺66切片,其相对粘度在1.8~2.7。粒料在120℃真空干燥12h备用。
[0062]
实施例三
[0063]
本发明实施例提供一种聚酰胺膜,组分包括硅系反应型阻燃剂gapd、磷系反应型阻燃剂ddp、己二胺和己二酸。
[0064]
本发明实施例三提供的聚酰胺膜的制备方法包括如下步骤:
[0065]
第一步,制备聚酰胺盐:将1393.3g的己二胺与1107g的己二酸加入50℃的去离子水中成盐,得到聚酰胺盐溶液,聚酰胺盐溶液的质量浓度为50%。
[0066]
第二步,制备磷系反应型阻燃剂预聚体:取50g己二胺与50g磷系反应型阻燃剂ddp加入90℃的去离子水中成盐,得到磷系反应型阻燃剂预聚体,磷系反应型阻燃剂预聚体的质量浓度为50%。
[0067]
第三步,制备硅磷反应型阻燃剂预聚体:取10g的己二酸与10g的硅系反应型阻燃剂gapd加入90℃的去离子水中成盐,得到硅系反应型阻燃剂预聚体,硅系反应型阻燃剂预聚体质量浓度为50%,之后加入100g第二步制备的磷系反应型阻燃剂预聚体,继续反应3h,得到硅磷反应型阻燃剂预聚体。
[0068]
第四步,制备聚酰胺膜:将2000g聚酰胺盐溶液加入高温高压反应釜,再加入200g硅磷反应型阻燃剂预聚体。经过三次正压和负压置换,使反应釜中含有0.04mpa的氮气,加热使温度达到230℃,压力达到2.5mpa。再经过40分钟降至大气压,同时升温至280℃,抽真空,保持温度在275℃,抽真空至-0.06mpa,保持5分钟。然后通氮气使釜内压力达到0.1mpa,出料、切粒,得到聚酰胺66切片,其相对粘度在1.8~2.7。粒料在120℃真空干燥12h备用。
[0069]
实施例四
[0070]
本发明实施例提供一种聚酰胺膜,组分包括硅系反应型阻燃剂1,3-双-(2-氨基乙基氨基甲基)四甲基二硅烷、磷系反应型阻燃剂ddp、己二胺和己二酸。
[0071]
本发明实施例四提供的聚酰胺膜的制备方法包括如下步骤:
[0072]
第一步,制备聚酰胺盐:将1393.3g的己二胺与1107g的己二酸加入50℃的去离子水中成盐,得到聚酰胺盐溶液,聚酰胺盐溶液的质量浓度为50%。
[0073]
第二步,制备磷系反应型阻燃剂预聚体:取50g己二胺与50g磷系反应型阻燃剂ddp加入90℃的去离子水中成盐,得到磷系反应型阻燃剂预聚体,磷系反应型阻燃剂预聚体的质量浓度为50%。
[0074]
第三步,制备硅磷反应型阻燃剂预聚体:取10g的己二酸与10g的硅系反应型阻燃剂1,3-双-(2-氨基乙基氨基甲基)四甲基二硅烷加入90℃的去离子水中成盐,得到硅系反应型阻燃剂预聚体,硅系反应型阻燃剂预聚体质量浓度为50%,之后加入100g第二步制备的磷系反应型阻燃剂预聚体,继续反应3h,得到硅磷反应型阻燃剂预聚体。
[0075]
第四步,制备聚酰胺膜:将4000g聚酰胺盐溶液加入高温高压反应釜,再加入160g硅磷反应型阻燃剂预聚体。经过三次正压和负压置换,使反应釜中含有0.04mpa的氮气,加热使温度达到230℃,压力达到2.5mpa。再经过40分钟降至大气压,同时升温至280℃,抽真空,保持温度在275℃,抽真空至-0.06mpa,保持5分钟。然后通氮气使釜内压力达到0.1mpa,出料、切粒,得到聚酰胺66切片,其相对粘度在1.8~2.7。粒料在120℃真空干燥12h备用。
[0076]
实施例五
[0077]
