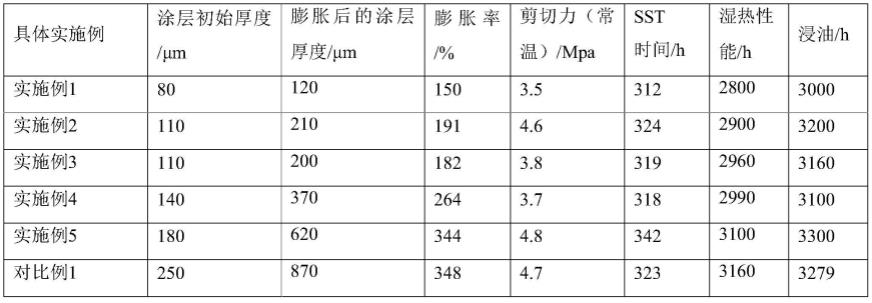
1.本实用新型涉及磁体表面防护处理领域,具体涉及一种涂层和包含所述涂层的磁体,尤其是钕铁硼磁体。
背景技术:2.钕铁硼磁体因其优良的磁性能,广泛应用于汽车电机、风力发电、电梯、曳引机等领域。对于高速运行的永磁电机,转子磁体损耗已成为影响其可靠运行的关键因素。为了减少磁钢涡流损耗,内置式永磁电机(ipm)通常是将一片或多片永磁钕铁硼磁钢单片组装在一起,涂覆绝缘涂层后封装在磁钢槽内,以此来降低磁钢的涡流损耗。在这个过程中,灌封树脂一直是电机设计改进的重点,树脂的流动性、粘接强度、绝缘性、导热性、耐油性、环保性都是设计者要考虑的要素。
3.常规装配方式虽然已经取得了很好的装配效果,但是仍存在不同的问题,如,灌胶树脂,磁体表面只布置树脂类涂层,极寒环境下可能会有发生碎屑现象,破坏环氧树脂类涂层。磁体表面环氧树脂类涂层与磁钢槽紧密接触时,环氧树脂类涂层会发生磨损或者龟裂,可能会腐蚀磁体表面,导致磁体过早损坏,且环氧树脂的制备与使用过程不环保、工艺制备复杂、周期长等。粘结胶、粘合片等装配过程中,若混入泥、砂、碎石时,更加速了环氧树脂类涂层的毁坏。
4.膨胀涂层广泛应用于建筑防火涂料、油墨印刷、包装保护涂料等领域,以及应用含有膨胀微球制备的可膨胀片材来代替粘结剂的作用。但将其应用在电极装配时,仍存在诸多问题。
技术实现要素:5.为了解决磁性材料装配难度及节省人工的问题,本实用新型提供一种涂层结构和包含所述涂层结构的磁体,尤其是钕铁硼磁体。
6.本实用新型提供一种涂料组合物,所述涂料组合物含有发泡体。
7.优选地,所述发泡体在膨胀温度或高于膨胀温度下加热时,所述发泡体可产生膨胀,所述膨胀不可逆。优选地,产生膨胀后的发泡体的体积可膨胀增加至少100%。优选地,所述发泡体选自物理发泡体或化学发泡体。优选地,所述发泡体的膨胀温度为100-250℃。
8.根据本实用新型的实施方案,所述涂料组合物包含树脂、发泡体、固化剂、添加剂和助剂。
9.根据本实用新型的实施方案,所述涂料组合物的组份按重量份计,包含:树脂10-50重量份,发泡体5-40重量份,固化剂2-10重量份,添加剂0.5-10重量份和助剂0.5-15重量份。
10.根据本实用新型的实施方案,所述树脂选自水性热塑性树脂、水性热固性树脂或热熔填充树脂中的至少一种。
11.优选地,所述水性热塑性树脂选自水性丙烯酸树脂、聚氨酯树脂中的至少一种。
12.优选地,所述水性热固性树脂选自水性环氧树脂、羟基丙烯酸中的至少一种。
13.优选地,所述热熔填充树脂选自改性氯化聚氯乙烯、聚酯、聚氨酯、聚酰胺、聚醚砜、环氧树脂和聚甲基丙烯酸甲酯中的至少一种。
14.示例性地,所述环氧树脂为双酚a型环氧树脂,优选为软化点在50-95℃之间的双酚a型环氧树脂。
15.优选地,所述树脂含量为15-25重量份。
16.根据本实用新型的实施方案,所述发泡体选自可膨胀微球、碳酸盐无机发泡剂、偶氮系有机发泡剂、磺酰肼系有机发泡剂,优选为可膨胀微球。优选地,所述可膨胀微球的平均粒径为5-50μm,优选为5-20μm,更优选为10-15μm。示例性地,所述可膨胀微球选自akzo-nobel公司的expancel系列中920du80与 920du40混合物,其中,两者的重量比为(1-2):(1-2),所述可膨胀微球的平均粒径为14μm、17μm或20μm。
17.优选地,所述发泡体的含量为5-25重量份或5-40重量份。
