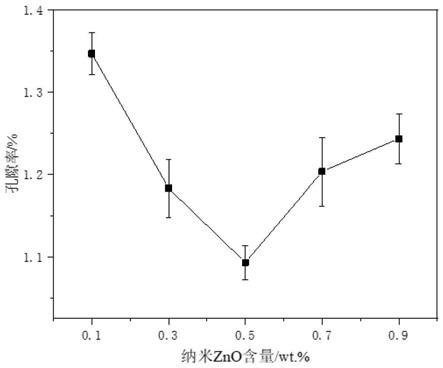
1.本发明属于金属防腐技术领域,具体涉及一种含纳米填料的无铬锌铝涂料及其制备方法和应用。
背景技术:2.达克罗涂层由于其对提高设备部件的耐腐蚀性非常有效,在金属防腐领域广泛使用,但达克罗涂液的主要成分为锌铝粉、铬酐、去离子水及其他助剂,而铬酐中cr
6+
毒性极强,具有很强的致癌性和污染性,我国越来越严格的环保规定要求摒弃了铬酐的使用。因此,无铬锌铝涂层得以开发使用,但其耐蚀性能和硬度(耐磨性)均不及达克罗涂层,不适用于防腐要求较高及承受载荷的环境下使用,极大地限制了其工业化发展进程。
技术实现要素:3.针对上述技术问题,本发明提供一种含纳米填料的无铬锌铝涂料及其制备方法和应用,具体的技术方案为:
4.一种含纳米填料的无铬锌铝涂料,包括纳米氧化锌(zno)和多壁碳纳米管(mwcnts)填料,所述纳米氧化锌添加质量百分比范围为0.1%~0.9%,所述多壁碳纳米管填料添加质量百分比为0.1%~0.7%,所述纳米氧化锌粒径为30
±
10nm,纯度大于99.9%;
5.所述的多壁碳纳米管为羧基化的多壁碳纳米管,所述氧化锌添加质量百分比为0.3%~0.7%范围内,多壁碳纳米管填料添加质量百分比为0.1~0.4%,内径5
‑
12nm,外径10
‑
20nm,长度10
‑
30μm,纯度大于90%。
6.上述的一种含纳米填料的无铬锌铝涂料的制备方法,包括以下步骤:
7.1)分别配置由a组分和b组分两部分浆料,a组分与b组分的比例是4:1~3:1;
8.2)a组分包括kh560硅烷偶联剂、甲醇、去离子水、锌粉及铝粉,所述kh560硅烷偶联剂的比例为15~20%、甲醇为45~50%、锌粉及铝粉为25~30%,其余是去离子水,将kh560硅烷偶联剂、甲醇和去离子水混合搅拌使其充分水解,加入锌粉和铝粉搅拌30min,其中,锌粉:铝粉=6:1的比例;
9.3)b组分包括乙二醇、吐温20和去离子水,所述乙二醇占比为45~50%、吐温20占比为:40~45%,其余是去离子水,将乙二醇、去离子水和吐温20混合搅拌40min,使其融合均匀;
10.4)将a组分、b组分混合,并添加增稠剂(羟乙基纤维素),消泡剂(异辛醇)和缓蚀剂(钼酸钠),将整个混合物用超声搅拌器进行超声分散2h获得涂料。
11.将不同比例的纳米氧化锌颗粒加入b组分用磁力搅拌器搅拌均匀,并用超声搅拌器进行超声分散2h,本发明采用表面酸化过的多壁碳纳米管,表面带有羧基,有利于分散。
12.本发明提供的含纳米填料的无铬锌铝涂料用于制备金属材料表面防腐涂层。
13.本发明的有益效果:
14.所述的含纳米填料的无铬锌铝涂料形成的mwcnts
‑
纳米和zno复合增强涂层具有
以下几个特性:
15.(1)随纳米zno添加量增多,涂层阻抗模量先增大后减小,自腐蚀电流密度先减小后增大,当纳米zno添加量为0.5%时,涂层阻抗模量值为1.37
×
104ω2cm2,自腐蚀电流密度为4.755
×
10
‑6a/cm2,比未添加纳米填料的涂层降低两个数量级。
16.(2)纳米填料影响涂层耐蚀性能的机理是,mwcnts可以增强涂层的屏蔽性能,同时增加锌铝粉之间的电连接,提高阴极保护性能;纳米zno可以填充涂层孔隙,提高涂层屏蔽性能。
17.(3)未添加纳米填料的涂层摩擦系数为0.84,添加0.3%mwcnts的涂层摩擦系数变化不大为0.89,而添加纳米zno后涂层摩擦系数变化明显,呈先减小后增大的趋势,当纳米zno添加量为0.3%时涂层摩擦系数最小,仅为0.67比未添加纳米颗粒的涂层降低了20.2%。
