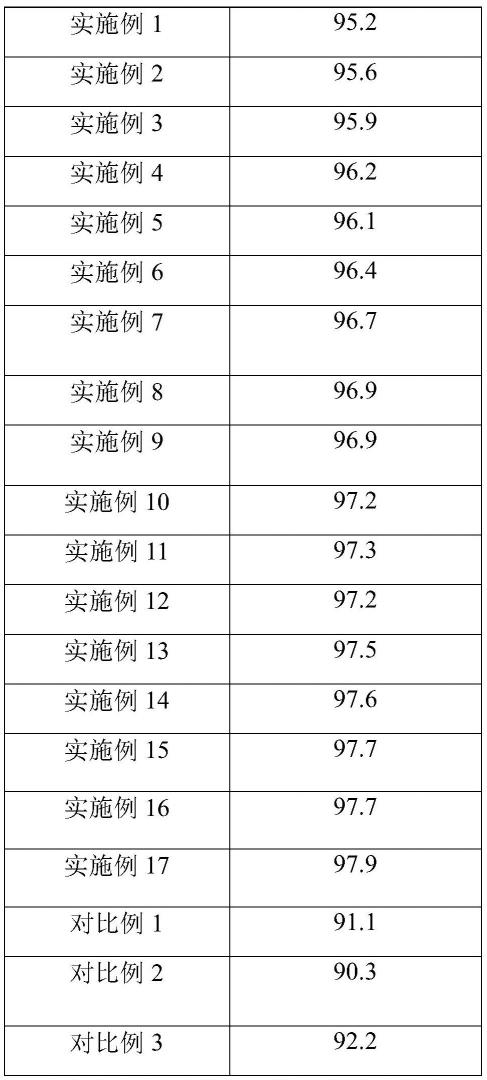
1.本发明涉及生物柴油回收的领域,特别涉及一种粗甘油中回收生物柴油工艺。
背景技术:2.近年来,生物柴油的生产是通过植物油或动物油与甲醇等小分子醇类在酸、碱或酶催化剂的作用下发生酯交换反应制得,生物柴油具有可再生、易生物降解、燃烧污染物排放低等特点,符合环保的理念,有利于实现社会的可持续发展;但是在生物柴油的制备过程中会产生大量的粗甘油副产物,在生产过程中每生产10kg生物柴油就产生1kg左右的粗甘油副产物;粗甘油副产物中含有大量的甘油,还含有少量的生物柴油、盐类和硬脂酸等,现有技术中通常采用萃取、减压蒸馏技术对粗甘油中的生物柴油进行回收提纯,提高整个生物柴油制备工艺的综合利用率和经济性。
3.上述相关技术中,发明人认为:现有技术中对粗甘油中提纯的生物柴油的纯度有待提高。
技术实现要素:4.为了提高粗甘油中提纯的生物柴油的纯度,本技术提供一种粗甘油中回收生物柴油工艺。
5.第一方面,本技术提供的一种粗甘油中回收生物柴油工艺,采用如下的技术方案:一种粗甘油中回收生物柴油工艺,主要包括如下步骤:s1:将粗甘油加热至110-130℃,减压脱水1-2h,冷却,加入甲醇和氢氧化钾,加热至60-70℃,回流反应1-2h,冷却、静置,得到上下分层的处理液,除去下层,得到粗生物柴油;所用甲醇与氢氧化钾的质量比为(1-2):(4-6);所用氢氧化钾与粗甘油的质量比为(2-3):(30-45);s2:将步骤s1中制得的粗生物柴油与水进行混合,搅拌,静置分层,除去下层,得到预精制生物柴油;s3:在步骤s2中制得的预精制生物柴油中添加絮凝剂,搅拌混合、过滤,即得;所述絮凝剂与预精制生物柴油的质量比为(3-5):(45-60);所述絮凝剂由硅酸钠、硫酸、硫酸铝和氯化铁按照摩尔比(7-10):(0.5-1.5):(1-3):(1-2)组成。
6.通过采用上述技术方案,先通过甲醇和氢氧化钾共同对粗甘油进行提取,并配合加热萃取、回收冷凝工艺,使得粗甘油中的甘油与生物柴油互相分离出来,并通过静置分层,使得甘油位于下层,对下层的甘油进行分离,除去粗甘油中的大部分甘油,得到粗生物柴油;然后通过水对粗生物柴油进行混合,使得水对甘油进行溶解提取,进一步提高制备的生物柴油的纯度;然后通过添加絮凝剂,由于硫酸铝形成的絮体较大,对预精制生物柴油内杂质的吸附效果较好,但是絮体易松散,沉降速率慢;氯化铁形成的絮体密实、沉降速率快,但是絮体小,卷扫作用差,通过将硅酸钠、硫酸、硫酸铝和氯化铁配合,利用硅酸钠、硫酸对硫酸铝和氯化铁的螯合和吸附,使得生成的絮凝剂克服硫酸铝和氯化铁的缺点,具备更好的絮凝效果和絮凝速率,使得预精制生物柴油中带电荷的杂质在絮凝剂的作用下产生电中
和而聚沉,利用过滤对絮凝剂和杂质进行去除后,使得制备的生物柴油的纯度较高。
7.可选的,所述絮凝剂的制备方法包括如下步骤:s11:将硅酸钠溶于水中制成硅酸钠溶液,将硫酸添加至硅酸钠溶液中,不断搅拌制备成混合液;s12:将硫酸铝和氯化铁添加至步骤s11中制得的混合液中,在35-45℃下搅拌熟化24h,即得。
