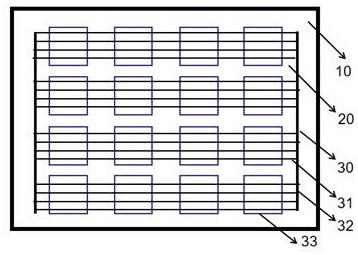
1.本实用新型属于光伏组件封装领域,特别是涉及一种封装胶膜。
背景技术:2.光伏组件在户外使用时,户外高温、高湿及强烈光照的条件下会导致光伏封装胶膜体系中残留的过氧化物类交联剂发生分解,所分解的物质会进一步形成氢过氧化物,氢过氧化物活性较高,晶体硅电池表面的焊带被腐蚀成黑色的氧化银,被氧化而变黑。对于乙烯-乙酸乙烯酯,高温高湿的环境会引起乙烯-乙酸乙烯酯分解产生醋酸,醋酸腐蚀焊带和汇流条,降低组件的输出功率,组件的耐久性也降低。
3.因此,为了防止组件内部焊带、汇流条的腐蚀,同时保持组件输出功率的稳定,延长组件使用寿命,因此亟待解决光伏封装胶膜在高温高湿环境下使用产生的醋酸或过氧化物的分解产物等对组件内部的焊带和汇流条的金属腐蚀。
4.目前,专利cn102318080 b提供一种太阳能电池密封膜,通过加入ph大于9.0的水滑石作为吸附剂,来抑制导线、电极生锈,但水滑石价格相对较贵,增加了密封膜的生产成本。专利cn101542748 b公开一种太阳能电池密封膜,该eva薄膜受光侧含有酸吸收剂氢氧化镁,此类酸吸收剂为极性无机物,表面能大,表面活性高,与乙烯-醋酸乙烯酯共聚物 (eva) 的相容性很差,易造成界面缺陷,导致材料性能下降,不能很好的保证太阳能电池的耐久性,同时此类酸吸收剂的加入会造成eva胶膜的透光率降低,老化性能下降,进而引起组件的光电转换效率降低。cn110093112a提出对抗腐蚀填料进行偶联剂改性同时加入成核增透剂,虽然一定程度解决了抗腐蚀的同时透光率降低的问题,但胶膜生产成本显著提高。
5.本实用新型提供一种封装胶膜,以解决光伏组件焊带和汇流条的腐蚀问题,同时保证不会影响电池片区域胶膜的透光率,最终提高光伏组件的功率和长期抗腐蚀抗老化性能,满足光伏组件二十年的使用寿命,并且大幅度减少了抗腐蚀填料的使用,降低了封装胶膜的成本,契合了现在光伏领域“降本增效”的政策。
技术实现要素:6.本实用新型的目的是弥补现有技术的不足,提供一种封装胶膜。
7.本实用新型所述封装胶膜解决了现有的抗腐蚀胶膜由于填料的加入或填料分散不均匀引起的胶膜透光率降低的问题;整个胶膜体系中抗腐蚀填料的加入也会影响胶膜的老化,出现老化发黄的问题。本技术所述封装胶膜减少了抗腐蚀填料的使用,显著降低了光伏封装胶膜的成本。本实用新型的封装胶膜具有较好的抗腐蚀性,且成本低。
8.为了达到上述的目的,本实用新型采取以下技术方案:
9.一种封装胶膜包括基体胶膜层和抗腐蚀层,抗腐蚀层位于基体胶膜层的一侧表面上,抗腐蚀层设置在电池串的焊带和汇流条相对应的投影位置。
10.进一步的,所述抗腐蚀层与焊带对应位置的宽度不小于焊带的宽度,所述抗腐蚀层与汇流条对应位置的宽度不小于汇流条的宽度。
11.进一步的,所述抗腐蚀层的厚度为10-45μm。
12.进一步的,所述抗腐蚀层含有抗腐蚀填料,所述抗腐蚀填料为氧化镁、氧化钙、氧化锌、氢氧化镁、氢氧化钙、氢氧化锌中的一种或几种。
13.进一步的,所述抗腐蚀填料的粒径为0.01-150μm,优选为60-100μm。
14.进一步的,所述基体胶膜层和所述抗腐蚀层为同种树脂材料,所述树脂材料选自乙烯-乙酸乙烯酯、聚烯烃、聚乙烯醇缩甲醛中的一种或多种。
15.进一步的,所述基体胶膜层和所述抗腐蚀层为不同种树脂材料,基体胶膜层和抗腐蚀层的树脂材料分别相互独立地选自乙烯-乙酸乙烯酯、聚烯烃、聚乙烯醇缩甲醛中的一种或多种。
