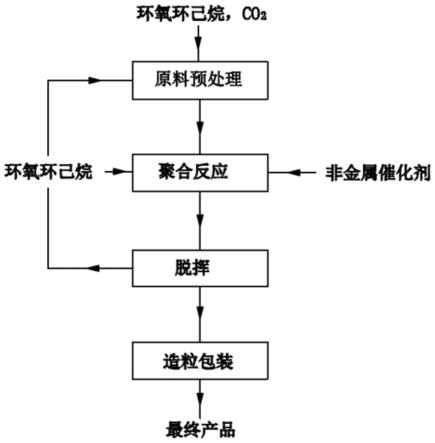
1.本发明属于聚碳酸酯生产工艺领域,具体涉及一种二氧化碳基聚碳酸环己撑酯生产工艺。
背景技术:2.随着国内外“禁塑令”的推行,可降解材料将逐步替代传统塑料,尤其是二氧化碳基聚碳酸酯可降解材料,在“双碳”政策的背景下,未来必将作为一项重大技术应用于工业领域。
3.聚碳酸环己撑酯pchc作为二氧化碳基聚碳酸酯中的一种重要产品,目前制备工艺主要有溶液聚合法和本体聚合法。本体聚合法是在反应体系中,通入环氧环己烷、二氧化碳、催化剂及分子量调节剂,聚合反应结束后,将单体与催化剂分离,得到最终产物。溶液聚合法是在本体聚合法的基础上,加入四氢呋喃、dmf或二氯甲烷等一种或几种可以溶解pchc的溶剂,反应结束后分离溶剂、环氧环己烷及催化剂,得到最终产物。
4.本体聚合主要以间歇釜式操作为主,通常粘度随着反应的进行逐步增长,反应开始仅有几厘泊,随着转化率的不断增高可达几万厘泊,因此机械搅拌的设计及制造难度较大,同时能耗将大幅提高。其次,间歇釜式反应单程转换率较低,造成单体回收工序设备负荷较大。更关键的是聚合反应本身属于强放热反应,需及时移除反应热,但是随着粘度的增加,体系传热愈发困难,增加了工艺放大风险。
5.溶液聚合法克服了上述反应体系粘度较大的问题,但是需增加溶剂回收工序,回收溶剂过程中又会造成溶剂损失,且产物中也不可避免会夹带部分溶剂,造成产物不纯。
6.更重要的是,目前pchc制备工艺中主要为金属催化体系,聚合反应放热量大,且产物中存在金属残留,影响产物色泽度,因此在工艺流程中还必须设催化剂分离工序。
技术实现要素:7.本发明旨在解决pchc制备过程中存在的体系粘度高、聚合反应放热量大、产品中金属残留及工艺流程长等问题,提供一种非金属催化体系下的二氧化碳基聚碳酸环己撑酯生产工艺,该工艺无需催化剂分离工序,工艺条件温和,不存在体系粘度高,反应放热量大的问题,经济性更好;同时所得的pchc无金属残留,色泽度优良,耐温性更优。
8.为实现上述目的,本发明采用的技术方案包括如下步骤:
9.一种二氧化碳基聚碳酸环己撑酯生产工艺,包括以下步骤:
10.将非金属催化剂加入到的聚合反应装置中,通入除水后的环氧环己烷和二氧化碳,在压力为0.1~2mpa,温度为25~150℃下进行聚合反应2h~12h,得到聚合溶液,从聚合溶液中分离聚碳酸环己撑酯;非金属催化剂为路易斯酸碱对催化剂。
11.进一步的,从聚合溶液中分离聚碳酸环己撑酯时,采用溶剂萃取、螺杆挤出脱挥、减压蒸馏及闪蒸中的一种或几种进行分离。
12.进一步的,环氧环己烷与非金属催化剂的摩尔比为1000:1~25000:1。
13.进一步的,聚合反应装置为聚合反应釜与卧式平推流反应器中的一种或两种组合。
14.进一步的,聚合反应装置采用聚合反应釜时,聚合反应釜采用多釜并联布置。
15.进一步的,进行聚合反应后采用环氧环己烷、一氯甲烷、二氯甲烷、二氯乙烷、四氢呋喃、丙酮、环己酮与n,n-二甲基酰胺中的一种或几种清洗聚合反应装置。
16.进一步的,环氧环己烷中的水分为10~500ppm,环氧环己烷中的醇类化合物为0~200ppm;二氧化碳中的水分为5~500ppm。
17.进一步的,环氧环己烷通过精馏、吸附与闪蒸中一种或几种进行除水后进行聚合反应。
18.进一步的,向聚合反应装置中加入用于降低粘度的聚碳酸环己撑酯。
