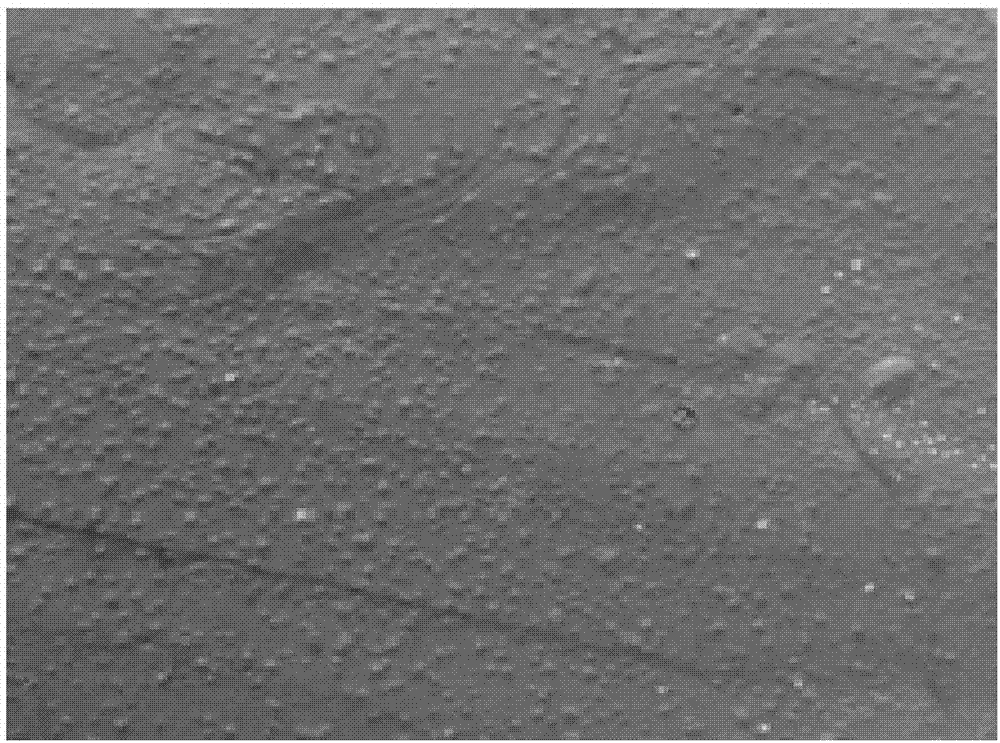
本发明属于涂料领域,涉及一种富锌防腐涂料及其制备方法与应用,尤其涉及一种含有石墨烯的环氧富锌涂料及其制备方法与应用。
背景技术:
富锌涂料分为有机富锌涂料和无机富锌涂料。有机富锌涂料常用环氧树脂、氯化橡胶、乙烯基树脂和聚氨酯树脂为成膜基料。最为常用的是环氧富锌涂料,其中聚酰胺固化环氧富锌底漆是有机富锌底漆中应用最大的品种。有机富锌涂料的有机成膜物的导电性能差,必须增加锌粉含量以保证导电性。美国钢结构涂装协会sspcpaint-20中规定有机富锌涂料锌粉占干膜质量不少于77%,无机富锌涂料锌粉占干膜质量不少于74%,此规定就是为了增加涂膜导电性的。此外,有机树脂的粘结性优于无机树脂,这样也为高含量锌粉附着提供了更好的保证。有机型防锈性能比无机稍差,导电性、耐热性、耐溶剂性不如无机型的,但施工性能好,对钢材表面的处理质量容忍度较大。同时环氧富锌底漆与大多数涂料可以兼容,且配套涂层之间有着协同作用,使配套涂层的寿命较单独使用时提高1.5~2.4倍。冷涂锌涂料是近年来新出现的一个涂料品种,主要是代替热镀锌或者说是在热镀锌施工较困难的情况下,可以使用。是由锌粉、有机树脂和溶剂组成。因此应该划分为有机富锌涂料中。此涂料的特点是锌粉含量高,来达到良好的防腐蚀效果。无机富锌涂料有溶剂型和水性两类。溶剂型无机富锌涂料是以正硅酸乙酯为基料,因为正硅酸乙酯可以溶于有机溶剂,喷涂后,在溶剂挥发的同时正硅酸乙酯中的烷氧基吸收空气中水分并发生水解反应,交联固化成高分子硅氧烷聚合物。也就是硅酸乙酯水解缩聚,形成网状高聚物涂膜的过程。水性无机富锌涂料是由水性无机硅酸盐(纳、钾、锂)树脂、锌粉、助剂组成的双组分涂料。现在也开发出磷酸盐类的富锌涂料,水性无机富锌涂料的发展已经有50多年的历史了,该产品最早是由美国航空航天总署(nasa)研发出来的,作为太平洋小岛的卫星接收站的防锈用。水性无机富锌涂料分为后固化型和自固化型两种,后固化型无机富锌涂料漆膜干燥后,需要加热或者涂上酸性固化剂(稀磷酸或者mgcl2水溶液),施工较为复杂,漆膜较脆。目前市场上广泛应用的是水性自固化无机富锌涂料。cn108192470a公开了一种富锌防腐蚀涂料,所述的富锌防腐蚀涂料主要由质量比为3.5-6:1的a组分和b组分混合而成,其中,所述的a组分按照质量分数计包括以下组分:无机纳米锌粉100份、双酚s环氧树脂45-75份、气相法白炭黑20-35份、酚醛环氧树脂10-25份、氢化双酚a型环氧树脂15-20份、四溴双酚a树脂5-10份、邻苯二甲酸双缩水甘油酯6-15份以及流平剂0.5-1.5份;所述的b组分按照质量分数计包括以下组分:氨烃基硅油50-65份、聚苯胺15-25份、石墨烯微片5-10份、含硼聚硅烷5-8份、消泡剂1-3份以及润湿分散剂3-5份。本此方法得到的富锌防腐蚀涂料:(1)增强涂料中聚合物的导电性能;(2)防腐蚀性能优异;(3)涂层物理性能好。但是经过测试,其防腐蚀性能并不能满足实际需求,无法达到最理想的效果,并且成分复杂,不易于制备。