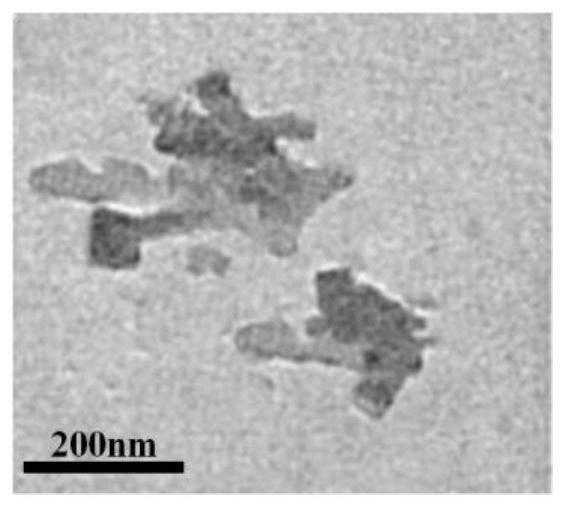
1.本发明属于纺纱技术领域,具体涉及一种利用色纺纤维制备花式羊绒纱的方法。
背景技术:2.色纺纱是将纤维染成有色纤维,能实现白坯染色所不能达到的朦胧立体效果和质感。色纺纱使用起来无污染,还可以最大程度的控制色差。因此颜色柔和时尚,能应对小批量多品种灵活生产的色纺纱,被越来越多的运用于中高档服饰产品中。色纺由于采用“先染色、后纺纱”的新工艺,缩短了后道加工企业的生产流程、降低了生产成本,具有较高的附加值,相对于采用“先纺纱后染色”的传统工艺,色纺纱产品性能优于其它纺织产品,有较强的市场竞争力和较好的市场前景。
3.尽管中国纺织工业生产能力多年来占据全球第一位,但是中国纺织纤维资源有限,节能、减排、降耗、减少环境污染的任务沉重。同时,国际服装和家纺产品已进入生态、安全、保健的新时代,这一切都对中国传统纺织行业提出了更高的要求,需要全行业以科技创新为切入,研究这一系列问题并付诸实施。目前,随着信息技术的广泛应用,纺织机械、机电一体化水平的不断提高,国外先进设备的引进和学习,纺织行业总体技术水平得到不断提高。
4.色纺纱作为纺织工业的细分子行业,与“先纺纱、后染色”的传统工艺相比,因其通过“先染色、后纺纱”的新技术手段,缩短了后续加工企业的生产流程,降低了生产成本,具有较高的附加值,尤其是突破性地解决了传统染整行业污染大的问题,极大降低了能源消耗和环境破坏。色纺纱一般由两种及以上的不同色泽纤维或不同性能的纤维混和纺成纱,该过程主要为物理混合过程。色纺纱线色彩丰富,层次清晰,颜色立体感强,色光一致性好,而织成布后布面呈现出多彩色、手感柔和、表感丰满的特。
5.色纺行业领域的核心技术主要体现在污水处理与节能减排、棉纤维染色和新品种开发等方面。若要在色纺行业占据一席之地,在技术层面上述三是必须解决的难题。
技术实现要素:6.本发明的目的在于提供一种利用色纺纤维制备花式羊绒纱的方法,该方法大大缩短了工艺流程,降低了成本,提高了纱线出货的效率,避免了色差问题,具有节能减排的优势;且制得的花式羊绒纱力学性能优异,柔软度良好,颜料在织物上的色牢度高,上染率更佳。
7.本发明为实现上述目的所采取的技术方案为:
8.一种聚合物杂化颜料,包括:颜料/聚合物复合材料;所述聚合物包覆在颜料表面;
9.所述聚合物为苯丙树脂,其交联单体包括4
‑
[(2r)
‑
3,4
‑
二氢
‑7‑
羟基
‑
2h
‑1‑
苯并吡喃
‑2‑
基]
‑3‑
(3
‑
甲基
‑2‑
丁烯
‑1‑
基)
‑
1,2
‑
苯二酚。本发明采用4
‑
[(2r)
‑
3,4
‑
二氢
‑7‑
羟基
‑
2h
‑1‑
苯并吡喃
‑2‑
基]
‑3‑
(3
‑
甲基
‑2‑
丁烯
‑1‑
基)
‑
1,2
‑
苯二酚改性苯丙树脂作为聚合物,包裹颜料,可有效避免颜料颗粒间的大规模聚集现象;4
‑
[(2r)
‑
3,4
‑
二氢
‑7‑
羟基
‑
2h
‑
1
‑
苯并吡喃
‑2‑
基]
‑3‑
(3
‑
甲基
‑2‑
丁烯
‑1‑
基)
‑
1,2
‑
苯二酚的存在,能够有效提升聚合物对颜料颗粒的包覆率,进一步改善了杂化颜料在水相中的分散稳定性,其超声分散稳定性和存储稳定性显著增强,使得颜料充分发挥其着色潜能;将其应用于织物的染色工艺中,大大增强了颜料在织物上的着色强度及遮盖力,日晒牢度、耐摩擦牢度和耐水洗褪色牢度的等级显著提升,有效改善染色织物的色牢度;且可进一步提升颜料的上染率。此外,在一定程度上,还可改善织物的力学性能,增强其断裂强力。
[0010]
