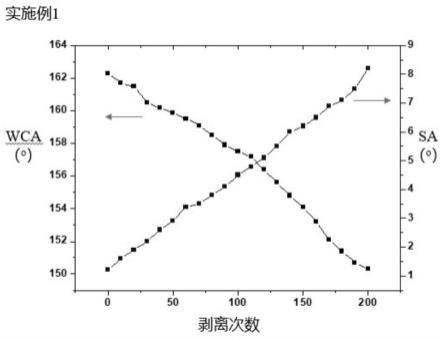
1.本发明涉及防水与防护涂料技术领域,具体涉及一种超耐磨超疏水涂料及其制备方法与应用。
2.
背景技术:3.超疏水材料因具有油水分离、防霜抗冻、金属防腐、水汽收集、节能减阻、防污防尘、木材防霉、防生物粘附、自清洁等功能而具有广阔的应用前景。然而,超疏水表面不可避免地会受到外界复杂因素(氧化、腐蚀性介质、机械摩擦等)的影响。尤其地,机械摩擦作用会破坏超疏水表面的微观粗糙结构,导致材料丧失超疏水性。较差的耐久性和较短的使用寿命极大地限制了超疏水材料的工程应用。因此,提高超疏水材料的耐磨性,对突破限制超疏水材料应用的技术瓶颈具有重大意义,也是目前的研究热点之一。
4.公开号为cn 113896430 a的中国专利申请文献公开了一种胶黏剂复合耐磨超疏水涂层及其制备方法,具体公开了一种以胶黏剂为辅助涂层的无氟超疏水涂层。胶黏剂强力的粘接作用可以将疏水纳米粒子与基底牢固地附着在一起从而提升涂层的耐磨性。涂层在经受50次剥离测试后,虽然有部分区域受损严重,但表面仍能使水珠轻松滚下,滚动角《8
°
。公开号为cn 112898886 a的中国专利申请文献公开了一种防腐防冰耐磨超疏涂层及其制备方法,具体公开了一种耐磨性纳米sio2粒子和弹性tpu涂层协同作用提升超疏水涂层耐磨性的方法。本身具有一定的耐磨性的纳米sio2粒子半嵌入具有一定弹性的tpu涂层表面,使得外界物体不会直接作用于tpu涂层,而是首先触及到纳米sio2粒子。因此,该涂层的耐磨性得到了显著提升。然而,这些传统的制备超疏水涂层的方法中,都是以物理共混的方法将纳米粒子掺杂到树脂体系中,导致超疏水涂层的耐磨性提升有限。
5.公开号为cn 113637401 a的中国专利申请公开了一种双组份耐磨超疏水涂料的制备方法及应用,具体公开了一种基于金属有机框架(mof)材料的耐磨超疏水涂层。功能化的mof和氨基化的硅油先通过共价键预接枝在树脂骨架上,然后再与固化剂固化。涂料固化后漆膜自上而下都有粗糙结构和低表面能的组分,磨损后表面仍能露出新的表面继续发挥超疏水效应。使用2000目砂纸以100 g砝码负重摩擦7.6 m后接触角150
°
,滚动角8
°
,耐磨性优异。然而,由于所使用的mof uio-66粒径~180 nm,涂层固化后只能形成微米级的粗糙结构,而无法形成纳米级的粗糙结构,导致涂层的超疏水性提升有限。
6.