8.通过采用上述技术方案,在硫酸的作用下,硅酸钠溶液进行聚合,生成混合液中包含聚硅酸钠溶液,同时硫酸铝水解生成氢氧化铝胶体,氯化铁水解生成氢氧化铁胶体,聚硅酸钠溶液对铝离子和铁离子起到螯合作用,使得氢氧化铝胶体和氢氧化铁胶体与聚硅酸钠稳定结合生成絮凝剂;絮凝剂添加至预精制生物柴油中可以提供大量的络合离子,胶体微粒吸附带电荷的杂质后,这些络合离子可以强烈吸附胶体微粒,起到桥架、交联的作用,中和凝聚后的胶体微粒的表面电荷,降低电位,使得胶体微粒由相斥转变为相吸,从而快速生成絮状的胶体微粒,方便后续进行过滤去除,提高制备的生物柴油的纯度。
9.可选的,步骤s3中在对所述预精制生物柴油中添加絮凝剂,搅拌过滤后,还在预精制生物柴油中添加氢氧化钠,过滤即得;所述氢氧化钠与预精制生物柴油的质量比为(1-3):(9-11)。
10.通过采用上述技术方案,预精制生物柴油经过絮凝剂处理后,预精制生物柴油中还可能残留有氯化铁,通过添加氢氧化钠,将多余的氯化铁转变为氢氧化铁沉淀,同时还可对预精制生物柴油中残留的脂肪酸进行皂化处理,将脂肪酸以皂的形式固定下来并被过滤除去,减少脂肪酸对生物柴油纯度的影响。
11.可选的,步骤s3中将所述氢氧化钠添加至预精制生物柴油中,搅拌混合过滤后,还在预精制生物柴油中添加了活性炭。
12.通过采用上述技术方案,活性炭本身具备多孔结构,可以与预精制生物柴油进行大面积的接触,同时活性炭具有良好的吸附作用,可以对过滤残留的细小的杂质进行吸附,进一步提高生物柴油的纯度。
13.可选的,所述活性炭添加至预精制生物柴油中时,先将活性炭分为两份,先添加一份,搅拌静置3-5min后,再添加剩下的另一半活性炭,搅拌静置,过滤即得。
14.通过采用上述技术方案,将活性炭分批添加,因为活性炭一次加入只建立一次平衡,将活性炭分批添加,第二批添加的活性炭会发挥新的吸附作用,与第一次添加的活性炭建立平衡后剩余的色素和杂质建立起新的平衡,从而达到更好的吸附效果,提高制备的生物柴油的纯度。
15.可选的,所述活性炭与预精制生物柴油的质量比为(2-5):(50-60)。
16.通过采用上述技术方案,调节活性炭与预精制生物柴油的质量比,当活性炭用量较少时,对预精制生物柴油中杂质的吸附效果不足,制备的生物柴油的纯度较低,但是当活性炭用量过多时,由于活性炭在杂质的吸附过程中对生物柴油也具有一定的吸附效果,过多的活性炭使用易使得生物柴油的回收率降低;因此调节活性炭的用量,在活性炭对预精制生物柴油具有良好的除杂效果的前提下,减少活性炭对生物柴油的吸附,提高生物柴油的纯度和收率。
17.可选的,步骤s2中得到预精制生物柴油后,在将絮凝剂添加至预精制生物柴油中
前,还对预精制生物柴油进行减压蒸馏,减压蒸馏的温度为160-210℃。
