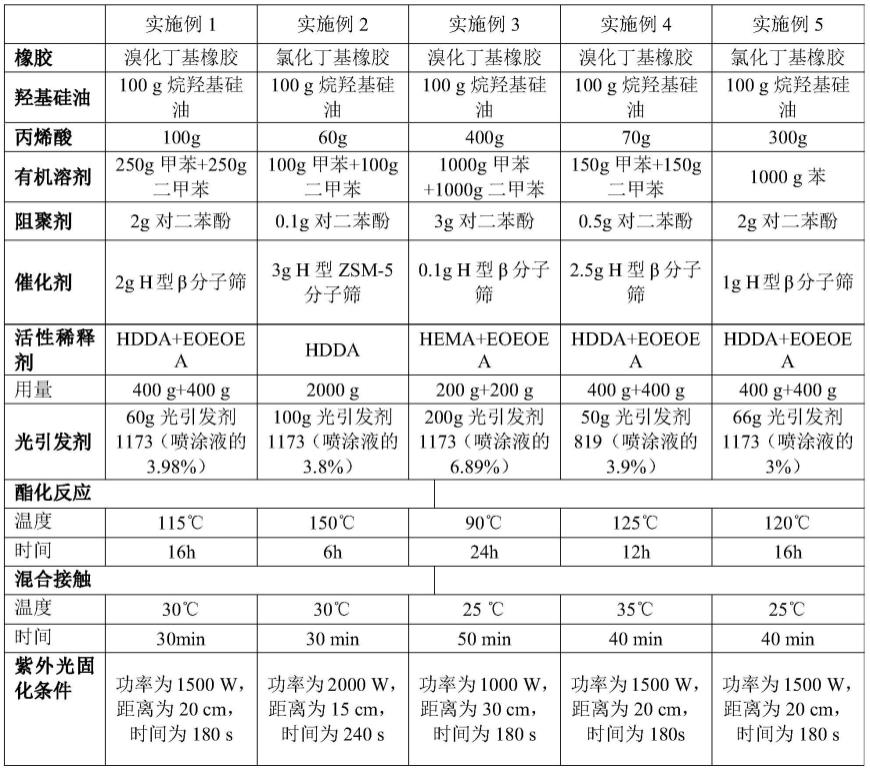
1.本发明涉及药用胶塞生产技术领域,具体地,涉及一种覆膜胶塞用涂覆液组合物,一种酯化反应制备涂覆液的方法以及由该方法制备得到的覆膜胶塞用涂覆液,一种覆膜胶塞及其制备方法。
背景技术:2.胶塞生产企业在胶塞生产过程中,常会对胶塞进行硅化处理,利用硅油的润滑性可以防止胶塞在生产、运输的过程中发生粘结。
3.但硅化处理所带来的技术缺陷在于,药品灌装完成后需要带塞高压灭菌,硅油残留会从胶塞中释放并溶出到药品中;另外,硅化还会造成不溶性颗粒和可见异物检查不合格而返工或者报废的情况。
4.为此,国内外科学工作者进行了大量工作。
5.cn107629240a公开了一种免硅化胶塞的制备工艺,其采用钛酸酯等均相催化剂,反应后难于回收和重复再用,并且易水解失活;其采用高温热固化的方式对涂层进行固化,固化周期较长,且固化温度较高;另外,覆膜胶塞主要针对酸碱度较高的药品包装,而且易出现膜材粘附力不强,膜易脱落,膜材弹性差,覆膜胶塞硬度较大,易出现自密封差、针刺性能差等问题,同时价格也较贵。
6.因此,有必要对现有技术中的覆膜胶塞制备方法进行优化和改进。
技术实现要素:7.本发明的目的是为了克服现有技术存在的膜材粘附力不强、膜易脱落的问题,硅油残留会从胶塞中释放出来的缺陷问题,提供一种覆膜胶塞用涂覆液组合物、酯化反应制备涂覆液的方法和涂覆液、覆膜胶塞及其制备方法,该覆膜胶塞由于其表面的覆膜不发生脱落,具有更好的附着力,与盐酸氯丙嗪之间具有更好的抗耐性。
8.为了实现上述目的,本发明第一方面提供了一种覆膜胶塞用涂覆液组合物,其中,所述涂覆液组合物中含有两者以上混合保存或者各自独立保存的以下组分:
9.羟基硅油、丙烯酸、催化剂、阻聚剂和有机溶剂;
10.其中,所述催化剂为分子筛催化剂;
11.相对于100重量份的所述羟基硅油,所述丙烯酸的含量为60-400重量份,所述催化剂的含量为0.1-3重量份,所述阻聚剂的含量为0.1-3重量份,所述有机溶剂的含量为200-2000重量份。
12.本发明第二方面提供了一种采用前述所述的覆膜胶塞用涂覆液组合物制备覆膜胶塞用涂覆液的方法,其中,在有机溶剂存在下,将含有羟基硅油、丙烯酸、催化剂和阻聚剂的各组分进行酯化反应。
13.本发明第三方面提供了一种由前述所述的方法制备得到的覆膜胶塞用涂覆液。
14.本发明第四方面提供了一种制备覆膜胶塞的方法,其中,该方法包括:
15.(1)将前述所述的覆膜胶塞用涂覆液与活性稀释剂和光引发剂进行混合接触,得到喷涂液;
16.(2)将所述喷涂液涂覆于待喷涂胶塞的至少部分区域,得到喷涂后的胶塞;
17.(3)将所述喷涂后的胶塞进行光固化处理。
18.本发明第五方面提供了一种由前述所述的方法制备得到的覆膜胶塞。
19.通过上述技术方案,本发明具有如下优势:
20.本发明提供的覆膜胶塞的制备工艺简单,不影响待喷涂胶塞的品质,无需重复处理,易于实施,效果明显。
21.并且,本发明获得的覆膜胶塞可免于胶塞生产工艺中的硅化工序,耐化学药品性能良好,并且可以将胶塞与药物、药液隔离开,避免相互扩散与渗透,降低微粒污染,保护药物稳定性,满足胶塞与药品抗耐性要求,具有非常可靠的生物安全性和生物稳定性。
22.进一步地,通过本发明的实施例结果可知,相比传统硅油硅化胶塞,本发明所述胶塞表面摩擦系数低,由于其表面的涂层不发生脱落,与常用药物例如盐酸氯丙嗪之间具有更好的抗耐性。
