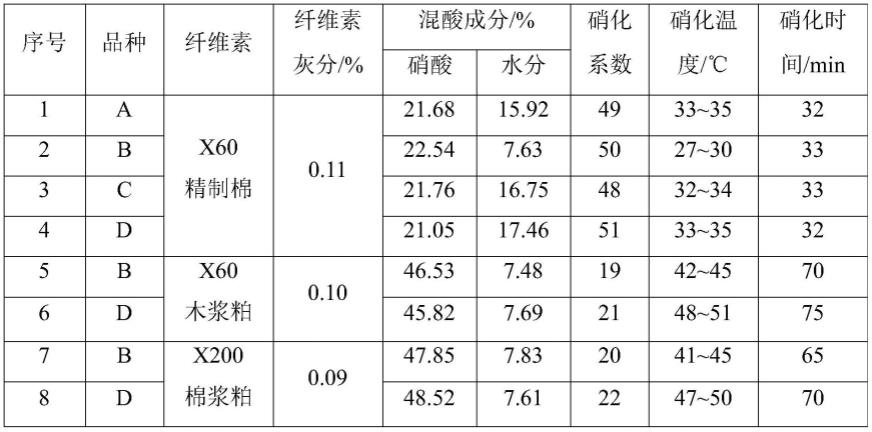
1.本发明属于硝化棉生产技术领域,具体涉及一种高纯净度硝化棉制备方法。
背景技术:2.硝化纤维素(又叫硝化棉,英文nitrocellulose,缩写nc)是单基药、双基药、三基药、改性双基、交联改性双基及复合改性双基推进剂的主要成分。其中,单基发射药中硝化棉含量一般在94~97%,(改性)双基发射药中硝化棉的含量一般在50%以上。
3.硝化棉是纤维素中的羟基被硝酸酯基取代得到产物,现有技术生产过程主要包括纤维素预处理、硝化、驱酸、煮洗、细断、精洗等过程。纤维素预处理后,与硝化混酸(硝酸、硫酸、水混合物,不同组分混酸的酯化能力不同,目前,硝化棉主要分为a、b、c、d棉,而a、b、c、d棉区分的主要依据就是以硝化棉的含氮量的不同进行区间进行分类,控制硝化棉含氮量的主要由参与反应的混酸组分和酯化条件决定)在反应釜内完成酯化反应,酯化反应过程的主要工艺条件有硝化系数(参与反应的混酸与纤维素干量的质量比)、反应温度和反应时间。
4.酯化反应过程,混酸中的硝酸降低、水分升高,反应后的酸棉混合物在离心机内完成驱酸和置换洗涤,驱除的废酸回用于配酸机,再补加原料硝酸和硫酸后配制为硝化混酸使用;硝化棉驱酸后物料吸附的残酸量数量(一般以残酸度表示)仍然较大,为降低硝化棉吸附残酸,还须进行置换洗涤。
5.驱酸洗涤后物料在煮洗釜内进行安定处理和调整粘度。现有技术中,煮洗过程首先在一定酸度、温度、时间下进行酸煮,再在一定碱度、温度、时间下进行碱煮。碱煮完毕,物料再经过细断、精洗、脱水过程获得含能硝化棉产品。为确保含能硝化棉的安定性,细断和精洗过程还须加入一定数量的碳酸钠和碳酸钙,其碳酸钠、碳酸钙加入数量约为硝化棉绝干量的2
‰
~3
‰
。
6.硝化棉的纯净度直接影响后续发射药的纯净度。衡量硝化棉纯净度的主要技术指标为灰分和丙酮不溶物,其中,灰分指标是是将硝化棉硝解炭化后,测试其灼烧残渣,灼烧后残渣组分主要为盐分杂质;而丙酮不溶物则是表示产品中含氮量低于10.5%的占比。就目前国内硝化棉的纯净度技术水平看,其灰分一般为0.2%左右,丙酮不溶物一般为0.25%左右。
技术实现要素:7.本发明要解决的是现有技术生产的硝化棉纯净度偏低的技术问题。
8.为解决上述技术问题,本发明提供了一种高纯净度硝化棉制备方法,包括以下步骤:
9.a、硝化反应:将纤维素原料与混酸混合进行硝化反应,得硝化棉粗品;所述纤维素原料为精制棉纤维素或浆粕纤维素;所述纤维素原料的灰分含量不超过0.15wt%;所述混酸中的硝化棉纤维含量不超过0.3wt%;
10.其中,当以精制棉纤维素为原料时,控制所述混酸中硝酸含量为21wt%~23wt%;控制硝化系数为40~60;控制硝化反应的时间为30~35min;目标产物为b棉的反应温度为27~30℃;目标产物为a、c或d棉的反应温度为32~35℃;
11.当以浆粕纤维素为原料时,控制所述混酸中硝酸含量为45.5wt%~49wt%;控制硝化系数为18~25;硝化反应的时间为60~80min;目标产物为b棉的反应温度为40~45℃;目标产物为a、c或d棉的反应温度为47~52℃;
12.b、驱酸洗涤:将步骤a所得粗品进行驱酸洗涤,控制驱酸洗涤后物料的残酸度低于20%;
13.c、煮洗:酸煮:对驱酸洗涤后物料进行酸煮,控制煮洗水初始酸度:2~6g/l,目标产物为b棉的酸煮时间不低于6h,目标产物为a、c或d棉的酸煮时间不低于4h;
