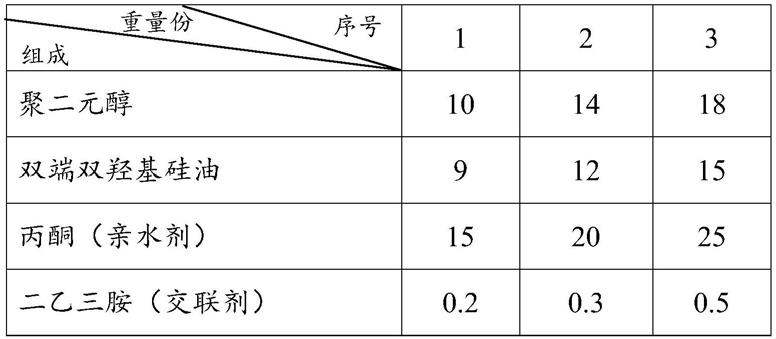
1.本发明涉及放射性去污膜及其制备领域,具体涉及一种可剥离式放射性 去污膜及其制备方法。
背景技术:2.放射性去污是指针对放射性污染物项,采用相适应的方法从物项上除去或 减少不希望其存在的放射性核素的活动。去污可以降低放射性水平、减少操 作人员的受照剂量;使得有些设施可再循环利用,场址可以无限制开放;减 少废物量,降低废物贮存、运输和处置的负担。主要的污染形式分为非固定 性污染、弱固定性污染以及强固定性污染,非固定性污染的污染核素与物体 表面之间以分子间作用力结合,二者结合疏松,易于去污;固定性污染的污 染核素与物体表面之间以化学吸附或离子交换形式结合,二者结合紧密,去 污比较困难;强固定性污染的污染核素扩散渗入基体材料内或基体材料内微 量元素受放射性辐射产生放射性核素,这种污染一般很难去除。
3.现有的放射性去污材料主要有干法消除剂、洗消剂、化学泡沫/凝胶去污 剂和可剥离膜材料等。其中,采用可剥离膜材料具有非常高的去污效果,而 且只产生极少量的易于压缩或焚烧的废物。可剥离式放射性去污膜是一种具 有多种官能团的高分子化合物,通过加入各种添加剂(例如络合剂、乳化剂、 成膜助剂、浸润剂等)以增强去污能力和改善涂料的物理化学性能。成膜前 是一种溶液或者水性的分散乳液,用喷雾法或抹刷法将其涂于沾污表面,等 待其干燥成膜。成膜过程中高分子链上的官能团以及其中的络合剂与引起沾 污的核素发生物理化学作用,使其从污染表面进入膜中,剥离掉涂膜达到去 污目的。具有使用简便、容易剥离回收、不产生废液、易于机械化作业等优 点,适用于金属、水泥、塑料、玻璃、木材和许多其它固体表面的快速去污, 在国防工业和民用上都有十分广泛的应用前景。
4.可剥离膜材料主要分为有机溶剂型和水溶(乳液)型两大类,国内市场 上目前已有的可剥离式的放射性去污涂料主要是溶剂型,由于溶剂的溶解作 用,使其在物理干燥型涂膜上使用受到限制。林晓艳课题组在2020年的西南 科技大学学报上发表了一种以聚乙烯乙酸酯为成膜主体,乙酸乙酯为有机溶 剂的可剥离膜,聚乙烯乙酸酯溶解于乙酸乙酯中待乙酸乙酯挥发后干燥成膜, 干燥时间约为5-7h,且乙酸乙酯易挥发,产生挥发性有机物(voc)排放, 容易对人体健康造成危害。cn112552753a公开了一种可剥离去污涂料及其制 备方法和应用,包括水性聚合物溶液和改性吸附纳米材料的组合,并且采用 多孔纳米材料、无孔纳米材料和络合剂三种材料的组合,制备得到了可剥离 去污涂料;其去污率为95.5~99.5%,拉伸强度为30.3~37.4mpa,断裂伸长 率为195~240%。但其成膜时间过长,在低温情况下容易脆断,断裂强度不 够高,成膜后的固含量较低且单次成膜太薄,在剥离膜的过程中容易断裂。
5.综上所述,由于现有公开技术中的可剥离去污涂料的性能仍然不够优异 稳定,因此如何开发一种低温(0℃)韧性好,成膜后拉伸强度高、且去污效 率高的可剥离去污膜是
本领域技术人员亟待解决的技术问题。
技术实现要素:6.为了解决上述技术问题,需要提供一种成膜后拉伸强度高且固含量高的 可剥离式放射性去污膜及其制备方法,以克服现有去污膜存在的缺陷。
