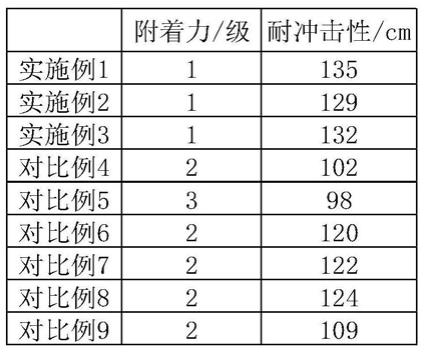
1.本发明属于防腐涂料技术领域。更具体地,涉及一种应用于船舶的防腐涂料及其制备方法。
背景技术:2.随着海洋航运的快速发展及对海洋资源的不断开发利用,海洋生物污损带来的危害日益突出。对于在海洋里航行的船舶,如果不对海洋污损生物进行有效的防治,其会附着在船体表面,增加船体重量及船体表面粗糙度,增加航行阻力,导致船舶的航速及其机动性能降低,防止海洋生物污损是人类进行海洋活动的重点研究方向,而涂装防污涂料是目前最便捷、经济有效的防治方法。
3.石墨烯具有高比表面积、高导电性、极大的拉伸强度、独特的结构和电学性质,在许多领域得到了广泛研究。石墨烯晶格的几何孔隙为0. 064 nm,理论上可以阻隔像氦气(0. 208 nm)或氢气(0. 314 nm)这样的小分子。作为防腐填料,可以有效阻隔腐蚀因子。此外,堆叠的石墨烯层会延长腐蚀因子的侵入途径,从而形成扩散屏障,产生“迷宫效应”。其中,曹祥康等将不同质量分数的石墨烯纳米片添加到环氧富锌(40%锌)涂层中,随着石墨烯添加量的增加,涂层中锌粉的牺牲阳极作用先增强后减弱。0.5%~1. 0%石墨烯添加量可以有效地提高阴极保护作用。陈中华等对石墨烯环氧富锌涂层进行电化学阻抗谱(eis)测试发现40%锌粉、0.80%石墨烯的水性环氧涂料性能最佳,且石墨烯基填料在环氧富锌涂层中依旧表现出“迷宫效应”。
4.鳞片填料可在涂层中层叠排列,延长腐蚀介质的渗透路径,提高涂层的防腐蚀性能。玄武岩鳞片是一种新型鳞片材料,选用天然玄武岩矿石经高温熔融、澄清、均化成型、筛选等工艺加工而成的新型材料,呈现透明或深绿色片状结构,其化学组成和结构赋予了玄武岩鳞片防腐涂料耐磨损、耐高温氧化、耐腐蚀的特性,且成本低廉,玄武岩鳞片聚合物涂料可以降低金属腐蚀速率8~9倍,水蒸气透过率5~9 倍,在防水耐水防腐蚀领域具有广泛的行业应用前景,可以替代玻璃鳞片涂料用于石化、海洋船舶、桥梁、建筑等防腐领域。
5.cn109777262a公开了一种石墨烯改性抑菌防腐涂料,所述抑菌防腐涂料的原料按重量份计包括:环氧树脂30-50份、改性硅藻土15-35份、石墨烯材料0.5-10份、纳米银粒子0.5-1份、填料8-20份、助剂1.5-6份、纳米银铜负载poss基树脂13-15份与水16-25份。本发明制备的一种石墨烯改性抑菌防腐涂料能够解决船舶、海洋设备、粮仓等需要抑菌防腐领域的实际问题,有很好的经济效益,节约能源材料;在钢结构、金属板等方面具有优异的附着力,耐磨性好、可以经受高低温、高盐度、能够很好耐受细菌腐蚀,达到抑菌防腐作用。
6.尽管上述涂料已经取得了一定的效果,但是上述防腐涂料仍不能满足实际生产的需求,因而仍急需一种新的防腐涂料来解决耐磨性、耐水性、耐盐雾性、柔韧性、附着力以及抑菌防腐等问题。
技术实现要素:7.本发明要解决的技术问题是克服现有防腐涂料的耐磨性、耐水性、耐盐雾性、柔韧性、附着力以及抑菌防腐差的缺陷和不足,提供一种应用于船舶的防腐涂料及其制备方法。
8.本发明的目的是提供一种应用于船舶的防腐涂料。所述应用于船舶的防腐涂料的原料按重量份计包括:环氧树脂40-60份、改性玄武岩鳞片/氮化碳复合材料5~15份、钐和铜共掺杂的氧化锌/石墨烯复合材料3-8份、填料10-18份、助剂1.5-6份与水20~30份。本发明制备的一种应用于船舶的防腐涂料能够解决船舶需要抑菌防腐的实际问题,且其具有优异的附着力,耐磨性好、可以经受高低温、高盐度、能够很好耐受细菌腐蚀,达到抑菌防腐作用。
9.本发明另一目的是提供一种应用于船舶的防腐涂料的其制备方法。
