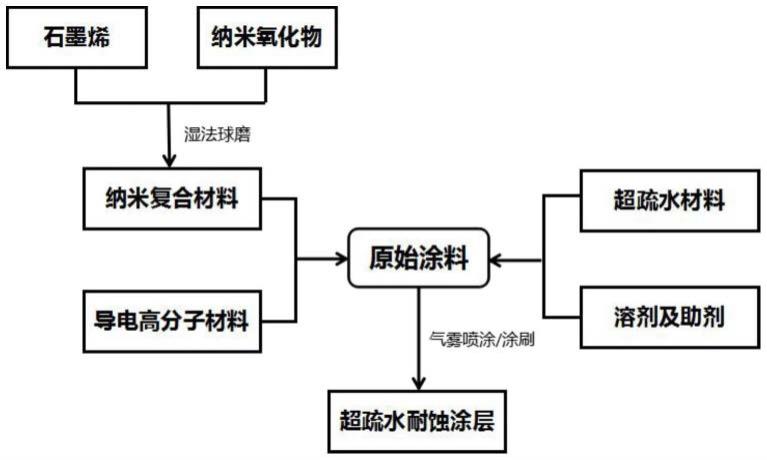
:
1.本发明涉及一种用于接地极的超疏水耐蚀涂料及其涂层制备方法。
背景技术:2.接地极作为接地装置的核心部件,长期埋置于土壤、阴暗、潮湿的环境中,极易受土壤ph值、含水量、含盐总量、各种阴阳离子含量和微生物细菌活动等多种因素影响发生腐蚀。由于其工作环境复杂,影响其腐蚀的因素不仅仅有土壤的化学腐蚀,而且还存在杂散电流腐蚀、电化学腐蚀等等。当接地极发生腐蚀后,接地极材料受损,表层腐蚀产物会造成接地性能不良,无法满足泄流时对热、动稳定的要求,危及人身安全,形成严重的安全隐患。因此需要开发一种稳定、高效的新型接地极防腐涂层具有重要的意义。
3.目前,常用的接地极防护措施主要有以下几种:(1)采用碳钢、镀锌钢、铜包钢等;(2)利用导电防腐涂料;(3)利用阴极防护;(4)利用降阻剂减阻等。这些措施各有优缺点,如钢表面镀锌是提高钢铁材料耐蚀性最经济有效的方法之一,由于价格低廉,加工性能好,镀锌钢占接地极市场份额的90%以上,但其材料或因生产工艺弊端带来包覆层过薄、厚度不均或金属间结合力较弱等问题,使用寿命却无法达到预期年限;阴极保护虽然操作施工相当简单,但其维护成本高;降阻剂则是施工难度大,条件苛刻,防腐成本高。涂料防腐是防止接地极和接地网设施发生腐蚀的常用措施之一,近年来出现的导电防腐涂料因其具备低电阻率的同时兼具良好防腐性能,又因其施工便捷、成本低、效率高,受到了越来越多的关注。目前大部分导电涂料主要以环氧树脂、聚氨酯或丙烯酸树脂为主,它们在潮湿土壤环境中长时间放置,易发生老化、降解等问题。常用的导电填料主要采用金属粉系(如镍粉、铝粉、铜粉、银粉等)导电填料,存在着与树脂兼容性差,导电能力不强、易氧化、引发土壤污染等不足。
技术实现要素:4.本发明的目的是为了解决电网接地极在潮湿土壤环境中长时间放置,易发生腐蚀、导电能力不强以及目前常规导电防腐涂料易老化、降解的问题,利用非金属导电填料替代常规金属导电填料,避免金属与树脂兼容性差,且易氧化、引发土壤污染等缺陷,提供了一种非金属导电填料的可用于接地极的超疏水耐蚀涂料及其涂层制备方法。
5.本发明一种用于接地极的超疏水耐蚀涂料按质量份数由10~30份导电高分子材料、20~50份纳米复合材料、40~65份超疏水材料、2~10份溶剂和0.35~2份助剂组成;所述的纳米复合材料为石墨烯改性的纳米氧化物颗粒。
6.本发明一种用于接地极的超疏水耐蚀涂层的制备方法,包括以下步骤:
7.一、称取导电高分子材料、纳米复合材料、超疏水材料、溶剂和助剂加入到容器中,进行超声分散,得到涂料;
8.二、对基体进行清洗、除油除锈和表面粗化,得到预处理后的基体;
9.三、以步骤一制备的涂料为原料,利用气雾喷涂或涂覆方式,在预处理后的基体表
面制备厚度为100~300μm的超疏水耐蚀涂层。
