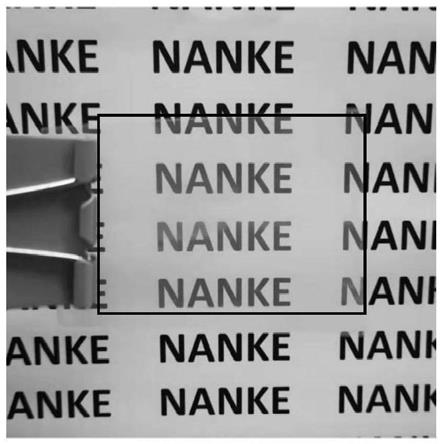
1.本发明属于高分子材料技术领域,涉及一种防雾防霜膜及其制备方法。
背景技术:2.透明材料表面(例如玻璃表面)在有湿度且内外冷热不均的条件下,容易产生一层由水而结成的雾或霜,这会导致透明材料的透明度或反射度变差。例如汽车挡风玻璃在冬天结上一层雾,会对司机造成很大麻烦,要在行驶的情况下不断地擦玻璃,这对交通造成了很大的潜在的危害。此外,航空飞机、车间里的仪器仪表、眼镜等的玻璃表面也容易结雾,这给人们带来了很大的不便。
3.目前,防雾涂层(或防雾膜)一般使用亲水或疏水表面处理,其中疏水处理较难使雾气中极小的液滴摊开,使用效果好的膜表面均使用亲水处理。防霜涂层(或防霜膜),一般使用超疏水表面处理,降低水与表面的附着,从而减少霜的形成。
4.雾与霜的形成,均是由于水汽+温差+平面导致。同一场景,例如冷链仓库agv叉车,从冷库出来进入室温过程中,在摄像头上会由于温差起雾。当使用防雾涂层(或防雾膜)处理后,水汽可摊平成水膜,但当防雾表面温度过低时,水膜会起霜,因此,很多防雾产品(防雾涂料或防雾膜)在寒冷环境下,会比不防雾表面更易起霜。故亟需一款兼具防雾防霜的涂料或膜。
5.cn113004730a公开了一种海藻糖改性聚乙烯醇防雾防霜涂层及其制备方法。涂层包括聚乙烯醇-接枝-海藻糖、低聚乙二醇二甲基丙烯酸酯、安息香二甲醚和去离子水;将上述物质混合均匀涂在透明玻璃片上,用紫外光照射固化,形成亲水性接枝聚合物半互穿网络涂层。所制备的防雾防霜涂层,在防雾过程透光率能保持在89~90%,防霜时间可延长9~31min,将两面涂覆有涂层的玻璃片使用可见分光光度计在400~800nm波段透光率数值。具有良好的防雾防霜性能。该发明制备方法简便,反应温和,在防雾防霜领域具有很大的应用潜力。但是,该发明的防雾防霜涂层的防霜效果及长时间持续防雾效果有待进一步提高。
6.因此,在本领域中,期望开发一种既具有较好的防雾效果又具有较好的防霜效果,尤其具有长时间持续防雾效果的防雾防霜膜。
技术实现要素:7.针对现有技术的不足,本发明的目的在于提供一种防雾防霜膜及其制备方法。
8.为达到此发明目的,本发明采用以下技术方案:
9.第一方面,本发明提供一种防雾防霜膜,所述防雾防霜膜包括底层uv固化防雾层和顶层水性防雾防霜层,所述底层uv固化防雾层的制备原料按照重量份数计,包括如下组分:
[0010][0011]
所述顶层水性防雾防霜层的制备原料按照重量份数计,包括如下组分:
[0012]
水性聚氨酯
ꢀꢀꢀꢀꢀꢀꢀꢀꢀꢀꢀꢀꢀꢀꢀꢀꢀꢀꢀꢀꢀꢀꢀꢀꢀꢀꢀꢀꢀ
70~90份;
[0013]
表面活性剂
ꢀꢀꢀꢀꢀꢀꢀꢀꢀꢀꢀꢀꢀꢀꢀꢀꢀꢀꢀꢀꢀꢀꢀꢀꢀꢀꢀꢀꢀ
5~30份;
[0014]
可降低水冰点的材料
ꢀꢀꢀꢀꢀꢀꢀꢀꢀꢀꢀꢀꢀꢀꢀꢀꢀꢀꢀꢀꢀ
5~10份。
[0015]
在本发明中,所述防雾防霜膜具有双层膜结构,底层uv固化防雾层中含有极高含量的含丙烯酸基团的表面活性剂(含丙烯酸基团的表面活性剂在底层uv固化防雾层中的重量含量可以为20%~80%,高达80%),顶层水性防雾防霜层中含有表面活性剂及可降低水冰点的材料,从而使得制备的防雾防霜膜既具有较好的防雾效果又具有较好的防霜效果。
[0016]
