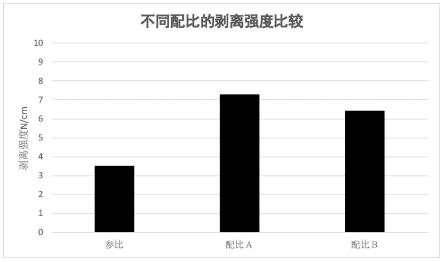
1.本发明涉及质子交换膜燃料电池、液流电池领域,具体涉及一种膜电极用胶粘剂及膜电极制备方法。
背景技术:2.燃料电池能够将燃料和氧化剂的化学能转换为电能,其能量转换效率不受卡诺热机循环理论效率的限制,具有高效、环境友好、安静、可靠性高等优点,在众多领域具有广阔的发展前景。
3.其中质子交换膜燃料电池功率密度高、启动快、对负载变化响应快,成为交通运输领域能源重要发展方向。燃料电池是几十至几百个膜电极的组合体,膜电极是燃料电池电堆的心脏,其性能和使用寿命决定了燃料电池的使用条件和寿命,在电池的运行过程中,只要有任何一个膜电极出现损坏及漏气,整个电池就不能工作。膜电极作为燃料电池的核心组件,主要由阳极气体扩散层、阳极催化剂层、质子交换膜、阴极催化剂层和阴极气体扩散层组成。当前膜电极的主流封装方法是双边框封装法,首先在质子交换膜的两面分别涂布阳极催化剂层和阴极催化剂层,制备出具有三层结构的催化剂涂布膜,然后把催化剂涂布膜的边缘与两个边框边缘通过胶粘剂粘接密封起来,形成一个五层组件,最后两层气体扩散层分别通过胶粘剂来粘接边框,形成七层的膜电极。现有技术中也有采用单边框封装技术的膜电极,但是无论是制备双边框结构的膜电极还是单边框结构的膜电极,都需要使用胶粘剂。胶粘剂在膜电极中不仅起到粘接固定作用,还起到密封作用,防止燃料电池在运行过程中出现催化剂涂布膜损坏及漏气现象,因此,胶粘剂的粘接性和稳定性对膜电极的性能和使用寿命有很大影响。胶粘剂的成分一般是高分子聚合物。在燃料电池运行过程中,氢气和氧气在铂金催化剂的作用下产生过氧化氢,过氧化氢与膜电极中的金属离子杂质反应产生自由基,从而攻击胶粘剂的高分子链,使胶粘剂发生降解从而失效,导致膜电极气密性降低,而且,胶粘剂降解产生的中间体或者产物可能会毒化燃料电池催化剂以及降解质子交换膜,进而影响膜电极的性能和使用寿命。
4.目前出现一些将添加剂用于膜电极各层的活性区域内的技术,这些添加剂可清除反应时产生的过氧化氢和自由基。然而,由于膜电极的活性区域和粘接区域的环境不一样,这些添加剂在其中存在的方式也不同,而且添加在活性区域的添加剂扩散速度及流失速度较快,难以对膜电极起到长时间的保护,难以大幅提高燃料电池的寿命。中国专利“一种膜电极用胶粘剂及膜电极”(公开号:cn113736390a,申请日:2021.09.03)公开了一种胶粘剂,胶粘剂中添加的有机光敏剂既可促进胶粘剂交联固化,提高其固化效率,又可作为自由基捕捉剂消灭燃料电池运行过程中产生的自由基。但是,对于边框的基材必须选择透光性良好的材料、边框处的质子膜必须是留白的(透明无催化剂),具有更高耐久性优势的聚酰亚胺和聚苯硫醚等无法使用。
技术实现要素:5.本发明的目的就是为了克服上述现有技术存在的缺陷而提供一种膜电极用胶粘剂,该胶粘剂适合各种基膜使用、稳定性高、成本低、固化方式灵活,制备出的膜电极既能保证具有很好的粘结力、气密性,又能耐受运行中各种环境,不需要大规模的提高工艺设备即可实现,成本低适合规模化生产。
6.本发明技术原理如下:
7.燃料电池膜电极边框的主要功能包括为膜电极活性区提供支撑、气体密封和冷却液密封及绝缘作用。常用的膜电极边框构成:质子交换膜或者双侧涂有催化剂的质子交换膜,双侧与含胶粘剂的基膜粘而成的。由于燃料电池的运行环境是一个高温、高湿度、酸性、自由基和防冻液的环境,因此对胶粘剂材料要求非常高。材料除了要耐受上述环境之外,边框中胶粘剂固化后还要保证一定的韧性。
