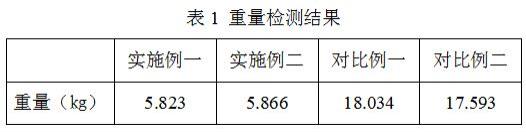
1.本发明属于摩擦材料技术领域,具体涉及一种合成闸瓦及其制备方法。
背景技术:2.随着中国经济的发展,降低能耗,减少排放,提高安全性成为经济发展的主流,目前新造车辆设计之初往往使用合成材料闸瓦,制动参数等调配也与合成材料闸瓦性能相适配。但是我国仍然有数量巨大的在役国外内燃机车车辆,这些机车车辆使用铸铁闸瓦进行制动,由于经济效益等原因,短期内旧型机车车辆无法全部替换成新型机车车辆,基于不改动制动系统、保证行车安全、保护环境、降低旧型机车车辆运维成本等因素考量,由合成材料闸瓦替代铸铁材料闸瓦成为课题。
3.铸铁闸瓦的缺点:1.比重大、不易于搬运或携带,机车乘务员更换闸瓦劳动强度大;2.磨耗大,使用寿命短(约10天左石),更换须繁;3.制动过程中容易对机车基础制动装置造成的危害较大;4.在闸瓦生产过程中容易出现胀箱、表面粘砂、砂眼、气孔及缩孔等质量不良情况;5.铁路运输噪音主要来源是陈的货运车辆,且绝大多数货运列车又都在晚间运行,当货车以80km/h速度运行时,产生的噪音级在远离钢轨75mm处平均在92-94分贝之间。
4.因此,需要一种新的合成闸瓦,可以在不改动旧型机车车辆任何参数的情况下,实现完全替代,并且有效改善铸铁闸瓦比重大、磨耗大、危害大、外观质量不良、噪音大等缺点,有效延长旧型机车使用寿命。
技术实现要素:5.本发明的目的是提供一种合成闸瓦及其制备方法,以解决现有技术中的问题。
6.本发明是通过如下技术方案实现的:一种合成闸瓦,其特征在于:包括瓦背和摩擦体,所述摩擦体包括如下质量百分比的各组分:丁腈橡胶7-11%、橡胶促进剂0.5-1%、橡胶硫化剂0.5-0.9%、防老剂0.5-0.9%、粉状酚醛树脂7-12%、丁腈橡胶粉3-8%、棕刚玉3-6%、鳞片石墨8-15%、硫酸钡6-10%、陶土1-5%、还原铁粉3-7%、硫化亚铁1~3%、煅烧石油焦炭3-6%、硅藻土1-5%、岩棉8-15%、麻纤维7-12%、钛酸钾纤维5-10%、钢纤维3-8%、玻璃纤维2-5%。
7.本发明还公开了一种合成闸瓦的制备方法,其特征在于:首先制备摩擦体,包括如下步骤:s1,丁腈橡胶分两段开炼,第一段辊温40℃-45℃,辊距2mm-3mm,先加生胶,橡胶促进剂,出片停放;第二段辊温50℃-70℃,辊距3mm-4mm,加橡胶硫化剂,割刀混均,加防老剂,待全部混入后以割刀薄通方式混匀;s2,将得到的开炼胶和摩擦体其余组分都加入密炼机加压5-7mpa混合,温度控制在≤150℃,强力混合25-30分钟,倒出原料降温至室温,然后进行造粒即得到混合料待用;其中粒度1-3毫米;
s3,将制得的混合料和钢背投放到模具中进行压制在,压机力为3000n/cm2,保压温度170-180℃,成型时间依据产品厚度1毫米1分钟,得到成型半成品:s4,将制得的半成品在烘箱中采用热风循环电加热热处理24小时,前16小时为升温阶段,直至最高热处理温度达到220℃,后8小时保持热处理温度220℃,让所有原材料充分反应,保证彻底熟透,即制得摩擦体;最后,将摩擦体与瓦背压合,即得合成闸瓦。
