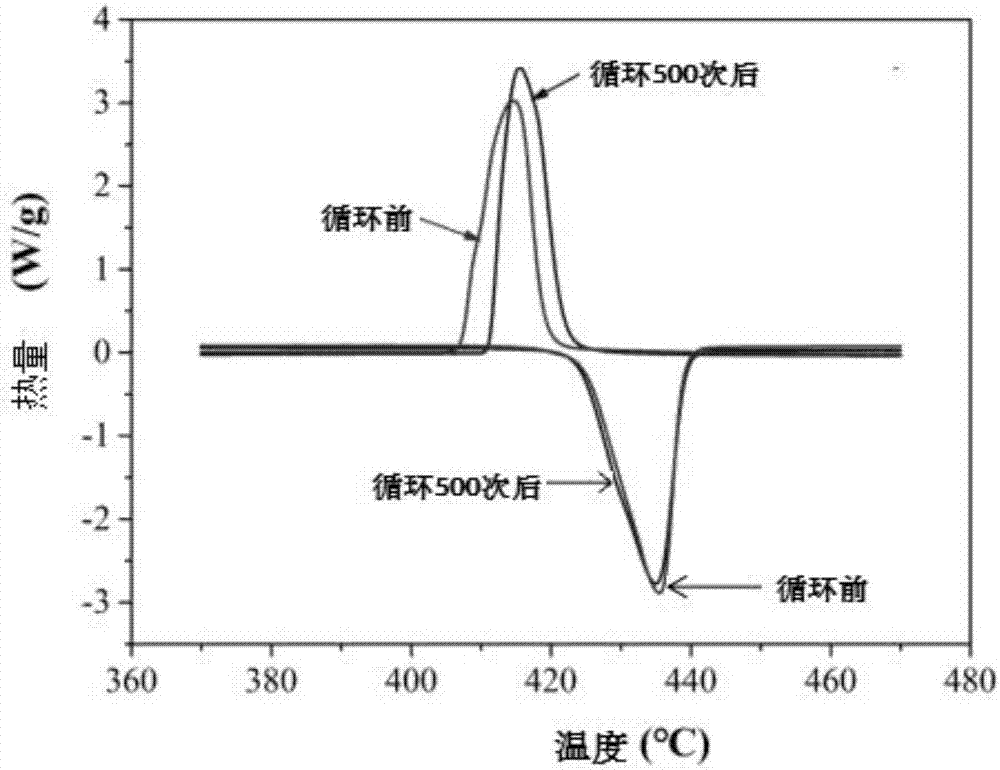
本发明涉及复合相变材料的
技术领域:
,特别涉及一种无机盐-膨胀石墨块体复合相变材料的制备方法。
背景技术:
:无机盐相变材料具有储能密度大、价格低廉、分布广泛等优点,在工业余热废热回收、太阳能热发电等领域具有重要应用。但是无机盐相变材料同时也存在腐蚀性强、导热系数低以及发生固-液相变后的液相流动和泄露问题,从而大大地制约了其性能以及应用。复合相变储热材料不仅可克服单一相变储热材料的缺陷,而且可改善相变材料的应用效果并拓展其应用范围。将无机盐相变材料与多孔载体复合是克服单一相变材料缺点并提高其应用性能简单且重要的途径。膨胀石墨具有大的孔体积和高的导热系数,是制备复合相变材料最常用载体。将无机盐相变材料与膨胀石墨复合,不仅可以提高其导热系数,而且还可以克服相变材料发生固-液相变后的液相流动和泄露问题。现有技术中,通常先把无机盐溶于去离子水中配制成溶液,然后采用蒸发溶液、冷却结晶等方法制备无机盐-膨胀石墨复合相变材料。然而,基于膨胀石墨的复合相变材料堆积密度往往低于0.6g/cm3,这使得基于膨胀石墨的复合相变材料具有较低的单位体积热能存储密度,为了提高体积储热密度,通常将上述方法制备的复合相变材料压制成块。但是,采用这种方法得到的复合相变材料块体体积膨胀率较高,从而会降低预期设计的热导率和体积热能存储密度,限制了工业设计和应用。技术实现要素:有鉴于此,本发明目的在于提供一种无机盐-膨胀石墨块体复合相变材料制备方法,降低无机盐-膨胀石墨块体复合相变材料的体积膨胀率,提高其热稳定性。为了实现上述发明目的,本发明提供以下技术方案:本发明提供了一种无机盐-膨胀石墨块体复合相变材料的制备方法,包括以下步骤:(1)将无机盐和膨胀石墨混合后进行粉碎搅拌,得到混合物;所述粉碎搅拌的转速为15000~20000r/min;(2)将所述混合物和膨胀石墨混合后进行搅拌,得到无机盐-膨胀石墨混合物;所述搅拌的转速为15~30r/min;(3)将所述无机盐-膨胀石墨混合物压块后进行热处理,得到无机盐-膨胀石墨块体复合相变材料。优选的,所述无机盐为碱金属氯化物和碱土金属氯化物中的一种或几种。优选的,所述步骤(1)和步骤(2)中膨胀石墨的总质量和无机盐的质量比为10~20:80~90;优选的,所述步骤(1)中膨胀石墨和步骤(2)中膨胀石墨的质量比为10~30:70~90。优选的,所述步骤(1)中粉碎搅拌的时间为10~30s。优选的,所述步骤(2)中搅拌的时间为1~3min。优选的,所述步骤(3)中压块的压力为10~20MPa;所述压块的时间为3~5min。优选的,所述步骤(3)中热处理的温度为无机盐熔点以上50~100℃;所述热处理的时间为1~3h。本发明提供了一种上述方案所述制备方法制备的无机盐-膨胀石墨块体复合相变材料,包括膨胀石墨块体和吸附在膨胀石墨块体中的无机盐;所述复合相变材料中膨胀石墨的质量分数为10~20%;所述复合相变材料中无机盐的质量分数为80~90%。优选的,所述复合相变材料的体积膨胀率为1.5~3%。