10.本发明采用导电高分子、纳米复合材料、超疏水材料,结合其他组分,通过特定的比例和配方,取代了目前常规导电涂料的金属类导电填料,使导电填料抗氧化性得到提升。超疏水表面其独特的疏水功能,广泛应用于在自清洁、防腐防污、油水分离、防冰雪等领域,该种功能表面浸入极性腐蚀环境,会形成一层空气层,高效阻止腐蚀介质进入涂层内部,是提升涂层防腐蚀性能的有效途径。本发明中的超疏水材料主要选用较高耐温性能的氟碳类超疏水材料,相比于目前常规环氧类、聚氨酯类树脂,其耐温性得到提升,这有利于接地极发生雷击、短路等故障时涂层的稳定性。导电高分子作为导电填料,相比于金属导电填料,其导电性良好,与树脂兼容性好,且不易氧化、无环境污染问题,如聚苯胺的防腐机理主要有自发钝化及减缓点蚀等,其在酸性条件下,可使钢材表面发生钝化,能较好的起到防腐蚀作用。利用湿法球磨制备石墨烯改性纳米氧化物,通过石墨烯对纳米粒子预包覆,实现石墨烯在整个涂料体系中的均匀分散。涂料体系中存在的石墨烯、纳米氧化物颗粒作为导电功能和超疏水功能的补充,涂层中片状分布的石墨烯在起到隔绝腐蚀介质进入,同时其还能联接分散其中的导电高分子,使导电高分子形成良好桥接通路,涂层导电性得到提升。此外,均匀分散的纳米氧化物可使涂层表面形成微结构,结合超疏水材料,表面形成微纳功能结构,形成类似荷叶效应,进一步提升涂层超疏水功能。
11.与现有的技术相比,本发明具有如下优势:
12.1、本发明提供了一种用于接地极的超疏水耐蚀涂料,其中导电高分子、纳米复合材料、超疏水材料的相互匹配,使制备的涂层具有良好的超疏水功能和耐蚀功能,同时兼具优异的导电性,可应用于潮湿土壤环境下接地极的长效防腐场景。
13.2、本发明中优化采用的气雾喷涂工艺,工艺简单,效率高,可低成本大面积制备涂层,且涂层与基体结合良好,适合现场施工。
附图说明
14.图1为本发明制备工艺流程图;
15.图2为本发明实施例1制备的超疏水耐蚀涂层的水接触角照片;
16.图3为本发明实施例1制备的超疏水耐蚀涂层盐雾试验2000小时后的数码照片;
17.图4为本发明对比例1制备的涂层的水接触角照片。
具体实施方式
18.具体实施方式一:本实施方式一种用于接地极的超疏水耐蚀涂料按质量份数由10~30份导电高分子材料、20~50份纳米复合材料、40~65份超疏水材料、2~10份溶剂和0.35~2份助剂组成;所述的纳米复合材料为石墨烯改性的纳米氧化物颗粒。
19.具体实施方式二:本实施方式与具体实施方式一不同的是:所述的所述的导电高分子材料为聚苯胺、聚吡咯或聚噻吩。其它与具体实施方式一相同。
20.具体实施方式三:本实施方式与具体实施方式一或二不同的是:所述的纳米氧化物颗粒为纳米二氧化钛、纳米二氧化硅、纳米氧化锌或纳米氧化铝,纳米氧化物颗粒的粒径为5~50nm。具体实施方式一或二相同。
21.具体实施方式四:本实施方式与具体实施方式一至三之一不同的是:所述的石墨
烯为氧化石墨烯、多层石墨烯或改性石墨烯,石墨烯粒径为2~50nm,表面石墨烯层数为1~10层。其它与具体实施方式一至三之一相同。
22.具体实施方式五:本实施方式与具体实施方式一至四之一不同的是:纳米复合材料制备方法为:按质量份数将80~95份的纳米氧化物、1~10份的石墨烯和1~5份的分散剂加入到球磨罐中进行湿法球磨1~6h,然后干燥获得纳米复合材料。其它与具体实施方式一至四之一相同。
23.具体实施方式六:本实施方式与具体实施方式一至五之一不同的是:所述的溶剂为n,n-二甲基乙酰胺、n,n-二甲基甲酰胺、二甲苯、乙酸乙酯或丙酮。其它与具体实施方式一至五之一相同。
