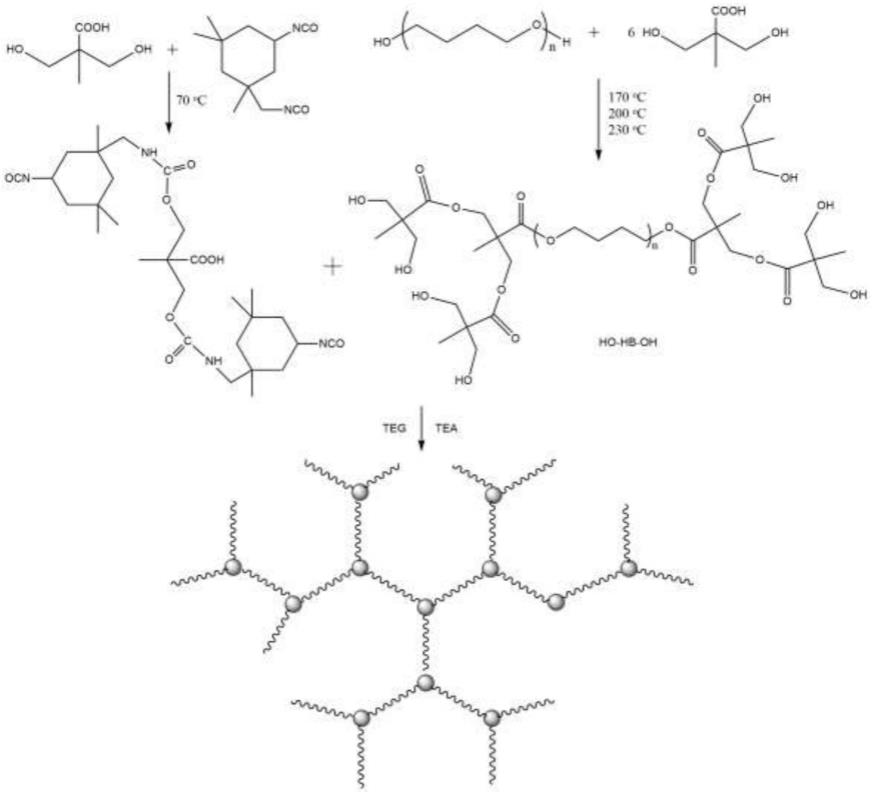
1.本发明涉及海洋防污技术领域,尤其涉及一种基于微纳聚水凝胶的海洋防污涂料用防污树脂及其制备方法。
背景技术:2.在海洋经济和海运事业的发展历程中,海洋生物污损问题持续地困扰着人们。海洋生物污损不仅会增加船舶航行的阻力和燃料的消耗,加快船体材料的腐蚀和降解,而且会破坏水域的生态平衡。英国国际油漆公司曾对船底污损与燃料的增耗进行过统计:若船底污损5%,燃耗将增10%;若船底污损大于50%,燃耗将增40%以上。
3.自2008年1月1日“特效武器”有机锡防污涂料被全面禁用以后,逐渐形成了以丙烯酸铜/锌/硅树脂为载体,氧化亚铜为主防污剂,有机小分子防污剂为辅防污剂的主流涂料复配体系。然而,这类防污体系中,载体自身的防污效果较差,需要添加较多的防污剂,在长期使用下,防污剂的毒性会对海洋环境和生态造成破坏。
4.例如,专利cn201511017972.2公开了一种自抛光防污漆及其制备方法,在100质量份的防污漆中,固体计树脂18~24份,防污剂50~55份,石墨烯微片0.5~1.5份,颜填料3~6份,分散剂1~2份,有机膨润土1~2份,余量为有机溶剂;其中,树脂由羟基丙烯酸树脂、丙烯酸锌树脂以及松香组成;防污剂由吡啶硫酮铜、4,5-二氯-2-正辛基-4-异噻唑啉-3-酮、氧化亚铜和氧化锌组成。该防污漆虽然避免了有机锡的使用,但有机小分子辅防污剂的用量为6%,主防污剂氧化亚铜的用量高达30~35%,仍会对海洋生态环境造成破坏,难以满足新环境下环保型防污涂料的发展需求。
技术实现要素:5.为了解决现有的海洋防污涂料中防污剂用量过大的技术问题,本发明提供了一种基于微纳聚水凝胶的海洋防污涂料用防污树脂及其制备方法。本发明将具有自抛光能力的主体树脂与能够迁移到涂层表面形成水凝胶层的辅助树脂相配合,能发挥较好的防污作用,并具有较长的防污期效,因而能减少防污剂的使用。
6.本发明的具体技术方案为:第一方面,本发明提供了一种基于微纳聚水凝胶的海洋防污涂料用防污树脂,包括主体树脂,以及以微纳态的形式分散在所述主体树脂中的辅助树脂;所述辅助树脂为具有吸水溶胀性的亲水性树脂;所述主体树脂为自抛光树脂;所述辅助树脂的亲水性高于主体树脂。
7.在由海洋防污涂料涂覆后形成的防污涂层中,主体树脂构成涂层的主体结构,辅助树脂以微纳态的形式分散于其中。在与海水接触后,亲水性较强的微纳态辅助树脂会逐渐迁移到涂层表面,并在迁移过程中不断吸水溶胀形成微纳聚水凝胶,最终在涂层表面形成光滑的水凝胶膜,发挥防止生物附着的作用。虽然水凝胶膜能在一定程度上提高涂层的
防污效果,但在长期与海水接触的过程中,水凝胶膜会逐渐降解,而本发明采用了自抛光树脂,在海水的作用下,涂层表面由辅助树脂形成的水凝胶膜和表层的主体树脂会逐渐降解脱落,从而使涂层内部的辅助树脂被进一步释放,在涂层表面形成新的水凝胶膜,继续发挥防污作用。
8.通过上述方式,本发明的防污树脂能发挥较好的防污作用,且具有较长的防污期效,能够减小海洋防污涂料中防污剂的使用量,从而减小防污剂对海洋环境和生态的破坏。经试验,当将本发明的防污树脂用于海洋防污涂料中时,无需向涂料中添加氧化亚铜,仅添加5~14wt%的有机小分子辅防污剂,即可发挥较好的防污效果。
9.此外,在本发明的防污树脂中,由于辅助树脂以微纳态的形式存在于主体树脂中,因而与主体树脂之间的分子链缠结较少,有利于辅助树脂迁移到涂层表面,同时吸水形成表面水凝胶层以发挥防止生物附着的作用。
10.作为优选,所述防污树脂还包括微纳促进剂;所述微纳促进剂为两亲性分子。
11.微纳促进剂能够促进辅助树脂内部形成亲水微区和疏水微区,使涂层具有更好的防污效果,具体机制如下:在辅助树脂迁移到主体树脂表面的过程中,亲水微区能够吸水溶胀,最终在涂层表面形成水凝胶层,发挥润滑防污作用;水凝胶层内部分子链之间并非通过共价键相连,与水接触时易被抛光磨蚀,而疏水微区与水接触较少,抛光速度较慢,因而能防止水凝胶层被过快地磨抛,从而延长涂层的防污期效。
12.此外,利用微纳促进剂的两亲性,配合辅助树脂和主体树脂的亲疏水性差异,还有助于在防污树脂的制备过程中,使辅助树脂在主体树脂内部形成微纳态,有利于防污涂层与水接触后,辅助树脂迁移到涂层表面。
13.作为优选,所述主体树脂、辅助树脂和微纳促进剂的质量比为1:0.2~0.6:0.05~0.15。
14.作为优选,所述微纳促进剂包括分子量为1000~6000的两亲性聚合物;所述两亲性聚合物的单体包括酸酐类单体和/或多元酸类单体,还包括多元醇类单体。
