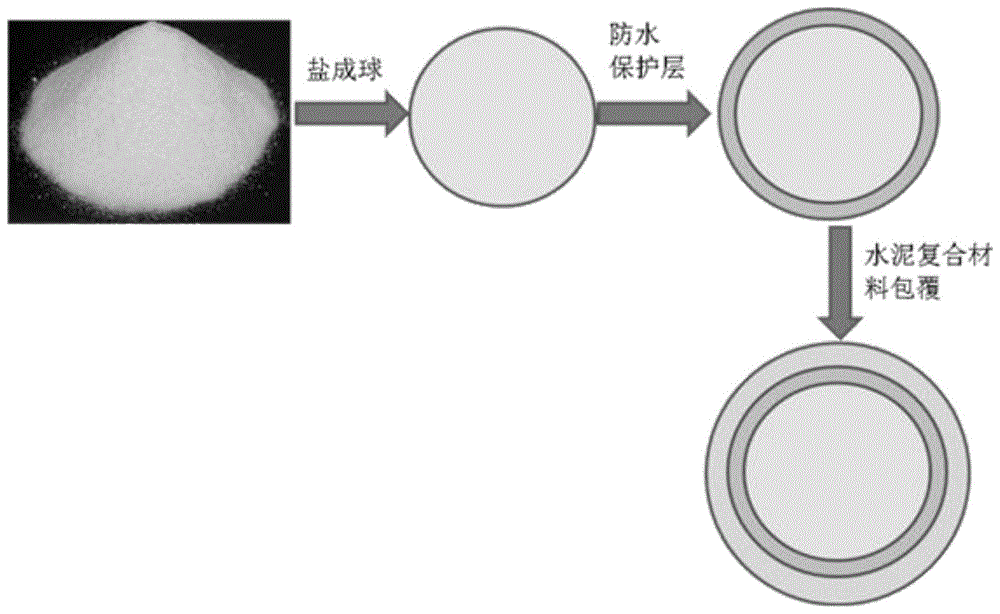
本发明涉及一种熔盐相变蓄热元件及其制备方法。
背景技术:
:太阳能、风能等可再生能源均存在波动性大,能源利用率不高的问题。同时炼钢、炼铝等行业的工业余热,均存在总量巨大、间歇性及利用率低等问题,极易造成能源的巨大浪费。中高温储热技术是解决这些问题的关键技术之一,通过蓄热技术可使热能实现稳定输出。熔盐由固相到液相的相变过程中会释放巨大的热量,利用熔盐相变蓄热技术可极大地提高系统储热密度,降低储热装置体积。因此开展熔盐蓄热储能研究具有重要价值,其中利用熔盐封装技术制成固态蓄热元件是拓展蓄热的关键技术。调查发现,直径3cm高铝蓄热球(65wt%al2o3)的成本可以降到约0.1元/个,其可适用于高温储热(≥500℃),但该固体蓄热元件存在热导率和蓄热量低(导热率低于2w/mk,没有相变,只有显热)的缺点。若将相变熔盐采用合金封装,相同蓄热量的熔盐根据不同的厚度(0.1-2mm),制得的相变蓄热元件,其包覆材料热导率能达到10w/mk,但成本约1-10元/个;若采用其它先进工艺封装,如气相沉积碳材料、压制石墨等工艺,制备得到的固态蓄热元件所需成本则更高(≥10元/个)。例如中国专利文献cn105810812a,公开了一种球形高温相变储热元件的组装方法和由此形成的储热元件,其提供了一种石墨包覆相变熔盐的技术,将相变材料微球与石墨化前驱体混合后放入准等静压硅胶模具中,预压成型,使得相变材料微球弥散在石墨化前驱体中,得到预压球坯;将预压球坯放入准等静压硅胶模具中,压制成型,使得多个相变材料微球形成为核心,而石墨化前驱体形成包围该核心的基体石墨层,得到终压球坯;将终压球坯进行热处理得到储热元件。该法采用准等静压技术和模压技术,对设备要求较高;且需多次压制成型,工序较复杂。另据中国专利文献cn107988506a,一种复合材料相变蓄热球及其制备方法所述,将铝硅合金粉置于成球机中,间歇式喷洒磷酸二氢铝溶液,制得铝硅合金球。向所述铝硅合金球喷洒表面改性剂,再于成球机中加入α-al2o3粉,滚动成球,得到复合材料相变蓄热球坯体。向所述复合材料相变蓄热球坯体喷洒去离子水,10~30s后加入α-al2o3粉,滚动成型,得到复合材料相变蓄热球坯ⅰ。重复复合材料相变蓄热球坯ⅰ的制备过程至复合材料相变蓄热球坯体ⅱ的直径与所述铝硅合金球的直径比为6:(1~5)。将所述复合材料相变蓄热球坯ⅱ置于马弗炉中,在800~1500℃保温2~8h,制得复合材料相变蓄热球。该发明工艺简单和成本低;所制制品的热量利用率大、使用温度高和壳层强度大。但该法采用铝硅合金,成本较高,且其性质与熔盐差异较大,不需要防水保护且烧成温度偏高,不适合包覆熔盐。因此,如何降低固态熔盐相变蓄热元件的成本,提高其导热性能是亟待解决的问题。技术实现要素:本发明所要解决的技术问题在于现有技术中固态熔盐相变蓄热元件存在难以同时做到高导热、低成本的问题,而提供了一种熔盐相变蓄热元件及其制备方法。本发明的固态相变蓄热元件具有低成本高导热的优点,工艺简单安全,操作方便,适合大批量生产。本发明通过以下技术方案解决上述技术问题。