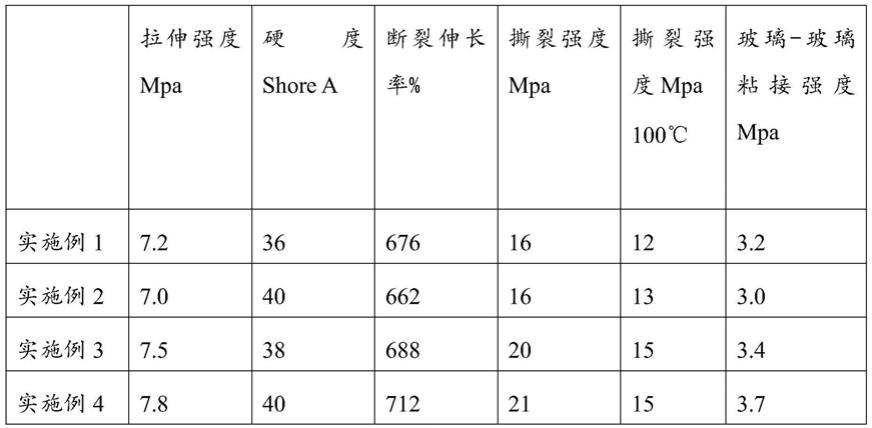
1.本发明涉及有机粘接剂的技术领域,尤其涉及一种可喷涂的自粘型液体硅橡胶制剂及其制备方法。
背景技术:2.硅橡胶是以线形聚有机硅氧烷为基础聚合物(生胶),加入交联剂,补强填料及其他配合剂,经配合、硫化,形成的弹性体。硅橡胶按其商品形态,分为混炼硅橡胶与液体硅橡胶两大类。液体硅橡胶与混炼硅橡胶不同,是由中等聚合度的线形聚有机硅氧烷为基础聚合物配合填料、各种助剂及添加剂配制的具有自流平性或触变性的基料。液体硅橡胶又称双组份加成性硅橡胶。
3.液体硅橡胶被广泛用于电子、机械、文物、工艺品、汽车、航空航天等多个领域。如用于水晶胶、聚氨脂、环氧树脂等的成型模具、注塑成型工艺、蛋糕模具等硅胶制品,在电子工业上广泛用作电子元器件的防潮、托运、绝缘的涂覆及灌封材料,对电子元件及组合件起防尘、防潮、防震及绝缘保护作用。如采用透明凝胶灌封电子元器件,不但可起到防震防水保护作用,还可以看到元器件并可以用探针检测出元件的故障,进行更换,损坏了的硅凝胶可再次灌封修补。还可用于制造石膏、蜡、环氧树脂、聚酯树脂、聚氨酯树脂和低熔点合金等材料的制品成型模具,应用于人造革的高频压花、鞋的面和底造型、工艺美术的制造、陶瓷、玩具行业、家具、家用电器电子元件业复制以及石膏、水泥材料的成型、腊制品的成型、模特儿的制造、材料的制模等。
4.但是由于它的粘接性较差,在作为灌封、涂覆、镶嵌材料使用时,通常需要对基材做底涂处理或添加增粘剂,因此导致液体硅橡胶在粘接剂的领域应用不多,且相对来说,制备工艺较为复杂,使用成本高,特别是粘接性能差,局限了其应用。
5.中国专利申请2016106421624公开了一种可喷涂的自粘型液体硅橡胶的制备方法,该制备方法包括以下步骤:将含有硅氢键的硅氢化合物与含环氧基烯丙基类化合物的碳碳双键摩尔比为1:5
‑
5:1的两种物质混合,加热到60℃通氮气保护后得到混合液以备用;取100g混合液,加入0.1
‑
2g阻聚剂搅拌均匀;搅拌均匀后,再用5
‑
10g的甲苯与0.02
‑
0.1g的2000ppm铂金催化剂混合,缓慢滴加到反应器中,边搅拌边加热;滴加完后控制反应温度在60
‑
100℃之间并反应1
‑
5h;加入1
‑
3g活性炭吸附0.5
‑
2h,最后将反应物抽滤脱除低分子得到偶联剂;将偶联剂、含环氧基偶联剂和乙烯基偶联剂按质量比为100:5
‑
40:4
‑
35的比例配制得到增粘剂;在100g液体硅橡胶中,加入0.5
‑
10g增粘剂,混合均匀经溶剂稀释到20
‑
40%固含量后得到喷涂用的自粘液体硅橡胶。
6.中国专利申请201910800917.2公开了一种自润滑加成型液体硅橡胶,所述液体硅橡胶包括如下重量份的原料:120
‑
200份含烯基聚硅氧烷;1
‑
15份氢化聚硅氧烷;30
‑
80份气相白炭黑;10
‑
30份硅氮烷白炭黑处理剂;1
‑
30份甲基苯基硅油;0.004
‑
0.06份si
‑
h加成催化剂;0.03
‑
0.6份抑制剂。本发明通过筛选基胶、组分a和组分b中含烯基聚硅氧烷以及氢化聚硅氧烷的种类和用量,本发明通过原料筛选、配方设计来控制渗油速率和产品性能,从而
