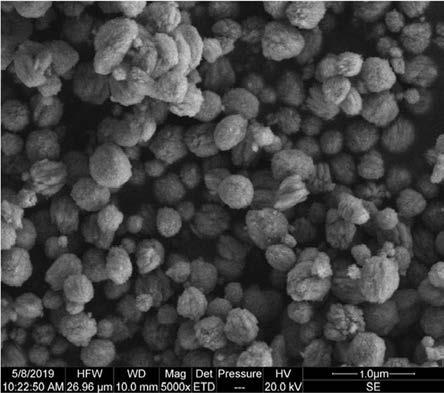
[0001]
本发明属于纳米稀土材料制备技术领域,特别涉及一种微波条件下氟化二氧化铈抛光粉的制备方法。
背景技术:[0002]
稀土氧化铈抛光粉的抛光原理是化学机械抛光,对表面进行物理研磨的同时也不断进行着化学反应,这使得氧化铈抛光粉拥有传统抛光粉难以企及的高抛光效率和优异的抛光质量。此外,氧化铈抛光粉硬度适中、使用寿命长、对抛光表面污染小,故在光学仪器玻璃、磁盘玻璃基片、光学仪器玻璃和显像管等抛光领域,氧化铈成为众多抛光材料中的最优之选。随着科技的进步,用于高精尖设备上的元器件表面的粗糙度要求不断提高,相应地对稀土氧化铈抛光粉的性能及种类要求也越来越高。以何种制备方法以及怎样的生产工艺条件可以制备出抛光性能更加优越的氧化铈抛光粉,已成为国内外关注的焦点。
[0003]
目前市场上多对二氧化铈进行氟化来改善其抛光性能。采用沉淀-焙烧的液相反应法制备氧化铈抛光粉时,在合成抛光粉的前驱体时添加各种氟化剂,如h2sif6、hf或nh4f等,从而在抛光粉中引入氟离子。氟元素的加入并未改变二氧化铈立方萤石结构,但改变了二氧化铈抛光粉颗粒的形貌,呈现出类球形,明显地提高了抛光粉的抛光性能。但是仍存在着明显的团聚现象,抛光粉颗粒呈现出类葡萄状,且粒径分布不均匀。现有技术中往往采用在沉淀反应体系中添加辅助试剂的方式来改善团聚情况。这种方式往往会带来额外的成本和操作步骤,有着耗费时间、增加设备以及降低产品纯度的风险。
技术实现要素:[0004]
本发明针对现有的液相沉淀法对氧化铈颗粒形貌控制的不足,提供了一种微波环境下合成粒径均匀、分散性较好的球形纳米二氧化铈的制备方法。
[0005]
本发明采用的技术方案如下:一种微波条件下氟化二氧化铈抛光粉的制备方法,包括以下步骤:(1)取ce(no3)3·
6h2o、nh4hco3和nh4f溶于去离子水中,配置成水溶液;(2)微波预热:取ce(no3)3·
6h2o水溶液以微波方式预热至温度为55℃~75℃;取nh4f水溶液加入到ce(no3)3·
6h2o溶液中搅拌均匀;(3)沉淀反应:取nh4hco3水溶液加入步骤(2)制得的混合溶液中;接着,在持续搅拌条件下、以微波方式恒温反应60min~90min生成前驱体ce2(co3)3;微波恒温温度为55℃~75℃;(4)陈化:步骤(3)停止搅拌,将制得的前驱体ce2(co3)3于微波恒温中继续陈化;陈化时间为45min~75min,微波恒温温度为70℃~90℃;(5)前驱体制粉:将步骤(4)陈化后的前驱体ce2(co3)3进行真空抽滤得到沉淀,将沉淀恒温干燥,并研磨成纳米粉状颗粒;其中干燥温度为100℃~140℃,干燥时间为20h~28h;(6)焙烧:将步骤(5)制得的颗粒进行焙烧,焙烧温度为850℃~950℃,焙烧时间为4h~6h;焙烧结束之后随炉冷却制室温;
(7)研磨:将步骤(6)制得的成品粉末进行二次研磨,得到成品氟化二氧化铈抛光粉。
[0006]
更进一步,nh4f的量为其氟元素质量占最终成品质量的5%~7%;此外,nh4f可用hf、naf或kf等氟化物代替。
[0007]
更进一步,nh4hco3和ce(no3)3·
6h2o的摩尔比为4.5:1以上。