24.具体实施方式七:本实施方式与具体实施方式一至六之一不同的是:所述的超疏水材料为全氟聚甲基酸丙烯酸酯、氟碳树脂、聚碳酸酯、氟树脂或氟硅烷。其它与具体实施方式一至六之一相同。
25.具体实施方式八:本实施方式与具体实施方式一至七之一不同的是:所述的助剂为聚丙烯酸、羧甲基纤维素、聚二甲基硅氧烷、聚甲基苯基硅氧烷、聚乙二醇、tego410或byk333。其它与具体实施方式一至七之一相同。
26.具体实施方式九:本实施方式一种用于接地极的超疏水耐蚀涂层的制备方法,包括以下步骤:一、称取导电高分子材料、纳米复合材料、超疏水材料、溶剂和助剂加入到容器中,进行超声分散,得到涂料;
27.二、对基体进行清洗、除油除锈和表面粗化,得到预处理后的基体;
28.三、以步骤一制备的涂料为原料,利用气雾喷涂或涂覆方式,在预处理后的基体表面制备厚度为100~300μm的超疏水耐蚀涂层。
29.具体实施方式十:本实施方式与具体实施方式九不同的是:气雾喷涂的工艺参数为:气压0.2~0.4mpa,喷涂距离为100~300mm,流量20~100ml/min,雾化嘴1.3~2.0mm,喷枪速度为50~400mm/s,涂层喷涂遍数为5~20遍。其它与具体实施方式九相同。
30.通过以下试验验证本发明的有益效果:
31.实施例1:
32.本实施例的基体材料为镀锌钢接地极材料,在该基体上制备超疏水耐蚀涂层的方法按以下步骤进行:
33.(1)纳米复合材料制备:将85g纳米二氧化钛、10g氧化石墨烯、5g peg-800分散剂加入到球磨罐中,并加入无水乙醇进行湿法球磨,球磨时间6h。球磨完成后,放入80℃鼓风干燥箱烘干干燥获得氧化石墨烯包覆的纳米二氧化钛粒子,得到纳米复合材料;其中,纳米二氧化钛粒径为25nm,氧化石墨烯粒径为5~50nm,层数5~10层。
34.(2)涂料制备:按质量分数将20%纳米复合材料,25%聚苯胺,45%氟碳树脂,8%n,n-二甲基乙酰胺,2%助剂(1%聚二甲基硅氧烷,1%byk333)加入到容器中,然后利用超声破碎仪对其进行分散,得到稳定分散的超疏水耐蚀涂料;其中,超声破碎仪频率25khz,功率800w,超声运行方式1s停2s,时间20min。
35.(3)基体预处理:将基体依次用酒精、丙酮清洗数次去除油污,然后使用32目棕刚玉砂对基体进行喷砂处理;
36.(4)涂层制备:以超疏水耐蚀涂料为原料,采用气雾喷涂方式在步处理后的基体表
面进行涂层制备,获得厚度为240mm的超疏水耐蚀涂层。其中喷涂参数为:气压为0.4mpa,喷涂距离为150mm,流量40ml/min,雾化嘴1.3mm,喷枪速度150mm/s,涂层喷涂遍数10遍。
37.本实施例涂层的制备工艺流程图如图1所示,对本实施例制备的超疏水耐蚀涂层进行标准中性盐雾试验、水接触角测试和导电性能测试。水接触角结果如图2所示,其水接触角达到152
°
,具备超疏水功能;中性盐雾试验结果如图3所示,其经过2000h盐雾试验后,表面未发生明显腐蚀,耐蚀性能优异;导电性能测试结果表面,涂层体积电阻率22ω.m,具有良好的导电率,满足实际使用要求。
38.实施例2
39.本实施例的基体材料为45号钢材料,在该基体上制备超疏水耐蚀涂层的方法按以下步骤进行:
40.(1)纳米复合材料制备:将90g纳米氧化铝、8g改性石墨烯、2g peg-800分散剂加入到球磨罐中,并加入无水乙醇进行湿法球磨,球磨时间6h。球磨完成后,放入80℃鼓风干燥箱烘干干燥获得氧化石墨烯包覆的纳米氧化铝粒子,得到纳米复合材料;其中,纳米氧化铝粒径为50nm,改性石墨烯粒径为15~50nm,层数2~8层。
41.(2)涂料制备:按质量分数将22%纳米复合材料,28%聚苯胺,40%氟碳树脂,8%n,n-二甲基甲酰胺,2%助剂(1%聚二甲基硅氧烷,1%byk333)加入到容器中,然后利用超声破碎仪对其进行分散,得到稳定分散的超疏水耐蚀涂料;其中,超声破碎仪频率25khz,功率800w,超声运行方式1s停2s,时间30min。
42.(3)基体预处理:将基体依次用酒精、丙酮清洗数次去除油污,然后使用32目棕刚玉砂对基体进行喷砂处理;
43.(4)涂层制备:以超疏水耐蚀涂料为原料,采用气雾喷涂方式在处理后的基体表面进行涂层制备,获得厚度为240mm的超疏水耐蚀涂层。其中喷涂参数为:气压为0.4mpa,喷涂距离为150mm,流量40ml/min,雾化嘴1.5mm,喷枪速度150mm/s,涂层喷涂遍数10遍。
44.对本实施例制备的超疏水耐蚀涂层进行标准中性盐雾试验、水接触角测试和导电性能测试。水接触角结果表明其水接触角达到150
°
,具备超疏水功能;中性盐雾试验结果表明,经过2000h盐雾试验后,表面未发生明显腐蚀,耐蚀性能优异;导电性能测试结果表面,涂层体积电阻率24ω.m,具有良好的导电率,满足实际使用要求。
45.实施例3
46.本实施例的基体材料为铸铁材料,在该基体上制备超疏水耐蚀涂层的方法按以下步骤进行:
47.(1)纳米复合材料制备:将90g纳米氧化铝、8g改性石墨烯、2g peg-800分散剂加入到球磨罐中,并加入无水乙醇进行湿法球磨,球磨时间6h。球磨完成后,放入80℃鼓风干燥箱烘干干燥获得氧化石墨烯包覆的纳米氧化铝粒子,得到纳米复合材料;其中,纳米氧化铝粒径为50nm,改性石墨烯粒径为15~50nm,层数2~8层。
48.(2)涂料制备:按质量分数将22%纳米复合材料,28%聚吡咯,40%全氟聚甲基酸丙烯酸酯,9%二甲苯,1%助剂(0.35%聚二甲基硅氧烷,0.65%聚乙二醇)加入到容器中,然后利用超声破碎仪对其进行分散,得到稳定分散的超疏水耐蚀涂料;其中,超声破碎仪频率25khz,功率800w,超声运行方式1s停2s,时间30min。
49.(3)基体预处理:将基体依次用酒精、丙酮清洗数次去除油污,然后使用32目棕刚
玉砂对基体进行喷砂处理;
50.(4)涂层制备:以超疏水耐蚀涂料为原料,采用气雾喷涂方式在处理后的基体表面进行涂层制备,获得厚度为240mm的超疏水耐蚀涂层。其中喷涂参数为:气压为0.4mpa,喷涂距离为200mm,流量40ml/min,雾化嘴1.5mm,喷枪速度150mm/s,涂层喷涂遍数10遍。
51.对本实施例制备的超疏水耐蚀涂层进行标准中性盐雾试验、水接触角测试和导电性能测试。水接触角结果表明其水接触角达到153
°