具体实施方式
23.在本文中所披露的范围的端点和任何值都不限于该精确的范围或值,这些范围或值应当理解为包含接近这些范围或值的值。对于数值范围来说,各个范围的端点值之间、各个范围的端点值和单独的点值之间,以及单独的点值之间可以彼此组合而得到一个或多个新的数值范围,这些数值范围应被视为在本文中具体公开。
24.在本发明中,除非特殊说明,常压是指一个大气压。
25.本发明第一方面提供了一种覆膜胶塞用涂覆液组合物,其中,所述涂覆液组合物中含有两者以上混合保存或者各自独立保存的以下组分:
26.羟基硅油、丙烯酸、催化剂、阻聚剂和有机溶剂;
27.其中,所述催化剂为分子筛催化剂;
28.相对于100重量份的所述羟基硅油,所述丙烯酸的含量为60-400重量份,所述催化剂的含量为0.1-3重量份,所述阻聚剂的含量为0.1-3重量份,所述有机溶剂的含量为200-2000重量份。
29.本发明的发明人经过研究发现:在有机溶剂存在下,将含有羟基硅油、丙烯酸、催化剂和阻聚剂的各组分进行酯化反应,其中,羟基硅油中的羟基与丙烯酸中的羧基在酸性催化剂的作用下发生酯化反应,制备得到覆膜胶塞用涂覆液,将该涂覆液固化在待喷涂胶塞的至少部分区域,形成覆膜胶塞,由于涂覆液直接在胶塞表面固化,该覆膜胶塞表面的覆膜不发生脱落,具有更好的附着力,与盐酸氯丙嗪之间具有更好的抗耐性。
30.另外,在本发明中,采用酯化反应制备聚合物,因此,采用酸催化剂,相对于浓硫酸催化剂,分子筛催化剂具有绿色无污染、不腐蚀设备、易于回收的优点。
31.根据本发明,所述催化剂为h型β-分子筛催化剂或h型zsm-5分子筛催化剂;其中,所述h型β-分子筛催化剂的硅铝分子(sio2/al2o3)摩尔比为20-60,优选为25-40;所述h型zsm-5分子筛催化剂的硅铝分子(sio2/al2o3)摩尔比为25-300,优选为38-100。
32.根据本发明,优选情况下,相对于100重量份的所述羟基硅油,所述丙烯酸的含量为70-300重量份,所述催化剂的含量为0.5-2.5重量份,所述阻聚剂的含量为0.5-2.5重量份,所述有机溶剂的含量为300-1500重量份。
33.更优选情况下,相对于100重量份的所述羟基硅油,所述丙烯酸的含量为80-200重量份,所述催化剂的含量为1.0-2.0重量份,所述阻聚剂的含量为1.0-2.0重量份,所述有机溶剂的含量为400-1000重量份。
34.更进一步优选情况下,相对于100重量份的所述羟基硅油,所述丙烯酸的含量为80-150重量份,所述催化剂的含量为1.0-2.0重量份,所述阻聚剂的含量为1.0-2.0重量份,所述有机溶剂的含量为500-1000重量份。
35.在本发明中,将羟基硅油、丙烯酸、催化剂、阻聚剂和有机溶剂的含量限定为前述范围之内,能够使得采用该涂覆液组合物制备得到覆膜胶塞用涂覆液,将该涂覆液固化在待喷涂胶塞的至少部分区域,能够使得形成的覆膜胶塞表面的覆膜不发生脱落,具有更好的附着力,与盐酸氯丙嗪之间具有更好的抗耐性。另外,在本发明中,如果组分阻聚剂过量,会使得产物聚合从而影响紫外光固化反应,同时会发生阻聚剂的变色等副反应。
36.根据本发明,所述羟基硅油选自二甲基羟基硅油、烷羟基硅油、二羟基聚二甲基硅氧烷和107硅橡胶中的一种或多种;优选为烷羟基硅油。
37.优选地,所述二甲基羟基硅油在25℃下黏度为20-5000cst;
38.优选地,所述烷羟基硅油在20℃下黏度为1000-100000cst;