本发明提供了一种熔盐相变蓄热元件,所述熔盐相变蓄热元件为一核壳结构,其包括内核和外壳;所述内核为熔盐球;所述外壳的材质包括碳基导热材料和水泥;其中,所述熔盐球的半径占所述熔盐相变蓄热元件半径的29%~90%;所述熔盐球的半径占所述熔盐相变蓄热元件半径比例,以及所述外壳的厚度占所述熔盐相变蓄热元件半径的比例之和<100%;所述碳基导热材料占“所述碳基导热材料和所述水泥”总质量的质量百分比为1.0~50.0%。本发明中,所述熔盐球中的熔盐可为本领域常规的熔盐。较佳地,所述熔盐为水合盐、硝酸盐、氯化盐、碳酸盐、氟化盐和硫酸盐的一种或多种。更佳地,所述熔盐为水合盐。其中,所述水合盐是指带有结晶水的盐类,其种类可为本领域常规。例如,所述水合盐为ba(oh)2·8h2o。其中,较佳地,在所述水合盐中加入成核剂和/或增稠剂。其中,较佳地,所述成核剂与所述水合盐晶格参数相近。例如当水合盐为ba(oh)2·8h2o时,所述成核剂为bacl2·2h2o。其中,较佳地,所述增稠剂为cmc。其中,较佳地,所述水合盐:所述成核剂:所述增稠剂的质量比为(97~99):(0~2):(0~2),例如为98:1:1。例如,所述熔盐为ba(oh)2·8h2o,所述成核剂为bacl2·2h2o,所述增稠剂为cmc,ba(oh)2·8h2o:bacl2·2h2o:cmc的质量比为98:1:1。更佳地,所述熔盐为氯化盐。其中,所述氯化盐的种类可为本领域常规,较佳地为nacl和/或kcl。当所述氯化盐为nacl和kcl的混合物时,nacl:kcl的摩尔比优选地为(40~60):(40~60),例如为50.6:49.4。更佳地,所述熔盐为碳酸盐。所述碳酸盐的种类可为本领域常规,较佳地为li2co3、na2co3和k2co3中的一种或多种。当所述碳酸盐为li2co3、na2co3和k2co3的混合物时,li2co3:na2co3:k2co3的质量比优选地为(15~25):(55~65):(15~25),例如为20:60:20。其中,所述水合盐的熔点温度一般低于100℃。例如ba(oh)2·8h2o熔盐中加入成核剂和增稠剂(ba(oh)2·8h2o:bacl2·2h2o:cmc的质量比为98:1:1)的熔点为78℃。其中,所述硝酸盐的熔点温度一般为90~550℃。例如nano3的熔点约为308℃。其中,所述氯化盐、所述碳酸盐、所述氟化盐或所述硫酸盐的熔点温度一般为300℃~900℃。例如,nacl的熔点为801℃。再例如,nacl和kcl的混合物(nacl:kcl的摩尔比为50.6:49.4)的熔点为657℃。再例如,li2co3、na2co3和k2co3的混合物(li2co3:na2co3:k2co3的质量比为20:60:20)的熔点为550℃。本发明中,较佳地,所述熔盐球的半径占所述熔盐相变蓄热元件半径的65%~90%,例如为65.1%、68.5%、86.2%、77.7%、72.7%或88.9%。本发明中,所述熔盐相变蓄热元件的半径可为本领域常规,较佳地为10~60mm,更佳地为14~23mm,例如为14.6mm、16.5mm、17.4mm、19.3mm、21.5mm或22.5mm。本发明中,所述熔盐球的半径较佳地为0.5~5cm,更佳地为1~2cm,例如为1、1.2、1.4、1.5或2cm。本发明中,如图2所示,所述熔盐相变蓄热元件的半径为r,所述熔盐球的半径为r1,所述包覆层的厚度为r2。所述熔盐相变蓄热元件在制备过程中,防水层会发生分解,或者防水层会发生融化渗出熔盐相变蓄热元件,在包覆层和熔盐球之间产生空隙。