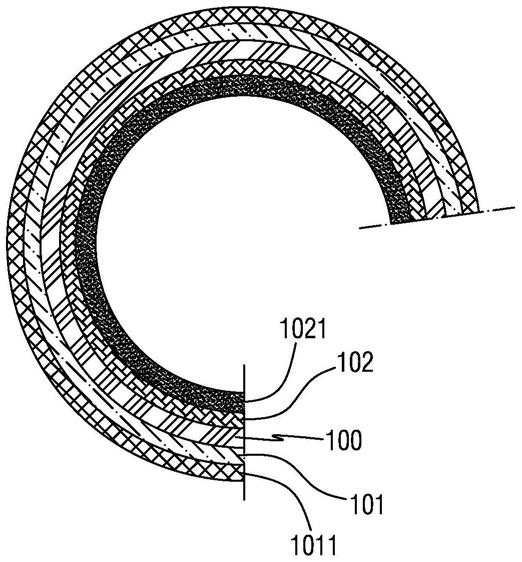
一种用于ab胶膜的离型膜
技术领域
1.本技术涉及保护膜领域,尤其涉及一种用于ab胶膜的离型膜。
背景技术:2.ab胶是以光学级pet(聚酯薄膜)为基材,一面(a面)涂布硅胶,另一面(b面)涂布oca光学胶,用于钢化玻璃保护的专用双面胶。其中,a面硅胶粘度较低,易于替换分离,用于贴合保护对象;b面oca光学胶是一层高粘胶层,具有良好的粘合性,用于贴合保护层。由于其双面具有粘性,因此在生产过程中双面都需要覆合离型膜,以便在卷材时相互隔离保护。
3.cn 110982437 a公开了一种ab胶膜的制备方法。包括第一离型层、第一胶粘剂层、第二胶粘剂层和第二离型层,所述第一胶粘剂层、第二胶粘剂层上下排布并直接粘合在一起,所述第一胶粘剂层的上侧粘结有所述第一离型层,所述第二胶粘剂层的下侧粘结有所述第二离型层。该现有技术的ab胶膜的制备方法包括以下步骤:步骤一、第一胶粘剂层的制备:将配制第一胶粘剂层用的丙烯酸胶粘剂溶液用微凹、逗号轴或狭缝挤出的方式涂布于第一离型层上,经烘箱干燥后与工程膜进行贴合收卷,制得第一胶粘剂层,且该第一胶粘剂层粘贴在所述第一离型层的下侧面上;步骤二、第二胶粘剂层的制备:剥离上述工程膜,并在制得的第一胶粘剂层上用逗号轴或狭缝挤出的方式涂布配制好的有机硅胶粘剂,经烘箱干燥后与第二离型层贴合收卷,有机硅胶粘剂形成第二胶粘剂层且位于所述第一胶粘剂层与所述第二离型层之间;最后,熟化处理,将步骤二形成的四层复合胶膜置于40~50℃的烘箱中,放置2~3d进行熟化,从而将第一离型层、第一胶粘剂层、第二胶粘剂层和第二离型层连接在一起。第一离型层、第二离型层可设置为氟素离型膜、硅系离型膜或非硅离型膜。上述现有技术的离型膜给出了三种表面处理方法,硅系、非硅系和氟系,覆盖了现有技术中离型膜所有的表面处理方法。离型膜主要目的是用于对胶粘剂层进行保护,使用的时候需要剥离,所以剥离的时候不可以连胶粘剂层一起剥离下来,因而离型膜对离型效果、粘接力、剥离力等有一定的要求。
4.图1显示了一种可用于本发明的ab胶膜卷材状态下的剖面结构示意图,其中包括ab胶基材100以及分别设置在ab胶基材100的两侧的低粘胶层101和高粘胶层102,低粘胶层101和高粘胶层102的外表面分别贴附有低粘胶层离型膜1011和高粘胶层离型膜1021。由于ab胶膜的一侧是高粘胶层102,另一侧是低粘胶层101,如果将低粘胶层101一侧先粘贴好配件,在高粘胶层102离型时会把低粘胶层101从已经粘好的配件上撕下来。如果先粘贴高粘胶层102,在高粘胶层102离型时很大的可能会先造成低粘胶层101的离型膜离型。所以一般情况下针对ab胶膜需要四种离型膜进行离型。具体区分如下:(1)高粘胶层先离型,其分别包括对高粘胶层具有轻离型力的离型膜,以及对低粘胶层具有中离型力的离型膜;(2)低粘胶层先离型,其分别包括对高粘胶层具有中离型力的离型膜,以及对低粘胶层具有轻离型力的离型膜。其中,现有技术中的离型膜通常都是对低粘胶层具有轻离型力的离型膜,其余三种离型膜现有技术中没有提供统一的解决方案。