在本发明中,底层利用uv固化防雾涂料,加入过量的含丙烯酸基团的表面活性剂,使其反应成膜不完全,即表面有些黏、表面存在空隙缺陷、过量表面活性剂会渗出。常规的聚氨酯类防雾膜是通过薄膜表面结构孔隙负载防雾材料,但由于薄膜表面具有孔隙,且会在常温下继续缓慢固化,从而影响了薄膜的耐刮擦及耐存放性能,而本发明中,通过在底层上涂布水性防雾涂料,放入烘箱固化,由于底层成膜不完全,水性防雾涂料会更好的结合在底层上,并在水性涂层固化后,由于结构或与底层作用,水性涂料不会进一步固化,从而增强了防雾防霜膜的耐擦性(即耐水性)。
[0017]
常规的防雾涂料配方中,表面活性材料的添加量有限(例如上限20-30%),否则就无法成膜或成膜后表面粘黏或力学强度极差。而在本发明中,底层利用uv固化防雾涂料,通过加入含丙烯酸基团的表面活性剂,可以添加极高含量的活性材料(60~80%以上),且依然可以成膜(只是膜表面会偏粘),并在其上涂覆极薄的水性聚氨酯涂料,成膜性能好。这样使得防雾膜具有极高的表面活性材料含量,在使用过程中渗出流失,从而极大提高防雾防霜膜的防雾耐久性。
[0018]
此外,本发明的顶层使用水性防雾层,使得可以引入可降低水冰点的材料组分,可在极冷环境防雾时,析出表面活性材料(防雾用)的同时,析出部分可降低水冰点的材料,使雾气摊平后的水层冰点降低,从而达到防霜的功能。
[0019]
在本发明中,所述底层uv固化防雾层的制备原料中,uv树脂低聚物的用量可以为10份、13份、15份、18份、20份、23份、25份、28份或30份等。
[0020]
在本发明中,所述底层uv固化防雾层的制备原料中,丙烯酸类单体的用量可以为10份、13份、15份、18份、20份、23份、25份、28份或30份等。
[0021]
在本发明中,所述底层uv固化防雾层的制备原料中,含丙烯酸基团的表面活性剂的用量可以为20份、25份、30份、35份、40份、45份、50份、55份、60份、65份、70份、75份、80份、85份、90份、95份或100份等。
[0022]
在本发明中,所述底层uv固化防雾层的制备原料中,光引发剂的用量可以为3份、4
份、5份、6份、7份、8份、9份或10份等。
[0023]
在本发明中,所述顶层水性防雾防霜层的制备原料中,水性聚氨酯的用量可以为70%、75%、80%、85%或90%等。
[0024]
在本发明中,所述顶层水性防雾防霜层的制备原料中,表面活性剂的用量可以为5%、10%、15%、20%、25%或30%等。
[0025]
在本发明中,所述顶层水性防雾防霜层的制备原料中,可降低水冰点的材料的用量可以为5%、6%、7%、8%、9%或10%等。
[0026]
优选地,所述底层uv固化防雾层的厚度为50~500μm,例如50μm、100μm、150μm、200μm、250μm、300μm、350μm、400μm、450μm或500μm等。
[0027]
优选地,所述顶层水性防雾防霜层的厚度为5~20μm,例如5μm、6μm、7μm、8μm、9μm、10μm、11μm、12μm、13μm、14μm、15μm、16μm、17μm、18μm、19μm或20μm等。
[0028]
作为本发明的优选技术方案,当顶层水性防雾防霜层的厚度大于20μm时,会影响底层表面活性材料的防雾效果。
[0029]
优选地,所述uv树脂低聚物的数均分子量为1000~3000,例如1000、1200、1400、1600、1800、2000、2200、2400、2600、2800或3000等。
[0030]
优选地,所述丙烯酸类单体包括丙烯酸、甲基丙烯酸甲酯、甲基丙烯酸乙酯、甲基丙烯酸丁酯、甲基丙烯酸异丁酯、甲基丙烯酸叔丁酯、丙烯酸甲酯、丙烯酸乙酯、丙烯酸丁酯、丙烯酸异冰片酯、甲基丙烯酸异冰片酯、双环戊二烯丙烯酸酯、三羟甲基环己基丙烯酸酯、羟基丁基丙烯酸酯或苯氧基乙基丙烯酸酯中的任意一种或至少两种的组合。