15.进一步地,所述酸酐类单体和多元酸类单体的总摩尔量与多元醇类单体的摩尔量之比为1.05~1.35:1或1:1.1~1.5。
16.作为优选,所述辅助树脂为亲水性加聚树脂和/或亲水性聚氨酯树脂;所述亲水性加聚树脂的单体包括质量比为1:0~0.5的亲水性单体和憎水性单体;所述亲水性单体为20℃时在水中的溶解度不低于10g/l的单体,所述憎水性单体为20℃时在水中的溶解度低于10g/l的单体;所述亲水性单体和/或憎水性单体包括丙烯酸类单体。
17.进一步地,所述亲水性单体还包括n-乙烯基吡咯烷酮和/或丙烯酰胺。
18.作为优选,所述亲水性聚氨酯树脂为超支化亲水性聚氨酯树脂;所述超支化亲水性聚氨酯树脂的制备方法包括以下步骤:(a)以质量比为1:6~10的聚四氢呋喃醚二醇和二羟基酸为原料,进行酯化反应,制得超支化聚酯;(b)以质量比为1:4.5~5.5:0.8~1.2的二羟基酸、二异氰酸酯和步骤(a)中制得的超支化聚酯为原料,进行聚合反应,制得超支化亲水性聚氨酯树脂。
19.相较于非超支化亲水性聚氨酯树脂而言,超支化亲水性聚氨酯树脂具有合适的降解速度,有利于涂料发挥更好的长期防污作用,具体而言:超支化亲水性聚氨酯树脂可自降
解,因而能在由辅助树脂形成的表面水凝胶层被破坏后,使表层的主体树脂及时降解并释放出内部的辅助树脂,形成新的表面水凝胶层,从而赋予涂料较好的防污效果;同时,超支化亲水聚氨酯树脂的高度支化结构能够赋予表面水凝胶层较高的强度,能减缓水流冲蚀,防止其被过快消耗,从而延长涂料的防污期效。
20.进一步地,步骤(a)和(b)中,所述二羟基酸包括二羟基丙酸和/或二羟基丁酸。
21.作为优选,所述主体树脂为加聚树脂和/或聚氨酯树脂;所述加聚树脂的单体包括质量比为0~1:1的亲水性加聚单体和憎水性加聚单体;所述亲水性单体为20℃时在水中的溶解度不低于10g/l的单体,所述憎水性单体为20℃时在水中的溶解度低于10g/l的单体;所述亲水性加聚单体和/或憎水性加聚单体包括丙烯酸酯类单体;所述聚氨酯树脂的单体包括多元胺和/或多元醇,还包括多异氰酸酯。
22.进一步地,所述聚氨酯树脂的单体中,羟基与氨基的总摩尔量与异氰酸酯基的摩尔量之比为0.7~0.95:1。
23.进一步地,所述亲水性加聚单体还包括醋酸乙烯酯、n-乙烯基吡咯烷酮和丙烯腈中的一种或多种。
24.第二方面,本发明提供了一种所述防污树脂的制备方法,包括以下步骤:将主体树脂分散液加热至60~70℃后,加入微纳促进剂分散液,在搅拌下,向其中以1.0~2.5ml/min的速度滴加辅助树脂分散液,滴加完成后,升温至90~100℃,继续搅拌1h,获得防污树脂。
25.本发明中采用特定的方法制备防污树脂,能够使辅助树脂以微纳态分散于主体树脂中,具体机制如下:辅助树脂的极性高于主体树脂,在微纳促进剂及特殊工艺条件下,分子链柔性较大的辅助树脂能够发生分子链形变,通过亲疏水相互作用和分子次价键作用力聚集在一起,形成纳米或微米结构(粒径在280nm至1.5微米之间),并分散在主体树脂中,构成防污树脂中的亲水微纳区,而主体树脂则构成疏水性相对较高的疏水区。
26.作为优选,所述主体树脂分散液、辅助树脂分散液和微纳促进剂分散液的固含量分别为45~55wt%、45~55wt%和65~75wt%;所述主体树脂分散液、辅助树脂分散液和微纳促进剂分散液的质量比为1:0.25~0.50:0.05~0.10。
27.第三方面,本发明提供了所述防污树脂在无铜稳控释海洋防污涂料中的应用。
28.作为优选,所述无铜稳控释防污涂料按重量百分数计,包括以下组分:所述防污树脂5~25%,防污剂5~16%,松香0~10%,增粘剂0~4%,颜料0~6%,填料0~40%,增塑剂0~2%,助剂0~7%,余量为溶剂。
29.作为优选,所述助剂包括分散剂、流平剂、防沉触变剂和抗氧剂中的一种或多种。
30.作为优选,所述松香包括氢化松香。
31.作为优选,所述增粘剂包括液态丁苯橡胶。液体聚丁二烯橡胶能够赋予涂层较好的初粘性和柔韧性。
32.作为优选,所述填料包括氧化锌。
33.作为优选,所述防污剂包括溴代吡咯腈和/或吡啶硫酮锌。
34.与现有技术相比,本发明具有以下优点:(1)本发明将具有自抛光能力的主体树脂与能够迁移到涂层表面形成水凝胶层的辅助树脂相配合,能发挥较好的防污作用,并具有较长的防污期效,因而能减少防污剂的使用;