18.通过采用上述技术方案,调节减压蒸馏的温度,因为随着温度的升高,使得预精制生物柴油中残留的甘油进行气化,与生物柴油分离;但是当温度继续增加时,甘油在高温下发生聚合和分解,使得甘油溶于预精制生物柴油中,使得预精制生物柴油中杂质的含量增加;因此通过控制减压蒸馏的温度,使得甘油可以有效气化回收,提高后续制备的生物柴油的纯度。
19.可选的,所述活性炭的制备方法包括如下步骤:1)取甘蔗渣与粘合剂进行混合,制粒后,放置在n2环境中热解0.5-1.5h,热解温度为200-400℃,制得预处理料;所述甘蔗渣与粘合剂的质量比为(3-5):(1-2);2)将步骤1)中制得的预处理料放入活化箱内,在活化箱内通入水蒸气,加热活化10-14h,冷却后取出,烘干即得。
20.通过采用上述技术方案,甘蔗渣是一种天然原料,主要化学组成为纤维素、半纤维素和木质素,本身的吸附性能不强,将甘蔗渣与粘合剂混合并胶粘制粒后,在n2环境下热解,使得甘蔗渣发生脱水、脱酸,随着温度的不断提高,甘蔗渣中糖苷键断裂,生成酮、醇互变的中间产物,再进一步分解出水、二氧化碳和一氧化碳,使得分解残渣固体生成物进行芳香族化,然后再发生脱氢反应,最终形成聚合芳香族平面状分交联结构,使得甘蔗渣的纤维结构转变为具有发达的微细孔构造和巨大比表面积的活性碳微晶结构,制备的活性炭具有较大的孔隙和比表面积,使得活性炭具备良好的吸附性能;同时由于粘合剂在热解过程会析出,对活性碳微晶结构进行占据,通过活化作用,活性碳微晶结构中粘合剂被除去,开放了原本闭塞的孔隙,同时活性碳微晶结构继续发生烧失,使得新的孔隙生成,同时原有的孔隙加宽,进一步提高制备的活性炭的比表面积和吸附性能,使得后续制备的生物柴油的纯度提高。
21.可选的,所述设置活化箱内的活化温度为700-900℃。
22.通过采用上述技术方案,设置活化温度,当活化温度较低时,对甘蔗渣的活化效果不足,影响制备的活性炭的吸附性能,当活化温度较高时,会使得活性炭表面发生烧失,降低了活性炭的成品收率。
23.综上所述,本技术具有以下有益效果:通过在粗甘油中添加甲醇和氢氧化钾,配合加热回收冷凝的工艺,使得大部分甘油从粗甘油中分离出来,得到粗生物柴油,然后通过将硅酸钠、硫酸、硫酸铝和氯化铁复配制备成絮凝剂,在硫酸的作用下将硅酸钠进行聚合生成聚硅酸钠,并通过聚硅酸钠对硫酸铝和氯化铁进行络合,使得生成的絮凝剂具备较好的絮凝效果,同时沉降速率较快,对预精制生物柴油中的杂质进行中和聚沉,使得制备的生物柴油的纯度更高。
具体实施方式
24.以下结合实施例和对比例对本技术作进一步详细说明;本技术实施例及对比例的原料除特殊说明以外均为普通市售。
25.制备例活性炭制备例1本制备例中活性炭的制备方法包括如下步骤:
1)取甘蔗渣与粘合剂放入混合桶内进行混合,搅拌均匀后,放入制粒机内压制成粒,制备成混合粒,然后将混合粒放置在加热炉中,在加热炉中通入n2,设置加热炉内的温度为300℃,热解1h,制得预处理料;所用甘蔗渣与粘合剂的质量比为3:2;所用粘合剂为煤焦油;2)将步骤1)中制得的预处理料放入活化箱内,在活化箱内通入水蒸气,活化10h,冷却后取出,烘干即得,活化温度设置为700℃。