[0031]
优选地,所述含丙烯酸基团的表面活性剂包括含丙烯酸基团的聚醚、含丙烯酸基团的聚酯、含丙烯酸基团的氟醚、含丙烯酸基团的硅聚醚、含丙烯酸基团的聚二甲基硅氧烷、含丙烯酸基团的烷基酚聚醚或含丙烯酸基团的烷基聚醚中的任意一种或至少两种的组合。
[0032]
优选地,所述光引发剂包括光引发剂1173、光引发剂184、光引发剂tpo、光引发剂tpo-l或光引发剂819中的任意一种或至少两种的组合。
[0033]
优选地,所述底层uv固化防雾层的制备原料中还包括其他助剂。
[0034]
优选地,所述其他助剂的重量份数为3~5份,例如3份、4份或5份等。
[0035]
优选地,所述其他助剂包括消泡剂和/或流平剂。
[0036]
优选地,所述水性聚氨酯包括单组份水性聚氨酯。
[0037]
优选地,所述单组份水性聚氨酯的固含量为30%~40%,例如30%、31%、32%、33%、34%、35%、36%、37%、38%、39%或40%等。
[0038]
优选地,所述单组份水性聚氨酯选自非离子单组份水性聚氨酯、阳离子单组份水性聚氨酯或阴离子单组份水性聚氨酯中的任意一种或至少两种的组合。
[0039]
优选地,所述表面活性剂包括聚醚改性聚二甲基硅氧烷、全氟聚氧乙烯醚、长链脂肪醇聚氧乙烯醚、烷基酚聚氧乙烯醚、脂肪酸聚氧乙烯酯、聚氧乙烯烷基胺或聚氧乙烯烷基醇酰胺中的任意一种或至少两种的组合。
[0040]
优选地,所述可降低水冰点的材料包括甘油、乙二醇、无机盐或盐类表面活性材料中的任意一种或至少两种的组合。上述可降低水冰点的材料既是水溶性的,又可急剧降低水冰点。
[0041]
优选地,所述无机盐包括氯化钙。
[0042]
优选地,所述盐类表面活性材料包括十二烷基苯磺酸钠。
[0043]
第二方面,本发明提供一种第一方面所述的防雾防霜膜的制备方法,所述制备方法包括以下步骤:
[0044]
(1)将配方量的uv树脂低聚物、丙烯酸类单体、含丙烯酸基团的表面活性剂、光引发剂和任选的其他助剂混合,涂布,然后uv固化,得到底层uv固化防雾层;
[0045]
(2)将配方量的水性聚氨酯、表面活性剂和可降低水冰点的材料混合,然后涂布在步骤(1)的底层uv固化防雾层上,加热固化,得到所述防雾防霜膜。
[0046]
优选地,步骤(1)所述涂布为涂布在基材(例如玻璃等)上,在实际使用中,可以涂布在需要防雾的基材上,本发明对涂布所用基材不作限制。
[0047]
优选地,步骤(1)所述uv固化通过led灯或汞灯照射的方式固化。
[0048]
优选地,所述led灯或汞灯的功率为500w~3000w,例如500w、800w、1000w、1300w、1500w、1800w、2000w、2300w、2500w、2800w或3000w等。
[0049]
优选地,所述led灯的波长为365nm。
[0050]
优选地,步骤(1)所述uv固化的时间为5s~30s,例如5s、10s、15s、20s、25s或30s等。
[0051]
优选地,步骤(2)所述加热固化在烘箱中进行。
[0052]
优选地,步骤(2)所述加热固化的温度为60℃~100℃,例如60℃、70℃、80℃、90℃或100℃等,加热热固化的时间为10min~180min,例如10min、30min、60min、90min、120min、150min或180min等。
[0053]
相对于现有技术,本发明具有以下有益效果:
[0054]
