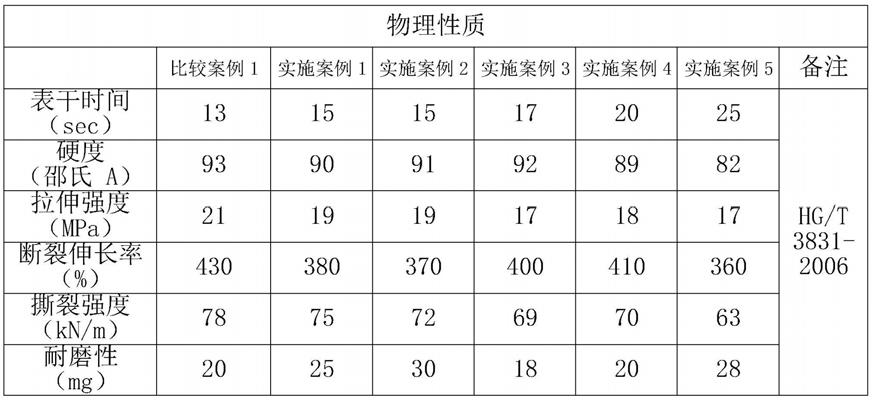
1.本发明涉及涂料生产及施工方式技术领域,尤其涉及一种防爆性能高抗冲击防层降组合型聚脲涂料及其施工方法。
背景技术:2.人类在居住地球上的发展,从石器时代慢慢转向工业现代化时代,个人生活状态的改变,日益提升并快速发展,所以居住的条件及安全系数也随之提高,建筑本身的进步也日新月异的提升,非常多采用高新技术的案例也越来越多,被取而代之的老工法也一一实现,但针对大自然现象的气候变化,地震的发生,建筑本身的层降问题,外力影响的爆炸状况等等问题。
3.综上所述,本发明通过设计一种防爆性能高抗冲击防层降组合型聚脲涂料及其施工方法来解决存在的问题。
技术实现要素:4.本发明的目的在于提供一种防爆性能高抗冲击防层降组合型聚脲涂料及其施工方法,以解决防爆性能高抗冲击防层降组合型聚脲涂料及其施工方法,可有效防止由大自然现象的气候变化,地震的发生,建筑本身的层降问题,外力影响的爆炸状况等等问题,引起的压力负荷对对保护的基材及建筑物本体,水泥砖墙或钢筋混凝土结构物的损坏,并有效防止建筑物的层降问题,导致不必要的破坏隐患的问题。
5.为实现上述目的,本发明提供如下技术方案:
6.一种防爆性能高抗冲击防层降组合型聚脲涂料,包括主剂和固化剂,所述主剂按照重量百分比包括:聚醚胺60~65%,二乙基甲苯二胺20~25%,色料8~10%,抗紫外线剂1~2%,抗黄变剂1~2%,附着力加强剂1~2%,分散剂0.1~1%,稳定剂0.1~0.5%,消泡剂1~2%,改性氨基硅油10~15%,所述固化剂为改性异氰酸酯预聚物。
7.优选的,所述改性异氰酸酯预聚物nco%含量百分比为15%~25%,并且nco为化学材料中异氰酸酯基,其值是指100g试样所含的异氰酸酯基团的质量,所述主剂和固化剂按重量比为1.15:1混合。
8.优选的,所述改性异氰酸酯预聚物由下列重量百分比含量百分比的原料制成的:分子量255二苯基甲烷二异氰酸酯45~55%、分子量2000的多元醇或分子量3000的聚醚多元醇45~55%,磷系阻燃剂10~15%;其制备方法步骤如下:
9.s1,向反应釜中依次加二苯基甲烷二异氰酸酯、多元醇或聚醚多元醇,在温度70~90℃、搅拌速度100~200rpm下,反应3~4小时;加入磷系阻燃剂,在温度50~70℃、搅拌速度100~200rpm下,混合30~60分钟,即得到分子量2000的改性异氰酸酯预聚物;
10.优选的,所述改性异氰酸酯预聚物由下列重量百分比含量百分比的原料制成的:分子量275的碳化二亚胺改性4,4二苯基甲烷二异氰酸酯50~60%,分子量2000的多元醇或分子量3000的聚醚多元醇45~55%,磷系阻燃剂10~15%;其制备方法步骤如下:
11.s2,向反应釜中依次碳化二亚胺改性4,4二苯基甲烷二异氰酸酯、多元醇或聚醚多元醇,在温度70~90℃、搅拌速度100~200rpm下,反应3~4小时;加入磷系阻燃剂,在温度50~70℃、搅拌速度100~200rpm下,混合30~60分钟,即得到分子量2000的改性异氰酸酯预聚物。
12.优选的,所述改性异氰酸酯预聚物由下列重量百分比含量百分比的原料制成的:分子量255二苯基甲烷二异氰酸酯30~45%,分子量275的碳化二亚胺改性4,4二苯基甲烷二异氰酸酯30~45%,分子量2000的多元醇或分子量3000的聚醚多元醇45~55%,磷系阻燃剂10~15%;其制备方法步骤如下:
13.s3,向反应釜中依次加入二苯基甲烷二异氰酸酯、碳化二亚胺改性4,4二苯基甲烷二异氰酸酯、多元醇或聚醚多元醇,在温度70~90℃、搅拌速度100~200rpm下,反应3~4小时;加入磷系阻燃剂,在温度50~70℃、搅拌速度100~200rpm下,混合30~60分钟,即得到分子量2000的改性异氰酸酯预聚物。
14.优选的,包括以下步骤:
15.步骤一、基材事先处理:首先清洁附着于基材表面的油污、灰尘、突起物、浆皮等污染物;
16.步骤二、基材调整涂敷:以重量比为1:1:3的主剂、固化剂、砂浆粉末充分搅拌后作为基材调整涂敷材料,涂覆于经过步骤一修护清洁处理后的基材上,填充于基材上的缝隙、裂纹;
17.步骤三、基础底漆涂敷:以50μm的厚度涂敷基础底漆;
18.步骤四、防爆性能高抗冲击防层降组合型聚脲涂料涂敷:涂覆防爆性能高抗冲击防层降组合型聚脲涂料,所述防爆性能高抗冲击防层降组合型聚脲涂料由所述主剂和固化剂按重量比为1.15:1混合而成;
19.步骤五、抗紫外线、抗黄变漆涂敷:室外以75μm(室内部分50μm)的厚度涂敷抗紫外线、抗黄变漆。
20.与现有技术相比,本发明的有益效果是:
21.1、本发明中,通过设计可有效防止由大自然现象的气候变化,地震的发生,建筑本身的层降问题,外力影响的爆炸状况等等问题,引起的压力负荷对对保护的基材及建筑物本体,水泥砖墙或钢筋混凝土结构物的损坏,并有效防止建筑物的层降问题,导致不必要的破坏隐患。
22.2、本发明中,通过设计主剂中减少了扩链剂用量,加大了特性中的黏着力、吸收量能,有效提升了防爆性能高抗冲击防层降组合型聚脲涂料的物理性质。
23.3、本发明中,通过设计具有极大的拉伸强度、收缩力量,可完成无缝隙的连续喷涂。
24.4、本发明中,通过设计具有超快速固化的性能(15秒/25℃,表干),施工作业省力,即使是垂直面的作业,也不会有流淌现象,同时可保证在合格的涂膜厚度内。
25.5、本发明中,通过设计原材料中不含溶剂、催化剂、增塑剂等对人体有害物质(voc 0),因此,可以运用在净水厂及饮用水储存箱等的防护涂料。
具体实施方式
26.下面将结合本发明实施例中,对本发明实施例中的技术方案进行清楚、完整地描述,显然,所描述的实施例仅仅是本发明一部分实施例,而不是全部的实施例,基于本发明中的实施例,本领域普通技术人员在没有做出创造性劳动前提下所获得的所有其他实施例,都属于本发明保护的范围。
27.本发明提供一种技术方案:
28.一种防爆性能高抗冲击防层降组合型聚脲涂料,包括主剂和固化剂,所述主剂与固化剂按重量比为1.15:1混合而成;
29.其中,所述主剂按照重量百分比包括:聚醚胺60~65%,二乙基甲苯二胺20~25%,色料8~10%,防紫外线剂1~2%,抗黄变剂1~2%,附着力加强剂1~2%,分散剂0.1~1%,稳定剂0.1~0.5%,消泡剂1~2%,改性改性氨基硅油10~15%;
30.所述固化剂为重量百分比为100%的改性异氰酸酯预聚物。
31.进一步的,所述改性异氰酸酯预聚物nco%含量百分比为15%~25%。