同时,包覆层在烧结过程中发生收缩(包覆层厚度的收缩率约为6%~20%),与熔盐球之间留出一定空隙,为后续熔盐相变蓄热元件在使用的过程中,熔盐的固液相变体积变化留有所需的空间。因此,本领域技术人员可以理解,包覆层与熔盐球之间留有空隙,所述熔盐球的半径占所述熔盐相变蓄热元件半径比例,以及所述包覆层的厚度占所述熔盐相变蓄热元件半径的比例之和<100%。本发明中,为了使制备得到的熔盐相变蓄热元件具有高导热性能,同时保证制备得到的熔盐相变蓄热元件在使用过程中整体结构的稳定性,本发明设计以由碳基导热材料和水泥组成的包覆层封装熔盐。本发明中,所述碳基导热材料占“所述碳基导热材料和所述水泥”总质量的质量百分比较佳地为3.0~50.0%,更佳地为10.0~50.0%,例如为3%、5%、25%、30%或50%。本发明中,所述碳基导热材料较佳地为石墨粉、石墨烯和碳纳米管一种或多种,更佳地为石墨粉、石墨烯或碳纳米管。其中,所述石墨粉较佳地为鳞片石墨粉或土状石墨粉经气流粉碎机破碎制备得到。其中,所述石墨粉的平均粒径较佳地为5~15微米。本发明中,所述水泥较佳地为低温烧结的耐高温水泥,更佳地为高铝硅酸盐水泥。其中,本领域技术人员知晓,高铝硅酸盐水泥是指以氧化铝、氧化钙为主要成分、氧化铝含量约50%的水泥。所述低温烧结一般是指烧结温度低于1000℃。本发明还提供了一种如前所述的熔盐相变蓄热元件的制备方法,其特征在于,其包括如下步骤:s1.将所述熔盐球在有机材料中滚动成型,或者,将有机材料刷涂在所述熔盐球表面,在所述熔盐球表面形成一防水层,得到所述防水层包覆的熔盐球;s21.若所述熔盐球中的熔盐的熔点低于100℃,将步骤s1所述防水层包覆的熔盐球在混合料浆中滚动成型,在所述防水层表面形成一包覆层;依次进行水化和干燥后,在所述熔盐球的表面形成所述外壳;所述有机材料的融化温度低于步骤s21中干燥的温度;s22.若所述熔盐球中的熔盐的熔点为100℃及以上,将步骤s1所述防水层包覆的熔盐球在混合料浆中滚动成型,在所述防水层表面形成一包覆层;依次进行水化,干燥和热处理后,在所述熔盐球的表面形成所述外壳;所述有机材料的分解温度低于步骤s22中的热处理的温度;s21或者s22中,所述混合浆料包括所述碳基导热材料、所述水泥和水。本领域技术人员知晓,可以根据所述熔盐相变蓄热元件使用工况条件进行熔盐类型的选择。例如,若选择nano3作为相变熔盐材料,其熔点约308℃,其使用温度可达到500℃。再例如,若选择nacl作为相变熔盐材料,其熔点可达801℃,其使用温度可达到1000℃。本领域技术人员可根据使用需要,配置不同熔点和不同焓值的熔盐。并且,可根据所述熔盐球熔化后体积变化,确定在制备时所述熔盐球的体积密度。s1中,所述熔盐球的密度较佳地为1.70~1.93g/cm3。s1中,较佳地,所述熔盐球为将熔盐经滚动成型和/或压制成型得到的熔盐球。所述滚动成型或所述压制成型可为本领域常规的熔盐球的制备工艺。本发明中,由于步骤s21或者s22中需要在混合料浆中滚动成型进行包覆,以及在包覆混合料浆后需要进行水化的步骤,都需要在湿度较大的环境中,为防止熔盐吸水,本发明设计步骤s1中以有机材料在所述熔盐球表面形成一防水层,形成防水层。并且,经步骤s21的干燥(熔盐球中的熔盐的熔点低于100℃),或者步骤s22的干燥和热处理(熔盐球中的熔盐的熔点为100℃及以上)后,防水层受热融化或分解,为烧结过程中包覆层的收缩,以及为后续熔盐相变蓄热元件在使用的过程中,熔盐的固液相变体积变化留有所需的空间。