18.根据本实用新型的实施方案,所述固化剂选自咪唑、咪唑的环氧树脂加合物或多胺的环氧树脂加合物中的至少一种,优选为2-甲基咪唑。优选地,所述固化剂含量为3-6重量份。
19.根据本实用新型的实施方案,所述添加剂选自颜料和/或填料,具体地,所述添加剂选自滑石粉、碳酸钙、硫酸钡或绝缘炭黑中的至少一种。优选地,所述添加剂含量为1-2.5重量份。
20.发明人发现,在所述涂层中加入上述添加剂不仅能降低原料成本,还赋予涂层良好的光泽。
21.根据本实用新型的实施方案,所述助剂选自分散剂、偶联剂、消泡剂、润湿剂、增稠剂、固化剂、成膜助剂中的至少一种。示例性地,所述分散剂可选自硬脂酸镁、聚磷酸盐的一种。示例性地,所述偶联剂可选用硅烷偶联剂。示例性地,所述消泡剂选自聚硅氧烷、脂肪酸酯的一种,例如二甲基硅油等。示例性地,所述润湿剂可以选用聚氧乙烯烷基酚醚、聚氧乙烯脂肪醇醚中的一种。示例性地,所述增稠剂可选用膨润土、聚丙烯酸钠中的一种。示例性地,所述固化剂可选自二乙烯三胺、三乙烯四胺的一种。示例性地,所述成膜助剂可丙二醇丁醚或乙二醇丁醚中的至少一种。
22.发明人发现,分散剂和润湿剂可以使发泡体和填料更好分散,涂层形成的漆膜更加均;增稠剂可以赋予涂料更好的流变性能,生产便利,便于固化成型;消泡剂与润湿剂可以减少填料或发泡体中的气泡。
23.根据本实用新型的实施方案,所述涂料组合物还任选含有无机纤维。优选地,所述无机纤维选自纳米硅酸铝纤维、碳纤维和硼纤维中的一种、两种或更多种。
24.根据本实用新型的实施方案,所述组合物中还可以含有溶剂。优选地,所述溶剂选自醇类溶剂(如甲醇、乙醇)、醚类溶剂(如乙醚)、芳烃类溶剂(如苯)中的至少一种,优选为醇类溶剂,如乙醇。
25.根据本实用新型的实施方案,所述涂料组合物可以选自粉末状、液体状、浑浊液等中的任一种。
26.根据本实用新型示例性的方案,当所述涂料组合物中不含溶剂时,所述涂料组合物为固体粉末,其中,可膨胀微球的含量为5-40重量份。将所述涂料组合物加热后挤出、冷
却并研磨成固体粉末,固体粉末的粒径为10-80μm,平均粒径优选为20-50μm。
27.优选地,所述涂料组合物为固体粉末,在静电荷的作用下,固体粉末在磁体表面均匀分布,并可以稳定地附着在磁体上。
28.根据本实用新型示例性的方案,当所述涂料组合物中含有溶剂时,所述涂料组合物为液体或悬浊液,其中,可膨胀微球的含量为5-25重量份。所述涂料组合物为液体或悬浊液,所述涂料组合物布置到磁体表面的工艺操作更加简单,涂层厚度的均一性更好。
29.本实用新型还提供一种涂层,所述涂层包括第一涂层和第二涂层,所述第一涂层介于磁体与第二涂层之间;所述第一涂层的厚度为大于等于0μm且小于等于20μm,所述第二涂层的厚度为大于等于20μm且小于等于300μm,例如大于等于50μm且小于等于250μm。
30.应当理解,当所述第一涂层的厚度为0μm时,所述第二涂层与磁体接触;当所述第一涂层的厚度大于0μm时,所述第一涂层与磁体接触。
31.根据本实用新型的实施方案,所述第二涂层含有发泡体。优选地,所述发泡体由上述涂料组合物提供。
32.优选地,所述发泡体选自可膨胀微球、碳酸盐无机发泡剂、偶氮系有机发泡剂、磺酰肼系有机发泡剂;
33.更优选地,所述发泡体选自可膨胀微球,所述可膨胀微球的平均粒径为 5-50μm,优选为5-20μm,更优选为10-15μm;
34.更优选地,至少两个所述可膨胀微球之间不彼此接触。
35.根据本实用新型的实施方案,所述第二涂层可用于加热膨胀。优选地,在膨胀温度或高于膨胀温度下加热后,所述第二涂层可产生膨胀。优选地,加热膨胀后,第二涂层的厚度为初始厚度的100-400%,优选为150-300%。