聚合物杂化颜料的制备方法,包括,上述颜料/聚合物复合材料由细乳液法制备而得。
[0011]
进一步地,上述聚合物杂化颜料的制备方法,具体为:
[0012]
1)采用洗涤方法将工业级颜料晶体的盐等物质除去;
[0013]
2)取洗净的颜料晶体分散液、乳化剂op
‑
10以及水混合搅拌20~40min,加入st、ba和4
‑
[(2r)
‑
3,4
‑
二氢
‑7‑
羟基
‑
2h
‑1‑
苯并吡喃
‑2‑
基]
‑3‑
(3
‑
甲基
‑2‑
丁烯
‑1‑
基)
‑
1,2
‑
苯二酚,再加入hd和sds,混合搅拌预乳化0.5~1h,然后130~150w功率下超声10~20min;接着加入引发剂kps,水浴锅保持75~80℃下搅拌反应8~12h,离心、洗涤、干燥即得聚合物杂化颜料。
[0014]
根据本发明,颜料晶体分散液、op
‑
10、水的质量比为1:0.2~0.35:60~70;st、ba和4
‑
[(2r)
‑
3,4
‑
二氢
‑7‑
羟基
‑
2h
‑1‑
苯并吡喃
‑2‑
基]
‑3‑
(3
‑
甲基
‑2‑
丁烯
‑1‑
基)
‑
1,2
‑
苯二酚的质量比为1:0.9~1.4:0.8~1.2;st、hd和sds的质量比为1:0.05~0.15:0.03~0.08;颜料晶体分散液与单体总质量之比为1:1.5~4。
[0015]
一种利用色纺纤维制备花式羊绒纱的方法,具体工艺包括:羊绒毛染色、花捻、拉毛、蒸纱、倒筒。
[0016]
更进一步地,一种利用色纺纤维制备花式羊绒纱的方法,具体包括:
[0017]
s1:先对1/3量的羊绒毛进行染色,再与剩余2/3羊绒毛混合,制成均匀的毛条,投入生产,通过精纺或半精纺做成粗纱;
[0018]
s2:花捻pafa生产,采用花捻机对羊绒粗纱进行花式纱生产得到花式羊绒纱线;
[0019]
s3:拉毛,对做好的花式羊绒纱线进行拉毛;
[0020]
s4:蒸纱,对拉毛后的纱线进行蒸纱;
[0021]
s5:倒筒,蒸完的纱线通过倒成筒纱即得产品。
[0022]
本发明提供的花式羊绒纱的制备方法中,花捻生产可以从源头控制纱线纱支的均匀;拉毛操作使得纱线柔软保暖;接着对拉毛后的纱线进行蒸纱,可有效消除纱线内应力,使得捻度平衡,纱线强力变高,纱线质量变高,增加产能。整个制备过程缩短了工艺流程:使用色纺纤维生产花式羊绒纱,省去了纱线生产染色再生产的流程,大大节省人力物力,提高了纱线出货的效率;减少了纱支偏差和色差,避免了因染色而导致的纱支偏差和染色不匀而导致的色差问题;在节能减排、环保上有明显的优势,色纺纱仅对1/3的纤维进行染色,通过混纺,可得100%的彩色纱,从纺纱到织布,用色纺纱生产同其他工业相比,可以减少近1/3的废水排放,且利用原液着色纤维进行纺纱的工艺则完完全全实现零废水污染排放,响应了国家提倡的碳中和号召。
[0023]
根据本发明,染色过程中所用颜料包括上述聚合物杂化颜料。
[0024]
进一步地,染色工艺包括:
[0025]
(1)将羊绒毛浸泡在水中3~6min,取出拧干,备用;
[0026]
(2)颜料浓度owf(颜料与羊绒毛的质量比)为4.8~9.6%,染色温度为70~90℃,ph=4~6,浴比为1:15~30,染色时间40~60min,取出被染羊绒毛后经过酸性皂洗,水洗后烘干即可。
[0027]
根据本发明,染色后还进行柔软整理,即采用柔软剂浸渍处理。
[0028]
进一步地,柔软剂浸渍处理具体为:
[0029]
取有机硅油,按照体积比1:1~1.5的比例加入水混合,搅拌15~20min得到均匀乳液,过滤后通过浸渍工艺对染色羊绒毛进行柔软整理,乳液用量为1.0~3wt%(对织物重),浴比为1:4~7,30~35℃下整理10~20min;最后脱水、100~120℃烘干、定型即可。