s1中,所述有机材料可为本领域常规的热固性有机材料或热塑性有机材料。s1中,较佳地,所述滚动成型或所述刷涂的过程中,所述有机材料为液体状态。较佳地,所述有机材料为环氧树脂、酚醛树脂、烃类聚合物和脂肪酸类有机材料一种或多种。更佳地,所述有机材料为环氧树脂、酚醛树脂、烃类聚合物或脂肪酸类有机材料。其中,本领域技术人员知晓,所述环氧树脂一般为热固性有机材料。所述酚醛树脂一般为热固性或热塑性有机材料。所述烃类聚合物一般为热塑性有机材料。所述脂肪酸类一般为热塑性有机材料。例如,所述环氧树脂为e-51环氧树脂,或者为e-51环氧树脂与聚氨酯预聚体发生聚合后的产物。更佳地,在所述有机材料中加入固化剂。所述固化剂优选为胺类固化剂,例如为二乙烯三胺。所述固化剂的用量优选为3%~10%,例如为6.67%,所述百分比为所述固化剂与所述有机材料的质量比。例如,在e-51环氧树脂与聚氨酯预聚体的混合物中加入二乙烯三胺。本发明一优选实施方式中,在100ge-51环氧树脂与50g聚氨酯预聚体的混合物中加入10g二乙烯三胺。例如,所述烃类聚合物为热塑性聚乙烯或热塑性聚苯乙烯树脂。例如,所述脂肪酸类有机材料为相变点为30℃~50℃的脂肪酸,例如为相变点为30℃的脂肪酸或者相变点为50℃的脂肪酸;其中,所述相变点是指固液相变点。s1中,需要根据所述熔盐球中熔盐的沸点,选择有机材料的种类。若所述熔盐球中的熔盐的熔点低于100℃,则所述有机材料的融化温度需低于步骤s21中干燥的温度;若所述熔盐球中的熔盐的熔点为100℃以上,所述有机材料的分解温度低于步骤s22中的热处理的温度。在选择了有机材料的种类后,再根据不同有机材料的材料特性,选择合适的配方、操作温度、粘度等工艺参数,经滚动成型,得到防水层包覆的熔盐球。s1中,所述有机材料在液体状态时的粘度较佳地大于10000mpa·s或者为20~250mpa·s,更佳地为14000~20000mpa·s或者50~200pa·s。例如,热塑性聚乙烯在液态状态下时的粘度为17000mpa·s~20000mpa·s。再例如,热塑性聚苯乙烯树脂在液态状态下时的粘度为14000mpa·s~16000mpa·s。再例如,100ge-51环氧树脂、50g聚氨酯预聚体和10g二乙烯三胺的混合物在液态状态下时的粘度为14000mpa·s~16000mpa·s。再例如,相变点为30℃的脂肪酸在液态状态下时的粘度为20~50mpa·s。再例如,相变点为50℃的脂肪酸在液态状态下时的粘度为200~250mpa·s。s1中,较佳地,当所述有机材料为热固性有机材料时,所述滚动成型的操作较佳地按下述步骤进行:常温下,所述熔盐球在有机材料中滚动成型后,在所述热固性有机材料相变点温度以上的温度下,固化成型。其中,所述热固性有机材料相变点温度一般是指热固性有机材料液态转为固态的温度。其中,较佳地,所述热固性有机材料于50~70℃固化成型。其中,所述常温一般指的温度为20~30℃。本发明一优选实施方式中,所述有机材料为e-51环氧树脂100g:聚氨酯预聚体50g:二乙烯三胺10g的混合物;常温下,所述熔盐球在有机材料中滚动成型后,于60℃固化成型。s1中,较佳地,当所述有机材料为热塑性有机材料时,所述滚动成型的操作较佳地按下述步骤进行:在所述热塑性有机材料相变点温度以上的温度下,所述熔盐球在有机材料中滚动成型后,在常温下固化成型。