,具备超疏水功能;中性盐雾试验结果表明,经过2000h盐雾试验后,表面未发生明显腐蚀,耐蚀性能优异;导电性能测试结果表面,涂层体积电阻率28ω.m,具有良好的导电率,满足实际使用要求。
52.实施例4
53.本实施例中,选择基体材料为铸铁材料,在该基体上具体涂层制备流程如下:
54.(1)纳米复合材料制备:以质量计,将92g纳米氧化硅、7g改性石墨烯、1g peg-800分散剂加入到球磨罐中,并加入无水乙醇进行湿法球磨,球磨时间6h。球磨完成后,放入80℃鼓风干燥箱烘干干燥获得氧化石墨烯包覆的纳米氧化铝粒子;其中,纳米氧化硅粒径为50nm,改性石墨烯粒径为15~50nm,层数2~8层。
55.(2)涂料制备:按质量分数将25%上述纳米复合材料,30%聚苯胺,40%氟树脂,4.5%二甲苯,0.5%助剂(0.35%聚二甲基硅氧烷,0.15%聚乙二醇)加入到容器中,然后利用超声破碎仪对其进行分散,得到稳定分散的超疏水耐蚀涂料;其中,超声破碎仪频率25khz,功率800w,超声运行方式1s停2s,时间30min。
56.(3)基体预处理:将基体依次用酒精、丙酮清洗数次去除油污,然后使用32目棕刚玉砂对基体进行喷砂处理;
57.(4)涂层制备:以超疏水耐蚀涂料为原料,采用气雾喷涂方式在处理后的基体表面进行涂层制备,获得厚度为240mm的超疏水耐蚀涂层。其中喷涂参数为:气压为0.4mpa,喷涂距离为200mm,流量40ml/min,雾化嘴1.5mm,喷枪速度150mm/s,涂层喷涂遍数10遍。
58.对实施例4制备的超疏水耐蚀涂层进行标准中性盐雾试验、水接触角测试和导电性能测试。水接触角结果表明其水接触角达到160
°
,具备超疏水功能;中性盐雾试验结果表明,经过2000h盐雾试验后,表面未发生明显腐蚀,耐蚀性能优异;导电性能测试结果表面,涂层体积电阻率22ω.m,具有良好的导电率,满足实际使用要求。
59.实施例5
60.本实施例中,选择基体材料为铸铁材料,在该基体上具体涂层制备流程如下:
61.(1)纳米复合材料制备:以质量计,将92g纳米氧化硅、7g改性石墨烯、1g peg-800分散剂加入到球磨罐中,并加入无水乙醇进行湿法球磨,球磨时间6h。球磨完成后,放入80℃鼓风干燥箱烘干干燥获得氧化石墨烯包覆的纳米氧化铝粒子;其中,纳米氧化硅粒径为50nm,改性石墨烯粒径为15~50nm,层数2~8层。
62.(2)涂料制备:按质量分数将20%上述纳米复合材料,30%聚苯胺,45%氟树脂,4.5%二甲苯,0.5%助剂(0.35%聚二甲基硅氧烷,0.15%聚乙二醇)加入到容器中,然后利用超声破碎仪对其进行分散,得到稳定分散的超疏水耐蚀涂料;其中,超声破碎仪频率25khz,功率800w,超声运行方式1s停2s,时间30min。
63.(3)基体预处理:将基体依次用酒精、丙酮清洗数次去除油污,然后使用32目棕刚玉砂对基体进行喷砂处理;
64.(4)涂层制备:以超疏水耐蚀涂料为原料,采用气雾喷涂方式在处理后的基体表面进行涂层制备,获得厚度为200mm的超疏水耐蚀涂层。其中喷涂参数为:气压为0.3mpa,喷涂距离为200mm,流量40ml/min,雾化嘴1.5mm,喷枪速度150mm/s,涂层喷涂遍数8遍。
65.对实施例5制备的超疏水耐蚀涂层进行标准中性盐雾试验、水接触角测试和导电性能测试。水接触角结果表明其水接触角达到145