36.优选地,加热膨胀后,所述第二涂层中的发泡体发生膨胀,所述膨胀温度具有如上所述含义。
37.优选地,加热膨胀后,第二涂层的截面中,所述发泡体的面积占总面积的 70-95%。优选地,加热膨胀后,第二涂层呈蜂窝状(如图4所示)或者褶皱状(如图5所示)。优选地,所述蜂窝状或者褶皱状的第二涂层由膨胀后的发泡体形成。
38.为此,本实用新型还提供一种涂层(例如通过上述涂层加热膨胀后得到),所述涂层包括第一涂层和第二涂层,所述第一涂层介于磁体与第二涂层之间。
39.所述第一涂层的厚度为大于等于0μm且小于等于20μm,所述第二涂层的厚度为大于等于100μm且小于等于700μm,例如大于等于100μm且小于等于650μm。
40.应当理解,当所述第一涂层的厚度为0μm时,所述第二涂层与磁体接触;当所述第一涂层的厚度大于0μm时,所述第一涂层与磁体接触。
41.根据本实用新型的实施方案,所述加热膨胀是指在加热条件下和空气中的自由膨胀。
42.根据本实用新型的实施方案,所述第二涂层的至少一个表面呈蜂窝状或者褶皱状。
43.根据本实用新型的实施方案,所述第二涂层包含膨胀后的发泡体。优选地,所述发泡体选自可膨胀微球、碳酸盐无机发泡剂、偶氮系有机发泡剂、磺酰肼系有机发泡剂。
44.根据本实用新型的实施方案,所述第二涂层包含树脂、膨胀后的发泡体、固化剂、
添加剂和助剂。
45.根据本实用新型的实施方案,所述膨胀后的发泡体选自膨胀后的可膨胀微球,并且膨胀后的微球中,50%以上的微球与其他微球接触。
46.根据本实用新型的优选实施方案,所述膨胀后的发泡体选自膨胀后的可膨胀微球,并且膨胀后的微球彼此之间的接触面积大于膨胀前的微球彼此之间的接触面积。
47.根据本实用新型的实施方案,所述发泡体由上述涂料组合物提供。
48.根据本实用新型的实施方案,所述第一涂层选自短期防腐涂层、金属涂层或绝缘涂层中的至少一种。示例性地,所述第一涂层包括金属镀层和绝缘涂层,所述金属镀层涂覆在所述磁体基体上,所述绝缘涂层涂覆在所述金属镀层上。
49.优选地,所述短期防腐涂层选自磷化层、钝化层、陶化层、硅烷化层或螯合化层等中的至少一种。优选地,所述短期防腐涂层通过磷化、钝化、陶化、硅烷化或螯合化等方式处理得到。优选地,所述短期防腐涂层的厚度为大于等于0μm且小于等于5μm。示例性地,当所述短期防腐涂层选自磷化层时,所述短期防腐涂层的厚度为大于等于0μm且小于等于1μm。
50.优选地,所述金属涂层选自锌、镍、铜、铝等中的至少一种或含有上述至少一种金属的合金。优选地,所述金属涂镀层通过电镀、物理涂镀、化学镀等中的任一种方式获得。优选地,所述金属涂镀层的厚度为大于等于0μm且小于等于15μm,优选为大于等于5μm且小于等于15μm。
51.优选地,所述绝缘涂层选自溶剂型涂料、粉末类涂料、水性涂料中的至少一种。优选地,所述绝缘涂层可通过电泳、喷涂、浸涂、静电涂装、流化床涂装、熔射法涂装等任一种方式制备得到。示例性地,所述绝缘涂层为聚氨酯涂层、环氧树脂涂层等。优选地,所述绝缘涂层的厚度为大于等于0μm且小于等于 20μm,优选为大于等于10μm且小于等于20μm。
52.根据本实用新型示例性的方案,所述涂层包括第一涂层和第二涂层,其中,所述第一涂层为短期防腐层,所述第二涂层为膨胀涂层。
53.根据本实用新型示例性的方案,所述涂层包括第一涂层和第二涂层,其中,所述第一涂层为金属涂镀层,所述第二涂层为膨胀涂层。
54.根据本实用新型示例性的方案,所述涂层包括第一涂层和第二涂层,其中,所述第一涂层为绝缘涂层,所述第二涂层为膨胀涂层。