技术实现要素:5.本技术要解决的技术问题是提供一种用于ab胶膜的离型膜,以减少或避免前面所提到的问题。
6.为解决上述技术问题,本技术提出了一种用于ab胶膜的离型膜,所述用于ab胶膜的离型膜是一种适于贴附在所述高粘胶层(102)的表面的对高粘胶层具有轻离型力的离型膜,所述离型膜包括离型膜基材以及涂布在所述离型膜基材的表面的离型剂层,所述离型剂层由下列重量份的原料制备而成的离型剂制成:60
‑
140重量份的聚丁二烯聚氨酯,45
‑
85重量份的聚丙烯酸酯树脂,10
‑
25重量份的甲基丙烯酸羟丙酯,25
‑
55重量份的甲基丙烯酸三氟乙酯活性单体稀释剂,20
‑
25重量份的2
‑
甲基
‑2‑
丙烯酸二十二烷基酯活性单体稀释剂,1
‑
5重量份的引发剂为2
‑
羟基
‑2‑
甲基
‑1‑
苯基
‑1‑
丙酮。
7.本发明还提供了另一种用于ab胶膜的离型膜,所述用于ab胶膜的离型膜是一种适于贴附在所述低粘胶层(101)的表面的对低粘胶层具有中离型力的离型膜,所述离型膜包括离型膜基材以及涂布在所述离型膜基材的表面的离型剂层,所述离型剂层由下列重量份的原料制备而成的离型剂制成:60
‑
140重量份的聚丁二烯聚氨酯,45
‑
85重量份的聚丙烯酸酯树脂,10
‑
25重量份的甲基丙烯酸羟丙酯,25
‑
55重量份的甲基丙烯酸三氟乙酯活性单体稀释剂,20
‑
25重量份的甲基丙烯酸十八烷基酯活性单体稀释剂,1
‑
5重量份的引发剂为2
‑
羟基
‑2‑
甲基
‑1‑
苯基
‑1‑
丙酮。
8.本发明还提供了又一种用于ab胶膜的离型膜,所述用于ab胶膜的离型膜是一种适于贴附在所述高粘胶层(101)的表面的对高粘胶层具有中离型力的离型膜,所述离型膜包括离型膜基材以及涂布在所述离型膜基材的表面的离型剂层,所述离型剂层由下列重量份的原料制备而成的离型剂制成:60
‑
140重量份的聚丁二烯聚氨酯,45
‑
85重量份的聚丙烯酸酯树脂,10
‑
25重量份的甲基丙烯酸羟丙酯,25
‑
55重量份的甲基丙烯酸三氟乙酯活性单体稀释剂,20
‑
25重量份的甲基丙烯酸十二烷基酯活性单体稀释剂,1
‑
5重量份的引发剂为2
‑
羟基
‑2‑
甲基
‑1‑
苯基
‑1‑
丙酮。
9.优选地,所述离型膜基材为三层共挤复合结构的聚酯薄膜,该三层共挤复合结构的聚酯薄膜包括表层、底层以及夹持在二者之间的中间层,所述离型剂层形成在所述聚酯薄膜的表层的外表面上。
10.优选地,所述离型膜基材的表面形成有活化涂层,所述离型剂层形成在所述活化涂层的表面上。
11.另外,本发明还提供了用于上述离型膜的制备方法,包括如下步骤:将除引发剂之外的离型剂成分按照前述实施例的配方均匀混合,最后加入引发剂,磁力搅拌120秒,获得离型剂;将离型剂均匀涂布到离型膜基材的表面,真空消泡1小时,n2条件下经紫外光照射固化120秒,固化形成离型剂层。
