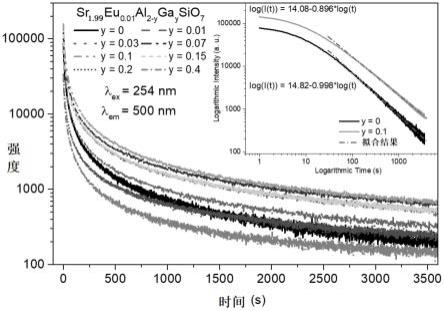
1.本发明涉及稀土长余辉发光材料技术领域,特别涉及一种铕、镱共掺杂硅铝酸盐的长余辉发光材料及其制备方法和应用。
背景技术:2.长余辉发光材料可储存光能,再以光的形式释放能量,在家庭装饰、应急指示、光电子器件和国防军事等方面有广泛的应用。目前,商用的长余辉材料有sral2o4:eu
2+
,dy
3+
、caal2o4:eu
2+
,nd
3+
和y2o2s:eu
3+
,mg
2+
,ti
4+
等,余辉强度和持续时间都较佳。但硫化物长余辉材料结构稳定性较差,被紫外光长时间照射后出现变黑;铝酸盐长余辉材料的耐水性较差,在实际应用中这些材料经包覆来改善。相对地,硅酸盐长余辉材料物化稳定性较佳,如:已报道的sr2znsi2o7:eu
2+
,dy
3+
、(sr,ba)2mgsi2o8:eu
2+
,dy
3+
和ba4(si3o8)2:eu
2+
,dy
3+
等硅酸盐长余辉材料,发光波长主要在蓝光波段,余辉时间仅仅为3小时左右。所以余辉持续时间长的绿、红光硅酸盐长余辉材料必须有所探索。
3.无机长余辉发光材料大多选择具有f-d跃迁的ce
3+
和eu
2+
为激活离子,其发光量子效率较高。此外,材料通过引入陷阱能级、改变陷阱密度与深度,可有效优化余辉性能,但缺少翔实理论和统一的机制模型作指导,大多选择了dy
3+
为共掺杂离子,制约着长余辉材料的拓展。因此,开发一种具有高亮、持续和eu
2+
长波段发光特征的其他稀土共掺杂硅酸盐余辉材料具有重要的应用价值和研究意义。
技术实现要素:4.本发明克服了现有技术中的缺点,提供了一种铕、镱共掺杂硅酸盐绿光长余辉材料及其制备方法和应用,余辉时间持续,余辉亮度更亮。
5.为了解决上述技术问题,本发明是通过以下技术方案实现的:
6.一种铕、镱共掺杂硅酸盐绿光长余辉材料,其特征在于,化学组成式为:sr
1.99-2x
eu
0.01
yb
x
na
x
al
2-y
gaysio7,其中,0.003≤x≤0.007,0≤y≤0.4,na
+
离子为电荷补偿离子,yb
3+
为优选的余辉增强剂,绿色余辉发光来自eu
2+
发光,经ga
3+
/al
3+
调控,余辉强度增强,余辉时间延长,在紫外-蓝光(激发光波长范围为250~450nm)激发后,撤去光源,可保持较长时间的绿黄色余辉发光,当所述x的数值在0.003~0.007时,所述长余辉发光材料的余辉性能较佳,当所述激发波长从250nm到450nm变化时,所述发光材料的余辉强度在逐渐增强,450nm激发光充能时,余辉强度最强,余辉持续时间最长。
7.铕、镱共掺杂硅酸盐绿光长余辉材料的制备方法,包括以下步骤:
8.s1、按照化学组成式计量比取锶盐、二氧化硅、三氧化二铝、三氧化二镓、三氧化二铕、三氧化二镱和钠盐进行混合,得混合物,再往混合物中加入溶剂进行研磨,干燥后备用;
9.s2、将s1干燥后的混合物在空气中进行高温焙烧处理,冷却后,在还原气氛条件下进行二次高温焙烧处理,冷却后,即可得到所述长余辉材料。
10.进一步,步骤s1中,所述锶盐为碳酸锶或氧化锶,所述钠盐为碳酸钠或硼酸钠,作
为电荷补偿剂。
11.进一步,步骤s1中,所述混合的过程中还加入硼酸,加入的硼酸含量为混合物的1-3%摩尔分数。
12.进一步,所述溶剂为无水乙醇。
13.进一步,所述还原气氛为一氧化碳或不含氢气的其他还原气。
14.进一步,所述高温焙烧处理的具体过程为:以3~5℃/min的升温速率,从室温升温到850~1050℃,焙烧4~6h;二次高温焙烧过程:以4~6℃/min的升温速率,从室温升温到1320~1390℃,然后这个温度范围下继续焙烧2~4h。
15.本发明的第二个目的在于提供长余辉材料在交通运输、应急消防和装饰中的应用。