39.优选地,所述二羟基聚二甲基硅氧烷在20℃下黏度为2000-100000cst;
40.优选地,所述107硅橡胶在20℃下黏度为750-100000cst。
41.根据本发明,所述阻聚剂选自苯酚、2,6-二叔丁基对甲酚和对二苯酚中的一种或多种,优选为对二苯酚。
42.根据本发明,所述有机溶剂选自苯、乙酸乙酯、甲苯和二甲苯中的一种或多种,优选为甲苯和二甲苯的混合溶剂,且当所述溶剂为甲苯和二甲苯的混合溶剂时,甲苯和二甲苯的用量的重量比为1:1。
43.本发明第二方面提供了一种采用前述所述的覆膜胶塞用涂覆液组合物制备覆膜胶塞用涂覆液的方法,其中,在有机溶剂存在下,将含有羟基硅油、丙烯酸、催化剂和阻聚剂的各组分进行酯化反应。
44.应当说明的是,在本发明中,所述有机溶剂在进行涂覆之前的溶液配制中是必须的,但是,本发明中的产品在作为商品进行售卖时,为了便于运输存储等,组分羟基硅油、丙烯酸、催化剂、阻聚剂可以与所述有机溶剂分开存储,在进行涂覆应用之前按照本发明的方法进行制备即可。
45.本发明第二方面中所涉及的各组分的种类均与本发明第一方面中所述的组合物中的组分的种类对应相同,为了避免重复,本发明在此不再赘述,本领域技术人员不应理解为对本发明的限制。
46.根据本发明,所述酯化反应的条件包括:温度为90-150℃,优选为100-140℃,更优选为115-120℃;时间为6-24h,优选为8-18h,更优选为14-16h。
47.根据本发明,所述的方法还包括:将经所述酯化反应得到的混合物进行固液分离,得到覆膜胶塞用涂覆液。
48.本发明对所述固液分离的步骤没有特别地限定,可以为本领域的常规选择,只要能够实现将所述酯化反应后得到的混合物中的液体和固体从空间上分开的目的即可。本发明中的固液分离的目的是将催化剂从所述酯化反应后得到的混合物中分离出来。优选地,所述固体分离的方式为离心和/或过滤。对于实现所述离心和/或过滤的设备,本领域的技术人员可根据实际需要进行选择。
49.本发明第三方面提供了一种由前述所述的方法制备得到的覆膜胶塞用涂覆液。
50.本发明第四方面提供了一种制备覆膜胶塞的方法,其中,该方法包括:
51.(1)将前述所述的覆膜胶塞用涂覆液与活性稀释剂和光引发剂进行混合接触,得到喷涂液;
52.(2)将所述喷涂液涂覆于待喷涂胶塞的至少部分区域,得到喷涂后的胶塞;
53.(3)将所述喷涂后的胶塞进行光固化处理。
54.根据本发明,本领域的技术人员熟知胶塞制备过程中所述喷涂液需要涂覆的区域,所述部分区域包括但不限于胶塞的冠部面、颈部面和底部面,本领域技术人员可根据实际需要进行涂覆。
55.根据本发明,本领域的技术人员熟知,在将所述喷涂液进行胶塞涂覆之前,胶塞的制备过程还包括但不限于以下步骤:混炼橡胶、橡胶出片、模压硫化成型、分切和清洗烘干。进一步地,必要的话,本发明提供的制备覆膜胶塞的方法还可以包括:将固化处理后的胶塞进行冲切、清洗、灭菌等工艺。
56.根据本发明,所述胶塞的材质为溴化丁基橡胶或氯化丁基橡胶。
57.根据本发明,在步骤(1)中,所述混合接触的条件包括:温度为20-40℃,时间为10-60min;优选地,温度为25-35℃,时间为20-40min;所述混合接触的方式为搅拌和/或超声分散。