提供一种兼具高的抗撕裂强度(≥45kn/m)和低的永久压缩变形率(≤20%)的加成型液体硅橡胶,同时渗油稳定,能保持长久的自润滑效果。
7.再如中国专利申请202010690113.4公开了一种加成型液体硅橡胶增粘剂的制备方法,包括如下步骤:将含氢聚硅氧烷和含苯乙烯基的酯类化合物在含铂催化剂的作用下反应,反应完成加入抑制剂,得到增粘剂。
8.目前国内虽然对加成型粘接性液体硅橡胶专利申请比较多,但这些专利申请多集中于聚硅氧烷及其衍生物作为基料的制备,虽然硅氧烷成本低,但是也具有粘接性能差的特点,往往需要增粘剂配合使用,而增粘剂要么组份复杂,要么对催化剂不友好,同时,在高温下,它们的稳定性不好,导致粘接性能下降,这严重影响了加成型粘接性液体硅橡胶的生产和推广。特别是针对陶瓷或玻璃用品,亟需环保、粘接性能和稳定性良好的液体硅橡胶粘接剂。
技术实现要素:9.针对上述技术中存在的不足之处,本发明提供一种可喷涂的自粘型液体硅橡胶制剂及其制备方法,该制剂及方法通过对液体硅橡胶的配方改进,提高液体硅橡胶的粘接性能和稳定性,特别满足陶瓷及玻璃制品之间的粘接。
10.本发明的另一个目的是提供一种可喷涂的自粘型液体硅橡胶制剂及其制备方法,该制剂及方法具有高温稳定性,在50
‑
80℃下能够保持良好的粘接性能,并具备可喷涂的特性,使用方便。
11.为实现上述目的,本发明是这样实现的:
12.一种可喷涂的自粘型液体硅橡胶制剂,其特征在于所述液体硅橡胶制剂,其是通过有将100
‑
120份聚二甲基硅氧烷作为基料、混合40
‑
60份氢化苯乙烯
‑
异戊二烯嵌段共聚物作为改性剂、30
‑
40份气相法白炭黑、0.8
‑
2份改性单体三羟甲基丙烷三丙烯酸酯、0.6
‑
1.5份辅助单体苯乙烯、0.1
‑
0.5份催化剂过氧化氢、加入0.02
‑
0.1份的2000ppm铂金催化剂和20
‑
45份水制得。
13.本发明的液体硅橡胶制剂中,反应后的氢化苯乙烯
‑
异戊二烯嵌段共聚物分子链是星型的,没有主链和侧链之分,同时,聚二甲基硅氧烷作为与氢化苯乙烯
‑
异戊二烯嵌段共聚物发生接枝反应,作为氢化苯乙烯
‑
异戊二烯嵌段共聚物的支链,不仅增加了液体硅橡胶的分子量,在稳定的星型基础上,支链增加了制剂的粘接性能,由此大大提高液体硅橡胶制剂的粘接性能,对陶瓷、玻璃等光滑表面具有足够的吸附力和粘接性能。
14.这是因为,在本发明的制备中,有两个反应过程,一是依靠氢化苯乙烯
‑
异戊二烯嵌段共聚物分子链上的聚丙烯结构单元在过氧化物存在下发生裂解形成自由基,在辅助单体苯乙烯的存在下,与多官能度改性单体三羟甲基丙烷三丙烯酸酯发生反应,形成星型的聚合物共聚物,分子上的羰基不是接枝在嵌段上,而是作为共聚物的臂,起到支化的作用,由此能够提高制剂的稳定性和粘接性能;二是聚二甲基硅氧烷与氢化苯乙烯
‑
异戊二烯嵌段共聚物发生接枝反应,聚二甲基硅氧烷作为支链接枝在氢化苯乙烯
‑
异戊二烯嵌段共聚物的烷基部位,由此增加分子链的长度和支链,从而大幅度提高粘接性能,能够在低浓度的情况下具有足够的粘接力,保证了可喷涂仍具有良好的粘接性能。
15.所述聚二甲基硅氧烷是粘度为3