16.进一步的,所述抗腐蚀层胶膜的预交联度为3%-75%,优选10-40%。
17.进一步的,所述基体胶膜层和所述抗腐蚀层为一体设置。
18.根据本实用新型的另一方面,还提供了一种光伏组件,包括封装胶膜和电池片,其中,封装胶膜为上述封装胶膜,抗腐蚀层设置在电池串的焊带和汇流条相对应的投影位置,在光伏组件封装时,抗腐蚀层临近电池片一侧放置。
19.进一步的,所述光伏组件为双面双玻电池组件。
20.本实用新型公开了一种封装胶膜。该封装胶膜包括基体胶膜层和抗腐蚀层,抗腐蚀层位于基体胶膜层的一侧表面上,抗腐蚀层具有与电池串的焊带和汇流条相对应的结构,在光伏组件封装时,抗腐蚀层临近电池片一侧放置。所述封装胶膜解决了现有的抗腐蚀胶膜由于填料的加入引起的胶膜透光率降低的问题;解决了由于抗腐蚀填料的加入组件老化后胶膜发黄的问题;本技术所述封装胶膜减少了抗腐蚀填料的使用,显著降低了光伏封装胶膜的成本。本实用新型的封装胶膜具有较好的抗腐蚀性,且成本低。
附图说明
21.构成本技术的一部分的说明书附图用来提供对本实用新型的进一步理解,本实用新型的示意性实施例及其说明用于解释本实用新型,并不构成对本实用新型的不当限定。在附图中:
22.图1示出了根据本实用新型的一种实施例提供的封装胶膜的俯视示意图;
23.图2示出了根据本实用新型的一种实施例提供的光伏组件的部分拆分结构示意图。
24.其中,上述附图包括以下附图标记:
25.10、基体胶膜层;20、抗腐蚀层;30、电池串;31、焊带;32、汇流条;
26.33、电池片。
具体实施方式
27.需要说明的是,在不冲突的情况下,本技术中的实施例及实施例中的特征可以相互组合。下面将参考附图并结合实施例来详细说明本实用新型。
28.为了使本技术领域的人员更好地理解本实用新型方案,下面将结合本实用新型实施例中的附图,对本实用新型实施例中的技术方案进行清楚、完整地描述,显然,所描述的实施例仅仅是本实用新型一部分的实施例,而不是全部的实施例。基于本实用新型中的实
施例,本领域普通技术人员在没有做出创造性劳动前提下所获得的所有其他实施例,都应当属于本实用新型保护的范围。
29.除非另作定义,本公开所使用的技术术语或者科学术语应当为本实用新型所属领域内有一般技能的人士所理解的通常意义。
30.如本技术背景技术所分析的,光伏组件的焊带和汇流条会发生腐蚀问题,引起光伏组件老化,现有技术通过在整个胶膜体系中加入抗腐蚀填料,会影响电池片区域胶膜的透光率和雾度,导致光转换效率降低。为了解决该问题,本技术提供了一种封装胶膜和光伏组件。
31.在本技术一种典型的实施方式中,提供了一种封装胶膜,如图1所示,所述封装胶膜包括基体胶膜层10和抗腐蚀层20,抗腐蚀层20位于基体胶膜层10的一侧表面上,抗腐蚀层20设置在电池串30的焊带31和汇流条32相对应的投影位置。
32.为了实现对抗腐蚀层20对光伏组件的焊带和汇流条更有效的抗腐蚀性能,所述抗腐蚀层20与焊带31对应位置的宽度不小于焊带的宽度,所述抗腐蚀层20与汇流条32对应位置的宽度不小于汇流条的宽度。进一步,在一种优选的实施方式中,优选所述抗腐蚀层20与焊带31对应位置的宽度等于焊带的宽度,所述抗腐蚀层20与汇流条32对应位置的宽度等于汇流条的宽度。
33.出于更好地兼顾抗腐蚀性能和透光性的目的,在一种优选的实施方式中,抗腐蚀层20的厚度为10-45μm。