14.水煮:对酸煮后物料进行水煮,控制煮洗水初始ph为中性,目标产物为b棉的水煮时间不低于6h,目标产物为a、c或d棉的水煮时间不低于4h;
15.浸泡热洗:将水煮后物料使用0.2~0.5g/l的碳酸钠水溶液进行浸泡热洗,热洗温度50~70℃;
16.d、细断、精洗:细断过程加入硝化棉干量0.5~1.0
‰
的碳酸钠,精洗过程加入硝化棉干量0~1.0
‰
的碳酸钠;
17.e、精洗后,脱水,即得高纯净度硝化棉。
18.优选的,上述高纯净度硝化棉制备方法,步骤a中,所述纤维素原料的灰分含量不超过0.12wt%。
19.优选的,上述高纯净度硝化棉制备方法,步骤a中,所述混酸中的硝化棉纤维含量不超过0.2wt%。
20.优选的,上述高纯净度硝化棉制备方法,步骤a中,当以精制棉纤维素为原料时,控制硝化系数为48~52;控制硝化反应的时间为32~33min。
21.优选的,上述高纯净度硝化棉制备方法,步骤a中,当以浆粕纤维素为原料时,控制硝化系数为19~22;硝化反应的时间为65~75min。
22.优选的,上述高纯净度硝化棉制备方法,步骤b中,控制驱酸洗涤后物料的残酸度低于15%。
23.优选的,上述高纯净度硝化棉制备方法,步骤c中,酸煮时,控制煮洗水初始酸度:3~6g/l。
24.其中,上述高纯净度硝化棉制备方法,步骤c中,酸煮时,控制酸煮温度<120℃。
25.其中,上述高纯净度硝化棉制备方法,步骤c中,酸煮后洗涤时间以洗涤后物料ph为中性为准。
26.其中,上述高纯净度硝化棉制备方法,步骤c中,水煮时,控制水煮温度<120℃。
27.其中,上述高纯净度硝化棉制备方法,步骤c中,水煮后洗涤时间以洗涤后物料ph为中性为准。
28.其中,上述高纯净度硝化棉制备方法,步骤c中,浸泡热洗时,控制热洗时间1~2h。
29.其中,上述高纯净度硝化棉制备方法,步骤d中,细断和精洗过程不加入碳酸钙。
30.其中,上述高纯净度硝化棉制备方法中,所述高纯净度硝化棉的丙酮不溶物和灰分含量均不超过于0.1wt%。
31.本发明中,所述硝化系数是指硝化过程中,纤维素原料干量与混酸的质量比。
32.本发明中,所述残酸度是指驱酸洗涤后物料夹带残酸(以硫酸计)占硝化棉干重的质量比。
33.本发明的有益效果:
34.本发明深入研究了硝化棉生产中影响硝化棉纯净度的相关因素,对硝化棉生产过程中原材料的品质进行把控,结合优化硝化、驱酸、煮洗、细断、精洗等步骤,可获得丙酮不溶物和灰分含量均低于0.1%的高纯净度硝化棉,大幅度的提高了硝化棉的纯净度,提升了硝化棉的品质。
附图说明
35.图1为本发明的工艺流程图。
具体实施方式
36.具体的,高纯净度硝化棉制备方法,包括以下步骤:
37.a、硝化反应:将纤维素原料与混酸混合进行硝化反应,得硝化棉粗品;所述纤维素原料为精制棉纤维素或浆粕纤维素;所述纤维素原料的灰分含量不超过0.15wt%;所述混酸中的硝化棉纤维含量不超过0.3wt%;
38.其中,当以精制棉纤维素为原料时,控制所述混酸中硝酸含量为21wt%~23wt%;控制硝化系数为40~60;控制硝化反应的时间为30~35min;目标产物为b棉的反应温度为27~30℃;目标产物为a、c或d棉的反应温度为32~35℃;
39.当以浆粕纤维素为原料时,控制所述混酸中硝酸含量为45.5wt%~49wt%;控制硝化系数为18~25;硝化反应的时间为60~80min;目标产物为b棉的反应温度为40~45℃;目标产物为a、c或d棉的反应温度为47~52℃;