°
,具备超疏水功能;中性盐雾试验结果表明,经过2000h盐雾试验后,表面未发生明显腐蚀,耐蚀性能优异;导电性能测试结果表面,涂层体积电阻率38ω.m,具有良好的导电率,满足实际使用要求。
66.对比例1
67.本实施例的基体材料为镀锌钢接地极材料,在该基体上制备涂层的方法按以下步骤进行:
68.(1)涂料制备:按质量分数将35%聚苯胺,55%氟碳树脂,8%n,n-二甲基乙酰胺,2%助剂(1%聚二甲基硅氧烷,1%byk333)加入到容器中,然后利用超声破碎仪对其进行分散,得到涂料;其中,超声破碎仪频率25khz,功率800w,超声运行方式1s停2s,时间20min。
69.(2)基体预处理:将基体依次用酒精、丙酮清洗数次去除油污,然后使用32目棕刚玉砂对基体进行喷砂处理;
70.(3)涂层制备:以步骤(1)制备的涂料为原料,采用气雾喷涂方式在步处理后的基体表面进行涂层制备,获得厚度为240mm的超疏水耐蚀涂层。其中喷涂参数为:气压为0.4mpa,喷涂距离为150mm,流量40ml/min,雾化嘴1.3mm,喷枪速度150mm/s,涂层喷涂遍数10遍。
71.对本实施例制备的涂层进行水接触角测试、导电性能及耐腐蚀性能测试。水接触角结果如图4所示,其水接触角为130
°
左右,相比于实施例,其涂层超疏水功能大幅下降;导电性能测试结果表明,涂层体积电阻率1000ω.m,导电性较差,不能满足实际使用要求。中性盐雾试验2000h后,且未发生明显的基体腐蚀现象。
72.对比例2
73.本实施例的基体材料为镀锌钢接地极材料,在该基体上制备涂层的方法按以下步骤进行:
74.(1)纳米复合材料制备:以质量计,将85g纳米二氧化钛、10g氧化石墨烯、5g peg-800分散剂加入到球磨罐中,并加入无水乙醇进行湿法球磨,球磨时间6h。球磨完成后,放入80℃鼓风干燥箱烘干干燥获得氧化石墨烯包覆的纳米二氧化钛粒子;其中,纳米二氧化钛粒径为25nm,氧化石墨烯粒径为5~50nm,层数5~10层。
75.(2)涂料制备:按质量分数将30%上述纳米复合材料,8%聚苯胺,50%氟树脂,10%n,n-二甲基乙酰胺,2%助剂(1%聚二甲基硅氧烷,1%byk333)加入到容器中,然后利用超声破碎仪对其进行分散,得到涂料;其中,超声破碎仪频率25khz,功率800w,超声运行方式1s停2s,时间20min。
76.(2)基体预处理:将基体依次用酒精、丙酮清洗数次去除油污,然后使用32目棕刚玉砂对基体进行喷砂处理;
77.(3)涂层制备:以步骤(1)制备的涂料为原料,采用气雾喷涂方式在步处理后的基体表面进行涂层制备,获得厚度为240mm的超疏水耐蚀涂层。其中喷涂参数为:气压为0.4mpa,喷涂距离为150mm,流量40ml/min,雾化嘴1.3mm,喷枪速度150mm/s,涂层喷涂遍数
10遍。
78.对本实施例制备的涂层进行水接触角测试、导电性能测试及耐腐蚀性能测试。水接触角为140
°
左右,其涂层超疏水功能良好;导电性能测试结果表明,涂层体积电阻率820ω.m,导电性一般,不能满足实际使用要求。中性盐雾试验2000h后,涂层且未发生明显的基体腐蚀现象。
79.对比例3