16.优选地,在地下隧道、应急指示牌和发光瓷砖中应用。
17.与现有技术相比,本发明的有益效果是:
18.(1)本发明发光材料以eu
2+
稀土离子为激活剂,钠盐为电荷补偿剂,通过组成元素ga
3+
和共掺杂离子yb
3+
合适地调控使sr2al2sio7:eu
2+
,ga
3+
材料的余辉时间持续,余辉亮度更亮。
19.(2)本发明以硅酸盐为基质,相比目前的铝酸盐和硫化物长余辉材料的物化稳定性更佳,制备方法采用高温固相法合成,操作简单易行,适应工业化生产。
附图说明
20.下面结合附图和实施例对本发明做进一步的说明。
21.图1为实施例1的sr2al2sio7基质的高分辨x射线粉末衍射图和rietveld精修结果。
22.图2为实施例2~9的sr2al
2-y
gaysio7:eu
2+
材料的x射线粉末衍射图和上述计算的sr2al2sio7基质标准卡。
23.图3为实施例2的sr2al2sio7:eu
2+
材料的常温激发和发射光谱。
24.图4为实施例2~9的sr2al
2-y
gaysio7:eu
2+
材料的常温发射光谱,插图为优选的y=0和0.4样品的cie色坐标。
25.图5为实施例2~9在90k条件下充能5min后,sr
1.99
eu
0.01
al
2-y
gaysio7(y=0~0.4)材料的热释光谱。
26.图6为实施例2~9在常温条件下充能5min后,sr
1.99
eu
0.01
al
2-y
gaysio7(y=0~0.4)材料的热释光谱。
27.图7为实施例2~9在常温条件下充能5min后,sr
1.99
eu
0.01
al
2-y
gaysio7(y=0~0.4)材料的余辉寿命曲线。
28.图8为实施例10~16在常温条件下充能5min后,sr
1.99
eu
0.01
yb
0.005
al
2-y
gaysio7(y=0~0.2)材料的余辉寿命曲线,插图为y=0和0.1时的拟合结果。
29.图9为实施例14在常温条件下,通过不同波长的激发光充能5min后,sr
1.985
eu
0.01
yb
0.005
al
1.9
ga
0.1
sio7材料的余辉寿命曲线。
具体实施方式
30.以下对本发明的优选实施例进行说明,应当理解,此处所描述的优选实施例仅用
于说明和解释本发明,并不用于限定本发明。
31.除非特别说明,以下实施例所用试剂和材料均为市购。
32.实施例1
33.sr2al2sio7基质的制备方法,包括如下步骤:
34.称取碳酸锶(srco3)0.5905g,二氧化硅(sio2)0.1202g,三氧化二铝(al2o3)0.2039g和硼酸(h3bo3)0.0200g,置于玛瑙研钵中,加入5~10ml无水乙醇,研磨20min,混合均匀并干燥后装入刚玉坩埚中,并将其置于箱式炉中,用300min从常温逐步升温到1350℃,在空气中焙烧,恒定温度下继续焙烧3小时,随后样品放在炉子里自然冷却退火至室温,将样品取出研磨得到产物。
35.实施例2
36.sr
1.98
eu
0.01
al2sio7材料的制备方法:称取碳酸锶(srco3)0.5876g,二氧化硅(sio2)0.1202g,三氧化二铝(al2o3)0.2039g,硼酸(h3bo3)0.0200g和三氧化二铕(eu2o3)0.0035g,置于玛瑙研钵中,加入5~10ml无水乙醇,研磨20min,混合均匀并干燥后装入刚玉坩埚中,并将其置于箱式炉中,用240min从常温逐步升温到950℃,在空气中焙烧,恒定温度下继续焙烧5小时,随后样品放在炉子里自然冷却退火至室温;用300min从常温逐步升温到1350℃,在热碳还原气氛(一氧化碳)下焙烧3小时,随后样品放在炉子里自然冷却退火至室温,将样品取出研磨得到产物。
37.实施例3
38.sr
1.99
eu
0.01
al
1.99
ga
0.01