cn107987666a公开了一种富锌重防腐粉末涂料,它包括下述重量份组成的原料:环氧树脂20-35份,聚酯树脂20-35份,固化剂3-5份,钛白粉0-35份,硫酸钡0-40份,丙烯酸流平剂0.8-1.5份,丙烯酸润湿剂0.4-2.5份,苯偶姻0-1.8份,硬脂酸0-1.2份,消光剂0-5份,聚乙烯蜡0-1份,聚酰胺蜡0-1份,消泡剂0-1份,聚四氟乙烯蜡0-1份,电荷调节剂0-1份,有机膨润土0-1份,催化剂0-2份,锌粉5-40份。此方法制备的涂料的具有耐化学品性能和储存稳定性,优异的机械性能和流平性能以及极强的耐盐雾性能,适用于恶劣盐雾环境,用作防腐底漆,广泛适用于实验设备、汽车配件、铁管、钢瓶等的涂装。但是,这种传统的防腐涂料,其防腐蚀效果也有待加强提高。cn107674577a公开了一种碳纳米管石墨烯无机富锌防腐涂料,包括a组分和b组分,所述a组分和b组分的质量配比为(50-60):(40-50);其中a组分按照质量百分比包括:纳米碳酸钙1-5%、沉淀硫酸钡10-40%、锌粉:15-30%、聚乙烯醇缩丁醛1-3%、溶剂20-40%、防沉剂0.5-2%、石墨烯0.1-10%、碳纳米管0.01-0.4%;b组分按照质量百分比包括:聚硅酸乙酯15-65%、溶剂30-50%、水1-5%、盐酸0.01-0.6%。此方法提供的碳纳米管石墨烯无机富锌防腐涂料,通过石墨烯、碳纳米管和锌粉形成一个导电网络结构,提升涂膜导电性能,减少锌粉的含量,减少在焊接时产生的氧化锌雾气,环境友好。但是,此方法得到的涂料防腐性能较差,不利于应用于工业生产等领域。因此,现有的富锌防腐涂料,虽然可以达到一定的防腐效果,但是在部分领域仍然达不到要求,所以需要开发新型防腐涂料,以满足更严格的防腐要求,拓展更广的应用领域。技术实现要素:针对现有技术的不足,本发明的目的在于提供一种富锌防腐涂料及其制备方法与应用,以使得涂料减小阻抗值的下降幅度,提升防腐效果。为达到此发明目的,本发明采用以下技术方案:第一方面,本发明提供了一种富锌防腐涂料,所述富锌防腐涂料按质量百分比计由99%~99.8%(例如可以是99%、99.1%、99.2%、99.3%、99.4%、99.5%、99.6%、99.7%或99.8%)的a组分和0.2%~1%(例如可以是0.2%、0.3%、0.4%、0.5%、0.6%、0.7%、0.8%、0.9%或1%)的b组分组成;所述a组分按重量份计包括如下组分:所述b组分为石墨烯浆料。本发明提供的富锌防腐涂料,通过将a组分和b组分的质量百分比合理调配,使得涂料的防腐蚀性能得以提升,相比于未添加石墨烯的涂料,防腐性能大大提升,进行经过528h的海水浸泡测试,涂料仍然保持良好外观及性能;同时相比于其他配比的a组分与b组分形成的涂料,防腐性能也更加优异;此外由于含有石墨烯浆料,使得涂料还兼具一定的导电性,具有良好的应用前景。本发明意外地发现,当含量不在本发明限定的,涂料的性能会有所下降,不利于实际应用。因此严格限定了a组分与b组分的含量。