32.进一步的,所述改性异氰酸酯预聚物由下列重量百分比含量百分比的原料制成的:分子量255二苯基甲烷二异氰酸酯45~55%、分子量2000的多元醇或分子量3000的聚醚多元醇45~55%,磷系阻燃剂10~15%;其制备方法为:向反应釜中依次加二苯基甲烷二异氰酸酯、多元醇或聚醚多元醇,在温度70~90℃、搅拌速度100~200rpm下,反应3~4小时;加入磷系阻燃剂,在温度50~70℃、搅拌速度100~200rpm下,混合30~60分钟,即得到分子量2000的改性异氰酸酯预聚物。
33.进一步的,所述改性异氰酸酯预聚物由下列重量百分比含量百分比的原料制成的:分子量275的碳化二亚胺改性4,4二苯基甲烷二异氰酸酯50~60%,分子量2000的多元醇或分子量3000的聚醚多元醇45~55%,磷系阻燃剂10~15%;其制备方法为:向反应釜中依次碳化二亚胺改性4,4二苯基甲烷二异氰酸酯、多元醇或聚醚多元醇,在温度70~90℃、搅拌速度100~200rpm下,反应3~4小时;加入磷系阻燃剂,在温度50~70℃、搅拌速度100~200rpm下,混合30~60分钟,即得到分子量2000的改性异氰酸酯预聚物。
34.进一步的,所述改性异氰酸酯预聚物由下列重量百分比含量百分比的原料制成的:分子量255二苯基甲烷二异氰酸酯30~45%,分子量275的碳化二亚胺改性4,4二苯基甲烷二异氰酸酯30~45%,分子量2000的多元醇或分子量3000的聚醚多元醇45~55%,磷系阻燃剂10~15%;其制备方法为:向反应釜中依次加入二苯基甲烷二异氰酸酯、碳化二亚胺改性4,4二苯基甲烷二异氰酸酯、多元醇或聚醚多元醇,在温度70~90℃、搅拌速度100~200rpm下,反应3~4小时;加入磷系阻燃剂,在温度50~70℃、搅拌速度100~200rpm下,混合30~60分钟,即得到分子量2000的改性异氰酸酯预聚物。
35.其中,本发明所述防爆性能高抗冲击防层降组合型聚脲涂料组合物中所述色料与聚醚胺,均具有从有机聚合体的基体结构流体中,吸收冲击的充分弹性能力,当由弹性聚合体基本结构形状的分布,恒定的硬质超微粒子所形成的复合材料受到冲击时,被硬质微粒子的稠密层内部吸收,由此吸收冲击。
36.其中,本发明所述防爆性能高抗冲击防层降组合型聚脲涂料根据主剂、固化剂质量比调整来决定交联度,随着交联度的紧凑度高,耐化学性、耐磨耗性、伸长率、拉伸强度、扯裂强度、附着性、冲击性、耐寒性及耐热性等物性变高,如果交联度降低,就会使硬度减
少,耐热性减少,耐化学性减少,伸长率、拉伸强度及耐磨耗性等物性降低。
37.一种防爆性能高抗冲击防层降组合型聚脲涂料的施工方法,包括以下步骤:
38.步骤一、基材事先处理:首先清洁附着于基材表面的油污、灰尘、突起物、浆皮等污染物;
39.步骤二、基材调整涂敷:以重量比为1:1:3的主剂、固化剂、砂浆粉末充分搅拌后作为基材调整涂敷材料,涂覆于经过步骤一修护清洁处理后的基材上,填充于基材上的缝隙、裂纹;
40.步骤三、基础底漆涂敷:以50μm的厚度涂敷基础底漆;
41.步骤四、防爆性能高抗冲击防层降组合型聚脲涂料涂敷:涂覆防爆性能高抗冲击防层降组合型聚脲涂料,所述防爆性能高抗冲击防层降组合型聚脲涂料由所述主剂和固化剂按重量比为1.15:1混合而成;
