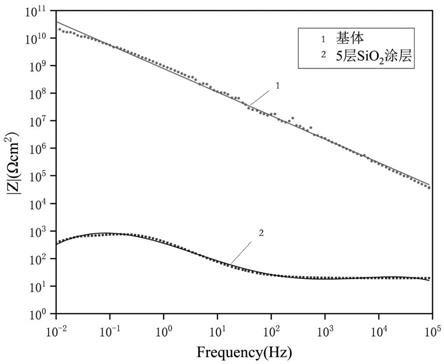
1.本发明涉及一种防腐材料,特别涉及在海洋船舶基板表面镀覆具有耐腐蚀、耐久性的超疏水保护涂层的制备方法。
背景技术:2.海洋是生命的摇篮,是人类可持续发展的重要战略空间,具有潜在的巨大经济利益和战略性的国防地位。然而,严峻的海洋腐蚀问题成为了海洋开发过程中面临的主要威胁之一。由于海水是组成复杂的强腐蚀性电解质溶液,其中含有大量且种类繁多的盐类,又有溶解的氧气,且海水的电导率、含盐量、ph值、温度、溶解物质、海水流速以及海洋中存在的大量海洋生物等都是海水中金属物质腐蚀的影响因素。因此,海洋腐蚀问题十分复杂和严重。目前,涂层保护是腐蚀防护中最重要和常用的手段,已广泛应用于海洋工程结构和船舶的腐蚀防护中。其原理是在活泼金属表面镀上一层不易发生腐蚀的涂层来进行腐蚀防护。醇酸树脂、酚醛树脂、环氧树脂、聚氨酯、乙酸树脂等树脂材料由于表面光洁度高,且其制品柔韧性好、耐腐蚀、耐高低温、抗老化,使用寿命长,被广泛应用于船舶的防腐蚀领域中。但是,树脂材料的自清洁性能并不是十分优异,在船舶行驶期间无法克服雨水、海水等污渍的沾附;此外,虽然树脂涂层与金属基板的粘结力强,但其抗划伤性差。因此,研发具有良好自清洁性以及优异耐腐蚀性、耐久性能的防护涂层,成为了海洋腐蚀亟待解决的问题。
3.目前,树脂涂料被广泛应用在船舶以及海洋工程结构的防腐中,其中环氧类重防腐涂料应用最为广泛。尽管环氧树脂对许多元素具有显著的抗水性,但其亲水表面存在缺陷,抗裂纹扩展能力较弱,这可能导致对水、氧和其他腐蚀元素的阻隔能力显著降低,涂层的自清洁不佳。为了在优异防腐蚀性的基础上提高涂层自清洁性,可以引入一些主链由si-o键组成有机高分子材料,例如聚二甲基硅氧烷等,这种分子结构的有机硅材料具有高疏水性和低表面能,广泛应用于海洋防污领域。除此之外,无机纳米颗粒可以构建较高的表面粗糙度来提高涂层的疏水性,其中二氧化硅纳米颗粒具有高机械强度以及高的化学稳定性,成本较低,被广泛应用。因此在活泼金属表面镀覆具有自清洁、耐腐蚀的超疏水有机-无机复合保护涂层是一种能提供长期解决海洋腐蚀、防止污渍沾附污染的有效方法。发明专利cn106587075a提出一种采用硅烷偶联剂改性得到超疏水二氧化硅粒子以及采用超声雾化的方法制备超疏水涂层。发明专利201110310590.4的一种超疏水丙烯酸树脂涂料中提到,将两种粒径不同的纳米材料混合,加入丙烯酸的混合溶剂中,再加入十七氟三甲氧基乙氧基硅烷制备出了超疏水涂料。发明专利cn109181530a提出将二氧化硅悬浮液与聚二甲基硅氧烷混合形成混合液,然后将混合液料涂覆于基材上,加热固化,采用灼烧的方法对固化后的涂层进行后处理,形成复合超疏水涂层。以上的专利研究都是在纳米颗粒表面修饰疏水性物质,然后与环氧树脂等混合制备涂层。但由于无机纳米颗粒与有机高分子聚合物的相容性较差,导致无机纳米颗粒的团聚,这样制备的涂层在强度和耐磨性上较差,且通过修饰无机纳米颗粒来提高溶解性会耗时以及浪费成本。除此之外,以上专利中用到了含氟硅烷
进行修饰,虽然能有效提高疏水性,但是本身是有毒的,对人体有危害以及对环境也会有所污染,不能满足当今海洋腐蚀防护中环保,且具有优异耐腐蚀、耐久、自清洁的要求。
技术实现要素:4.本发明的目的是提供一种二氧化硅纳米颗粒/有机树脂复合超疏水涂层的制备方法,涂层喷涂在基体上,依据该方法获得的涂层具超疏水性、耐腐蚀、在基体上的附着力好及抗划伤性好。