10.本发明上述目的通过以下技术方案实现:一种应用于船舶的防腐涂料,所述防腐涂料的原料按重量份计包括:环氧树脂40-60份、改性玄武岩鳞片/氮化碳复合材料5~15份、钐和铜共掺杂的氧化锌/石墨烯复合材料3-8份、填料10-18份、助剂1.5-6份与水20~30份。
11.优选的,所述钐和铜共掺杂的氧化锌/石墨烯复合材料的制备方法包括以下步骤:(1)首先将氧化石墨烯分散于去离子水中,得到氧化石墨烯分散液,然后加入硫代乙酰胺的乙醇溶液,搅拌均匀后装入水热釜中进行水热反应,水热反应完成后,干燥,得到前驱体;(2)将前驱体置于管式炉中,通以惰性气体保护进行热处理得到产物;(3)将锌源、六次甲基四胺、钐源和铜源溶于去离子水中的搅拌得到混合溶液;将步骤(2)所得到的产物添加到上述混合物溶液中,然后将得到的混合溶液转移到反应釜中于110~150℃下保温4~8h,将得到的沉淀物离心洗净并干燥,煅烧,获得钐和铜共掺杂的氧化锌/石墨烯复合材料。
12.优选的,在步骤(1)中,所述氧化石墨烯与硫代乙酰胺的质量比为1:0.5~1.5;氧化石墨烯分散液的浓度为6mg/ml~12mg/ml;去离子水与乙醇用量的体积比为1:1~3;水热反应温度为140~180℃,反应时间为12~24h。
13.优选的,在步骤(2)中,所述热处理的升温速率为4~6℃/min,热处理温度为600~800℃,热处理时间为2~5h;所述惰性气体为氦气、氩气或氖气。
14.优选的,在步骤(3)中,所述锌源、六次甲基四胺、钐源和铜源的摩尔比为1:1:0.01~0.03:0.01~0.03;所述锌源与步骤(2)得到的产物的质量比为1:2~4;所述干燥温度为100~120℃,干燥时间为10~20h,所述煅烧温度为400~500℃,煅烧时间为2~4h。
15.优选的,所述改性玄武岩鳞片/氮化碳复合材料的制备方法包括以下步骤:按硅烷偶联剂的质量分数为1~5wt%,将硅烷偶联剂加入到醇中,得到硅烷偶联剂的醇溶液;将玄武岩鳞片和氮化碳加入到硅烷偶联剂的醇溶液中,得到混合液;然后在500w超声波清洗机中超声分散30~60min;过滤、洗涤、于80~100℃干燥10~16h得到改性玄武岩鳞片/氮化碳复合材料。
16.优选的,所述醇为甲醇或乙醇;所述硅烷偶联剂为氯甲基三乙氧基硅烷、氨丙基三乙氧基硅烷或羟丙基三甲氧基硅烷;所述玄武岩鳞片、氮化碳与硅烷偶联剂的质量比为1: 0.8~1.2:0.2。
17.优选的,所述的助剂为分散剂、膜助剂、消泡剂、ph 稳定剂、流平剂与防沉剂。
18.优选的,所述的填料为纳米电气石粉、纳米二氧化钛、滑石粉、云母粉、重钙和海藻胶粉中的一种或几种的混合物。
19.优选的,所述分散剂为byk101、膜助剂为丙二醇丙醚,消泡剂为二甲基硅油、流平剂为异佛尔酮;防沉剂为聚乙烯蜡;基于上述所述的应用于船舶的防腐涂料的制备方法,所述制备方法包括以下步骤,先将环氧树脂、改性玄武岩鳞片/氮化碳复合材料、钐和铜共掺杂的氧化锌/石墨烯复合材料与水放入高速搅拌机中混合,搅拌速率为3000~4000r/min,搅拌20~40min,然后将填料和助剂添加到上述混合物中继续搅拌20~40min,得到防腐涂料。
20.本发明具有以下有益效果:(1)本发明通过对石墨烯进行改性能够增加表面活性基团,而且有利于为氧化锌的负载提供更多的活性位,而且通过钐和铜的共掺杂,进而提高氧化锌的杀菌性能以及提高防腐性能;(2)通过对玄武岩鳞片和氮化碳进行硅烷化改性提高其在涂料中的稳定性以及防腐性能,而且惊奇的发现通过同时添加玄武岩鳞片和氮化碳,两者之间具有相互协调作用,而且通过协调作用现在提高了涂料的防腐等性能(3)通过将钐和铜共掺杂的氧化锌/石墨烯复合材料和改性玄武岩鳞片/氮化碳复合材料添加到涂料中,惊奇的发现,两者之间具有相互协同作用,而且通过两者的协同配合提高了涂料的防腐等性能。
21.(4)本发明制备的涂料具有优异的附着力、耐磨性、耐腐蚀等性能。
附图说明