(2)通过使辅助树脂以微纳态分散在主体树脂中,使其易迁移到防污涂层表面发挥防止生物附着的作用,有利于辅助树脂在涂层与水接触后迁移到涂层表面,形成表面水凝胶层以发挥防污的作用;(3)通过在防污树脂中添加微纳促进剂,能够使辅助树脂形成亲水微区和疏水微区,进而延长防污涂料的防污期效,赋予其较好的防污效果,同时还有利于使辅助树脂在主体树脂内形成微纳态;(4)采用超支化亲水性聚氨酯树脂作为辅助树脂,能减缓水流对表面水凝胶层的冲蚀,还能在涂层表面的水凝胶层被破坏时,及时形成新的表面水凝胶层,从而使涂料具有较好的长期防污作用。
具体实施方式
35.下面结合实施例对本发明作进一步的描述。
36.总实施例一种基于微纳聚水凝胶的海洋防污涂料用防污树脂,包括主体树脂,微纳促进剂,以及以微纳态的形式分散在所述主体树脂中的辅助树脂。所述辅助树脂为具有吸水溶胀性的亲水性树脂;所述主体树脂为自抛光树脂;所述辅助树脂的亲水性高于主体树脂。所述主体树脂、辅助树脂和微纳促进剂的质量比为1:0.2~0.6:0.05~0.15。
37.所述主体树脂为加聚树脂和/或聚氨酯树脂。
38.所述加聚树脂的单体包括质量比为0~1:1的亲水性加聚单体和憎水性加聚单体;所述亲水性单体为20℃时在水中的溶解度不低于10g/l的单体,所述憎水性单体为20℃时在水中的溶解度低于10g/l的单体。所述亲水性加聚单体和/或憎水性加聚单体包括丙烯酸酯类单体;可选地,所述亲水性加聚单体还包括醋酸乙烯酯、n-乙烯基吡咯烷酮和丙烯腈中的一种或多种。
39.所述丙烯酸酯类单体可选自丙烯酸甲酯、甲基丙烯酸甲酯、丙烯酸乙酯、甲基丙烯酸乙酯、丙烯酸丁酯、甲基丙烯酸丁酯、甲基丙烯酸异丁酯、丙烯酸异丁酯、丙烯酸三异丙基硅酯、甲基丙烯酸三异丙基硅酯、丙烯酸三丁基硅酯、甲基丙烯酸三丁基硅酯、丙烯酸三甲基硅酯、甲基丙烯酸三甲基硅酯、丙烯酸异辛酯、甲基丙烯酸异辛酯、丙烯酸异癸酯、甲基丙烯酸异癸酯、丙烯酸-2-甲氧乙基酯、甲基丙烯酸-2-甲氧乙基酯、丙烯酸己酯、甲基丙烯酸己酯、丙烯酸乙氧基乙酯、甲基丙烯酸乙氧基乙酯、丙烯酸乙氧基乙氧基乙酯和甲基丙烯酸乙氧基乙氧基乙酯中的一种或多种。
40.作为一种具体实施方式,所述加聚树脂的制备方法包括以下步骤:按重量份,将200份单体(包括质量比为0~1:1的亲水性加聚单体和憎水性加聚单体)、0.9~1.5份偶氮二异丁腈(aibn)、0.3~0.9份偶氮二异戊腈(ambn)和190~210份反应溶剂混合后,在70~90℃下反应2.5~3.5h,而后加入0.2份过氧化醋酸叔戊酯(tapv),在80~100℃下反应2~3h,获得加聚树脂。可选地,单体是甲基丙烯酸三丁基硅酯,或者由质量比为1:0.5~1的甲基丙烯酸甲酯和甲基丙烯酸乙氧基乙氧基乙酯组成,或者由质量比为1:0.2~0.3:0.5~0.7的甲基丙烯酸异辛酯、醋酸乙烯酯和乙烯基吡咯烷酮组成,或者由质量比为1:0.5~0.8:0.4~0.6:0.3~0.4的丙烯酸异辛酯、甲基丙烯酸三甲基硅酯、甲基丙烯酸异癸酯和丙烯腈组成。
41.所述聚氨酯树脂的单体包括多元胺和/或多元醇,还包括多异氰酸酯。
42.所述多异氰酸酯可选自甲苯二异氰酸酯、异佛尔酮二异氰酸酯、六亚甲基二异氰酸酯、二苯基甲烷二异氰酸酯和二环己基甲烷二异氰酸酯中的一种或多种。所述多元醇可选自羟基封端的聚酯、羟基封端的聚醚、c2~8的二元醇、c3~10的三元醇中的一种或多种。所述多元胺可选自二元胺、三元胺中的一种或多种。
43.作为一种具体实施方式,所述聚氨酯树脂的制备方法包括以下步骤:将多元胺和/或多元醇、反应溶剂、多异氰酸酯、催化剂混合后,在60~70℃下反应至完全,而后加入丁二醇扩链,获得聚氨酯树脂。
44.作为一种具体实施方式,所述聚氨酯树脂的制备方法包括以下步骤:将多元胺和/或多元醇、反应溶剂、异佛尔酮二异氰酸酯(ipdi)、催化剂混合后,在60~70℃下反应3.5~4.5h,加入二苯基甲烷二异氰酸酯(mdi),继续在60~70℃下反应至完全,而后加入二元醇扩链,获得聚氨酯树脂。
45.所述辅助树脂为亲水性加聚树脂和/或亲水性聚氨酯树脂。
46.所述亲水性加聚树脂的单体包括质量比为1:0~0.5的亲水性单体和憎水性单体;所述亲水性单体为20℃时在水中的溶解度不低于10g/l的单体,所述憎水性单体为20℃时在水中的溶解度低于10g/l的单体。所述亲水性单体和/或憎水性单体包括丙烯酸类单体;可选地,所述亲水性单体还包括n-乙烯基吡咯烷酮和/或丙烯酰胺。
47.所述丙烯酸类单体可选自甲基丙烯酸、丙烯酸、甲基丙烯酸羟乙酯、丙烯酸羟乙酯、甲基丙烯酸羟丙酯、丙烯酸羟丙酯、丙烯酸甲氧基乙酯、甲基丙烯酸聚乙二醇酯、甲基丙烯酸四氢呋喃酯、丙烯酸二甲基氨基乙酯、甲基丙烯酸甲酯、丙烯酸甲酯、甲基丙烯酸乙酯、丙烯酸乙酯、甲基丙烯酸丁酯、丙烯酸丁酯、甲基丙烯酸异丁酯、丙烯酸异丁酯、丙烯酸异冰片酯、甲基丙烯酸异冰片酯、甲基丙烯酸环己酯、丙烯酸环己酯和甲基丙烯酸苄基酯中的一种或多种。