5.本发明的目的是这样实现的:一种二氧化硅纳米颗粒/有机树脂复合超疏水涂层的制备方法,包括如下步骤:(1)将乙酸乙酯、环氧树脂 、聚二甲基硅氧烷混合均匀;(2)加入环氧树脂固化剂和聚二甲基硅氧烷固化剂,再次混合;(3)将混合好的溶液喷涂于基体表面,形成底层喷涂层,然后进行固化;(4)将乙酸乙酯和二氧化硅纳米颗粒混合,使二氧化硅分散在乙酸乙酯溶剂中;(5)将上述二氧化硅与乙酸乙酯的混合液喷涂在底层表面,形成面层,并待其固化,在基体表面形成二氧化硅纳米颗粒/有机树脂复合超疏水涂层。
6.上述步骤(1)中,乙酸乙酯、环氧树脂、聚二甲基硅氧烷的重量用量比为(10-30):(3-4):1;步骤(1)中环氧树脂与步骤(2)中环氧树脂固化剂的重量比为(3.5-4.5):1;步骤(1)中聚二甲基硅氧烷与步骤(2)聚二甲基硅氧烷固化剂的重量比为(8-12):1;步骤(4)中,乙酸乙酯和二氧化硅纳米颗粒的重量比为:(25-50):1。
7.优选方案是,步骤(1)和步骤(2)中,乙酸乙酯、环氧树脂、聚二甲基硅氧烷的重量用量比为21.6:3.2:1;环氧树脂与环氧树脂固化剂的重量比为4:1;聚二甲基硅氧烷与聚二甲基硅氧烷固化剂的重量比为10:1;步骤(4)中,乙酸乙酯和二氧化硅纳米颗粒的重量比为32.5:1。
8.所述底层喷涂层和面层喷涂层分别通过喷涂2-5次获得。
9.所述基体的材质为玻璃、硅片、q235钢或q345钢。
10.进一步地,所述步骤(3)中在常温下固化8-12min,步骤(5)中于60-80℃下固化8-24h。
11.与现有技术相比,本发明的有益效果在于:本发明将环氧树脂、聚二甲基硅氧烷等有机涂料和无机纳米颗粒依次顺序喷涂在基体上,形成无机/有机复合超疏水涂层既综合了有机涂层易成膜和附着力好的优点,又发挥了无机涂层抗划伤性好的特点。树脂与无机纳米颗粒分开喷涂,使得无机纳米颗粒能更好的嵌入树脂中,且复合涂层不添加改性剂就能得到优异的超疏水性能,节约了改性的时间与成本,依据该方法获得的涂层具超疏水性、耐腐蚀、在基体上的附着力好及抗划伤性好,可用于船舶、海上石油平台的涂装。
附图说明
12.图1为本发明制备超疏水涂层的原理示意图。
13.图2为本发明实例1制备的超疏水涂层的sem图。
14.图3为本发明实例2制备的超疏水涂层的sem图。
15.图4为本发明实例3制备的超疏水涂层的sem图。
16.图5为本发明实例1制备的超疏水涂层的静态接触角图。
17.图6为本发明实例2制备的超疏水涂层的静态接触角图。
18.图7微本发明实例2制备的超疏水涂层经过摩擦后的静态接触角图。
19.图8为本发明实例3制备的超疏水涂层的静态接触角图。
20.图9为本发明实例3中q235钢基体的nyquist图。
21.图10为本发明实例3中制备的超疏水涂层的nyquist图。
22.图11为本发明实例3中q235钢基体和制备的超疏水涂层的bode阻抗图。
23.图中,1-计算机控制系统,2-全自动智能喷涂设备,3-搭建台,4-喷枪,5-钢片,6-玻璃底板。
具体实施方式
24.实施例1本实施例中采用常温喷涂技术在q235钢基体表面喷涂ep+pdms/sio2超疏水复合涂层,基体选用q235钢,底层采用ep+pdms混合,面层采用二氧化硅纳米颗粒,重复喷涂纳米颗粒三次。
25.环氧树脂牌号为m01-a,生产厂家为昆山久力美电子材料有限公司,该环氧树脂包括a液和b液,a液为环氧树脂,b液为环氧树脂固化剂;聚二甲基硅氧烷牌号为sylgard 184,生产厂家为道康宁上海有限公司,聚二甲基硅氧烷包括a液和b液,a液为聚二甲基硅氧烷,b液为聚二甲基硅氧烷固化剂。
26.具体步骤如下:(1)将24ml的乙酸乙酯(ea)、3.2g的环氧树脂(ep)、1g的聚二甲基硅氧烷(pdms)混合,然后在超声清洁器中超声30min,使环氧树脂与聚二甲基硅氧烷混合均匀。
