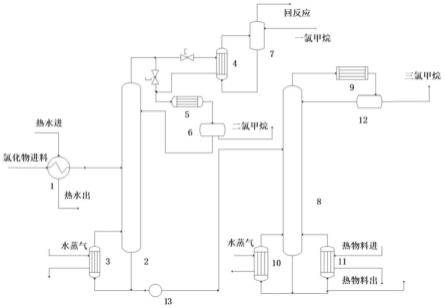
1.本发明涉及甲烷氯化物生产技术领域,具体是一种节能的甲烷氯化物精制工艺及系统。
背景技术:2.甲烷氯化物是一氯甲烷(氯甲烷)、二氯甲烷、三氯甲烷(氯仿)和四氯化碳四种甲烷氯化物的总称,简称cms,是重要的化工原料。热氯化工艺是以一氯甲烷和氯气为原料,生产二氯甲烷、氯仿和四氯化碳的过程,甲烷氯化物精馏工艺是主要是分离二氯和氯仿的过程。
3.为实现精馏效果,工艺流程中大量需要加热、冷却步骤,但加热和冷却均需外部热源、冷源实现,现有精馏过程中产生的热量未能进行很好再利用,从而导致热量的浪费。如中国专利文献cn 109734553 a(申请号201811599877.1)公开了一种节能的甲烷氯化物精制工艺,包括二氯甲烷精馏和物料预热两个过程,将二氯甲烷精馏塔塔顶馏出物中的部分给物料进行预热,另一部分经过精馏塔顶冷却器降温,省去了氯甲烷蒸发器的设置,降低了循环塔和二氯甲烷精馏塔顶冷却器负荷。但该工艺仅提供了二氯甲烷精馏过程中节能工艺,如何实现甲烷氯化物制备全过程中的节能效果,并未给出解决方案。
技术实现要素:4.本发明的目的是为解决上述技术问题,提供一种节能的甲烷氯化物精制工艺及系统,对甲烷氯化物精制工艺中二氯甲烷塔及氯仿塔产生的热量进行有效利用,并通过对精馏塔装置的改进,减少液沫夹带及蒸汽消耗,进一步降低精制过程中的能量损耗。
5.为实现上述目的,本发明采用下述技术方案:
6.一种节能的甲烷氯化物精制工艺,包括热氯化、二氯甲烷精馏和氯仿精馏三个过程,其中:
7.热氯化反应中,反应物料由二氯甲烷精馏产生的物料蒸汽加热;
8.二氯甲烷精馏中,进料物料由再沸器产生的蒸汽冷凝水加热;
9.氯仿精馏中,物料进料方式为热进料,精馏再沸热量由热氯化产物提供。
10.优选的,所述热氯化反应中,所述反应物料为一氯甲烷投料,汽化温度40-50℃,汽化压力0.8-1.0mpa。
11.优选的,所述热氯化反应中,所述二氯甲烷精馏产生的物料蒸汽为饱和的气相二氯甲烷,温度为65-75℃,压力为0.15-0.25mpa。塔顶压力由常规的0.4mpa,降低到0.15-0.25mpa,塔顶温度由94℃降低到65-75℃,塔釜温度由132℃降低到100-115℃。降低操作压力能够增加二氯甲烷和三氯甲烷相对挥发度,使得两者更容易分离,从而减少蒸汽消耗。
12.优选的,所述二氯甲烷精馏产生的物料蒸汽中直接通向冷凝器与加热反应物料的质量比为2-3:1。作为精馏反应,回流包括塔顶的液相回流与塔釜部分汽化造成的气相回流。回流是构成汽、液两相接触传质使精馏过程得以连续进行的必要条件。若塔顶没有液相
回流,或是塔底没有再沸器产生蒸汽回流,则塔板上的气液传质就缺少了相互作用的一方,也就失去了塔板的分离作用。因此,回流液的逐板下降和蒸汽的逐板上升是实现精馏的必要条件。同时,由于热氯化反应物料所需汽化温度较低,因此仅需部分二氯甲烷精馏产生的物料蒸汽,即可将热氯化反应物料进行有效汽化,同时能够保证精馏反应中回流的二氯甲烷足以保证反应的进行。