[0030]
根据本发明,柔软剂为有机硅油;上述有机硅油原料包括pmhs、n
‑
(甲氧基甲基)甲基丙烯酰胺。
[0031]
根据本发明,有机硅油原料还包括洋芹脑。本发明采用洋芹脑作为交联剂,与pmhs、n
‑
(甲氧基甲基)甲基丙烯酰胺复合交联,制得有机硅油,作为柔软剂应用于织物柔软整理工艺中,可有效改善纤维表面性能,增强羊绒纤维的柔滑性,使得纺纱过程中纤维间更容易被分梳和牵伸;且一定程度上可进一步改善染色织物的着色牢固度,日晒牢度和耐水洗褪色牢度的等级增强;能够有效增强织物的力学性能,断裂强力和断裂伸长率显著提升。
[0032]
进一步地,有机硅油的制备方法,包括:
[0033]
取pmhs、0.5%氯铂酸的异丙醇溶液加入四颈烧瓶中,连接冷凝管,通入氮气5~8min,缓慢加热搅拌升温至80~85℃,缓慢加入溶解有n
‑
(甲氧基甲基)甲基丙烯酰胺的甲苯溶液,1~2h内滴加完毕,体系温度升温至100~110℃,反应10~12h;最后缓慢降低温度至室温,减压蒸馏,三氯甲烷和无水乙醇依次进行溶解、沉淀,再将沉淀物溶于正己烷、离心、减压蒸馏,反复操作3~5次得到有机硅油。
[0034]
或,
[0035]
取pmhs、0.5%氯铂酸的异丙醇溶液加入四颈烧瓶中,连接冷凝管,通入氮气5~8min,缓慢加热搅拌升温至80~85℃,缓慢加入溶解有洋芹脑的甲苯溶液,1~2h内滴加完毕,体系温度升温至100~110℃,反应4~5h;接着缓慢加入溶解有n
‑
(甲氧基甲基)甲基丙烯酰胺的甲苯溶液,1~2h内滴加完毕,体系温度升温至100~110℃,反应10~12h;最后缓慢降低温度至室温,减压蒸馏,三氯甲烷和无水乙醇依次进行溶解、沉淀,再将沉淀物溶于正己烷、离心、减压蒸馏,反复操作3~5次得到有机硅油。
[0036]
根据本发明,pmhs、洋芹脑和n
‑
(甲氧基甲基)甲基丙烯酰胺的摩尔比为1:0.75~0.9:0.6~0.8;催化剂氯铂酸的用量为55~60μg/g(相对于反应单体总量)。
[0037]
根据本发明,上述有机硅油在增强羊绒纱力学性能和柔滑性中的用途。
[0038]
本发明还公开了上述聚合物杂化颜料在纺织品着色、油墨印刷及橡胶塑料制备中的应用。
[0039]
本发明又公开了4
‑
[(2r)
‑
3,4
‑
二氢
‑7‑
羟基
‑
2h
‑1‑
苯并吡喃
‑2‑
基]
‑3‑
(3
‑
甲基
‑2‑
丁烯
‑1‑
基)
‑
1,2
‑
苯二酚在增强颜料在织物上日晒牢度、耐摩擦牢度和耐水洗褪色牢度中的用途。
[0040]
相比于现有技术,本发明具有如下有益效果:
[0041]
本发明提供的利用色纺纤维制备花式羊绒纱的方法,缩短了工艺流程,大大节省
人力物力,提高了纱线出货的效率;避免了因染色而导致的纱支偏差和染色不匀而导致的色差问题;在节能减排、环保上有明显的优势,响应了国家提倡的碳中和号召。其中,染色工艺中采用4
‑
[(2r)
‑
3,4
‑
二氢
‑7‑
羟基
‑
2h
‑1‑
苯并吡喃
‑2‑
基]
‑3‑
(3
‑
甲基
‑2‑
丁烯
‑1‑
基)
‑
1,2
‑
苯二酚改性苯丙树脂作为聚合物,包裹颜料,能够有效提升聚合物对颜料颗粒的包覆率,进一步改善了杂化颜料在水相中的分散稳定性,其超声分散稳定性和存储稳定性显著增强;大大增强了颜料在织物上的色牢度,日晒牢度、耐摩擦牢度和耐水洗褪色牢度的等级显著提升;颜料的上染率显著提升;且还改善了织物的力学性能。此外,柔软整理剂有机硅油中洋芹脑的加入,对染色纤维整理后,有效增强羊绒纤维的柔滑性,进一步改善染色织物的着色牢固度,日晒牢度和耐水洗褪色牢度的等级增强;且能够有效增强织物的力学性能,断裂强力和断裂伸长率显著提升。