[0008]
进一步,关于微波条件的独特设置在上述方法中作用的部分说明如下:微波条件下,电磁波辐射到ce(no3)3溶液内部,利用极性介质的介电损耗发热,在极短的时间内加剧分子运动与碰撞,使得预热过程升温速度很快。参加反应的极性介质吸收微波后降低了反应活化能,促进了沉淀反应进程,反应效率提高。微波条件实现分子水平上的均匀加热,反应体系中各处的温度均匀,有助于陈化过程中所有晶粒同步生长为均匀的颗粒,形成均匀分散性体系;并且获得结晶度更高的前驱体晶粒。上述结论在后续的具体实施方式中得以验证。
[0009]
与现有技术相比,本发明具有以下有益效果:1.本发明的前驱体ce2(co3)3沉淀反应在微波条件下进行,减弱沉淀颗粒的团聚,细化产品颗粒粒度;相比现有操作技术,工艺流程更为方便简化,同时也更为环保,更容易得到高纯度的产品。
[0010]
2.合理控制上述微波处理后前驱体的焙烧温度,可制备出粒径均匀、表面圆润、分散性较好的微米级球形氧化铈颗粒,有利于减少被抛光件表面划痕等缺陷。
附图说明
[0011]
图1为本发明实施例1制得的水浴条件下前驱体碳酸铈的sem图。
[0012]
图2为本发明实施例2制得的微波条件下前驱体碳酸铈的sem图。
[0013]
图3为本发明实施例1制得的水浴条件下氟化二氧化铈的sem图。
[0014]
图4为本发明实施例2制得的微波条件下氟化二氧化铈的sem图。
[0015]
图5为本发明实施例1、2制得的氟化二氧化铈颗粒的x射线衍射(xrd)图谱。
[0016]
图6为本发明实施例1制得的水浴条件下氟化二氧化铈的粒度图。
[0017]
图7为本发明实施例2制得的微波条件下氟化二氧化铈的粒度图。
[0018]
图8为本发明实施例3制得的氟化二氧化铈的sem图。
[0019]
图9为本发明实施例3及相同条件下其它微波强度下制得的氟化二氧化铈的粒度分布宽度r折线图。
[0020]
图10为本发明实施例4制得的氟化二氧化铈的sem图。
[0021]
图11为本发明实施例5制得的氟化二氧化铈的sem图。
[0022]
图12为本发明实施例2、4、5制得的氟化二氧化铈颗粒的x射线衍射(xrd)图谱。
[0023]
图13为本发明实施例4制得的氟化二氧化铈的粒度图。
[0024]
图14为本发明实施例5制得的氟化二氧化铈的粒度图。
[0025]
图15为本发明实施例2、4、5制得的氟化二氧化铈的中位粒径d
50
折线图;其中三个关键坐标数据信息为(850,8.308),(900,6.964),(1000,43.5)。
[0026]
图16为本发明实施例2、4、5制得的氟化二氧化铈的粒度分布宽度r折线图;其中三个关键坐标数据信息为(850,3.87),(900,2.10),(1000,1.87)。
具体实施方式
[0027]
为了使本领域技术人员更好地理解本发明的技术方案并能予以实施,下面结合具体实施例和附图对本发明作进一步说明,但所举实施例不作为对本发明的限定。
[0028]
下述实施例中所述的实验方法和检测方法,如无特殊说明,均为常规方法;所述的试剂和原料,如无特殊说明,均可在市场购买得到。
[0029]
实施例1(无微波对照组)一种水浴条件下氟化二氧化铈抛光粉的制备方法,包括以下步骤:(1)取ce(no3)3·
