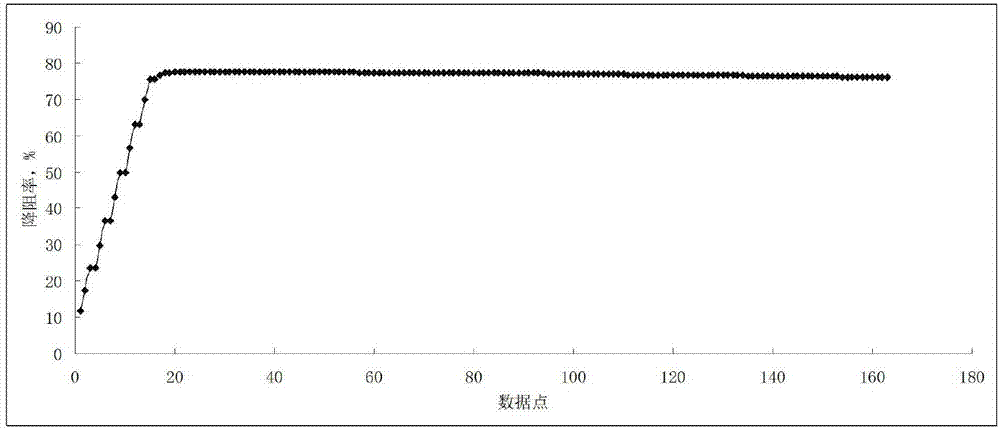
本发明属于油气井储层改造
技术领域:
,具体涉及一种页岩气压裂用多功能清洁减阻剂及其制备方法。
背景技术:
:页岩气是一种优质、高效、清洁的低碳能源。我国页岩油气储量约为26×1012m3,约占全球页岩气储量的5.7%。因此,加大页岩气资源的勘探和开发,有利于改变我国油气资源格局,缓解油气资源短缺。页岩储层具有低孔、低渗的特点,储层渗透率一般小于0.01×10-3μm2,泥质含量较高,一般为20-70%,勘探开发难度大,大多数页岩气井需储层改造才能获得较理想的产量。目前,国内外主要利用减阻水压裂液进行体积改造。减阻水压裂液体系是针对页岩气储层改造而发展的一种压裂液体系,该体系主要成分是水,及很少量的减阻剂、黏土稳定剂和表面活性剂,与常规冻胶压裂相比,易产生复杂的裂缝孔隙,可实现较大的压裂增产改造,经济成本低且易返排、对储层损害小,在多个地区成功应用。页岩气用压裂液的研究已取得一定进展,显示出较好的发展前景和潜力,但还处于起步和发展的阶段。滑溜水压裂液还存在着一系列的问题,比如:添加剂使用较多,现场使用繁琐;对返排性能差,储层伤害严重等问题。有的井压裂后油气井的日产量大大低于预期,而压裂液选择不当造成的储层伤害可能是产生这一现象的关键因素。根据现场需求,特别是开发成本和环保,要求压裂返排水100%回用,开发高矿化度下降阻性能优异、对地层伤害低、符合现场压裂施工要求、多功能的“环保绿色”减阻剂是未来研究的重点。技术实现要素:本发明的一个目的是解决至少上述问题和/或缺陷,并提供至少后面将说明的优点。本发明还有一个目的是解决现有的常规滑溜水需要添加减阻剂、杀菌剂、防膨剂、助排剂等多种药剂而造成的现场配液操作复杂、工作量大、成本高等技术问题。本发明还有一个目的是提供一种页岩气压裂用多功能清洁减阻剂的制备方法,其工艺步骤简单,易于工业化生产。为了实现本发明这些目的和其它优点,本发明提供了一种页岩气压裂用多功能清洁减阻剂,该减阻剂由内相和外相在引发剂作用下引发聚合反应制成;所述外相由碳酸甘油酯和烯丙基聚氧乙烯醚组成;所述内相由(2-丙烯酰氧基)乙氧基苄基三乙基氯化铵、N-乙烯基吡咯烷酮、有机盐和水组成。优选的是,所述减阻剂的各原料组分的质量百分比为:碳酸甘油酯8-12%、烯丙基聚氧乙烯醚6-10%、(2-丙烯酰氧基)乙氧基苄基三乙基氯化铵10-15%、N-乙烯基吡咯烷酮5-8%、有机盐15-20%、水40-52%、引发剂0.01%-0.1%。优选的是,所述烯丙基聚氧乙烯醚结构通式为CH2=CHCH2O(CH2CH2O)mH,其中m为4、6、8、10、12、14、16、18、20其中的一种。优选的是,所述有机盐为甲酸盐、乙酸盐、草酸盐、柠檬酸盐中的一种。优选的是,所述甲酸盐为甲酸钠、甲酸钾或甲酸铵。优选的是,所述引发剂为过硫酸盐或亚硫酸氢钠或两者的混合物。优选的是,所述过硫酸盐为过硫酸铵。