12.本发明提供了统一解决方案的三种适用于ab胶膜的离型膜,其采用不同链长的烷基丙烯酸酯作为活性单体稀释剂,利用不同链长的烷基丙烯酸酯对离型力进行调节,因而可以采用近似的含量比例和同样的工艺制备,而且制备的离型剂无硅油成分,不需要高温烘烤,杜绝了硅油成分转移现象。本发明采用了复合活性单体稀释剂,以含短链氟单体提高离型力,以长链烷基丙烯酸酯对离心力进行调节,以此制备的离型膜的离型力较低且附着力较高,离型性能优异。
附图说明
13.以下附图仅旨在于对本技术做示意性说明和解释,并不限定本技术的范围。其中,
14.图1显示了一种可用于本发明的ab胶膜卷材状态下的剖面结构示意图;
15.图2显示的是根据本发明的一个具体实施例的一种可用于ab胶膜的离型膜的结构示意图;
16.图3显示的是根据本技术的另一个具体实施例的离型膜的结构示意图;
17.图4显示的是根据本技术的又一个具体实施例的离型膜的结构示意图。
具体实施方式
18.为了对本技术的技术特征、目的和效果有更加清楚的理解,现对照附图说明本技术的具体实施方式。其中,相同的部件采用相同的标号。
19.下面仍然以图1所示ab胶膜为例,详细说明本发明的离型膜。正如背景技术所述,ab胶膜对应于两侧的高粘胶层和低粘胶层,可以获得高粘胶层先离型和低粘胶层先离型两种类别共四种离型膜,这四种离型膜中,对低粘胶层具有轻离型力的离型膜最为常见,可以采用现有的离型膜。
20.因而本发明关注于提供一种统一的解决方案,其可以分别提供对高粘胶层具有轻离型力的离型膜、对低粘胶层具有中离型力的离型膜以及对高粘胶层具有中离型力的离型膜。
21.图2显示的是根据本发明的一个具体实施例的一种可用于ab胶膜的离型膜的结构示意图,其包括离型膜基材10以及涂布在离型膜基材10的表面的离型剂层20。图2所示的离型膜是一种基本结构,其可以通用于上述三种离型膜。对应于前述三种离型膜,本发明分别提供了三种离型剂,通过三种不同的离型剂,分别制备获得适用于三种离型膜的离型剂层20。
22.当然,本领域技术人员应当理解,本发明的三种离型剂的大部分成分和形成原理是相同的,只是为了对应不同的需求,对某些成分进行了精细的调整,用以降低研发和制造成本。
23.实施例1
24.本实施例提供了一种适于贴附在图1所示高粘胶层102的表面的高粘胶层具有轻离型力的离型膜,其具体结构可以如图2所示,包括离型膜基材10以及涂布在所述离型膜基材10的表面的离型剂层20,所述离型剂层20由下列重量份的原料制备而成的离型剂制成:
25.60
‑
140重量份的聚丁二烯聚氨酯,45
‑
85重量份的聚丙烯酸酯树脂,10
‑
25重量份的甲基丙烯酸羟丙酯,25
‑
55重量份的甲基丙烯酸三氟乙酯活性单体稀释剂,20
‑
25重量份的2
‑
甲基
‑2‑
丙烯酸二十二烷基酯活性单体稀释剂,1
‑
5重量份的引发剂为2
‑
羟基
‑2‑
甲基
‑1‑
苯基
‑1‑
丙酮。
26.实施例1的离型剂是一种无硅油成分的紫外光固化离型剂,不需要高温烘烤,无硅油渗出,杜绝了硅油成分转移导致高粘胶或者低粘胶被拉起的现象。本发明采用了复合活性单体稀释剂,以含短链氟单体提高离型力,以二十二烷的长链烷基丙烯酸酯对离型力进行调节,以此制备的离型膜对于高粘胶而言,附着力高但离型力较低,离型性能优异。
27.实施例2