58.根据本发明,所述光引发剂选自2-羟基-2-甲基-1-苯基-1-丙基酮(光引发剂1173)、1-羟基-环己基-苯基甲酮(光引发剂184)、2,4,6-三甲基苯甲酰基二苯基氧化膦(光引发剂tpo)、苯偶酰二甲基缩酮和双(2,4,6-三甲基苯甲酰基)苯基氧化膦(光引发剂819)中的至少一种;优选地,所述光引发剂为光引发剂1173或光引发剂819。
59.根据本发明,所述光引发剂的用量为喷涂液的1-8重量%,优选为2-6重量%,更优选为3-4重量%。
60.根据本发明,所述活性稀释剂选自甲基丙烯酸-β-羟乙酯(hema)、1,6-己二醇二丙烯酸酯(hdda)、三丙烯酸三羟甲基丙酯、三丙二醇二丙烯酸酯、乙氧基乙氧基乙基丙烯酸酯(eoeoea)、乙氧化壬基苯酚丙烯酸酯和丙烯酸异辛酯中的一种或多种;优选地,所述活性稀释剂为hdda和eoeoea的混合物,且hdda和eoeoea的用量的质量比为1:1。
61.根据本发明,相对于100重量份的所述羟基硅油,所述活性稀释剂的含量为400-2000重量份,优选为500-1500重量份,更优选为800-1000重量份。
62.根据本发明,优选地,所述固化处理采用紫外光固化方式进行。
63.根据本发明,所述紫外光固化采用中压汞灯进行;
64.根据本发明一种优选实施方式,所述紫外光固化的条件包括:中压汞灯的功率为300-2000w,照射距离为10-50cm,固化时间为60-300s。在本发明中,所述紫外光固化可以在惰性气氛下,也可以在含氧气氛下进行,为了降低生产成本,所述紫外光固化在空气中进
行。在该种优选实施方式下,经紫外光固化的胶塞具有更低的表面摩擦系数,具有更好的抗紫外线、耐化学药品和耐老化性能。
65.根据本发明,所述待喷涂胶塞的材质选自异戊二烯橡胶、丁基橡胶和卤化丁基橡胶中的至少一种。
66.根据本发明一种特别优选的实施方式,所述的采用前述所述的覆膜胶塞用涂覆液组合物制备覆膜胶塞用涂覆液的方法包括:
67.覆膜胶塞用涂覆液组合物:相对于100重量份的所述羟基硅油(具体为烷羟基硅油),所述丙烯酸的含量为90-110重量份,所述催化剂(h型β分子筛,硅铝分子摩尔比为25,圆柱状)的含量为1.5-2.0重量份,所述阻聚剂(对二苯酚)的含量为1.5-2重量份,所述活性稀释剂(hdda+eoeoea)的含量为750-850重量份,所述有机溶剂(甲苯质量:二甲苯质量=1:1)的含量为450-650重量份。
68.本实施例的覆膜胶塞的制备工艺,具体步骤如下:
69.(1)按上述重量配比将烷羟基硅油、丙烯酸、催化剂和对二苯酚溶解在甲苯和二甲苯中进行酯化反应(酯化反应条件包括:温度为115-120℃,时间为14-16h),制得混合物溶液;
70.(2)将上述混合物溶液进行离心;
71.(3)将上述混合物溶液与hdda、eoeoea混合均匀,制得涂覆液;
72.(4)将上述涂覆液与4重量%(以制得的涂覆液的总量计)的光引发剂1173进行混合接触(混合接触条件包括:温度为28-32℃,时间为28-32min),制得喷涂液;
73.(5)将配制好的喷涂液装进喷硅设备,对硫化后的胶片进行冠部面喷涂;
74.(6)对喷涂后的胶塞进行紫外光固化处理,中压汞灯的功率为1000-1500w,照射距离为20-22cm,固化时间为150-200s;
75.(7)将处理后的胶塞进行冲切、清洗、灭菌工艺。
76.结果采用本发明特别优选的实施方式制备得到的覆膜胶塞由于其表面的覆膜不发生脱落,具有更好的附着力,与盐酸氯丙嗪之间具有更好的抗耐性。
77.本发明第五方面提供了一种由前述所述的方法制备得到的覆膜胶塞。