42.步骤五、抗紫外线、抗黄变漆涂敷:室外以75μm(室内部分50μm)的厚度涂敷抗紫外线、抗黄变漆。
43.具体实施案例
44.实施案例1
45.防爆性能高抗冲击防层降组合型聚脲涂料,包括主剂和固化剂,所述主剂与固化剂按体积比为1.15:1混合而成;
46.其中,所述主剂按照重量百分比包括:聚醚胺62%,二乙基甲苯二胺21%,色料8%,防紫外线剂1%,附着力促进剂1%,分散剂0.5%,稳定剂0.5%,消泡剂1%,改性改性氨基硅油8%;
47.所述固化剂为重量百分比为100%的改性异氰酸酯预聚物。
48.进一步的,向反应釜中依次加入分子量255的二苯基甲烷二异氰酸酯40~50wt%、分子量2000的多元醇或分子量3000的聚醚多元醇45~55wt%,在温度70~90℃、搅拌速度100~200rpm下,反应3~4小时;加入磷系阻燃剂8~16wt%,在温度50~70℃、搅拌速度100~200rpm下,混合30~60分钟,得到分子量2000的改性异氰酸酯预聚物。
49.其中,所述二苯基甲烷二异氰酸酯的nco基含量百分比(%)优选为22%;所述nco基含量百分比(%)越高,硬度越高,相反,nco基含量百分比(%)越低,硬度越低。
50.根据主剂、固化剂质量比调整来决定交联度,随着交联度的紧凑度高,耐化学性、耐磨耗性、伸长率、拉伸强度、扯裂强度、附着性、冲击性、耐寒性及耐热性等物理性变高,如果交联度降低,就会使硬度减少,耐热性减少,耐化学性减少,伸长率、拉伸强度及耐磨耗性等物理性降低。
51.防爆性能高抗冲击防层降组合型聚脲涂料的施工方法,包括以下步骤:
52.步骤一、基材事先处理:将基材在25℃的温度下充分养护25天以上后,清洁附着于基材表面的油污、灰尘、突起物、浆皮等污染物;
53.步骤二、基材调整涂敷:以重量比为1:1:3的主剂、固化剂、砂浆粉末充分搅拌后作为基材调整涂敷材料,涂覆于经过步骤一修护清洁处理后的基材上,填充于基材上的缝隙、裂纹;
54.所述步骤二基材调整涂覆过程,因季节温度不同,不同固化时间如表1所示:
55.表1基材调整涂敷材料不同温度的固化时间
56.温度(℃)510152025时间(hr)2412842
57.步骤三、基础底漆涂敷:确认步骤二基材调整涂敷步骤中形成充分固化后,利用辊子或喷枪喷涂1次50μm的基础底漆;
58.步骤四、防爆性能高抗冲击防层降组合型聚脲涂料涂敷:涂覆防爆性能高抗冲击防层降组合型聚脲涂料,在25℃的温度下,在2小时以上且24小时以内清洁涂膜上的所有污染物,计算涂装面积及涂膜厚度5mm~10mm的需要量来以1.15:1的重量比混合主剂和固化剂来进行喷涂;
59.防爆性能高抗冲击防层降组合型聚脲涂料的主剂和固化剂在混合式聚脲专用喷涂设备内形成,作业条件为:喷嘴口径(扇形图案:0.024~0.048inch,圆形图案:0.020~0.086inch),喷射温度65~75℃,喷射压力2000~3000psi,若当进行喷涂时,如果因喷涂设备的喷枪或设备故障,造成过量喷涂主剂或固化剂中的一种,应立刻对受污染的部分进行擦拭,并进行养护处理,之后实施重新喷涂。
60.步骤五、抗紫外线、抗黄变漆涂敷:使用喷枪或辊子以室外75μm(室内部分50μm)的涂敷抗紫外线、抗黄变漆。
61.实施案例2