[0042]
因此,本发明提供了一种利用色纺纤维制备花式羊绒纱的方法,该方法大大缩短了工艺流程,降低了成本,提高了纱线出货的效率,避免了色差问题,具有节能减排的优势;且制得的花式羊绒纱力学性能优异,柔软度良好,颜料在织物上的色牢度高,上染率更佳。
附图说明
[0043]
图1为本发明颜料红170的tem测试结果;
[0044]
图2为本发明实施例1中聚合物杂化颜料的tem测试结果;
[0045]
图3为本发明试验例1中红外光谱测试结果;
[0046]
图4为本发明对比例1制得聚合物杂化颜料超声分散稳定性测试结果;
[0047]
图5为本发明实施例1制得聚合物杂化颜料超声分散稳定性测试结果;
[0048]
图6为本发明试验例1中聚合物杂化颜料存储稳定性谱测试结果。
具体实施方式
[0049]
以下结合具体实施方式和附图对本发明的技术方案作进一步详细描述:
[0050]
本发明实施例所用工业级颜料晶体为颜料红170晶体分散液,购自杭州百合科莱恩颜料有限公司。
[0051]
实施例1:
[0052]
聚合物杂化颜料的制备:
[0053]
1)采用洗涤方法将工业级颜料晶体的盐等物质除去,具体为:将颜料晶体分散液依次通过10000r/min、8000r/min、5000r/min进行离心洗涤,每次离心8min;
[0054]
2)取洗净的颜料晶体分散液、乳化剂op
‑
10以及水(三者质量比为1:0.28:64)混合搅拌30min,加入st、ba和4
‑
[(2r)
‑
3,4
‑
二氢
‑7‑
羟基
‑
2h
‑1‑
苯并吡喃
‑2‑
基]
‑3‑
(3
‑
甲基
‑2‑
丁烯
‑1‑
基)
‑
1,2
‑
苯二酚(三者的质量比为1:1.2:1),其中颜料晶体分散液与单体的总质量之比为1:3.1,再加入hd和sds(st、hd和sds的质量比为1:0.11:0.06),混合搅拌预乳化1h,然后150w功率下超声20min;接着加入引发剂kps,水浴锅保持78℃下搅拌反应10h,离心、洗涤、干燥即得聚合物杂化颜料。
[0055]
有机硅油的制备:
[0056]
取pmhs、0.5%氯铂酸的异丙醇溶液(氯铂酸的用量为58μg/g)加入四颈烧瓶中,连接冷凝管,通入氮气6min,缓慢加热搅拌升温至80℃,缓慢加入溶解有n
‑
(甲氧基甲基)甲基
丙烯酰胺的甲苯溶液,其中,pmhs和n
‑
(甲氧基甲基)甲基丙烯酰胺的摩尔比为1:0.7,于2h内滴加完毕,体系温度升温至105℃,反应11h;最后缓慢降低温度至室温,减压蒸馏,三氯甲烷和无水乙醇依次进行溶解、沉淀,再将沉淀物溶于正己烷、离心、减压蒸馏,反复操作5次得到改性硅油。
[0057]
一种利用色纺纤维制备花式羊绒纱的方法,具体为:
[0058]
s1:先对1/3量的羊绒毛进行染色,再与剩余2/3羊绒毛混合,制成均匀的毛条,投入生产,通过半精纺做成粗纱;
[0059]
s2:花捻pafa生产,采用花捻机对羊绒粗纱进行花式纱生产得到花式羊绒纱线;
[0060]
s3:拉毛,对做好的花式羊绒纱线进行拉毛;
[0061]
s4:蒸纱,对拉毛后的纱线进行蒸纱;
[0062]
s5:倒筒,蒸完的纱线通过倒成筒纱即得产品。
[0063]
其中,
[0064]
染色工艺具体为:
[0065]
(1)将羊绒毛浸泡在水中5min,取出拧干,备用;
[0066]