78.根据本发明,所述覆膜胶塞包括待喷涂胶塞以及涂覆在所述待喷涂胶塞至少部分区域的涂覆膜。
79.根据本发明,所述涂覆膜的厚度为30-80nm,优选为30-60nm,更优选为30-41nm,更进一步优选为34-36nm。
80.根据本发明,所述覆膜胶塞的表面摩擦系数为0.7-1.2,优选为0.7-1.1,优选为0.7-1,更进一步优选为0.7416-0.7896。
81.以下将通过实施例对本发明进行详细描述。
82.以下实施例和对比例中:
83.胶塞的材质:溴化丁基橡胶和氯化丁基橡胶购自安徽华峰医药橡塑有限公司,牌号分别为hfg-08b、hfg-10;
84.二甲基羟基硅油购买自北京百灵威科技有限公司;
85.烷羟基硅油、二羟基聚二甲基硅氧烷和107硅橡胶购买自山东大易化工有限公司;
86.丙烯酸购买自北京百灵威科技有限公司;
87.β分子筛、zsm-5分子筛购买自天津南化催化剂有限公司;
88.活性稀释剂:hdda、hema、eoeoea购买自天津天骄化工有限公司;
89.光引发剂:光引发剂1173、光引发剂819、tpo、光引发剂184均购自北京百灵威科技有限公司;
90.甲苯、二甲苯购买自北京化工厂;
91.对二苯酚购买自北京百灵威科技有限公司;
92.盐酸氯丙嗪为购买自北京百灵威科技有限公司;
93.紫外光固化机牌号为ldst13002-11az,购自北京鸿昌机电设备有限公司;
94.本发明中进行硅油微粒测试采用的是购买自天津大学精密仪器厂的型号为gwj-4的仪器。
95.以下制备过程中的室温指25
±
1℃。
96.实施例1
97.本实施例在于说明采用本发明的覆膜组合物制备涂覆液,以及采用该涂覆液制备覆膜胶塞。具体地,包括将覆膜组合物制备得到涂覆液,在清洗烘干的胶塞表面涂覆所述涂覆液以及涂层光固化处理的步骤。
98.本实施例的覆膜胶塞的材质为溴化丁基橡胶。
99.其中,覆膜组合物的组成为:烷羟基硅油100g、丙烯酸100g、h型β分子筛催化剂(硅铝分子摩尔比为25,圆柱状)2g、对二苯酚2g、甲苯250g、二甲苯250g。
100.其中,涂覆液的制备方法包括:
101.(1)按上述重量配比将烷羟基硅油、丙烯酸、h型β分子筛催化剂和对二苯酚溶解在甲苯和二甲苯的混合溶液中进行酯化反应,其中,酯化反应条件包括:温度为115℃,时间为16h,制得混合物溶液;
102.(2)将上述混合物溶液进行离心分离,得到覆膜胶塞用涂覆液。
103.其中,覆膜胶塞的方法包括:
104.(3)将上述覆膜胶塞用涂覆液与hdda、eoeoea混合均匀,制得混合液;其中,相对于100g的烷羟基硅油,hdda400g、eoeoea 400g;
105.(4)将上述混合液与4重量%(以制得的涂覆液的总量计)的光引发剂1173进行混合接触,其中,混合接触条件包括:温度为30℃,时间为30min,制得喷涂液;
106.(5)将配制好的喷涂液装进喷硅设备,对硫化后的胶塞进行冠部面喷涂;
107.(6)对喷涂后的胶塞进行紫外光固化处理,其中,中压汞灯的功率为1500w,照射距离为20cm,固化时间为180s;
108.(7)将处理后的胶塞进行冲切、清洗、灭菌工艺。
109.具体工艺条件列于表1。
110.结果制备得到覆膜胶塞的性质如表2所示。
111.实施例2-7
112.本实施例在于说明采用本发明的覆膜组合物制备涂覆液,以及采用该涂覆液制备覆膜胶塞。