28.本实施例提供了一种适于贴附在图1所示低粘胶层101的表面的低粘胶层具有中离型力的离型膜,其具体结构可以如图2所示,包括离型膜基材10以及涂布在所述离型膜基材10的表面的离型剂层20,所述离型剂层20由下列重量份的原料制备而成的离型剂制成:
29.60
‑
140重量份的聚丁二烯聚氨酯,45
‑
85重量份的聚丙烯酸酯树脂,10
‑
25重量份的甲基丙烯酸羟丙酯,25
‑
55重量份的甲基丙烯酸三氟乙酯活性单体稀释剂,20
‑
25重量份的甲基丙烯酸十八烷基酯活性单体稀释剂,1
‑
5重量份的引发剂为2
‑
羟基
‑2‑
甲基
‑1‑
苯基
‑1‑
丙酮。
30.实施例2的离型剂是一种无硅油成分的紫外光固化离型剂,不需要高温烘烤,无硅油渗出,杜绝了硅油成分转移导致高粘胶或者低粘胶被拉起的现象。本发明采用了复合活性单体稀释剂,以含短链氟单体提高离型力,以十八烷的长链烷基丙烯酸酯对离型力进行调节,以此制备的离型膜的离型力中等且附着力较高,离型性能优异。
31.实施例3
32.本实施例提供了一种适于贴附在图1所示高粘胶层101的表面对高粘胶层具有中离型力的离型膜,其具体结构可以如图2所示,包括离型膜基材10以及涂布在所述离型膜基材10的表面的离型剂层20,所述离型剂层20由下列重量份的原料制备而成的离型剂制成:
33.60
‑
140重量份的聚丁二烯聚氨酯,45
‑
85重量份的聚丙烯酸酯树脂,10
‑
25重量份的甲基丙烯酸羟丙酯,25
‑
55重量份的甲基丙烯酸三氟乙酯活性单体稀释剂,20
‑
25重量份的甲基丙烯酸十二烷基酯活性单体稀释剂,1
‑
5重量份的引发剂为2
‑
羟基
‑2‑
甲基
‑1‑
苯基
‑1‑
丙酮。
34.实施例3的离型剂是一种无硅油成分的紫外光固化离型剂,不需要高温烘烤,无硅油渗出,杜绝了硅油成分转移导致高粘胶或者低粘胶被拉起的现象。本发明采用了复合活性单体稀释剂,以含短链氟单体提高离型力,以十二烷基丙烯酸酯对离型力进行调节,以此制备的离型膜的离型力中等且附着力较高,离型性能优异。
35.如前所述,为了节约研发和制造成本,实施例1~3提供了三种不同的离型剂,这三种离型剂的区别在于采用了不同链长的烷基丙烯酸酯作为活性单体稀释剂,利用不同链长的烷基丙烯酸酯对离型力进行调节,因而可以采用近似的含量比例和同样的工艺制备,从而为ab胶膜提供了统一的解决方案。
36.下面以具体实施例的方式详细说明适用于实施例1~3的离型膜的制备方法。
37.实施例4
38.将除引发剂之外的离型剂成分按照前述实施例的配方均匀混合,最后加入引发剂,磁力搅拌120秒,获得离型剂。
39.将离型剂均匀涂布到离型膜基材10的表面,真空消泡1小时,n2条件下经紫外光照射固化120秒,固化形成离型剂层。
40.实施例5
41.对实施例1~3的离型剂层20进行检测,发现本发明的离型剂层20在150℃以下具备良好的稳定性,无分解、脱离现象,在150℃~350℃区间仍然具备相当的热稳定性,超过350℃离型剂层开始分解、脱离。