13.优选的,所述二氯甲烷精馏中,进料物料为热氯化产生的甲烷氯化物混合物料,组成分别为二氯甲烷、三氯甲烷和四氯化碳质量百分数分别是45-50%、45-50%、5%,其余为重组分。
14.优选的,所述再沸器中产生的蒸汽冷凝水,温度为95-105℃,进料物料加热至80-90℃。蒸汽冷凝水来自精馏工段再沸器中所用0.8mpa蒸汽,蒸汽释放潜热和少量的显热后的蒸汽还原成温度100℃的蒸汽冷凝水。
15.优选的,所述热氯化产物为热氯化反应出料,温度为180℃,压力为0.5mpa-0.65mpa,组成分别为氯化氢、一氯甲烷和二氯甲烷、氯仿质量百分数分别是10-15%、60-62%、10-15%,10-15%,其余为四氯化碳和重组分。
16.本发明还提供了一种用于实施上述工艺的系统,包括热氯化组件、二氯甲烷精馏组件和氯仿精馏组件,
17.所述热氯化组件包括一氯甲烷进料罐、一氯甲烷汽化器和热氯化反应釜,所述一氯甲烷汽化器用于加热一氯甲烷进料罐中的反应物料,反应物料经汽化后由一氯甲烷进料罐进入热氯化反应釜进行反应;
18.所述二氯甲烷精馏组件包括二氯甲烷塔进料预热器、二氯甲烷塔和二氯甲烷塔再沸器,所述二氯甲烷塔进料预热器中利用再沸器中产生的蒸汽冷凝水对进料物料进行加热后,进料物料进入二氯甲烷塔中进行反应,所述二氯甲烷塔还包括塔顶设置的二氯甲烷塔顶冷凝器和二氯甲烷塔回流罐,所述二氯甲烷塔再沸器用于加热二氯甲烷塔塔釜中的物料;
19.所述氯仿精馏组件包括氯仿塔再沸器、氯仿塔、氯仿塔顶冷凝器和氯仿塔回流罐,所述氯仿塔再沸器的热量由热氯化反应釜反应所得热氯化产物和蒸汽提供;
20.所述二氯甲烷塔和氯仿塔之间还设有泵送装置,二氯甲烷塔的塔釜产物由泵送装置在保温下直接输送至氯仿塔进行反应。
21.优选的,所述二氯甲烷塔和氯仿塔的塔板数分别为140块和160块,板间距为500mm。相较现有常用精馏塔,本发明通过增加塔板数有利于降低回流比,提高产品纯度,降低能耗;同时,通过提高板间距,可以有效防止液沫夹带,提高塔的处理量。
22.优选的,所述二氯甲烷塔塔顶操作压力为0.15-0.25mpa,塔顶温度为65-75℃,塔釜温度为100-115℃。通过降低操作压力能够增加二氯甲烷和三氯甲烷相对挥发度,使得两者更容易分离,从而减少蒸汽消耗。
23.本发明的有益效果:
24.1.本发明提供的精制工艺有效利用各反应过程中产生的热量,节省冷却反应出料的冷负荷,也节省加热部位的热负荷;
25.2.本发明通过将氯仿塔的进料由常规的冷进料改为热进料,升高进料的温度可减少加热过程中热量的消耗,有效减轻了再沸器的热负担;
26.3.本发明提供的系统中,通过对二氯甲烷塔和氯仿塔设备进行优化,增加了塔板数和板间距,可以提高分离精度,减少回流,防止液沫夹带,增加塔的生产能力;
27.4.本发明提供的系统中,通过对二氯甲烷塔操作压力进行了调整,由传统的0.4mpa,降低到0.15-0.25mpa,压力降低,组分的相对挥发度提高,可以减少回流量,节约蒸汽。
附图说明
28.图1为实施例2提供的系统的示意图;
