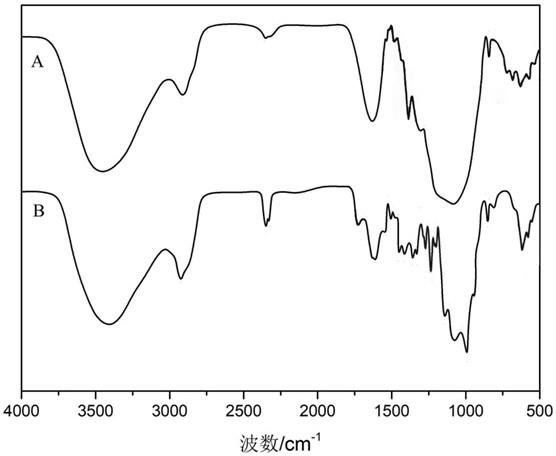
1.本发明属于太阳能电池技术领域,具体涉及一种太阳能电池硅片的制绒工艺。
背景技术:2.随着化石燃料的大量燃烧,环境污染日益严重,清洁无污染的能源越来越受到世界各国的关注。太阳能电池作为一种新型清洁无污染的能源,应用越来越广泛。太阳能电池是一种将太阳能转换成电能的半导体器件,在光照条件下太阳能电池内部会产生光生电流,通过电极将电能输出。太阳能电池可由多种半导体制造,常用的一种半导体材料是结晶硅,但太阳能电池硅片存在表面反射率较高的问题。为解决上述问题,在太阳能电池硅片表面制绒是降低太阳能电池成本、提高光电转化效率的有效途径之一。
3.制绒是用化学或物理方法去除硅片表面损伤层,并形成减反射的绒面结构的过程,常规制绒工艺一般为酸制绒、碱制绒。目前多晶硅太阳能电池工业化生产中,普遍采用酸溶液体系制备多晶绒面,一般采用氢氟酸和硝酸的混和溶液对硅片表面进行腐蚀,利用多晶硅在氢氟酸和硝酸溶液中的各向同性腐蚀,在硅片不同晶粒表面形成相似的凹坑状绒面,但这种酸溶液的制绒效果并不是十分理想,存在绒面尺寸较大且均匀性不佳、不同晶粒之间色差比较明显、宏观形貌如黑线状的深腐蚀坑、表面反射率较高、制绒稳定性不好等问题。现有技术已证明,在制绒液中加入添加剂,有助于解决上述问题,如专利cn103409808a公开了一种多晶硅片制绒添加剂及其使用方法,其是将含有柠檬酸三胺、聚乙烯吡咯烷酮、聚乙烯醇、柠檬酸的混合水溶液与酸溶液混合制得制绒液,利用上述制绒液对多晶硅片进行表面制绒,可以得到均匀性良好的绒面,降低反射率。
4.虽然目前对多晶硅酸溶液制绒的研究已经取得了一定的进展,但仍有需改进之处,因此,仍有必要提出一种新的太阳能电池硅片的制绒工艺。
技术实现要素:5.为解决现有技术存在的问题,本发明提供了一种制绒液用于刻蚀太阳能电池硅片,所述制绒液可用于多晶硅片表面制绒,不仅能得到均匀性好的微结构绒面,有效降低多晶硅太阳能电池对太阳光的反射率,光电转换效率提升,且硅片质量损失少。
6.本发明采取的技术方案如下:一种制绒液的制备方法,所述方法包括下述步骤:1)依次将木聚糖酯化衍生物、柠檬酸三钠、乙二醇单丁醚加入到去离子水中搅拌均匀得第一溶液;2)将氢氟酸、硝酸加入到去离子水中搅拌均匀得第二溶液;3)第一溶液与第二溶液按照0.5~3:100的质量比混合,得到制绒液。
7.本发明提供上述制绒液,是在传统的制绒酸溶液即氢氟酸/硝酸混合溶液中,添加木聚糖酯化衍生物、柠檬酸三钠、乙二醇单丁醚所得,该制绒液可用于多晶硅片表面制绒,其刻蚀速率高,可迅速在硅片表面形成均匀的绒面,减少硅片的损失,从而降低硅片表面的
反射率,提高电池转化效率。
8.进一步地,所述第一溶液中,各组分的质量百分含量为:木聚糖酯化衍生物1~2%、柠檬酸三钠0.5~1%、乙二醇单丁醚0.5~2%,去离子水余量。
9.进一步地,所述第二溶液中,各组分的质量百分含量为:氢氟酸5~10%、硝酸18~30%,去离子水余量。
10.进一步地,所述木聚糖酯化衍生物是羧苯甲酰磺胺噻唑改性木聚糖。
11.进一步地,所述木聚糖酯化衍生物的取代度是0.3~0.5。