42.实施例1的离型膜24小时的室温离型力为6.8g/25mm,附着力等级为0级,可用作轻离型膜;实施例2的离型膜24小时的室温离型力为26.0g/25mm,附着力等级为0级,可用作中
离型膜;实施例3的离型膜24小时的室温离型力为25.0g/25mm,附着力等级为0级,可用作中离型膜。
43.实施例6
44.对实施例1~3的离型剂层20进行对比测试,分别去除组分中的甲基丙烯酸三氟乙酯,以同样的工艺固化,所获得的涂层与高粘层胶结合力太大,完全不具备离型特性。
45.作为另一个对比,去除组分中的长链烷甲基丙烯酸酯,以同样的工艺固化,所获得的涂层与高粘胶结合力太小,太容易脱落,与本发明的离型剂层20不具备可比性。
46.实施例7
47.本实施例对离型膜基材10的结构进行了改进,例如,本发明可以在离型膜基材10上用于涂布离型剂层20的表面,形成了一层活化涂层30,如图3所示,其显示的是根据本技术的另一个具体实施例离型膜的结构示意图。设置活化涂层30的目的用于提高离型剂20的附着力,以利于与无硅油成分的离型剂的结合,避免硅油成分转移到高粘胶层102上导致高粘胶层102被拉起来的现象。
48.离型膜基材10优选由双向拉伸pet薄膜制成,其可以是图3所示的单层结构,也可以是图4所示的多层复合结构,其中图4显示的是根据本技术的又一个具体实施例的离型膜的结构示意图。在图4所示具体实施例中,本发明的离型膜基材10为三层共挤复合结构的聚酯薄膜,该三层共挤复合结构的聚酯薄膜可以包括表层11、底层12以及夹持在二者之间的中间层13。活化涂层30形成在聚酯薄膜的表层11的外表面上。离型剂涂覆在活化涂层30的表面形成离型剂层20。图3所示的单层结构的离型膜基材10的成分优选与图4所示的三层共挤复合结构的离型膜基材10的表层11的成分相同。
49.本发明的活化涂层30可以包含如下组分:丙烯酸树脂、二甲基甲硅烷基化硅石表面活性剂、乙醇胺表面侵蚀剂、聚季铵盐表面活性杀菌剂、非水溶性碳酸盐、三聚氰胺固化剂以及丙二醇溶剂。
50.其中,乙醇胺表面侵蚀剂可以对离型膜基材10的外表面形成一定的降解侵蚀,降低离型膜基材10的外表面的平整度,有利于活化涂层30中的亲水成分与离型膜基材10形成牢固的结合;而且乙醇胺在涂层固化过程中易于分解出气体,可使得活化涂层30形成蓬松多孔的结构。丙烯酸树脂具有亲水性,通过二甲基甲硅烷基化硅石表面活性剂进一步乳化,且该含硅表面活性剂与离型膜基材10可以获得很强的结合力。聚季铵盐表面活性杀菌剂可以降低固化后的涂层表面的表面张力,提高涂层对含长链硅烷的离型剂的吸附能力,避免离型剂脱离,且聚季铵盐具备杀菌功能,可以使离型剂层20长时间保持使用状态。三聚氰胺相对其它固化剂对水分不敏感,且与含长链硅烷离型剂的亲和性更好。非水溶性碳酸盐可以选择碳酸钙或者碳酸镁,需要避免与乙醇胺反应,也要避免溶解在水及其它水溶性成分中。
51.在一个具体实施例中,本发明的活化涂层30包含80
‑
100重量份的丙烯酸树脂、1
‑
2重量份的二甲基甲硅烷基化硅石、10
‑
15重量份的乙醇胺、0.5
‑
0.8重量份的聚季铵盐、5
‑
10重量份的非水溶性碳酸盐、1
‑
2重量份的三聚氰胺以及80
‑
100重量份的丙二醇。