22.附图1是实施例1-3与对比例4-9的涂料的附着力及耐冲击力结果图。
23.附图2是测试实施例1-3和对比例1-9制得的涂料的防腐性能对比图。
24.附图3是杀菌测试结果图。
具体实施方式
25.以下结合具体实施例来进一步说明本发明,但实施例并不对本发明做任何形式的限定。除非特别说明,本发明采用的试剂、方法和设备为本技术领域常规试剂、方法和设备。
26.除非特别说明,以下实施例所用试剂和材料均为市购。
27.本发明中实施例与对比例中所采用的助剂为分散剂、膜助剂、消泡剂、ph稳定剂、流平剂与防沉剂,其中,分散剂为byk101、膜助剂为丙二醇丙醚,消泡剂为二甲基硅油、流平剂为异佛尔酮;防沉剂为聚乙烯蜡,可从市场购得;在本发明中,分散剂、膜助剂、消泡剂、ph稳定剂、流平剂与防沉剂的质量相同。
28.实施例1一种应用于船舶的防腐涂料,所述防腐涂料的原料按重量份计包括:环氧树脂50份、改性玄武岩鳞片/氮化碳复合材料10份、钐和铜共掺杂的氧化锌/石墨烯复合材料6份、纳米二氧化钛14份、助剂4份与水25份;所述钐和铜共掺杂的氧化锌/石墨烯复合材料的制备方法包括以下步骤:
(1)首先将9mg氧化石墨烯分散于10ml去离子水中,得到氧化石墨烯分散液,然后加入20ml浓度为0.45mg/ml的硫代乙酰胺的乙醇溶液,搅拌均匀后装入水热釜中进行水热反应,于160℃水热反应18h后,干燥,得到前驱体;(2)将前驱体置于管式炉中,在氩气保护下,从室温以5℃/min的升温速率升至700℃,并在该温度下热处理4h得到产物;(3)将10mmol醋酸锌、10mmol六次甲基四胺、0.2mmol硝酸钐和0.2mmol硝酸铜溶于50ml去离子水中的搅拌得到混合溶液;将步骤(2)所得到的5.51g产物添加到上述混合物溶液中,然后将得到的混合溶液转移到反应釜中于130℃下保温5h,将得到的沉淀物离心洗净并于110℃干燥16h,然后于450℃煅烧3h,获得钐和铜共掺杂的氧化锌/石墨烯复合材料;所述改性玄武岩鳞片/氮化碳复合材料的制备方法包括以下步骤:按氨丙基三乙氧基硅烷的质量分数为3wt%,将氨丙基三乙氧基硅烷加入到乙醇中,得到氨丙基三乙氧基硅烷的乙醇溶液;将15g玄武岩鳞片和15g氮化碳加入到100g氨丙基三乙氧基硅烷的乙醇溶液中,得到混合液;然后在500w超声波清洗机中超声分散45min;过滤、洗涤、于90℃干燥13h得到改性玄武岩鳞片/氮化碳复合材料;所述防腐涂料的制备方法包括以下步骤,先将环氧树脂、改性玄武岩鳞片/氮化碳复合材料、钐和铜共掺杂的氧化锌/石墨烯复合材料与水放入高速搅拌机中混合,搅拌速率为3500r/min,搅拌30min,然后将纳米二氧化钛和助剂添加到上述混合物中继续搅拌30min,得到防腐涂料。
29.实施例2一种应用于船舶的防腐涂料,所述防腐涂料的原料按重量份计包括:环氧树脂60份、改性玄武岩鳞片/氮化碳复合材料5份、钐和铜共掺杂的氧化锌/石墨烯复合材料8份、纳米电气石粉10份、助剂6份与水20份;所述钐和铜共掺杂的氧化锌/石墨烯复合材料的制备方法包括以下步骤:(1)首先将12mg氧化石墨烯分散于10ml去离子水中,得到氧化石墨烯分散液,然后加入20ml浓度为0.4mg/ml的硫代乙酰胺的乙醇溶液,搅拌均匀后装入水热釜中进行水热反应,于180℃水热反应12h后,干燥,得到前驱体;(2)将前驱体置于管式炉中,从室温以6℃/min的升温速率升至800℃,并在该温度下热处理2h得到产物;(3)将10mmol硝酸锌、10mmol六次甲基四胺、0.3mmol醋酸钐和0.1mmol氯化铜溶于50ml去离子水中的搅拌得到混合溶液;将7.58mg步骤(2)所得到的产物添加到上述混合物溶液中,然后将得到的混合溶液转移到反应釜中于150℃下保温4h,将得到的沉淀物离心洗净并于120