8.与现有技术相比,本发明具的优点是:1.本方案所述产品中不含石棉、铅等可能危害人体健康的物质,属于环保型产品;2.摩擦性能可按机车制动需要调整摩擦系数。通过改变、调整配方和工艺的办法可以改变合成闸瓦的摩擦性能,同种工况下合成闸瓦摩擦系数平稳且制动曲线更为集中,更为满足原车设计制动摩擦系数范围;3.合成材料闸瓦比重小,重量为原配套闸瓦1/3左右,易于搬运及运输,更换闸瓦更省力、劳动强度较低的优点,同时减轻车辆自重,降低机车车辆能耗;4.原铸铁闸瓦耐磨性差,使用寿命延长5~6倍,减少更换频次;5.安全性好,制动时无火花通过使用合成闸瓦,可有效避免磨耗铁粉的污损及因制动喷射火星而引起的火灾事故。合成闸瓦制动时没有或很少有磨耗铁粉飞散,从而能防止火灾事故,轻对车辆的不良影响;合成闸瓦在使用过程中无沟槽,对车轮和钢轨的伤害非常轻微,延长了车轮和钢轨的使用寿命;6.如使用合成闸瓦配合表面磨光车轮和有良好减震性能的转向架,使制动更加舒适平稳,使货运所产生的噪音降低20%左右,即相当于当前噪音级的25%,本产品具有明显的降低噪音小作用;7.本发明摩擦体材料组成中采用固体块状胶与胶粉共混使用,在保证粘结组分比重的同时,兼顾不同性态原材料优点。固体块状胶有良好的耐磨性和弹性,胶粉分散性更强,共混使用使其性能更加稳定。固体块状胶弹性高、耐磨性好、耐寒性好,胶粉强度高、分散性好、分子量稳定,硫化后可以很好的固化闸瓦性能;8.本发明摩擦体材料组成使用亚态金属化合物,亚态金属在不同条件下可以发生氧化还原反应,由于原铸铁闸瓦车辆制动时升温大,当温度高,发生还原反应,可以有效吸热,阻止进一步升温,且还原后的组分也是闸瓦常用组分,不会影响产品性能;在环境温度适宜情况又会缓慢氧化,调节制动过热伤车轮的情况。
具体实施方式
9.一种合成闸瓦,包括瓦背和摩擦体,所述摩擦体包括如下质量百分比的各组分:丁腈橡胶7-11%、橡胶促进剂0.5-1%、橡胶硫化剂0.5-0.9%、防老剂0.5-0.9%、粉状酚醛树脂7-12%、丁腈橡胶粉3-8%、棕刚玉3-6%、鳞片石墨8-15%、硫酸钡6-10%、陶土1-5%、还原铁粉3-7%、硫化亚铁1~3%、煅烧石油焦炭3-6%、硅藻土1-5%、岩棉8-15%、麻纤维7-12%、钛酸钾纤维5-10%、钢纤维3-8%、玻璃纤维2-5%。
10.本发明还公开了一种合成闸瓦的制备方法,首先制备摩擦体,包括如下步骤:s1,丁腈橡胶分两段开炼,第一段辊温40℃-45℃,辊距2mm-3mm,先加生胶,橡胶促进剂,出片停放;第二段辊温50℃-70℃,辊距3mm-4mm,加橡胶硫化剂,割刀混均,加防老剂,待全部混入
后以割刀薄通方式混匀;s2,将得到的开炼胶和摩擦体其余组分都加入密炼机加压5-7mpa混合,温度控制在≤150℃,强力混合25-30分钟,倒出原料降温至室温,然后进行造粒即得到混合料待用;其中粒度1-3毫米;s3,将制得的混合料和钢背投放到模具中进行压制在,压机力为3000n/cm2,保压温度170-180℃,成型时间依据产品厚度1毫米1分钟,得到成型半成品:s4,将制得的半成品在烘箱中采用热风循环电加热热处理24小时,前16小时为升温阶段,直至最高热处理温度达到220℃,后8小时保持热处理温度220℃,让所有原材料充分反应,保证彻底熟透,即制得摩擦体;最后,将摩擦体与瓦背压合,即得合成闸瓦。