‑
8万的聚二甲基硅氧烷。
16.所述氢化苯乙烯
‑
异戊二烯嵌段共聚物,其数均分子量为10~30万。
17.所述铂金催化剂为2000ppm的karstedt催化剂。
18.进一步,所述制剂还可加入偶联剂,所述偶联剂为kh
‑
560、kh
‑
566、kh
‑
567中的任意一种或任意组合。
19.一种可喷涂的自粘型液体硅橡胶制剂的制备方法,其特征在于该方法包括如下步骤:
20.步骤一,溶解共聚物,将氢化苯乙烯
‑
异戊二烯嵌段共聚物粉碎成小颗粒,颗粒外径不大于1cm,向反应釜中先加入基料聚二甲基硅氧烷,然后分批次加入氢化苯乙烯
‑
异戊二烯嵌段共聚物颗粒,控制温度不超过130℃,开动搅拌器;
21.步骤二,制备星型共聚物,升温至160
‑
200℃,再向反应釜中注入过氧化氢,等待10
‑
15min,再注入改性单体三羟甲基丙烷三丙烯酸酯和辅助单体苯乙烯,持续搅拌30min,这个过程是依靠氢化苯乙烯
‑
异戊二烯嵌段共聚物分子链上的聚丙烯结构单元在过氧化物存在下发生裂解形成自由基,在辅助单体苯乙烯的存在下,与多官能度改性单体三羟甲基丙烷三丙烯酸酯发生反应,形成星型的聚合物共聚物。
22.步骤三,接枝,然后降温至100
‑
120℃,加入30
‑
40份气相法白炭黑、0.02
‑
0.1份的2000ppm铂金催化剂和20
‑
45份水,混合持续搅拌45
‑
60min,出料,即得到自粘型液体硅橡胶制剂。此步骤中,聚二甲基硅氧烷与氢化苯乙烯
‑
异戊二烯嵌段共聚物发生接枝反应,聚二甲基硅氧烷作为支链接枝在氢化苯乙烯
‑
异戊二烯嵌段共聚物上,增加分子链的长度和支链数量,由此可以提高粘接性能。
23.在该制备方法中,先以过氧化氢为催化剂制备星型共聚物,此时保持适当的温度是促进反应顺利进行的前提(通常是150℃以上),苯乙烯才能起到交联抑制作用(由于分子结构特殊性),才能在在过氧化氢催化下,促使反应向生成星型聚合物的方向进行,防止或减少了交联反应发生,从而使得星型结构的共聚物得到成功制备。
24.星型共聚物制备完成后,再加入铂金催化剂,使聚二甲基硅氧烷附着在氢化苯乙烯
‑
异戊二烯嵌段共聚物上,其
‑
o
‑
键与氢化苯乙烯
‑
异戊二烯嵌段的烷基能够发生接枝反应,从而增加星型共聚物的分子链长度和支链数量,进而在保证稳定性的基础上增加制剂的粘接性能。
25.所述的水,依据所有条件的浓度进行添加,最好的用量为30
‑
35份。
26.所述步骤三中,进一步包括有加入偶联剂,加入气相法白炭黑、铂金催化剂和水后,再加入偶联剂,以对增加制剂的黏度,混合持续搅拌一段时间即可出料,进一步提高粘接性能。
27.与现有技术相比,本发明具有如下有益效果:
28.1)本发明配制得自粘性液体硅橡胶制剂,具有强烈的吸附能力,能与玻璃,陶瓷等材质实现很好的粘接,并且耐高温,在50
‑
80℃下能够保持良好的粘接性能。
29.2)本发明合成的制剂,由于具有稳定的结构,能够与液体硅橡胶有很好的相容性,并且能改善硅橡胶的力学性能。
30.3)本发明合成的制剂具备可喷涂的特性,使用方便,且合成工艺简单,能够满足工业化生产的需求。
具体实施方式
