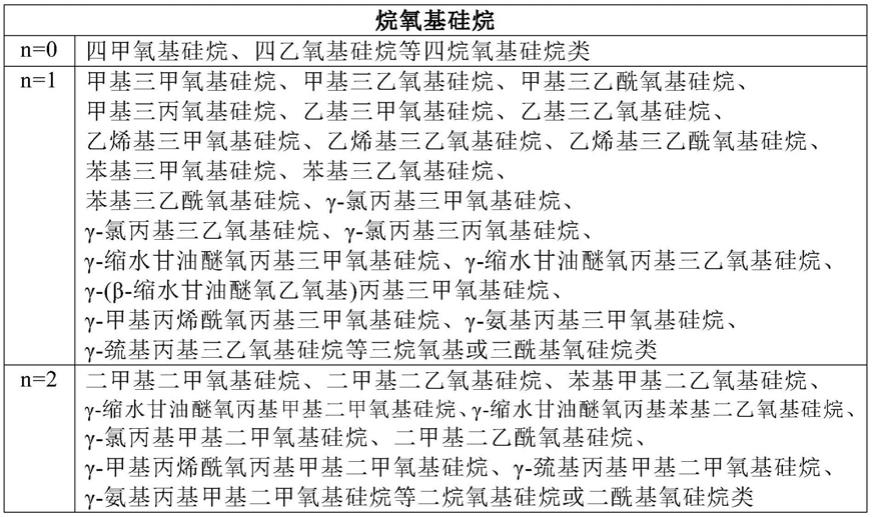
1.本发明涉及含有导电粒子以及粘合剂成分的用于形成导电膜的涂布液。特别地,涉及保存稳定性优异的涂布液。
背景技术:2.一直以来,使用含有导电粒子的涂布液在基板上形成导电性覆膜。例如,透明导电膜已经用于显示装置、触摸面板、太阳能电池等中。作为用于形成导电膜的涂布液,已知含有链状导电粒子(鎖状導電粒子)以及烷氧基硅烷低聚物的组合物(例如专利文献1)。在专利文献1中,使用烷氧基硅烷低聚物作为粘合剂成分。由于烷氧基硅烷低聚物容易与链状导电粒子结合,因此可以提高所得膜的强度。
3.现有技术文献
4.专利文献
5.专利文献1:日本特开2019
‑
157026号公报
技术实现要素:6.发明要解决的技术问题
7.如专利文献1那样,在含有导电粒子以及结合至该导电粒子的粘合剂成分的涂布液中,随着时间流逝,导电粒子的表面被粘合剂成分覆盖。由于粘合剂成分具有绝缘性,因此在含有被粘合剂成分覆盖的导电粒子的膜中,无法由大量导电粒子形成导电通路(導電
パス
),所以存在与由初始涂布液所形成的膜相比导电性降低这样的问题。
8.因此,本发明的目的是提供一种保存稳定性优异的用于形成导电膜的涂布液。
9.解决技术问题的技术手段
10.本发明的用于形成导电膜的涂布液含有链状导电粒子、高沸点溶剂、低沸点溶剂以及可结合至链状导电粒子的烷氧基硅烷低聚物。相对于链状导电粒子和烷氧基硅烷低聚物的总量,含有35质量%~75质量%的链状导电粒子。此外,在用动态光散射式粒度分布计测定的涂布液的粒径分布中,平均粒径为100nm以上;以体积为基准,从粒径小的一侧累积到16%时的粒径d
16
与累积到84%时的粒径d
84
之间的差(d
84
‑
d
16
)为200nm以上。
11.此外,高沸点溶剂和低沸点溶剂的质量比在1:9~1:3的范围内。此外,涂布液中所含的水低于5质量%。
12.相对于链状导电粒子1质量份,涂布液中含有0.0005质量份~0.008质量份的酸。此外,烷氧基硅烷低聚物的重均分子量为3500~5000。
具体实施方式
13.在本发明的涂布液中,链状导电粒子和粘合剂成分分散在高沸点溶剂和低沸点溶剂中。此处,粘合剂成分是可结合至链状导电粒子表面的烷氧基硅烷低聚物。在该涂布液中,相对于链状导电粒子和粘合剂成分的总质量,含有35质量%~75质量%的链状导电粒
子。另外,在用动态光散射式粒度分布计测定涂布液而得到粒径分布时,以体积为基准,从粒径小的一侧累积到16%时的粒径d
16
与累积到84%时的粒径d
84
之间的差(d
84
‑
d
16
)为200nm以上,平均粒径为100nm以上。另外,在下文中,将上述粒径差(d
84
‑
d
16
)称为粒径分布宽度。
14.此处,高沸点溶剂是在常压下沸点为100℃以上的溶剂,低沸点溶剂是在常压下沸点低于100℃的溶剂。高沸点溶剂和低沸点溶剂的质量比合适地为1:9~13:7,最优选为1:9~1:3。如果用高沸点溶剂相对于高沸点溶剂和低沸点溶剂的总量的质量比来表示,合适地为0.10~0.65,最优选为0.10~0.25。在该范围内时,由于涂布时的干燥速度合适,所以不容易出现条痕(筋状)和不均匀(
ムラ
)等涂膜缺陷以及溶剂在膜中的残留等。因此,能够形成平滑且均匀的导电膜。