7.为实现上述目的,本发明提供了一种可剥离式放射性去污膜及其制备方 法,具体采用以下技术方案:
8.本发明的可剥离式放射性去污膜的制备原料包括:水性聚合物、增强纤 维、络合剂及去离子水,所述水性聚合物为有机硅改性聚氨酯和/或有机硅改 性聚乙烯醇,所述增强纤维为硼复合木质素纳米纤维,所述络合剂为硫代氨 基羧酸盐、有机膦酸盐以及聚丙烯酸盐按0.1-0.3:1:1-2的质量比组成的复 合络合剂。
9.进一步地,按重量份数计,所述可剥离式放射性去污膜的制备原料包括: 20-65份水性聚合物,2-7份硼复合木质素纳米纤维,2-28份络合剂及30-60 份去离子水。
10.更进一步地,按重量份数计,所述可剥离式放射性去污膜的制备原料包 括:25-45份水性聚合物,2-7份硼复合木质素纳米纤维,6-20份络合剂及30-50 份去离子水。
11.进一步地,所述有机硅改性聚氨酯通过以下方法制备得到,所述方法包 括:
12.(1)将重量份为10-18份的聚二元醇,9-15份的双端双羟基硅油,15-25 份的亲水剂,0.2-0.5份的交联剂,140-170份二异氰酸酯在55-75℃下进行搅 拌,所述搅拌时间为25-40min;
13.(2)向步骤(1)所述混合溶液加入0.2-2份催化剂,升温至80-95℃恒温 反应1.5-3h;
14.(3)向步骤(2)所述混合溶液中加入1-4份除酸剂,恒温反应20-45min, 得到有机硅改性聚氨酯。进一步地,步骤(1)中,所述亲水剂选自甲醇、乙 醇、丙酮中的任意一种,特别优选丙酮。
15.进一步地,步骤(1)中,所述交联剂为二乙三胺。
16.进一步地,步骤(2)中,所述催化剂为二丁基二月桂酸锡。
17.进一步地,步骤(3)中,所述除酸剂选自二乙胺、三乙胺、氨水中的任 意一种,特别优选三乙胺。
18.进一步地,所述有机硅改性聚乙烯醇通过以下方法制备得到,所述方法 包括:将重量份为10-25份的烷氧基硅烷和45-80份的聚乙烯醇,55-90份的 溶剂,6-9份的酸在75-90℃下搅拌3.5-5h得到有机硅改性聚乙烯醇。
19.进一步优选的,所述溶剂选自甲醇、乙醇、甲苯、二氯甲烷中的任意一 种,特别优选乙醇。
20.进一步优选的,所述酸选自盐酸、磷酸、次磷酸、醋酸、乳酸中的任意 一种,特别优选醋酸。
21.进一步的,所述硼复合木质素纳米纤维的制备方法如下:
22.(a)硼酸改性木质素的制备:配制质量分数为3-5%的硼酸溶液,将硼 酸溶液加热至35-40℃,然后将木质素浸泡于硼酸溶液中1-5h,过滤,所得固 体在100-105℃下干燥2-5h,得到硼酸改性木质素;
23.(b)改性硼粉的制备:将硅烷偶联剂与硼粉按1:10-15的质量比加入 到丙酮和水的混合溶剂中,超声分散12-24h后,于70-80℃的温度下真空烘 干,得到改性硼粉;
24.(c)硼复合木质素纳米纤维前驱体的制备:将步骤(a)制备得到的硼 酸改性木质素用丙酮和水组成的混合溶剂进行溶解,按硼酸改性木质素:改 性硼粉的质量比为5-10:1的比例将改性硼粉在超声分散的条件下混入溶解有 硼酸改性木质素的混合溶剂中,得到硼复合木质素纳米纤维前驱体;
25.(d)静电纺丝法制备硼复合木质素纳米纤维:纺丝电压为20-25kv,针 头到接收铝箔的距离为10-15cm,溶液流速为4-6ml/h。