本发明提供了一种无机盐-膨胀石墨块体复合相变材料的制备方法,包括以下步骤:(1)将无机盐和膨胀石墨混合后进行粉碎搅拌,得到混合物;所述粉碎搅拌的转速为15000~20000r/min;(2)将所述混合物和膨胀石墨混合后进行搅拌,得到无机盐-膨胀石墨混合物;所述搅拌的转速为15~30r/min;(3)将所述无机盐-膨胀石墨混合物压块后进行热处理,得到无机盐-膨胀石墨块体复合相变材料。本发明提供的方法首先通过高速的粉碎搅拌将无机盐和膨胀石墨粉碎成粒径较小的颗粒,再将所得混合物通过低速搅拌与剩余的膨胀石墨混合,使压块后膨胀石墨和无机盐之间的连接更加牢固,从而使无机盐熔融后能充分吸附到膨胀石墨孔隙中,减少无机盐和膨胀石墨之间的空隙,从而减小复合相变材料的体积膨胀率,提高其热稳定性;并且本发明提供的方法步骤简单、成本低、容易进行工业化生产。本发明一种上述方案所述制备方法制备的无机盐-膨胀石墨块体复合相变材料。实施例表明,采用本发明的制备方法得到的无机盐-膨胀石墨块体复合相变材料体积膨胀率仅为1.5~3%,且热导率高,热稳定性好、潜热量大。附图说明图1为本发明实施例1制备的无机盐-膨胀石墨块体复合相变材料的扫描电子显微镜照片;图2为本发明实施例1制备的无机盐-膨胀石墨块体复合相变材料循环处理500次前后的DSC曲线图;图3为本发明实施例1制备的无机盐-膨胀石墨块体复合相变材料循环处理500次前后的体积对比图。具体实施方式本发明提供了一种无机盐-膨胀石墨块体复合相变材料制备方法,包括以下步骤:(1)将无机盐和膨胀石墨混合后进行粉碎搅拌,得到混合物;所述粉碎搅拌的转速为15000~20000r/min;(2)将所述混合物和膨胀石墨混合后进行搅拌,得到无机盐-膨胀石墨混合物;所述搅拌的转速为15~30r/min;(3)将所述无机盐-膨胀石墨混合物压块后进行热处理,得到无机盐-膨胀石墨块体复合相变材料。本发明将无机盐和膨胀石墨混合后进行粉碎搅拌,得到混合物。在本发明中,所述粉碎搅拌的转速为15000~20000r/min,优选为16000~19000r/min,更优选为17000~18000r/min,最优选为17500r/min;所述粉碎搅拌的时间优选为10~30s,更优选为15~25s,最优选为18~22s;本发明对粉碎搅拌使用的仪器没有特殊要求,使用本领域的常规仪器即可;本发明优选使用高速粉碎机进行粉碎搅拌。在本发明中,所述膨胀石墨的粒径优选为50~150目,更优选为80~120目,最优选为90~110目;所述无机盐优选为碱金属氯化物和碱土金属氯化物中的一种或几种的混合物,更优选为氯化钠、氯化钾、氯化镁和氯化钙中的一种或几种的混合物,所述混合物优选为2~3种无机盐的混合物。本发明首先将无机盐和膨胀石墨进行高速的粉碎混合,在高速的搅拌作用下无机盐和膨胀石墨发生粉碎,得到粒径更小的颗粒,从而使无机盐和膨胀石墨充分混合均匀;在本发明中,所述粉碎搅拌后所得混合物的粒径约为100~200目。本发明将所述混合物和膨胀石墨混合后进行搅拌,得到无机盐-膨胀石墨混合物。在本发明中,所述搅拌的转速为15~30r/min,优选为18~25r/min,更优选为20~22r/min;所述搅拌的时间优选为1~3min,更优选为1.5~2.5min,最优选为2min。本发明对步骤(2)中搅拌的方式没有特殊要求,使用本领域技术人员熟知的搅拌方法即可,具体的为机械搅拌;在本发明的具体实施例中,可以使用机械搅拌器进行搅拌。