15.此外,链状导电粒子是三个以上的初级粒子(导电性无机粒子)以链状连接而成的粒子。粒子中也可存在分支连接部分。即,主链部分中为三个以上的初级粒子连接而成的结构,并且也可以存在分支部分(分岐部)。此时,初级粒子的平均粒径优选为2nm~50nm。若平均粒径过小,则晶体结构发展不充分,可能无法充分得到初级粒子本身的导电性。反之,若平均粒径过大,则难以发展链状结构,即使将其链状化也难以有效地形成导电通路,可能无法充分得到膜的导电性。
16.此外,烷氧基硅烷低聚物是将烷氧基硅烷的至少一部分水解而得到的水解产物(部分水解物、水解聚合物(加水分解重合物)等),重均分子量优选为3000~6500,较优选为3500~5000。此处,重均分子量是通过gpc求出的换算为聚苯乙烯的值。
17.另外,在涂布液中,相对于链状导电粒子和粘合剂成分的总量,含有35质量%~75质量%的链状导电粒子。特别优选为45质量%~70质量%。若涂布液中链状导电粒子的浓度低,则导电通路的形成不充分,导电膜的导电性存在不充分、不均匀的可能。另外,若链状导电粒子的浓度过高,则所得导电膜的透射率和硬度存在出现降低的可能。
18.在根据本发明的涂布液中,链状导电粒子不仅各自单独存在,还形成不沉淀的凝聚体。此外,在该涂布液中,也可存在保持未连接形态的初级粒子。通过动态光散射式粒度分布计测定出这种涂布液的平均粒径为100nm以上且粒径分布宽度为200nm以上。在这种含有不沉淀的凝聚体的涂布液中,由于链状导电粒子能够与粘合剂成分发生反应(具有羟基等)的表面积比较小,所以链状导电粒子的表面很难被绝缘性的粘合剂成分覆盖。此外,通过涂布涂布液而形成的导电膜中容易充分形成导电通路。另一方面,在不具有上述粒径分布的涂布液中,由于链状导电粒子的分散性高,所以链状导电粒子之间难以形成导电通路;此外,由于链状导电粒子的表面积大,所以粒子与粘合剂成分之间的反应快速进行,粒子表面易于被绝缘成分覆盖。因此,不能成为保存稳定性优异的用于形成导电膜的涂布液。
19.此外,在该涂布液中,链状导电粒子和烷氧基硅烷低聚物的合计固体成分浓度(总固体成分浓度)优选在0.1质量%~15质量%的范围内,较优选在0.5质量%~10质量%的范围内。若总固体成分浓度在上述范围内,则可以将在通常涂布条件下得到的膜厚控制为适当厚度。此外,由于涂布液的保存稳定性也变得充分,所以可以稳定地获得所得导电膜的膜厚、导电性、硬度等特性。
20.此外,总固体成分浓度为5质量%的该涂布液在20℃下的粘度优选在0.5mpa
·
s~20mpa
·
s的范围内,较优选在1mpa
·
s~10mpa
·
s的范围内。若20℃下的粘度在上述范围内,则可以将通过常规涂布方法得到的膜厚控制为适当厚度。
21.另外,由于该涂布液含有链状导电粒子的凝聚体,所以从低浓度的状态浓缩时粘度容易增加。对于显示出粘度增加的涂布液,在形成导电膜时,链状导电粒子之间难以解凝聚,容易形成导电通路。具体而言,当进行浓缩以使得总固体成分为30%时,20℃下的粘度优选在10mpa
·
s~300mpa
·
s的范围内,较优选在20mpa
·
s~100mpa
·
s的范围内。
22.涂布液中所含的水优选低于5质量%。当涂布液含有5质量%以上的水时,会促进烷氧基硅烷低聚物的水解反应,进而促进链状导电粒子的表面与烷氧基硅烷低聚物的反应,链状导电粒子的表面可能被绝缘成分覆盖。含有这样状态的链状导电粒子的导电膜不能在膜内充分形成导电通路,可能无法获得良好的导电性。
23.以下对构成涂布液的各成分进行详细说明。
24.<烷氧基硅烷低聚物>