℃干燥10h,于500℃煅烧2h,获得钐和铜共掺杂的氧化锌/石墨烯复合材料;所述改性玄武岩鳞片/氮化碳复合材料的制备方法包括以下步骤:按羟丙基三甲氧基硅烷的质量分数为5wt%,将羟丙基三甲氧基硅烷加入到甲醇中,得到羟丙基三甲氧基硅烷的甲醇溶液;将25g玄武岩鳞片和20g氮化碳加入到100g羟丙基三甲氧基硅烷的甲醇溶液中,得到混合液;然后在500w超声波清洗机中超声分散60min;过滤、洗涤、于100℃干燥10h得到改性玄武岩鳞片/氮化碳复合材料;所述防腐涂料的制备方法包括以下步骤,先将环氧树脂、改性玄武岩鳞片/氮化碳复合材料、钐和铜共掺杂的氧化锌/石墨烯复合材料与水放入高速搅拌机中混合,搅拌速率
为4000r/min,搅拌20min,然后将纳米电气石粉和助剂添加到上述混合物中继续搅拌20min,得到防腐涂料。
30.实施例3一种应用于船舶的防腐涂料,所述防腐涂料的原料按重量份计包括:环氧树脂40份、改性玄武岩鳞片/氮化碳复合材料15份、钐和铜共掺杂的氧化锌/石墨烯复合材料3份、云母粉18份、助剂1.5份与水30份;所述钐和铜共掺杂的氧化锌/石墨烯复合材料的制备方法包括以下步骤:(1)首先将9mg氧化石墨烯分散于10ml去离子水中,得到氧化石墨烯分散液,然后加入10ml浓度为0.45mg/ml的硫代乙酰胺的乙醇溶液,搅拌均匀后装入水热釜中进行水热反应,于140℃水热反应24h后,干燥,得到前驱体;(2)将前驱体置于管式炉中,在氖气保护下,从室温以4℃/min的升温速率升至600℃,并在该温度下热处理5h得到产物;(3)将10mmol氯化锌、10mmol六次甲基四胺、0.1mmol醋酸钐和0.3mmol硝酸铜溶于50ml去离子水中的搅拌得到混合溶液;将步骤(2)所得到的2.73g产物添加到上述混合物溶液中,然后将得到的混合溶液转移到反应釜中于110℃下保温8h,将得到的沉淀物离心洗净并于100℃干燥20h,于400℃煅烧4h,获得钐和铜共掺杂的氧化锌/石墨烯复合材料;所述改性玄武岩鳞片/氮化碳复合材料的制备方法包括以下步骤:按羟丙基三甲氧基硅烷的质量分数为1wt%,将羟丙基三甲氧基硅烷加入到乙醇中,得到羟丙基三甲氧基硅烷的乙醇溶液;将5g玄武岩鳞片和6g氮化碳加入到100g羟丙基三甲氧基硅烷的乙醇溶液中,得到混合液;然后在500w超声波清洗机中超声分散30min;过滤、洗涤、于80℃干燥16h得到改性玄武岩鳞片/氮化碳复合材料;所述防腐涂料的制备方法包括以下步骤,先将环氧树脂、改性玄武岩鳞片/氮化碳复合材料、钐和铜共掺杂的氧化锌/石墨烯复合材料与水放入高速搅拌机中混合,搅拌速率为3000r/min,搅拌40min,然后将云母粉和助剂添加到上述混合物中继续搅拌40min,得到防腐涂料。
31.对比例1一种应用于船舶的防腐涂料,所述防腐涂料的原料按重量份计包括:环氧树脂50份、改性玄武岩鳞片/氮化碳复合材料10份、钐和铜共掺杂的氧化锌/石墨烯复合材料6份、纳米二氧化钛14份、助剂4份与水25份;所述钐和铜共掺杂的氧化锌/石墨烯复合材料的制备方法包括以下步骤:(1)首先将9mg氧化石墨烯分散于10ml去离子水中,得到氧化石墨烯分散液,然后加入20ml乙醇,搅拌均匀后装入水热釜中进行水热反应,于160℃水热反应18h后,干燥,得到前驱体;(2)将前驱体置于管式炉中,在氩气保护下,从室温以5℃/min的升温速率升至700℃,并在该温度下热处理4h得到产物;(3)将10mmol醋酸锌、10mmol六次甲基四胺、0.2mmol硝酸钐和0.2mmol硝酸铜溶于50ml去离子水中的搅拌得到混合溶液;将步骤(2)所得到的5.51g产物添加到上述混合物溶液中,然后将得到的混合溶液转移到反应釜中于130℃下保温5h,将得到的沉淀物离心洗净并于110℃干燥16h,然后于450℃煅烧3h,获得钐和铜共掺杂的氧化锌/石墨烯复合材料;