在本发明中,所述步骤(2)中膨胀石墨的粒径和步骤(1)中膨胀石墨粒径相同,在此不再赘述;所述步骤(1)和步骤(2)中膨胀石墨的总质量和无机盐的质量比优选为10~20:80~90,更优选为13~18:82~87,最优选为15:85;所述步骤(1)中膨胀石墨和步骤(2)中膨胀石墨的质量比优选为10~30:70~90,更优选为15~25:75~85,最优选为20:80。本发明对膨胀石墨的来源没有特殊要求,使用市场上购买的商品或自行制备均可。在本发明中,所述膨胀石墨优选通过可膨胀石墨微波膨化制备得到;所述微波膨化的功率优选为800~1000W,更优选为850~950W,最优选为900W;所述微波膨化的时间优选为10~30s,更优选为15~25s,最优选为20s。本发明通过低速混合将上述混合物和膨胀石墨混合,低速搅拌过程不会降低膨胀石墨的热导率,从而保证了复合相变材料具有较高的导热系数;本发明通过分步搅拌混合的方式使无机盐在膨胀石墨中分布的更加均匀,后续的压块过程中膨胀石墨的结构不易被损坏,压块后无机盐和膨胀石墨之间连接更加紧密,又保证了复合相变材料具有较高的热导率。得到无机盐-膨胀石墨混合物后,本发明将所述无机盐-膨胀石墨混合物压块,得到无机盐-膨胀石墨块体。在本发明中,所述压块的压力优选为10~20MPa,更优选为12~18MPa,最优选为13~15MPa;所述压块的时间优选为3~5min,更优选为3.5~4.5min,最优选为4min;所述无机盐-膨胀石墨块体的密度优选为1000~1500kg/m3,更优选为1100~1400kg/m3,最优选为1200~1300kg/m3。本发明对压块的形状尺寸没有特殊要求,在本发明的具体实施例中,可以根据实际需求确定形状及尺寸。本发明对压块使用的装置没有特殊限制,使用本领域技术人员熟知的装置进行压块即可,具体的如压块机;在本发明的具体实施例中,可以将无机盐-膨胀石墨混合物加入压块模具中,再使用压块机进行压块处理。得到无机盐-膨胀石墨块体后,本发明将所述无机盐-膨胀石墨块体进行热处理,得到无机盐-膨胀石墨块体复合相变材料。在本发明中,所述热处理的温度优选为无机盐熔点以上50~100℃,更优选为无机盐熔点以上60~90℃,最优选为无机盐熔点以上70~80℃;所述热处理的时间优选为1~3h,更优选为1.5~2.5h,最优选为2h;升温至所述热处理温度的升温速率优选为5~10℃/min,更优选为6~8℃/min,最优选为7℃/min;本发明的热处理时间自升温至热处理所需温度时开始计算。所述热处理后,本发明优选将热处理所得样品自然冷却至室温。本发明通过先压块后进行热处理的方法,使熔融后的无机盐能够充分吸附到膨胀石墨的孔隙中,减少膨胀石墨和无机盐之间的空隙,从而降低复合相变材料的体积膨胀率。本发明提供了一种上述方案所述制备方法制备的无机盐-膨胀石墨块体复合相变材料,包括膨胀石墨块体和吸附在膨胀石墨块体中的无机盐。在本发明中,所述复合相变材料中膨胀石墨的质量分数为10~20%,优选为13~18%,更优选为15~16%;所述复合相变材料中无机盐的质量分数为80~90%,优选为82~88%,更优选为85~86%;所述复合相变材料的体积膨胀率优选为1.5~3%,更优选为1.6~2.5%。