在本发明中,所述环氧树脂的重量份为10~20份,例如可以是10份、11份、12份、13份、14份、15份、16份、17份、18份、19份或20份等。优选地,所述环氧树脂包括阴离子型环氧树脂和/或阳离子型环氧树脂。在本发明中,环氧树脂作为主要的成膜物质,其中阴离子型环氧树脂与阳离子型环氧树脂可以同时添加,也可任选一种进行单独添加。阴离子型环氧树脂与阳离子型环氧树脂一般为水性环氧树脂。在本发明中,所述锌粉的重量份为50~65份,例如可以是50份、52份、55份、56份、58份、59份、60份、62份、63份、64份或65份等。锌粉具有防锈及耐大气侵蚀作用。在本发明中,所述硫酸钡的重量份为5~10份,例如可以是5份、6份、7份、8份、9份或10份等。在本发明中,硫酸钡可以改进色相和细度。一般优选使用超细硫酸钡,致密颗粒,粒径分布范围窄,化学稳定性高。硫酸钡含量达98%以上,能显著提升涂料的耐磨性能。在本发明中,所述增稠剂的重量份为1~2份,例如可以是1份、1.1份、1.2份、1.3份、1.4份、1.5份、1.6份、1.7份、1.8份、1.9份或2份等。优选地,所述增稠剂包括膨润土、羧甲基纤维素、羟乙基纤维素、聚丙烯酰胺、羟丙基甲基纤维素或黄原胶中的任意一种或至少两种的组合。在本发明中,所述助剂的重量份为4~8份,例如可以是4份、4.5份、5份、5.5份、6份、6.5份、7份、7.5份或8份等。优选地,所述助剂包括滑石粉和蜡粉。在本发明中,滑石粉和蜡粉需同时添加使用,以保证涂料的性能达到最佳。滑石粉可以改善涂膜的性能,蜡粉可起到消光和涂膜的效果。优选地,所述滑石粉和蜡粉的质量比为(15~20):1,例如可以是15:1、16:1、17:1、18:1、19:1或20:1等。在本发明中,滑石粉和蜡粉的质量比是特定的,如果滑石粉的比例过高,则涂膜的性能会下降;如果滑石粉的比例过低,消光作用过强,造成涂膜的光泽度较低,涂膜的性能也会有所下降。在本发明中,所述溶剂的重量份为7~10份,例如可以是7份、8份、9份或10份等。优选地,所述溶剂包括苯、甲苯、二甲苯、乙醇、正丁醇、石油醚、煤油、乙酸丁酯、乙酸乙酯、丙酮、甲乙酮、环己酮、乙醚、乙二醇乙醚或乙二醇丁醚中的任意一种或至少两种的组合。在本发明中,常用的溶剂均可作为a组分的溶剂使用,并不仅仅限于上述所列举的范围。优选地,所述石墨烯浆料的制备方法包括以下步骤:(1)将石墨烯粉加入到浓硫酸中,而后依次加入硝酸钠、高锰酸钾经搅拌第一次反应后,加入水和双氧水继续进行第二次反应,干燥得到混合物;(2)将步骤(1)得到的混合物加入到苯胺中,而后继续加入盐酸、过硫酸铵进行反应,洗涤得到石墨烯浆料。优选地,相对于1g石墨烯粉,步骤(1)中所述浓硫酸的用量为20~30ml(例如可以是20ml、22ml、25ml、28ml、29ml或30ml等),所述硝酸钠的用量为0.3~0.6g(例如可以是0.3g、0.4g、0.5g或0.6g等),所述高锰酸钾的用量为2~4g(例如可以是2g、2.5g、3g、3.5g或4g等),所述水的用量为40~60ml(例如可以是40ml、45ml、50ml、55ml或60ml等),所述双氧水的用量为40~60ml(例如可以是40ml、45ml、50ml、55ml或60ml等)。