本发明实施例提供一种聚酰胺膜,组分包括硅系反应型阻燃剂1,3-双-(2-氨基乙基氨基甲基)四甲基二硅烷、磷系反应型阻燃剂ceppa、己二胺和己二酸。
[0078]
本发明实施例五一提供的聚酰胺膜的制备方法包括如下步骤:
[0079]
第一步,制备聚酰胺盐:将1393.3g的己二胺与1107g的己二酸加入50℃的去离子水中成盐,得到聚酰胺盐溶液,聚酰胺盐溶液的质量浓度为50%。
[0080]
第二步,制备磷系反应型阻燃剂预聚体:取50g己二胺与50g磷系反应型阻燃剂ceppa加入90℃的去离子水中成盐,得到磷系反应型阻燃剂预聚体,磷系反应型阻燃剂预聚体的质量浓度为50%。
[0081]
第三步,制备硅磷反应型阻燃剂预聚体:取10g的己二酸与10g的硅系反应型阻燃剂1,3-双-(2-氨基乙基氨基甲基)四甲基二硅烷加入90℃的去离子水中成盐,得到硅系反应型阻燃剂预聚体,硅系反应型阻燃剂预聚体质量浓度为50%,之后加入100g第二步制备的磷系反应型阻燃剂预聚体,继续反应3h,得到硅磷反应型阻燃剂预聚体。
[0082]
第四步,制备聚酰胺膜:将4000g聚酰胺盐溶液加入高温高压反应釜,再加入160g硅磷反应型阻燃剂预聚体。经过三次正压和负压置换,使反应釜中含有0.04mpa的氮气,加热使温度达到230℃,压力达到2.5mpa。再经过40分钟降至大气压,同时升温至280℃,抽真空,保持温度在275℃,抽真空至-0.06mpa,保持5分钟。然后通氮气使釜内压力达到0.1mpa,出料、切粒,得到聚酰胺66切片,其相对粘度在1.8~2.7。粒料在120℃真空干燥12h备用。
[0083]
对比例一
[0084]
本发明对比例提供一种聚酰胺膜,组分包括己二胺和己二酸。
[0085]
本发明对比例一提供的聚酰胺复合膜的制备方法包括如下步骤:
[0086]
第一步,制备聚酰胺盐溶液:将1393.3g的己二胺与1107g的己二酸加入50℃的去离子水中成盐,得到聚酰胺盐溶液,聚酰胺盐溶液的质量浓度为50%。
[0087]
第二步,制备聚酰胺膜:将2000g聚酰胺盐溶液加入高温高压反应釜,经过三次正压和负压置换,使反应釜中含有0.04mpa的氮气,加热使温度达到230℃,压力达到2.5mpa。再经过40分钟降至大气压,同时升温至280℃,抽真空,保持温度在275℃,抽真空至-0.06mpa,保持5分钟。然后通氮气使釜内压力达到0.1mpa,出料、切粒,得到聚酰胺66切片,其相对粘度在1.8~2.7。粒料在120℃真空干燥12h备用。
[0088]
对比例二
[0089]
本发明对比例提供一种聚酰胺膜,组分包括磷系反应型阻燃剂ceppa、己二胺和己
二酸。
[0090]
本发明对比例二提供的聚酰胺膜的制备方法包括如下步骤:
[0091]
第一步,制备聚酰胺盐溶液:将1393.3g的己二胺与1107g的己二酸加入50℃的去离子水中成盐,得到聚酰胺盐溶液,聚酰胺盐溶液的质量浓度为50%。
[0092]
第二步,制备磷系反应型阻燃剂预聚体:取50g己二胺与50g磷系反应型阻燃剂ceppa加入90℃的去离子水中成盐,得到磷系反应型阻燃剂预聚体,磷系反应型阻燃剂预聚体的质量浓度为50%。
[0093]