技术实现要素:7.解决的技术问题:针对现有技术中存在超疏水涂层的耐磨性和耐久性有待于提升的问题,本发明提供一种超耐磨超疏水涂料及其制备方法与应用,所述超耐磨超疏水涂料是将改性二氧化硅纳米粒子、改性二氧化硅微米粒子和氨基硅油引入到氟树脂中,然后再与固化剂反应获得,本发明所述方法不同于传统的物理共混方法,改性二氧化硅纳米粒子、
8014、毕克化学公司的byk-085和byk-088中的至少一种。
15.基于上述一种超耐磨超疏水涂料的制备方法,步骤如下:步骤一.a组分改性氟树脂的制备:将羟基氟树脂、氨基硅油、改性二氧化硅纳米粒子、改性二氧化硅微米粒子、润湿分散剂和环保型稀释剂混合均匀得到改性氟树脂;步骤二. b组分固化剂的制备:将脂肪族异氰酸酯和助剂用环保型稀释剂混合分散均匀,得到含活性氢树脂组分;步骤三.将a组分和b组分按照质量比混合均匀后施工即可。将涂料均匀涂覆于经过处理的基面,所述经过处理的基面为经表面清洁、抛丸处理、坑洞修补、涂刷底漆等工艺处理后的混凝土或金属基面。
16.基于上述超耐磨超疏水涂料在制备混凝土、金属及木材表层防水、防腐、抗污涂层中的应用。
17.作为优选,所述涂层施工方式为喷涂、刷涂或滚涂施工,涂布厚度为1.5-3.0 mm,单遍涂覆厚度为0.5~1 mm,两遍以上施工,喷涂工艺条件为:气压0.6mpa、喷枪与基面间隔15cm、喷涂时间为10s、均匀涂布。
18.有益效果:本发明提供一种制备简便的超耐磨超疏水涂料,通过ydh-660改性二氧化硅纳米/微米粒子,形成氨基功能化的改性二氧化硅纳米/微米粒子;利用改性二氧化硅纳米粒子和改性二氧化硅微米粒子分别形成表面的纳米尺度和微米尺度的粗糙结构,利用硅油中的聚硅氧烷链段和氟树脂中的碳氟链段降低表面张力,形成具有超疏水性的涂层,达到超疏水和抗污的效果;利用氨基与固化剂聚异氰酸酯的化学反应将改性二氧化硅纳米/微米粒子和氨基硅油共价接枝到树脂基体,形成超耐磨的超疏水涂层表面。本发明所述方法不同于传统的物理共混方法,改性二氧化硅纳米粒子、改性二氧化硅微米粒子和氨基硅油以共价键的形式连接到树脂基体中,极大提升了超疏水涂层的耐磨性和耐久性,具有制备简便、同时兼具防水及防腐等优点。
19.附图说明
20.图1为实施例1的超疏水涂层耐磨性变化趋势图。
21.图2为对比例1的超疏水涂层耐磨性变化趋势图。
22.图3为实施例2的超疏水涂层耐磨性变化趋势图。
23.图4为对比例2的超疏水涂层耐磨性变化趋势图。
具体实施方式
24.下面结合附图和具体实施例对本发明作进一步描述,并不代表对本发明技术方案的限制。
25.本发明说明书实施例中原料与试剂均为工业级,市售可得。
26.实施例中部分原材料的厂家及型号如下:1、二氧化硅纳米粒子(1)型号999121,北京百灵威科技有限公司,粒径~20 nm;(2)型号972472,北京百灵威科技有限公司,粒径~40 nm;
2、二氧化硅微米粒子(1)型号s5505,北京百灵威科技有限公司,粒径0.2~0.3
ꢀµ
m;(2)型号2748684,北京百灵威科技有限公司,粒径0.2~0.8
ꢀµ
m;3、羟基氟树脂(1)gk570,大金氟化工(中国)有限公司,羟值60
±
5 mgkoh/g;(2)jf-2x,三爱富中昊化工新材料有限公司,羟值50
±
5 mgkoh/g;4、氨基硅油(1)hy-2300,上海荟研新材料有限公司,粘度60-150cp,25℃;(2)ofx-8040a,陶氏化学,粘度800-5000cp,25℃;5、脂肪族异氰酸酯(1)hdi,巴斯夫(中国)有限公司生产,工业品名为basonat hb 175mp/x cn,nco含量为16~17%;(2)n3390,拜耳(中国)有限公司生产,工业品名为desmodur
®ꢀ
n3390,nco含量为(19.6
±
0.3)%;6、润湿分散剂:(1)毕克化学公司生产、型号为byk-163(以下简称“byk-163”);(2)毕克化学公司生产、型号为byk-p104s(以下简称“byk-p104s”);7、环保型稀释剂:(1)碳酸丙酯,百灵威科技有限公司生产、工业级;(2)丁二甲酸二甲酯,百灵威科技有限公司生产、工业级;8、流平剂:(1)毕克化学公司生产、型号为byk-306(以下简称“byk-495”);(2)毕克化学公司生产、型号为byk-333(以下简称“byk-333”);9、消泡剂:(1)陶氏化学公司生产、型号为af-80144(以下简称“af-8014”);(2)毕克化学公司生产、型号为byk-088(以下简称“byk-088”)。