31.为了使本发明的目的、技术方案及优点更加清楚明白,以下结合实施例,对本发明进行进一步详细说明。应当理解,此处所描述的具体实施例仅仅用以解释本发明,并不用于限定本发明。
32.申请人研究发现,粘接剂的粘接性能与其分子链的长度是有密切关系的,通常情况下,分子链越长,粘接性能越好,分子链越短,粘接性能越差,因此要保持良好的粘接性能,必须使粘接剂具有足够的分子链;同时,对于一定长度的分子链,又存在稳定性的问题,通常分子链越长则稳定性越差,这反过来会给粘接性能带来负面的影响,因此,要保持粘接剂稳定性和粘接性能,是目前液体硅橡胶粘接剂所面临的主要问题。
33.基于此,本发明从稳定性和提高分子链长度的两个方面入手来实现液体硅橡胶粘接剂,使其既具有良好的粘接性能,又具有足够的稳定性。
34.基于此,本发明所实现的可喷涂的自粘型液体硅橡胶制剂,是通过有将100
‑
120份聚二甲基硅氧烷作为基料、混合40
‑
60份氢化苯乙烯
‑
异戊二烯嵌段共聚物作为改性剂、30
‑
40份气相法白炭黑、0.8
‑
2份改性单体三羟甲基丙烷三丙烯酸酯、0.6
‑
1.5份辅助单体苯乙烯、0.1
‑
0.5份催化剂过氧化氢、加入0.02
‑
0.1份的2000ppm铂金催化剂和20
‑
45份水制得。
35.其中,制备步骤包括:
36.步骤一,溶解共聚物,将氢化苯乙烯
‑
异戊二烯嵌段共聚物粉碎成小颗粒,颗粒外径不大于1cm,向反应釜中先加入基料聚二甲基硅氧烷,然后分批次加入氢化苯乙烯
‑
异戊二烯嵌段共聚物颗粒,控制温度不超过130℃,开动搅拌器;
37.步骤二,制备星型共聚物,升温至160
‑
200℃,再向反应釜中注入过氧化氢,等待10
‑
15min,再注入改性单体三羟甲基丙烷三丙烯酸酯和辅助单体苯乙烯,持续搅拌30min,这个过程是依靠氢化苯乙烯
‑
异戊二烯嵌段共聚物分子链上的聚丙烯结构单元在过氧化物存在下发生裂解形成自由基,在辅助单体苯乙烯的存在下,与多官能度改性单体三羟甲基丙烷三丙烯酸酯发生反应,形成星型的聚合物共聚物。
38.步骤三,接枝,然后降温至100
‑
120℃,加入30
‑
40份气相法白炭黑、0.02
‑
0.1份的2000ppm铂金催化剂和20
‑
45份水,混合持续搅拌45
‑
60min,出料,即得到自粘型液体硅橡胶制剂。此步骤中,聚二甲基硅氧烷与氢化苯乙烯
‑
异戊二烯嵌段共聚物发生接枝反应,聚二甲基硅氧烷作为支链接枝在氢化苯乙烯
‑
异戊二烯嵌段共聚物上,增加分子链的长度和支链数量,由此可以提高粘接性能。
39.在步骤二中,制备星型共聚物时,须注意的是必须在高温下(通常是150℃以上),苯乙烯才能起到交联抑制作用(由于分子结构特殊性),才能在在过氧化物催化下,促使反应向生成星型聚合物的方向进行,防止或减少了交联反应发生,从而使得星型结构的共聚物得到成功制备。
40.所述步骤三中,可以加入偶联剂,如加入气相法白炭黑、铂金催化剂和水后,再加入偶联剂,以对增加制剂的黏度,混合持续搅拌一段时间即可出料,进一步提高粘接性能。
41.实施例1。
42.步骤一,溶解共聚物,将氢化苯乙烯
‑