29.其中,其中:1、二氯甲烷塔进料预热器,2、二氯甲烷塔,3、二氯甲烷塔再沸器,4、一氯甲烷汽化器,5、二氯甲烷塔顶冷凝器,6、二氯甲烷塔回流罐,7、一氯甲烷进料罐,8、氯仿塔,9、氯仿塔顶冷凝器,10、氯仿塔蒸汽再沸器,11、氯仿塔物料再沸器,12、氯仿塔回流罐;13、泵送装置。
具体实施方式
30.下面结合附图及实施例对本发明进行进一步说明。
31.实施例1:
32.一种节能的甲烷氯化物精制工艺,包括热氯化、二氯甲烷精馏和氯仿精馏三个过程,其中:
33.热氯化反应中,反应物料由二氯甲烷精馏产生的物料蒸汽加热;所述热氯化反应中,所述反应物料为一氯甲烷投料,汽化温度45℃,汽化压力0.9mpa。所述二氯甲烷精馏产生的物料蒸汽为饱和的气相二氯甲烷,温度为65-75℃,压力为0.15-0.25mpa;
34.二氯甲烷精馏中,进料物料由再沸器产生的蒸汽冷凝水加热,蒸汽冷凝水的温度为95-105℃,进料物料加热至80-90℃;二氯甲烷精馏中,所述二氯甲烷精馏产生的物料蒸汽中直接通向冷凝器与加热反应物料的质量比为2-3:1。所述二氯甲烷精馏中,进料物料为热氯化产生的甲烷氯化物混合物料,组成分别为二氯甲烷、三氯甲烷和四氯化碳质量百分数分别是45-50%、45-50%、5%,其余为重组分;
35.氯仿精馏中,物料进料方式为热进料,精馏再沸热量由热氯化产物提供;所述热氯化产物为热氯化反应出料,温度为180℃,压力为0.6mpa,组成分别为氯化氢、一氯甲烷和二氯甲烷、氯仿质量百分数分别是10-15%、60-62%、10-15%,10-15%,其余为四氯化碳和重组分。
36.实施例2:
37.一种用于实施实施例1提供的工艺的系统,如图1所示,包括热氯化组件、二氯甲烷精馏组件和氯仿精馏组件,
38.所述热氯化组件包括一氯甲烷进料罐7、一氯甲烷汽化器4和热氯化反应釜,其中一氯甲烷进料罐7分别与一氯甲烷汽化器4和热氯化反应釜连接,所述一氯甲烷汽化器4用于加热一氯甲烷进料罐7中的反应物料,反应物料经汽化后由一氯甲烷进料罐7进入热氯化反应釜进行反应;
39.所述二氯甲烷精馏组件包括二氯甲烷塔进料预热器1、二氯甲烷塔2和二氯甲烷塔再沸器3,所述二氯甲烷塔进料预热器1的入口与热氯化反应釜的出口连接,二氯甲烷塔进
料预热器1的出口连接至二氯甲烷塔2的进料口,所述二氯甲烷塔再沸器3与二氯甲烷塔2连接,所述二氯甲烷塔再沸器3用于加热二氯甲烷塔2塔釜中的物料,所述二氯甲烷塔进料预热器1中利用再沸器(包括二氯甲烷塔再沸器3和氯仿塔蒸汽再沸器10)中产生的蒸汽冷凝水对进料物料进行加热后,进料物料进入二氯甲烷塔2中进行反应,所述二氯甲烷塔2还包括塔顶设置的二氯甲烷塔顶冷凝器5和二氯甲烷塔回流罐6,所述二氯甲烷塔顶冷凝器5的入口连接至二氯甲烷塔2塔顶出料口,所述二氯甲烷塔顶冷凝器5的出口连接至二氯甲烷塔回流罐6的入口,所述二氯甲烷塔回流罐6的出口分别连接外部收集装置和二氯甲烷塔2进料口;