27.实施例1本实施例中所述超耐磨超疏水涂料的制备方法如下:将3 g二氧化硅纳米粒子(型号999121)/微米粒子(型号s5505)和丙酮(100 ml)加入250 ml圆底烧瓶中,超声分散30 min。然后,将γ-氨丙基甲基二甲氧基硅烷(ydh-660,1g)加入反应瓶中,电磁搅拌2 h之后离心(2000 r/min,10 min)并收集固体沉淀物。最后,用丙酮洗涤干燥即得到改性二氧化硅纳米/微米粒子。
28.在机械分散搅拌器开启1000 r/min的条件下依次加入10 g环保型稀释剂丁二甲酸二甲酯、65g羟基氟树脂gk570、1g润湿分散剂byk-163、9g改性二氧化硅纳米粒子、3g改性二氧化硅微米粒子和12g氨基硅油hy-2300,继续搅拌30min,得到a组分改性氟树脂;在烧杯中依次加入12g固化剂hdi、16g环保型稀释剂碳酸丙酯、15.5g钛白粉r-902、0.5g炭黑、5g粉体填料、0.5g流平剂byk-306、0.5g消泡剂af-8014,室温下2000r/min搅拌1h得到b组分固化体系;将a组分与b组分按照质量比为2:1混合均匀后,喷涂于处理后的混凝土基面上得到超耐磨超疏水涂层。然后通过剥离测试,并测定接触角和滚动角,以表征涂层的耐磨性。
29.对比例1在机械分散搅拌器开启1000r/min的条件下依次加入10g环保型稀释剂丁二甲酸二甲酯、65g羟基氟树脂gk570、1g润湿分散剂byk-163、9g未改性二氧化硅纳米粒子(型号999121)、3g未改性二氧化硅微米粒子(型号s5505)和12g氨基硅油hy-2300,继续搅拌30min,得到a组分改性氟树脂;在烧杯中依次加入12g固化剂hdi、16g环保型稀释剂碳酸丙酯、15.5g钛白粉r-902、0.5g炭黑、5g粉体填料、0.5g流平剂byk-306、0.5g消泡剂af-8014,室温下2000r/min搅拌1h得到b组分固化体系;将a组分与b组分按照质量比为2:1混合均匀后,喷涂于处理后的混凝土基面上得到超耐磨超疏水涂层。然后通过剥离测试,并测定接触角和滚动角,以表征涂层的耐磨性。
30.实施例2将3g二氧化硅纳米粒子(型号972472)/微米粒子(型号2748684)和丙酮(100 ml)加入250 ml圆底烧瓶中,超声分散30 min。然后,将γ-氨丙基甲基二甲氧基硅烷(ydh-660,1g)加入反应瓶中,电磁搅拌2h之后离心(2000 r/min,10min)并收集固体沉淀物。最后,用丙酮洗涤干燥即得到改性的二氧化硅纳米/微米粒子。
31.在机械分散搅拌器开启1000r/min的条件下依次加入10g环保型稀释剂丁二甲酸二甲酯、65g羟基氟树脂jf-2x、1g分散剂byk-p104s、3g改性二氧化硅纳米粒子、9g改性二氧化硅微米粒子和12g氨基硅油ofx-8040a,继续搅拌30min,得到a组分改性氟树脂;在烧杯中依次加入8g固化剂n3390、20g环保型稀释剂碳酸丙酯、15.5g钛白粉r-902、0.5g炭黑、5g粉体填料、0.5g流平剂byk-333、0.5g消泡剂byk-088,室温下2000r/min搅拌1h得到b组分固化体系;将a组分和b组分按照质量比为2:1混合均匀后,喷涂于处理后的金属基面上得到超耐磨超疏水涂层。然后通过剥离测试,并测定接触角和滚动角,以表征涂层的耐磨性。
32.对比例2在机械分散搅拌器开启1000r/min的条件下依次加入10g环保型稀释剂丁二甲酸二甲酯、65g羟基氟树脂jf-2x、1g分散剂byk-p104s、3g未改性二氧化硅纳米粒子、9g未改性二氧化硅微米粒子和12g氨基硅油ofx-8040a,继续搅拌30min,得到a组分改性氟树脂;在烧杯中依次加入8g固化剂n3390、20g环保型稀释剂碳酸丙酯、15.5g钛白粉r-902、0.5g炭黑、5g粉体填料、0.5g流平剂byk-333、0.5g消泡剂byk-088,室温下2000r/min搅拌1h得到b组分固化体系;将a组分和b组分按照质量比为2:1混合均匀后,喷涂于处理后的金属基面上得到超耐磨超疏水涂层。然后通过剥离测试,并测定接触角和滚动角,以表征涂层的耐磨性。
33.对比例3将3 g二氧化硅纳米粒子(型号999121)和丙酮(100 ml)加入250 ml圆底烧瓶中,超声分散30 min。然后,将γ-氨丙基甲基二甲氧基硅烷(ydh-660,1g)加入反应瓶中,电磁搅拌2 h之后离心(2000 r/min,10 min)并收集固体沉淀物。最后,用丙酮洗涤干燥即得到改性二氧化硅纳米粒子。