(2)颜料浓度owf(颜料与羊绒毛的质量比)为6.5%,染色温度为75℃,ph=5.5,浴比为1:20.5,染色时间50min,取出被染羊绒毛后经过酸性皂洗,水洗后烘干即可。
[0067]
根据本发明,染色后还进行柔软整理,即采用柔软剂浸渍处理。
[0068]
进一步地,柔软剂浸渍处理具体为:
[0069]
取有机硅油,按照体积比1:1.5的比例加入水混合,搅拌20min得到均匀乳液,过滤后通过浸渍工艺对染色羊绒毛进行柔软整理,乳液用量为2.4wt%(对织物重),浴比为1:6,32℃下整理20min;最后脱水、100℃烘干、定型即可。
[0070]
实施例2:
[0071]
聚合物杂化颜料的制备与实施例1的不同之处在于:颜料晶体分散液、op
‑
10、水的质量比为1:0.22:62.5;st、ba和4
‑
[(2r)
‑
3,4
‑
二氢
‑7‑
羟基
‑
2h
‑1‑
苯并吡喃
‑2‑
基]
‑3‑
(3
‑
甲基
‑2‑
丁烯
‑1‑
基)
‑
1,2
‑
苯二酚的质量比为1:1.3:0.84;st、hd和sds的质量比为1:0.06:0.07;颜料晶体分散液与单体总质量之比为1:2.4。
[0072]
有机硅油的制备与实施例1相同。
[0073]
一种利用色纺纤维制备花式羊绒纱的方法与实施例1相同。
[0074]
实施例3:
[0075]
聚合物杂化颜料的制备与实施例1的不同之处在于:颜料晶体分散液、op
‑
10、水的质量比为1:0.32:61.5;st、ba和4
‑
[(2r)
‑
3,4
‑
二氢
‑7‑
羟基
‑
2h
‑1‑
苯并吡喃
‑2‑
基]
‑3‑
(3
‑
甲基
‑2‑
丁烯
‑1‑
基)
‑
1,2
‑
苯二酚的质量比为1:0.95:1.1;st、hd和sds的质量比为1:0.14:0.05;颜料晶体分散液与单体总质量之比为1:1.6。
[0076]
有机硅油的制备与实施例1相同。
[0077]
一种利用色纺纤维制备花式羊绒纱的方法与实施例1相同。
[0078]
实施例4:
[0079]
聚合物杂化颜料的制备与实施例1的不同之处在于:颜料晶体分散液、op
‑
10、水的质量比为1:0.3:69.5;st、ba和4
‑
[(2r)
‑
3,4
‑
二氢
‑7‑
羟基
‑
2h
‑1‑
苯并吡喃
‑2‑
基]
‑3‑
(3
‑
甲基
‑2‑
丁烯
‑1‑
基)
‑
1,2
‑
苯二酚的质量比为1:1:1.2;st、hd和sds的质量比为1:0.15:0.07;
颜料晶体分散液与单体总质量之比为1:3.9。
[0080]
有机硅油的制备与实施例1相同。
[0081]
一种利用色纺纤维制备花式羊绒纱的方法与实施例1相同。
[0082]
实施例5:
[0083]
聚合物杂化颜料的制备与实施例1相同。
[0084]
有机硅油的制备:
[0085]
取pmhs、0.5%氯铂酸的异丙醇溶液(氯铂酸的用量为58μg/g)加入四颈烧瓶中,连接冷凝管,通入氮气6min,缓慢加热搅拌升温至80℃,缓慢加入溶解有洋芹脑的甲苯溶液,2h内滴加完毕,体系温度升温至105℃,反应5h;接着缓慢加入溶解有n
‑
(甲氧基甲基)甲基丙烯酰胺的甲苯溶液,2h内滴加完毕,体系温度升温至105℃,反应11h;最后缓慢降低温度至室温,减压蒸馏,三氯甲烷和无水乙醇依次进行溶解、沉淀,再将沉淀物溶于正己烷、离心、减压蒸馏,反复操作5次得到改性硅油。反应过程找那个,pmhs、洋芹脑和n
‑
(甲氧基甲基)甲基丙烯酰胺的摩尔比为1:0.82:0.7。
[0086]
一种利用色纺纤维制备花式羊绒纱的方法与实施例1相同。
[0087]
实施例6:
[0088]