25.烷氧基硅烷低聚物的重均分子量优选为3500~5000。烷氧基硅烷低聚物是由下述式(1)表示的烷氧基硅烷的水解聚合物,其中n为0~2的整数。当n为3时,由于只能在两个分子之间键合,所以不能形成重均分子量为3500以上的低聚物。此处,n越小越好,最优选使用n为0的烷氧基硅烷。若使用这样的烷氧基硅烷,烷氧基硅烷之间就会形成致密的三维网状结构,从而可以增强整个膜的强度。
26.r
1n
‑
si(or2)4‑
n
···
(1)
27.此处,r1和r2为氢原子、卤素原子、碳原子数1~10的非取代或取代烃基,二者可以彼此相同也可以不同。此外,一般n为0~3的整数。
28.此外,涂布液中存在的烷氧基硅烷低聚物以固体成分计优选为1.2质量%~3.3质量%,进一步优选为1.5质量%~2.8质量%。若烷氧基硅烷低聚物的浓度低,则膜的粘合剂成分变少,膜中的链状导电粒子之间的密合性变得不足,可能得不到足够的硬度。另外,若浓度过高,则在涂布液中与链状导电粒子表面的反应过度进行,保存稳定性可能降低。
29.烷氧基硅烷的具体例子示于表1中。
30.[表1]
[0031][0032]
<链状导电粒子>
[0033]
如前所述,链状导电粒子是三个以上的初级粒子以链状连接而成的粒子。初级粒子是单分散状态的导电性无机粒子。初级粒子的平均粒径为2nm~50nm。从透射型电子显微镜(tem)拍摄的图像中对任意100个初级粒子测定粒径,将其平均值设为初级粒子的平均粒径。此外,从该图像中选择任意50个粒子,并测量每个粒子的连接数(連結数)。将50个粒子的连接数的平均值作为平均连接数。平均连接数优选为3以上,特别优选为5以上。若初级粒子的平均连接数少,则可能无法充分获得提高导电性的效果。
[0034]
此处,作为初级粒子,只要是具有导电性的粒子即可。例如,可以使用金属氧化物粒子等。根据膜的用途,有时也要求透明性。作为这种金属氧化物粒子,列举氧化铟、氧化锡等。此外,也可以使用以一种以上金属氧化物为主要成分并掺杂有锡、锑的粒子,例如锑掺杂氧化锡(ato)、锡掺杂氧化铟(ito)。从透明性、导电性和化学特性优异的观点出发,优选包含ato和ito中至少一者的粒子,特别优选ato粒子。
[0035]
此外,优选用上述式(1)表示的烷氧基硅烷对链状导电粒子进行表面处理。通过进行表面处理,除了防止链状导电粒子再次分散为原来的初级粒子之外,还能提高在涂布液中的分散性,抑制像沉淀那样的凝聚的发生。
[0036]
作为此处使用的烷氧基硅烷,除了表1中所示的以外,还可列举n=3的三甲基氯硅烷等,它们可以单独使用或将两种以上组合使用。
[0037]
这种烷氧基硅烷的使用量根据烷氧基硅烷的种类、链状导电粒子的粒径等而不同,但链状导电粒子与烷氧基硅烷的量的比(水解性有机硅化合物/链状导电粒子,重量比)优选在0.01~0.5的范围内,进一步优选在0.02~0.3的范围内。当链状导电粒子与烷氧基硅烷的量的比小于下限时,以链状连接的粒子在涂布液中有可能恢复为原来的初级粒子,即使维持连接,在涂料中的分散性也可能变得不充分。因此,使用该涂料形成的覆膜的雾度(
ヘーズ
)高,有时会导致抗静电性能不充分。若链状导电粒子与烷氧基硅烷的量的比超出上限,则链状导电粒子的表面会被烷氧基硅烷的水解物覆盖得很厚,可能会导致导电性降低。
[0038]
<溶剂>
[0039]
此处使用的溶剂只要在涂布后能通过干燥工序等去除即可。作为高沸点溶剂,可列举1
‑
甲氧基
‑2‑
丙醇、二丙酮醇、乙二醇、二乙二醇等;作为低沸点溶剂,可列举甲醇、乙醇、异丙醇、丙酮等。
[0040]
高沸点溶剂和低沸点溶剂优选作为混合物存在,高沸点溶剂与高沸点溶剂和低沸点溶剂的总量的质量比合适地为0.10~0.65。若使用这样的混合溶剂,涂布涂布液时的干燥速度合适。该质量比较优选为0.10~0.40,最优选为0.10~0.25。