11.下面通过具体实施例对本发明进一步说明。
12.实施例1本实施例采用的技术方案是合成材料替代铸铁材料的机车用合成闸瓦,其组成包括摩擦体和钢背,所述摩擦体材料包括如下质量百分比的各组分:丁腈橡胶8.5%、橡胶促进剂0.8%、橡胶硫化剂0.6%、防老剂0.6%、酚醛树脂9%、丁腈橡胶粉5%、棕刚玉4%、鳞片石墨10%、硫酸钡8%、陶土3%、还原铁粉5%、硫化亚铁1.5%、煅烧石油焦炭4.5%、硅藻土3%、岩棉11%、麻纤维9%、钛酸钾纤维8%、钢纤维5%、玻璃纤维3.5%。
13.所述合成闸瓦制备方法为:丁睛橡胶分两段开炼,第一段辊温40℃-45℃,辊距2mm-3mm,先加生胶,橡胶促进剂,出片停放;第二段辊温50℃-70℃,辊距3mm-4mm,加橡胶硫化剂,割刀混均,加防老剂,待全部混入后以割刀薄通方式混匀;1)将得到的胶和摩擦体其余组分都加入密炼机加压5-7mpa混合,温度控制在≤150℃,强力混合25-30分钟,排出原料降温至室温,然后进行造粒处理(粒度1-3毫米)得到混合料待用:2)将1)制得的混合料和钢背投放到设计的模具中进行压制,压机压力为3000n/cm2,保压温度170-180℃,成型时间依据产品厚度1毫米1分钟,得到成型半成品:3)将2)制得的半成品在烘箱中采用热风循环电加热热处理24小时,前16小时温度逐渐升高,直至最高热处理温度达到220℃,后8小时保持热处理温度220℃,让所有原材料充分反应,保证彻底熟透,制得合成闸瓦。热处理采用分段热处理的方式,温度逐渐升高,保证闸瓦表面与其内部温度一致,力保合成材料熟成度一致,采用热风循环电加热既能保证热处理的有效进行。
14.实施例2本实施例中,合成闸瓦包括摩擦体和钢背,所述摩擦体材料包括如下质量百分比的各组分:丁腈橡胶8.5%、橡胶促进剂0.8%、橡胶硫化剂0.6%、防老剂0.6%、酚醛树脂9%、丁腈橡胶粉5%、棕刚玉4%、鳞片石墨10%、硫酸钡8%、陶土3%、还原铁粉4%、硫化亚铁2.5%、煅烧石油焦炭4.5%、硅藻土3%、岩棉11%、麻纤维9%、钛酸钾纤维8%、钢纤维5%、玻璃纤维3.5%。
15.所述摩擦体材料制备方法为:丁睛橡胶分两段开炼,第一段辊温40℃-45℃,辊距2mm-3mm,先加生胶,橡胶促进剂,出片停放;第二段辊温50℃-70℃,辊距3mm-4mm,加橡胶硫化剂,割刀混均,加防老剂,待
全部混入后以割刀薄通方式混匀;1)将得到的胶和摩擦体其余组分都加入密炼机加压5-7mpa混合,温度控制在≤150℃,强力混合25-30分钟,排出原料降温至室温,然后进行造粒处理(粒度1-3毫米)得到混合料待用:2)将1)制得的混合料和钢背投放到设计的模具中进行压制在,压机力为3000n/cm2,保压温度170-180℃,成型时间依据产品厚度1毫米1分钟,得到成型半成品:3)将2)制得的半成品在烘箱中采用热风循环电加热热处理24小时,前16小时温度逐渐升高,直至最高热处理温度达到220℃,后8小时保持热处理温度220℃,让所有原材料充分反应,保证彻底熟透,制得合成闸瓦。热处理采用分段热处理的方式,温度逐渐升高,保证闸瓦表面与其内部温度一致,力保合成材料熟成度一致,采用热风循环电加热既能保证热处理的有效进行。
