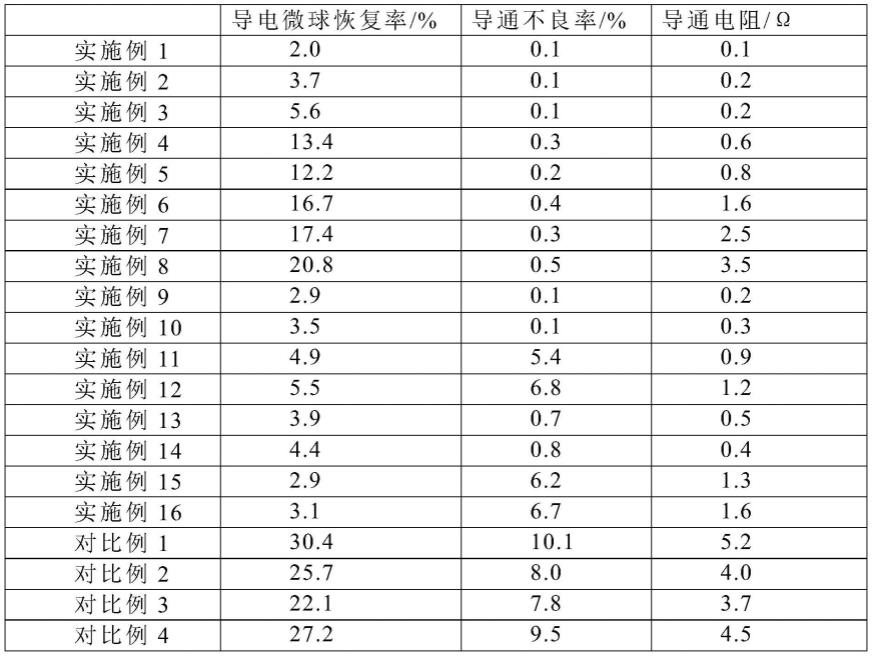
1.本发明属于异方性导电胶技术领域,涉及一种低恢复率的导电微球及其制备方法与应用。
背景技术:2.异方性导电胶在电子产品中应用时,通过异方性导电胶中的导电微球与上下金属触点接触,在加压、加热条件下,导电球被挤压与金属触点形成一定的接触面积后产生通导。但是目前市场上的很多导电微球在加热加压后,导电粒微球有一定的回弹,使与金属触点的接触面积下降,导致电子产品的导电性能降低。因此需要解决导电微球在加压、加热后与金属触点的恢复率较高的问题。
技术实现要素:3.本发明的目的是针对现有技术存在的上述问题,提出了一种低恢复率的导电微球,在预压温度和压力下形状保持不变,在本压后产生形变,形变恢复率为1~5%。
4.本发明的目的可通过下列技术方案来实现:
5.一种低恢复率的导电微球,包括内核和外层金属层,所述低恢复率的导电微球内核的原料,包括中间体,苯乙烯,引发剂aibn;其中,中间体由羧基化石墨烯、甲基丙烯酸缩水甘油酯(gma)、催化剂制成。
6.聚苯乙烯为一种高硬度的热塑性树脂,在一定温度下会发生形变,之后形状不会随着温度降低而恢复,但是聚苯乙烯材料偏脆,压力过大容易发生破裂;石墨烯具有高韧性,gma提供一部分柔韧性,在聚苯乙烯中引入石墨烯、gma,可以增加聚苯乙烯的韧性,减少聚苯乙烯材料在高压过程中产生破裂的情况的发生。同时适度过量的gma还可以提供一部分环氧基团,并且控制gma、石墨烯的量比例可以制备不同要求强度的导电粒子。
7.作为优选,内核的原料按重量份数计,包括2~10份中间体,60~90份苯乙烯,0.1~1份引发剂aibn。
8.进一步优选,所述内核中中间体、苯乙烯、引发剂aibn的质量比为(8~12):(120~170):1。
9.作为优选,所述中间体中羧基化石墨烯、甲基丙烯酸缩水甘油酯(gma)、催化剂的质量比为(5~8):(60~80):1。
10.进一步优选,所述羧基化石墨烯的纯度为98%,羧基比率为3~5%,厚度为0.55~3.74nm,尺寸为0.5~3μm,层数为1~10。
11.进一步优选,所述催化剂为koh、n,n-二甲基乙醇胺中的一种或多种。
12.作为优选,所述内核的直径为2~6um,金属层的厚度为80~150nm;导电微球的直径为3~6um。
13.进一步优选,所述内核直径、金属层厚度的比例为1um:(20~30)nm。
14.本发明还公开了一种低恢复率的导电微球的制备方法,所述的制备方法包括:
15.s1、将中间体原料加入反应瓶中经两次加热反应后,降温出料,得到中间体;
16.s2、将制得的中间体,与引发剂aibn分别溶于苯乙烯中,加热中间体混合液,恒温滴加引发剂混合液,保温后出料,得内核材料;
17.s3、利用微球成型技术把内核材料制成球体作为内核;
18.s4、在内核表面镀金属镀层,得导电微球。
19.作为优选,金属镀层包括但不限于au、ag、ni中的一种或多种。
20.作为优选,s1中两次加热反应中第一次的加热温度为70~120℃,第一次的加热时间为2~6h;第二次加热温度为90~150℃,第二次的加热时间为1~6h。