[0041]
<酸>
[0042]
另外,涂布液优选含有酸。作为酸,可列举盐酸、硝酸、醋酸、磷酸等。此类酸促进链状导电粒子之间的凝聚,促进涂布液中导电通路的形成。相对于链状导电粒子1质量份,酸的量优选含有0.0005质量份~0.008质量份,较优选含有0.001质量份~0.004质量份。若酸的量多,则链状导电粒子过度凝聚,可能发生链状导电粒子的沉淀。由这样的涂布液形成的导电膜的雾度可能变高,不适合作为透明导电膜。若酸的量少,则链状导电粒子的凝聚不能充分发生,此外会促进烷氧基硅烷低聚物与链状导电粒子的结合,链状导电粒子的表面可能会被绝缘成分覆盖。对于使用这样的涂布液形成的导电膜,在膜中有时可能没有充分形
成导电通路,并且可能显示出比由初始涂布液形成的导电膜更低的导电性。
[0043]
以下详细说明涂布液的制造方法。
[0044]
首先,准备分散有由导电性无机氧化物构成的链状导电粒子的分散液。这种分散液可以通过日本特开2006
‑
339113号公报中公开的方法等来制备。链状导电粒子的浓度优选为20质量%以上。
[0045]
接着,将第一溶剂(含有高沸点溶剂和低沸点溶剂中的至少一者)与上述烷氧基硅烷低聚物混合到该链状导电粒子的分散液中。此时,相对于分散液100质量份,混合链状导电粒子和烷氧基硅烷低聚物共计8.5质量份~15质量份。另外,也可以在将链状导电粒子的分散液与烷氧基硅烷低聚物混合后再加入第一溶剂。将这样得到的混合液在室温至低于第一溶剂沸点的温度下搅拌1小时。
[0046]
接着,在该混合液中加入第二溶剂(含有高沸点溶剂和低沸点溶剂中的至少一者),从而得到涂布液。第一溶剂和第二溶剂可以相同也可以不同,但是所得涂布液中要同时含有高沸点溶剂和低沸点溶剂。此时,相对于涂布液100质量份,使链状导电粒子和烷氧基硅烷低聚物共计为3.5质量份~10质量份。
[0047]
以下对使涂布液固化而得到的导电膜进行说明。通过对液膜进行加热而除去溶剂,并进行链状无机导电粒子与烷氧基硅烷低聚物的脱水缩合反应。导电性膜具有优异的导电性等高电特性,适用于要求光学特性和电特性的部件。
[0048]
基材没有特别限制,可以使用玻璃、塑料等形成均匀液膜并能承受固化温度的基材。涂布方法也没有特别限制,可以使用棒式涂布机法、浸涂法、喷涂法、旋涂法、辊涂法、凹版涂布法、狭缝涂布法(
スリットコート
法)、加压涂布法等。膜的平均膜厚可根据用途适当选择。在通过涂布形成膜的情况下,平均膜厚优选为80nm~300nm。
[0049]
实施例
[0050]
以下详细说明含酸涂布液的实施例。
[0051]
[实施例1]
[0052]
首先,将23.0g烷氧基硅烷低聚物(固体成分浓度9.8质量%)和13.4g链状导电粒子(固体成分浓度20.5质量%)混合,搅拌60分钟。该溶液的烷氧基硅烷低聚物与链状导电粒子的总固体成分浓度为13.7质量%。此处使用的烷氧基硅烷低聚物为将四甲氧基硅烷水解而得的产物,分子量为3810。此外,相对于链状导电粒子的固体成分质量1质量份,含有0.002质量份盐酸。链状导电粒子是将用四乙氧基硅烷进行表面处理的ato粒子作为初级粒子以链状连接的粒子。
[0053]
一边搅拌该混合溶液一边加入43.6g异丙醇,搅拌5分钟。然后,混合20.0g的1
‑
甲氧基
‑2‑
丙醇,搅拌15分钟后,通过过滤制备总固体成分浓度为5质量%的涂布液。涂布液的制备条件示于表2中,所得涂布液的物理性质示于表3中。
[0054]