48.作为一种具体实施方式,所述亲水性加聚树脂的制备方法包括以下步骤:按重量份,将200份单体(包括质量比为1:0~0.5的亲水性加聚单体和憎水性加聚单体)、0.3份aibn、3份ambn、0.5份tapv和196份反应溶剂混合后,在70~90℃下反应2.5~3.5h,而后加入0.2份过氧化苯甲酰(bpo),在100~120℃下反应2~3h,获得亲水性加聚树脂。可选地,单体由质量比为1:0.8~1.2的乙烯基吡咯烷酮和丙烯酸甲氧基乙酯组成,或者由质量比为1:0.2~0.3:0.5~0.7的甲基丙烯酸异辛酯、醋酸乙烯酯和乙烯基吡咯烷酮组成,或者由质量比为0.1~0.3:0.6~0.8:0.9~1.1的甲基丙烯酸异冰片酯、乙烯基吡咯烷酮和丙烯酸甲氧基乙酯组成,或者由质量比为1:1.5~2.0:2.5~2.8:0.8~1.3的丙烯酸、甲基丙烯酸异冰片酯、丙烯酸甲氧基乙酯、丙烯酸羟乙酯组成。
49.所述亲水性聚氨酯树脂为超支化亲水性聚氨酯树脂;所述超支化亲水性聚氨酯树脂的制备方法包括以下步骤:(a)以质量比为1:6~10的聚四氢呋喃醚二醇和二羟基酸为原料,进行酯化反应,制得超支化聚酯;(b)以质量比为1:4.5~5.5:0.8~1.2的二羟基酸、二异氰酸酯和步骤(a)中制得的超支化聚酯为原料,进行聚合反应,制得超支化亲水性聚氨酯树脂。
50.作为一种具体实施方式,所述超支化亲水性聚氨酯树脂的制备方法包括以下步
骤:(a)将质量比为1:6~10聚四氢呋喃醚二醇(ptmg1000)和二羟基酸混合后,在165~175℃下反应3~4h后,升温至195~205℃反应至酸值低于3,升温至225~235℃后立即冷却降温,制得超支化聚酯;(b)将质量比为1:4.5~5.5的二羟基酸、二异氰酸酯和催化剂混合后,在70~80℃下反应50~90min,而后加入稀释剂,继续在70~80℃下反应至完全;加入超支化聚酯,所述超支化聚酯与2,2-二羟甲基丙酸之间的质量比为0.8~1.2:1,继续在70~80℃下反应至完全;而后加入二元醇扩链,获得超支化亲水性聚氨酯树脂。可选地,所述稀释剂是质量比为1~2:1的n-甲基吡咯烷酮和二甲苯,所述稀释剂与二异氰酸酯的质量比为1.6~2.1:1。
51.所述微纳促进剂包括分子量为1000~6000的两亲性聚合物。所述两亲性聚合物的单体包括酸酐类单体和/或多元酸类单体,还包括多元醇类单体;所述酸酐类单体和多元酸类单体的总摩尔量与多元醇类单体的摩尔量之比为1.05~1.35:1或1:1.1~1.5。
52.所述酸酐类单体可选自邻苯二甲酸酐、四氢苯酐、六氢苯酐、琥珀酸酐和偏苯三酸酐中的一种或多种。所述多元酸类单体可选自戊二酸和/或己二酸。所述多元醇类单体可选自乙二醇、丁二醇、己二醇、新戊二醇、1,4-环己烷二甲醇、二缩三乙二醇和四甘醇中的一种或多种。
53.作为一种具体实施方式,所述微纳促进剂的制备过程包括以下步骤:按重量份,将280~320份单体、50~60份反应溶剂、1.3~1.6份催化剂混合后,在155~165℃下反应2.5~3.5h,升温至190~210℃反应2~4h,再升温至220~240℃保持20~40min,加入62~81份反应溶剂,获得微纳促进剂。
54.一种所述防污树脂的制备方法,包括以下步骤:将固含量为45~55wt%的主体树脂分散液加热至60~70℃后,加入固含量为65~75wt%的微纳促进剂分散液,在搅拌下,以1.0~2.5ml/min的速度向其中滴加固含量为45~55wt%的辅助树脂分散液,所述主体树脂分散液、辅助树脂分散液和微纳促进剂分散液的质量比为1:0.25~0.50:0.05~0.10,滴加完成后,升温至90~100℃,继续搅拌1h,获得防污树脂。
55.一种无铜稳控释海洋防污涂料,按重量百分数计,包括以下组分:所述防污树脂5~25%,防污剂5~16%,松香0~10%,增粘剂0~4%,颜料0~6%,填料0~40%,增塑剂0~2%,助剂0~7%,余量为溶剂。所述助剂包括分散剂、流平剂、防沉触变剂和抗氧剂中的一种或多种。所述松香包括氢化松香。所述增粘剂包括液态丁苯橡胶。所述填料包括氧化锌。所述防污剂包括溴代吡咯腈和/或吡啶硫酮锌。
56.作为一种具体实施方式,所述防污涂料为船用无铜稳控释海洋防污涂料按重量百分数计,包括以下组分:所述防污树脂5~16%,防污剂5~16%,松香4~10%,增粘剂0.5~4%,颜料0~6%,填料5~40%,增塑剂0~2%,助剂0~7%,余量为溶剂。