在本发明中,上述涉及到的浓硫酸、硝酸钠、高锰酸钾和双氧水的用量须保持在所限定的范围内,否则无法制备性能良好的石墨烯材料。优选地,所述双氧水的体积分数为3%。优选地,所述第一次反应的温度为5~35℃,例如可以是5℃、10℃、15℃、20℃、25℃、30℃或35℃等。优选地,所述第一次反应的时间为0.5~2h,例如可以是0.5h、1h、1.5h或2h等。优选地,所述第二次反应的温度为70~85℃,例如可以是70℃、75℃、80℃或85℃等。优选地,所述第二次反应的时间为0.5~3h,例如可以是0.5h、1h、1.5h、2h、2.5h或3h等。优选地,相对于1g步骤(1)中得到的混合物,步骤(2)中所述苯胺的用量为10~50ml(例如可以是10ml、20ml、30ml、40ml或50ml等),所述盐酸的用量为10~30ml(例如可以是10ml、15ml、20ml、25ml或30ml等),所述过硫酸铵的用量为15~50ml(例如可以是15ml、20ml、25ml、30ml、35ml、40ml、45ml或50ml等)。优选地,所述盐酸的浓度为5%~20%,例如可以是5%、10%、15%或20%等。优选地,所述过硫酸铵的浓度为0.05~0.2mol/l,例如可以是0.05mol/l、0.1mol/l、0.15mol/l或0.2mol/l等。优选地,步骤(2)中所述反应的温度为30~50℃,例如可以是30℃、35℃、40℃、45℃或50℃等。优选地,步骤(2)中所述反应的时间为5~8h,例如可以是5h、6h、7h或8h等。优选地,步骤(2)中所述洗涤的方法为使用体积分数为95%的乙醇洗涤两次,再使用蒸馏水洗涤5次。作为优选技术方案,本发明提供的富锌防腐涂料按质量百分比计由99.3%~99.6%的a组分和0.4%~0.7%的b组分组成;所述a组分按重量份计包括如下组分:所述b组分为石墨烯浆料。进一步地,作为优选技术方案,本发明提供的富锌防腐涂料按质量百分比计由99.5%的a组分和0.5%的b组分组成;所述a组分按重量份计包括如下组分:所述b组分为石墨烯浆料。第二方面,本发明提供了一种如第一方面所述的富锌防腐涂料的制备方法,所述制备方法为:将b组分通过边搅拌边加入的方式,加入到a组分中,且搅拌按照同一方向进行,过滤、静置后得到所述富锌防腐涂料。本发明提供的制备方法,操作时需将b组分添加到a组分中,否则会造成涂料混合不均,性能下降;同时,在搅拌的过程中,搅拌速度要均匀且保证按照同一方向进行,避免搅拌过程中产生气泡,造成涂料的性能下降。优选地,所述搅拌的时间为0.5~2h,例如可以是0.5h、1h、1.5h或2h等。优选地,所述过滤的方法为:使用100~300目的筛绢过滤杂质至无沉淀为止。第三方面,本发明提供了一种如第一方面所述的富锌防腐涂料在大型机械表面防护、工业生产防腐中的应用。本发明提供的富锌防腐涂料,具有广泛的应用。