聚合物杂化颜料的制备与实施例1的不同之处在于:制备过程中不添加4
‑
[(2r)
‑
3,4
‑
二氢
‑7‑
羟基
‑
2h
‑1‑
苯并吡喃
‑2‑
基]
‑3‑
(3
‑
甲基
‑2‑
丁烯
‑1‑
基)
‑
1,2
‑
苯二酚。
[0089]
有机硅油的制备与实施例5相同。
[0090]
一种利用色纺纤维制备花式羊绒纱的方法与实施例1的不同之处在于:步骤s1的染色过程中所用颜料为本实施例制得的。
[0091]
实施例7:
[0092]
一种利用色纺纤维制备花式羊绒纱的方法,具体为:
[0093]
s1:先对1/3量的羊绒毛进行染色(常规染色工艺),再与剩余2/3羊绒毛混合,制成均匀的毛条,投入生产,通过半精纺做成粗纱;
[0094]
s2:花捻pafa生产,采用花捻机对羊绒粗纱进行花式纱生产得到花式羊绒纱线;
[0095]
s3:拉毛,对做好的花式羊绒纱线进行拉毛;
[0096]
s4:蒸纱,对拉毛后的纱线进行蒸纱;
[0097]
s5:倒筒,蒸完的纱线通过倒成筒纱即得产品。
[0098]
对比例1:
[0099]
聚合物杂化颜料的制备与实施例6相同。
[0100]
有机硅油的制备与实施例1相同。
[0101]
一种利用色纺纤维制备花式羊绒纱的方法与实施例1的不同之处在于:步骤s1的染色过程中所用颜料为本对比例制得的。
[0102]
试验例1:
[0103]
1、透射电镜(tem)测试
[0104]
采用jsm
‑
1200ext20型透射电镜观察改性前后颜料红170的形貌变化情况,加速电压为80kv。
[0105]
对颜料红170以及实施例1制得的聚合物杂化颜料进行上述测试,结果如图1、图2所示。从图中分析可知,颜料红170粒径分布均匀,颜料表面光滑;而实施例1制得的聚合物
杂化颜料表面变得模糊,有明显的类似胶装的聚合物附着,表明聚合物有效包覆在颜料颗粒表面。
[0106]
2、红外光谱(ftir)表征
[0107]
采用spectrum one型傅里叶变换红外光谱分析仪测试,获得合成产物的红外图谱,分析图谱上的各结构基团。其中测试波数范围为4000~500cm
‑1,扫描频率32。
[0108]
对实施例1和实施例5制得的有机硅油进行上述测试,结果如图3所示。从图中分析可知,两种物质的红外光谱中,2160cm
‑1附近的si
‑
h特征吸收峰消失,1094cm
‑1、1014cm
‑1附近为si
‑
o
‑
si的特征吸收峰。此外,相比实施例1制得的有机硅油的红外光谱,实施例5制得有机硅油的红外光谱中,在3000~2800cm
‑1范围内出现的甲基特征吸收峰强度明显增强,在1600~1500cm
‑1范围内出现苯环骨架振动特征吸收峰;且在1250cm
‑1附近出现醚键的特征吸收峰强度显著增强;以上结果表明,实施例5中有机硅油成功制备。
[0109]
3、颜料包覆率测试
[0110]
将制备好的样品乳液离心,收集上层清液的空白乳胶烘干,称重记为m;下层沉淀烘干后称重记为m,按照下列式子计算包覆率:
[0111]
包覆率=m/(m+m)
×
100%
[0112]
对对比例1、实施例1~4制得的聚合物杂化颜料进行上述测试,结果如表1所示:
[0113]
表1包覆率测试结果
[0114]
样品包覆率/%对比例147.4实施例160.3实施例259.4实施例358.9实施例459.8
[0115]
从表1中分析可知,实施例1制得的聚合物杂化颜料的包覆率显著高于对比例1,表明聚合物单体中4
‑
[(2r)
‑
3,4
‑
二氢
‑7‑
羟基
‑
2h
‑1‑
苯并吡喃
‑2‑
基]
‑3‑