52.本发明的上述活化涂层,可以通过如下步骤制备获得。
53.首先,将80
‑
100重量份的丙烯酸树脂、1
‑
2重量份的二甲基甲硅烷基化硅石、10
‑
15重量份的乙醇胺、0.5
‑
0.8重量份的聚季铵盐、5
‑
10重量份的非水溶性碳酸盐、1
‑
2重量份的
三聚氰胺以及80
‑
100重量份的丙二醇均匀混合之后,通过旋涂或者喷涂方式涂覆在离型膜基材10的外表面,在70
‑
120℃下固化1
‑
2小时,从而在离型膜基材10的外表面获得预涂层。
54.在一个具体实施例中,所述预涂层的厚度为5
‑
10μm,优选添加的非水溶性碳酸盐为碳酸钙或者碳酸镁,粒径为0.5
‑
1.0μm。
55.之后,对预涂层进行等离子表面活化处理。等离子表面活化处理为本领域常用处理方式,在本发明的一个实施例中通过氧气进行活化处理,氧气流量不低于100sccm进行活化处理,真空度0.1
‑
0.2mbar时间为30s
‑
60s。
56.然后,对活化处理之后的预涂层进行酸洗。优选采用6
‑
8mol/l的盐酸50
‑
60摄氏度浸泡预涂层10
‑
20分钟。通过酸洗,预涂层上裸露的碳酸盐成分可以部分溶解,可以进一步获得多孔的结构,进一步提高了涂层的表面活性,有利于后续与离型剂的紧密结合。
57.最后用水冲洗、烘干,获得本发明的活化涂层30。用水冲洗时间10
‑
20分钟,50
‑
60度烘干30分钟。
58.通过在本发明的离型膜基材10的表面形成的多孔的亲水性活化涂层30,离型膜基材10的表面活性和亲水性大大提高,有利于与含长链硅烷离型剂紧密结合,可以避免离型剂脱离。
59.实施例8
60.本实施例对离型膜基材10的成分进行了改进,用以对离型剂层20提供更好的附着力,同时使得本发明中的离型膜基材10具备优异的加工性能、良好的拉伸强度和透光率以及阻燃性能。
61.在图3所示离型膜基材10中,本发明的离型膜基材10优选为含有二氧化硅和碱土金属硅酸盐以及聚二甲基硅氧烷的pet薄膜。类似的,在图4所示离型膜基材10中,表层11优选为含有二氧化硅和碱土金属硅酸盐以及聚二甲基硅氧烷的pet薄膜。下面以图3所示离型膜基材10进行详细说明,本领域技术人员可以将其类推至图4所示离型膜基材10的表层11中。
62.在另一个具体实施例中,pet薄膜中的二氧化硅的含量为0.3wt%~1.5wt%,碱土金属硅酸盐的含量为0.05wt%~0.5wt%,聚二甲基硅氧烷的含量为0.2wt%~1.2wt%。
63.pet薄膜中的二氧化硅可以提高聚酯薄膜的透光性、加工性能以及强度,同时可以与活化涂层中的硅烷成分产生吸附作用,避免活化涂层脱离。碱土金属硅酸盐可以降低由于聚酯薄膜中二氧化硅含量增高导致的热收缩性,所述碱土金属硅酸盐优选为硅酸镁或者硅酸钙,最优选为硅酸镁。聚二甲基硅氧烷可以提高聚酯中二氧化硅的分散性,避免团聚,有利于减少无机粒子的添加量,提高聚酯薄膜的光学性能,另外,聚二甲基硅氧烷还可以与活化涂层30中的二甲基甲硅烷基化硅石产生更强的附着力。
