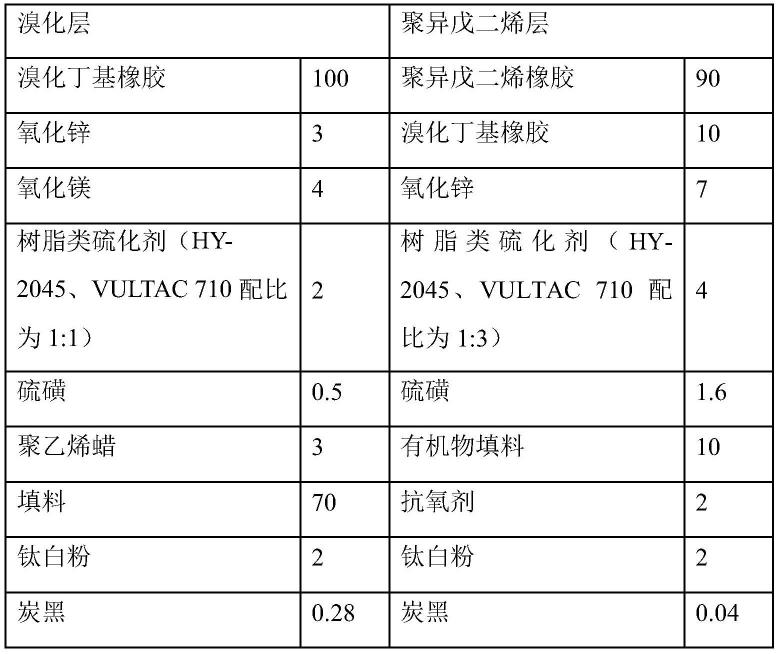
1.本发明涉及一种溴化丁基/聚异戊二烯橡胶垫片及其生产方法,属于医用橡胶附件技术领域。
背景技术:2.卡式瓶医药内包装体系的使用方便、适用性广。卡式瓶是没有底的管制抗生素瓶,瓶口用笔式注射器用垫片和笔式注射器用铝盖密封,底部用丁基橡胶活塞密封。就笔式注射器用垫片而言,国外技术明显领先国内。国外第二代垫片,由上下两层结构组成,上层橡胶材料弹性好,耐穿刺性能和密合性能好;下层橡胶材料与药品配伍性好,整体上呈现梯形圆台结构,与笔式注射器用铝盖接触面大,摩擦力大,过盈配合好,从而达到与笔式注射器用铝盖的良好装配效果。国内第一代垫片为单层结构,橡胶材料为丁基橡胶,硬度高,与药品配伍性好,而在多次针刺后,垫片会产生微孔容易漏液。目前,国内第二代双层垫片均处于研制状态,专利号为“cn202110261173.9”的专利提供了一种卡式瓶用双层垫片的生产方法,采用三次硫化的方式硫化出双层硫化胶片,制得双层垫片。但三次硫化出的产品两层间粘接力不强,且操作较为繁琐;同时因为收缩率不同的原因,采用二次硫化的方式硫化出来的双层硫化胶容易发生卷曲,无法冲切除边制备出成品。
技术实现要素:3.本发明提供了一种溴化丁基/聚异戊二烯橡胶垫片的配方及其生产方法,采用本配方及生产方法制备的双层硫化胶片两层间粘接力强,硫化后产品平坦不卷曲,易于冲切除边。
4.为实现上述目的,本发明的技术方案为:一种溴化丁基/聚异戊二烯橡胶垫片及其生产方法,其特征在于,其配方由如下重量份的原材料组成:溴化层配方:溴化丁基橡胶100份、氧化锌0.5~7份、氧化镁2~5份、树脂类硫化剂1~5份、硫磺0.1~0.5份、聚乙烯蜡0.5~5份、填料55~90份、钛白粉0.5~3份、炭黑0.1~0.4份。
5.聚异戊二烯层配方:聚异戊二烯橡胶90~100份、溴化丁基橡胶0~10份、氧化锌0.5~7份、树脂类硫化剂3~6份、硫磺0.1~2份、有机物填料5~25份、抗氧剂0.5~3份、钛白粉0.5~3份、炭黑0.02~0.08份。
6.优选地,原料组成中,树脂类硫化剂由对-特辛基酚醛硫化树脂和烷基苯酚二硫化物组合而成,对-特辛基酚醛硫化树脂和烷基苯酚二硫化物的重量之比为1:(1~4)。
7.所述的烷基苯酚二硫化物包括对叔戊基苯酚二硫化物或对叔丁基苯酚二硫化物。
8.烷基苯酚二硫化物是一种不产生亚硝胺的硫的给予体,因苯酚基团位阻效应,二硫基团不容易靠近,能够形成以双硫键为主的交联键,同时形成高交联密度的网络结构,具有较好的耐热氧老化性和抗硫化返原性,网络结构中自由体积小,分子结构稳定,不易被破坏;对-特辛基酚醛硫化树脂分子两段主要以羟甲基活性基团封端,特别试用于不饱和橡胶
的硫化,形成更稳定的c-c键,耐热性和抗硫化返原性好。采用树脂类硫化剂制备的产品耐热性好,不喷霜,同时增强两橡胶层间粘接力。
9.所述的填料为硅藻土、碳酸钙、膨润土、硅微粉或高岭土;所述的有机物填料为超高分子量聚乙烯粉末,分子量为1.6
×
10
6-2.2
×
106,平均粒径应低于40μm,密度0.930g/cm
3-0.960g/cm3。
10.优选地,聚异戊二烯层配方原料组成中,所用有机物填料为超高分子量聚乙烯粉末,分子量为2
×