其中,所述热塑性有机材料相变点温度一般是指热塑性有机材料液态转为固态的温度。其中,较佳地,所述热塑性有机材料在35~220℃下进行所述滚动成型。其中,所述常温一般指的温度为20~30℃。本发明一优选实施方式中,所述有机材料为相变点为30℃的脂肪酸;在35℃下,所述熔盐球在有机材料中滚动成型后,于常温下固化成型。本发明一优选实施方式中,所述有机材料为相变点为50℃的脂肪酸;在60℃下,所述熔盐球在有机材料中滚动成型后,于常温下固化成型。本发明一优选实施方式中,所述有机材料为热塑性聚苯乙烯;在150℃下,所述熔盐球在有机材料中滚动成型后,于常温下固化成型。本发明一优选实施方式中,所述有机材料为热塑性聚乙烯;在220℃下,所述熔盐球在有机材料中滚动成型后,于常温下固化成型。s1中,较佳地,所述熔盐球在所述有机材料中滚动成型,通过控制所述滚动成型中滚动的时间,控制所述防水层厚度。s1中,所述防水层的厚度较佳地为0.1~2mm,更佳地为0.2~0.3mm。s1中,所述刷涂可为本领域常规的有机材料刷涂工艺。s21或者s22中,较佳地,所述混合料浆的水灰比为0.1~0.6,所述水灰比为水与“碳基导热材料和水泥”的混合粉料的质量比。s21或者s22中,较佳地,所述混合料浆为将所述碳基导热材料和所述水泥的混合粉料与水混合均匀即可。其中,所述混合粉料一般可通过搅拌或者球磨的方法获得。其中,所述搅拌的速度较佳地为4000~5000r/min。其中,所述搅拌时间较佳地为20~90min。其中,所述球磨的转速较佳地为200~300r/min。其中,所述球磨的时间较佳地为30~120min。s21或者s22中,较佳地,通过控制所述滚动成型中滚动的时间,控制所述包覆层的厚度。s21或者s22中,所述包覆层的厚度较佳地为0.5~10.0mm,更佳地为3~8mm例如为3、5或8cm。s21或者s22中,所述水化的操作和条件可为本领域常规。s21或者s22中,较佳地,所述水化的温度为15~40℃。s21或者s22中,较佳地,所述水化的湿度为100%。s21或者s22中,较佳地,所述水化的时间≥5天。s21或者s22中,所述干燥的操作和条件可为本领域常规。s21或者s22中,较佳地,所述干燥的温度为60~120℃。s21或者s22中,较佳地,所述干燥的时间为12小时以上。s22中,所述热处理的操作和条件可为本领域常规。s22中,较佳地,所述热处理的温度低于所述熔盐球中的熔盐的熔点30℃以下。例如,若选择nacl作为相变熔盐材料,其熔点为801℃,所述热处理的温度为770℃或者更低。更佳地,所述热处理的温度为70℃~900℃,优选为500℃~750℃,例如为500℃、600℃或750℃。s22中,较佳地,所述热处理的时间为1~6小时。较佳地,所述熔盐相变蓄热元件的使用温度为60~1000℃,例如为室温至100℃或大于800℃。在符合本领域常识的基础上,上述各优选条件,可任意组合,即得本发明各较佳实例。本发明所用试剂和原料均市售可得。本发明的积极进步效果在于:(1)本发明的熔盐相变蓄热元件具有低成本高导热的优点,工艺简单安全,操作方便,适合大批量生产。(2)本发明可结合固态蓄热元件的具体工况条件,选择合适温度和相变焓的熔盐体系。(3)本发明工艺简单,制得的熔盐相变蓄热元件热量利用率大、适用温度广和壳层强度大、导热性能好。