26.活性炭制备例2本制备例中活性炭的制备方法包括如下步骤:1)取甘蔗渣与粘合剂放入混合桶内进行混合,搅拌均匀后,放入制粒机内压制成粒,制备成混合粒,然后将混合粒放置在加热炉中,在加热炉中通入n2,设置加热炉内的温度为300℃,热解1h,制得预处理料;所用甘蔗渣与粘合剂的质量比为5:1;所用粘合剂为煤焦油;2)将步骤1)中制得的预处理料放入活化箱内,在活化箱内通入水蒸气,活化14h,冷却后取出,烘干即得,活化温度设置为700℃。
27.活性炭制备例3本制备例中活性炭的制备方法包括如下步骤:1)取甘蔗渣与粘合剂放入混合桶内进行混合,搅拌均匀后,放入制粒机内压制成粒,制备成混合粒,然后将混合粒放置在加热炉中,在加热炉中通入n2,设置加热炉内的温度为300℃,热解1h,制得预处理料;所用甘蔗渣与粘合剂的质量比为4:1.5;所用粘合剂为煤焦油;2)将步骤1)中制得的预处理料放入活化箱内,在活化箱内通入水蒸气,活化12h,冷却后取出,烘干即得,活化温度设置为700℃。
28.活性炭制备例4本制备例中活性炭的制备方法与活性炭制备例3中的不同之处在于,步骤2)中的活化温度为900℃。
29.活性炭制备例5本制备例中活性炭的制备方法与活性炭制备例3中的不同之处在于,步骤2)中的活化温度为800℃。
30.絮凝剂制备例1本制备例中絮凝剂的制备方法包括如下步骤:s11:取反应瓶,将硅酸钠和水共同放入反应瓶中,搅拌至硅酸钠完全溶解,制成硅酸钠溶液,将硫酸溶液缓慢添加至硅酸钠溶液中,不断搅拌制备成混合液;所用硅酸钠与水的质量比为1:1;s12:将硫酸铝和氯化铁添加至步骤s11中制得的混合液中,在40℃搅拌、熟化24h,即得;所用硅酸钠、硫酸、硫酸铝和氯化铁的摩尔比为7:0.5:1:1;所用硫酸溶液中硫酸的质量浓度为75%。
31.絮凝剂制备例2本制备例中絮凝剂的制备方法与絮凝剂制备例1中的不同之处在于,所用絮凝剂中所用硅酸钠、硫酸、硫酸铝和氯化铁的摩尔比为10:1.5:3:2。
32.絮凝剂制备例3本制备例中絮凝剂的制备方法与絮凝剂制备例1中的不同之处在于,所用絮凝剂中所用硅酸钠、硫酸、硫酸铝和氯化铁的摩尔比为8:1:2:1.5。实施例
33.实施例1本实施例中的粗甘油中回收生物柴油工艺包括如下步骤:s1:将粗甘油放入反应瓶中加热至120℃,减压脱水1.5h,冷却,加入甲醇和氢氧化钾,加热至65℃,回流反应1.5h,冷却、静置,得到上下分层的处理液,除去下层,得到粗生物柴油;所用甲醇与氢氧化钾的质量比为1.5:5;所用氢氧化钾与粗甘油的质量比为2.5:40;s2:在步骤s1中制得的粗生物柴油中添加水,搅拌混合,静置分层,除去下层,得到预精制生物柴油;所用水与粗生物柴油的质量比为1:1;s3:在步骤s2中制得的预精制生物柴油中添加絮凝剂,搅拌混合、静置3min,过滤即得;所用絮凝剂与预精制生物柴油的质量比为4:55;所述絮凝剂由絮凝剂制备例1中制备而成。