(1)在本发明中,所述防雾防霜膜具有双层膜结构,底层uv固化防雾层中含有极高含量的含丙烯酸基团的表面活性剂,顶层水性防雾防霜层中含有表面活性剂及可降低水冰点的材料,从而使得制备的防雾防霜膜既具有较好的防雾效果又具有较好的防霜效果(防雾性和防霜性均为1级)。
[0055]
(2)在本发明中,底层利用uv固化防雾涂料,加入过量的含丙烯酸基团的表面活性剂,使其反应成膜不完全,即表面有些黏、表面存在空隙缺陷、过量表面活性剂会渗出;再在底层上涂布水性防雾涂料,放入烘箱固化,由于底层成膜不完全,水性防雾涂料会更好的结合在底层上,并在水性涂层固化后,由于结构或与底层作用,水性涂料不会进一步固化,从而增强了防雾防霜膜的耐擦性(即耐水性)。
[0056]
(3)常规的防雾涂料配方中,表面活性材料的添加量有限(例如上限20-30%),否则就无法成膜或成膜后表面粘黏或力学强度极差。而在本发明中,底层利用uv固化防雾涂料,通过加入含丙烯酸基团的表面活性剂,可以添加极高含量的活性材料(60-80%以上),且依然可以成膜(只是膜表面会偏粘),并在其上涂覆极薄的水性聚氨酯涂料,成膜性能好。这样使得防雾膜具有极高的表面活性材料含量,在使用过程中渗出流失,从而极大提高防雾防霜膜的防雾耐久性。
[0057]
(4)本发明的顶层使用水性防雾层,使得可以引入可降低水冰点的材料组分,可在极冷环境防雾时,析出表面活性材料(防雾用)的同时,析出部分可降低水冰点的材料,使雾气摊平后的水层冰点降低,从而达到防霜的功能。
附图说明
[0058]
图1为实施例1提供的防雾防霜膜的防雾性测试结果图。
[0059]
图2为对比例5(左侧图)和实施例5(右侧图)提供的防雾防霜膜的防雾性测试结果图。
[0060]
图3为对比例1(左侧图)和对比例2(右侧图)提供的防雾防霜膜的防雾性测试结果图。
[0061]
图4为对比例3(左侧图)和对比例4(右侧图)提供的防雾防霜膜的防雾性测试结果图。
[0062]
图5为进行2次防雾材料渗出测试时实施例5的测试结果图。
[0063]
图6为进行2次防雾材料渗出测试时对比例2(左侧图)和对比例4(右侧图)的测试结果图。
[0064]
图7为进行5次防雾材料渗出测试时对比例1的测试结果图。
[0065]
图8为进行7次防雾材料渗出测试时对比例5的测试结果图。
[0066]
图9为进行10次防雾材料渗出测试时实施例1的测试结果图。
[0067]
图10为进行10次防雾材料渗出测试时对比例3的测试结果图。
[0068]
图11为第1天进行防雾耐久性测试时实施例5的测试结果图。
[0069]
图12为第1天进行防雾耐久性测试时对比例2(左侧图)和对比例4(右侧图)的测试结果图。
[0070]
图13为第3天进行防雾耐久性测试时对比例1的测试结果图。
[0071]
图14为第10天进行防雾耐久性测试时实施例1(左侧图)和对比例5(右侧图)的测试结果图。
[0072]
图15为第10天进行防雾耐久性测试时对比例3的测试结果图。
[0073]
图16-图22分别为实施例1、对比例5、实施例5、对比例1-4的防霜性测试结果图。
具体实施方式
[0074]
下面通过具体实施方式来进一步说明本发明的技术方案。本领域技术人员应该明了,所述实施例仅仅是帮助理解本发明,不应视为对本发明的具体限制。
[0075]
本发明实施例及对比例部分所用原料的来源如下:
[0076]
uv树脂低聚物:无锡维都斯电子材料有限公司;
[0077]
含丙烯酸基团的聚醚:德国毕克;
[0078]
含丙烯酸基团的聚酯:德国毕克;
[0079]
含丙烯酸基团的氟醚:巴斯夫;
[0080]