sio7材料的制备方法:称取碳酸锶(srco3)0.5876g,三氧化二镓(ga2o3)0.0019g,二氧化硅(sio2)0.1202g,三氧化二铝(al2o3)0.2029g,硼酸(h3bo3)0.0200g和三氧化二铕(eu2o3)0.0035g,置于玛瑙研钵中,加入5~10ml无水乙醇,研磨20min,混合均匀并干燥后装入刚玉坩埚中,并将其置于箱式炉中,用240min从常温逐步升温到950℃,在空气中焙烧,恒定温度下继续焙烧5小时,随后样品放在炉子里自然冷却退火至室温;用300min从常温逐步升温到1350℃,在热碳还原气氛(一氧化碳)下焙烧3小时,随后样品放在炉子里自然冷却退火至室温,将样品取出研磨得到产物。
39.实施例4
40.sr
1.99
eu
0.01
al
1.97
ga
0.03
sio7材料的制备方法:称取碳酸锶(srco3)0.5876g,三氧化二镓(ga2o3)0.0056g,二氧化硅(sio2)0.1202g,三氧化二铝(al2o3)0.2009g,硼酸(h3bo3)0.0200g和三氧化二铕(eu2o3)0.0035g,置于玛瑙研钵中,加入5~10ml无水乙醇,研磨20min,混合均匀并干燥后装入刚玉坩埚中,并将其置于箱式炉中,用240min从常温逐步升温到950℃,在空气中焙烧,恒定温度下继续焙烧5小时,随后样品放在炉子里自然冷却退火至室温;用300min从常温逐步升温到1350℃,在热碳还原气氛(一氧化碳)下焙烧3小时,随后样品放在炉子里自然冷却退火至室温,将样品取出研磨得到产物。
41.实施例5
42.sr
1.99
eu
0.01
al
1.93
ga
0.07
sio7材料的制备方法:称取碳酸锶(srco3)0.5876g,三氧化二镓(ga2o3)0.0131g,二氧化硅(sio2)0.1202g,三氧化二铝(al2o3)0.1968g,硼酸(h3bo3)0.0200g和三氧化二铕(eu2o3)0.0035g,置于玛瑙研钵中,加入5~10ml无水乙醇,研磨20min,混合均匀并干燥后装入刚玉坩埚中,并将其置于箱式炉中,用240min从常温逐步升温到950℃,在空气中焙烧,恒定温度下继续焙烧5小时,随后样品放在炉子里自然冷却退火
至室温;用300min从常温逐步升温到1350℃,在热碳还原气氛(一氧化碳)下焙烧3小时,随后样品放在炉子里自然冷却退火至室温,将样品取出研磨得到产物。
43.实施例6
44.sr
1.99
eu
0.01
al
1.9
ga
0.1
sio7材料的制备方法:称取碳酸锶(srco3)0.5876g,三氧化二镓(ga2o3)0.0187g,二氧化硅(sio2)0.1202g,三氧化二铝(al2o3)0.1937g,硼酸(h3bo3)0.0200g和三氧化二铕(eu2o3)0.0035g,置于玛瑙研钵中,加入5~10ml无水乙醇,研磨20min,混合均匀并干燥后装入刚玉坩埚中,并将其置于箱式炉中,用240min从常温逐步升温到950℃,在空气中焙烧,恒定温度下继续焙烧5小时,随后样品放在炉子里自然冷却退火至室温;用300min从常温逐步升温到1350℃,在热碳还原气氛(一氧化碳)下焙烧3小时,随后样品放在炉子里自然冷却退火至室温,将样品取出研磨得到产物。
45.实施例7
46.sr
1.99
eu
0.01
al
1.85
ga
0.15
sio7材料的制备方法:称取碳酸锶(srco3)0.5876g,三氧化二镓(ga2o3)0.0281g,二氧化硅(sio2)0.1202g,三氧化二铝(al2o3)0.1886g,硼酸(h3bo3)0.0200g和三氧化二铕(eu2o3)0.0035g,置于玛瑙研钵中,加入5~10ml无水乙醇,研磨20min,混合均匀并干燥后装入刚玉坩埚中,并将其置于箱式炉中,用240min从常温逐步升温到950℃,在空气中焙烧,恒定温度下继续焙烧5小时,随后样品放在炉子里自然冷却退火至室温;用300min从常温逐步升温到1350℃,在热碳还原气氛(一氧化碳)下焙烧3小时,随后样品放在炉子里自然冷却退火至室温,将样品取出研磨得到产物。