26.进一步地,步骤b中所述硅烷偶联剂选自kh-550、kh-570及kh-792 中的任意一种或多种。
27.进一步地,所述硫代氨基羧酸盐选自二甲基二硫代氨基甲酸钠、二乙基 二硫代氨基甲酸钠中的一种;所述有机膦酸盐选自乙二胺四甲叉磷酸钠、二 乙烯三胺五甲叉膦酸盐、氨基三甲叉膦酸中的一种或者几种,所述聚丙烯酸 盐络合剂选自聚丙烯酸钠、聚羟基丙烯酸钠中的一种。相比于单一的络合剂, 本发明采用的复合络合剂去污能力更好。
28.进一步地,所述可剥离式放射性去污膜的制备原料还包括助剂,所述助 剂包括0.01-1.5份消泡剂,0.02-0.8份分散剂或0.02-1份色素中的一种或几种。
29.进一步地,所述消泡剂选自聚醚改性硅氧烷、磷酸三丁酯中的一种。
30.进一步地,所述分散剂选自阴离子型水性分散剂(可例举的有油酸钠、 甲酸钠、甲磺酸钠)或阳离子型水性分散剂(可例举的有氨基丙胺二油酸酯) 中的一种。
31.进一步地,所述色素可为有机色素或无机色素,可为体系提供不同的颜 色,其中有机色素是由碳氢化合物构成的有机混合物,无机色素是不含金属、 不含有机物的色粉,可例举的有白炭黑、二氧化钛、酞菁蓝、酞菁绿、联苯 胺黄、宝红4b、永固紫、永固红等。
32.本发明还提供了上述可剥离式放射性去污膜的制备方法:将水性聚合物 与去离子水混合均匀后,将除络合剂之外的其余原料投入水性聚合物溶液中 并进行超声机械共混,所述共混时间为2-7h,再将络合剂投入共混溶液中进 行反应,得到制备所述可剥离式放射性去污膜的原料混合物,所述反应时间 为20-180min,所述反应温度为60-85℃;将原料混合物均匀喷涂于受到污染 的材料表面,在5-60℃下干燥成膜,即得可剥离式放射性去污膜。
33.优选的,所述可剥离式放射性去污膜可应用于受到放射性核素污染的材 料表面的清洁去污。
34.区别于现有技术,本发明具有以下有益效果:
35.1.本发明中的水性聚合物溶液采用有机硅改性后的聚合物溶液,使得其与 增强纤维之间的浸润性增强,并且使得制得的可剥离式去污膜成膜后的低温 韧性得以增强。
36.2.本发明中通过给水性聚合物溶液中加入硼复合木质素纳米纤维进一步 提高了去污膜的抗断裂性能,并且增强了制得的可剥离式去污膜的中子吸收 能力,可以屏蔽环境辐射剂量。
37.3.本发明中的络合剂采用硫代氨基羧酸盐、有机膦酸盐以及聚丙烯酸盐进 行复合,使可剥离式去污膜的络合容量高,络合稳定常数大,金属离子等被 络合后不容易解离,且耐化学稳定性好,易生物降解。
具体实施方式
38.为详细说明技术方案的技术内容、构造特征、所实现目的及效果,以下 结合具体实施例详予说明。
39.一种可剥离式去污膜,由如下重量份的原料制备:20-65份的有机硅改性 聚氨酯和/或有机硅改性聚乙烯醇,2-7份硼复合木质素纳米短纤维,2-28份 络合剂(硫代氨基羧酸盐、有机膦酸盐以及聚丙烯酸盐按0.1-0.3:1:1-2的 质量比复合)及30-60份去离子水,另外还包括0.01-1.5份消泡剂,0.02-0.8 份分散剂或0.02-1份色素中的一种或几种。