消泡剂:德国毕克,byk-141;
[0081]
流平剂:德国毕克,byk-333;
[0082]
非离子单组份水性聚氨酯:安徽安大华泰新材料有限公司;
[0083]
阳离子单组份水性聚氨酯:广东一三七化工科技有限公司;
[0084]
阴离子单组份水性聚氨酯:巴斯夫;
[0085]
聚醚改性聚二甲基硅氧烷:德国毕克;
[0086]
全氟聚氧乙烯醚:科慕化学;
[0087]
烷基酚聚氧乙烯醚:深圳市吉田化工有限公司。
[0088]
实施例1
[0089]
在本实施例中提供一种防雾防霜膜,所述防雾防霜膜包括底层uv固化防雾层和顶层水性防雾防霜层,所述底层uv固化防雾层的制备原料按照重量份数计,包括如下组分:
[0090][0091][0092]
所述顶层水性防雾防霜层的制备原料按照重量份数计,包括如下组分:
[0093]
水性聚氨酯
ꢀꢀꢀꢀꢀꢀꢀꢀꢀꢀꢀꢀꢀꢀꢀꢀꢀꢀꢀꢀꢀꢀꢀꢀꢀꢀꢀꢀꢀ
80份;
[0094]
表面活性剂
ꢀꢀꢀꢀꢀꢀꢀꢀꢀꢀꢀꢀꢀꢀꢀꢀꢀꢀꢀꢀꢀꢀꢀꢀꢀꢀꢀꢀꢀ
12份;
[0095]
可降低水冰点的材料
ꢀꢀꢀꢀꢀꢀꢀꢀꢀꢀꢀꢀꢀꢀꢀꢀꢀꢀꢀꢀꢀ
8份。
[0096]
其中,uv树脂低聚物为非离子单组份水性聚氨酯;丙烯酸类单体为丙烯酸;含丙烯酸基团的表面活性剂为含丙烯酸基团的聚醚;光引发剂为光引发剂1173;其他助剂为消泡剂;水性聚氨酯为单组份水性聚氨酯;表面活性剂为聚醚改性聚二甲基硅氧烷;可降低水冰点的材料为甘油。
[0097]
制备方法包括以下步骤:
[0098]
(1)将配方量的uv树脂低聚物、丙烯酸类单体、含丙烯酸基团的表面活性剂、光引发剂和其他助剂混合,涂布在玻璃上,然后通过功率为1000w的led灯(波长:365nm)照射固化20s,得到底层uv固化防雾层;
[0099]
(2)将配方量的水性聚氨酯、表面活性剂和可降低水冰点的材料混合,然后涂布在步骤(1)的底层uv固化防雾层上,放入烘箱,在80℃下加热固化90min,得到所述防雾防霜膜。
[0100]
其中,底层uv固化防雾层的厚度为300μm;顶层水性防雾防霜层的厚度为10μm。
[0101]
实施例2
[0102]
在本实施例中提供一种防雾防霜膜,所述防雾防霜膜包括底层uv固化防雾层和顶层水性防雾防霜层,所述底层uv固化防雾层的制备原料按照重量份数计,包括如下组分:
[0103][0104]
[0105]
所述顶层水性防雾防霜层的制备原料按照重量份数计,包括如下组分:
[0106]
水性聚氨酯
ꢀꢀꢀꢀꢀꢀꢀꢀꢀꢀꢀꢀꢀꢀꢀꢀꢀꢀꢀꢀꢀꢀꢀꢀꢀꢀꢀꢀꢀ
70份;
[0107]
表面活性剂
ꢀꢀꢀꢀꢀꢀꢀꢀꢀꢀꢀꢀꢀꢀꢀꢀꢀꢀꢀꢀꢀꢀꢀꢀꢀꢀꢀꢀꢀ
25份;
[0108]
可降低水冰点的材料
ꢀꢀꢀꢀꢀꢀꢀꢀꢀꢀꢀꢀꢀꢀꢀꢀꢀꢀꢀꢀꢀ
5份。
[0109]
其中,uv树脂低聚物为阳离子单组份水性聚氨酯;丙烯酸类单体为甲基丙烯酸甲酯;含丙烯酸基团的表面活性剂为含丙烯酸基团的聚酯;光引发剂为光引发剂184;其他助剂为流平剂;水性聚氨酯为单组份水性聚氨酯;表面活性剂为全氟聚氧乙烯醚;可降低水冰点的材料为乙二醇。
[0110]
制备方法包括以下步骤:
[0111]
(1)将配方量的uv树脂低聚物、丙烯酸类单体、含丙烯酸基团的表面活性剂、光引发剂和其他助剂混合,涂布在玻璃上,然后通过功率为500w的led灯(波长:365nm)照射固化30s,得到底层uv固化防雾层;
[0112]
(2)将配方量的水性聚氨酯、表面活性剂和可降低水冰点的材料混合,然后涂布在步骤(1)的底层uv固化防雾层上,放入烘箱,在60℃下加热固化180min,得到所述防雾防霜膜。