57.作为一种具体实施方式,所述防污涂料为网衣用无铜稳控释海洋防污涂料,包括以下组分:所述防污树脂5~22%,防污剂6~16%,增粘剂0.5~4%,颜料0~6%,增塑剂0~2%,助剂0~7%,余量为溶剂。
58.作为一种具体实施方式,所述防污涂料为海上平台用无铜稳控释海洋防污涂料按重量百分数计,包括以下组分:所述防污树脂5~16%,防污剂6~16%,松香4~10%,增粘剂0.5~4%,颜料0~6%,填料5~40%,增塑剂0~2%,助剂0~7%,余量为溶剂。
59.制备例1:主体树脂(加聚树脂)的合成(1)主体树脂1a的合成:在装有搅拌器和回流冷凝管,并由氮气保护的1l四口烧瓶中加入200g甲基丙烯酸三丁基硅酯、1.5g aibn、0.3g ambn、178g二甲苯、20g丙二醇单甲醚,在85℃下保温3h,而后加入0.2g tapv,升温至95℃保温2.5h后,冷却至室温,获得固含量为50%左右的主体树脂1a分散液。
60.(2)主体树脂1b的合成:在装有搅拌器和回流冷凝管,并由氮气保护的1l四口烧瓶中加入100g甲基丙烯酸甲酯、100g甲基丙烯酸乙氧基乙氧基乙酯、1.5g aibn、0.3g ambn、178g二甲苯、20g乙二醇单丁醚,在70℃下保温3h,而后加入0.2g tapv,升温至80℃保温2.5h后,冷却至室温,获得固含量为50%左右的主体树脂1b分散液。
61.(3)主体树脂1c的合成:在装有搅拌器和回流冷凝管,并由氮气保护的1l四口烧瓶中加入100g甲基丙烯酸异辛酯、30g醋酸乙烯酯、70g乙烯基吡咯烷酮、0.9g aibn、0.9g ambn、178g溶剂油、20g乙二醇单丁醚,在90℃下保温3h,而后加入0.2g tapv,升温至100℃保温2.5h后,冷却至室温,获得固含量为50%左右的主体树脂1c分散液。
62.(4)主体树脂1d的合成:在装有搅拌器和回流冷凝管,并由氮气保护的1l四口烧瓶中加入80g丙烯酸异辛酯、50g甲基丙烯酸三甲基硅酯、40g甲基丙烯酸异癸酯、30g丙烯腈、0.9g aibn、0.9g ambn、178g溶剂油、20g乙二醇单丁醚,在90℃下保温3h,而后加入0.2g tapv,升温至100℃保温2.5h后,冷却至室温,获得固含量为50%左右的主体树脂1d分散液。
63.制备例2:主体树脂(聚氨酯树脂)的合成(1)主体树脂2a的合成:在氩气保护下,将干燥的200g羟基封端的聚酯、240g n-甲基吡咯烷酮、33.4g mdi和4滴二月桂酸二正丁基锡(dbtdl)混合,在65℃下持续反应至nco达到理论值(二正丁胺滴定法),而后加入1.8g丁二醇扩链3h,冷却后得到目标产物,即固含量为50%左右的主体树脂2a分散液。
64.(2)主体树脂2b的合成:在氩气保护下,将干燥的100g羟基封端的聚酯、100g羟基封端的聚醚、235g n-甲基吡咯烷酮、30g ipdi和4滴dbtdl混合,在65℃下持续反应至nco达到理论值,而后加入1.8g丁二醇扩链3h,冷却后得到目标产物,即固含量为50%左右的主体树脂2b分散液。
65.(3)主体树脂2c的合成:在氩气保护下,将干燥的100g羟基封端的聚酯、100g羟基封端的聚醚、237g n-甲基吡咯烷酮、22.2g ipdi和4滴dbtdl混合,在65℃下反应4h后,加入8.3g mdi,继续在65℃下反应至nco达到理论值,而后加入1.8g丁二醇扩链3h,冷却后得到目标产物,即固含量为50%左右的主体树脂2c分散液。
66.制备例3:辅助树脂(亲水性加聚树脂)的合成(1)辅助树脂3a的合成:在装有搅拌器和回流冷凝管,并由氮气保护的1l四口烧瓶中加入100g乙烯基吡咯
烷酮、100g丙烯酸甲氧基乙酯、0.3g aibn、3.0g ambn、0.5g tapv、176g溶剂油、20g丙二醇单甲醚,在100℃下保温3h,而后加入0.2g bpo,升温至110℃保温2.5h后,冷却至室温,获得固含量为50%左右的辅助树脂3a分散液。
67.(2)辅助树脂3b的合成:在装有搅拌器和回流冷凝管,并由氮气保护的1l四口烧瓶中加入30g甲基丙烯酸异冰片酯、70g乙烯基吡咯烷酮、100g丙烯酸甲氧基乙酯、0.3g aibn、3.0g ambn、0.5g tapv、176g二甲苯、20g丙二醇单甲醚,在100℃下保温3h,而后加入0.2g bpo,升温至110℃保温2.5h后,冷却至室温,获得固含量为50%左右的辅助树脂3b分散液。