(4)本发明一优选实施方式中,采用高铝硅酸盐水泥,可以根据使用温度降低烧结温度,实现低温烧结。附图说明图1是固态熔盐相变蓄热元件制备工艺示意图。图2为实施例1~6中的熔盐相变蓄热元件示意图。图3:(a)未添加石墨粉的;(b)添加25%石墨粉的;(c)添加50%石墨粉的(d)热处理阶段的高铝硅酸盐水泥包覆蓄热元件。图4添加25%石墨粉蓄热元件sem表面形貌照片(×500倍)。图5添加25%石墨粉蓄热元件sem表面形貌照片(×2000倍)。图2的附图标记说明:r为熔盐相变蓄热元件的半径,r1为熔盐球的半径,r2为包覆层的厚度。具体实施方式下面通过实施例的方式进一步说明本发明,但并不因此将本发明限制在所述的实施例范围之中。下列实施例中未注明具体条件的实验方法,按照常规方法和条件,或按照商品说明书选择。本系列实施例中,热导率测试使用德国耐驰lfa激光热导仪测定。对于熔盐相变蓄热元件的包覆层的热导率,其测量的具体操作为:将包覆层加工成10mm×10mm×d的样品,d为千分尺多次测量的样品厚度,然后将样品放入样品台。等待温度稳定在25℃进行测量。其中激光电压为1528v,滤光片透射率为100%,采样时间为582ms,数据点数为3000。本系列实施例中,熔盐相变蓄热元件使用温度测试装置为采用高温炉,温度范围为室温~1000℃,以1~20℃/min的速度升到设定温度,保温20小时。若包覆元件破损率(包覆层破损的比例)低于0.5%,为满足使用性能。本系列实施例中,sem表面形貌照片测试使用扫描电子显微镜leo1530vp。本系列实施例中,石墨粉为鳞片石墨经气流粉碎机破碎制备得到,石墨粉的平均粒径为5~15微米。本系列实施例中,水泥为高铝硅酸盐水泥。该高铝硅酸盐水泥购自郑州科瑞耐火材料有限公司的625号耐高温水泥。本系列实施例中,所制得的熔盐相变蓄热元件如图2所示。实施例1如图1的制备工艺示意图所示:(1)选用nacl为熔盐,其熔点为801℃,采用滚动成型的方式,制得熔盐球,熔盐球成型后的密度为1.80g/cm3,熔盐球的半径r1为14mm。(2)选用热塑性聚乙烯为有机材料,其在液体状态下的粘度为18000mpa·s。在220℃下,将熔盐球在有机材料中滚动10min,于常温下固化成型,在熔盐球表面形成0.2mm的防水层。(3)选取质量百分比为50wt%石墨粉与水泥混合,采用球磨的方式混合,转速300r/min,球磨时间30min,得到混合粉料。加入水灰比(水与“石墨和水泥”的混合粉料的质量比)为0.3的水,将混合粉料与水混合均匀,得到混合料浆。(4)将防水层包覆的熔盐球在混合料浆中滚动成型15分钟,在防水层表面形成厚度为8mm的包覆层,如图3(c)所示。(5)在25℃,100%水汽下进行水化28天。(6)90℃下进行干燥12小时。(7)750℃下进行热处理,热处理的时间为1小时,得到实施例1样品(如图3(d)所示),熔盐相变蓄热元件的半径r为21.5mm。实施例2(1)选用nacl:kcl=50.6:49.4(摩尔比),其熔点为657℃,采用滚动成型的方式,制得熔盐球,熔盐球成型后的密度为1.77g/cm3,熔盐球的大小为半径r1为10mm。(2)选用热固性环氧树脂为有机材料,其由100ge-51环氧树脂、50g聚氨酯预聚体和10g二乙烯三胺组成,其在液体状态下的粘度为15000mpa.s。