12.进一步地,所述木聚糖酯化衍生物具体是以二甲基甲酰胺为反应溶剂,阿拉伯木聚糖与羧苯甲酰磺胺噻唑在催化剂的催化作用下发生酯化反应制得。
13.进一步地,所述木聚糖酯化衍生物的制备方法具体包括下述步骤:将阿拉伯木聚糖加入到二甲基甲酰胺中,加入催化剂,60~80℃下搅拌0.5~2h得混合溶液;将羧苯甲酰磺胺噻唑溶于二甲基甲酰胺中,然后将其缓慢滴加到前述混合溶液中,70~80℃下搅拌反应3~8h,反应完后,依次用无水乙醇、丙酮、去离子水洗涤,抽滤,干燥得到木聚糖酯化衍生物。
14.更进一步地,所述阿拉伯木聚糖与羧苯甲酰磺胺噻唑的质量比是1:6~8。
15.更进一步地,所述催化剂为氯化锂,催化剂的添加量是阿拉伯木聚糖质量的10
‑
30%。
16.阿拉伯木聚糖是一种天然半纤维素多糖,其分子中含有大量的活性羟基,本发明选用平均分子量为25~50kda的阿拉伯木聚糖,利用羧苯甲酰磺胺噻唑对其进行酯化改性,制得取代度为0.3~0.5的木聚糖酯化衍生物,木聚糖经改性后可以破坏其分子间存在的强氢键作用,减弱木聚糖的团聚问题,将其添加到制绒液中对太阳能电池硅片进行刻蚀制绒,可缩短制绒时间、加快制绒速率,得到均匀性好的微结构绒面,提高制绒效果,从而有效降低多晶硅太阳能电池对太阳光的反射率,反射率降至6%以下,光电转换效率提升,这可能是因为木聚糖酯化衍生物的添加,能够降低制绒液的表面张力,使得制绒液能很好的浸润硅片表面,并使刻蚀制绒过程中产生的气泡迅速脱离单晶硅片表面,加快制绒反应的进行,并且阿拉伯木聚糖经改性后,其致密结构得到破坏,并引入了支链结构,增加了对分散体系中重金属离子等的螯合能力,减少重金属离子对制绒效果的影响,制绒效果得到进一步提升;此外,在获得相同反射率的情况下,阿拉伯木聚糖的存在还能减少硅片质量的损失。
17.前述方法制备得到的制绒液在太阳能电池硅片制绒中的应用。
18.本发明还提供了一种太阳能电池硅片的制绒工艺,所述工艺包括下述步骤:s1:表面预处理:用预处理液对太阳能电池硅片进行预处理;s2:制绒:应用前述方法所得制绒液对预清洗后的太阳能电池硅片进行刻蚀制绒;s3:表面清洗:利用碱溶液对制绒后的太阳能电池硅片进行清洗。
19.进一步地,所述步骤s1中,预处理液中各组分的质量百分含量为:表面活性剂15~25%、乙二醇5~15%、氟化氢2~15%、次氯酸钠0.1~0.5%,余量为去离子水;上述各组分在常温下混合,超声处理10~30min得到预处理液。
20.进一步地,所述步骤s1中,预处理温度为70~90℃,时间为30~60min,并利用超声波辅助预处理,超声波频率为20~30khz,功率密度为0.3~0.5w/cm2。
21.进一步地,所述步骤s2中,制绒温度为5~20℃,制绒时间为20~100s。
22.进一步地,所述步骤s3中,碱溶液中各组分的质量百分含量为:氢氧化钾2~4%、碳酸钠0.5~2%、次氯酸钠0.01~0.03%,余量为去离子水;上述各组分在常温下混合搅拌均匀,得到碱溶液。
23.进一步地,所述步骤s3中,碱清洗温度为30~40℃,碱清洗时间为10~30s。