下面结合实施例对本发明提供的无机盐-膨胀石墨块体复合相变材料的制备方法进行详细的说明,但是不能把它们理解为对本发明保护范围的限定。实施例1将2.9g氯化镁粉体、5.1g氯化钾粉体和0.4g目数为150目的膨胀石墨颗粒(使用可膨化石墨经800W微波炉膨化30s后得到)加入15000r/min的高速粉碎机中,然后进行高速粉碎式搅拌30s,形成均匀的混合物;将得到的混合物与1.6g目数为150目的膨胀石墨颗粒进行低速的机械搅拌,转速为30r/min,搅拌时间为1min,得到无机盐-膨胀石墨混合物;将无机盐-膨胀石墨混合物加入到压块模具中,使用压块机进行压块处理,其中,压块压力为20MPa,保压时间为5min,压块密度为1500kg/m3;将得到的块体放入500℃的加热炉(升温速率为5℃/min)中加热处理1h,得到无机盐-膨胀石墨块体复合相变材料。所得无机盐-膨胀石墨块体复合相变材料中无机盐质量分数为80%;经检测,所得相变材料的相变温度为424.1℃,相变潜热152.7J/g,热导率为5.42W/m.K;使用扫描电子显微镜对所得复合相变材料进行观测,所得结果如图1所示,图1为所得无机盐-膨胀石墨块体复合相变材料的扫描电子显微镜照片;根据图1可以看出,无机盐相变材料充分的吸附在膨胀石墨的孔隙中,二者连接紧密;对所得复合相变材料的体积膨胀率进行检测,测试方法为:测量复合相变材料的初始体积,记为V1,将复合相变材料加热至相变温度以上,冷却到室温后测量其体积,记为V2,(V2-V1)/V1即为复合相变材料的体积膨胀率;经检测,所得复合相变材料的体积膨胀率为2.96%;热稳定性测试:将所得复合相变材料升温至相变温度以上,然后冷却至室温,循环处理500次,使用差示扫描热量法绘制处理前后的复合相变材料的DSC曲线,所得结果如图2所示,图2为无机盐-膨胀石墨块体复合相变材料循环处理500次前后的DSC曲线图;根据DSC曲线计算得到复合相变材料循环处理500次前后相变温度和相变焓的对比数据,所得结果见表1;根据图2和表1可以看出,循环处理500次后的复合相变材料的DSC曲线的变化不大,发生相变时的温度和相变焓也非常接近,说明得到的复合相变材料具有优良的热稳定性;表1无机盐-膨胀石墨块体复合相变材料循环处理500次前后相变温度和相变焓数据对比项目熔化温度(℃)熔化焓值(J/g)凝固温度(℃)凝固焓值(J/g)循环处理前424.14161.37418.39160.28循环500次后424.42161.29422.37161.54对上述循环处理500次后的复合相变材料的体积膨胀率进行检测,可得其相对于循环处理前的体积膨胀率为2.98%;循环处理500次前后的复合相变材料的体积对比图如图3所示,图3为所得无机盐-膨胀石墨块体复合相变材料循环处理500次前后的体积对比图;根据图3可以看出,循环处理500次前后所得复合相变材料的体积没有明显变化。