55.本实用新型还提供一种钕铁硼磁体,所述钕铁硼磁体的至少一个表面布置有所述的涂层,其中所述第一涂层介于所述钕铁硼磁体与第二涂层之间。
56.根据本实用新型的实施方案,将上述涂料组合物布置在磁体基体表面、预固化处理后得到所述涂层。
57.示例性地,当所述钕铁硼磁体为方形时,方型磁体中至少一个表面涂覆有涂层,例如其1个、2个、3个、4个、5个或6个表面涂覆有涂层。
58.根据本实用新型的实施方案,所述钕铁硼磁体具有如下性能:
59.(1)第二涂层的膨胀率为150-400%;
60.(2)涂层的剪切力为1-15mpa;
61.(3)耐油性能大于2000h;
62.(4)中性盐雾性能达到240h以上。
63.本实用新型还提供上述钕铁硼磁体的制备方法,所述制备方法包括:
64.第一步:磁体基体表面预处理;
65.第二步:在磁体基体表面布置所述涂层:所述涂层包括第一涂层和/或第二涂层;
66.第三步:预固化处理,得到钕铁硼磁体。
67.根据本实用新型的实施方案,在第一步中,磁体基体表面预处理包括对磁体基体的表面进行洁净度处理,所述磁体基体为钕铁硼磁体基体。
68.优选地,所述洁净度处理包括脱脂、除锈、除灰、水洗或活化中的至少一种。
69.优选地,所述脱脂是指采用无泡无磷常温脱脂液对钕铁硼产品进行脱脂处理,处理时间120s。优选地,所述除锈是指采用体积浓度5%的稀硝酸对脱脂后的产品进行除锈处理,处理时间为40s。优选地,所述水洗可以为超声水洗。优选地,所述活化是指使用活化液对除锈后的钕铁硼产品进行活化,活化时间为 12s,其中,所述活化液由3.5wt%柠檬酸、1g/l硫脲和1g/l十二烷基苯磺酸钠组成。
70.示例性地,所述洁净度处理包括脱脂、水洗、除锈、超声水洗-水洗、活化和水洗。
71.根据本实用新型的实施方案,在第二步中,所述第一涂层具有如上所述定义。在本实用新型中,对第一涂层的类型不作具体限定,可以根据对磁体的防腐性、导电性等性能要求,选择布置上述任一种第一涂层。
72.优选地,在布置第一涂层后,还需充分烘干。优选地,烘干温度为40-200℃,优选为60-110℃。优选地,烘干时间为5-90min,优选为15-50min。
73.示例性地,当第一涂层为短期防腐涂层时,所述第一涂层可以通过磷化、钝化、陶化、硅烷化、螯合化等任一种方式制备得到。优选地,处理时间为1-20min,优选为1-10min。例如,所述第一涂层通过浸渍法磷化制备得到,其中磷化时间为5min,磷化液温度为50℃,磷化后产品进行吹干、烘干处理。
74.示例性地,当第一涂层为金属涂层时,所述金属涂层可通过电镀、物理涂镀、化学镀等任一种方式制备得到。例如,所述金属涂层通过电沉积滚镀镍制备得到。
75.示例性地,当第一涂层为绝缘涂层时,所述绝缘涂层可通过电泳、喷涂、浸涂、静电涂装、流化床涂装、熔射法涂装等任一种方式制备得到。例如,所述第一涂层通过环氧电泳漆的电泳制备得到,其中,环氧电泳漆的ph为5.0-6.5、电导率为900-1500μs/cm,电泳条件为:电泳电压为100v-200v,电泳时间为 100s-350s,电泳温度28-36℃。
76.根据本实用新型的实施方案,在第二步中,所述第二涂层由涂料组合物制备得到。所述涂料组合物具有如上文所述的定义。