所述改性玄武岩鳞片/氮化碳复合材料的制备方法包括以下步骤:按氨丙基三乙氧基硅烷的质量分数为3wt%,将氨丙基三乙氧基硅烷加入到乙醇中,得到氨丙基三乙氧基硅烷的乙醇溶液;将15g玄武岩鳞片和15g氮化碳加入到100g氨丙基三乙氧基硅烷的乙醇溶液中,得到混合液;然后在500w超声波清洗机中超声分散45min;过滤、洗涤、于90℃干燥13h得到改性玄武岩鳞片/氮化碳复合材料;所述防腐涂料的制备方法包括以下步骤,先将环氧树脂、改性玄武岩鳞片/氮化碳复合材料、钐和铜共掺杂的氧化锌/石墨烯复合材料与水放入高速搅拌机中混合,搅拌速率为3500r/min,搅拌30min,然后将纳米二氧化钛和助剂添加到上述混合物中继续搅拌30min,得到防腐涂料。
32.对比例2一种应用于船舶的防腐涂料,所述防腐涂料的原料按重量份计包括:环氧树脂50份、改性玄武岩鳞片/氮化碳复合材料10份、钐掺杂的氧化锌/石墨烯复合材料6份、纳米二氧化钛14份、助剂4份与水25份;所述钐掺杂的氧化锌/石墨烯复合材料的制备方法包括以下步骤:(1)首先将9mg氧化石墨烯分散于10ml去离子水中,得到氧化石墨烯分散液,然后加入20ml浓度为0.45mg/ml的硫代乙酰胺的乙醇溶液,搅拌均匀后装入水热釜中进行水热反应,于160℃水热反应18h后,干燥,得到前驱体;(2)将前驱体置于管式炉中,在氩气保护下,从室温以5℃/min的升温速率升至700℃,并在该温度下热处理4h得到产物;(3)将10mmol醋酸锌、10mmol六次甲基四胺和0.4mmol硝酸钐溶于50ml去离子水中的搅拌得到混合溶液;将步骤(2)所得到的5.51g产物添加到上述混合物溶液中,然后将得到的混合溶液转移到反应釜中于130℃下保温5h,将得到的沉淀物离心洗净并于110℃干燥16h,然后于450℃煅烧3h,获得钐掺杂的氧化锌/石墨烯复合材料;所述改性玄武岩鳞片/氮化碳复合材料的制备方法包括以下步骤:按氨丙基三乙氧基硅烷的质量分数为3wt%,将氨丙基三乙氧基硅烷加入到乙醇中,得到氨丙基三乙氧基硅烷的乙醇溶液;将15g玄武岩鳞片和15g氮化碳加入到100g氨丙基三乙氧基硅烷的乙醇溶液中,得到混合液;然后在500w超声波清洗机中超声分散45min;过滤、洗涤、于90℃干燥13h得到改性玄武岩鳞片/氮化碳复合材料;所述防腐涂料的制备方法包括以下步骤,先将环氧树脂、改性玄武岩鳞片/氮化碳复合材料、钐掺杂的氧化锌/石墨烯复合材料与水放入高速搅拌机中混合,搅拌速率为3500r/min,搅拌30min,然后将纳米二氧化钛和助剂添加到上述混合物中继续搅拌30min,得到防腐涂料。
33.对比例3一种应用于船舶的防腐涂料,所述防腐涂料的原料按重量份计包括:环氧树脂50份、改性玄武岩鳞片/氮化碳复合材料10份、铜掺杂的氧化锌/石墨烯复合材料6份、纳米二氧化钛14份、助剂4份与水25份;所述铜掺杂的氧化锌/石墨烯复合材料的制备方法包括以下步骤:(1)首先将9mg氧化石墨烯分散于10ml去离子水中,得到氧化石墨烯分散液,然后加入20ml浓度为0.45mg/ml的硫代乙酰胺的乙醇溶液,搅拌均匀后装入水热釜中进行水热
反应,于160℃水热反应18h后,干燥,得到前驱体;(2)将前驱体置于管式炉中,在氩气保护下,从室温以5℃/min的升温速率升至700℃,并在该温度下热处理4h得到产物;(3)将10mmol醋酸锌、10mmol六次甲基四胺和0.4mmol硝酸铜溶于50ml去离子水中的搅拌得到混合溶液;将步骤(2)所得到的5.51g产物添加到上述混合物溶液中,然后将得到的混合溶液转移到反应釜中于130℃下保温5h,将得到的沉淀物离心洗净并于110℃干燥16h,然后于450℃煅烧3h,获得铜掺杂的氧化锌/石墨烯