24.本发明通过上述方法,首先利用预处理液对太阳能电池硅片进行预处理,所述预处理液具有较好的去污能力,能够对硅片表面进行有效的清洗,减少硅片表面的重金属等杂质对后续制绒效果的影响;接着利用自制的制绒液对硅片表面进行刻蚀制绒,制绒速度快,可在硅片表面形成均匀性好的微结构绒面,从而有效降低反射率,提升光电转换效率;最后利用碱溶液对制绒后的硅片进行清洗,清除多余的制绒液和制绒过程中形成的多孔硅,减少对太阳能电池的光电转换效率的影响。
25.与现有技术相比,本发明具有以下有益效果:本发明首先用预处理液对太阳能电池硅片进行预处理,减少硅片表面的重金属等杂质对后续制绒效果的影响,然后利用自制的制绒液对太阳能电池硅片进行刻蚀制绒,制绒液中添加木聚糖酯化衍生物,可缩短制绒时间、加快制绒速率,得到均匀性好的微结构绒面,提高制绒效果,从而有效降低多晶硅太阳能电池对太阳光的反射率,反射率降至6%以下,光电转换效率提升;最后利用碱溶液对制绒后的硅片进行清洗,去除表面的多孔硅和多余制绒液。此外,本发明的工艺简单易操作,与现行工艺兼容,重复性好。
附图说明
26.图1是实施例1中木聚糖酯化衍生物的ftir图;图中a代表未改性的阿阿拉伯木聚糖,b代表木聚糖酯化衍生物;图2是木聚糖酯化衍生物的取代度测试结果示意图;图3是太阳能电池硅片的反射率测试结果示意图;图4是太阳能电池的转化效率测试结果示意图;图5是太阳能电池硅片的质量损失率测试结果示意图。
具体实施方式
27.下面结合实施例,对本发明的具体实施方式作进一步描述。以下实施例仅用于更加清楚地说明本发明的技术方案,而不能以此来限制本发明的保护范围。
28.在硅片制绒后,表面会残留制绒液,且制绒过程中会在绒面表面形成一层多孔硅,这层多孔硅会对后续工艺造成危害,严重影响电池的光电转效率,现有技术多为利用氢氧化钠或氢氧化钾溶液进行清洗,不仅容易清洗不彻底,且清洗时间久,容易造成硅片表面抛光,电池性能下降。在本发明中,为提高清洗效果,进一步提高电池的光电转换效率,碱溶液中还添加了0.05~0.1%的苯氧乙醇、0.02~0.035%的四异丙基焦磷酸亚胺,也即是所述碱溶液具体包含下述组分:氢氧化钾2~4%、碳酸钠0.5~2%、次氯酸钠0.01~0.03%、苯氧乙醇0.05~0.1%、四异丙基焦磷酸亚胺0.02~0.035%,余量为去离子水;用该碱溶液清洗,条件温和,清洗效果好,既能清洗掉硅片制绒后表面残留的制绒液,也可彻底去除酸液制绒所产生的多孔硅和尖锐的微结构,减少硅片表面的复合中心,提升短路电流和开压,达到提高太阳能电池光电转换效率的效果。
29.实施例1:本实施例提供了一种太阳能电池硅片的制绒工艺,所述工艺包括下述步骤:s1:表面预处理:将太阳能电池硅片浸于预处理液中,在80℃下超声处理40min,超声波频率为20khz,功率密度为0.4w/cm2,所述预处理液由20重量份十二醇聚环氧乙烷醚、10重量份乙二醇、8重量份氟化氢、8重量份硝酸、0.4重量份次氯酸钠加入到53.6重量份去离子水中,超声处理20min得到预处理液,超声波频率为20khz,功率密度为0.3w/cm2;s2:制绒:将1.6重量份木聚糖酯化衍生物、0.8重量份柠檬酸三钠、1重量份乙二醇单丁醚加入到96.6重量份去离子水中,300r/min下搅拌均匀得到第一溶液;将8重量份氢氟酸、25重量份硝酸加入到67重量份去离子水中,200r/min下搅拌均匀得第二溶液;第一溶液与第二溶液按照1:100的质量比混合,得到制绒液;将太阳能电池硅片浸入制绒液中进行腐蚀制绒,制绒温度为10℃,制绒时间为80s;s3:表面清洗:将制绒后的太阳能电池硅片浸于碱溶液中,35℃下清洗20s,所述碱溶液由3重量份氢氧化钾、1重量份碳酸钠、0.02重量份次氯酸钠加入到95.98重量份去离子水中,室温下搅拌溶解制得。