一种制备上述的页岩气压裂用多功能清洁减阻剂的方法,其包括如下步骤:S1、配制外相:将碳酸甘油酯、烯丙基聚氧乙烯醚按比例混合并搅拌均匀,得到外相,备用;S2、配制内相:将水、(2-丙烯酰氧基)乙氧基苄基三乙基氯化铵、N-乙烯基吡咯烷酮以及有机盐,按比例混合并搅拌均匀,得到内相,备用;S3、聚合反应:将配制的外相转移至反应容器中,搅拌,再加入配制的内相溶液,得到乳液基液;同时通氮气搅拌除去氧气,搅拌20-40min后,再滴加入引发剂,然后将反应容器密闭,聚合反应数小时,得到目标物减阻剂。进一步优选的是,步骤S3具体为:将配制的外相转移至反应容器中,搅拌,再将反应容器置于20-25℃的恒温水浴中,然后缓慢加入配制的内相溶液,得到乳液基液;通氮气高速搅拌除去氧气,搅拌20-40min后,再滴加入引发剂,然后将反应容器密闭,聚合反应12h,得到目标物减阻剂。本发明的有益之处在于:其一、本发明的减阻剂集降阻、杀菌、防膨、助排等多种功能于一体,解决了常规滑溜水需要添加减阻剂、杀菌剂、防膨剂、助排剂等多种药剂而造成的现场配液操作复杂、工作量大、成本高等诸多问题;降低压裂的施工费用,避免压裂液残渣对支撑裂缝的伤害,提高压裂井的增产功效,减少现场施工工作量,可在页岩气和其他低渗透致密油气藏的开发中推广应用。其二、采用该减阻剂配制的滑溜水,可有效降低摩阻,携砂性能优异,防膨及助排效果良好,并且对水质要求低,其返排液可以重复利用,提高了压裂用水利用率,降阻增效明显,可广泛应用于页岩气大排量大规模压裂施工;且该减阻剂中不含矿物油,也不含有害物质,清洁环保。附图说明图1、0.08%减阻剂减阻率随时间变化曲线。图2、0.1%减阻剂减阻率随时间变化曲线。图3、0.12%减阻剂减阻率随时间变化曲线。图4、4井第18段压裂施工曲线。具体实施方式以下结合附图对本发明的优选实施例进行说明,应当理解,此处所描述的优选实施例仅用于说明和解释本发明,并不用于限定本发明。一、制备减阻剂的实施例实施例1制备压裂用多功能清洁减阻剂1000g的具体操作步骤如下:S1、外相配制:将80g碳酸甘油酯和100g烯丙基聚氧乙烯醚(结构式CH2=CHCH2O(CH2CH2O)4H)混合并搅拌均匀,备用。S2、内相配制:将100g(2-丙烯酰氧基)乙氧基苄基三乙基氯化铵、50gN-乙烯基吡咯烷酮、150g甲酸钾,加入519.98g水中混合并搅拌溶解均匀,备用。S3、乳液聚合:将配制好的外相倒入反应容器中,再将反应容器置于20-25℃的恒温水浴中,开启搅拌器,将配制好的内相溶液缓慢加入到外相中,配成乳液基液。同时通氮气高速搅拌除氧,搅拌20min-40min后,再将引发剂0.01g过硫酸铵及0.01g亚硫酸氢钠加入反应容器中,并将反应容器密闭,反应12h,得到所需的减阻剂。实施例2制备压裂用多功能清洁减阻剂1000g的具体操作步骤如下:S1、外相配制:将120g碳酸甘油酯和60g烯丙基聚氧乙烯醚(结构式CH2=CHCH2O(CH2CH2O)20H)混合并搅拌均匀,备用。S2、内相配制:将140g(2-丙烯酰氧基)乙氧基苄基三乙基氯化铵、79.9gN-乙烯基吡咯烷酮、200g乙酸钠,加入400g水中混合并搅拌溶解均匀,备用。S3、乳液聚合:将配制好的外相倒入反应容器中,再将反应容器置于20-25℃的恒温水浴中,开启搅拌器,将配制好的内相溶液缓慢加入到外相中,配成乳液基液。