复合材料;所述改性玄武岩鳞片/氮化碳复合材料的制备方法包括以下步骤:按氨丙基三乙氧基硅烷的质量分数为3wt%,将氨丙基三乙氧基硅烷加入到乙醇中,得到氨丙基三乙氧基硅烷的乙醇溶液;将15g玄武岩鳞片和15g氮化碳加入到100g氨丙基三乙氧基硅烷的乙醇溶液中,得到混合液;然后在500w超声波清洗机中超声分散45min;过滤、洗涤、于90℃干燥13h得到改性玄武岩鳞片/氮化碳复合材料;所述防腐涂料的制备方法包括以下步骤,先将环氧树脂、改性玄武岩鳞片/氮化碳复合材料、铜掺杂的氧化锌/石墨烯复合材料与水放入高速搅拌机中混合,搅拌速率为3500r/min,搅拌30min,然后将纳米二氧化钛和助剂添加到上述混合物中继续搅拌30min,得到防腐涂料。
34.对比例4一种应用于船舶的防腐涂料,所述防腐涂料的原料按重量份计包括:环氧树脂50份、改性玄武岩鳞片/氮化碳复合材料16份、纳米二氧化钛14份、助剂4份与水25份;所述改性玄武岩鳞片/氮化碳复合材料的制备方法包括以下步骤:按氨丙基三乙氧基硅烷的质量分数为3wt%,将氨丙基三乙氧基硅烷加入到乙醇中,得到氨丙基三乙氧基硅烷的乙醇溶液;将15g玄武岩鳞片和15g氮化碳加入到100g氨丙基三乙氧基硅烷的乙醇溶液中,得到混合液;然后在500w超声波清洗机中超声分散45min;过滤、洗涤、于90℃干燥13h得到改性玄武岩鳞片/氮化碳复合材料;所述防腐涂料的制备方法包括以下步骤,先将环氧树脂、改性玄武岩鳞片/氮化碳复合材料与水放入高速搅拌机中混合,搅拌速率为3500r/min,搅拌30min,然后将纳米二氧化钛和助剂添加到上述混合物中继续搅拌30min,得到防腐涂料。
35.对比例5一种应用于船舶的防腐涂料,所述防腐涂料的原料按重量份计包括:环氧树脂50份、钐和铜共掺杂的氧化锌/石墨烯复合材料16份、纳米二氧化钛14份、助剂4份与水25份;所述钐和铜共掺杂的氧化锌/石墨烯复合材料的制备方法包括以下步骤:(1)首先将9mg氧化石墨烯分散于10ml去离子水中,得到氧化石墨烯分散液,然后加入20ml浓度为0.45mg/ml的硫代乙酰胺的乙醇溶液,搅拌均匀后装入水热釜中进行水热反应,于160℃水热反应18h后,干燥,得到前驱体;(2)将前驱体置于管式炉中,在氩气保护下,从室温以5℃/min的升温速率升至700℃,并在该温度下热处理4h得到产物;(3)将10mmol醋酸锌、10mmol六次甲基四胺、0.2mmol硝酸钐和0.2mmol硝酸铜溶于50ml去离子水中的搅拌得到混合溶液;将步骤(2)所得到的5.51g产物添加到上述混合物溶液中,然后将得到的混合溶液转移到反应釜中于130℃下保温5h,将得到的沉淀物离心洗净
并于110℃干燥16h,然后于450℃煅烧3h,获得钐和铜共掺杂的氧化锌/石墨烯复合材料;所述防腐涂料的制备方法包括以下步骤,先将环氧树脂、钐和铜共掺杂的氧化锌/石墨烯复合材料与水放入高速搅拌机中混合,搅拌速率为3500r/min,搅拌30min,然后将纳米二氧化钛和助剂添加到上述混合物中继续搅拌30min,得到防腐涂料。
36.对比例6一种应用于船舶的防腐涂料,所述防腐涂料的原料按重量份计包括:环氧树脂50份、玄武岩鳞片5份、氮化碳5份、钐和铜共掺杂的氧化锌/石墨烯复合材料6份、纳米二氧化钛14份、助剂4份与水25份;所述钐和铜共掺杂的氧化锌/石墨烯复合材料的制备方法包括以下步骤:(1)首先将9mg氧化石墨烯分散于10ml去离子水中,得到氧化石墨烯分散液,然后加入20ml浓度为0.45mg/ml的硫代乙酰胺的乙醇溶液,搅拌均匀后装入水热釜中进行水热反应,于160℃水热反应18h后,干燥,得到前驱体;(2)将前驱体置于管式炉中,在氩气保护下,从室温以5℃/min的升温速率升至700℃,并在该温度下热处理4h得到产物;(3