34.所述抗腐蚀层20含有抗腐蚀填料,所述抗腐蚀填料为氧化镁、氧化钙、氧化锌、氢氧化镁、氢氧化钙、氢氧化锌中的一种或几种。上述几种抗腐蚀填料具有较高的抗腐蚀性能,能够在较少用量的基础上保证焊带和汇流条避免腐蚀。
35.在本技术一种实施例中,所述抗腐蚀填料的粒径为0.01-150μm,优选60-100μm。现有的抗腐蚀填料均要求粒径低于50μm以下,抗腐蚀填料粒径越小,加工工艺难度越大,成产成本越高,因此,粒径越小,抗腐蚀填料的价格越贵。同时现有的抗腐蚀胶膜均是在整个胶膜配方体系中加入抗腐蚀填料,显著提高了封装胶膜的生产成本。本技术所述封装胶膜优选60-100μm的抗腐蚀填料,并且仅用于抗腐蚀层20,只设置在电池串30的焊带31和汇流条32相对应的投影位置,一方面降低了抗腐蚀填料的成本,一方面降低了抗腐蚀填料的用量,综上,显著降低了封装胶膜的生产成本。
36.所述基体胶膜层10和所述抗腐蚀层20为同种材料,所述材料选自乙烯-乙酸乙烯酯、聚烯烃、聚乙烯醇缩甲醛中的一种或多种。
37.在一种优选的实施方式中,所述基体胶膜层10和所述抗腐蚀层20为不同种材料,基体胶膜层10和抗腐蚀层20的材料分别相互独立地选自乙烯-乙酸乙烯酯、聚烯烃、聚乙烯醇缩甲醛中的一种或多种。为了达到更好地抗腐蚀效果,本技术的抗腐蚀层20的材料优选聚烯烃树脂。
38.在一种优选的实施方式中,所述基体胶膜层10和所述抗腐蚀层20为一体设置。制备过程中可以整体制作,比如:基体胶膜层10和抗腐蚀层20采用同一材料同时挤出流延成型,花辊设置固定花纹,对应于电池串尺寸,使得抗腐蚀层20对应于电池串30的焊带和汇流条位置,抗腐蚀层20采用丝网印刷、喷墨打印、凹版印刷、涂布等工艺设置于焊带和汇流条区域。
39.在一种优选的实施方式中,所述基体胶膜层10和所述抗腐蚀层20为非一体化结构,基体胶膜层10先流延成膜,抗腐蚀层20流延成膜后,将其裁成相应的尺寸,用胶黏剂贴于基体胶膜层上焊带和汇流条所对应的投影位置。
40.在本技术一种实施例中,所述基体胶膜层10和所述抗腐蚀层20为非一体化结构时,所述抗腐蚀层20胶膜的预交联度为3%-75%,优选10-40%。抗腐蚀层20经过了预交联,因此其在层压时的流动性和变形性得到有效控制,从而有效避免了其在焊带31或汇流条32的脱落、变形和迁移,保证了抗腐蚀层20与电池串30的焊带31或汇流条32的对准效果。在利用本技术的封装胶膜作为光伏组件的前层胶膜时,避免抗腐蚀层20溢出到电池片上对电池片造成遮挡影响光电转换效率以及后续的光伏组件黑斑问题。
41.在对抗腐蚀层20进行辐射或者紫外照射时,利用掩膜将不需要交联的部分进行遮挡即可。
42.本技术仅对抗腐蚀层20的部分进行预交联,其它没有被预交联的部分在层压时可以在一定程度上流动对电池片进行更充分的粘结。
43.根据本实用新型的另一方面,还提供了一种光伏组件,包括封装胶膜和电池片,其中,封装胶膜为本技术所述封装胶膜,抗腐蚀层20设置在电池串30的焊带31和汇流条32相对应的投影位置,在光伏组件封装时,抗腐蚀层20临近电池片一侧放置。
44.优选的,所述光伏组件为双面双玻电池组件。
45.以下结合具体实施例对本技术作进一步详细描述,这些实施例不能理解为限制本技术所要求保护的范围。
46.实施例1
47.制备如图1所示的封装胶膜,具体制备工艺如下:
48.抗腐蚀层和基体胶膜层为一体化结构,基体胶膜层(厚度400微米)和抗腐蚀层(厚度50微米)采用同一材料,基体胶膜挤出流延成型,花辊设置固定花纹,对应于电池串的焊带和汇流条的尺寸和位置,抗腐蚀层采用丝网印刷工艺将抗腐蚀层基体树脂和抗腐蚀填料的混合料设置于电池串的焊带和汇流条的尺寸和位置。
49.各层材料和性能结果见表1。
50.实施例2
51.制备工艺同实施例1,部分材料不同,和性能结果见表1。
52.实施例3
53.制备工艺同实施例1,部分材料不同,和性能结果见表1。
54.实施例4
55.制备工艺同实施例1,部分材料不同,和性能结果见表1。
56.实施例5
57.制备工艺同实施例1,部分材料不同,和性能结果见表1。
58.实施例6
59.制备工艺同实施例1不同之处在于:抗腐蚀层和基体胶膜层为非一体化结构,基体胶膜层先流延成膜,抗腐蚀层流延成膜后将其裁成相应的尺寸,用胶黏剂贴于基体胶膜层上焊带和汇流条所对应的投影位置。部分材料不同,和性能结果见表1。
60.实施例7
61.制备工艺同实施例4,部分材料不同,和性能结果见表1。
62.实施例8
63.制备工艺同实施例4,部分材料不同,和性能结果见表1。
64.实施例9
65.制备工艺同实施例4,对抗腐蚀层进行辐射照射,利用掩膜将不需要交联的部分进行遮挡即可,预交联度10%,部分材料不同,和性能结果见表1。
66.实施例10
67.制备工艺同实施例4,对抗腐蚀层进行辐射照射,利用掩膜将不需要交联的部分进行遮挡即可,预交联度40%,部分材料不同,和性能结果见表1。
68.对比例1
69.封装胶膜仅为一层eva胶膜,性能见表1。
70.对比例2
71.封装胶膜仅为一层poe胶膜,性能见表1。
72.对比例3
73.封装胶膜为两层胶膜,一层eva胶膜,一层poe胶膜,性能见表1。
74.性能测试
75.通过上述实施例和对比例得到的封装胶膜应用于太阳能电池组件的封装,经过下列测试方法进行评价,评价结果列于下述表1。
76.1. 组件中焊带和汇流条腐蚀情况和胶膜黄变情况外观评估:使用实施例1~10和比较例1~3的封装胶膜进行组件封装试验,按玻璃/封装胶膜/电池片/封装胶膜/盖板的次序放入真空层压机内,经过145℃层压(抽真空6min,层压12min)制得组件,将上述组件进行pct老化(121℃,100%rh),通过el跟踪观察pct老化240小时后组件的焊带和汇流条的外观腐蚀情况以及胶膜区域的黄变情况。
77.2胶膜透光率测试:对实施例1~10和比较例1~3的封装材料层压后进行透光率测试,透光率测试依据gb/t 2410-2008进行测定,用紫外-可见分光光度计测定胶膜700~400nm的透光率。
78.从以上的描述中,可以看出,本实用新型上述的实施例实现了如下技术效果:抗腐蚀层位于基体胶膜层的一侧表面上,抗腐蚀层具有与电池串的焊带和汇流条相对应的结构,在光伏组件封装时,抗腐蚀层临近电池片一侧放置。所述封装胶膜解决了现有的抗腐蚀胶膜由于填料的加入引起的胶膜透光率降低及老化后黄变的问题。另外,本技术所述封装胶膜减少了抗腐蚀填料的使用,显著降低了光伏封装胶膜的成本。因此,本实用新型的封装胶膜具有较好的抗腐蚀性,透光率优异,老化后不会发生黄变,且成本显著降低。
79.以上实施例的说明只是用于帮助理解本实用新型方法及其核心思想。应当指出,对于本技术领域的普通技术人员来说,在不脱离本实用新型原理的前提下,还可以对本实用新型进行若干改进和修饰,这些改进和修饰也落入本实用新型权利要求保护范围内。