异戊二烯嵌段共聚物粉碎成小颗粒,颗粒外径不大于1cm,向反应釜中先加入100份基料聚二甲基硅氧烷,然后分批次加入总量40份的氢化苯乙烯
‑
异戊二烯嵌段共聚物颗粒,控制温度不超过130℃,开动搅拌器;
43.步骤二,制备星型共聚物,升温至160
‑
200℃,再向反应釜中注入0.1份过氧化氢,等待10
‑
15min,再注入0.8份改性单体三羟甲基丙烷三丙烯酸酯和0.6份辅助单体苯乙烯,持续搅拌30min。
44.步骤三,接枝,然后降温至100
‑
120℃,加入30份气相法白炭黑、0.02份的2000ppm铂金催化剂和20份水,混合持续搅拌45
‑
60min,出料,即得到自粘型液体硅橡胶制剂。
45.按一定比例稀释后喷涂在玻璃瓶上,在150℃固化10min。测试胶料的基本性能和附着力。如表1所示。
46.实施例2。
47.步骤一,溶解共聚物,将氢化苯乙烯
‑
异戊二烯嵌段共聚物粉碎成小颗粒,颗粒外径不大于1cm,向反应釜中先加入120份基料聚二甲基硅氧烷,然后分批次加入总量60份的氢化苯乙烯
‑
异戊二烯嵌段共聚物颗粒,控制温度不超过130℃,开动搅拌器;
48.步骤二,制备星型共聚物,升温至160
‑
200℃,再向反应釜中注入0.5份过氧化氢,等待10
‑
15min,再注入2份改性单体三羟甲基丙烷三丙烯酸酯和1.5份辅助单体苯乙烯,持续搅拌30min。
49.步骤三,接枝,然后降温至100
‑
120℃,加入40份气相法白炭黑、0.1份的2000ppm铂金催化剂和45份水,混合持续搅拌45
‑
60min,出料,即得到自粘型液体硅橡胶制剂。
50.按一定比例稀释后喷涂在玻璃瓶上,在150℃固化10min。测试胶料的基本性能和附着力。如表1所示。
51.实施例3。
52.步骤一,溶解共聚物,将氢化苯乙烯
‑
异戊二烯嵌段共聚物粉碎成小颗粒,颗粒外径不大于1cm,向反应釜中先加入110份基料聚二甲基硅氧烷,然后分批次加入总量50份的氢化苯乙烯
‑
异戊二烯嵌段共聚物颗粒,控制温度不超过130℃,开动搅拌器;
53.步骤二,制备星型共聚物,升温至160
‑
200℃,再向反应釜中注入0.4份过氧化氢,等待10
‑
15min,再注入1.5份改性单体三羟甲基丙烷三丙烯酸酯和1.2份辅助单体苯乙烯,持续搅拌30min。
54.步骤三,接枝,然后降温至100
‑
120℃,加入35份气相法白炭黑、0.08份的2000ppm铂金催化剂和35份水,混合持续搅拌45
‑
60min,出料,即得到自粘型液体硅橡胶制剂。
55.按一定比例稀释后喷涂在玻璃瓶上,在150℃固化10min。测试胶料的基本性能和附着力。如表1所示。
56.实施例4。
57.步骤一,溶解共聚物,将氢化苯乙烯
‑
异戊二烯嵌段共聚物粉碎成小颗粒,颗粒外径不大于1cm,向反应釜中先加入105份基料聚二甲基硅氧烷,然后分批次加入总量52份的氢化苯乙烯
‑
异戊二烯嵌段共聚物颗粒,控制温度不超过130℃,开动搅拌器;
58.步骤二,制备星型共聚物,升温至160
‑
200℃,再向反应釜中注入0.35份过氧化氢,等待10
‑
15min,再注入1.2份改性单体三羟甲基丙烷三丙烯酸酯和1.1份辅助单体苯乙烯,持续搅拌30min。