[0113]
其中,底层uv固化防雾层的厚度为50μm;顶层水性防雾防霜层的厚度为5μm。
[0114]
实施例3
[0115]
在本实施例中提供一种防雾防霜膜,所述防雾防霜膜包括底层uv固化防雾层和顶层水性防雾防霜层,所述底层uv固化防雾层的制备原料按照重量份数计,包括如下组分:
[0116][0117]
所述顶层水性防雾防霜层的制备原料按照重量份数计,包括如下组分:
[0118]
水性聚氨酯
ꢀꢀꢀꢀꢀꢀꢀꢀꢀꢀꢀꢀꢀꢀꢀꢀꢀꢀꢀꢀꢀꢀꢀꢀꢀꢀꢀꢀꢀ
90份;
[0119]
表面活性剂
ꢀꢀꢀꢀꢀꢀꢀꢀꢀꢀꢀꢀꢀꢀꢀꢀꢀꢀꢀꢀꢀꢀꢀꢀꢀꢀꢀꢀꢀ
5份;
[0120]
可降低水冰点的材料
ꢀꢀꢀꢀꢀꢀꢀꢀꢀꢀꢀꢀꢀꢀꢀꢀꢀꢀꢀꢀꢀ
5份。
[0121]
其中,uv树脂低聚物为阴离子单组份水性聚氨酯;丙烯酸类单体为丙烯酸乙酯;含丙烯酸基团的表面活性剂为含丙烯酸基团的氟醚;光引发剂为光引发剂1173;其他助剂为消泡剂;水性聚氨酯为单组份水性聚氨酯;表面活性剂为烷基酚聚氧乙烯醚;可降低水冰点的材料为氯化钙。
[0122]
制备方法包括以下步骤:
[0123]
(1)将配方量的uv树脂低聚物、丙烯酸类单体、含丙烯酸基团的表面活性剂、光引发剂和其他助剂混合,涂布在玻璃上,然后通过功率为3000w的led灯(波长:365nm)照射固化5s,得到底层uv固化防雾层;
[0124]
(2)将配方量的水性聚氨酯、表面活性剂和可降低水冰点的材料混合,然后涂布在步骤(1)的底层uv固化防雾层上,放入烘箱,在100℃下加热固化10min,得到所述防雾防霜膜。
[0125]
其中,底层uv固化防雾层的厚度为500μm;顶层水性防雾防霜层的厚度为20μm。
[0126]
实施例4
[0127]
在本实施例中提供一种防雾防霜膜,所述防雾防霜膜包括底层uv固化防雾层和顶层水性防雾防霜层,所述底层uv固化防雾层的制备原料按照重量份数计,包括如下组分:
[0128][0129]
所述顶层水性防雾防霜层的制备原料按照重量份数计,包括如下组分:
[0130]
水性聚氨酯
ꢀꢀꢀꢀꢀꢀꢀꢀꢀꢀꢀꢀꢀꢀꢀꢀꢀꢀꢀꢀꢀꢀꢀꢀꢀꢀꢀꢀꢀ
75份;
[0131]
表面活性剂
ꢀꢀꢀꢀꢀꢀꢀꢀꢀꢀꢀꢀꢀꢀꢀꢀꢀꢀꢀꢀꢀꢀꢀꢀꢀꢀꢀꢀꢀ
15份;
[0132]
可降低水冰点的材料
ꢀꢀꢀꢀꢀꢀꢀꢀꢀꢀꢀꢀꢀꢀꢀꢀꢀꢀꢀꢀꢀ
10份。
[0133]
其中,uv树脂低聚物为阴离子单组份水性聚氨酯;丙烯酸类单体为丙烯酸;含丙烯酸基团的表面活性剂为含丙烯酸基团的氟醚;光引发剂为光引发剂184;水性聚氨酯为单组份水性聚氨酯;表面活性剂为聚醚改性聚二甲基硅氧烷;可降低水冰点的材料为十二烷基苯磺酸钠。
[0134]
制备方法包括以下步骤:
[0135]
(1)将配方量的uv树脂低聚物、丙烯酸类单体、含丙烯酸基团的表面活性剂、光引发剂混合,涂布在玻璃上,然后通过功率为2000w的汞灯照射固化10s,得到底层uv固化防雾层;
[0136]
(2)将配方量的水性聚氨酯、表面活性剂和可降低水冰点的材料混合,然后涂布在步骤(1)的底层uv固化防雾层上,放入烘箱,在80℃下加热固化90min,得到所述防雾防霜膜。
[0137]
其中,底层uv固化防雾层的厚度为100μm;顶层水性防雾防霜层的厚度为15μm。
[0138]
实施例5
[0139]
本实施例与实施例1不同之处仅在于,顶层水性防雾防霜层的厚度为25μm。
[0140]
对比例1
[0141]