113.按照与实施例1相同的方法制备覆膜组合物、涂覆液和覆膜胶塞,所不同之处在于:覆膜组合物中的组分和组分含量,涂覆液中的组分和组分含量,以及制备条件进行改
变,具体,如表1和表2所示。
114.对比例1
115.按照与实施例1相同的方法制备覆膜组合物、涂覆液和覆膜胶塞,所不同之处在于:将h型β分子筛催化剂(硅铝分子摩尔比为25,圆柱状)替换为二月桂酸二丁基锡(浓度为98%,重量2g),具体,如表1和表2所示。
116.对比例2
117.按照与实施例1相同的方法制备覆膜组合物、涂覆液和覆膜胶塞,所不同之处在于:覆膜组合物中的各个组分含量不在本发明限定的范围之内,具体,如表1和表2所示。
118.对比例3
119.采用传统硅化方法处理胶塞,即按照二甲基硅油含量0.01-0.03mg/cm2配制二甲基硅油喷涂液,在胶塞清洗前后,利用喷涂设备对胶塞表面进行喷涂作业,使得二甲基硅油吸附在胶塞表面,以起到润滑的作用。
120.结果制备得到覆膜胶塞的性质如表2所示。
121.表1
[0122][0123]
表1(续)
[0124]
[0125][0126]
备注h型β分子筛,硅铝摩尔比为25,圆柱状;h型zsm-5分子筛,硅铝摩尔比为38,三叶草状。
[0127]
表2
[0128] 涂覆膜的厚度(nm)覆膜胶塞的表面摩擦系数实施例1350.7542实施例2721.1345实施例3781.1546实施例4390.9854实施例5410.8695实施例6360.7677实施例7360.7416对比例1391.3211对比例2841.3445对比例3301.3246
[0129]
通过上述的结果可以看出,相对于对比例1-3,本发明所提供的胶塞具有较低的表面摩擦系数。
[0130]
测试例1
[0131]
涂层附着力检测:采用划格法检测涂层附着力,评价标准如表3所示:
[0132]
表3
[0133][0134]
测试结果列于表4。
[0135]
测试例2
[0136]
将以上制备例和对比例中制备得到的胶塞进行硅油微粒测试,方法为:取同批次两组三批注射液胶塞成品,进行硅油微粒测试(参考国家食品药品监督管理局颁布的包装材料不溶性微粒测定法ybb00272016中的光阻法),取平均值,测试结果列于表4。
[0137]
测试例3
[0138]
将以上制备例和对比例中制备得到的胶塞对放在置于安剖瓶中的盐酸氯丙嗪进行包装处理,倒置,在恒温和恒湿条件下(60℃,75%rh)进行10天和30天高温试验,比较浊度(参考中华人民共和国药典2000年版二部附录
ⅸ
),测试结果列于表4。
[0139]
表4
[0140][0141]
注:硅油微粒中,≥10μm表示每1ml输液中含10μm以上的不溶性微粒个数,≥25μm表示每1ml输液中含25μm以上的不溶性微粒个数;
[0142]
浊度为<0.5表示浊度均值低于0.5号浊度标准液的值;浊度为0.5-1表示浊度均值介于0.5号浊度标准液-1号浊度标准液的值之间。
[0143]
通过表4的结果可以看出,相对于对比例1-3,本发明所提供的胶塞由于其表面的含硅化合物不发生脱落,具有更好的附着力,与盐酸氯丙嗪之间具有更好的抗耐性。
[0144]
以上详细描述了本发明的优选实施方式,但是,本发明并不限于此。在本发明的技术构思范围内,可以对本发明的技术方案进行多种简单变型,包括各个技术特征以任何其它的合适方式进行组合,这些简单变型和组合同样应当视为本发明所公开的内容,均属于本发明的保护范围。