将该涂布液通过棒式涂布机法涂布在玻璃基板上,在80℃下干燥1分钟后在130℃的干燥机内加热30分钟。测定得到的带膜基材的表面电阻。结果示于表4中。
[0055]
另外,将该涂布液在调节至水温40℃的浴槽中静置24小时。将该加温处理后的涂布液通过旋涂机法涂布在玻璃基板上,在室温下干燥1分钟后在130℃的干燥机内加热30分钟。测定得到的带膜基材的表面电阻。结果示于表4中。
[0056]
此外,对于后述实施例和比较例,也如下所述对涂布液以及带膜基材的各物理性
质进行了测定、评价。
[0057]
(平均粒径、粒径分布宽度)
[0058]
用动态光散射式粒度分布计(microtrac公司制造的nanotrac wave 2
‑
ut151)测定涂布液,得出涂布液的平均粒径和粒径分布宽度(粒径差:d
84
‑
d
16
)。表3中记录了该粒径分布宽度的一半的值。
[0059]
(粘度)
[0060]
使用e型粘度计(东机产业公司制造的tv
‑
25型)测定20℃下的粘度。测定了总固体成分浓度为5质量%的涂布液和将其浓缩至总固体成分30%的涂布液的粘度。
[0061]
(表面电阻)
[0062]
使用表面电阻测量仪(三菱化学
アナリテック
公司制造的
ハイレスター
ux mcp
‑
ht800)测定表面电阻。
[0063]
(保存稳定性)
[0064]
对于保存稳定性,根据通过(由加温处理后的涂布液而得的带膜基材的表面电阻值)/(由初始涂布液而得的带膜基材的表面电阻值)得到的比值来进行评价。
[0065]
[实施例2]
[0066]
在本实施例中,烷氧基硅烷低聚物的添加量为20.4g,链状导电粒子的添加量为14.6g,异丙醇的添加量为45.0g。除此之外,以与实施例1相同的方式制备并评价了涂布液和带膜基材。
[0067]
[实施例3]
[0068]
在本实施例中,烷氧基硅烷低聚物的添加量为28.1g,链状无机导电性粒子的添加量为11.1g,异丙醇的添加量为40.8g。除此之外,以与实施例1相同的方式制备并评价了涂布液和带膜基材。
[0069]
[比较例1]
[0070]
在43.6g异丙醇中加入13.4g与实施例1相同的链状导电粒子(固体成分浓度20.5质量%),搅拌5分钟。然后,混合20.0g的1
‑
甲氧基
‑2‑
丙醇,搅拌15分钟。混合23.0g与实施例1相同的烷氧基硅烷低聚物,搅拌60分钟。此时,烷氧基硅烷低聚物和链状导电粒子的总固体成分浓度为5质量%。然后,用1μm的尼龙过滤器过滤,制备总固体成分浓度为5质量%的涂布液。所得涂布液中各成分的浓度等示于表1中。除此之外,以与实施例1相同的方式进行制备并评价。
[0071]
[比较例2]
[0072]
异丙醇的添加量为45.0g,与实施例1相同的链状导电粒子的添加量为14.6g,与实施例1相同的烷氧基硅烷低聚物的添加量为20.4g。除此之外,以与比较例1相同的方式制备并评价了涂布液和带膜基材。
[0073]
[比较例3]
[0074]
异丙醇的添加量为40.8g,与实施例1相同的链状导电粒子的添加量为11.1g,与实施例1相同的烷氧基硅烷低聚物的添加量为28.1g。除此之外,以与比较例1相同的方式制备并评价了涂布液和带膜基材。
[0075]
[表2]
[0076][0077]
①
:ato
[0078]
②
:四乙氧基硅烷
[0079]
③
:四甲氧基硅烷
[0080]
④
:异丙醇
[0081]
⑤
:1
‑
甲氧基
‑2‑
丙醇
[0082]
[表3]
[0083][0084]
[表4]
[0085]