77.优选地,所述第二涂层的制备方法包括:将涂料组合物布置到第一涂层的上面或磁体基体表面,形成第二涂层。所述第二涂层可以通过浸涂、刮涂、刷涂、压印或者喷涂中的任一种方式制备得到。例如,所述第二涂层采用静电粉末喷涂制备得到,具体包括:通过高压静电发生器将涂料组合物的固体粉末带上负电,由于电势差的关系,在电场力作用下,将带负电的粉末吸附到带正电的磁体表面,其中,在布置前,所述涂料组合物经加热后挤出、冷却并研磨成固体粉末,固体粉末的粒径为10-80μm,平均粒径优选为20-50μm。
78.发明人发现,当第二涂层涂覆过薄,在装配后加热时,第二涂层的膨胀力不够,达不到要求的顶出力,易于脱落;若涂覆太厚,虽然磁体表面更有利于形成完整的涂层,且拥有较高的膨胀率,但涂层过厚,更易脱落、龟裂,而且涂层过厚,转子在使用过程中会造成较高的涡流损失。
79.本实用新型中,在第三步中,预固化处理时,可以采用任意的加热方式进行加热,例如在烘箱中、使用加热辊或电磁加热,加热温度低于发泡体的膨胀温度即可。优选地,所述预固化处理的条件包括:预固化的温度为35-90℃,预固化的时间30-60min。
80.发明人发现经过预固化处理,磁体表面的涂层中树脂开始熔融、聚集,从而在磁体的表面形成平整且致密的涂层。经过预固化处理后,第二涂层中的发泡体(例如可膨胀微球)在涂层中保持合适位置,从而在后期的膨胀温度下加热实现发泡体(例如可膨胀微球)的自然膨胀。
81.发明人还发现,当预固化温度过高,会降低涂层的平整度,甚至会造成磁体的黏连,进而影响膨胀效果。应控制烘箱等加热处理方式的均温性,避免造成受热不均。
82.在室温与第一加热工序前,固化剂与环氧树脂,已经发生了微量的反应,使得运输前第二涂层与磁体表面或第一涂层的粘合效果增加,第二涂层能够更好的粘合在磁体基体上,运输稳定性更高。
83.本实用新型还提供一种转子,所述转子包括上述钕铁硼磁体。
84.优选地,所述钕铁硼磁体装配到所述转子上后,经加热膨胀后,使所述钕铁硼磁体固定在所述转子上,完成装配。
85.优选地,膨胀条件包括加热温度为膨胀温度或高于膨胀温度。优选地,所述膨胀温度为100-210℃。
86.本实用新型还提供一种电机,所述电机装配有上述钕铁硼磁体或上述转子。
87.有益效果:
88.本实用新型的钕铁硼磁体表面布置有涂层,涂层厚度为20-300μm,在加热后,其膨胀率为100-400%,剪切力为1-15mpa,耐油性能大于2000h,中性盐雾可达到240h以上。
89.本实用新型的钕铁硼磁体表面布置有涂层,不仅改善了因自身孔隙大耐腐蚀较低的劣势,还提高了磁体整体的耐腐蚀性,绝缘性,厚度一致性佳,具有较好的耐蚀性,以及与磁体和磁钢槽的结合力。
90.本实用新型的钕铁硼磁体,对第一涂层与第二涂层的种类、厚度等进行选择,改善了因设计公差与制作公差的不匹配造成的叠片铁芯或叠层定位不精准,转子不够平衡问题。且在磁体与转子本身制造过程中产生公差较大时,也可以通过对第一涂层与第二涂层的种类、厚度等选择进行改善,进而实现永磁体的精准定位。
91.将含有本实用新型涂层的磁体装配至电机,因为涂层在加热时具有膨胀性,可代替普通粘胶、灌胶等装配方式,直接将覆有涂层的磁体产品装配好,利用涂层的膨胀性使其固定,节省装配成本,工艺简单、且操作便捷,装配精度更高且环境友好。
92.将本实用新型的涂层应用于电机装配时,具有环保性好、工艺过程简单、制备周期短等的特点,可以有效提高磁体整体的耐腐蚀性、绝缘性,且制备工艺稳定性好,具有较好的耐蚀性,进而提高与磁体和磁钢槽的结合力。
附图说明
93.图1为本实用新型的涂层示意图,其中第一涂层和第二涂层的厚度分别为 h1、h2。
94.图2为本实用新型涂层示意图(加热膨胀后),加热膨胀后的第二涂层的厚度为h2’。