64.二氧化硅以及碱土金属硅酸盐的硅原子由于结合了聚二甲基硅氧烷的硅原子,聚二甲基硅氧烷另一端的高分子可以与聚酯的烷烃结合,有利于将二氧化硅和碱土金属硅酸盐均匀分散保持在聚酯内部。碱土金属硅酸盐中的碱土元素易于与聚酯中常用磷类化合物催化剂、稳定剂、阻燃剂等形成具有适当强度的相互作用的络合物,除了可以提高二氧化硅的分散性之外,还可以提高二氧化硅以及碱土金属硅酸盐在聚酯中的结合力,有利于提高聚酯薄膜的光线透过率。另外如前所述,硅酸镁或硅酸钙之类的碱土金属硅酸盐的加入,可以降低聚酯薄膜的收缩率,尤其适用于添加到光学领域聚酯薄膜之中,有利于提高基膜的
光学性能。
65.需要提及的是,由于二氧化硅的添加,制得的聚酯薄膜的收缩率会发生较为明显的变化,对于热收缩薄膜是相当有利的。然而对于离型膜来说,要求薄膜的收缩率保持较低的水平较为理想。本发明中,通过硅酸盐成分与二氧化硅的结合,一方面提高分散性,另一方面利用碱土金属降低添加了二氧化硅的薄膜的收缩率,进而提高薄膜的光学性能。
66.在一个优选实施例中,pet薄膜中的二氧化硅优选采用二氧化硅气凝胶。二氧化硅气凝胶是一种具有多孔、无序、具有纳米量级连续网络结构的低密度二氧化硅气凝胶,比表面积比普通二氧化硅大很多,用现有技术的磷酸酯偶联剂、硅烷偶联剂(例如乙烯基三乙氧基硅烷、乙烯基三甲氧基硅烷、乙烯基三(β
‑
甲氧乙氧基)硅烷等)比普通二氧化硅更加难以分散。由于密度非常低,很容易漂浮,无法分散到聚酯内部。气凝胶的多孔结构可以通过聚二甲基硅氧烷产生强大的结合力,增大了气凝胶的密度,可以使气凝胶沉入聚酯内部。碱土金属硅酸盐的比表面积也很大,疏松多孔特性与气凝胶类似,但是分散性却较好,利用碱土金属硅酸盐的硅元素成分与气凝胶产生的吸附,可以提高气凝胶的分散性,避免团聚。
67.添加有二氧化硅或二氧化硅气凝胶、碱土金属硅酸盐以及聚二甲基硅氧烷的pet薄膜,其粘度相对本体聚酯变化很小,有利于保持聚酯薄膜参数的稳定性;还可降低抗粘连粒子的用量;提高了聚酯薄膜的加工性能、拉伸强度、透光率和阻燃性能。另外也可以改善聚酯薄膜的光泽度、耐磨、耐高温、隔热性能。
68.综上所述,本发明提供了统一解决方案的三种适用于ab胶膜的离型膜,其采用不同链长的烷基丙烯酸酯作为活性单体稀释剂,利用不同链长的烷基丙烯酸酯对离型力进行调节,因而可以采用近似的含量比例和同样的工艺制备,而且制备的离型剂无硅油成分,不需要高温烘烤,杜绝了硅油成分转移现象。本发明采用了复合活性单体稀释剂,以含短链氟单体提高离型力,以长链烷基丙烯酸酯对离心力进行调节,以此制备的离型膜的离型力较低且附着力较高,离型性能优异。
69.本领域技术人员应当理解,虽然本技术是按照多个实施例的方式进行描述的,但是并非每个实施例仅包含一个独立的技术方案。说明书中如此叙述仅仅是为了清楚起见,本领域技术人员应当将说明书作为一个整体加以理解,并将各实施例中所涉及的技术方案看作是可以相互组合成不同实施例的方式来理解本技术的保护范围。
70.以上所述仅为本技术示意性的具体实施方式,并非用以限定本技术的范围。任何本领域的技术人员,在不脱离本技术的构思和原则的前提下所作的等同变化、修改与结合,均应属于本技术保护的范围。