27.(2)按照重量比4:1和10:1的比例依次加入0.8g环氧树脂固化剂和0.1g聚二甲基硅氧烷固化剂,即环氧树脂与环氧树脂固化剂的重量比为4:1;聚二甲基硅氧烷与聚二甲基硅氧烷固化剂的重量比为10:1;混合之后将混合液体置于磁力搅拌中,在室温下搅拌2h。
28.(3)将混合好的溶液置于全自动智能喷涂成膜设备中,在常温下进行喷涂,喷涂结束后,在常温下固化10min,以便二氧化硅纳米颗粒更好的嵌入ep+pdms的底层中,同时可提高涂层与基体的结合力。
29.(4)将12ml的乙酸乙酯(ea)和0.3g的二氧化硅纳米颗粒混合,然后在超声清洁器中超声30min,使二氧化硅更好的分散在乙酸乙酯溶剂中,减少团聚。
30.(5)超声结束后,将上述二氧化硅与乙酸乙酯的混合液体置于全自动智能喷涂成膜设备中,在常温下重复喷涂3次,喷涂结束后,将涂层置于70℃的马弗炉中固化12h,待样品冷却至室温后,取出样品。
31.喷涂装置的工作原理:通过计算机控制系统1发出指令,控制全自动智能喷涂设备2供料,设置在搭建台3上的喷枪4进行喷涂工作,喷涂时,作为基体的钢片5设置在玻璃底板6上。
32.所制备的超疏水复合涂层的表面形貌如图2所示(所用设备型号是geminisem 300场发射扫描电镜系统),从图2可以看出有明显的二氧化硅纳米颗粒凸起,具有粗糙的表面结构,具备了形成超疏水的条件;复合涂层的接触角如图5所示为153
°±2°
,滚动角为3
°±
0.15
°
(所用设备型号是oca40micro接触角测试仪)。
33.实施例2本实施例中采用常温喷涂技术在q235钢基体表面沉积ep+pdms/sio2超疏水复合涂层,基体选用q235钢,底层采用ep+pdms混合,面层采用二氧化硅纳米颗粒,重复喷涂纳米颗粒四次。
34.环氧树脂及聚二甲基硅氧烷牌号、生产厂家与实施例1相同。
35.具体步骤如下:(1)首先制备ep+pdms的耐腐蚀底层,将24ml的乙酸乙酯(ea)、3.2g的环氧树脂(ep)、1g的聚二甲基硅氧烷(pdms)混合,然后在超声清洁器中超声30min,使环氧树脂与聚二甲基硅氧烷混合均匀。
36.(2)超声结束以后,按照重量比4:1和10:1的比例依次加入0.8g环氧树脂固化剂和0.1g聚二甲基硅氧烷固化剂,之后将混合液体置于磁力搅拌中,在室温下搅拌2h。
37.(3)将混合好的溶液置于全自动智能喷涂成膜设备中,在常温下进行喷涂,喷涂结束后,在常温下固化10min,以便二氧化硅纳米颗粒更好的嵌入ep+pdms的底层中,同时也提高涂层与基体的结合力。
38.(4)与此同时,将12ml的乙酸乙酯(ea)和0.3g的二氧化硅纳米颗粒混合,然后在超声清洁器中超声30min,使二氧化硅更好的分散在乙酸乙酯溶剂中,减少团聚。
39.(5)超声结束后,将上述二氧化硅与乙酸乙酯的混合液体置于全自动智能喷涂成膜设备中,在常温下重复喷涂4次,喷涂结束后,将涂层置于70℃的马弗炉中固化12h,提高涂层与基体的结合力,样品冷却至室温后,取出样品。
40.制备的超疏水复合涂层的表面形貌如图3所示(所用设备型号是geminisem 300场发射扫描电镜系统),图3可以看出有明显的二氧化硅纳米颗粒凸起,具有粗糙的表面结构,具备了形成超疏水的条件;复合涂层的接触角如图6所示为148
°±
1.8
°
,滚动角为3
°±
0.13
°
;通过砂纸摩擦法,将100g的砝码与600#砂纸粘连在一起,在涂层上水平滑动,来回摩擦50次,结束后测量接触角来判定涂层的耐久性,复合涂层经过摩擦后的静态接触角如图7为146
°±
1.7
°
,可以看出其接触角在摩擦前后变化不大,说明涂层具有良好的耐久性(接触角测试所用设备型号是oca40micro接触角测试仪)。