6h2o、nh4hco3和nh4f溶于去离子水中,配置500ml的0.0582mol/l硝酸铈水溶液、125ml的1.047mol/l碳酸氢铵水溶液和125ml的0.126mol/l氟化铵水溶液;本发明主要研究微波、焙烧等条件对抛光粉制备的影响,并不研究上述成分含量对抛光粉的影响,上述成分用量为本发明研究过程中的一种优选方案,其选择范围满足如下条件即可:a.nh4f的量为其氟元素质量占最终成品质量的5%~7%;b.nh4hco3和ce(no3)3·
6h2o的摩尔比为4.5:1以上;c.nh4f可用hf、naf或kf等氟化物代替;以下实施例都采用相同的浓度和用量;(2)取上述(1)配置的硝酸铈溶液放入水浴槽中水浴加热,加热温度至65℃,并取上述(1)中氟化铵溶液加入其中,并磁力搅拌均匀;(3)取上述(1)配置的碳酸氢铵溶液,加入上述(2)中得到的硝酸铈和氟化铵混合溶液,磁力搅拌并以水浴方式于65℃恒温下反应75min;通过上述三步制得前驱体;(4)上述(3)反应结束之后,停止搅拌,取上述(3)中混合悬浮液以水浴方式于80℃恒温下陈化60min;(5)上述(4)陈化结束之后,取其悬浮液真空抽滤,分离出固体沉淀产物;(6)取上述(5)所得固体沉淀产物,将其置于鼓风干燥箱中,干燥温度为120℃,干燥时间为24h;(7)取上述(6)干燥后沉淀产物,用玛瑙研磨成纳米粉状颗粒;(8)取上述(7)粉末,置于马弗炉中以900℃焙烧,焙烧时间为5h,焙烧结束之后随炉冷却制室温;(9)取上述(8)产品,进一步用玛瑙研磨成粉状颗粒,得到成品氟化二氧化铈抛光粉。
[0030]
实施例2一种微波条件下氟化二氧化铈抛光粉的制备方法,包括以下步骤:(1)取ce(no3)3·
6h2o、nh4hco3和nh4f溶于去离子水中,配置500ml的0.0582mol/l硝酸铈水溶液、125ml的1.047mol/l碳酸氢铵水溶液和125ml的0.126mol/l氟化铵水溶液;(2)取上述(1)配置的硝酸铈溶液放入微波反应器中微波加热,加热温度至65℃,并取上述(1)中氟化铵溶液加入其中,并磁力搅拌均匀;(3)取上述(1)配置的碳酸氢铵溶液,加入上述(2)中得到的硝酸铈和氟化铵混合溶液,磁力搅拌并以微波方式于65℃恒温下反应75min;步骤(2)、(3)中微波加热温度相同,通过上述三步制得前驱体;(4)上述(3)反应结束之后,停止搅拌,取上述(3)中混合悬浮液以微波方式于80℃恒温
下陈化60min;(5)上述(4)陈化结束之后,取其悬浮液真空抽滤,分离出固体沉淀产物;(6)取上述(5)所得固体沉淀产物,将其置于鼓风干燥箱中,干燥温度为120℃,干燥时间为24h;(7)取上述(6)干燥后沉淀产物,用玛瑙研磨成纳米粉状颗粒;(8)取上述(7)粉末,置于马弗炉中以900℃焙烧,焙烧时间为5h,焙烧结束之后随炉冷却制室温;(9)取上述(8)产品,进一步用玛瑙研磨成粉状颗粒,得到成品氟化二氧化铈抛光粉。
[0031]
实施例1、2对比分析如下:(1)如图1所示为实施例1制得的水浴条件下前驱体碳酸铈的sem图,如图2所示为实施例2制得的微波条件下前驱体碳酸铈的sem图;通过两张sem图对比可知,微波条件下制得的碳酸铈颗粒更圆润、颗粒的分散性更好。