40.所述氯仿精馏组件包括氯仿塔再沸器、氯仿塔8、氯仿塔顶冷凝器9和氯仿塔回流罐12,所述氯仿塔顶冷凝器9的入口连接至氯仿塔8塔顶出料口,所述氯仿塔顶冷凝器9的出口连接至氯仿塔回流罐12的入口,所述氯仿塔回流罐12的出口分别连接外部收集装置和氯仿塔8进料口,所述氯仿塔再沸器的热量由热氯化反应釜反应所得热氯化产物和蒸汽提供,具体的,氯仿塔再沸器包括氯仿塔蒸汽再沸器10和氯仿塔物料再沸器11,所述氯仿塔物料再沸器11上分别设有热氯化物料入口和热氯化物料出口,所述热氯化物料入口和热氯化物料出口分别连接至热氯化反应釜;
41.所述二氯甲烷塔2和氯仿塔8之间还设有泵送装置13,二氯甲烷塔2的塔釜产物由泵送装置13在保温下直接输送至氯仿塔8的物料入口进行反应。
42.所述二氯甲烷塔2和氯仿塔8的塔板数分别为140块和160块,板间距为500mm。相较现有常用精馏塔,本发明通过增加塔板数有利于降低回流比,提高产品纯度,降低能耗;同时,通过提高板间距,可以有效防止液沫夹带,提高塔的处理量。
43.所述二氯甲烷塔2塔顶操作压力为0.15-0.25mpa,塔顶温度为65-75℃,塔釜温度为100-115℃。通过降低操作压力能够增加二氯甲烷和三氯甲烷相对挥发度,使得两者更容易分离,从而减少蒸汽消耗。仅对二氯甲烷塔2的塔顶压力和温度进行调整,而不对氯仿塔8的参数进行调整,是为了确保氯仿塔8出料的纯度,避免因参数调整导致出料纯度受影响,这样反而得不偿失。
44.实验例1:
45.利用实施例1提供的工艺进行实际甲烷氯化物的精制,具体为:
46.常温下12500kg/hr的氯化物(其中二氯甲烷50%、氯仿45%,四氯化碳及重组分5%)经过二氯甲烷塔进料预热器1用再沸器中产生的蒸汽冷凝水预热到85℃后进入二氯甲烷塔2,塔顶压力0.25mpa、温度75℃二氯甲烷物料蒸汽10000kg/hr进入一氯甲烷汽化器4,汽化反应所需要来自一氯甲烷进料罐7的6000kg/hr的新鲜一氯甲烷,二氯甲烷塔2产生的物料中,10000kg/hr二氯甲烷物料直接进入二氯甲烷塔顶冷凝器5冷凝,最终冷凝后二氯甲烷进入二氯甲烷回流罐6,13750kg/hr回流,6250kg/hr作为出料。二氯甲烷塔釜再沸器3每小时通入蒸汽2吨,二氯甲烷塔釜物料由泵送装置13增压到1.0mpa后直接打入氯仿塔8进行分离,氯仿塔顶每小时出5625kg/h氯仿,回流量15000kg/h,氯仿塔蒸汽再沸器10每小时通入1.5吨蒸汽,氯仿塔物料再沸器11每小时通入热氯化反应出料20吨。
47.实验例2:
48.利用实施例1提供的工艺进行实际甲烷氯化物的精制,具体为:
49.常温下12500kg/hr的氯化物(其中二氯甲烷50%、氯仿45%,四氯化碳及重组分
5%)经过二氯甲烷塔进料预热器1用再沸器中产生的蒸汽冷凝水预热到85℃后进入二氯甲烷塔2,塔顶压力0.15mpa、温度65℃二氯甲烷物料蒸汽12000kg/hr进入一氯甲烷汽化器4汽化反应所需要的来自一氯甲烷进料罐7,6000kg/hr的新鲜一氯甲烷,6000kg/hr二氯甲烷物料直接进入二氯甲烷塔顶冷凝器5冷凝,最终冷凝后二氯甲烷进入二氯甲烷回流罐6,11750kg/hr回流,6250kg/hr作为出料。二氯甲烷塔釜再沸器3每小时通入蒸汽1.8吨,二氯甲烷塔釜物料由泵送装置13增压到1.0mpa后直接打入氯仿塔8进行分离,氯仿塔顶每小时出5625kg/h氯仿,回流量15000kg/h,氯仿塔蒸汽再沸器10每小时通入1.5吨蒸汽,氯仿塔物料再沸器11每小时通入热氯化反应出料20吨。