106,平均粒径25μm,密度0.940g/cm3。其颗粒小,在橡胶中易于分散,可以改善橡胶自润滑性能,提高橡胶产品的硬度、弹性和耐化学性能。双层垫片中,聚异戊二烯层主要起到再密封作用,保证注射针多次穿刺后双层垫片仍旧具有良好的密封作用,同时防止漏液,因此配方设计时聚异戊二烯层灰分需控制到极低的程度。但配方中含胶率过高时混炼胶片的收缩率较大,导致混炼后压延出片时难以压延成型得到合适的混炼胶片,同时硫化后的胶片强度也比较低,因此在配方中加入有机填料,以便于压延出片并提高硫化胶片强度。
11.优选地,所述抗氧剂为pdm和抗氧剂1076组合而成,重量之比为1:1。pdm即间苯撑双马来酰亚胺hva-2,多用于橡塑的助交联剂和橡胶防焦剂,可以大幅降低压缩永久变形提高弹性和耐热性能,增加橡胶粘接力,也具有抗热氧老化作用,抗氧剂1076则主要起到防老化作用。
12.优选地,一种溴化丁基/聚异戊二烯橡胶垫片及其生产方法其特征在于包括以下步骤:(1)配料:根据溴化层配方和聚异戊二烯层配方配料备用;(2)混炼:采用密炼机和相应的开炼机,按照溴化层配方和聚异戊二烯层配方混炼工艺进行混炼,制备相应配方混炼胶;(3)压延出片:根据硫化时胶片尺寸需求,将步骤(3)中得到的混炼胶于三辊压延机中压延成型,分别制成便于硫化的溴化层混炼胶胶片和聚异戊二烯层混炼胶胶片;(4)一次硫化:将步骤(3)中压延好的溴化层混炼胶胶片放入硫化模具中,欠硫生产,得到欠硫的溴化层胶片;(5)二次硫化:将步骤(4)中欠硫的溴化层胶片用无水乙醇或丙酮擦拭处理,去除其表面的脱模剂及杂质,烘干后将欠硫的溴化层胶片放入二次硫化模具中,贴上步骤(3)中聚异戊二烯层混炼胶胶片进行硫化,得到双层胶片,硫化温度为160℃~165℃,硫化时长为4~6min;(6)冲切:将步骤(5)中的双层硫化胶片放到冲模上冲切,即得双层垫片;(7)清洗包装:将双层垫片放入胶塞清洗机,进行清洗、烘干并包装。
13.进一步地:上述步骤(4)一次硫化时需要先硫化溴化层,且溴化层需欠硫硫化,硫化温度为175℃~185℃,取混炼好的溴化层混炼胶在相应温度下于无转子硫变仪器中进行检测,测定相应温度下的溴化层混炼胶正硫化时间(tc
90
),欠硫硫化时间设定为以上测定的正硫化时间(tc
90
)的75%-85%。相比与聚异戊二烯橡胶,溴化丁基橡胶抗硫化返原性更强,不会在二次硫化时发生返原现象,弹性也更小;而聚异戊二烯橡胶的弹性较大,若先硫化聚异戊二烯层,二次硫化时溴化层混炼胶流动会带动一次硫化得到的橡胶片,导致其变形,于是二次硫化后的双层橡胶片发生卷曲,因此选择先硫化弹性更小的溴化层。欠硫硫化可以
使溴化层胶片初步定型,且具备较大的强度,提高两橡胶层间的粘接力;欠硫生产时的硫化时间如过短,溴化层橡胶片交联度不够,强度不够,二次硫化时易被上层流动的异戊二烯层混炼胶带动发生变形,导致二次硫化后双层胶片卷曲;欠硫生产时的硫化时间如过长,溴化层橡胶片交联程度过于完全,则难以和异戊二烯层共交联,二次硫化后两橡胶层间粘接力不足,易发生脱层。
14.本发明具有以下有益效果:(1)本发明采用二次硫化的方式,先欠硫硫化溴化层,得到欠硫的溴化层胶片,使用无水乙醇及丙酮清除表面脱模剂和杂质后,再将处理后的欠硫溴化层胶片放入二次硫化模具中,贴上压延好的聚异戊二烯橡胶配方混炼胶,硫化成型。本发明提供的配方及生产方法解决了二次硫化时双层硫化胶片卷曲的问题,硫化后产品平坦不卷曲,易于冲切除边。