8.根据本发明的第一个方面,本发明提供了一种固化胶粘剂,包括胶粘剂本体、改性助剂、自由基淬灭剂和有机溶剂;所述的改性助剂为含有共轭双键的聚合物;所述自由基淬灭剂为含有金属离子的金属配合物的一种或多种混合物,和/或含有金属离子的硬脂酸盐中的一种或多种混合物。
9.优选地,所述胶粘剂本体包括酚醛树脂、聚氨酯、聚丙烯酸酯、聚环氧丙烯酸酯中的一种或多种混合物。
10.优选地,所述改性助剂包天然橡胶、合成橡胶、环氧橡胶、丁苯橡胶。
11.优选地,所述金属离子为铈离子、锰离子或钴离子的一种或多种。
12.优选地,所述含有金属离子的硬脂酸盐为硬脂酸铈、钴的一种或两种混合物。
13.优选地,所述改性助剂的添加量为胶粘剂本体质量的5%~30%。
14.优选地,所述自由基淬灭剂添加量为胶粘剂本体质量的0.1%~5%。
15.优选地,所述有机溶剂为烷基酮或烷基酸酯;所述烷基酮为丙酮、丁酮、氮甲基吡咯烷酮;所述烷基酸酯为乙酸乙酯、乙酸异丙酯;
16.根据本发明的第二个方面,本发明提供了一种膜电极,包括边框和膜电极本体,所述边框和膜电极本体通过上述固化胶粘剂粘接,所述膜电极本体和边框的粘结通过热压、微波方式进行固化。
17.优选地,所述膜电极本体是层叠的阳极气体扩散层、质子交换膜和阴极气体扩散层,所述质子交换膜在设置所述阳极气体扩散层的一侧涂布阳极催化剂层,在另一侧涂布阴极催化剂层。
18.优选地,所述热压温度为60-150℃或微波功率为300-1500w。
19.本发明主要实现方式:
20.s1:原胶的制备:将胶粘剂,改性助剂及淬灭剂充分混合,并加入适量溶剂调整到合适的粘度范围;静置,真空脱气泡;
21.s2:单层边框制备:将基膜水平置于基台上,s1胶水从刮刀处沿着传动方向刮涂,在基膜上形成固定厚度的胶层;该胶层经过溶剂去除,预固化及收卷得到单层边框膜。
22.s3:膜电极的制造:将已涂覆有阴阳极催化剂的膜材料,与裁切后的单层边框在适当温度下进行粘合,再转移到另一工序,在另一侧同样复合单层边框,充分固化,随后依次将阴阳极的gdl进行粘贴,即得到复合膜电极组件(mea)。
23.本发明通过在高稳定性的酚醛树脂中加入橡胶作为助剂,调节粘结剂的韧性;加入自由基淬灭剂来提高化学耐久性;微波固化工艺进一步提高批量生产效率、降低成本。
24.与现有技术相比,本发明具有如下优点:
25.1、酚醛树脂中加入柔性的橡胶作为助剂,有助于形成柔性的聚合物分子链段,提高胶粘剂的韧性,满足卷对待(r2r)连续化生产要求。
26.2、胶粘剂中的自由基淬灭剂,能够将反应中的自由基捕获,降低胶层、基材和活性区的分解,提高膜电极的耐受性;
27.3、采用微波固化方法,通过分子的内部膨胀反应,固化充分、均匀、时间短、成本低。
附图说明
28.图1为不同胶层配方的粘结性能对比;
29.图2为本发明燃料电池用膜电极边框的制备工艺流程,其中标注1-6分别为:1、上胶;2、刮涂;3、干燥;4、预固化;5、冲切;6、收装。
具体实施方式
30.本发明实施例中性能测试方法:
31.1)粘接强度测试方法:将单层边框,裁切为宽为2cm的长条,将两片边框胶层相对进行热压(120℃@3min),使用万能试验机测试将两片粘接后的边框材料之间的剥离强度,来表征胶粘剂的粘接性能。
32.2)耐受测试方法:称取初重量为1.5g的上述胶膜置于100ml烧杯中,再取30ml的10%h2o2以及称取0.7克新鲜配制的0.1%feso4溶液加入烧杯中(烧杯中混合溶液中的fe