95.图3为实施例2的样品在热膨胀前的第二涂层截面形貌扫描图。
96.图4为实施例2的样品在热膨胀后的第二涂层截面形貌扫描图。
97.图5为实施例4的样品在热膨胀后的第二涂层截面形貌扫描图。
具体实施方式
98.如图1所示,为本实用新型的涂层示意图,其中第一涂层和第二涂层的厚度分别为h1、h2。所述涂层包括第一涂层和第二涂层,所述第一涂层介于磁体与所述第二涂层之间;所述第一涂层的厚度为大于等于0μm且小于等于20μm,所述第二涂层的厚度为大于等于20μm且小于等于300μm。当所述第一涂层的厚度为0μm时,所述第二涂层与磁体接触;当所述第一涂层的厚度大于0μm时,所述第一涂层与磁体接触。
99.在本实用新型的一个具体实施方式中,所述第一涂层的厚度为0-20μm,所述第二涂层的厚度为20-300μm。优选地,所述第二涂层的厚度为50-250μm。
100.在膨胀温度或高于膨胀温度下加热后,本实用新型中所述第二涂层可产生膨胀。如图2所示,为本实用新型的涂层经加热膨胀后示意图,膨胀后的第二涂层的厚度为h2’。优选地,加热膨胀,第二涂层的厚度h2’为初始厚度h的 100-400%,优选为150-300%。在本实用新型的一个具体实施方式中,经加热膨胀后,所述第二涂层的厚度h2’为大于等于100μm且小于等于700μm,例如大于等于100μm且小于等于650μm。
101.下文将结合具体实施例对本实用新型的技术方案做更进一步的详细说明。应当理解,下列实施例仅为示例性地说明和解释本实用新型,而不应被解释为对本实用新型保护范围的限制。凡基于本实用新型上述内容所实现的技术均涵盖在本实用新型旨在保护的范围内。
102.除非另有说明,以下实施例中使用的原料和试剂均为市售商品,或者可以通过已知方法制备。
103.以下实施例及对比例均选用规格20mm
×
10mm
×
3.5mm的方形钕铁硼磁体产品,下述实施例与对比例中涂层的厚度均指的是涂层中心点处的厚度。
104.以下实施例中,样品的测试方法如下:
105.sst实验(中性盐雾性能)测试条件为:35℃,nacl水溶液浓度为50g/l
±
5g/l, ph介于6.5-7.2之间,通过喷雾的形式使nacl水溶液形成盐雾,并沉积到待测的钕铁硼磁体产品上,记录磁体表面开始出现生锈现象的时间。
106.湿热实验的测试条件为:将钕铁硼磁体产品置于85℃、湿度为85%rh的密闭环境中,观察磁体表面的锈蚀情况,记录磁体表面涂层开始出现发生变化的时间,以及再检测磁体涂层的性能,并未产生影响时,该时间为耐湿热时间。
107.浸油的测试条件为:将钕铁硼磁体产品置于150℃、变速箱油下全面覆盖浸泡,观察磁体表面的锈蚀、鼓泡、起皮等情况,记录磁体表面涂层开始出现发生变化的时间,以及再检测磁体涂层的性能,并未产生影响时,该时间为耐浸油时间。
108.剪切力的测试条件为:gb/t 7124-2008(胶粘剂.拉伸剪切强度的测定(刚性材料对刚性材料))。
109.实施例1
110.制备钕铁硼磁体,选用规格20mm
×
10mm
×
3.5mm的方块钕铁硼产品作为磁体基体,
其步骤为:
111.一、磁体基体表面预处理:
112.1)脱脂:采用无泡无磷常温脱脂液对钕铁硼产品进行脱脂处理,处理时间 120s;
113.2)水洗两次;
114.3)除锈:采用体积浓度5%的稀硝酸对脱脂后的产品进行除锈处理,处理时间为40s;
115.4)除锈完成后,对产品进行超声水洗-水洗;
116.5)活化:使用活化液对除锈后的钕铁硼产品进行活化,活化液由3.5wt%柠檬酸、1g/l硫脲和1g/l十二烷基苯磺酸钠组成,活化时间为12s;