30.所述木聚糖酯化衍生物经由下述方法制备得到:将1重量份阿拉伯木聚糖(平均分子量为30kda)加入到40重量份的二甲基甲酰胺中,加入0.2重量份氯化锂,75℃下搅拌20min;将5重量份羧苯甲酰磺胺噻唑溶于15重量份的二甲基甲酰胺中,然后将其缓慢滴加到前述混合溶液中,控制滴加时间为1h,滴加完后,75℃下搅拌反应5h,反应完后,依次用无水乙醇、丙酮、去离子水洗涤,抽滤,50℃下干燥得到木聚糖酯化衍生物。
31.实施例2:本实施例提供了另一种太阳能电池硅片的制绒工艺,其步骤与实施例1的不同之处仅在于,木聚糖酯化衍生物制备过程中,羧苯甲酰磺胺噻唑的添加量为6重量份。
32.实施例3:本实施例提供了另一种太阳能电池硅片的制绒工艺,其步骤与实施例1的不同之处仅在于,木聚糖酯化衍生物制备过程中,羧苯甲酰磺胺噻唑的添加量为7重量份。
33.实施例4:本实施例提供了另一种太阳能电池硅片的制绒工艺,其步骤与实施例1的不同之处仅在于,木聚糖酯化衍生物制备过程中,羧苯甲酰磺胺噻唑的添加量为7.4重量份。
34.实施例5:本实施例提供了另一种太阳能电池硅片的制绒工艺,其步骤与实施例1的不同之处仅在于,木聚糖酯化衍生物制备过程中,羧苯甲酰磺胺噻唑的添加量为8重量份。
35.实施例6:本实施例提供了另一种太阳能电池硅片的制绒工艺,其步骤与实施例1的不同之处仅在于,木聚糖酯化衍生物制备过程中,羧苯甲酰磺胺噻唑的添加量为9重量份。
36.实施例7:本实施例提供了另一种太阳能电池硅片的制绒工艺,其步骤与实施例1的不同之处仅在于,利用未改性的阿拉伯木聚糖(平均分子量为30kda)代替木聚糖酯化衍生物。
37.实施例8:
本实施例提供了另一种太阳能电池硅片的制绒工艺,所述步骤与实施例1的不同之处仅在于,制绒液中未添加木聚糖酯化衍生物,所述制绒液经由下述方法制备得到:将0.8重量份柠檬酸三钠、1重量份乙二醇单丁醚加入到98.2重量份去离子水中,300r/min下搅拌均匀得到第一溶液;将8重量份氢氟酸、25重量份硝酸加入到67重量份去离子水中,200r/min下搅拌均匀得第二溶液;第一溶液与第二溶液按照1:100的质量比混合,得到制绒液。
38.实施例9:本实施例提供了另一种太阳能电池硅片的制绒工艺,其步骤与实施例4的不同之处仅在于,步骤s3中,碱溶液由3重量份氢氧化钾、1重量份碳酸钠、0.02重量份次氯酸钠、0.08重量份苯氧乙醇、0.03重量份四异丙基焦磷酸亚胺加入到95.87重量份去离子水中,室温下搅拌溶解制得。
39.实施例10:本实施例提供了另一种太阳能电池硅片的制绒工艺,其步骤与实施例9的不同之处仅在于,碱溶液由3重量份氢氧化钾、1重量份碳酸钠、0.02重量份次氯酸钠、0.03重量份四异丙基焦磷酸亚胺加入到95.95重量份去离子水中,室温下搅拌溶解制得,即碱溶液中未添加苯氧乙醇。