例如,大型机械可以是车辆、机床、水泵、反应罐等,作为表面防护使用;又如,工业生产中,可以在化工生产、石油贮藏等等方面作为防腐的涂料漆使用。相对于现有技术,本发明具有以下有益效果:本发明提供的富锌防腐涂料,通过将a组分和b组分的质量百分比合理调配,使得涂料的防腐蚀性能得以提升,相比于未添加石墨烯的涂料,防腐性能大大提升,进行经过528h的海水浸泡测试,涂料仍然保持良好外观及性能,耐盐雾时间可达到5000小时以上,最高可达5800小时左右;同时相比于其他配比的a组分与b组分形成的涂料,防腐性能也更加优异;此外由于含有石墨烯浆料,使得涂料还兼具一定的导电性,具有良好的应用前景和广阔的应用价值。附图说明图1是本发明实施例1制备的富锌防腐涂料进行海水浸泡前形貌图。图2是本发明实施例1制备的富锌防腐涂料进行海水浸泡后形貌图。图3是本发明对比例1制备的富锌涂料进行海水浸泡前形貌图。图4是本发明对比例1制备的富锌涂料进行海水浸泡后形貌图。具体实施方式下面通过具体实施方式来进一步说明本发明的技术方案。本领域技术人员应该明了,所述实施例仅仅是帮助理解本发明,不应视为对本发明的具体限制。实施例1本实施例提供的富锌防腐涂料中a组分质量分数为99.5%,b组分质量分数为0.5%,其中a组分包括以下组分:b组分为石墨烯浆料,其中石墨烯浆料通过以下方法制备:(1)使用电子分析天平称取4.000g石墨烯粉加入98%的浓硫酸100ml开始搅拌,边搅拌边加入2g的硝酸钠继续搅拌,并逐渐加入12g的高锰酸钾,并且在此过程中恒温30℃,搅拌1h后加入200ml的蒸馏水将温度升高到80℃,搅拌1h以后加入浓度为3%的双氧水200ml,继续搅拌半个小时,抽滤洗涤至中性,洗去多余的硫酸根离子,烘干得到混合物备用。(2)取步骤(1)得到的混合物200mg加入4ml的苯胺进行分散,再加入4ml10%的盐酸和6ml0.1mol/l的过硫酸铵,40℃搅拌6小时,用布氏漏斗进行过滤,保存滤液,并用体积分数为95%的乙醇洗涤两次,再用蒸馏水洗涤5次,制得石墨烯浆料。富锌防腐涂料由以下步骤制备:将b组分通过边搅拌边加入的方式,加入到a组分中,且搅拌1h按照同一方向进行,使用200目的筛绢过滤杂质至无沉淀为止,静置后得到富锌防腐涂料。实施例2本实施例提供的富锌防腐涂料中a组分质量分数为99.6%,b组分质量分数为0.4%,其中a组分包括以下组分:b组分为石墨烯浆料,其中石墨烯浆料通过以下方法制备:(1)使用电子分析天平称取4.000g石墨烯粉加入98%的浓硫酸80ml开始搅拌,边搅拌边加入1.2g的硝酸钠继续搅拌,并逐渐加入8g的高锰酸钾,并且在此过程中恒温5℃,搅拌2h后加入160ml的蒸馏水将温度升高到70℃,搅拌0.5h以后加入浓度为3%的双氧水160ml,继续搅拌半个小时,抽滤洗涤至中性,洗去多余的硫酸根离子,烘干得到混合物备用。(2)取步骤(1)得到的混合物200mg加入2ml的苯胺进行分散,再加入2ml10%的盐酸和3ml0.2mol/l的过硫酸铵,30℃搅拌8小时,用布氏漏斗进行过滤,保存滤液,并用体积分数为95%的乙醇洗涤两次,再用蒸馏水洗涤5次,制得石墨烯浆料。