15.(2)本发明使用由对-特辛基酚醛硫化树脂和烷基苯酚二硫化物按一定比例组合而成的混合树脂硫化剂,硫化出的产品耐热性好,不喷霜,且两橡胶层间粘接力强,不发生脱层。
附图说明
16.图1为经二次硫化成型得到的双层橡胶片。
17.图2为双层橡胶片冲切除边后的双色垫片产品。
具体实施方式
18.以下结合实施例,对本发明进行进一步详细说明。应当理解,此处所描述的具体实施例仅用以解释本发明,并不用于限定本发明。
19.溴化丁基橡胶使用胶塞基料的丁基橡胶,优选型号为埃克森美孚2211;氧化锌选用美国阿科隆科技公司活性氧化锌,牌号205;选用运城市八星化工有限公司氧化镁;树脂类硫化剂由对-特辛基酚醛硫化树脂和烷基苯酚二硫化物组成,对-特辛基酚醛硫化树脂选用山西省化工研究所(有限公司)hy-2045,烷基苯酚二硫化物优选荷兰arkema公司vultac 710;选用美国struktol公司硫磺;溴化层配方填料选择范围包括但不限于白炭黑、滑石粉、高岭土、硫酸钡、碳酸钙、陶土,优选的填料为滑石粉;聚异戊二烯层配方中使用有机填料超高分子量聚乙烯粉末作为填充剂,提高产品的弹性和硬度,优选牌号具体为三井化学株式会社xm-221u。
20.实施例1按重量份数计,实施例1中原料的组成见下表1:表1实施例1原料组成
本实施例中溴化层中填料为高岭土;聚异戊二烯层配方原料组成中,所用有机物填料为超高分子量聚乙烯粉末,分子量为2
×
106,平均粒径25μm,密度0.940g/cm3。
21.具体生产方法如下(1)配料:根据溴化层配方和聚异戊二烯层配方配料备用;(2)混炼:采用密炼机和相应的开炼机,按照溴化层配方和聚异戊二烯层配方混炼工艺进行混炼,制备相应配方混炼胶;(3)压延出片:根据硫化时胶片尺寸需求,将步骤(3)中得到的混炼胶于三辊压延机中压延成型,分别制成便于硫化的溴化层混炼胶胶片和聚异戊二烯层混炼胶胶片;(4)一次硫化:将步骤(3)中压延好的溴化层混炼胶胶片放入硫化模具中,欠硫生产,得到欠硫的溴化层胶片,硫化温度设定为180℃,此配方在该温度下于无转子流变仪中测定的正硫化时间(tc
90
)为240s,硫化时间设定为正硫化时间的80%,即192s;(5)二次硫化:将步骤(4)中欠硫的溴化层胶片用无水乙醇或丙酮擦拭处理,去除其表面的脱模剂及杂质,烘干后将欠硫的溴化层胶片放入二次硫化模具中,贴上步骤(3)中聚异戊二烯层混炼胶胶片进行硫化,得到双层胶片,硫化温度为160℃~165℃,硫化时长为240s~360s;(6)冲切:将步骤(5)中的双层硫化胶片放到冲模上冲切,即得双层垫片;(7)清洗包装:将双层垫片放入胶塞清洗机,进行清洗、烘干并包装。
22.根据上述配方及生产方法制备的双层橡胶片平坦不卷曲,经冲切除边后可以得到满足使用要求的双色垫片,如图1、图2所示。
23.实施例2-6实施例2-6基于实施例1,区别在于:
实施例2溴化层欠硫硫化时,硫化时间设定为相应硫化温度下溴化层混炼胶正硫化时间(tc90)的40%,即96s;实施例3溴化层欠硫硫化时,硫化时间设定为相应硫化温度下溴化层混炼胶正硫化时间(tc90)的75%,即180s;实施例4溴化层欠硫硫化时,硫化时间设定为相应硫化温度下溴化层混炼胶正硫化时间(tc90)的85%,即204s;实施例5溴化层欠硫硫化时,硫化时间设定为相应硫化温度下溴化层混炼胶正硫化时间(tc90)的100%,即240s;实施例6溴化层欠硫硫化时,硫化时间设定为相应硫化温度下溴化层混炼胶正硫化时间(tc90)的110%,即264s。
24.上述实施例2制备得到的双层橡胶片出现卷曲现象,无法进行后续冲切生产,实施例3-6制备的双层橡胶片平坦不卷曲。为保证双层橡胶片平坦不卷曲且两橡胶层间具备较好的粘接力,需确定较为合适的溴化层硫化时间,因此,使用《国家药包材标准》中ybb00102003-2015剥离强度测定法对上述实施例3-6制备的双层橡胶片进行两橡胶层间粘接力测定。测试结果如下表2,根据表中数据显示,一次硫化的欠硫硫化时间设定为相应硫化温度下正硫化时间(tc
90
)的75%~85%较为合适。
25.表2实施例1、实施例3-6粘接力实施例7-10实施例7-10基于实施例1中原料配比以及实施例1中的生产方法制备双层橡胶垫片,区别在于:实施例7中有机物填料使用份数为0,即,不使用有机物填料,其他原料配比不变;实施例8中有机物填料使用三井化学xm-330牌号产品;实施例9中有机物填料使用三井化学xm-220牌号产品;实施例10中有机物填料使用三井化学xm-220u牌号产品。
26.以上三种牌号有机物填料的物理特性如下表3所示,根据不同有机物填料制备的双层橡胶片呈现不同结果,实施例7中,聚异戊二烯层混炼胶在压延出片后停放时胶片尺寸变短,厚度变厚。胶片实施例8中二次硫化后得到的部分双层橡胶片出现局部卷曲凹陷现象,实施例9、实施例10则平坦不卷曲。有机物填料的加入可以保证低灰分的同时赋予混炼胶较好的压延出片性能,但若有机物填料的粒径过大,会出现双层胶片出现局部的卷曲凹
陷现象,推测可能是较大粒径的有机物填料在硫化温度下程高弹态分散到橡胶交联网络中,冷却后恢复塑料特性,使橡胶交联网络发生变形,宏观上双层橡胶片局部出现卷曲和凹陷。因此,使用平均粒径小于40μm的有机物填料较为合适。
27.表3有机物填料物理特性表实施例11-13按重量份数计,实施例11-13中原料的组成见下表4:表4实施例11-13原料组成实施例11-13中,溴化层中填料为高岭土;聚异戊二烯层配方原料组成中,所用有机物填料为超高分子量聚乙烯粉末,分子量为2
×
106,平均粒径25μm,密度0.940g/cm3。
28.根据上表实施例11-13配方按照实施例1的生产方法制备溴化丁基/聚异戊二烯橡胶垫片,制备的产品平坦不卷曲。另,将二次硫化后得到的双层橡胶片按照《国家药包材标准》中《ybb00102003-2015剥离强度测定法》测定粘接力,同时将最终制备的双层垫片产品按照《国家药包材标准》中《ybb00162004-2015笔试注射器用溴化丁基橡胶活塞和垫片》标准要求进行产品性能测试,测试结果如下表5所示,制备的产品满足国家相关标准要求。表5产品性能测试结果
29.本领域的技术人员容易理解,以上所述仅为本发明的较佳实施例而已,并不用以限制本发明,凡在本发明的精神和原则之内所作的任何修改、等同替换和改进等,均应包含在本发明的保护范围之内。