16.对实施例与对比例进行重量检测,其中对比例为外形相同铸铁闸瓦。检测结果见下表,从检测结果可见,合成闸瓦重量大大减轻,约为相同外形铸铁闸瓦1/3,方便更换操作。
17.对实施例合成闸瓦与tb/t3104.1-2020标准中低摩合成闸瓦要求进行对比,其检测值完全符合机车闸瓦行业标准。
18.对实施例一与对比例铸铁闸瓦摩擦性能进行对比(详见表3),同等工况下,实施例一合成闸瓦制动踏面温度低对比例铸铁闸瓦制动踏面温度低,在低速情况下踏面温度降低10~70℃,在整个试验程序中踏面温度降低30℃左右。
19.在空载干燥条件下的一次轻停车制动,实施例合成闸瓦磨耗量约为对比例铸铁闸
瓦磨耗量1/15;在负载干燥条件下的一次轻停车制动,实施例合成闸瓦磨耗量约为对比例铸铁闸瓦磨耗量1/10;在持续制动条件下,实施例一合成闸瓦磨耗量约为对比例铸铁闸瓦磨耗量1/2;在潮湿条件下一次轻停车制动,实施例合成闸瓦磨耗量约为对比例铸铁闸瓦磨耗量1/6,在整个试验程序完成后,实施例合成闸瓦磨耗量约为对比例铸铁闸瓦磨耗量1/2。
20.在整个试验程序中,实施例合成闸瓦平均摩擦系数低于与对比例铸铁闸瓦平均摩擦系数10~40%,更满足低摩闸瓦摩擦系数要求(详见表4)。合成闸瓦摩擦系数更为平稳集中,波动范围小,其各工况下平均摩擦系数极差均小于对比例铸铁闸瓦(详见表4),平稳的摩擦系数,有稳定的刹车距离,提高制动安全性。
21.综上所述,本发明所述产品中不含石棉、铅等可能危害人体健康的物质,属于环保型产品;本发明中摩擦性能可按机车制动需要调整摩擦系数。通过改变、调整配方和工艺的办法可以改变合成闸瓦的摩擦性能,同种工况下合成闸瓦摩擦系数平稳且制动曲线更为集中,更为满足原车设计制动摩擦系数范围;合成材料闸瓦比重小,重量为原配套闸瓦1/3左
右,易于搬运及运输,更换闸瓦更省力、劳动强度较低的优点,同时减轻车辆自重,降低机车车辆能耗;原铸铁闸瓦耐磨性差,使用寿命延长5~6倍,减少更换频次;安全性好,制动时无火花通过使用合成闸瓦,可有效避免磨耗铁粉的污损及因制动喷射火星而引起的火灾事故。合成闸瓦制动时没有或很少有磨耗铁粉飞散,从而能防止火灾事故,轻对车辆的不良影响;合成闸瓦在使用过程中无沟槽,对车轮和钢轨的伤害非常轻微,延长了车轮和钢轨的使用寿命;如使用合成闸瓦配合表面磨光车轮和有良好减震性能的转向架,使制动更加舒适平稳,使货运所产生的噪音降低20%左右,即相当于当前噪音级的25%,本产品具有明显的降低噪音小作用;本发明摩擦体材料组成中采用固体块状胶与胶粉共混使用,在保证粘结组分比重的同时,兼顾不同性态原材料优点。固体块状胶有良好的耐磨性和弹性,胶粉分散性更强,共混使用使其性能更加稳定。固体块状胶弹性高、耐磨性好、耐寒性好,胶粉强度高、分散性好、分子量稳定,硫化后可以很好的固化闸瓦性能;本发明摩擦体材料组成使用亚态金属化合物,亚态金属在不同条件下可以发生氧化还原反应,由于原铸铁闸瓦车辆制动时升温大,当温度高,发生还原反应,可以有效吸热,阻止进一步升温,且还原后的组分也是闸瓦常用组分,不会影响产品性能;在环境温度适宜情况又会缓慢氧化,调节制动过热伤车轮的情况。