50.实验例3:
51.利用实施例1提供的工艺进行实际甲烷氯化物的精制,具体为:
52.常温下12500kg/hr的氯化物(其中二氯甲烷40%、氯仿54%,四氯化碳及重组分6%)经过二氯甲烷塔进料预热器1用再沸器中产生的蒸汽冷凝水预热到85℃后进入二氯甲烷塔2,塔顶压力0.25mpa、温度75℃二氯甲烷物料蒸汽10000kg/hr进入氯甲烷汽化器4汽化反应所需要的来自氯甲烷进料罐7,6000kg/hr的新鲜一氯甲烷,10000kg/hr二氯甲烷物料直接进入二氯甲烷塔顶冷凝器5冷凝,最终冷凝后二氯甲烷进入回流罐6,13750kg/hr回流,5000kg/hr作为出料。二氯甲烷塔釜再沸器3每小时通入蒸汽2吨,二氯甲烷塔釜物料由泵送装置13增压到1.0mpa后直接打入氯仿塔8进行分离,氯仿塔顶每小时出6750kg/h氯仿,回流量13000kg/h,再沸器10每小时通入1.2吨蒸汽,再沸器11每小时通入热氯化反应出料20吨。
53.实验例4:
54.利用实施例1提供的工艺进行实际甲烷氯化物的精制,具体为:
55.常温下12500kg/hr的氯化物(其中二氯甲烷40%、氯仿54%,四氯化碳及重组分6%)经过二氯甲烷塔进料预热器1用再沸器中产生的蒸汽冷凝水预热到85℃后进入二氯甲烷塔2,塔顶压力0.15mpa、温度65℃二氯甲烷物料蒸汽12000kg/hr进入氯甲烷汽化器4汽化反应所需要的来自氯甲烷进料罐7,6000kg/hr的新鲜一氯甲烷,6000kg/hr二氯甲烷物料直接进入二氯甲烷塔顶冷凝器5冷凝,最终冷凝后二氯甲烷进入回流罐6,11750kg/hr回流,5000kg/hr作为出料。二氯甲烷塔釜再沸器3每小时通入蒸汽1.5吨,二氯甲烷塔釜物料由泵送装置13增压到1.0mpa后直接打入氯仿塔8进行分离,氯仿塔顶每小时出6750kg/h氯仿,回流量13000kg/h,再沸器10每小时通入1.2吨蒸汽,再沸器11每小时通入热氯化反应出料20吨。
56.上述实验例通过调整二氯甲烷进料温度、二氯甲烷塔操作压力、二氯塔馏出物热量回收、反应器出料热量利用方式均实现了系统余热再利用,降低了能量消耗。若按照常规的操作,不采用节能措施的情况下,实验例同样的12500kg/hr氯化物进料情况下,得到合格的产品每小时消耗蒸汽6-7t。实验例通过采用节能措施,利用系统内的余热,12500kg/hr氯化物进料情况下,得到合格的产品每小时消耗蒸汽2-3t,每小时减少蒸汽消耗4-5吨。
57.对比例1:
58.本对比例与实验例1的不同之处在于,二氯甲烷塔2的塔顶压力为常规生产中使用的0.4mpa,塔釜温度132℃,塔顶温度95℃,其他条件与实施例1均相同。
59.经计量,使用对比例1的二氯甲烷塔控制参数,每小时消耗蒸汽4.3t,与实验例1相比,每小时消耗蒸汽多出了0.8t,这是因为提高操作压力降低了加二氯甲烷和三氯甲烷相
对挥发度,挥发度由1.5降至1.3,产物相对不易分离,从而增加了蒸汽消耗。