2+
的浓度为10ppm)后,将烧杯置于90℃恒温环境下反应3h,反应完毕后,取出胶膜,用大量超纯水多次冲洗胶膜去除胶膜表面的h
2 o2和fe
2+
等残余物质,然后使胶膜在80℃下真空干燥过夜,称量胶膜质量得终重量数值,根据初重量数值和终重量数值计算出胶膜的重量损失比。
33.实施例1
34.原胶的制备(配比a):将粘接剂酚醛树脂50g,天然橡胶20g,丁酮50ml,硬脂酸铈0.15g充分搅拌混合,分散均匀,配置成原液胶水。
35.单层边框制备:将基膜pen(聚萘二甲酸乙二醇酯,东洋纺制造)水平置于基台上,上胶水从刮刀处沿着传动方向刮涂,在基膜上形成固定厚度40um的胶层;该胶层经过高温(70℃@30min)脱除溶剂丁酮,预固化(温度90℃@5min)及收卷得到单层边框膜。经过双层边框胶层热压固化,再进行边框的剥离强度测试,剥离力7.0n/cm。
36.膜电极的制造:将已涂覆有阴阳极催化剂的膜材料,与裁切后的单层边框在120℃温度下进行粘合,再转移到另一工序,在另一侧同样复合单层边框,充分固化(固化温度140℃),随后依次将阴阳极的gdl(气体扩散层)进行粘贴,即得到复合膜电极组件(mea)。
37.实施例2
38.原胶的制备(配比b):将粘接剂聚环氧丙烯酸酯60g,合成橡胶15g,乙酸乙酯45ml,硬脂酸铈0.2g充分搅拌混合,分散均匀,配置成原液胶水。
39.单层边框制备:将基膜pps(聚苯硫醚,日本东丽制造)水平置于基台上,上胶水从刮刀处沿着传动方向刮涂,在基膜上形成固定厚度60um的胶层;该胶层经过高温处理(75℃@20min)去除溶剂乙酸乙酯,预固化(微波800w@2min)及收卷得到单层边框膜。经过双层边框胶层热压固化,再进行边框的剥离强度测试,剥离力6.5n/cm。
40.膜电极的制造:将已涂覆有阴阳极催化剂的膜材料,与裁切后的单层边框在110℃温度下进行粘合,再转移到另一工序,在另一侧同样复合单层边框,充分固化(固化温度120℃),随后依次将阴阳极的gdl进行粘贴,即得到复合膜电极组件。
41.对比例(参比)
42.原胶的制备:将粘接剂聚氨酯60g,乙酸乙酯45ml,分散均匀,配置成原液胶水。
43.单层边框制备:将基膜pen(聚萘二甲酸乙二醇酯,东洋纺制造)水平置于基台上,上胶水从刮刀处沿着传动方向刮涂,在基膜上形成固定厚度40um的胶层;该胶层经过高温处理(75℃@20min)去除溶剂乙酸乙酯,预固化(85℃@2min)及收卷得到单层边框膜。边框的剥离强度测试,剥离力3.5n/cm。
44.膜电极的制造:将已涂覆有阴阳极催化剂的膜材料,与裁切后的单层边框在90℃温度下进行粘合,再转移到另一工序,在另一侧同样复合单层边框,充分固化(固化温度120℃),随后依次将阴阳极的gdl进行粘贴,即得到复合膜电极组件。
45.实施例1-2及其对比例边框的剥离强度测试结果表明(如图1所示),实施例1中方法制备得到的边框材料,在实际使用的过程中,即双层边框胶层相对热压后,保持较高的剥离强度,达到很好的密封强度。同样的,使用实施例2的方法,所得的剥离强度也是明显优于对比例。从上述的实施例1和2表明,本案发明的边框材料具有优异的剥离强度,提高燃料电池的气密性。
46.上述实施例为本发明较佳的实施方式,但本发明的实施方式并不受上述实施例的限制,其他的任何未背离本发明的精神实质与原理下所作的改变、修饰、替代、组合、简化,均应为等效的置换方式,都包含在本发明的保护范围之内。