富锌防腐涂料由以下步骤制备:将b组分通过边搅拌边加入的方式,加入到a组分中,且搅拌1h按照同一方向进行,使用200目的筛绢过滤杂质至无沉淀为止,静置后得到富锌防腐涂料。实施例3本实施例提供的富锌防腐涂料中a组分质量分数为99.8%,b组分质量分数为0.2%,其中a组分包括以下组分:b组分为石墨烯浆料,其中石墨烯浆料通过以下方法制备:(1)使用电子分析天平称取4.000g石墨烯粉加入98%的浓硫酸120ml开始搅拌,边搅拌边加入2.4g的硝酸钠继续搅拌,并逐渐加入16g的高锰酸钾,并且在此过程中恒温35℃,搅拌1h后加入240ml的蒸馏水将温度升高到80℃,搅拌1h以后加入浓度为3%的双氧水240ml,继续搅拌半个小时,抽滤洗涤至中性,洗去多余的硫酸根离子,烘干得到混合物备用。(2)取步骤(1)得到的混合物200mg加入10ml的苯胺进行分散,再加入10ml10%的盐酸和15ml0.1mol/l的过硫酸铵,50℃搅拌5小时,用布氏漏斗进行过滤,保存滤液,并用体积分数为95%的乙醇洗涤两次,再用蒸馏水洗涤5次,制得石墨烯浆料。富锌防腐涂料由以下步骤制备:将b组分通过边搅拌边加入的方式,加入到a组分中,且搅拌1h按照同一方向进行,使用200目的筛绢过滤杂质至无沉淀为止,静置后得到富锌防腐涂料。性能测试将实施例1制备的富锌防腐涂料进行电化学阻抗谱测试,实验条件是海水环境,水浴温度为30℃。使用parstat2273电化学工作站。在测量电化学阻抗谱时,施加的激励信号电位振幅为10mv,频率范围是105hz-10-2hz。电解池采用三电极体系,涂层破损率为1%,工作电极有效测试面积为1cm2,辅助电极为直径4mm铂铌丝,以饱和甘汞电极(sce)作为参比电极,盐桥中的溶液为饱和kcl溶液,电解液为天然海水。采用origin8.5软件、zsimpwin软件对数据进行处理。将富锌防腐涂料分别浸泡2h、24h、72h、120h、360h、432h、528h后,得到交流阻抗谱拟合结果,如下表1所示:表1时间cp/(ω·m-2)rp/(ω·m2)cd/(ω·m-2)rr/(ω·m2)2h1.969e-65.419e31.927e-52.845e524h1.245e-49.818e33.149e-64.162e772h3.205e-62.862e31.539e-47.824e7120h1.969e-47.628e33.343e-62.667e7360h4.647e-63.050e32.931e-49.103e7432h2.679e-41.201e45.272e-63.156e8528h4.800e-52.308e54.142e-63.927e8由表1中数据可知,根据最后一列电荷转移电阻变化值来看,随着时间的增加电荷转移电阻呈现先减小后增大循环波动的趋势。对比例1本对比例与实施例1的区别仅在于,本对比例不包括b组分石墨烯浆料,制备得到富锌涂料。将对比例1制备的富锌涂料按照实施例1性能测试的方法同样进行电化学阻抗谱测试,交流阻抗谱拟合结果如表2所示。