实施例2将3g氯化镁粉体、5.5g氯化钾粉体和0.4g目数为100目的膨胀石墨颗粒加入18000r/min的高速粉碎机中,高速粉碎式搅拌20s,形成均匀的混合物;将得到的混合物与1.1g目数为100目的膨胀石墨颗粒进行低速的机械搅拌,转速为20r/min,搅拌2min,形成无机盐-膨胀石墨混合物;将无机盐-膨胀石墨混合物使用压块机进行压块处理,其中,压块压力为15MPa,保压时间为4min,所得块体密度为1200kg/m3;将得到的块体放入500℃的加热炉(升温速率为8℃/min)中加热处理2h,得到无机盐-膨胀石墨块体复合相变材料。所得无机盐/膨胀石墨块体块体复合相变材料中无机盐质量分数为85%;经检测,所得复合相变材料的相变温度为424.1℃,相变潜热162.3J/g,热导率为4.26W/m.K;使用扫描电子显微镜对所得复合相变材料进行观测,所得结果和实施例1相似;按照实施例1所述的方法对所得复合相变材料的热稳定性进行测试,可得该复合相变材料具有优良的热稳定性;按照实施例1所述的方法对所得复合相变材料的体积膨胀率进行测试,可得体积膨胀率为2.16%;按照实施例1的方法对循环处理500次后的复合相变材料的体积膨胀率进行计算,可得其相对于循环处理前的复合相变材料的体积膨胀率为2.37%。实施例3将3.2g氯化镁粉体、5.8g氯化钾粉体和0.3g经目数为50目膨胀石墨颗粒加入20000r/min的高速粉碎机中,然后进行高速粉碎式搅拌10s,形成均匀的混合物;将得到的混合物与0.7g目数为50目膨胀石墨颗粒进行低速的机械搅拌,转速为15r/min,搅拌3min,得到无机盐和膨胀石墨混合物;将无机盐和膨胀石墨混合物使用压块机进行压块处理,其中,压块压力为10MPa,保压时间为3min,所得块体密度为1000kg/m3;将得到的块体放入500℃的加热炉(升温速率为10℃/min)中加热处理3h,得到无机盐-膨胀石墨块体复合相变材料。所得无机盐-膨胀石墨块体复合相变材料中无机盐质量分数为90%,经检测,所得复合相变材料的相变温度为424.1℃,相变潜热171.8J/g,体积膨胀率为1.52%,热导率为3.69W/m.K;按照实施例1所述的方法对所得复合相变材料的热稳定性进行测试,可得该复合相变材料具有优良的热稳定性;按照实施例1所述的方法对所得复合相变材料的体积膨胀率进行测试,可得体积膨胀率为1.52%;按照实施例1的方法对循环处理500次后的复合相变材料的体积膨胀率进行计算,可得其相对于循环处理前的复合相变材料的体积膨胀率为1.78%。实施例4将8g氯化镁粉体和0.4g目数为150目的膨胀石墨颗粒加入15000r/min的高速粉碎机中,然后进行高速粉碎式搅拌30s,形成均匀的混合物;将得到的混合物与1.6g目数为150目的膨胀石墨颗粒进行低速的机械搅拌,转速为30r/min,搅拌时间为1min,得到无机盐-膨胀石墨混合物;将无机盐-膨胀石墨混合物加入到压块模具中,使用压块机进行压块处理,其中,压块压力为20MPa,保压时间为5min,压块密度为1500kg/m3;将得到的块体放入800℃的加热炉(升温速率为5℃/min)中加热处理1h,得到无机盐-膨胀石墨块体复合相变材料。