在常温下,将熔盐球在有机材料中滚动10min,于60℃下固化成型,在熔盐球表面形成0.2mm的防水层。(3)选取质量百分比为25wt%石墨粉与水泥混合,采用球磨的方式混合,转速300r/min,球磨时间60min,得到混合粉料。加入水灰比(水与“石墨和水泥”的混合粉料的质量比)为0.6的水,将混合粉料与水混合均匀,得到混合料浆。(4)将防水层包覆的熔盐球在混合料浆中滚动成型10分钟,在防水层表面形成厚度为5mm的包覆层。(5)在25℃,100%水汽下水化7天。(6)90℃下进行干燥12小时。(7)600℃进行热处理,热处理的时间为6小时,得到实施例2样品,如图3(b)、图4和图5所示,熔盐相变蓄热元件的半径r为14.6mm。实施例3(1)选用li2co3:na2co3:k2co3=20:60:20(质量比)为熔盐,其熔点为550℃,采用滚动成型的方式,制得熔盐球,熔盐球成型后的密度为1.70g/cm3,熔盐球的半径r1为15mm。(2)选用热塑性聚苯乙烯树脂为有机材料,其在液体状态下的粘度为15000mpa·s。在150℃下,将熔盐球在有机材料中滚动15min,于常温下固化成型,在熔盐球表面形成0.3mm的防水层。(3)选取质量百分比为30wt%石墨粉与水泥混合,采用球磨的方式混合,转速200r/min,球磨时间60min,得到混合粉料。加入水灰比(水与“石墨和水泥”的混合粉料的质量比)为0.5的水,将混合粉料与水混合均匀,得到混合料浆。(4)将防水层包覆的熔盐球在混合料浆中滚动成型5分钟,在防水层表面形成厚度为3mm的包覆层。(5)在25℃,100%水汽下进行水化14天。(6)90℃下进行干燥12小时。(7)500℃下进行热处理,热处理的时间为5小时,得到实施例3样品,熔盐相变蓄热元件的半径r为17.4mm。实施例4(1)选用ba(oh)2·8h2o:bacl2·2h2o:cmc=98:1:1(质量比)为熔盐,(其中bacl2·2h2o作为成核剂,cmc作为增稠剂),其熔点为78℃,采用滚动成型的方式,制得熔盐球,熔盐球成型后的密度为1.93g/cm3,熔盐球的半径r1为15mm。(2)选用相变点30℃的脂肪酸作为防水层。其在液体状态下的粘度为50mpa.s。在35℃下,将熔盐球在有机材料中滚动2min,冷却,在熔盐球表面形成0.2mm的防水层。(3)选取质量百分比为25wt%石墨粉与水泥混合,采用球磨的方式混合,转速300r/min,球磨时间60min,得到混合粉料。加入水灰比(水与“石墨和水泥”的混合粉料的质量比)为0.6的水,将混合粉料与水混合均匀,得到混合料浆。(4)将防水层包覆的熔盐球在混合料浆中滚动成型5分钟,在防水层表面形成厚度为5mm的包覆层。(5)在25℃,100%水汽下水化7天。(6)75℃下进行干燥12小时,得到实施例4样品,熔盐相变蓄热元件的半径r为19.3mm。实施例5(1)选用ba(oh)2·8h2o:bacl2·2h2o:cmc=98:1:1(质量比)为熔盐,(其中bacl2·2h2o作为成核剂,cmc作为增稠剂),其熔点为78℃,采用滚动成型的方式,制得熔盐球,熔盐球成型后的密度为1.93g/cm3,熔盐球的半径r1为12mm。(2)选用相变点50℃的脂肪酸作为防水层。其在液体状态下的粘度为200mpa.s。在60℃下,将熔盐球在有机材料中滚动2min,冷却,在熔盐球表面形成0.2mm的防水层。