68.(3)辅助树脂3c的合成:在装有搅拌器和回流冷凝管,并由氮气保护的1l四口烧瓶中加入30g丙烯酸、60g甲基丙烯酸异冰片酯、80g丙烯酸甲氧基乙酯、30g丙烯酸羟乙酯、0.3g aibn、3.0g ambn、0.5g tapv、146g二甲苯、50g丙二醇单甲醚,在100℃下保温3h,而后加入0.2g bpo,升温至110℃保温2.5h后,冷却至60℃,加入三乙胺36g,反应0.5h后冷却至室温,完成反应,获得固含量为50%左右的辅助树脂3c分散液。
69.制备例4:辅助树脂(超支化亲水性聚氨酯树脂)的合成(1)超支化聚酯ho-hb-oh的合成:在氮气保护下,将100g ptmg1000和600g二羟基丙酸(dmpa)加入到反应器中。搅拌均匀后,缓慢升温至170℃,维持温度3h,继续升温至200℃(整个过程期间,氮气连续吹),反应至酸值低于3,升温至230℃后立即冷却降温。当温度降至100℃时,减压除水1h后,降低至室温,得到超支化聚酯ho-hb-oh。
70.(2)辅助树脂4a的合成:在高纯氮气保护下,将干燥的100g dmpa、498g ipdi和6滴催化剂dbtdl混合,在70℃下反应1h后,加入500g干燥的n-甲基吡咯烷酮和400g干燥的二甲苯,继续反应至nco达到理论值;而后加入100g超支化聚酯ho-hb-oh,继续反应至nco达到理论值;而后加入96g三甘醇(teg),反应完全后,用67g三乙胺(tea)中和,得到固含量为50%左右的辅助树脂4a分散液。
71.超支化聚酯ho-hb-oh和辅助树脂4a的制备路线如下:
(3)辅助树脂4b的合成:在高纯氮气保护下,将干燥的110g二羟甲基丁酸(dmba)、390g六亚甲基二异氰酸酯(hdi)和6滴催化剂dbtdl混合,在70℃下反应1h后,加入500g干燥的n-甲基吡咯烷酮和300g干燥的二甲苯,继续反应至nco达到理论值;而后加入100g超支化聚酯ho-hb-oh,继续反应至nco达到理论值;而后加入99g四甘醇,反应完全后,用60g tea中和,得到固含量为50%左右的辅助树脂4b分散液。
72.(4)辅助树脂4c的合成:在高纯氮气保护下,将干燥的110g dmba、590g 4,4'-二环己基甲烷二异氰酸酯(hmdi)和7滴催化剂dbtdl混合,在70℃下反应1h后,加入600g干燥的n-甲基吡咯烷酮和400g干燥的二甲苯,继续反应至nco达到理论值;而后加入100g超支化聚酯ho-hb-oh,继续反应至nco达到理论值;而后加入99g四甘醇,反应完全后,用66g二乙醇胺(dea)中和,得到固含量为50%左右的辅助树脂4c分散液。
73.制备例5:辅助树脂(亲水性聚氨酯树脂)的合成在高纯氮气保护下,将干燥的100g dmpa、498g ipdi和一定量的催化剂dbtdl混合,在70℃下反应1h后,加入500g干燥的n-甲基吡咯烷酮和400g干燥的二甲苯,继续反应至nco达到理论值;而后加入100g ptmg1000,继续反应至nco达到理论值;而后加入96g三甘醇(teg),反应完全后,用67g三乙胺(tea)中和,得到固含量为50%左右的辅助树脂5a分散液。
74.制备例6:微纳促进剂的合成(1)微纳促进剂6a的合成:取苯酐180g、乙二醇80g、己二醇40g、二甲苯60g及c-94催化剂1.5g,混合后升温至160℃,维持3h后,升温至200℃,维持2.5h后,继续升温至230℃,保持0.5h后,降温至90℃,加入二甲苯71g,结束反应,获得固含量为70%左右、数均分子量为2846的微纳促进剂6a分散液。
75.(2)微纳促进剂6b的合成:取苯酐110g、偏苯三酸酐90g、乙二醇80g、己二醇40g、二甲苯60g及c-94催化剂1.6g,混合后升温至155℃,维持2.5h后,升温至200℃,维持2h后,继续升温至230℃,保持0.5h后,降温至90℃,加入二甲苯81g,结束反应,获得固含量为70%左右、数均分子量为1473的微纳促进剂6b分散液。
76.(3)微纳促进剂6c的合成:取苯酐110g、偏苯三酸酐90g、乙二醇50g、己二醇30g、二甲苯50g及c-94催化剂1.3g,混合后升温至165℃,维持3.5h后,升温至210℃,维持4h后,继续升温至230℃,保持0.5h后,降温至90℃,加入二甲苯62g,结束反应,获得固含量为70%左右、数均分子量为5695的微纳促进剂6c分散液。
77.实施例1~9和对比例1~4:船用无铜稳控释防污涂料(1)防污树脂分散液的制备:实施例1~9:将主体树脂分散液(由制备例1获得)加热至60℃,加入相当于主体树脂分散液质量6%的微纳促进剂6a分散液(由制备例6获得),在3500r/min分散条件下,以1.0ml/min的速度向其中缓慢滴加相当于主体树脂分散液质量25%的辅助树脂分散液(由制备例3获得),滴加完后升温至90℃,继续在3500r/min分散条件下维持1h后冷却降温,获得防污树脂分散液。