[0032]
(2)如图3所示为实施例1制得的水浴条件下氟化二氧化铈的sem图,如图4所示为实施例2制得的微波条件下氟化二氧化铈的sem图;通过对比可知,水浴条件下制得的二氧化铈颗粒出现了大规模的团聚现象,而微波条件下制得的二氧化铈颗粒分散性较好,说明微波条件对于抛光粉颗粒的团聚有明显的抑制作用;并且微波条件可以细化抛光粉颗粒粒径。
[0033]
(3)如图5所示为施例1、2制得的氟化二氧化铈颗粒的x射线衍射(xrd)图谱,从图中可以看出,不同反应条件下,xrd曲线的特征峰位置均与ceo2的标准卡片pdf#43-1002相一致,表明微波反应条件下产物仍然保持立方萤石晶体结构;微波条件下x射线衍射峰的强度较强,说明微波使得产物的结晶度提高。
[0034]
(4)如图6所示为实施例1制得的水浴条件下氟化二氧化铈的粒度图,如图7所示为实施例2制得的微波条件下氟化二氧化铈的粒度图;两图对比可知,水浴条件下制得的二氧化铈颗粒粒径分布极不均匀,出现双峰;而微波条件下制得的二氧化铈颗粒粒径分布较窄、较均匀;可见微波反应条件起到均匀颗粒粒径的作用。
[0035]
实施例3一种微波条件下氟化二氧化铈抛光粉的制备方法,包括以下步骤:(1)取ce(no3)3·
6h2o、nh4hco3和nh4f溶于去离子水中,配置500ml的0.0582mol/l硝酸铈水溶液、125ml的1.047mol/l碳酸氢铵水溶液和125ml的0.126mol/l氟化铵水溶液;(2)取上述(1)配置的硝酸铈溶液放入微波反应器中微波加热,加热温度至45℃,并取上述(1)中氟化铵溶液加入其中,并磁力搅拌均匀;(3)取上述(1)配置的碳酸氢铵溶液,加入上述(2)中得到的硝酸铈和氟化铵混合溶液,磁力搅拌并以微波方式于45℃恒温下反应75min;步骤(2)、(3)中微波加热温度相同,通过上述三步制得前驱体;(4)上述(3)反应结束之后,停止搅拌,取上述(3)中混合悬浮液以微波方式于60℃恒温下陈化60min;(5)上述(4)陈化结束之后,取其悬浮液真空抽滤,分离出固体沉淀产物。
[0036]
(6)取上述(5)所得固体沉淀产物,将其置于鼓风干燥箱中,干燥温度为120℃,干燥时间为24h;
(8)取上述(7)粉末,置于马弗炉中以900℃焙烧,焙烧时间为5h,焙烧结束之后随炉冷却制室温。
[0037]
(9)取上述(8)产品,进一步用玛瑙研磨成粉状颗粒,得到成品氟化二氧化铈抛光粉。
[0038]
实施例2、3对比分析如下:实施例3主要用于研究不同强度微波条件下对于抛光粉制备性能的影响,与实施例2相比,其变量为不同步骤中微波温度的不同,具体的,实施例2中步骤(2)、(3)微波温度为65℃,步骤(4)微波温度为80℃;实施例3中步骤(2)、(3)微波温度为45℃,步骤(4)微波温度为60℃;如图8所示为实施例3制得的氟化二氧化铈的sem图,与图4比较可知,在微波强度较弱的反应条件下,制得的产物颗粒粒径不均匀、部分颗粒发生团聚,与图3对比,其情况要优于没有微波条件;这一点充分说明微波要想取得较好的效果其强度是重要影响因素;为此,本发明还重点在50℃、55℃、65℃、75℃和80℃等不同微波温度条件下进行了沉淀反应研究,即将实施例3中步