40.本发明制备有机硅改性聚氨酯的方法包括:将重量份为10-18份的聚二元 醇,9-15份的双端双羟基硅油,15-25份的亲水剂,0.2-0.5份的交联剂,140-170 份二异氰酸酯在55-75℃下进行搅拌,所述搅拌时间为25-40min,再给其中加 入0.2-2份催化剂,升温至80-95℃恒温反应1.5-3h;最后给所述混合溶液中 加入1-4份除酸剂,恒温反应20-45min,得到有机硅改性聚氨酯。
41.本发明制备有机硅改性聚乙烯醇的方法包括:将重量份为10-25份的烷氧 基硅烷和45-80份的聚乙烯醇,55-90份的溶剂,6-9份的酸在75-90℃下搅拌 3.5-5h得到有机硅改性聚乙烯醇。
42.本发明制备所述硼复合木质素纳米纤维的方法包括:
43.(a)硼酸改性木质素的制备:配制质量分数为3-5%的硼酸溶液,将硼 酸溶液加热至35-40℃,然后将木质素浸泡于硼酸溶液中1-5h,过滤,所得固 体在100-105℃下干燥2-5h,得到硼酸改性木质素;
44.(b)改性硼粉的制备:将硅烷偶联剂与硼粉按1:10-15的质量比加入 到丙酮和水的混合溶剂中,超声分散12-24h后,于70-80℃的温度下真空烘 干,得到改性硼粉;
45.(c)硼复合木质素纳米纤维前驱体的制备:将步骤(a)制备得到的硼 酸改性木质素用丙酮和水组成的混合溶剂进行溶解,按硼酸改性木质素:改 性硼粉的质量比为5-10:1的比例将改性硼粉在超声分散的条件下混入溶解有 硼酸改性木质素的混合溶剂中,得到硼复合木质素纳米纤维前驱体;
46.(d)静电纺丝法制备硼复合木质素纳米纤维:纺丝电压为20-25kv,针 头到接收铝箔的距离为10-15cm,溶液流速为4-6ml/h。
47.以下具体说明制备本发明实施例所需要的有机硅改性聚氨酯、有机硅改 性聚乙烯醇以及硼复合木质素纳米纤维。
48.有机硅改性聚氨酯的制备:
49.按照表1重量份依次取聚二元醇,双端双羟基硅油,亲水剂丙酮,交联 剂二乙三胺,二异氰酸酯进行搅拌,序号为1的共混溶液在55℃下进行搅拌, 搅拌时间为40min,序号为2的共混溶液在65℃下进行搅拌,搅拌时间为 33min,序号为3的共混溶液在75℃下进行搅拌,搅拌时间为25min,随后分 别按表1中的重量份向三份反应溶液中加入催化剂二丁基二月桂酸锡,序号 为1的共混溶液升温至80℃恒温反应3h,序号为2的共混溶液升温至85℃恒 温反应2h,序号为3的共混溶液升温至95℃恒温反应1.5h;最后分别按表1 中的重量份向三份反应溶液中加入除酸剂三乙胺,序号为1的共混溶液恒温 反应35min,序号为2的共混溶液恒温反应45min,序号为3的共混溶液恒温 反应20min,即可得到3份有机硅改性聚氨酯溶液。
50.表1
[0051][0052][0053]
有机硅改性聚乙烯醇的制备:
[0054]
按照表2重量份分别取烷氧基硅烷,聚乙烯醇,无水乙醇以及醋酸,将 其依次投入配有三口烧瓶的加热装置中,序号为4的共混溶液在75℃下恒温 反应3.5h,序号为5的共混溶液在83℃下恒温反应4.5h,序号为6的共混溶 液在90℃下恒温反应5h,即可得到3份有机硅改性聚乙烯醇溶液。
[0055]
表2
[0056][0057]
硼复合木质素纳米纤维的制备:
[0058]
(a)硼酸改性木质素的制备:配制质量分数为5%的硼酸溶液,将硼酸 溶液加热至38
±