62.防爆性能高抗冲击防层降组合型聚脲涂料,包括主剂和固化剂,所述主剂与固化剂按体积比为1.12:1混合;
63.其中,所述主剂按照重量百分比包括:聚醚胺65%,二乙基甲苯二胺20%,色料8%,防紫外线剂1%,附着力促进剂1%,分散剂0.5%,稳定剂0.5%,消泡剂1%,改性氨基硅油6%;
64.所述固化剂为重量百分比为100%的改性异氰酸酯预聚物。
65.进一步的,向反应釜中依次加入分子量255的二苯基甲烷二异氰酸酯15~35wt%、加入分子量275的碳化二亚胺改性4,4二苯基甲烷二异氰酸酯45~60wt%、分子量2000的多元醇或分子量3000的聚醚多元醇45~55wt%,在温度70~90℃、搅拌速度100~200rpm下,反应3~4小时;加入磷系阻燃剂8~16wt%,在温度50~70℃、搅拌速度100~200rpm下,混合30~60分钟,得到分子量2000的改性异氰酸酯预聚物。
66.其中,所述二苯基甲烷二异氰酸酯的nco基含量百分比(%)优选为22%;所述nco基含量百分比(%)越高,硬度越高,相反,nco基含量百分比(%)越低,硬度越低。
67.实施案例3
68.防爆性能高抗冲击防层降组合型聚脲涂料,包括主剂和固化剂,所述主剂与固化剂按重量比为1.09:1混合;
69.其中,所述主剂按照重量百分比包括:聚醚胺62%,二乙基甲苯二胺23%,色料8%,防紫外线剂1%,附着力促进剂1%,分散剂0.5%,稳定剂0.5%,消泡剂1%,改性氨基硅油6%;
70.所述固化剂为重量百分比为100%的改性异氰酸酯预聚物。
71.进一步的,向反应釜中依次加入分子量255的二苯基甲烷二异氰酸酯15~35wt%、分子量275的碳化二亚胺改性4,4二苯基甲烷二异氰酸酯,分子量2000的多元醇或分子量3000的聚醚多元醇45~55wt%,在温度70~90℃、搅拌速度100~200rpm下,反应3~4小时;
加入磷系阻燃剂8~16wt%,在温度50~70℃、搅拌速度100~200rpm下,混合30~60分钟,得到分子量2000的改性异氰酸酯预聚物。
72.其中,所述二苯基甲烷二异氰酸酯的nco基含量百分比(%)优选为22%;所述nco基含量百分比(%)越高,硬度越高,相反,nco基含量百分比(%)越低,硬度越低。
73.实施案例4
74.防爆性能高抗冲击防层降组合型聚脲涂料,包括主剂和固化剂,所述主剂与固化剂按体积比为1.07:1混合;
75.其中,所述主剂按照重量百分比包括:聚醚胺63.5%,二乙基甲苯二胺18%,色料8%,防紫外线剂1%,附着力促进剂1%,分散剂0.5%,稳定剂0.5%,消泡剂1%,改性氨基硅油9%;
76.所述固化剂为重量百分比为100%的改性异氰酸酯预聚物。
77.进一步的,向反应釜中依次加入分子量255的二苯基甲烷二异氰酸酯40~50wt%、分子量2000的多元醇或分子量3000的聚醚多元醇45~55wt%,在温度70~90℃、搅拌速度100~200rpm下,反应3~4小时;加入磷系阻燃剂8~16wt%,在温度50~70℃、搅拌速度100~200rpm下,混合30~60分钟,得到分子量2000的改性异氰酸酯预聚物。
78.其中,所述二苯基甲烷二异氰酸酯的nco基含量百分比(%)优选为22%;所述nco基含量百分比(%)越高,硬度越高,相反,nco基含量百分比(%)越低,硬度越低。