59.步骤三,接枝,然后降温至100
‑
120℃,加入36份气相法白炭黑、0.07份的2000ppm铂金催化剂和30份水,混合持续搅拌45
‑
60min,出料,即得到自粘型液体硅橡胶制剂。
60.按一定比例稀释后喷涂在玻璃瓶上,在150℃固化10min。测试胶料的基本性能和
附着力。如表1所示。
61.实施例5。
62.步骤一,溶解共聚物,将氢化苯乙烯
‑
异戊二烯嵌段共聚物粉碎成小颗粒,颗粒外径不大于1cm,向反应釜中先加入116份基料聚二甲基硅氧烷,然后分批次加入总量54份的氢化苯乙烯
‑
异戊二烯嵌段共聚物颗粒,控制温度不超过130℃,开动搅拌器;
63.步骤二,制备星型共聚物,升温至160
‑
200℃,再向反应釜中注入0.36份过氧化氢,等待10
‑
15min,再注入1.28份改性单体三羟甲基丙烷三丙烯酸酯和1.0份辅助单体苯乙烯,持续搅拌30min。
64.步骤三,接枝,然后降温至100
‑
120℃,加入38份气相法白炭黑、0.06份的2000ppm铂金催化剂和25份水,混合持续搅拌45
‑
60min,出料,即得到自粘型液体硅橡胶制剂。
65.按一定比例稀释后喷涂在玻璃瓶上,在150℃固化10min。测试胶料的基本性能和附着力。如表1所示。
66.实施例6。
67.步骤一,溶解共聚物,将氢化苯乙烯
‑
异戊二烯嵌段共聚物粉碎成小颗粒,颗粒外径不大于1cm,向反应釜中先加入112份基料聚二甲基硅氧烷,然后分批次加入总量48份的氢化苯乙烯
‑
异戊二烯嵌段共聚物颗粒,控制温度不超过130℃,开动搅拌器;
68.步骤二,制备星型共聚物,升温至160
‑
200℃,再向反应釜中注入0.25份过氧化氢,等待10
‑
15min,再注入1.0份改性单体三羟甲基丙烷三丙烯酸酯和0.8份辅助单体苯乙烯,持续搅拌30min。
69.步骤三,接枝,然后降温至100
‑
120℃,加入32份气相法白炭黑、0.04份的2000ppm铂金催化剂和25份水,混合持续搅拌45
‑
60min,出料,即得到自粘型液体硅橡胶制剂。
70.按一定比例稀释后喷涂在玻璃瓶上,在150℃固化10min。测试胶料的基本性能和附着力。如表1所示。
71.比较例以本申请人在2019年申请的一种自粘性液体硅橡胶中的实施例作为比较例。
72.比较例1
73.步骤s1:将79.2g1,4
‑
丁二醇二丙烯酸酯,23.2g丙烯酸羟乙酯,0.42g4000ppm的铂金催化剂,搅拌均匀形成混合液备用;
74.步骤s2:将220g四甲基环四硅氧烷,0.45g对羟基苯酚加入带温度计和冷凝回流管的四口烧瓶,在氮气保护下搅拌并升温至60℃。把步骤1的混合液缓慢加入,加完以后继续升温至120℃反应4h,冷却,加入20g活性炭吸附1h。最后抽滤,脱除低分子后得到增粘剂1;
75.步骤s3:将50份粘度为8万的乙烯基封端聚二甲基硅氧烷,20份的2万的乙烯基封端聚二甲基硅氧烷,1份粘度为300mpa.s乙烯基质量分数为1%的乙烯基硅油,25份气相法白炭黑,5份六甲基二硅氮烷,1.52份水,在室温下加入捏合机搅拌均匀,然后升温到180℃,真空度为0.01mpa,处理3h,冷却后依次加入0.65份含氢量为0.8%的含氢硅油,0.005份乙炔基环己醇,0.5份的增粘剂搅拌均匀,再加入0.01份4000ppm的铂金催化剂搅匀,最后在130℃固化5min成型。试样性能如表1所示。