40.实施例11:本实施例提供了另一种太阳能电池硅片的制绒工艺,其步骤与实施例9的不同之处仅在于,碱溶液由3重量份氢氧化钾、1重量份碳酸钠、0.02重量份次氯酸钠、0.08重量份苯氧乙醇加入到95.9重量份去离子水中,室温下搅拌溶解制得,即碱溶液中未添加四异丙基焦磷酸亚胺。
41.试验例1:木聚糖酯化衍生物的红外光谱表征:利用madison公司的nicolet 5700型傅里叶变换红外光谱仪,对实施例1中改性前后的阿拉伯木聚糖进行红外光谱测试,测得结果如图1所示。
42.观察图1可知,曲线a、b分别代表阿拉伯木聚糖、木聚糖酯化衍生物,曲线a和b在3400cm
‑1附近均具有一个较强的特征吸收峰,这是
‑
oh的伸缩振动峰,曲线a的
‑
oh特征峰在3460cm
‑1附近,而曲线b在3425cm
‑1附近,且曲线b中的
‑
oh特征峰强度减弱,并在1720cm
‑1附近出现酯基
‑
o=c
‑
o的特征吸收峰,说明羧苯甲酰磺胺噻唑对木聚糖的酯化改性消耗了木聚糖中的羟基,改变了木聚糖的空间结构,使
‑
oh形成的氢键的形式发生了改变,曲线b在1230cm
‑1和815cm
‑1附近分别出现o=s=o、
‑
so3h的特征伸缩振动吸收峰,这些峰在曲线a中未出现,说明羧苯甲酰磺胺噻唑通过酯化反应已经成功键接到阿拉伯木聚糖上。
43.试验例2:木聚糖酯化衍生物的取代度:采用酸碱滴定法对实施例1~6中的木聚糖酯化衍生物进行羧酸酯化取代度测定,具体方法及步骤如下:准确称取约0.5g样品置入50ml锥形瓶中,加入10ml蒸馏水,摇匀,加入2滴5%的酚酞指示剂,用浓度为0.1mol/l的氢氧化钠标准溶液滴定至浅红色(30s内不会褪色),再用移液管加入2.5ml浓度为0.5mol/l的氢氧化钠标准溶液,摇匀,密封,在室温下震荡皂化4h,之后用浓度为0.5mol/l的盐酸标准溶液滴定至无色,即为滴定终点,羧酸酯化
取代度(ds)的计算式如下:;;式中,w——木聚糖酯化衍生物中酯羰基的质量分数,%;v——滴定木聚糖酯化衍生物消耗的盐酸标准溶液的体积,ml;c
hcl
——盐酸标准溶液浓度,mol/l;m——木聚糖酯化衍生物的质量,g;403和132——羧苯甲酰磺胺噻唑和阿拉伯木聚糖脱水木糖单元的相对分子质量。
44.测得取代度结果如图2所示。
45.观察图2可知,实施例1~6的木聚糖酯化衍生物制备过程中,随着羧苯甲酰磺胺噻唑添加量的增加,与木聚糖的酯化程度越高,酯化取代度越高,其中,实施例2~5中,所得木聚糖酯化衍生物的取代度在0.3~0.5之间,将其添加到制绒液中对太阳能电池硅片制绒,得到的太阳能电池综合性能优异。
46.试验例3:反射率测试:以实施例1~8所得制绒后的太阳能电池硅片为样品,采用d8反射率测试仪测试制绒硅片的平均反射率,波长400~1100nm,测得结果如图3所示。
47.观察图3可知,经本发明优选实施例2~5所述方法制绒后得到的硅片表面反射率低于6%,说明本发明提供的制绒方法,具有有效降低太阳能电池硅片表面反射率的作用;观察实施例1~8中数据可知,实施例7和8所得制绒后硅片的反射率相当,说明未改性的木聚糖对制绒液的制绒效果无明显增益作用,实施例1~6所得制绒后硅片的反射率高于实施例8,说明木聚糖酯化衍生物添加到制绒液中,有助于提升制绒效果,降低硅片表面反射率,还可以看出,仅当以一定量的羧苯甲酰磺胺噻唑对木聚糖进行改性,即木聚糖酯化衍生物的取代度介于0.3~0.5之间时才能赋予制绒液以优异的制绒效果。