1℃,然后将木质素浸泡于硼酸溶液中5h,过滤,所得固体 在105℃下干燥2h,得到硼酸改性木质素;
[0059]
(b)改性硼粉的制备:将硅烷偶联剂kh-550与硼粉按1:10的质量比 加入到丙酮和水按体积比1:1组成的混合溶剂中,超声分散20h后,于70℃ 的温度下真空烘干,得到改性硼粉;
[0060]
(c)硼复合木质素纳米纤维前驱体的制备:将步骤(a)制备得到的硼 酸改性木质素用丙酮和水按体积比2:1组成的混合溶剂进行溶解,按硼酸改 性木质素:改性硼粉的质量比为8:1的比例将改性硼粉在超声分散的条件下 混入溶解有硼酸改性木质素的混合溶剂中,得到硼复合木质素纳米纤维前驱 体;
[0061]
(d)静电纺丝法制备硼复合木质素纳米纤维:纺丝电压为20kv,针头 到接收铝箔的距离为10cm,溶液流速为4.5ml/h,即得到硼复合木质素纳米 纤维。
[0062]
实施例1
[0063]
按重量份计,将30份序号为1的有机硅改性聚氨酯与40份去离子水混 合均匀,将5份上述制备得到的硼复合木质素纳米纤维、0.01份聚醚改性硅 氧烷、0.5份甲磺酸钠及0.02份白炭黑投入水性聚合物溶液中并进行超声机械 共混5h,再将6份由二甲基二硫代氨基甲酸钠、乙二胺四甲叉磷酸钠及聚丙 烯酸钠按0.3:1:1的质量比组成的复合络合剂投入共混溶液中,并加热至 70℃下反应2h,备用。
[0064]
实施例2
[0065]
按重量份计,将40份序号为2的有机硅改性聚氨酯与50份去离子水混 合均匀,将6份上述制备得到的硼复合木质素纳米纤维、0.01份聚醚改性硅 氧烷、0.5份甲磺酸钠及0.02份白炭黑投入水性聚合物溶液中并进行超声机械 共混6h,再将8份由二甲基二硫代氨基甲酸钠、乙二胺四甲叉磷酸钠及聚丙 烯酸钠按0.1:1:2的质量比组成的复合络合剂投入共混溶液中,并加热至 80℃下反应3h,备用。
[0066]
实施例3
[0067]
按重量份计,将30份序号为3的有机硅改性聚氨酯与40份去离子水混 合均匀,将5份上述制备得到的硼复合木质素纳米纤维、0.01份聚醚改性硅 氧烷、0.5份甲磺酸钠及0.02份白炭黑投入水性聚合物溶液中并进行超声机械 共混6h,再将10份由二甲基二硫代氨基甲酸钠、乙二胺四甲叉磷酸钠及聚羟 基丙烯酸钠按0.2:1:1的质量比组成的复合络合剂投入共混溶液中,并加热 至65℃下反应3h,备用。
[0068]
实施例4
[0069]
按重量份计,将40份序号为4的有机硅改性聚乙烯醇与30份去离子水 混合均匀,将6份上述制备得到的硼复合木质素纳米纤维、0.01份聚醚改性 硅氧烷、0.5份氨基丙胺二油酸酯及0.02份白炭黑投入水性聚合物溶液中并进 行超声机械共混6h,再将15份由二甲基二硫代氨基甲酸钠、乙二胺四甲叉磷 酸钠及聚丙烯酸钠按0.2:1:2的质量比组成的复合络合剂投入共混溶液中, 并加热至70℃下反应1.5h,备用。
[0070]
实施例5
[0071]
按重量份计,将60份序号为5的有机硅改性聚乙烯醇与50份去离子水 混合均匀,将7份上述制备得到的硼复合木质素纳米纤维、0.01份聚醚改性 硅氧烷、0.5份氨基丙胺二油酸酯及0.02份白炭黑投入水性聚合物溶液中并进 行超声机械共混6h,再将10份由二甲基二硫代氨基甲酸钠、乙二胺四甲叉磷 酸钠及聚丙烯酸钠按0.3:1:2的质量比组成的复合络合剂投入共混溶液中, 并加热至75℃下反应2h,备用。