78.实施例1~9中,采用的主体树脂和辅助树脂分别如表1所示。
79.表1树脂编号1a1b1c3a实施例1实施例4实施例73b实施例2实施例5实施例83c实施例3实施例6实施例9对比例1与实施例1的区别仅在于,在防污树脂分散液的制备过程中,不添加辅助树脂分散液。
80.对比例2与实施例1的区别仅在于,在防污树脂分散液的制备过程中,将主体树脂1a分散液换成等质量且固含量相同的市售m133树脂分散液(苯乙烯-甲基丙烯酸甲酯-丙烯酸丁酯三元共聚物,该树脂在海水中不能抛光)。
81.对比例3与实施例1的区别仅在于,在防污树脂分散液的制备过程中,不添加微纳促进剂分散液。
82.对比例4:将主体树脂1a分散液(由制备例1获得)加热至60℃,加入相当于主体树脂1a分散液质量6%的微纳促进剂6a分散液(由制备例6获得)和相当于主体树脂1a分散液质量25%的辅助树脂3a分散液(由制备例3获得),升温至90℃,在3500r/min分散条件下维
持2.5h后冷却降温,获得防污树脂分散液。
83.(2)船用无铜稳控释防污涂料的制备:按照表2和3的配方(各原料的用量均为质量百分数),将所有原料混合均匀后,制得实施例1~9和对比例1~3的船用无铜稳控释防污涂料(对比例1和3中,通过改变防污树脂分散液和二甲苯、丙二醇单甲醚的用量,控制防污涂料固含量与实施例1相同)。
84.(3)一年防污评价:将实施例1~9的船用无铜稳控释防污涂料分别涂覆到样板表面,形成厚度为100μm的防污涂层。按照gb/t 7789-2007中的方法,在浙江舟山螺门海域进行实海挂板测试,1年生物附着量(生物附着面积)小于5%评定为优,5~10%(含5%,不含10%)评定为良,10~20%(含10%,不含20%)评定为一般,大于等于20%评定为差。结果见表2。
85.表2表2表3原料对比例1对比例2对比例3对比例4防污树脂分散液/%25.625.826.725.8氢化松香/%9999液态丁苯橡胶/%2222溴代吡咯腈/%3333吡啶硫酮锌/%2222氧化铁红/%3333氧化锌/%40404040邻苯二甲酸二辛酯/%1111聚醚硅et102/%0.70.70.70.7二甲苯/%10.1109.310丙二醇单甲醚/%3.63.53.33.5一年防污评价差一般一般一般(4)数据分析:
从表2可以看出,实施例1~9中的一年生物附着量均小于10%,说明采用本发明的方法获得的船用无铜稳控释防污涂料,在不添加氧化亚铜且有机小分子辅防污剂的添加量仅为5%的情况下,即可实现较好的长期防污效果。
86.从表2和表3可以看出,实施例1~3的一年防污效果明显优于对比例1,说明通过在防污树脂中添加辅助树脂,能够提高防污涂料的防污效果。原因在于:在与海水接触后,亲水性较强的辅助树脂会逐渐迁移到涂层表面,并在迁移过程中不断吸水溶胀,最终在涂层表面形成光滑的水凝胶膜,发挥防止生物附着的作用。
87.从表2和表3可以看出,实施例1、4和7的一年防污效果明显优于对比例2,说明相较于市售m133树脂而言,采用本发明中的主体树脂,能够赋予防污涂料更好的防污效果。原因在于:在长期与海水接触的过程中,由辅助树脂形成的表面水凝胶膜会逐渐降解,防污效果变差。本发明采用的主体树脂具有自抛光能力,在海水的作用下,表层的主体树脂会降解脱落,从而使涂层内部的辅助树脂被进一步释放出来,在涂层表面形成新的水凝胶膜;而市售m133树脂在海水中无法进行自抛光,在长期使用的过程中,辅助树脂的释放速度大幅下降,当由辅助树脂形成的表面水凝胶膜被破坏时,难以及时形成新的水凝胶膜,因而会造成防污涂料的长期防污效果较差。
88.从表2和表3可以看出,实施例1的一年防污效果明显优于对比例3,说明通过在防污树脂中添加微纳促进剂,能够提高防污涂料的防污效果。原因在于:微纳促进剂能够促进辅助树脂内部形成亲水微区和疏水微区,在辅助树脂迁移到主体树脂表面的过程中,亲水微区能够吸水溶胀,最终在涂层表面形成水凝胶层,发挥润滑防污作用;水凝胶层内部分子链之间并非通过共价键相连,与水接触时易被抛光磨蚀,而疏水微区与水接触较少,抛光速度较慢,因而能防止水凝胶层被过快地磨抛,从而延长涂层的防污期效;并且,利用微纳促进剂的两亲性,配合辅助树脂和主体树脂的亲疏水性差异,还有助于在防污树脂的制备过程中,使辅助树脂在主体树脂内部形成微纳态,有利于防污涂层与水接触后,辅助树脂迁移到涂层表面。通过这种方式,微纳促进剂能赋予防污涂料较好的长期防污效果。