18.本发明采用微量纳米填料便可极大的提升防腐涂层的耐蚀性能、硬度和耐磨性能,延长涂层使用寿命。
附图说明
19.图1为本发明的涂层制备工艺流程图;
20.图2为本发明的0.3%mwcnts
‑
纳米zno复合涂层的宏观形貌;
21.图3为本发明的纳米zno添加量0.5%涂层表面的sem图;
22.图4为本发明的纳米zno添加量0.5%涂层截面的sem图;
23.图5为本发明的纳米zno添加量0.5%涂层的eds图谱;
24.图6为本发明的纳米zno添加量0.5%的涂层的xrd谱图;
25.图7为本发明的涂层孔隙率与纳米zno添加量的关系;
26.图8为本发明的不同纳米zno添加量对应涂层的水接触角;
27.图9为本发明的不同纳米zno添加量对应涂层的结合力;
28.图10为未添加纳米zno的涂层xrd图谱。
具体实施方式
29.结合实施例说明本发明的具体技术方案。
30.实施例1
31.本实施例提供一种含纳米填料的无铬锌铝涂料,包括纳米氧化锌(zno)和多壁碳纳米管(mwcnts)填料,所述的纳米氧化锌粒径为30
±
10nm,纯度大于99.9%;所述的多壁碳纳米管为羧基化的多壁碳纳米管,内径5
‑
12nm,外径10
‑
20nm,长度10
‑
30μm,纯度大于90%。
32.含纳米填料的无铬锌铝涂料的制备方法,包括以下步骤:
33.1)分别配置由a组分和b组分两部分浆料,a组分与b组分的比例是4:1~3:1;
34.2)a组分包括kh560硅烷偶联剂、甲醇、去离子水、锌粉及铝粉,所述kh560硅烷偶联剂的比例为15~20%、甲醇为45~50%、锌粉及铝粉为25~30%,其余是去离子水,将kh560硅烷偶联剂、甲醇和去离子水混合搅拌使其充分水解,加入锌粉和铝粉搅拌30min,其中,锌粉:铝粉=6:1的比例;
35.3)b组分包括乙二醇、吐温20和去离子水,所述乙二醇占比为45~50%、吐温20占
比为:40~45%,其余是去离子水,将乙二醇、去离子水和吐温20混合搅拌40min,使其融合均匀;
36.4)将a组分、b组分混合,并添加增稠剂(羟乙基纤维素),消泡剂(异辛醇)和缓蚀剂(钼酸钠),将整个混合物用超声搅拌机进行超声分散2h获得涂料。
37.本发明提供的含纳米填料的无铬锌铝涂料用于制备金属材料表面防腐涂层。
38.a、b组分的组成及各试剂在涂液中的占比为:
39.表1
[0040][0041]
采用本实施例获得的含纳米填料的无铬锌铝涂料,进行涂层涂覆,无铬锌铝涂层涂覆方法主要有浸涂、喷涂、刷涂等,本实施例采用刷涂的涂覆方式制备涂层,工艺流程如图1所示,涂液均匀刷涂在预处理过的基体上,静置待其自然流平后于70℃的高温干燥箱中预烘固化10min,预防烧结过程中水醇等蒸发速度过快,成膜物质来不及补足而留下孔洞,涂层烧结的温度为300℃,保温25min后出炉冷却并进行二次涂覆,固化烧结得到所需涂层。
[0042]
实施例2
[0043]
获得的纳米zno增强涂层基本性能:
[0044]
1涂层形貌及成分
[0045]
图2为0.3%mwcnts
‑
纳米zno复合涂层的宏观形貌,图2中,a到e中纳米zno添加质量百分比依次为0.1%、0.3%,、0.5%、0.7%、0.9%。所有涂层表面均平整光滑,厚度均匀,在33~35μm范围内,无麻点气孔等缺陷,与未添加纳米zno的涂层形貌及厚度没有明显区
别。可见涂层中的纳米zno并未出现严重团聚现象,涂液粘稠度适中,流平性很好,涂层的烘干及烧结过程条件适宜,所有涂层均呈现银灰色金属光泽,不存在明显区别。
[0046]
由于不同纳米zno添加量对应微观形貌并无明显区别,因此图3仅列出了纳米zno添加量为0.5%的0.3%mwcnts