(3
‑
甲基
‑2‑
丁烯
‑1‑
基)
‑
1,2
‑
苯二酚的存在,可有效增强聚合物杂化颜料的包覆效果,使得颜料与聚合物的符合程度更高。
[0116]
4、分散稳定性测试
[0117]
取聚合物杂化颜料样品,1000r/min转速下离心8min,重复操作三次后干燥;接着取干燥样品0.05g,分散到200g去离子水中,搅拌均匀后待用。超声稳定性:将分散液置于烧杯中,使用超声波细胞粉碎机150w功率下进行超声,1min、15min、30min、60min分别取样观察样品的紫外吸收光谱。
[0118]
对对比例1和实施例1制得的聚合物杂化颜料进行上述测试,结果如图4和图5所示。从图中分析可知,不同的超声时间下,相比于图4所示对比例1制得的聚合物杂化颜料在最大吸收波长处吸收值发生明显的变化,图5所示的实施例1制得的聚合物杂化颜料在最大吸收波长(570nm)处吸收值保持不变,且吸收值明显增高,表明聚合物单体中4
‑
[(2r)
‑
3,4
‑
二氢
‑7‑
羟基
‑
2h
‑1‑
苯并吡喃
‑2‑
基]
‑3‑
(3
‑
甲基
‑2‑
丁烯
‑1‑
基)
‑
1,2
‑
苯二酚的存在,使得包覆的杂化颜料在超声作用下保持更佳优异的分散稳定性。
[0119]
5、存储稳定性测试
[0120]
将所制备的聚合物杂化颜料样品在室温下存储,每个一周取适量样品测试粒径大小,连续观察5周。
[0121]
对对比例1和实施例1制得的聚合物杂化颜料进行上述测试,结果如图6所示。从图中分析可知,放置6周后,对比例1制得的聚合物杂化颜料的粒径较最初的平均粒径增加了87nm,而实施例1聚合物杂化颜料的粒径较最初的平均粒径仅增加了38nm,表明聚合物单体中4
‑
[(2r)
‑
3,4
‑
二氢
‑7‑
羟基
‑
2h
‑1‑
苯并吡喃
‑2‑
基]
‑3‑
(3
‑
甲基
‑2‑
丁烯
‑1‑
基)
‑
1,2
‑
苯二酚的存在,显著增强了聚合物杂化颜料的存储稳定性。
[0122]
试验例2:
[0123]
羊绒纱性能测试
[0124]
耐晒色牢度参照gb/t8427
‑
2008《纺织品色牢度试验耐人造色牢度:氙弧》进行测试,摩擦色牢度参照gb/t 3920
‑
2008《纺织品色牢度试验耐摩擦色牢度标准》进行测试,耐洗色牢度参照gb/t3921
‑
2008《纺织品色牢度耐皂洗色牢度》进行测试。
[0125]
对对比例1、实施例1~6制得的色纺纱进行上述测试,结果如表2所示:
[0126]
表2染色性能测试结果
[0127][0128][0129]
从表2中分析可知,实施例1制得色纺纱的日晒牢度、耐摩擦牢度和耐水洗褪色牢度明显高于对比例1,表明羊绒毛染色过程用聚合物杂化颜料中4
‑
[(2r)
‑
3,4
‑
二氢
‑7‑
羟基
‑
2h
‑1‑
苯并吡喃
‑2‑
基]
‑3‑
(3
‑
甲基
‑2‑
丁烯
‑1‑
基)
‑
1,2
‑
苯二酚的加入,能够有效改善染色织物的色牢度,其日晒牢度、耐摩擦牢度和耐水洗褪色牢度的等级显著提升。实施例5的制得色纺纱的日晒牢度和耐水洗褪色牢度好于实施例1,实施例6的效果好于对比例1,表明羊绒毛染色后柔软整理用有机硅油中洋芹脑的加入,与其它组分复配使用,可进一步增强染色织物的日晒牢度和耐水洗褪色牢度。
[0130]
表观色深k/s值测试
[0131]
采用ce 7000a测色配色仪测定染色织物的k/s值。
[0132]
对对比例1、实施例1~6制得的色纺纱进行上述测试,结果如表3所示:
[0133]
表3k/s值测试结果
[0134]