47.实施例8
48.sr
1.99
eu
0.01
al
1.8
ga
0.2
sio7材料的制备方法:称取碳酸锶(srco3)0.5876g,三氧化二镓(ga2o3)0.0375g,二氧化硅(sio2)0.1202g,三氧化二铝(al2o3)0.1835g,硼酸(h3bo3)0.0200g和三氧化二铕(eu2o3)0.0035g,置于玛瑙研钵中,加入5~10ml无水乙醇,研磨20min,混合均匀并干燥后装入刚玉坩埚中,并将其置于箱式炉中,用240min从常温逐步升温到950℃,在空气中焙烧,恒定温度下继续焙烧5小时,随后样品放在炉子里自然冷却退火至室温;用300min从常温逐步升温到1350℃,在热碳还原气氛(一氧化碳)下焙烧3小时,随后样品放在炉子里自然冷却退火至室温,将样品取出研磨得到产物。
49.实施例9
50.sr
1.99
eu
0.01
al
1.6
ga
0.4
sio7材料的制备方法:称取碳酸锶(srco3)0.5876g,三氧化二镓(ga2o3)0.0750g,二氧化硅(sio2)0.1202g,三氧化二铝(al2o3)0.1631g,硼酸(h3bo3)0.0200g和三氧化二铕(eu2o3)0.0035g,置于玛瑙研钵中,加入5~10ml无水乙醇,研磨20min,混合均匀并干燥后装入刚玉坩埚中,并将其置于箱式炉中,用240min从常温逐步升温到950℃,在空气中焙烧,恒定温度下继续焙烧5小时,随后样品放在炉子里自然冷却退火至室温;用300min从常温逐步升温到1350℃,在热碳还原气氛(一氧化碳)下焙烧3小时,随后样品放在炉子里自然冷却退火至室温,将样品取出研磨得到产物。
51.实施例10
52.sr
1.98
eu
0.01
yb
0.005
na
0.005
al2sio7材料的制备方法:称取碳酸锶(srco3)0.5846g,二氧化硅(sio2)0.1202g,三氧化二铝(al2o3)0.2039g,硼酸(h3bo3)0.0200g,碳酸钠(na2co3)0.0005g,三氧化二铕(eu2o3)0.0035g和三氧化二镱(yb2o3)0.0020g,置于玛瑙研钵中,加入5~10ml无水乙醇,研磨20min,混合均匀并干燥后装入刚玉坩埚中,并将其置于箱式炉中,
用240min从常温逐步升温到950℃,在空气中焙烧,恒定温度下继续焙烧5小时,随后样品放在炉子里自然冷却退火至室温;用300min从常温逐步升温到1350℃,在热碳还原气氛(一氧化碳)下焙烧3小时,随后样品放在炉子里自然冷却退火至室温,将样品取出研磨得到产物。
53.实施例11
54.sr
1.98
eu
0.01
yb
0.005
na
0.005
al
1.99
ga
0.01
sio7材料的制备方法:称取碳酸锶(srco3)0.5846g,三氧化二镓(ga2o3)0.0019g,二氧化硅(sio2)0.1202g,三氧化二铝(al2o3)0.2029g,硼酸(h3bo3)0.0200g,碳酸钠(na2co3)0.0005g,三氧化二铕(eu2o3)0.0035g和三氧化二镱(yb2o3)0.0020g,置于玛瑙研钵中,加入5~10ml无水乙醇,研磨20min,混合均匀并干燥后装入刚玉坩埚中,并将其置于箱式炉中,用240min从常温逐步升温到950℃,在空气中焙烧,恒定温度下继续焙烧5小时,随后样品放在炉子里自然冷却退火至室温;用300min从常温逐步升温到1350℃,在热碳还原气氛(一氧化碳)下焙烧3小时,随后样品放在炉子里自然冷却退火至室温,将样品取出研磨得到产物。
55.实施例12
56.sr
1.98