‑
纳米zno复合增强涂层表面sem图及局部放大图。(a)图中涂层表面致密,银灰色锌粉和铝粉层片堆叠,排列有序。部分锌粉及铝粉外圈出现白亮色物质,为锌铝粉氧化物,这些氧化物导电性较差在sem图中呈现明显的白亮色。(b)图为a区放大图,图中红圈区域不规则形状颗粒物为纳米zno,这些纳米颗粒分散较为良好,均匀填充在锌铝粉孔隙中,并未影响周围锌粉和铝粉的有序排列,且在一定程度上降低了涂层的孔隙率,减少了电解质渗入涂层的途径,并且这些硬质纳米颗粒对涂层具有一定的支撑作用,可以提高涂层硬度。
[0047]
图4为纳米zno添加量0.5%的涂层截面sem图。涂层中锌铝粉大致平行于基体排列,厚度方向上锌铝粉之间接触紧密,平行于表面方向上交错相叠不存在直达基体的孔洞,由于放大倍数较小,并未观察到纳米zno,说明不存在严重团聚,涂层与基体结合较好。
[0048]
图5为添加0.5%纳米zno的0.3%mwcnts
‑
纳米zno复合增强涂层微区eds图谱。该处o元素含量高达28.34wt.%,远远超过图10中未加纳米zno的无铬锌铝涂层中的氧含量,zn元素含量也高达30.03%,并结合左图中该物质形态,可以判定该处为纳米zno。该处c元素含量仅次于o元素含量,可能是由于mwcnts混入纳米zno当中所致,其余al元素及si元素分别来自于周围吸附在纳米zno上的铝粉及硅烷偶联剂。
[0049]
2涂层物相
[0050]
图6为纳米zno添加量为0.5%的0.3%mwcnts
‑
纳米zno复合增强涂层测得的xrd谱,涂层中主要存在单质zn,单质al及锌的氧化物,与图10中未添加纳米zno的涂层xrd图谱相比,单质al峰强度相差不大,但由于纳米zno的添加使涂层中含有更多的zno相,而zno的最强衍射峰与zn的峰重叠,因此导致图中单质zn及zno峰强度成倍增长。除此之外,xrd图谱中并未出现其他衍射峰,说明在涂层制备过程中,纳米zno并不会与涂层中其他物质发生反应生成新相。
[0051]
3涂层孔隙率
[0052]
图7呈现了0.3%mwcnts
‑
纳米zno复合增强涂层孔隙率随纳米zno添加量的变化规律。纳米zno添加量为0、0.1%、0.3%、0.5%、0.7%、0.9%的涂层孔隙率分别为1.63%、1.35%、1.18%、1.09%、1.20%、1.24%。可见涂层孔隙率随纳米zno添加量的上升呈先减小后增大的趋势,添加量为0.5%时,涂层孔隙率最低,比未添加纳米zno的涂层下降了33.1%,可见适量纳米zno可以均匀分散在涂层中,有效减少涂层表面直达基体的孔隙,阻碍了电解质渗入涂层的进程。
[0053]
4涂层水接触角
[0054]
图8为不同纳米zno添加量(纳米zno添加量依次为0.1%、0.3%,、0.5%、0.7%、0.9%)对应0.3%mwcnts
‑
纳米zno复合增强涂层的水接触角,当纳米zno添加量小于0.5%时,涂层水接触角随其添加量增加仅出现微量的增大,从67.1
°
增至71.8
°
,涂层亲水性略有减弱。而纳米zno添加量达到0.7%及以上时,水接触角下降到60
°
以下,此时涂层亲水性增强,说明此时电解质溶液更容易浸湿涂层表面。涂层中仅添加0.3%的mwcnts而未添加纳米zno时其水接触角为72.4
°
,可知纳米zno添加量小于0.5%时对涂层水接触角的影响并不
大。
[0055]
涂层的水接触角增大,水分子在涂层表面的附着和渗透能力会减小,有效降低金属基材电化学腐蚀的发生,提高涂层耐蚀性能。添加mwcnts前后涂层的水接触角测试结果,水接触角随着mwcnts添加量的增加呈先增大后减小的趋势,含mwcnts的涂层水接触角均大于未添加mwcnts涂层,最大可达到72.4