(3)选取质量百分比为3wt%石墨烯与水泥混合,采用球磨的方式混合,转速300r/min,球磨时间120min,得到混合粉料。加入水灰比(水与“石墨烯和水泥”的混合粉料的质量比)为0.5的水,将混合粉料与水混合均匀,得到混合料浆。(4)将防水层包覆的熔盐球在混合料浆中滚动成型5分钟,在防水层表面形成厚度为5mm的包覆层。(5)在25℃,100%水汽下水化7天。(6)75℃下进行干燥12小时,得到实施例5样品,熔盐相变蓄热元件的半径r为16.5mm。实施例6(1)选用li2co3:na2co3:k2co3=20:60:20(质量比)为熔盐,其熔点为550℃,采用滚动成型的方式,制得熔盐球,熔盐球成型后的密度为1.70g/cm3,熔盐球的半径r1为20mm。(2)选用热塑性聚苯乙烯树脂为有机材料,其在液体状态下的粘度为15000mpa·s。在150℃下,将熔盐球在有机材料中滚动15min,于常温下固化成型,在熔盐球表面形成0.3mm的防水层。(3)选取质量百分比为5wt%碳纳米管添加,采用球磨的方式混合,转速200r/min,球磨时间60min,得到混合粉料。加入水灰比(水与“碳纳米管和水泥”的混合粉料的质量比)为0.5的水,将混合粉料与水混合均匀,得到混合料浆。(4)将防水层包覆的熔盐球在混合料浆中滚动成型5分钟,在防水层表面形成厚度为3mm的包覆层。(5)在25℃,100%水汽下进行水化14天。(6)90℃下进行干燥12小时。(7)500℃下进行热处理,热处理的时间为2小时,得到实施例6样品,熔盐相变蓄热元件的半径r为22.5mm。对比例1(1)选用nacl为熔盐,其熔点为801℃,采用滚动成型的方式,制得熔盐球,熔盐球成型后的密度为1.80g/cm3,熔盐球的大小为14mm。(2)选用热塑性聚乙烯为有机材料,其在220℃下的粘度为18000mpa·s。在220℃下,将熔盐球在有机材料中滚动10min,于常温下固化成型,在熔盐球表面形成0.2mm的防水层。(3)在水泥中加入水,水灰比(水泥与水的质量比)为0.3,混合均匀,得到水泥料浆。4)将防水层包覆的熔盐球在水泥料浆中滚动成型15分钟,在防水层表面形成厚度8mm的包覆层。(5)在25℃,100%水汽下进行水化28天。(6)90℃下进行干燥12小时。(7)750℃下进行热处理,热处理的时间为6小时,得到对比例1样品,如图3(a)所示,熔盐相变蓄热元件的半径r为21.5mm。效果实施例1各个实施例和对比例的热导率和使用温度如下表1所示。表1热导率使用温度实施例17.6w/m·k大于800℃实施例24.2w/m·k大于700℃实施例35.1w/m·k大于800℃实施例44.2w/m·k室温至100℃实施例53.0w/m·k室温至100℃实施例62.6w/m·k大于800℃对比例10.1w/m·k大于800℃效果实施例2如实施例2,制备得到半径为14.6mm的熔盐相变蓄热元件,其中,石墨粉/高铝硅酸盐水泥包覆层的厚度为5mm,其成本仅为0.2元/个(其计算成本考虑原料价格和各制备工序成本)。以上所述的,仅为本发明的较佳实施例,并非用以限定本发明的范围,本发明的上述实施例还可以做出各种变化。即凡是依据本发明申请的权利要求书及说明书内容所作的简单、等效变化与修饰,皆落入本发明专利的权利要求保护范围。本发明未详尽描述的均为常规技术内容。当前第1页12