76.比较例2
77.步骤s1:将93.6g1,6
‑
丁二醇二丙烯酸酯,0.41g4000ppm的铂金催化剂,搅拌均匀
形成混合液备用;
78.步骤s2:将185g粘度为30mpa.s含氢量为1.5%的含氢硅油,0.4g对羟基苯酚加入带温度计和冷凝回流管的四口烧瓶,在氮气保护下搅拌并升温至50℃。把步骤1的混合液缓慢加入,加完以后继续升温至90℃反应4h,冷却,加入20g活性炭吸附1h。最后抽滤,脱除低分子后得到增粘剂2;
79.步骤s3:将40份粘度为8万的乙烯基封端聚二甲基硅氧烷,20份的2万的乙烯基封端聚二甲基硅氧烷,2份粘度为300mpa.s乙烯基质量分数为1%的乙烯基硅油,28份气相法白炭黑,6份六甲基二硅氮烷,1.6份水,在室温下加入捏合机搅拌均匀,然后升温到180℃,真空度为0.01mpa,处理3h,冷却后依次加入0.95份含氢量为0.8%的含氢硅油,0.005份乙炔基环己醇,4.5份的增粘剂搅拌均匀,再加入0.01份4000ppm的铂金催化剂搅匀,最后在130℃固化5min成型。试样性能如表1所示。
80.比较例3
81.步骤s1:将198g1,4
‑
丁二醇二丙烯酸酯丙烯酸酯类化合物,142g甲基丙烯酸缩水甘油酯,1.6g4000ppm的铂金催化剂,搅拌均匀形成混合液备用;
82.步骤s2:将580g四甲基环四硅氧烷,1.0g对羟基苯酚加入带温度计和冷凝回流管的四口烧瓶,在氮气保护下搅拌并升温至50℃。把步骤1的混合液缓慢加入,加完以后继续升温至90℃反应4h,冷却,加入30g活性炭吸附1h。最后抽滤,脱除低分子后得到增粘剂3;
83.步骤s3:将60份粘度为8万的乙烯基封端聚二甲基硅氧烷,25份的2万的乙烯基封端聚二甲基硅氧烷,4份粘度为50mpa.s乙烯基质量分数为2%的乙烯基硅油,32份气相法白炭黑,8份六甲基二硅氮烷,2份水,在室温下加入捏合机搅拌均匀,然后升温到180℃,真空度为0.01mpa,处理3h,冷却后依次加入2份含氢量为1.1%的含氢硅油,0.005份乙炔基环己醇,1.5份的增粘剂搅拌均匀,再加入0.01份4000ppm的铂金催化剂搅匀,试样性能如表1所示。
84.[0085][0086]
表1
[0087]
其中,表1中产品性能测试方法如下:
[0088]
1、按照gb/t
‑
531
‑
1999测定硬度、拉伸强度和断裂伸长率。
[0089]
2、按照gb/t
‑
529
‑
1999测定抗撕裂强度。
[0090]
3、按照gbt gbt7124
‑
2008测定与玻璃的粘接强度。
[0091]
由表1可以看出,实施例1、2、3、4、5及6与比较例1、2和3相比,对玻璃陶瓷的粘接性都有了明显的提高,特别是100℃下粘接性大大由于比较例,证明本发明具有优良的稳定性和耐温性能。
[0092]
以上公开的仅为本发明的几个具体实施例,但是本发明并非局限于此,任何本领域的技术人员能思之的变化都应落入本发明的保护范围。