40.b、驱酸洗涤:将步骤a所得粗品进行驱酸洗涤,控制驱酸洗涤后物料的残酸度低于20%;
41.c、煮洗:酸煮:对驱酸洗涤后物料进行酸煮,控制煮洗水初始酸度:2~6g/l,目标产物为b棉的酸煮时间不低于6h,目标产物为a、c或d棉的酸煮时间不低于4h;
42.水煮:对酸煮后物料进行水煮,控制煮洗水初始ph为中性,目标产物为b棉的水煮时间不低于6h,目标产物为a、c或d棉的水煮时间不低于4h;
43.浸泡热洗:将水煮后物料使用0.2~0.5g/l的碳酸钠水溶液进行浸泡热洗,热洗温度50~70℃;
44.d、细断、精洗:细断过程加入硝化棉干量0.5~1.0
‰
的碳酸钠,精洗过程加入硝化棉干量0~1.0
‰
的碳酸钠;
45.e、精洗后,脱水,即得高纯净度硝化棉。
46.硝化棉生产中,原材料的灰分含量,煮洗、细断、精洗加入的无机盐数量均会影响硝化棉的灰分含量;生产过程中,硝化、驱酸、煮洗等过程都会影响硝化棉的丙酮不溶物含量。因此本发明对硝化棉生产过程中原材料的品质,硝化、驱酸、煮洗、细断、精洗等步骤进行优化,综合调整各因素,以期获得高纯净度硝化棉。
47.本领域中,生产硝化棉的纤维素原料一般为精制棉纤维素或浆粕纤维素,其需要
先预处理再进行硝化反应。以精制棉纤维素为原料时,一般采用梳解机或抓花机将打包精制棉疏解为蓬松的絮状精制棉,以浆粕纤维素为原料时,一般采用切片机将浆粕卷剪切为一定规格的颗粒状浆粕。此外,精制棉纤维长、蓬松,因此需要较大的混酸用量才能确保精制棉被混酸浸润并保持流动性;而切片浆粕为颗粒状,因此只需要较小的混酸用量就能确保物料被混酸浸润并保持流动性。
48.纤维素原料的灰分含量直接影响硝化棉的灰分含量,因此本发明对精制棉、浆粕原料的灰分进行控制。经试验,需要控制纤维素原料含量不超过0.15%,更优为不超过0.12%。
49.纤维素与混酸的硝化反应过程是决定硝化棉丙酮不溶物含量关键,其低丙酮不溶物含量的高纯净度硝化棉的主要硝化条件为:
50.(1)、硝化用混酸清洁度要求:硝化棉生产过程,其混酸配制均使用驱酸后废酸为母液酸,再补加原料硝酸、硫酸,配制成硝酸、硫酸和水的三元混合物,即为硝化用混酸。现有工艺中,并未注重混酸的清洁程度。然而本发明经过大量试验发现,由于驱酸过程,废酸中不可避免带入一些细小硝化棉,这部分硝化棉在酸中停留时间过长,存在脱硝、再硝化等不规则反应,带入产品内不仅产品质量,而且会很大程度影响产品的丙酮不溶物升高。本发明所采用的混酸可采用现有技术进行配置,但本发明为降低硝化棉产品中丙酮不溶物含量,需要控制选用的硝化用混酸中的硝化棉纤维含量不超过0.3%,优选为不超过0.2%。本发明可采用自然澄清或者过滤处理等实现对混酸的净化,从而才能制备得到高纯净度硝化棉。
51.(2)、主要硝化条件:工业生产中,硝化反应的操作一般为:一定数量的纤维素被一定数量的混酸浸润后一起进入反应器内,在反应过程控制一定的反应时间和反应温度。但现有技术中对硝化反应的条件控制较为粗放,难以满足高纯净度硝化棉生产要求,本发明则对硝化条件进行大量试验,以提高硝化棉纯净度。具体而言:
52.现有技术中,以精制棉为原料的反应混酸,一般按照硝酸含量18~25%控制,但该范围并非都能满足高纯净度硝化棉的反应要求,同时硝酸含量过高,过程挥发大,成本增加;现有技术中,b棉的反应温度一般为20~30℃,a、c、d棉的反应温度一般为30~40℃,该温度同样并非都能满足高纯净度硝化棉的反应要求。发明人通过大量试验确定,在满足高纯净度硝化棉的硝化质量的前提下,控制混酸中硝酸含量为21~23%,b棉反应温度为27~30℃,a、c、d棉反应温度为32~35℃。
53.硝化系数和硝化时间同样影响硝化棉纯净度,当以精制棉纤维素为原料时,经试验,需要控制硝化系数为40~60,硝化反应的时间为30~35min;优选的,控制硝化系数为48~52,硝化反应的时间为32~33min。
54.同样,现有技术中,以浆粕为原料的反应混酸,一般按照硝酸含量45%~50%控制,但该范围并非都能满足高纯净度硝化棉的反应要求,同时硝酸含量过高,过程挥发大,成本增加;现有技术中,b棉的反应温度一般为35~45℃,a、c、d棉的反应温度一般为45~55℃,该温度同样并非都能满足高纯净度硝化棉的反应要求。发明人通过大量试验确定,在满足高纯净度硝化棉的硝化质量的前提下,控制混酸中硝酸含量为45.5wt%~49wt%,b棉反应温度为40~45℃,a、c、d棉反应温度为47~52℃。
55.硝化系数和硝化时间同样影响硝化棉纯净度,当以浆粕纤维素为原料时,经试验,
需要控制控制硝化系数为18~25,硝化反应的时间为60~80min;优选的,控制硝化系数为19~22,硝化反应的时间为65~75min。
56.硝化反应后的酸棉混合物一般在离心机内完成驱酸和置换洗涤。驱酸洗涤要求:硝化棉驱酸洗涤效果也是影响硝化棉纯净度的主要因素,驱酸洗涤效果好,其物料夹带残酸数量少,利于后续安定处理,驱酸洗涤效果差,其物料夹带残酸数量多,后续安定处理困难,为确保产品的最终安定性,其后续精洗不仅需要热洗增加能耗,还需增加碳酸钠碱用量以中和物料残酸,增加了产品的灰分含量。本发明步骤b可采用现有驱酸洗涤工艺进行操作,但需要严格控制驱酸洗涤后物料的残酸度低于20%,低于15%则更优,以利于后续安定处理;若残酸度过高,后续安定处理后其安定性合格率低。
57.现有技术的硝化棉工艺中,煮洗均采用“酸煮+碱煮((碱煮温度一般在100℃以上,且碱煮时间长)”工艺,而碱煮过程中,存在一定程度的硝化纤维素酯皂化反应,这会造成硝化棉产品中的丙酮不溶解含量升高。基于此,本发明采用“酸煮+水煮+浸泡热洗”工艺,即硝化棉在一定工艺条件进行酸煮后再进行水煮,水煮后再进行低强度碱洗,有效降低了原工艺中碱煮对硝化棉质量的影响,确保了产品的丙酮不溶物含量。煮洗主要工艺条件如下:
58.酸煮工艺条件:控制煮洗水初始酸度:2~6g/l,优选为3~6g/l;根据目标产品不同,需要控制适宜的酸煮时间,以有利于纤维腔道的低级、低氮硝化物不安定杂质释放,有利于降低产品的丙酮不溶物含量,确保安定性符合要求:b棉酸煮时间不低于6h,a、c、d棉酸煮时间不低于4h;酸煮温度<120℃(具体温度可根据产品粘度调整);酸煮后进行常规洗涤,洗涤时间以洗涤后物料ph为中性为准。
59.水煮工艺条件:控制煮洗水初始ph为中性(若只写中性,一般默认为7,保护范围太小,建议请补充范围);根据目标产品不同,同样需要控制适宜的酸煮时间:b棉水煮时间不低于6h,a、c、d棉水煮时间不低于4h;水煮温度<120℃(具体温度可根据产品粘度调整);水煮后进行常规洗涤,洗涤时间以洗涤后物料ph为中性为准。