79.实施案例5
80.防爆性能高抗冲击防层降组合型聚脲涂料,包括主剂和固化剂,所述主剂与固化剂按体积比为1.05:1混合;
81.其中,所述主剂按照重量百分比包括:聚醚胺56%,二乙基甲苯二胺19%,色料8%,防紫外线剂1%,附着力促进剂1%,分散剂0.5%,稳定剂0.5%,消泡剂1%,改性氨基硅油15%;
82.所述固化剂为重量百分比为100%的改性异氰酸酯预聚物。
83.进一步的,向反应釜中依次加入分子量255的二苯基甲烷二异氰酸酯40~50wt%、分子量2000的多元醇或分子量3000的聚醚多元醇45~55wt%,在温度70~90℃、搅拌速度100~200rpm下,反应3~4小时;加入磷系阻燃剂8~16wt%,在温度50~70℃、搅拌速度100~200rpm下,混合30~60分钟,得到分子量2000的改性异氰酸酯预聚物。
84.其中,所述二苯基甲烷二异氰酸酯的nco基含量百分比(%)优选为22%;所述nco基含量百分比(%)越高,硬度越高,相反,nco基含量百分比(%)越低,硬度越低。
85.比较案例1
86.普通聚脲组合物,包括主剂和固化剂,所述主剂与固化剂按体积比为1.1:1混合;
87.其中,所述主剂按照重量百分比包括:聚醚胺70.5%,二乙基甲苯二胺20%,色料8%,防紫外线剂1%,附着力促进剂1%,分散剂0.5%,稳定剂0.5%,消泡剂1%;
88.所述固化剂为重量百分比为100%的改性异氰酸酯预聚物。
89.进一步的,向反应釜中依次加入分子量255的二苯基甲烷二异氰酸酯40~50wt%、分子量2000的多元醇或分子量3000的聚醚多元醇45~55wt%,在温度70~90℃、搅拌速度100~200rpm下,反应3~4小时;加入磷系阻燃剂8~16wt%,在温度50~70℃、搅拌速度100~200rpm下,混合30~60分钟,得到分子量2000的改性异氰酸酯预聚物;其中,所述二苯基
甲烷二异氰酸酯的nco基含量百分比(%)优选为22%。
90.将上述实施案例1至实施案例5,以及比较例1,按防爆性能高抗冲击防层降组合型聚脲涂料组合物的混合比分别制作涂膜样片,所述涂膜试片长500mm、宽500mm,涂膜厚度为2mm,通过hg/t 3831-2006的试验方法测定上述涂膜试片的硬度试验、拉伸强度、伸长率、耐磨耗性、扯裂强度,试验结果如表2所示。
91.表2比较案例1和实施案例1至实施案例5的物理性质表
[0092][0093]
如上述表2所示,从实施案例1至实施案例5相比,比较案例1的防爆性能高抗冲击防层降组合型聚脲涂料组合物呈现出耐磨耗性好、拉伸强度强和扯裂强度相对低的物理性数值;
[0094]
实施案例1至实施案例5中,改性氨基硅油的添加量影响着摩擦系数的变化,随着添加量的增加,耐磨耗性越高,表面能值越低;
[0095]
实施案例5与实施案例1至实施案例4相比,实施案例5因过多改性氨基硅油的添加而使机械物性伸长率大幅度增加,但硬度、拉伸强度、扯裂强度等物性大大减少。:
[0096]
以上所述,仅为本发明较佳的具体实施方式,但本发明的保护范围并不局限于此,任何熟悉本技术领域的技术人员在本发明揭露的技术范围内,根据本发明的技术方案及其发明构思加以等同替换或改变,都应涵盖在本发明的保护范围之内。