°
。
[0056]
5涂层结合力
[0057]
分别对不同纳米zno添加量(纳米zno添加量依次为0.1%、0.3%,、0.5%、0.7%、0.9%)对0.3%mwcnts
‑
纳米zno复合增强应涂层进行附着力测试,图9为测试结果,对比附着力等级评价标准,加入纳米zno的涂层附着力均为iso
‑
1级,与mwcnts单独存在的涂层结合力并无明显差异。这可能是由于涂层烧结温度较低,纳米zno存在形式并未发生变化,过程中并无新相生成,这与xrd测试结果一致。对结合力起关键影响作用的是硅烷偶联剂,纳米zno的加入对涂层的结合力并无明显作用。
[0058]
6涂层硬度
[0059]
表2不同纳米zno添加量对应涂层的显微硬度
[0060][0061]
表2为不同纳米zno添加量(纳米zno添加量依次为0.1%、0.3%,、0.5%、0.7%、0.9%)对应的0.3%mwcnts
‑
纳米zno复合增强涂层的硬度值。可见随着纳米zno添加量的增多,涂层平均硬度先上升后出现小幅度下降。当纳米zno添加量低于0.7%时,涂层硬度随其添加量上升而不断提高,且硬度值波动较小,分布较为均匀,在添加量达到0.7%时,涂层硬度为156.5hv
0.1
,比未添加纳米颗粒的涂层提高了50.3%。说明纳米zno在涂层中分散较好。当涂层中纳米zno添加量达到0.9%时,涂层平均硬度有所下降,且硬度分布非常不均匀,局部表现出高硬度值,其余区域硬度较低,推测硬度较高的地方可能是纳米zno的团聚体,硬度较低的地方为锌铝粉。适量纳米zno的添加之所以能够提高涂层硬度,是由于纳米zno尺寸小能够填充涂层孔隙,且其质硬对涂层有一定的支撑作用。
[0062]
实施例3
[0063]
图2中不同添加量mwcnts增强涂层试样宏观形貌,涂层样品厚度在33~35μm范围内,未添加mwcnts涂层呈银白色,有金属光泽,表面光滑连续,无孔洞、裂纹或麻点等缺陷,涂层中加入mwcnts后,涂层颜色略微变暗,表面形貌并无明显变化,说明mwcnts并未对涂层制备及烧结工艺产生不良影响,mwcnts的添加量为0%、0.1%、0.3%、0.5%、0.7%。
[0064]
图3中显示了不同mwcnts添加量对应涂层表面sem图,较低倍数下可观察到未添加
mwcnts的涂层表面平整致密,无明显孔洞缺陷,zn薄片和al薄片均匀分散,加入0.3%及0.7%的mwcnts涂层低倍形貌并无明显改变,其局部放大图中可观察到mwcnts添加量为0.3%的涂层中mwcnts分散较为良好,不存在mwcnts添加量为0.7%的涂层中大量团聚的现象。
[0065]
图4为不同mwcnts添加量对应涂层截面sem图,可见涂层是由缩合的硅烷偶联剂构成三维网络结构,片状锌粉和铝粉填充其中且几乎与基体平行,层层相叠,紧密连接,涂层与基体结合较好,3种涂层截面并无明显区别,mwcnts添加量为0%、0.3%、0.7%。
[0066]
图5为添加0.3%mwcnts的涂层表面微区图以及对应eds图谱。观察到添加了0.3%mwcnts的涂层中除无铬锌铝涂层本身所含有的zn、al、si、o等主要元素外,还出现c元素,且其净强度处于较高水平,结合对应微区sem图中物质形态,可以确定涂层中净强度高的c元素为mwcnts。
[0067]
图6为mwcnts添加量为0.3%的涂层测得的xrd谱,由图可看出涂层中主要存在zn,al及zno的衍射峰,这些物相主要来源于无铬锌铝涂层。图中峰强度与图6中未添加mwcnts的涂层xrd无明显改变,说明涂层中所添加的mwcnts并未与其他物质发生反应,依然保持原始的状态,同时mwcnts的存在也没有影响涂层烧结过程中其余反应的进行。