eu
0.01
yb
0.005
na
0.005
al
1.97
ga
0.03
sio7材料的制备方法:sr
1.98
eu
0.01
yb
0.005
na
0.005
al
1.99
ga
0.01
sio7材料的制备方法:称取碳酸锶(srco3)0.5846g,三氧化二镓(ga2o3)0.0056g,二氧化硅(sio2)0.1202g,三氧化二铝(al2o3)0.2009g,硼酸(h3bo3)0.0200g,碳酸钠(na2co3)0.0005g,三氧化二铕(eu2o3)0.0035g和三氧化二镱(yb2o3)0.0020g,置于玛瑙研钵中,加入5~10ml无水乙醇,研磨20min,混合均匀并干燥后装入刚玉坩埚中,并将其置于箱式炉中,用240min从常温逐步升温到950℃,在空气中焙烧,恒定温度下继续焙烧5小时,随后样品放在炉子里自然冷却退火至室温;用300min从常温逐步升温到1350℃,在热碳还原气氛(一氧化碳)下焙烧3小时,随后样品放在炉子里自然冷却退火至室温,将样品取出研磨得到产物。
57.实施例13
58.sr
1.98
eu
0.01
yb
0.005
na
0.005
al
1.93
ga
0.07
sio7材料的制备方法:称取碳酸锶(srco3)0.5846g,三氧化二镓(ga2o3)0.0131g,二氧化硅(sio2)0.1202g,三氧化二铝(al2o3)0.1968g,硼酸(h3bo3)0.0200g,碳酸钠(na2co3)0.0005g,三氧化二铕(eu2o3)0.0035g和三氧化二镱(yb2o3)0.0020g,置于玛瑙研钵中,加入5~10ml无水乙醇,研磨20min,混合均匀并干燥后装入刚玉坩埚中,并将其置于箱式炉中,用240min从常温逐步升温到950℃,在空气中焙烧,恒定温度下继续焙烧5小时,随后样品放在炉子里自然冷却退火至室温;用300min从常温逐步升温到1350℃,在热碳还原气氛(一氧化碳)下焙烧3小时,随后样品放在炉子里自然冷却退火至室温,将样品取出研磨得到产物。
59.实施例14
60.sr
1.98
eu
0.01
yb
0.005
na
0.005
al
1.9
ga
0.1
sio7材料的制备方法:称取碳酸锶(srco3)0.5846g,三氧化二镓(ga2o3)0.0187g,二氧化硅(sio2)0.1202g,三氧化二铝(al2o3)0.1937g,硼酸(h3bo3)0.0200g,碳酸钠(na2co3)0.0005g,三氧化二铕(eu2o3)0.0035g和三氧化二镱(yb2o3)0.0020g,置于玛瑙研钵中,加入5~10ml无水乙醇,研磨20min,混合均匀并干燥后装入刚玉坩埚中,并将其置于箱式炉中,用240min从常温逐步升温到950℃,在空气中焙烧,恒定温度下继续焙烧5小时,随后样品放在炉子里自然冷却退火至室温;用300min从常温逐步升温到1350℃,在热碳还原气氛(一氧化碳)下焙烧3小时,随后样品放在炉子里自
然冷却退火至室温,将样品取出研磨得到产物。
61.实施例15
62.sr
1.98
eu
0.01
yb
0.005
na
0.005
al
1.85
ga
0.15
sio7材料的制备方法:称取碳酸锶(srco3)0.5846g,三氧化二镓(ga2o3)0.0281g,二氧化硅(sio2)0.1202g,三氧化二铝(al2o3)0.1886g,硼酸(h3bo3)0.0200g,碳酸钠(na2co3)0.0005g,三氧化二铕(eu2o3)0.0035g和三氧化二镱(yb2o3)0.0020g,置于玛瑙研钵中,加入5~10ml无水乙醇,研磨20min,混合均匀并干燥后装入刚玉坩埚中,并将其置于箱式炉中,用240min从常温逐步升温到950℃,在空气中焙烧,恒定温度下继续焙烧5小时,随后样品放在炉子里自然冷却退火至室温;用300min从常温逐步升温到1350℃,在热碳还原气氛(一氧化碳)下焙烧3小时,随后样品放在炉子里自然冷却退火至室温,将样品取出研磨得到产物。