41.实施例3本实施例中采用常温喷涂技术在q235钢基体表面沉积ep+pdms/sio2超疏水复合涂层,基体选用q235钢,底层采用ep+pdms混合,面层采用二氧化硅纳米颗粒,重复喷涂纳米颗粒五次。
42.环氧树脂及聚二甲基硅氧烷牌号、生产厂家与实施例1相同。
43.具体步骤如下:(1)首先制备ep+pdms的耐腐蚀底层,将12ml的乙酸乙酯(ea)、3.2g的环氧树脂(ep)、1g的聚二甲基硅氧烷(pdms)混合,然后在超声清洁器中超声30min,使环氧树脂与聚二甲基硅氧烷混合均匀。
44.(2)超声结束以后,按照4:1和10:1的比例依次加入0.8g环氧树脂固化剂和0.1g聚二甲基硅氧烷固化剂,之后将混合液体置于磁力搅拌中,在室温下搅拌2h。
45.(3)将混合好的溶液置于全自动智能喷涂成膜设备中,在常温下进行喷涂,喷涂结
束后,在常温下固化10min,以便二氧化硅纳米颗粒更好的嵌入ep+pdms的底层中,同时也提高涂层与基体的结合力。
46.(4)与此同时,将12ml的乙酸乙酯(ea)和0.3g的二氧化硅纳米颗粒混合,然后在超声清洁器中超声30min,使二氧化硅更好的分散在乙酸乙酯溶剂中,减少团聚。
47.(5)超声结束后,将上述二氧化硅与乙酸乙酯的混合液体置于全自动智能喷涂成膜设备中,在常温下重复喷涂5次,喷涂结束后,将涂层置于70℃的马弗炉中固化12h,提高涂层与基体的结合力,样品冷却至室温后,取出样品。
48.所制备的超疏水复合涂层的表面形貌如图4所示(所用设备型号是geminisem 300场发射扫描电镜系统),图4可以看出有明显的二氧化硅纳米颗粒凸起,具有粗糙的表面结构,具备了形成超疏水的条件;复合涂层的接触角如图8所示为156
°±2°
,滚动角为3
°±
0.15
°
(所用设备型号是oca40micro接触角测试仪);通过电化学工作站测试涂层的阻抗来判定耐腐蚀性(所用设备型号是interface1010e多通道电化学工作站),图9、图10为q235钢基体和制备的超疏水涂层的nyquist图,可以看出,涂层的电容式循环直径远远大于基体,表明了涂层有效提高了基体的防腐性能;图11为中q235钢基体和制备的超疏水涂层的bode阻抗图,可以看出,涂层的低频阻抗幅值远远大于基体,证明了涂层能有效对基体产生保护。
49.对实例1、实例2、实例3进行sem分析,从三个实例中可以看出有明显的二氧化硅纳米颗粒凸起,具有粗糙的表面结构,具备了形成超疏水的条件;通过接触测试仪测试了涂层的接触角,可以看出3个涂层的静态接触角超过了150
°
,或者其附近,具有很好的超疏水性能;通过砂纸摩擦涂层,观察到接触角在摩擦前后变化不大,说明涂层具有良好的耐久性;通过观察q235钢基体和制备的超疏水涂层的nyquist图以及bode阻抗图,可以看出,涂层的电容式循环直径远远大于基体,表明了涂层有效提高了基体的防腐性能,同时涂层的低频阻抗幅值远远大于基体,证明了涂层能有效对基体产生保护。
50.改变基体材料,实践证明基体材料为玻璃、硅片q345钢时,也具有如q235钢相同的特性。
51.总之,步骤(1)中,乙酸乙酯、环氧树脂、聚二甲基硅氧烷的重量用量比可为(10-30):(3-4):1;步骤(1)中环氧树脂与步骤(2)中环氧树脂固化剂的重量比为(3.5-4.5):1;步骤(1)中聚二甲基硅氧烷与步骤(2)聚二甲基硅氧烷固化剂的重量比为(8-12):1;步骤(4)中,乙酸乙酯和二氧化硅纳米颗粒的重量比为:(25-50):1。
52.所述底层喷涂层和面层喷涂层分别通过喷涂2-5次获得。
53.本发明并不局限于上述实施例,在本发明公开的技术方案的基础上,本领域的技术人员根据所公开的技术内容,不需要创造性的劳动就可以对其中的一些技术特征作出一些替换和变形,这些替换和变形均在本发明的保护范围内。