表2时间cp/(ω·m-2)rp/(ω·m2)cd/(ω·m-2)rr/(ω·m2)2h5.62e-62.391e57.931e-74.756e424h8.493e-75.038e39.555e-78.814e672h2.509e-73.279e31.966e-67.812e6120h4.369e-84.059e38.821e-75.363e6360h1.485e-62.844e64.942e-87.573e3432h2.279e-63.217e62.567e-141.308e7528h4.924e-62.436e-163.191e-88.278e6由表2可知,最后一列电荷转移电阻变化值来看,从2h到360h,随着时间的增加电荷转移电阻不断减小,阻抗值也就不断减小,溶液的导电性增强反应阻力减小,增加了腐蚀速度;从432h到528h,随着时间的增加电荷转移电阻不但没有减小反而增加,分析其原因可能是因为随着浸泡时间的增加,腐蚀速率加快,在很短的时间内生成较多的腐蚀产物覆盖在其表面,从而起到了保护作用,抑制了部分腐蚀反应进行。由表1和表2对比可知,表1中的数值呈现稳定趋势,并且电荷转移电阻更大,抗腐蚀效果更优。将实施例1与对比例1制备的涂料分别进行海水浸泡测试,记录观察外观变化结果。实施例1制备的富锌防腐涂料进行海水浸泡,分别记录浸泡前形貌(图1)与浸泡后形貌(图2);对比例1制备的涂料,浸泡前形貌(图3)和浸泡后形貌(图4)。由上述形貌对比可知,未添加石墨烯的环氧富锌涂料在经过528h的海水浸泡后,漆膜出现了少量小气泡,发生了腐蚀反应。而本发明制备的富锌防腐涂料在同样的条件下漆膜未出现明显变化,外观依然完整。由此得出,本发明制备的富锌防腐涂料与传统的环氧富锌涂料相比,封闭性较好,能有效的阻止外界腐蚀介质通过漆膜微孔进入基材,起到很好的防腐蚀效果。对比例2本对比例与实施例1的区别仅在于,本对比例中a组分的质量分数为98%,b组分的质量分数为2%,其余组分与制备方法均与实施例1相同,制备得到富锌防腐涂料。将实施例1-3与对比例1-2制备的涂料进行盐雾试验测试,参考标准gb1771-1991,具体结果如下表3所示:表3样品耐盐雾时间(h)实施例15840实施例25252实施例35381对比例14535对比例24927通过实施例1-3与对比例1-2的对比可知,本发明提供的富锌防腐涂料耐盐雾时间可达到5000h以上,最高可达到5800小时左右;而未添加石墨烯浆料的普通涂料,耐盐雾时间短;而不在本发明限定的配比范围内时,耐盐雾时间也大大降低。综上,本发明提供了一种具有良好防腐性能的富锌防腐涂料,具有广阔的应用前景和较高的应用价值。申请人声明,本发明通过上述实施例来说明本发明的富锌防腐涂料及其制备方法与应用,但本发明并不局限于上述工艺步骤,即不意味着本发明必须依赖上述工艺步骤才能实施。所属
技术领域:
的技术人员应该明了,对本发明的任何改进,对本发明所选用原料的等效替换及辅助成分的添加、具体方式的选择等,均落在本发明的保护范围和公开范围之内。当前第1页12