89.从表2和表3可以看出,实施例1的一年防污效果明显优于对比例4,说明相较于将主体树脂分散液、辅助树脂分散液、微纳促进剂分散液直接共混而言,采用本发明的方法制备防污树脂分散液,有助于提高防污涂料的防污效果。原因在于:采用本发明的方法获得的防污树脂中,辅助树脂能够以微纳态存在于主体树脂中,与主体树脂之间的分子链缠结较少,有利于辅助树脂迁移到涂层表面形成水凝胶层,进而发挥防止生物附着的作用。
90.实施例10~18:网衣用无铜稳控释防污涂料(1)防污树脂分散液的制备:将主体树脂(由制备例2获得)加热至60℃,加入相当于主体树脂质量6%的微纳促进剂6b(由制备例6获得),在3500r/min分散条件下,以1.0ml/min的速度向其中缓慢滴加相当于主体树脂质量50%的辅助树脂(由制备例4获得)滴加完后升温至90℃,继续在3500r/min分散条件下维持1h后冷却降温,获得防污树脂分散液。
91.实施例10~18中,采用的主体树脂和辅助树脂分别如表4所示。
92.表4树脂编号2a2b2c4a实施例10实施例13实施例16
4b实施例11实施例14实施例174c实施例12实施例15实施例18(2)网衣用无铜稳控释防污涂料的制备:按照表5的配方(各原料的用量均为质量百分数),将所有原料混合均匀后,制得实施例10~18的网衣用无铜稳控释防污涂料。
93.(3)6个月防污评价:将实施例10~18的网衣用无铜稳控释防污涂料分别涂覆到样板表面,形成厚度为100μm的防污涂层。按照gb/t 7789-2007中的方法,在浙江舟山螺门海域进行实海挂板测试,6个月生物附着量小于5%评定为优,5~10%(含5%,不含10%)评定为良,10~20%(含10%,不含20%)评定为一般,大于等于20%评定为差。结果见表5。
94.表5(4)数据分析:从表5可以看出,实施例10~18中的一年生物附着量均小于10%,说明采用本发明的方法获得的网衣用无铜稳控释防污涂料,在不添加氧化亚铜且有机小分子辅防污剂的添加量仅为10%的情况下,即可实现较好的长期防污效果。
95.实施例19~27:海上平台用无铜稳控释防污涂料(1)防污树脂分散液的制备:将主体树脂(由制备例1获得)加热至60℃,加入相当于主体树脂质量6%的微纳促进剂6c(由制备例6获得),在3500r/min分散条件下,以2.5ml/min的速度向其中缓慢滴加相当于主体树脂质量50%的辅助树脂(由制备例4获得)滴加完后升温至90℃,继续在3500r/min分散条件下维持1h后冷却降温,获得防污树脂分散液。
96.实施例19~27中,采用的主体树脂和辅助树脂分别如表6所示。实施例28中,采用的主体树脂为1a,辅助树脂为5a。
97.表6树脂编号1a1b1c4a实施例19实施例22实施例254b实施例20实施例23实施例264c实施例21实施例24实施例27
(2)网衣用无铜稳控释防污涂料的制备:按照表7的配方(各原料的用量均为质量百分数),将所有原料混合均匀后,制得实施例19~27的网衣用无铜稳控释防污涂料。
98.(3)一年防污评价:将实施例19~27的网衣用无铜稳控释防污涂料分别涂覆到样板表面,形成厚度为100μm的防污涂层。按照gb/t 7789-2007中的方法,在浙江舟山螺门海域进行实海挂板测试,一年生物附着量小于5%评定为优,5~10%(含5%,不含10%)评定为良,10~20%(含10%,不含20%)评定为一般,大于等于20%评定为差。结果见表7。
99.表7(4)数据分析:从表7可以看出,实施例19~27中的一年生物附着量均小于10%,说明采用本发明的方法获得的海上平台用无铜稳控释防污涂料,在不添加氧化亚铜且有机小分子辅防污剂的添加量仅为10%的情况下,即可实现较好的长期防污效果。
100.从表7可以看出,实施例19~21的一年防污效果明显优于实施例28,说明相较于直链型亲水性聚氨酯树脂而言,采用超支化亲水性聚氨酯树脂作为辅助树脂,能够提高防污涂料的防污效果。原因在于:超支化亲水聚氨酯树脂的高度支化结构能够赋予表面水凝胶层较高的强度,能减缓水流冲蚀,防止其被过快消耗,从而延长涂料的防污期效。
101.本发明中所用原料、设备,若无特别说明,均为本领域的常用原料、设备;本发明中所用方法,若无特别说明,均为本领域的常规方法。
102.以上所述,仅是本发明的较佳实施例,并非对本发明作任何限制,凡是根据本发明技术实质对以上实施例所作的任何简单修改、变更以及等效变换,均仍属于本发明技术方案的保护范围。