48.试验例4:转化效率测试:将实施例1~11所得制绒后的硅片分别进行扩散、刻边、镀膜、印刷和快速烧结,得到太阳能电池1~11,将各太阳能电池放置在1000w/m2的光照强度中,测试电池转化效率。测得结果如图4所示。
49.观察图4可知,经本发明所述制绒方法得到的太阳能电池硅片的转化效率高,转化效率达19%以上,优选实施例4所得太阳能电池硅片的转化效率高达20.2%,相比常规制绒方法获得的硅片的转换效率得到了显著提升,对比实施例1~8中数据可以看出,实施例7和8所得太阳能电池硅片的转化效率低于实施例1~6,说明制绒液中木聚糖酯化衍生物的添加可有效提升制绒效果,观察实施例1~6所得数据还可以看出,木聚糖酯化衍生物制备过程中,羧苯甲酰磺胺噻唑的添加量对制绒效果具有较为明显的影响,随着羧苯甲酰磺胺噻唑
添加量的增加,木聚糖酯化衍生物的取代度升高,当取代度在0.3~0.5范围内时,所得制绒液有利于提升制绒效果,获得均匀性好的绒面,提升转化效率,羧苯甲酰磺胺噻唑添加过少或过量,均不利于硅片表面的制绒;对比实施例9~11中数据可以看出,实施例9所得转化效率高于实施例4,实施例10、11所得转化效率与实施例4相当,说明碱清洗过程中,利用添加苯氧乙醇和四异丙基焦磷酸亚胺的碱溶液对制绒后的硅片进行清洗,可加快清洗速度,提高清洗效果,能有效去除残留的制绒液和制绒所产生的多孔硅和尖锐的微结构,减少硅片表面的复合中心,提升短路电流和开压,达到提高太阳能电池光电转换效率的效果。
50.试验例5:质量损失率测试:以实施例1~8中制绒前后的太阳能电池硅片为样品,分别用天平称其质量,用制绒前后的质量差计算其质量损失率,测得结果如图5所示。
51.观察图5可知,经本发明所述制绒方法对太阳能电池硅片进行刻蚀制绒,可减少硅片的损失,质量损失率最低达0.22%,对比实施例1~8所得质量损失率可以看出,实施例7和8所得质量损失率高于实施例4,说明木聚糖未经改性添加到制绒液中,对加快制绒速率、提高制绒效果无明显增益作用,实施例2~5所得质量损失率低于实施例1和6,说明木聚糖酯化改性过程中,羧苯甲酰磺胺噻唑的添加量对制绒液的制绒效果具有较大的影响,当以一定量的羧苯甲酰磺胺噻唑对木聚糖进行改性后添加到制绒液中,有助于制绒液形成良好的稳定性和分散性能,具有较低的表面张力,使得制绒液能很好的浸润硅片表面,并使刻蚀制绒过程中产生的气泡迅速脱离单晶硅片表面,加快制绒反应的进行,减少制绒过程中多孔硅的形成,降低硅片的质量损失。
52.综上所述,本发明提供了一种太阳能电池硅片的制绒方法,经本发明所述制绒方法对太阳能电池硅片进行制绒,制绒速率快,能减少硅片的损失,制绒效果好,有助于获得均匀性优异的绒面,制绒后的硅片反射率明显降低,低于6%,转化效率得到有效提升,转化效率为19%以上。
53.本发明的操作步骤中的常规操作为本领域技术人员所熟知,在此不进行赘述。
54.以上实施方式仅用于说明本发明,而并非对本发明的限制,本领域的普通技术人员,在不脱离本发明的精神和范围的情况下,还可以做出各种变化和变型。因此,所有等同的技术方案也属于本发明的范畴,本发明的专利保护范围应由权利要求限定。