80.本实施例的基体材料为镀锌钢接地极材料,在该基体上制备涂层的方法按以下步骤进行:
81.(1)纳米复合材料制备:以质量计,将85g纳米二氧化钛、10g氧化石墨烯、5g peg-800分散剂加入到球磨罐中,并加入无水乙醇进行湿法球磨,球磨时间6h。球磨完成后,放入80℃鼓风干燥箱烘干干燥获得氧化石墨烯包覆的纳米二氧化钛粒子;其中,纳米二氧化钛粒径为25nm,氧化石墨烯粒径为5~50nm,层数5~10层。
82.(2)涂料制备:按质量分数将50%上述纳米复合材料,20%聚苯胺,20%氟树脂,10%n,n-二甲基乙酰胺,2%助剂(1%聚二甲基硅氧烷,1%byk333)加入到容器中,然后利用超声破碎仪对其进行分散,得到涂料;其中,超声破碎仪频率25khz,功率800w,超声运行方式1s停2s,时间20min。
83.(2)基体预处理:将基体依次用酒精、丙酮清洗数次去除油污,然后使用32目棕刚玉砂对基体进行喷砂处理;
84.(3)涂层制备:以步骤(1)制备的涂料为原料,采用气雾喷涂方式在步处理后的基体表面进行涂层制备,获得厚度为240mm的超疏水耐蚀涂层。其中喷涂参数为:气压为0.4mpa,喷涂距离为150mm,流量40ml/min,雾化嘴1.3mm,喷枪速度150mm/s,涂层喷涂遍数10遍。
85.对本实施例制备的涂层进行水接触角测试、导电性能测试及耐腐蚀性能测试。水接触角为120
°
左右,其涂层超疏水功能一般;导电性能测试结果表明,涂层体积电阻率780ω.m,导电性一般,不能满足实际使用要求。中性盐雾试验2000h后,涂层发生明显的基体腐蚀现象,主要树脂含量偏少,高固组份下,涂层裂纹孔隙多,涂层不连续,致密度差。
86.上述实施例防腐蚀性能的测试方法为:盐雾试验,具体根据标准iso 9227:1990《人造气氛腐蚀试验-盐雾试验》进行:根据标准要求,试验采用去离子水配制的化学纯nacl溶液,浓度为50g/l
±
5g/l,用盐酸或氢氧化钠调整溶液ph值在6.5~7.2之间;在25℃时,配置的氯化钠溶液的密度在1.0255~1.0400g/cm3范围内;将试样放置在角度为45
°
的标准塑料支架上;盐雾试验周期依据所检测样品确定,中间检查为12小时一次,样品取出频率与试验周期相同;盐雾箱内温度为35
±
2℃,喷雾空气压力为1kgf/cm2,通过调节盐雾沉降的速度,经24h喷雾后每80cm2面积上为1~2ml/h;利用数码相机对盐雾试验样品进行腐蚀形貌观察。
87.超疏水功能的验证方法为:利用接触角测试仪对涂层样品进行表面的水接触角测试,以考察其超疏水功能。
88.涂层的导电性能的测试方法为:根据hg/t 3331-2012标准,测试涂层的体积电阻率,以评价其导电功能是否满足接地极行业要求。
89.盐雾试验结果表明,具备本发明制备的超疏水耐蚀涂层的样品可耐中性盐雾试验
2000h,且未发生基体腐蚀现象。
90.接触角测试结果表明,本发明制备的超疏水耐蚀涂层其水接触角140~160
°
,具备良好的疏水功能,有利于涂层的耐腐蚀性能提升。
91.导电性能测试结果表明,本发明制备的超疏水耐蚀涂层具有较低的电阻,体积电阻率为15~38ω.m,具有良好的导电率,满足实际使用要求。