34.在机械分散搅拌器开启1000 r/min的条件下依次加入13 g环保型稀释剂丁二甲酸二甲酯、65g羟基氟树脂gk570、1g润湿分散剂byk-163、9g改性二氧化硅纳米粒子和12g氨基硅油hy-2300,继续搅拌30min,得到a组分改性氟树脂;在烧杯中依次加入12g固化剂hdi、16g环保型稀释剂碳酸丙酯、15.5g钛白粉r-902、0.5g炭黑、5g粉体填料、0.5g流平剂byk-306、0.5g消泡剂af-8014,室温下2000r/min搅拌1h得到b组分固化体系;将a组分与b组分按
照质量比为2:1混合均匀后,喷涂于处理后的混凝土基面上得到超耐磨超疏水涂层。然后通过剥离测试,并测定接触角和滚动角,以表征涂层的耐磨性。
35.对比例4将3 g二氧化硅微米粒子(型号s5505)和丙酮(100 ml)加入250 ml圆底烧瓶中,超声分散30 min。然后,将γ-氨丙基甲基二甲氧基硅烷(ydh-660,1g)加入反应瓶中,电磁搅拌2 h之后离心(2000 r/min,10 min)并收集固体沉淀物。最后,用丙酮洗涤干燥即得到改性二氧化硅微米粒子。
36.在机械分散搅拌器开启1000 r/min的条件下依次加入19 g环保型稀释剂丁二甲酸二甲酯、65g羟基氟树脂gk570、1g润湿分散剂byk-163、3g改性二氧化硅微米粒子和12g氨基硅油hy-2300,继续搅拌30min,得到a组分改性氟树脂;在烧杯中依次加入12g固化剂hdi、16g环保型稀释剂碳酸丙酯、15.5g钛白粉r-902、0.5g炭黑、5g粉体填料、0.5g流平剂byk-306、0.5g消泡剂af-8014,室温下2000r/min搅拌1h得到b组分固化体系;将a组分与b组分按照质量比为2:1混合均匀后,喷涂于处理后的混凝土基面上得到超耐磨超疏水涂层。然后通过剥离测试,并测定接触角和滚动角,以表征涂层的耐磨性。
37.对比例5将3 g二氧化硅纳米粒子(型号999121)/微米粒子(型号s5505)和丙酮(100 ml)加入250 ml圆底烧瓶中,超声分散30 min。然后,将γ-氨丙基甲基二甲氧基硅烷(ydh-660,1g)加入反应瓶中,电磁搅拌2 h之后离心(2000 r/min,10 min)并收集固体沉淀物。最后,用丙酮洗涤干燥即得到改性二氧化硅纳米/微米粒子。
38.在机械分散搅拌器开启1000 r/min的条件下依次加入22 g环保型稀释剂丁二甲酸二甲酯、65g羟基氟树脂gk570、1g润湿分散剂byk-163、9g改性二氧化硅纳米粒子和3g改性二氧化硅微米粒子,继续搅拌30min,得到a组分改性氟树脂;在烧杯中依次加入12g固化剂hdi、16g环保型稀释剂碳酸丙酯、15.5g钛白粉r-902、0.5g炭黑、5g粉体填料、0.5g流平剂byk-306、0.5g消泡剂af-8014,室温下2000r/min搅拌1h得到b组分固化体系;将a组分与b组分按照质量比为2:1混合均匀后,喷涂于处理后的混凝土基面上得到超耐磨超疏水涂层。然后通过剥离测试,并测定接触角和滚动角,以表征涂层的耐磨性。
39.上述实施例和对比例所得a组分和b组分,将所述a组分与b组分混合均匀后,涂附于基面上,形成超疏水涂层;通过剥离测试和sdc-100型号接触角测量仪测定涂层对水的接触角,表征涂层的耐磨性。测定时,利用接触角测量仪将10μl水或正己烷滴在材料表面,测量基板的4个角及中心处共5个点的接触角,取平均值作为此板的接触角值;用以判断下述实施例和对比例的超疏水性能。通过其接触角值随着剥离次数的变化,绘制其变化趋势图,判断其超疏水涂层的耐磨性。
40.表1 实施例及对比例的接触角
由上述实施例1~2中可以看出,所得的超耐磨超疏水涂层静态水接触角可提高至163.5o。参见附图1-附图4,与对比例1和对比例2比较,实施例1和实施例2中涂层的耐磨性可以提升至180次剥离实验以上,说明通过共价键的策略将改性二氧化硅纳米/微米粒子和氨基硅油接枝到树脂基体中可以显著提升超疏水涂层的耐磨性。
41.从对比例3~5的结果可以看出,与实施例1相比,改性二氧化硅纳米粒子与改性二氧化硅微米粒子协同作用,在涂层的表面形成微/纳粗糙结构;氨基硅油的引入可通过硅氧烷降低涂层表面能;涂层表面的微/纳粗糙结构和低表面能特性是涂层超疏水性的重要因素。