63.实施例16
64.sr
1.98
eu
0.01
yb
0.005
na
0.005
al
1.8
ga
0.2
sio7材料的制备方法:称取碳酸锶(srco3)0.5846g,三氧化二镓(ga2o3)0.0375g,二氧化硅(sio2)0.1202g,三氧化二铝(al2o3)0.1835g,硼酸(h3bo3)0.0200g,碳酸钠(na2co3)0.0005g,三氧化二铕(eu2o3)0.0035g和三氧化二镱(yb2o3)0.0020g,置于玛瑙研钵中,加入5~10ml无水乙醇,研磨20min,混合均匀并干燥后装入刚玉坩埚中,并将其置于箱式炉中,用240min从常温逐步升温到950℃,在空气中焙烧,恒定温度下继续焙烧5小时,随后样品放在炉子里自然冷却退火至室温;用300min从常温逐步升温到1350℃,在热碳还原气氛(一氧化碳)下焙烧3小时,随后样品放在炉子里自然冷却退火至室温,将样品取出研磨得到产物。
65.测试实验
66.1、对以上实施例采用如下相关测试方法进行测试:
67.(1)x-射线粉末衍射
68.样品的相纯度是rigaku d-max 2200 vpc x射线衍射仪在40kv和26ma的cu kα辐射条件下检测。用于rietveld精修的高质量xrd数据是bruker d8 x射线衍射仪在40kv和40ma的cu kα辐射条件下采集,2θ范围为5
°
~110
°
,扫描速度是0.6
°
/min。
69.(2)常温荧光光谱及余辉曲线
70.激发、发射光谱以及余辉衰减曲线是在edinburgh fls1000光谱仪上收集。450w xe900氙灯是稳态激发光源,用于收集激发、发射光谱;8w hg灯是充能光源,用于收集余辉寿命曲线。
71.(3)低温与常温热释光谱
72.充能温度在90k的热释曲线是在tosl-3ds光谱仪(guangzhou-radiation science and technology)上收集,降温用液氮灌入冷却控温装置,探测器为ccd探测器(ocean optics qe65 pro);充能温度在常温的热释曲线是在sl18 tl&osl reader光谱仪(guangzhou-radiation science and technology)上收集,探测器为滨松r928 pmt。
73.2、测试结果如下:
74.图1的sr2al2sio7属于黄长石结构,基于标准卡的结构,通过在topas 4.1版软件精修x-射线粉末衍射谱图。标准卡来源于无机晶体结构数据库(icsd)的sr2al2sio7晶体学信息文件(icsd号:30698)。精修结果进一步证明了sr2al2sio7基质属于黄长石结构。
75.图2的sr
1.99
eu
0.01
al
2-y
gaysio7(y=0~0.4)样品的xrd数据,与精修结果一一对应,
说明了合成的eu
2+
掺杂材料均为单一纯相。
76.图3的sr
1.99
eu
0.01
al2sio7材料的激发与发射光谱图,eu
2+
发射是主要的,含有少量未还原eu
3+
的发光,eu
2+
发射峰极值在515nm,为绿色发光。
77.图4的sr
1.99
eu
0.01
al
2-y
gaysio7(y=0.01~0.4)样品的发射光谱图,eu
2+
发射峰极值随ga
3+
掺杂而变化,但是变化幅度较小,为绿色发光。
78.图5的sr
1.99
eu
0.01
al
2-y
gaysio7(y=0~0.4)样品在90k下充能5min后的热释光谱图。材料的热释峰在100-600k都有分布,其中主要集中在低温段,极值约为200k;随着ga
3+
/al
3+