19.进一步的,从聚合溶液中分离聚碳酸环己撑酯的同时得到未反应的环氧环己烷,未反应的环氧环己烷能够再次进入聚合反应装置中进行反应。
20.与现有技术相比,本发明的有益效果在于:
21.本发明通过环氧环己烷和二氧化碳在非金属催化剂下进行聚合反应,聚合反应的机理为配位阴离子聚合,聚合机理如下:(i)非金属催化剂中的路易斯碱性的阴离子进攻环氧环己烷生成烷氧阴离子,并与路易斯酸性中心形成烷氧基配位结构;(ii)二氧化碳迅速插入到烷氧基配位结构中生成烷氧碳酸根阴离子;(iii)路易斯碱性的烷氧碳酸根阴离子再次进攻环氧环己烷并与路易斯酸性中心形成配位结构,二氧化碳再次插入,如此环氧环己烷和二氧化碳交替插入,从而得到聚合物链。由于阴离子聚合特点是快引发,慢增长,并且环氧环己烷和二氧化碳依次交替插入聚合物链段中,导致聚合物链段规整性好,基本无支链产生,因此反应放热温和,无明显爆聚现象发生。本发明的工艺由于不采用金属催化剂,所以产物无金属残留,色泽度优良,且无催化剂分离工序,可节约大量设备投入及能耗成本。pchc可以在环氧环己烷中溶解,因此当反应体系粘度较大时,可以补充环氧环己烷稀释反应体系,克服了现有反应体系下粘度增大导致传质、传热恶化的不利影响。
22.进一步的,聚合反应装置采用聚合反应釜时,可使用多釜并联操作,在工程上实现连续化生产,提高单程转化率。
附图说明
23.图1为本发明的生产过程示意图。
具体实施方式
24.下面结合附图通过实施例对本发明进行详细描述。
25.参见图1,本发明的一种二氧化碳基聚碳酸环己撑酯生产工艺,包括以下步骤:
26.本发明中采用的非金属催化剂为专利201910764053.3中的有机硼催化剂。
27.1)原辅料包括:非金属催化剂,环氧环己烷,二氧化碳,二氧化碳的来源包括且不限于煅烧法、乙醇发酵气回收法及工业废气回收法。
28.首先进行原料预处理:
29.将环氧环己烷与二氧化碳进行预处理,使环氧环己烷中的水分脱除至10~500ppm,醇类化合物脱除至0~200ppm,使二氧化碳中的水分脱除至5~500ppm。
30.所述的原料预处理的工艺包括且不限于精馏、吸附、闪蒸及反应除水中一种或几种的组合。特别地,如果环氧环己烷和二氧化碳满足聚合条件,可直接进行聚合反应。
31.优选的,采用精馏与吸附组合工艺的方式将环氧环己烷中的水分脱除至10~500ppm,醇类化合物脱除至0~200ppm。同时,采用吸附工艺将二氧化碳中的水分脱除至5~500ppm。
32.2)进行聚合反应:
33.将非金属催化剂加入到的聚合反应装置中,通入预处理后的环氧环己烷和二氧化碳,调节的聚合反应单元内压力0.1~2mpa,在25~150℃下进行聚合反应2~12h,得到聚合溶液。
34.其中,环氧环己烷与非金属催化剂的摩尔比为1000:1~25000:1。
35.所述的聚合反应装置采用聚合反应釜、卧式平推流反应器的一种或两种,当采用聚合反应釜与卧式平推流反应器时,聚合反应釜进行预聚后通入卧式平推流反应器中进行深度聚合,在该聚合反应装置中,环氧环己烷可实现单程转化率由低到高宽域分布。
36.聚合反应装置采用聚合反应釜时,聚合反应釜还可以采用多釜并联布置,交替进行聚合反应,在工程上实现连续操作。
37.优选的,聚合反应装置采用卧式平推流反应器。