所得无机盐-膨胀石墨块体复合相变材料中无机盐质量分数为80%;经检测,所得复合相变材料的相变温度为712.8℃,相变潜热362.1J/g,热导率为5.68W/m.K;按照实施例1所述的方法对所得复合相变材料的热稳定性进行测试,可得该复合相变材料具有优良的热稳定性;按照实施例1所述的方法对所得复合相变材料的体积膨胀率进行测试,可得体积膨胀率为2.86%;按照实施例1的方法对循环处理500次后的复合相变材料的体积膨胀率进行计算,可得其相对于循环处理前的复合相变材料的体积膨胀率为2.91%。实施例5将8.5g氯化镁粉体和0.4g目数为100目的膨胀石墨颗粒加入18000r/min的高速粉碎机中,高速粉碎式搅拌20s,形成均匀的混合物;将得到的混合物与1.1g目数为100目的膨胀石墨颗粒进行低速的机械搅拌,转速为20r/min,搅拌2min,形成无机盐-膨胀石墨混合物;将无机盐-膨胀石墨混合物使用压块机进行压块处理,其中,压块压力为15MPa,保压时间为4min,所得块体密度为1200kg/m3;将得到的块体放入800℃的加热炉(升温速率为8℃/min)中加热处理2h,得到无机盐-膨胀石墨块体复合相变材料。所得无机盐-膨胀石墨块体复合相变材料中无机盐质量分数为85%;经检测,所得复合相变材料的相变温度为712.8℃,相变潜热384.7J/g,体积膨胀率为2.16%,热导率为4.12W/m.K。按照实施例1所述的方法对所得复合相变材料的热稳定性进行测试,可得该复合相变材料具有优良的热稳定性;按照实施例1所述的方法对所得复合相变材料的体积膨胀率进行测试,可得体积膨胀率为2.07%;按照实施例1的方法对循环处理500次后的复合相变材料的体积膨胀率进行计算,可得其相对于循环处理前的复合相变材料的体积膨胀率为2.28%。实施例6将3.4g氯化镁粉体、1.8g氯化钙粉体、3.8g氯化钠粉体和0.3g经目数为50目膨胀石墨颗粒加入20000r/min的高速粉碎机中,然后进行高速粉碎式搅拌10s,形成均匀的混合物;将得到的混合物与0.7g目数为50目膨胀石墨颗粒进行低速的机械搅拌,转速为15r/min,搅拌3min,得到无机盐和膨胀石墨混合物;将无机盐和膨胀石墨混合物使用压块机进行压块处理,其中,压块压力为10MPa,保压时间为3min,所得块体密度为1000kg/m3;将得到的块体放入500℃的加热炉(升温速率为10℃/min)中加热处理3h,得到无机盐-膨胀石墨块体复合相变材料。所得无机盐-膨胀石墨块体复合相变材料中无机盐质量分数为90%;经检测,所得复合相变材料的相变温度为446.5℃,相变潜热181.5J/g,热导率为3.53W/m.K;按照实施例1所述的方法对所得复合相变材料的热稳定性进行测试,可得该复合相变材料具有优良的热稳定性;按照实施例1所述的方法对所得复合相变材料的体积膨胀率进行测试,可得体积膨胀率为1.65%;按照实施例1的方法对循环处理500次后的复合相变材料的体积膨胀率进行计算,可得其相对于循环处理前的复合相变材料的体积膨胀率为1.79%。由以上实施例可知,本发明提供的制备方法步骤简单,容易操作,且制备得到的无机盐-膨胀石墨块体复合相变材料体积膨胀率低、热稳定性好,潜热高。由以上实施例可知,本发明以上所述仅是本发明的优选实施方式,应当指出,对于本
技术领域:
的普通技术人员来说,在不脱离本发明原理的前提下,还可以做出若干改进和润饰,这些改进和润饰也应视为本发明的保护范围。当前第1页1 2 3