骤(2)、(3)微波温度改变为50℃、55℃、65℃、75℃和80℃进行实验研究;对应将实施例3中步骤(4)陈化过程微波温度改变为65℃、70℃、80℃、90℃和95℃;其中在50℃和80℃沉淀反应微波温度下制备得到的氟化二氧化铈粉体颗粒的sem图与45℃下的sem图(图8)相似,产物颗粒发生局部团聚,55℃、65℃、75℃分散性较好;图9为不同沉淀微波反应温度下制得的氟化二氧化铈颗粒的粒度分布宽度r折线图,由r折线图分布可知,当沉淀反应温度为55~75℃时,相应的微波辐射强度使得产物颗粒的粒度分布宽度r保持在较低水平。
[0039]
实施例4一种微波条件下氟化二氧化铈抛光粉的制备方法,步骤同实施例2,不同之处在于,焙烧温度为850℃。
[0040]
实施例5一种微波条件下氟化二氧化铈抛光粉的制备方法,步骤同实施例2,不同之处在于,焙烧温度为1000℃。
[0041]
实施例2、4、5对比分析如下:实施例2、4、5主要研究焙烧温度对于抛光粉性能的影响;(1)如图10和图11所示分别为实施例4和5制得的氟化二氧化铈的sem图,与图4对比分析可知,随着焙烧温度的升高,产物颗粒粒径不断增大;当焙烧温度较低(850℃)时,抛光粉颗粒出现局部团聚。
[0042]
(2)如图12所示为实施例2、4、5制得的氟化二氧化铈颗粒的x射线衍射(xrd)图谱,当焙烧温度在850℃~900℃时,产物的x射线衍射峰的强度较强,说明二氧化铈的结晶度良好。
[0043]
(3)如图13和图14所示分别为实施例4和5制得的氟化二氧化铈的粒度图,与图7对比分析可知,当焙烧温度在900~1000℃时,产物颗粒粒径分布较均匀。
[0044]
(4)如图15所示为实施例2、4、5制得的氟化二氧化铈的中位粒径d
50
折线图,当焙烧温度在850℃~900℃时,产物的中位粒径d
50
均保持较小水平;且随着焙烧温度进一步地升高,中位粒径d
50
急剧增大。
[0045]
(5)如图16所示为实施例2、4、5制得的氟化二氧化铈的粒度分布宽度r折线图,低温时随着温度的升高粒度分布宽度r急剧减小,当焙烧温度在900~1000℃时,产物的粒度分布宽度r保持较低水平。
[0046]
综上所述,将微波条件下生成的前驱体碳酸铈颗粒在850℃~950℃的合适温度下焙烧,可制得结晶度高、颗粒粒径小且粒径分布均匀、分散性良好的氟化二氧化铈抛光粉。
[0047]
总述本发明方法中通过如下核心条件控制实现了氟化二氧化铈抛光粉保持立方萤石晶体结构的同时,改善了颗粒的中位粒径(6.964~8.308μm)、粒度分布宽度(1.87~2.10)等;制得的颗粒结晶度更高、更圆润、分散性更好。
[0048]
(1)在步骤(2)、(3)中,即前驱体制备中两次介入微波调控;(2)在陈化过程中介入微波调控;(3)严格控制焙烧温度。
[0049]
以上所述实施例仅表达了本发明的几种实施方式,其描述较为具体和详细,但并不能因此而理解为对发明专利范围的限制。应当指出的是,对于本领域的普通技术人员来说,在不脱离本发明构思的前提下,还可以做出若干变形和改进。这里无需也无法对所有的实施方式进行穷举。倘若这些变形和改进属于本发明权利要求及其等同技术的范围之内,这些变形和改进仍处于本发明的保护范围之中。