38.优选的,本发明在聚合反应装置中还设有清洗系统,用于定期清洗聚合聚合反应釜,清洗液可循环利用。清洗液可以为环氧环己烷、一氯甲烷、二氯甲烷、二氯乙烷、四氢呋喃、丙酮、环己酮与n,n-二甲基酰胺等可以溶解pchc的溶剂中的一种或几种。
39.所述聚合反应过程中粘度增大时,可通过补充环氧环己烷以降低体系粘度。
40.3)进行脱挥:
41.从所得的聚合溶液中分离pchc,同时回收未反应的环氧环己烷。
42.进行脱挥时,仅需要分离产物(pchc)和原料(环氧环己烷和二氧化碳)即可,无需分离催化剂工序。
43.分离pchc和环氧环己烷的工艺包括且不限于溶剂萃取、螺杆挤出脱挥、减压蒸馏及闪蒸中的一种或几种的组合。
44.所述的未反应的环氧环己烷回收后返回到原料预处理单元。特别地,如果环氧环己烷满足聚合条件,可直接进行聚合反应。
45.4)进行造粒包装:
46.将分离得到的pchc进行造粒、包装得到最终产物。
47.优选的,采用双螺杆挤出机组真空抽提回收环氧环己烷,同时pchc被挤压造粒。从双螺杆挤出机组抽提出环氧环己烷水分及醇类化合物指标合格时,可直接进行聚合反应。
48.本发明工艺中所产生的废气采用环保处理经过多级冷凝收集后再进行火炬焚烧,可显著降低空气中vocs排放,所有的废液均收集到废液罐中后统一处理。
49.实施例1
50.采用分子筛分别将环氧环己烷(%.wt≥98,水≤2500ppm)的水含量脱除至173ppm,二氧化碳(≥99.99%)水含量脱除至10ppm,反应前采用处理后的环氧环己烷清洗反应釜,然后将二氧化碳通入100ml聚合反应釜,同时加入非金属催化剂(专利201910764053.3中b4催化剂)和环氧环己烷49.64g,环氧环己烷和催化剂的摩尔比为
20000:1),保持聚合反应釜100℃,1.5mpa下聚合12h,得到聚合物溶液,聚合物溶液在乙醇溶液(体积浓度95%)中萃取析出,得到pchc为36.22g。
51.聚合产物核磁结果表明pchc选择性>99%,凝胶色谱结果显示pchc分子量为41761,pdi为1.173。
52.实施例2
53.在实施例1的基础上,改变环氧环己烷与催化剂的摩尔比为15000:1,其他条件不变。最终得到pchc为33.81g。
54.聚合产物核磁结果表明pchc选择性>99%,凝胶色谱结果显示pchc分子量为32325,pdi为1.155。
55.实施例3
56.在实施例1的基础上,改变聚合反应时间为8h,其他条件不变,最终得到pchc为25.47g。
57.聚合产物核磁结果表明pchc选择性>99%,凝胶色谱结果显示pchc分子量为29949,pdi为1.199。
58.实施例4
59.采用分子筛与精馏组合工艺处理环氧环己烷(%.wt≥98,水≤2500ppm),结果显示环氧环己烷的水含量可脱除至106ppm,醇类化合物几乎未检测到。其他条件同实施例1,最终得到pchc为43.52g。
60.聚合产物核磁结果表明pchc选择性>99%,凝胶色谱结果显示pchc分子量为109719,pdi为1.168。
61.表1不同聚合条件下的结果对比表
[0062][0063]
备注:表中cho为环氧环己烷,cat为催化剂
[0064]
实施例5
[0065]