21.进一步优选,所述第二次加热温度高于第一次的加热温度,第二次的加热时间低于第一次的加热时间。
22.作为优选,s2中中间体混合液加热至70~100℃,保持恒温,滴加引发剂混合液,滴加完毕后,继续恒温保温1~5h。
23.作为优选,s2中中间体混合液、引发剂混合液中苯乙烯的含量比为(1~5):1。
24.本发明也公开了一种低恢复率的导电微球在异方性导电胶中的应用,所述低恢复率的导电微球在预压温度和预压压力下形状保持不变,在本压后产生形变,形变恢复率为1~5%。
25.作为优选,预压温度为60~90℃,预压压力为1~2mpa;本压压力为2~4mpa。
26.与现有技术相比,本发明具有以下有益效果:
27.1、本发明通过加入羧基化石墨烯与甲基丙烯酸缩水甘油酯(gma)复合的ggi(石墨烯、甲基丙烯酸缩水甘油酯中间体)中间体材料时制得的内核具有低恢复率,从而使制得的导电微球在异方性导电胶中的应用时,在预压温度和预压压力下形状保持不变,在本压后产生形变,具有低形变恢复率。
28.2、本发明的制备方法简单可控,可规模化生产。
29.3、本发明的低恢复率的导电微球可适用于多种异方性导电胶体系,适用范围广。
具体实施方式
30.以下是本发明的具体实施例,对本发明的技术方案作进一步的描述,但本发明并不限于这些实施例。
31.实施例1
32.1、中间体
33.将7份羧基化石墨烯、75份gma、1份催化剂(n,n-二甲基乙醇胺)加入反应瓶,加热到80℃,反应4h,再升温到100℃反应2h,温度降至室温后出料,得到中间体。
34.2、内核
35.将6份中间体与60份苯乙烯混合得中间体混合液,作为釜底;将0.6份引发剂溶解在20份苯乙烯中,得引发剂混合液,作为滴加单体;将中间体混合液加热至90℃,开始滴加引发剂混合液,匀速滴加,滴加时间为4h,接着保温1h,温度降至室温后出料,得内核材料。
36.将内核材料通过微球成型技术制成直径为5μm的均一球体,作为内核。
37.3、导电微球
38.在内核表面通过化学镀表面技术镀ag、ni混合镀层,ag、ni的质量比为1:2,镀层厚
度为120nm。
39.将导电微球与其余的异方性导电胶原料混合,制成异方性导电胶膜。在预压温度(80℃)和预压压力(1mpa)下形状保持不变,在本压(2mpa)后产生形变,将其进行性能测试,结果如表1所示。
40.实施例2
41.与实施例1相比,区别在于中间体中加入6.5份羧基化石墨烯、70份gma、1份催化剂(n,n-二甲基乙醇胺)。
42.实施例3
43.与实施例1相比,区别在于中间体中加入6份羧基化石墨烯、62份gma、0.8份催化剂(n,n-二甲基乙醇胺)。
44.实施例4
45.与实施例1相比,区别在于中间体中加入9份羧基化石墨烯、60份gma、1份催化剂(n,n-二甲基乙醇胺)。
46.实施例5
47.与实施例1相比,区别在于中间体中加入4份羧基化石墨烯、60份gma、1份催化剂(n,n-二甲基乙醇胺)。
48.实施例6