)将10mmol醋酸锌、10mmol六次甲基四胺、0.2mmol硝酸钐和0.2mmol硝酸铜溶于50ml去离子水中的搅拌得到混合溶液;将步骤(2)所得到的5.51g产物添加到上述混合物溶液中,然后将得到的混合溶液转移到反应釜中于130℃下保温5h,将得到的沉淀物离心洗净并于110℃干燥16h,然后于450℃煅烧3h,获得钐和铜共掺杂的氧化锌/石墨烯复合材料;所述防腐涂料的制备方法包括以下步骤,先将环氧树脂、玄武岩鳞片、氮化碳、钐和铜共掺杂的氧化锌/石墨烯复合材料与水放入高速搅拌机中混合,搅拌速率为3500r/min,搅拌30min,然后将纳米二氧化钛和助剂添加到上述混合物中继续搅拌30min,得到防腐涂料。
37.对比例7一种应用于船舶的防腐涂料,所述防腐涂料的原料按重量份计包括:环氧树脂50份、改性玄武岩鳞片10份、钐和铜共掺杂的氧化锌/石墨烯复合材料6份、纳米二氧化钛14份、助剂4份与水25份;所述钐和铜共掺杂的氧化锌/石墨烯复合材料的制备方法包括以下步骤:(1)首先将9mg氧化石墨烯分散于10ml去离子水中,得到氧化石墨烯分散液,然后加入20ml浓度为0.45mg/ml的硫代乙酰胺的乙醇溶液,搅拌均匀后装入水热釜中进行水热反应,于160℃水热反应18h后,干燥,得到前驱体;(2)将前驱体置于管式炉中,在氩气保护下,从室温以5℃/min的升温速率升至700℃,并在该温度下热处理4h得到产物;(3)将10mmol醋酸锌、10mmol六次甲基四胺、0.2mmol硝酸钐和0.2mmol硝酸铜溶于50ml去离子水中的搅拌得到混合溶液;将步骤(2)所得到的5.51g产物添加到上述混合物溶液中,然后将得到的混合溶液转移到反应釜中于130℃下保温5h,将得到的沉淀物离心洗净并于110℃干燥16h,然后于450℃煅烧3h,获得钐和铜共掺杂的氧化锌/石墨烯复合材料;所述改性玄武岩鳞片的制备方法包括以下步骤:按氨丙基三乙氧基硅烷的质量分数为3wt%,将氨丙基三乙氧基硅烷加入到乙醇中,得到氨丙基三乙氧基硅烷的乙醇溶液;将30g玄武岩鳞片加入到100g氨丙基三乙氧基硅
烷的乙醇溶液中,得到混合液;然后在500w超声波清洗机中超声分散45min;过滤、洗涤、于90℃干燥13h得到改性玄武岩鳞片;所述防腐涂料的制备方法包括以下步骤,先将环氧树脂、改性玄武岩鳞片、钐和铜共掺杂的氧化锌/石墨烯复合材料与水放入高速搅拌机中混合,搅拌速率为3500r/min,搅拌30min,然后将纳米二氧化钛和助剂添加到上述混合物中继续搅拌30min,得到防腐涂料。
38.对比例8一种应用于船舶的防腐涂料,所述防腐涂料的原料按重量份计包括:环氧树脂50份、改性氮化碳10份、钐和铜共掺杂的氧化锌/石墨烯复合材料6份、纳米二氧化钛14份、助剂4份与水25份;所述钐和铜共掺杂的氧化锌/石墨烯复合材料的制备方法包括以下步骤:(1)首先将9mg氧化石墨烯分散于10ml去离子水中,得到氧化石墨烯分散液,然后加入20ml浓度为0.45mg/ml的硫代乙酰胺的乙醇溶液,搅拌均匀后装入水热釜中进行水热反应,于160℃水热反应18h后,干燥,得到前驱体;(2)将前驱体置于管式炉中,在氩气保护下,从室温以5℃/min的升温速率升至700℃,并在该温度下热处理4h得到产物;(3)将10mmol醋酸锌、10mmol六次甲基四胺、0.2mmol硝酸钐和0.2mmol硝酸铜溶于50ml去离子水中的搅拌得到混合溶液;将步骤(2)所得到的5.51g产物添加到上述混合物溶液中,然后将得到的混合溶液转移到反应釜中于130℃下保温5h,将得到的沉淀物离心洗净并于110℃干燥16h,然后于450℃煅烧3h,获得钐和铜共掺杂的氧化锌/石墨烯复合材料;所述改性氮化碳的制备方法包括以下步骤:按氨丙基三乙氧基硅烷的质量分数为3wt%,将氨丙