在本对比例中提供一种防雾膜,所述防雾膜仅包括底层uv固化防雾层,所述底层uv固化防雾层的制备原料按照重量份数计,包括如下组分:
[0142][0143]
其中,uv树脂低聚物为非离子单组份水性聚氨酯;丙烯酸类单体为丙烯酸;含丙烯酸基团的表面活性剂为含丙烯酸基团的聚醚;光引发剂为光引发剂1173;其他助剂为消泡剂。
[0144]
制备方法包括以下步骤:
[0145]
将配方量的uv树脂低聚物、丙烯酸类单体、含丙烯酸基团的表面活性剂、光引发剂和其他助剂混合,涂布在玻璃上,然后通过功率为1000w的led灯(波长:365nm)照射固化20s,得到底层uv固化防雾层(厚度为300μm),即,得到所述防雾膜。
[0146]
对比例2
[0147]
在本对比例中提供一种防霜膜,所述防霜膜仅包括顶层水性防雾防霜层,所述顶层水性防雾防霜层的制备原料按照重量份数计,包括如下组分:
[0148]
水性聚氨酯
ꢀꢀꢀꢀꢀꢀꢀꢀꢀꢀꢀꢀꢀꢀꢀꢀꢀꢀꢀꢀꢀꢀꢀꢀꢀꢀꢀꢀꢀ
80份;
[0149]
表面活性剂
ꢀꢀꢀꢀꢀꢀꢀꢀꢀꢀꢀꢀꢀꢀꢀꢀꢀꢀꢀꢀꢀꢀꢀꢀꢀꢀꢀꢀꢀ
12份;
[0150]
可降低水冰点的材料
ꢀꢀꢀꢀꢀꢀꢀꢀꢀꢀꢀꢀꢀꢀꢀꢀꢀꢀꢀꢀꢀ
8份。
[0151]
其中,水性聚氨酯为非离子单组份水性聚氨酯;表面活性剂为聚醚改性聚二甲基硅氧烷;可降低水冰点的材料为甘油。
[0152]
制备方法包括以下步骤:
[0153]
将配方量的水性聚氨酯、表面活性剂和可降低水冰点的材料混合,然后涂布在玻璃上,放入烘箱,在80℃下加热固化90min,得到所述防霜膜(厚度为10μm)。
[0154]
对比例3
[0155]
本对比例与实施例1不同之处仅在于,顶层水性防雾防霜层的制备原料中不包括可降低水冰点的材料,水性聚氨酯的重量份数为88份。
[0156]
对比例4
[0157]
本对比例与实施例1不同之处仅在于,将含丙烯酸基团的表面活性剂(含丙烯酸基团的聚醚)替换为等量的聚醚改性聚二甲基硅氧烷。
[0158]
对比例5
[0159]
本对比例与实施例1不同之处仅在于,顶层水性防雾防霜层的制备原料中可降低水冰点的材料的重量份数为15份,水性聚氨酯的重量份数为73份。
[0160]
对实施例1-5的防雾防霜膜以及对比例1-5的防雾膜或防霜膜进行性能测试,测试方法如下:
[0161]
(1)膜外观:观察制备样品外观,是否出油,在白炽灯光下是否有彩虹状油花;并触摸样品表面,是否粘手。
[0162]
(2)防雾性测试:将样品粘贴于玻璃上,距离样品20cm,用100℃的高温蒸汽喷蒸,样品立刻通透,则为防雾。
[0163]
(3)防雾材料渗出测试:将样品粘贴于玻璃上,距离样品10cm,用100℃的高温蒸汽喷蒸2min,观察防雾效果后,将样品于室温下放置干燥,然后再喷蒸2min-观察防雾效果-室温干燥水分,如此反复;记录喷蒸后,样品30%的面积出现水珠及雾气时的喷蒸次数。
[0164]
(4)防雾耐久性测试:将样品粘贴于玻璃上,置于常温露天环境中23
±
5℃/50%rh,按时间0h,1h,1天(24h),2天
…
,之后每一天对样品进行一次防雾性测试,共进行10天的防雾性测试,直至样品30%的面积出现水珠及雾气,记录放置的天数。
[0165]
(5)防霜性测试:将样品贴于玻璃上,置于温度为-18℃的超低温恒温箱或冷柜中;60min后取出样品,置于常温环境下,放置15s后,目测观察样品起霜情况。
[0166]
起雾评价标准:
[0167]
等级1代表完全透明无水滴;
[0168]
等级2代表透明性较好,有少量不均匀大水滴,出现水滴面积不超过5%;