同时通氮气高速搅拌除氧,搅拌20min-40min后,再将引发剂0.1g过硫酸铵加入反应容器中,并将反应容器密闭,反应12h,得到所需的减阻剂。实施例3制备压裂用多功能清洁减阻剂1000g的具体操作步骤如下:S1、外相配制:将100g碳酸甘油酯和80g烯丙基聚氧乙烯醚(结构式CH2=CHCH2O(CH2CH2O)12H)混合并搅拌均匀,备用。S2、内相配制:将120g(2-丙烯酰氧基)乙氧基苄基三乙基氯化铵、59.95gN-乙烯基吡咯烷酮、180g柠檬酸钠,加入460g水中混合并搅拌溶解均匀,备用。S3、乳液聚合:将配制好的外相倒入反应容器中,再将反应容器置于20-25℃的恒温水浴中,开启搅拌器,将配制好的内相溶液缓慢加入到外相中,配成乳液基液。同时通氮气高速搅拌除氧,搅拌20min-40min后,再将引发剂0.05g亚硫酸氢钠加入反应容器中,并将反应容器密闭,反应12h,得到所需的减阻剂。二、性能测试对上述实施例1制备的减阻剂样品进行性能测试。(1)稳定性测试:将减阻剂样品倒入样品瓶中,室温下放置不同时间观察样品本身的稳定性,结果如表1所示。表1.样品稳定性实验放置时间实验现象1天均匀乳白色液体1周均匀乳白色液体2周均匀乳白色液体3周均匀乳白色液体4周均匀乳白色液体(2)降阻率测试:分别配置质量百分数为0.08%、0.1%和0.12%的减阻剂水溶液。测试各溶液的减阻率随时间变化情况,结果见图1、图2和图3。可以看出,该减阻剂的降阻率在76-77%之间,且随着减阻剂用量增加,其降阻率无明显变化。(3)表面张力测试依据SY/T5370-1999《表面及界面张力测定方法》测定。为了减少压裂液在地层的停留时间,防止压裂液在地层中滞留产生储层伤害,需降低压裂液的表面张力,促进返排。因此,在降阻水压裂液中优化添加助排剂。在常压0.1MPa、温度20℃下测得降阻水的表面张力仅为24.1mN/m,具有很好的表面活性,能够避免地层水锁现象,有利于压裂液有效返排。(4)水化分散性CST测试针对页岩气气储层物性情况,压裂液中的水分子进入地层,会使储集层黏土矿物膨胀、分散和运移,堵塞油气通道,降低油气产量。为使储层得到最大程度上的保护,需减阻水压裂液具有良好的防膨性能,防止黏土矿物膨胀、脱落、运移,堵塞孔道。将减阻剂配置成质量百分数0.1%的减阻液,该减阻液与质量百分数2%的KCl溶液进行防膨效果评价,以评价减阻液体系防膨性能。测试结果见表2,从中可看出,减阻液CST值小于同条件下2%KCl溶液,则说明减阻液水化分散程度小,具有较好防膨性能。表2.CST测定结果备注:上表中,CST值越大,水化分散程度越大,M、B值为线性回归参数,M值反应CST值随剪切速率变化趋势,B值反应瞬时破裂下来的数值。(5)杀菌率测试将腐生菌培养基于(121±1)℃在蒸汽压力灭菌器灭菌15min,冷却至(45±1)℃,灌入培养皿内。将无菌采样瓶采集的水样按不同稀释度分别接种到无菌培养皿中,每个稀释度重复接种5个皿,每皿接种1mL。彻底混合、固化后,倒置平皿,在生化培养箱中(29±1)℃培养24h。培养之后,选择平均菌落数在30-300之间的稀释度,立即进行计数。