基三乙氧基硅烷加入到乙醇中,得到氨丙基三乙氧基硅烷的乙醇溶液;将30g氮化碳加入到100g氨丙基三乙氧基硅烷的乙醇溶液中,得到混合液;然后在500w超声波清洗机中超声分散45min;过滤、洗涤、于90℃干燥13h得到改性玄武岩鳞片/氮化碳复合材料;所述防腐涂料的制备方法包括以下步骤,先将环氧树脂、改性氮化碳、钐和铜共掺杂的氧化锌/石墨烯复合材料与水放入高速搅拌机中混合,搅拌速率为3500r/min,搅拌30min,然后将纳米二氧化钛和助剂添加到上述混合物中继续搅拌30min,得到防腐涂料。
39.对比例9一种应用于船舶的防腐涂料,所述防腐涂料的原料按重量份计包括:环氧树脂50份、改性硅藻土10份、钐和铜共掺杂的氧化锌/石墨烯复合材料6份、纳米二氧化钛14份、助剂4份与水25份;所述钐和铜共掺杂的氧化锌/石墨烯复合材料的制备方法包括以下步骤:(1)首先将9mg氧化石墨烯分散于10ml去离子水中,得到氧化石墨烯分散液,然后加入20ml浓度为0.45mg/ml的硫代乙酰胺的乙醇溶液,搅拌均匀后装入水热釜中进行水热反应,于160℃水热反应18h后,干燥,得到前驱体;(2)将前驱体置于管式炉中,在氩气保护下,从室温以5℃/min的升温速率升至700℃,并在该温度下热处理4h得到产物;(3)将10mmol醋酸锌、10mmol六次甲基四胺、0.2mmol硝酸钐和0.2mmol硝酸铜溶于50ml去离子水中的搅拌得到混合溶液;将步骤(2)所得到的5.51g产物添加到上述混合物溶
液中,然后将得到的混合溶液转移到反应釜中于130℃下保温5h,将得到的沉淀物离心洗净并于110℃干燥16h,然后于450℃煅烧3h,获得钐和铜共掺杂的氧化锌/石墨烯复合材料;所述改性硅藻土的制备方法包括以下步骤:按氨丙基三乙氧基硅烷的质量分数为3wt%,将氨丙基三乙氧基硅烷加入到乙醇中,得到硅烷偶联剂乙醇溶液;将30g硅藻土加入到100g氨丙基三乙氧基硅烷的乙醇溶液中,得到混合液;然后在500w超声波清洗机中超声分散45min;过滤、洗涤、于90℃干燥13h得到改性硅藻土;所述防腐涂料的制备方法包括以下步骤,先将环氧树脂、改性硅藻土、钐和铜共掺杂的氧化锌/石墨烯复合材料与水放入高速搅拌机中混合,搅拌速率为3500r/min,搅拌30min,然后将纳米二氧化钛和助剂添加到上述混合物中继续搅拌30min,得到防腐涂料。
40.根据gb1720、gb1732测试实施例1-3与对比例4-9的涂料的附着力及耐冲击力,结果见附图1。
41.由附图1可以看出,通过实施例1与对比例4-9的对比,可以看出本发明的涂料具有优异的附着力和耐冲击性。
42.根据国标gb/t 9274-88和gb/t 1771-91测试实施例1-3和对比例1-9制得的涂料的防腐性能,检测结果见附图2。
43.由附图2可以看出,通过实施例1与对比例1-9的对比,可以看出本发明的涂料具有优异的耐腐蚀性。
44.杀菌测试,将这实施例1-3的涂料与对比例1-3的涂料分别涂覆于同个样品的不同位置,取0.2ml 0.3g/ml的大肠杆菌悬液滴在经消毒的已涂饰样品的表面(涂料干膜要预先烘烤去除voc的干扰),用聚乙烯薄膜覆于其上,在温度为37℃,且相对湿度90%的恒温恒湿培养箱内培养24h,然后,用无菌水将菌液洗下,稀释成适当的浓度梯度,取0.1ml均匀涂布在无菌琼脂培养基上,移至培养箱内于37℃培养24h,观察结果如附图3所示。
45.由附图3可以看出,通过实施例1-3与对比例1-3的对比,可以看出,本技术的涂料具有优异的抗菌性能。
46.上述实施例为本发明较佳的实施方式,但本发明的实施方式并不受上述实施例的限制,其他的任何未背离本发明的精神实质与原理下所作的改变、修饰、替代、组合、简化,均应为等效的置换方式,都包含在本发明的保护范围之内。