[0072]
实施例6
[0073]
按重量份计,将50份序号为6的有机硅改性聚乙烯醇与50份去离子水 混合均匀,将7份上述制备得到的硼复合木质素纳米纤维、0.01份聚醚改性 硅氧烷、0.5份甲磺酸钠及
0.02份白炭黑投入水性聚合物溶液中并进行超声机 械共混6h,再将15份由二乙基二硫代氨基甲酸钠、乙二胺四甲叉磷酸钠及聚 羟基丙烯酸钠按0.3:1:1的质量比组成的复合络合剂投入共混溶液中,并加 热至75℃下反应2.5h,备用。
[0074]
对比例1
[0075]
将实施例1中有机硅改性聚氨酯替换为市售水性聚氨酯(购自万华化学), 其余组分、用量及制备方法与实施例1相同。
[0076]
对比例2
[0077]
将实施例4中有机硅改性聚乙烯醇替换为市售聚乙烯醇(购自万瑾贸易 (上海)有限公司),其余组分、用量及制备方法与实施例4相同。
[0078]
对比例3
[0079]
与实施例6的区别在于不添加硼复合木质素纳米纤维。
[0080]
力学性能测试
[0081]
将实施例1-6及对比例1-3制备的原料搅拌均匀,分别喷涂在不锈钢表面, 喷涂量为1kg/m2,在室温下干燥备用,涂膜完全干燥后将其轻轻剥起备用, 在空气湿度40%、温度5℃计算成膜时间、成膜厚度拉伸强度以及断裂伸长率。 成膜时间按照gb/t 1728、成膜厚度按照gb/t 13452.2、拉伸强度和断裂伸长 率按照gb/t 13022-1991对涂膜进行测试。
[0082]
表3
[0083][0084][0085]
由表3可知,本发明制备的可剥离式去污膜在低温下的成膜时间均在8h 之内,由此可见本发明制备的可剥离式去污膜成膜时间短,干燥速度快,在 低温下仍有着优异的拉伸强度以及断裂伸长率,使可剥离式去污膜成膜后的 韧性得以增强,避免了去污膜在低温环境下的剥离过程中产生撕裂现象。
[0086]
去污效果测试:
[0087]
取9块10*10cm的钢板,使用表面污染测试仪(fj-2207α,β)测试钢 板的本底值,测试3次取平均值,记为a0;然后将1g/l的硝酸双氧铀溶液均 匀喷洒在钢板表面,待其在自然环境中干燥后得到铀污染钢板,测量铀污染 钢板的放射性污染值,测试3次取平均值,记为a1;再将上述实施例1-6及 对比例1-3制备得到的去污膜组合物分别均匀喷洒在铀污染的钢板表面,待其 干燥成膜后,剥离揭膜,完成去污过程,测试去污后钢板表面剩下的放射性 污染值,测试3次取平均值,记为a2;计算去污率:结果见下表
4。
[0088]
表4
[0089][0090][0091]
由上表4可知,本发明制备的去污膜去污率均高达90%以上,由此可见 本发明的去污膜具有优异的去污性能。
[0092]
尽管已经对上述各实施例进行了描述,但本领域内的技术人员一旦得知 了基本创造性概念,则可对这些实施例做出另外的变更和修改,所以以上所 述仅为本发明的实施例,并非因此限制本发明的专利保护范围,凡是利用本 发明说明书及内容所作的等效结构或等效流程变换,或直接或间接运用在其 他相关的技术领域,均同理包括在本发明的专利保护范围之内。