[0169]
等级3代表基本透明,有较多水滴,出现水滴面积不超过30%;
[0170]
等级4代表半透明,有很多小水珠,出现水滴面积50%以上;
[0171]
等级5代表完全不透明。
[0172]
起霜评价标准:
[0173]
等级1代表完全透明无霜;
[0174]
等级2代表表面结薄霜,但仍能基本透明;
[0175]
等级3代表完全不透明,表面结白色霜。
[0176]
性能测试结果如表1所示。
[0177]
表1
[0178] 膜外观防雾性(级)防雾材料渗出(次)防雾耐久性(天)防霜性(级)实施例1光滑,无油光1>10>101实施例2光滑,无油光1>10>101实施例3光滑,无油光1>10>101实施例4光滑,无油光1>10>101实施例5光滑,无油光1211对比例1粘,油光1533对比例2光滑,无油光1211对比例3光滑,无油光1>10>103对比例4光滑,无油光1211对比例5光滑,油光27>101
[0179]
由表1可以看出,本发明实施例1-4制备的防雾防霜膜均光滑、无油光,并且均具有优异的防雾性、防霜性以及防雾耐久性。实施例5中由于顶层过厚,底层的表面活性材料不易渗出,影响了底层表面活性材料的防雾效果。
[0180]
与实施例1相比,对比例1制备的防雾膜防雾耐久性明显下降,无防霜性能;对比例2制备的防霜膜仅喷蒸2次,样品即有30%的面积出现水珠及雾气;对比例3的防雾膜无防霜性能;对比例4制备的防雾防霜膜仅喷蒸2次,样品即有30%的面积出现水珠及雾气;对比例
5中由于加入的可降低水冰点的材料多,防雾防霜膜表面有油光,并且防雾性降低。
[0181]
从图1-4的防雾性测试结果图中也可以看出,实施例1(图1)、实施例5(图2右侧)、对比例1-4(图3和图4)的防雾防霜膜均具有优异的防雾性,经过防雾性测试后,膜表面完全透明无水滴,而对比例5的防雾防霜膜的防雾性稍差,膜表面有少量不均匀大水滴。其中,图中黑色方框圈起来的为防雾防霜膜,其他图里出现的黑色方框圈起来的也为防雾防霜膜,不再一一说明。
[0182]
从图5-10的防雾材料渗出测试结果图中也可以看出,实施例5(图5)、对比例2和对比例4(图6)的膜仅喷蒸2次,样品即有30%的面积出现水珠及雾气;对比例1(图7)的膜仅喷蒸5次,样品即有30%的面积出现水珠及雾气;对比例5(图8)的膜仅喷蒸7次,样品即有30%的面积出现水珠及雾气;而实施例1(图9)和对比例3(图10)喷蒸10次后仍未出现水珠及雾气。
[0183]
从图11-15的防雾耐久性测试结果图中可以看出,实施例5(图11)、对比例2和对比例4(图12)在第1天进行防雾耐久性测试时即有30%样品面积出现水珠及雾气;对比例1(图13)在第3天进行防雾耐久性测试时即有30%样品面积出现水珠及雾气;实施例1和对比例5(图14)、对比例3(图15)在第10天进行防雾耐久性测试时仍未明显出现水珠及雾气。
[0184]
从图16-22的防霜性测试图中可以看出,实施例1(图16)、对比例5(图17)、实施例5(图18)、对比例2(图20)、对比例4(图22)的防雾防霜膜具有优异的防霜性,对比例1(图19)和对比例3(图21)的防雾防霜膜无防霜性能。
[0185]
申请人声明,本发明通过上述实施例来说明本发明的防雾防霜膜及其制备方法,但本发明并不局限于上述实施例,即不意味着本发明必须依赖上述实施例才能实施。所属技术领域的技术人员应该明了,对本发明的任何改进,对本发明所选用原料的等效替换及辅助成分的添加、具体方式的选择等,均落在本发明的保护范围和公开范围之内。