117.6)水洗两次,得到预处理后的钕铁硼产品。
118.二、布置第一涂层:对经过预处理的磁体基体,采用浸渍法磷化,其中,磷化时间为5min,磷化液温度为50℃。磷化后对磁体进行吹干、烘干处理,得到表面含有磷化层为短期防腐涂层的磁体,磷化层的厚度为1μm。
119.三、制备涂料组合物:涂料组合物按照如下重量百分比配制:羟基丙烯酸树脂35%,可膨胀微球(akzo-nobel公司的expancel系列中920du80与920du40 按照重量比1:1混合,平均粒径为17μm)40%,2-甲基咪唑10%,绝缘炭黑5%,乙二醇丁醚5%,二甲基硅油5%,将上述将混合物加热后挤出、冷却并研磨至粉末状涂料,粉末涂料的粒径为10-80μm,平均粒径为40μm。
120.四、布置第二涂层:采用静电粉末喷涂的方式,通过高压静电发生器将粉末颗粒带上负电,在电场力作业下,粉末状涂料奔向带正电的磁体基体表面。
121.五、第一加热工序:布置第二涂层后,进行预固化处理,70℃烘箱烘干40min,固化后的第二涂层的厚度为80μm,得到钕铁硼磁体。
122.六、第二加热工序:热膨胀条件:烘箱170℃,5min,得到膨胀后的钕铁硼磁体,其中,第二涂层在加热后膨胀,记为样品1。
123.实施例2
124.本实施例采用同实施例1同样的磁体制备钕铁硼磁体,预处理的方法相同,第一涂层和第二涂层均同实施例1,其不同在于:
125.采用刷涂法,将涂料组合物粉末布置到磁体基体表面,进行预固化处理, 75℃烘箱烘干35min,固化后的第二涂层的厚度为110μm,得到钕铁硼磁体。加热膨胀条件:烘箱190℃,20min,得到膨胀后的钕铁硼磁体,其中,第二涂层在加热后膨胀,记为样品2。
126.实施例3
127.本实施例采用同实施例1同样的磁体制备钕铁硼磁体,预处理的方法相同,不同在于:
128.不施加第一涂层,直接布置同实施例1相同的第二涂层。
129.采用刷涂法,将涂料组合物粉末布置到磁体基体表面,进行预固化处理, 75℃烘箱烘干35min,固化后的第二涂层的厚度为110μm,得到钕铁硼磁体。加热膨胀条件:烘箱190℃,20min,得到膨胀后的钕铁硼磁体,其中,第二涂层在加热后膨胀,记为样品3。
130.实施例4
131.本实施例采用同实施例1同样的磁体制备钕铁硼磁体,预处理的方法相同,不同在
于:
132.对经过预处理的磁体基体,进行处理后产品采用电沉积滚镀镍制备第一涂层,第一涂层为镍金属镀层,厚度为10μm。
133.制备涂料组合物,按照下列重量百分比配置:水性丙烯酸树脂30%,可膨胀微球(akzo-nobel公司的expancel系列中920du80与920du40按照重量比2:1混合,平均粒径为20μm)25%,甲苯二异氰酸酯5%,绝缘炭黑2%,硬脂酸镁3%,丙二醇丁醚2%,余量为乙醇,得到液体状涂料组合物。
134.采用浸渍法,将涂料组合物布置到磁体基体表面,进行预固化处理,80℃烘箱烘干20min,固化后的第二涂层的厚度为140μm,得到钕铁硼磁体。加热膨胀条件:烘箱200℃,10min,得到膨胀后的钕铁硼磁体,其中,第二涂层在加热后膨胀,记为样品4。
135.实施例5
136.本实施例采用同实施例1同样的磁体制备钕铁硼磁体,预处理的方法相同,不同在于:
137.对经过预处理的磁体基体,进行预处理后采用如下方法制备环氧镀层作为第一涂层:采用环氧电泳漆的电泳电压为150v-200v;电泳时间为65s-120s;槽液ph为5.0-5.5;槽液电导率为1000-1500μs/cm;电泳温度28-36℃。第一涂层环氧镀层的厚度为15μm。