[0068]
图7为利用image j计算孔隙在涂层表面占比的结果,mwcnts添加量为0、0.1%、0.3%、0.5%、0.7%的涂层孔隙率分别为3.25%、1.97%、1.63%、2.45%、2.84%。可见随着mwcnts添加量的增加,涂层孔隙率先减小后增大,且存在最佳添加量使涂层孔隙率显著降低,当mwcnts添加量为0.3%时,涂层孔隙率最小,比未添加mwcnts的涂层降低了49.8%。可见适量mwcnts的加入,可有效降低涂层孔隙率,但当mwcnts添加量过多,会产生严重团聚,反而割裂了涂层本身的层叠连续性,影响锌铝粉的有序排列,使涂层孔隙率增加。
[0069]
图8中材料表面自由能及表面微米
‑
纳米粗糙结构是影响涂层疏水性的主要因素,分析表明,适量mwcnts的添加和均匀分散能够有效填补涂层中锌铝粉之间缝隙,减少腐蚀介质渗入侵蚀涂层内部和基体,涂层亲水性下降。并且mwcnts的均匀分布使得涂层表面构建起微米
‑
纳米凹凸结构,涂层表面粗糙度增大,水难以润湿涂层表面,水接触角变大。然而,当涂层中mwcnts添加量为0.5%和0.7%时,由于mwcnts自身的高表面能而产生了团聚,微结构劣势显现,水接触角变小,不同mwcnts添加量0%、0.1%、0.3%、0.5%、0.7%对应涂层的水接触角/(
°
)为38.9
°
、56.9
°
、72.4
°
、66.0
°
、60.9
°
。
[0070]
图9所示为通过划格法测试得到的不同mwcnts添加量对应涂层结合力的结果,5种mwcnts添加量的涂层测试结果差异不大,均表现为在切口的相交处有小片剥落,划格区内实际破损不超过5%,符合iso
‑
1级标准。但其中mwcnts添加量为0.3%的涂层剥落面积更小,结合力更靠近iso
‑
0级,结合力最好,推测适量的mwcnts可以在一定程度上提高涂层结合力的原因是,羧酸化的mwcnts均匀地分散在涂层中,在后期烧结过程中,mwcnts上的
‑
cooh与钢基体及锌粉和铝粉发生反应,形成金属
‑
o
‑
c共价键,该键合可以有效增加涂层与基体间及涂层内部的结合力。而随着mwcnts添加量继续增多,更容易发生团聚现象,影响涂层中锌铝粉的有序排列,割裂了涂层的连续性,降低了涂层间的结合力,不同mwcnts添加量0%、0.1%、0.3%、0.5%、0.7%对应涂层的结合力。
[0071]
mwcnts添加量在0%~0.7%时,涂层宏观形貌无明显变化,未添加mwcnts的涂层光滑平整,呈银灰色金属光泽,添加了mwcnts的涂层颜色略微变暗,无明显缺陷,涂层中物
相主要为zn,al及zno。涂层的水接触角随mwcnts添加量的增加先增大后减小,mwcnts添加量为0.3%时的水接触角最大,为72.4
°
。添加mwcnts的涂层结合力均为iso
‑
1级,在mwcnts添加量为0.3%时涂层剥落面积更小,结合力更靠近iso
‑
0级。
[0072]
随mwcnts添加量增大,涂层自腐蚀电流密度先减小后增大,mwcnts添加量为0.3%的涂层自腐蚀电流密度最小,为2.019
×
10
‑5a/cm2,比未添加纳米颗粒的涂层降低了一个数量级。随mwcnts添加量的增大,涂层耐3.5wt.%nacl溶液浸泡性能先上升后下降。在未出现起泡、脱落及出锈情况下,添加量为0.3%的涂层浸泡时长最长,预制损伤涂层浸泡时间可达240h,完好涂层浸泡时长超过480h,所有涂层中,mwcnts添加量0.3%的涂层耐蚀效果最好。