34.实施例2本实施例中的粗甘油中回收生物柴油工艺与实施例1中的不同之处在于,步骤s3中所用絮凝剂由絮凝剂制备例2中制备而成。
35.实施例3本实施例中的粗甘油中回收生物柴油工艺与实施例1中的不同之处在于,步骤s3中所用絮凝剂由絮凝剂制备例3中制备而成。
36.实施例4本实施例中的粗甘油中回收生物柴油工艺包括如下步骤:s1:将粗甘油放入反应瓶中加热至120℃,减压脱水1.5h,冷却,加入甲醇和氢氧化钾,加热至65℃,回流反应1.5h,冷却、静置,得到上下分层的处理液,除去下层,得到粗生物柴油;所用甲醇与氢氧化钾的质量比为1.5:5;所用氢氧化钾与粗甘油的质量比为2.5:40;s2:在步骤s1中制得的粗生物柴油中添加水,搅拌混合,静置分层,除去下层,得到预精制生物柴油;所用水与粗生物柴油的质量比为1:1;s3:在步骤s2中制得的预精制生物柴油中添加絮凝剂,搅拌混合、静置3min,过滤后,又在预精制生物柴油中添加了氢氧化钠,搅拌混合,静置2min过滤即得;所用絮凝剂与预精制生物柴油的质量比为4:55;所述絮凝剂由絮凝剂制备例3中制备而成;所用氢氧化钠与预精制生物柴油的质量比为1:50。
37.实施例5本实施例中的粗甘油中回收生物柴油工艺与实施例4中的不同之处在于,所用氢氧化钠与预精制生物柴油的质量比为3:35。
38.实施例6本实施例中的粗甘油中回收生物柴油工艺与实施例4中的不同之处在于,所用氢氧化钠与预精制生物柴油的质量比为2:45。
39.实施例7本实施例中的粗甘油中回收生物柴油工艺与实施例6中的不同之处在于,步骤s3
中将氢氧化钠添加至预精制生物柴油中,搅拌混合,过滤后,然后又在预精制生物柴油中添加了活性炭,搅拌,静置4min过滤;所用活性炭与预精制生物柴油的质量比为2:60;所用活性炭由活性炭制备例1中制备而成。
40.实施例8本实施例中的粗甘油中回收生物柴油工艺与实施例7中的不同之处在于,步骤s3中所用活性炭与预精制生物柴油的质量比为5:50。
41.实施例9本实施例中的粗甘油中回收生物柴油工艺与实施例7中的不同之处在于,步骤s3中所用活性炭与预精制生物柴油的质量比为4:55。
42.实施例10本实施例中的粗甘油中回收生物柴油工艺与实施例9中的不同之处在于,步骤s3中将活性炭添加至预精制生物柴油中前,先将活性炭按照质量均分为两份,先将其中一份活性炭添加至预精制生物柴油内,搅拌混合静置4min后,再添加另一份活性炭,搅拌均匀静置4min,过滤,即得。
43.实施例11本实施例中的粗甘油中回收生物柴油工艺与实施例10中的不同之处在于,步骤s3中将絮凝剂添加至预精制生物柴油中前,先对预精制生物柴油进行减压蒸馏,减压蒸馏的温度为160℃。
44.实施例12本实施例中的粗甘油中回收生物柴油工艺与实施例11中的不同之处在于,对预精制生物柴油的减压蒸馏的温度为210℃。
45.实施例13本实施例中的粗甘油中回收生物柴油工艺与实施例11中的不同之处在于,对预精制生物柴油的减压蒸馏的温度为190℃。