138.制备涂料组合物,按照下列重量百分比配置:羟基丙烯酸树脂15%,聚氨酯树脂20%,可膨胀微球(akzo-nobel公司的expancel系列中920du80与920du40 按照重量比1:2混合,平均粒径为14μm)15%,甲苯二异氰酸酯1%,纳米硅酸铝纤维5%,二乙烯三胺3%,硅烷偶联剂2%,膨润土3%,余量为乙醇,得到液体状涂料组合物。
139.采用浸渍法,将涂料组合物布置到磁体表面,进行预固化处理,90℃烘箱烘干15min,固化后的第二涂层的厚度为180μm,得到钕铁硼磁体。加热膨胀条件:烘箱210℃,15min,得到膨胀后的钕铁硼磁体,其中,第二涂层在加热后膨胀,记为样品5。
140.对比例1
141.本对比例采用同实施例1的磁体制备钕铁硼磁体,且磁体预处理的方法相同,不同在于:
142.制备涂料组合物,按照下列重量百分比配置:羟基丙烯酸树脂15%,聚氨酯树脂20%,可膨胀微球(akzo-nobel公司的expancel系列中920du80与 920du40按照重量比1:2混合,平均粒径为14μm)15%,甲苯二异氰酸酯1%,纳米硅酸铝纤维5%,硅烷偶联剂5%,膨润土3%,余量为乙醇。
143.采用浸渍法,将涂料组合物布置到磁体表面,进行预固化处理,90℃烘箱烘干15min,固化后的第二涂层的厚度为250μm,得到钕铁硼磁体。加热膨胀条件:烘箱210℃,15min,得到膨胀后的钕铁硼磁体,其中,第二涂层在加热后膨胀,记为对比样品。
144.实施例1-5和对比例1的样品处理条件及测试结果见表1。
145.表1
[0146][0147]
通过表1中实施例1与实施例2的数据可以看出,通过调整第二涂层的布置厚度,第二涂层厚度的增加,可以有效增加磁体在常温下的剪切力。图3为实施例 2的样品在加热膨胀前的第二涂层截面形貌扫描图,图4为实施例2的样品经加热膨胀后第二涂层的截面形貌扫描图,图5为实施例5的样品经加热膨胀后第二涂层的截面形貌扫描图。加热膨胀后的第二涂层呈蜂窝状(如图4)或者褶皱状(如图5),其中,发泡体的面积占所述第二涂层的截面面积的70-95%,所述蜂窝状或者褶皱状由膨胀后的发泡体形成。
[0148]
实施例2与实施例3的区别在于,实施例3不含有磷化层作为第一涂层,但由表1可以看出,第一涂层对第二涂层的膨胀率等影响较小,实施例3仍可以实现优异的膨胀效果,而实施例2中经过磷化布置第一涂层后,磁体表面的粗糙度增加,故其与第二涂层的结合力增加,在常温的剪切力均有一定的提升。
[0149]
对比表1中实施例4与实施例5的数据可以看出,实施例5增加了聚氨酯树脂、固化剂(二乙烯三胺)、成膜助剂(丙二醇丁醚)后,实施例5的膨胀率高,且剪切力与耐湿热性能、耐油性更优,这是因为,成膜助剂的增加使得涂层成膜效果更好,且固化剂在涂层成膜膨胀后,与树脂相互浸润,在涂层中起到骨架支撑和增加强度的效果,从而提高了涂层的强度与抗收缩性。对比例1的第二涂层的厚度为250μm,其不含有环氧涂层作为第一涂层,虽然对比例1的膨胀率与粘结推力并没有明显降低,但是由于热膨胀后涂层过厚,而过厚的涂层装配到电机中,一方面会出现涂层的收缩风险,导致工件错位,另一方面,过高的装配孔隙,会导致涡流损耗大,从而使磁体的性能受到影响。
[0150]
以上,对本实用新型的示例性实施方式进行了说明。但是,本实用新型不拘囿于上述实施方式。本领域技术人员在本实用新型的精神和原则之内,所做的任何修改、等同替换、改进等,均应包含在本实用新型的保护范围之内。