比例调控,低温段热释峰强度有明显增长,在y=0.1时达到最大值。
79.图6的sr
1.99
eu
0.01
al
2-y
gaysio7(y=0~0.4)样品在常温下充能5min后的热释光谱图。热释峰在325-600k都有分布,说明常温下充能,材料能储存能量;热释峰强度和极值都可随着ga
3+
/al
3+
比例改变而改变。
80.图7的sr
1.99
eu
0.01
al
2-y
gaysio7(y=0~0.4)样品在常温下充能5min后的余辉强度衰减曲线。检测波长为500nm,是eu
2+
发射峰位置,余辉主要来源于eu
2+
发光。随着ga
3+
/al
3+
比例增加,余辉初始强度有所增强,衰减速率也变慢。在y=0.1时,余辉强度衰减效果最佳,是y=0时的2倍,余辉时间是y=0时的4倍;衰减1h后,余辉强度依然很强,相比y=0的情况强了约4倍。
81.图8的sr
1.98
eu
0.01
yb
0.005
na
0.005
al
2-y
gaysio7(y=0~0.2)样品在常温下充能5min后的余辉强度衰减曲线,插图为归一化衰减曲线。相对没有共掺杂情况,共掺杂yb
3+
后的初始余辉强度相对地增强,余辉衰减也变缓慢;随着ga
3+
/al
3+
比例增加,余辉初始强度先增强后减弱,在y=0.07时,余辉强度最佳;衰减速率最慢的是y=0.1的样品。
82.图9的sr
1.98
eu
0.01
yb
0.005
na
0.005
al
1.9
ga
0.1
sio7样品在常温下通过不同波长的激发光充能5min后的余辉强度衰减曲线。随着激发波长变长,考虑到激发光波长与eu
2+
激发峰位置越来越匹配,余辉初始强度逐渐增强,说明选择紫外-蓝光可以对材料进行充能,都能产生eu
2+
余辉发光。
83.综上结果,sr2al
2-y
gaysio7:eu
2+
材料经yb
3+
掺杂和ga
3+
的调控后,具有强度较强、持续时间较长的余辉发光特征。优选的sr
1.98
eu
0.01
yb
0.005
na
0.005
al
1.9
ga
0.1
sio7材料的综合性能最佳,相比目前的大部分硅酸盐无机长余辉发光材料具有较强的余辉强度和较长余辉时间,在应急消防和交通运输等弱光照明领域具有重要的意义。
84.本发明长余辉发光材料以具有黄长石结构的sr2(al,ga)2sio7为基质,该基质具有一种晶体学sr
2+
格位可被eu
2+
离子占据。eu
2+
离子发光属于宇称允许的5d-4f跃迁,具有较高量子效率、可调控发射波长的特征,所以eu
2+
掺杂sr2(al,ga)2sio7长余辉发光材料在高效长余辉发光方面具有理论基础。其次,sr2(al,ga)2sio7具有较合适的sr
2+
配位环境,eu
2+
在基质晶格中表现绿黄光的发射,发射峰极大值在520nm左右。eu
2+
掺杂sr2(al,ga)2sio7材料在不同的al
3+
/ga
3+
比例下,eu
2+
发射峰极值变化较小,光色变化较小。再次,eu
2+
的最低5d能级受sr2(al,ga)2sio7基质带隙的影响较大,所以eu
2+
余辉发光性能受材料的带隙影响较大。因此,通过优化al
3+
/ga
3+
比例并引入陷阱能级yb
3+
,本发明的sr2(al,ga)2sio7:eu
2+
,yb
3+
材料的长余辉发光强度更强、余辉时间更持续,在消防应急和交通运输等领域具有潜在的应用,优选地,在地下隧道、应急指示牌和发光瓷砖中应用。
85.最后应说明的是:以上仅为本发明的优选实施例而已,并不用于限制本发明,尽管
参照实施例对本发明进行了详细的说明,对于本领域的技术人员来说,其依然可以对前述各实施例所记载的技术方案进行修改,或者对其中部分技术特征进行等同替换,但是凡在本发明的精神和原则之内,所作的任何修改、等同替换、改进等,均应包含在本发明的保护范围之内。