第三步,制备聚酰胺膜:将2000g聚酰胺盐溶液加入高温高压反应釜,再加入100g磷系反应型阻燃剂预聚体。经过三次正压和负压置换,使反应釜中含有0.04mpa的氮气,加热使温度达到230℃,压力达到2.5mpa。再经过40分钟降至大气压,同时升温至280℃,抽真空,保持温度在275℃,抽真空至-0.06mpa,保持5分钟。然后通氮气使釜内压力达到0.1mpa,出料、切粒,得到聚酰胺66切片,其相对粘度在1.8~2.7。粒料在120℃真空干燥12h备用。
[0094]
本发明对实施例与对比例制备的聚酰胺复合膜的极限氧指数、ul-94、黄色指数进行测试,测试方法如下:
[0095]
极限氧指数(loi)测试:参照astm d2863-2010《塑料用氧指数法测定燃烧行为》标准,采用极限氧指数测定仪在室温下进行测定,样条规格:80mm*10mm*4mm。
[0096]
ul-94测试垂直燃烧测试:参照din iec 60695-11-10-20《塑料燃烧性能实验方法水平法和垂直法》标准,采用cfz-5垂直燃烧测定仪在室温下进行测定。样条规格:125mm*3.2mm*3.2mm。
[0097]
黄色指数测试:
[0098]
参照dineniso11664-4标准。色泽以往用y值(黄色指数)表征,现则通常用l值(白度)、b值和a值表征,它们是由光电管中样品的三色(红、绿、蓝)差别所决定。从产品外观质量要求来说,切片的颜色应为天然本色,即b值为-3~0。b值为正表示产品偏黄色,同样a值为正表示偏红,为负则偏绿。l值(白度)越大的时候,白度越高。
[0099]
本发明对实施例与对比例中,实施例一至实施例五均制备的是含有硅磷反应型阻燃剂的聚酰胺膜,对比例一与本发明实施例相比不含有本发明实施例中的硅磷反应型阻燃剂,对比例二与本发明实施例相比不含有本发明实施例中的硅系反应型阻燃剂。实施例一与其余实施例相比加入的硅系阻燃剂含量低,本发明实施例与对比例的测试结果如下表:
[0100]
[0101][0102]
从上表可以看出,本发明实施例一至实施例五制备得到的聚酰胺膜,组分包括硅系反应型阻燃剂gapd、磷系反应型阻燃剂ceppa、己二胺和己二酸,对比例一制备得到的聚酰胺膜不含有本发明实施例中的硅磷反应型阻燃剂,仅含有聚酰胺,对比例二中仅有磷系反应型阻燃剂和聚酰胺。实施例一加入的硅系阻燃剂含量低于其余实施例,可见,本发明实施例二至实施例六的黄色指数中的l值明显大于对比例一和对比例二、实施例一,实施例二至实施例六的ul-94均为v-0,也就是说,对实施例二至实施例六的聚酰胺膜样品进行两次10秒的燃烧测试后,火焰可以在10秒内熄灭。因此,本发明实施例二至实施例六制备的聚酰胺膜可以提高聚酰胺膜的白度,还能提高聚酰胺膜的光学性能,从而提高聚酰胺膜的光稳定性。
[0103]
以上所述,仅为本发明的具体实施方式,显而易见的,在不脱离本发明的精神和范围的情况下,可对其进行各种修改和组合。相应地,本说明书和附图仅仅是所附权利要求所界定的本发明的示例性说明,且视为已覆盖本发明范围内的任意和所有修改、变化、组合或等同物。显然,本领域的技术人员可以对本发明进行各种改动和变型而不脱离本发明的精神和范围。这样,倘若本发明的这些修改和变型属于本发明权利要求及其等同技术的范围之内,则本发明的意图包括这些改动和变型在内。任何熟悉本技术领域的技术人员在本发明揭露的技术范围内,可轻易想到变化或替换,都应涵盖在本发明的保护范围之内。因此,本发明的保护范围应以所述权利要求的保护范围为准。