60.未碱煮的硝化棉纤维刚性较差,不利于细断,为确保细断度,细断过程须耗用较长的时间和能耗;且细断设备磨片大多为合金钢或白口铸铁磨片,硝化棉纤维夹带残酸会加入磨片腐蚀。因此本发明虽然经过了“酸煮+水煮”,但物料体系仍不能直接进行细断,同时也因为本发明已经进行过“酸煮+水煮”,此时采用一种低强度的碱洗方式,即可进一步中和物料夹带残酸,提高产品安定性,又可避免碱洗过程酯水解。经试验,在既提高细断效率、防止物料残酸腐蚀磨片或细断设备的情况下,本发明水煮洗涤后物料使用0.2~0.5g/l的碳酸钠水溶液浸泡热洗,控制热洗温度50~70℃,热洗时间1~2h。
61.现有技术硝化棉制造工艺的细断、精洗过程均会加入一定数量的碳酸钙,碳酸钙的加入,有利于产品安定性,但会增加产品的灰分和丙酮不溶物含量,导致难以获得低灰分和低丙酮不溶物的硝化棉产品。而本发明通过前端的驱酸洗涤、煮洗、碱洗工艺改进,在不加入碳酸钙的前提下保证了产品安定性。因此本发明方法中,细断、精洗过程不加入碳酸钙,细断过程加入碳酸钠数量为硝化棉绝干量的0.5~1.0
‰
,精洗过程加入碳酸钠数量为硝化棉绝干量的0~1.0
‰
(视硝化棉安定性情况)。
62.此外,目前大多硝化棉制造工艺中,细断后浆料均是直接送至精洗机;而本发明细断后增加抽滤洗涤过程,将细断物料中的不安定杂质再分离一次,这进一步确保了最终产品的安定性符合要求。具体步骤为:浸泡热洗结束后不排水,直接出料进行细断,细断过程
加入硝化棉干量0.5~1.0
‰
的碳酸钠,细断后浆料脱水至物料含水量低于70wt%,脱水后物料调浆浓度为8~12wt%进行精洗,精洗过程加入碳酸钠数量为硝化棉绝干量的0~1.0
‰
。
63.在硝化棉工业生产中,每批原料硝化时,为控制每个批次的硝化棉数量,会控制精制棉的投料数量,根据酯化取代反应和实际经验,实际得率较为清楚,因此实际生产时可以对硝化棉进行计算计量。
64.本发明综合上述总多因素的影响,对硝化棉生产过程中原材料的品质,硝化、驱酸、煮洗、细断、精洗等步骤进行优化,显著提高了所得硝化棉产品的纯净度,其丙酮不溶物和灰分含量均不超过于0.1wt%。
65.下面通过实施例对本发明作进一步详细说明,但并不因此将本发明保护范围限制在所述的实施例范围之中。
66.实施例1
67.以x60精制棉、x60木浆粕、x200棉浆粕为原料,预处理后,按照表1所示硝化参数进行硝化反应,得到a~d棉粗品。
68.表1硝化参数
[0069][0070]
a~d棉粗品采用五段逆流洗涤工艺进行驱酸洗涤,按表2控制驱酸洗涤后物料残酸度。
[0071]
表2驱酸洗涤后残酸度
[0072]
序号品种驱酸洗涤后残酸度/%1a13.62b10.73c14.24d15.85b12.96d8.77b7.28d11.5
[0073]
驱酸洗涤后物料按照表3中煮洗工艺条件,依次进行酸煮、水煮和热洗,酸煮物料和水煮物料进行常规洗涤,洗涤终点以ph试纸测试为中性为准;水煮洗涤后,用低浓度碱水热洗,热洗结束不排水,直接出料至后续细断。
[0074]
表3煮洗工艺条件
[0075][0076]
按照表4工艺条件进行细断、精洗,细断后浆料经真空带式抽滤机脱水至物料含水量低于70%,脱水后物料调浆浓度为8%~12%进行精洗,控制细断、精洗过程中碳酸钠加入量,各品种硝化棉细断后浆料在精洗机常温搅拌30min,未进行进一步热洗,精洗后脱水即得a~d棉成品,其质量技术指标如表5所示。
[0077]
表4细断、精洗碳酸钠加入量
[0078][0079]
表5各品种硝化棉质量技术指标
[0080]