试验结果:分别测定新鲜水和加减阻剂剂后的水中总细菌个数,按下式计算杀菌率:式中:K1—加减阻剂后水中细菌数;K0—新鲜水中细菌数。测定结果见表3。可以产出,在减阻剂浓度较小(0.05%)时,减阻剂的杀菌率依然较好;且随着减阻剂浓度增加,杀菌率也提高;减阻剂浓度增加至0.2%时,杀菌率提高至99%以上,几乎能够杀灭全部的细菌。因此,该减阻剂表现出显著的杀菌效果。表3杀菌率测试结果序号减阻剂浓度,%杀菌率,%10.0571.220.0887.330.195.640.1598.150.299.2三、施工应用实施例将实施例1制备的多功能清洁减阻剂实际应用于某平台4、5井上。某平台4井完钻井深4830m,完钻层位龙马溪组,采用139.7mm套管完井,水平段长1500m,本井设计压裂23段;5井完钻井深4740m,完钻层位龙马溪组,采用139.7mm套管完井,水平段长1441m,本井设计压裂21段。两口井均采用大通径桥塞作为分段工具,采用绿色清洁滑溜水体系,支撑剂采用70/140目石英砂和40/70目陶粒组合、设计施工排量13.5m3/min以上,控制施工压力95MPa以下,采用段塞式加砂模式,单段液量设计1800-2000m3,单段砂量80-120t;第一段注酸20m3,现场准备一定量的酸液,后续压裂段根据施工情况决定酸液使用量。采用每段分3簇射孔,每簇射孔段长1m,孔密16孔/m,相位角为60°,单段总孔数48孔。第一段采用连续油管传输射孔,后续段采用电缆泵送桥塞射孔,针对含宝塔组改造井段采用定向射孔工艺。该平台4、5井于2017年9月21日开始主压裂施工,至2017年11月4日,共完成4井23段、5井21段全部施工。4井共计配制并应用绿色清洁滑溜水44845方,5井共计配制并应用绿色清洁滑溜水41449方。图4为4井第18段压裂施工曲线。实施效果总结如下:(1)多功能清洁滑溜水配方简化,添加剂直接在混砂车上计量添加,无需混配,无需中间罐,操作简单,节省人力,降低成本;(2)多功能清洁滑溜水施工稳定,施工过程中施工排量在12-14m3/min,施工压力在62-72MPa,达到设计要求;(3)多功能清洁滑溜水降阻效果优异,施工过程中平均减阻率达到74.5%,优于常规油基乳液滑溜水;(4)多功能清洁滑溜水携砂效果良好,施工过程中单段平均加砂达到100吨以上;(5)多功能清洁滑溜水返排效果良好,平均返排率为20%,返排液重复利用,减阻率达到75.2%,与清水相当。综上所述,本发明的减阻剂集降阻、杀菌、防膨、助排等多种功能于一体,解决了常规滑溜水需要添加减阻剂、杀菌剂、防膨剂、助排剂等多种药剂而造成的现场配液操作复杂、工作量大、成本高等诸多问题。以上所述,仅是本发明的较佳实施例而已,并非对本发明作任何形式上的限制,虽然本发明已以较佳实施例揭露如上,然而并非用以限定本发明,任何熟悉本专业的技术人员,在不脱离本发明技术方案范围内,当可利用上述揭示的技术内容作出些许更动或修饰为等同变化的等效实施例,但凡是未脱离本发明技术方案的内容,依据本发明的技术实质对以上实施例所作的任何简单修改、等同变化与修饰,均仍属于本发明技术方案的范围内。当前第1页1 2 3