49.与实施例1相比,区别在于中间体中加入3.5份羧基化石墨烯、50份gma、0.8份催化剂(n,n-二甲基乙醇胺)。
50.实施例7
51.与实施例1相比,区别在于中间体中加入6份羧基化石墨烯、80份gma、0.8份催化剂(n,n-二甲基乙醇胺)。
52.实施例8
53.与实施例1相比,区别在于中间体中加入3份羧基化石墨烯、82份gma、0.8份催化剂(n,n-二甲基乙醇胺)。
54.实施例9
55.与实施例1相比,区别在于内核中中间体的加入量为7份,引发剂的加入量为0.6份。
56.实施例10
57.与实施例1相比,区别在于内核中中间体的加入量为5份,引发剂的加入量为0.6份。
58.实施例11
59.与实施例1相比,区别在于内核中中间体的加入量为4.5份,引发剂的加入量为0.6份。
60.实施例12
61.与实施例1相比,区别在于内核中中间体的加入量为7.5份,引发剂的加入量为0.6份。
62.实施例13
63.与实施例1相比,区别在于导电微球中内核直径为110nm,镀层厚度为5μm。
64.实施例14
65.与实施例1相比,区别在于导电微球中内核直径为100nm,镀层厚度为5μm。
66.实施例15
67.与实施例1相比,区别在于导电微球中内核直径为90nm,镀层厚度为5μm。
68.实施例16
69.与实施例1相比,区别在于导电微球中内核直径为160nm,镀层厚度为5μm。
70.对比例1
71.与实施例1相比,区别在于在异方性导电胶中加入常规的导电微粒(内核为聚乙烯/聚甲基丙烯酸酯)。
72.对比例2
73.与实施例1相比,区别在于中间体的原料中不包括羧基化石墨烯。
74.对比例3
75.与实施例1相比,区别在于中间体的原料中不包括催化剂。
76.对比例4
77.与实施例1相比,区别在于中间体的原料中采用甲基丙烯酸羟乙酯替换甲基丙烯酸缩水甘油酯(gma)。
78.表1、性能数据表
[0079][0080]
从表中可知,实施例1~8中,改变中间体的组分比例会影响形变恢复率,其中羧基化石墨烯加入量过多会导致形变恢复率变大,导通不良率增加,羧基化石墨烯加入量过少则中间体不稳定,易分层,合成的内核材料性能差,导致导电微球形变恢复率、导通不良率、导通电阻都会很差;实施例9~12中中间体加入量过多导致合成反应时间变长,聚合交联率
下降,内核材料性能变差,过少导致反应较快,分子量较小,内核性能也会变差;实施例13~16中镀层过薄导致导电粒子易形变,过厚导致难形变。对比例2中不加入羧基化石墨烯导致内核容易破裂;对比例4中采用甲基丙烯酸羟乙酯替换gma,导致内核韧性变差,恢复率变差。
[0081]
综上所述,本发明通过特殊组成的中间体材料时制得的内核具有低恢复率,从而使制得的导电微球在异方性导电胶中的应用时,在预压温度和预压压力下形状保持不变,在本压后产生形变,具有低形变恢复率。
[0082]
本文中所描述的具体实施例仅仅是对本发明精神作举例说明。本发明所属技术领域的技术人员可以对所描述的具体实施例做各种各样的修改或补充或采用类似的方式替代,但并不会偏离本发明的精神或者超越所附权利要求书所定义的范围。