样品k/s值对比例14.589实施例18.436实施例28.175实施例38.291实施例48.093实施例58.474实施例64.697
[0135]
从表3中分析可知,实施例1制得色纺纱的k/s值明显高于对比例1,表明羊绒毛染色过程用聚合物杂化颜料中4
‑
[(2r)
‑
3,4
‑
二氢
‑7‑
羟基
‑
2h
‑1‑
苯并吡喃
‑2‑
基]
‑3‑
(3
‑
甲基
‑2‑
丁烯
‑1‑
基)
‑
1,2
‑
苯二酚的加入,能够有效增强颜料的上染率。实施例5的制得色纺纱的k/s值与实施例1相当,实施例6的效果与对比例1相当,表明羊绒毛染色后柔软整理用有机硅油中洋芹脑的加入,对颜料在织物上的上染率无消极影响。
[0136]
拉伸性能
[0137]
参照gb/t 3916
‑
2013《纺织品卷装纱单根纱线断裂强力和断裂伸长率的测定(cre法)》进行测试。
[0138]
对对比例1、实施例1~6制得的色纺纱进行上述测试,结果如表4所示:
[0139]
表4力学性能测试结果
[0140]
样品断裂强力(cn/tex)断裂伸长率(%)对比例10.958.42实施例11.368.94实施例21.218.67实施例31.258.75实施例41.208.49实施例52.0315.18实施例61.5714.73
[0141]
从表3中分析可知,实施例1制得色纺纱的断裂强力明显高于对比例1,表明羊绒毛染色过程用聚合物杂化颜料中4
‑
[(2r)
‑
3,4
‑
二氢
‑7‑
羟基
‑
2h
‑1‑
苯并吡喃
‑2‑
基]
‑3‑
(3
‑
甲基
‑2‑
丁烯
‑1‑
基)
‑
1,2
‑
苯二酚的加入,能够有效增强色纺纱的断裂强力,改善其力学性能。实施例5的制得色纺纱的断裂强力和断裂伸长率均好于实施例1,实施例6的效果好于对比例1,表明羊绒毛染色后柔软整理用有机硅油中洋芹脑的加入,与其它组分复配使用,可有效增强色纺纱力学性能。
[0142]
试验例3:
[0143]
染色、柔软整理后纤维性能测试
[0144]
摩擦性能测试
[0145]
测试仪器:摩擦系数测定仪,型号y151,购自常州第二纺织机械有限公司。测试条件:标准大气条件下,预加张力为100mg,测定静摩擦系数时,手柄位置为bcg,转速1r/min;测定滑动摩擦系数时,手柄位置为adg,转速30r/min。根据欧拉公式,计算摩擦系数:
[0146][0147][0148]
式中,f—纤维食物悬挂张力钳质量,100mg;f0—悬挂张力钳质量与扭力天平读数m之间的差值,单位为mg;μ—绳子与圆柱表面之间的摩擦系数;θ—绳子与圆柱表面的接触角。
[0149]
纤维之间的摩擦系数可以表征纤维可纺性的好坏,
△
μ=μ静-μ动的数值越小,表示纤维手感柔滑,纺纱过程中纤维间越容易被分梳和牵伸。
[0150]
对实施例1和实施例5制得的染色、柔软整理后的纤维进行上述测试,结果如表5所示:
[0151]
表5摩擦性能测试结果
[0152]
样品
△
μ实施例10.0769实施例50.0345
[0153]
实施例5的制得染色、柔软整理后的纤维的
△
μ的值要低于实施例1,表明羊绒毛染色后柔软整理用有机硅油中洋芹脑的加入,与其它组分复配使用,可有效改善纤维表面性能,增强羊绒纤维的柔滑性。
[0154]
上述实施例中的常规技术为本领域技术人员所知晓的现有技术,故在此不再详细赘述。
[0155]
以上所述,仅为本发明的具体实施方式,但本发明的保护范围并不局限于此,任何熟悉本技术领域的技术人员在本发明揭露的技术范围内,可轻易想到变化或替换,都应涵盖在本发明的保护范围之内。因此,本发明的保护范围应以所述权利要求的保护范围为准。