46.实施例14本实施例中的粗甘油中回收生物柴油工艺与实施例13中的不同之处在于,所用活性炭由活性炭制备例2中制备而成。
47.实施例15本实施例中的粗甘油中回收生物柴油工艺与实施例13中的不同之处在于,所用活性炭由活性炭制备例3中制备而成。
48.实施例16本实施例中的粗甘油中回收生物柴油工艺与实施例13中的不同之处在于,所用活性炭由活性炭制备例4中制备而成。
49.实施例17本实施例中的粗甘油中回收生物柴油工艺与实施例13中的不同之处在于,所用活性炭由活性炭制备例5中制备而成。
50.对比例对比例1本实施例中的粗甘油中回收生物柴油工艺与实施例1中的不同之处在于,步骤s3
中所用絮凝剂为硫酸铝。
51.对比例2本实施例中的粗甘油中回收生物柴油工艺与实施例1中的不同之处在于,步骤s3中所用絮凝剂为氯化铁。
52.对比例3本实施例中的粗甘油中回收生物柴油工艺与实施例1中的不同之处在于,步骤s3中所用絮凝剂为硫酸铝和氯化铁按照质量比2:1.5组成。
53.检测方法取同一厂家生产的粗甘油,将其分成质量相等的20份,作为实验样品,然后按照实施例1-17和对比例1-3中的粗甘油中回收生物柴油工艺对生物柴油进行回收,得到的产品为生物柴油,通过生物柴油中脂肪酸甲酯含量测定仪对制备的生物柴油中脂肪酸甲酯的含量进行测量,记录数据到表1;表1实施例1-17与对比例1-3制备的生物柴油中脂肪酸甲酯的含量
结合实施例1-3、对比例1-3和表1可以看出,将硅酸钠、硫酸、硫酸铝和氯化铁按照质量比8:1:2:1.5复配,制备成絮凝剂,通过硫酸与硅酸钠的混合制备成聚硅酸钠,通过聚硅酸钠与硫酸铝和氯化铁中铝离子和铁离子的络合作用,对预精制生物柴油中的杂质进行沉降去除,相比较对比例1-3,本技术复配制成的絮凝剂具有絮体大,絮体密实,沉降速率快,沉降效果好的特点;使得制备的生物柴油的脂肪酸甲酯的含量更高,相应的纯度也更高;结合实施例4-13和表1可以看出,通过在预精制生物柴油中添加氢氧化钠和活性炭,氢氧化钠将预精制生物柴油中多余的氯化铁转变为氢氧化铁沉淀,同时还将脂肪酸以皂的形式固定,避免脂肪酸影响生物柴油的纯度;并通过添加活性炭,对过滤后的预精制生物柴油中残留的杂质和脂肪酸进行吸附,并通过限定活性炭分两次添加,使得活性炭对过
滤后预精制生物柴油中杂质的吸附效果更好,提高制备的生物柴油的纯度,同时调节对预精制生物柴油减压蒸馏的温度,使得甘油气化除去,也避免甘油的分解,进一步提高生物柴油的纯度;结合实施例14-17和表1可以看出,利用甘蔗渣制备活性炭,先通过热解使得甘蔗渣脱水、脱酸,生成具有微孔和巨大比表面积的活性碳微晶结构,并通过将活性碳微晶结构在800℃下进行活化,进一步开放原本闭塞的孔隙,生成新的孔隙并使得原有的孔隙,进一步提高活性炭的吸附性能,进而提高制备的生物柴油的纯度。
54.本具体实施例仅仅是对本技术的解释,其并不是对本技术的限制,本领域技术人员在阅读完本说明书后可以根据需要对本实施例做出没有创造性贡献的修改,但只要在本技术的权利要求范围内都受到专利法的保护。