采用精馏将环氧环己烷(%.wt≥98,水≤2500ppm)的水含量脱除至330ppm,醇类化合物几乎未检测到,采用吸附将二氧化碳(≥99.99%)水含量脱除至20ppm。聚合反应前二氯甲烷清洗卧式平推流反应器,将二氧化碳通入10l卧式平推流反应器,同时加入非金属催化剂(专利201910764053.3中b4催化剂)和环氧环己烷6.8kg,环氧环己烷和催化剂的摩尔比为1000:1),保持卧式平推流反应器80℃,压力为1mpa,聚合12h后,得到pchc为5.1kg。
[0066]
聚合产物核磁结果表明pchc选择性>99%,凝胶色谱结果显示pchc分子量为12474,pdi为1.182。
[0067]
实施例6
[0068]
采用闪蒸将环氧环己烷(%.wt≥98,水≤2500ppm)的水含量脱除至480ppm,醇类化合物含量为5400ppm,采用分子筛吸附将二氧化碳(≥99.99%)水含量脱除至10ppm。采用二氯甲烷清洗聚合反应釜,将二氧化碳通入100ml聚合反应釜,同时加入非金属催化剂(专利201910764053.3中b4催化剂)和环氧环己烷50.47g,环氧环己烷和催化剂的摩尔比为
5000:1),保持聚合反应釜100℃,2mpa下聚合8h,得到pchc为21.35g。
[0069]
聚合产物核磁结果表明pchc选择性>99%,凝胶色谱结果显示pchc分子量为7980,pdi为1.165。
[0070]
实施例7
[0071]
采用精馏与分子筛吸附的组合工艺将环氧环己烷(%.wt≥98,水≤2500ppm)的水含量脱除至55ppm,醇类化合物几乎未检测到,二氧化碳(≥99.99%)水含量脱除至10ppm。采用环氧环己烷清洗聚合反应釜,将非金属催化剂(专利201910764053.3中b4催化剂)和环氧环己烷15.1kg,环氧环己烷和催化剂的摩尔比为25000:1加入25l聚合反应釜中,充入二氧化碳保持2mpa压力,温度为120℃,聚合3h后再通入10l卧式平推流反应器中),保持卧式平推流反应器1.5mpa压力,120℃进行深度聚合1h后,得到pchc为14.66kg。
[0072]
聚合产物核磁结果表明pchc选择性>99%,凝胶色谱结果显示pchc分子量为178674,pdi为1.172。
[0073]
实施例8
[0074]
采用分子筛分别将环氧环己烷(%.wt≥98,水≤2500ppm)的水含量脱除至284ppm,将二氧化碳(≥99.99%)水含量脱除至13ppm。聚合反应前采用环氧环己烷清洗聚合反应釜,将二氧化碳通入100ml聚合反应釜,同时加入非金属催化剂(专利201910764053.3中b4催化剂)和环氧环己烷51.66g,环氧环己烷和催化剂的摩尔比为20000:1),保持聚合反应釜150℃,1.5mpa下聚合2h,得到pchc15.72g。
[0075]
聚合产物核磁结果表明pchc选择性>99%,凝胶色谱结果显示pchc分子量为25473,pdi为1.172。
[0076]
实施例9
[0077]
采用分子筛分别将环氧环己烷(%.wt≥98,水≤2500ppm)的水含量脱除至420ppm,二氧化碳(≥99.99%)水含量脱除至5ppm。将二氧化碳通入100ml聚合反应釜,同时加入非金属催化剂(专利201910764053.3中b4催化剂)和环氧环己烷50.07g,环氧环己烷和催化剂的摩尔比为15000:1),保持聚合反应釜80℃,0.5mpa下聚合6h,得到聚合物溶液,得到pchc为5.80g。
[0078]
聚合产物核磁结果表明pchc选择性>99%,凝胶色谱结果显示pchc分子量为9214,pdi为1.198。