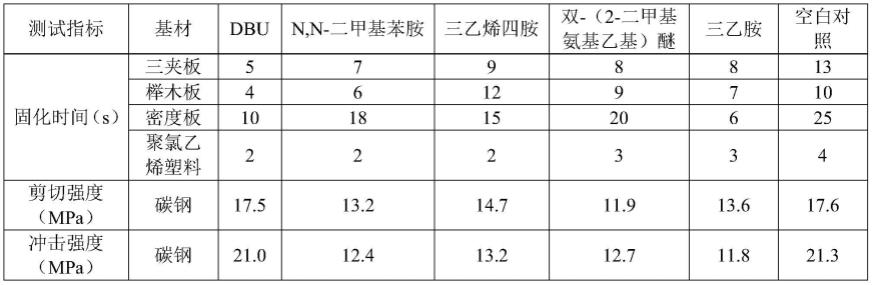
1.本发明涉及强力胶技术领域,具体而言,涉及一种强力胶加速剂。
背景技术:2.强力胶,也叫瞬干胶,主要成分为氰基丙烯酸酯,是一种常见的单组份胶粘剂,具有使用方便,可室温固化,粘接速度快,粘接材料广泛等优点。然而,由于强力胶是通过阴离子聚合反应固化的,在某些界面,如木质基材上,其固化速度会明显变慢,影响它的进一步推广使用。为了解决这个问题,目前的方案主要有两种,一种是在胶里面添加醚类、醇类等物质,来提高体系的亲水性;另一种方案,是在基材表面上使用胺类物质。然而,通常使用的胺类物质,如n,n-二甲基苯胺,三乙烯四胺,双-(2-二甲基氨基乙基)醚等,虽然能够加快固化速度,却会影响最终的粘接强度。
3.聂聪等的《促进剂在α-氰基丙烯酸酯胶粘剂中的应用研究》考察了18-冠-6对强力胶的固化速率的影响,但是该体系的粘接强度低于无加速体系;刘洁等在《缩短α-氰基丙烯酸酯胶粘剂固化时间的研究》中发现,采用70~100℃加热可有效提高强力胶固化速度,但是胶层容易变脆,而且不适用于实际生活中的应用。因此对于强力胶,添加促进剂来加速固化仍是首要选择。
4.针对现有技术中存在的问题,急需找到更合适的促进剂来加速固化,并且不会影响强力胶的粘结强度等性能。
技术实现要素:5.为解决现有技术存在的问题,本发明提供一种强力胶加速剂,包括1,8-二氮杂双环[5.4.0]十一碳-7-烯(dbu)和能溶解dbu的溶剂,通过在木质基材表面预先涂覆一层强力胶加速剂,干燥后再涂覆强力胶,能显著缩短强力胶在木质基材界面上的固化速度,加速效果明显,并且不会降低强力胶的粘结性能。
[0006]
一方面,本发明提供了一种强力胶加速剂,包括1,8-二氮杂双环[5.4.0]十一碳-7-烯(dbu)和溶剂,所述溶剂能溶解1,8-二氮杂双环[5.4.0]十一碳-7-烯;强力胶为氰基丙烯酸酯胶。
[0007]
本发明所述强力胶是指以α-氰基丙烯酸酯为主要成分,并添加稳定剂(如对苯二酚)、增稠剂(如pmma)等添加剂制备的α-氰基丙烯酸酯胶。
[0008]
强力胶是通过阴离子聚合反应固化的,在某些界面,如木材、纸张等基材上,其固化速度会明显变慢,因此通在木质基材上预先涂敷碱性的胺类物质,干燥后再涂覆强力胶,可以提升强力胶在木材表面的固化速度,但现有的胺类物质添加剂如n,n-二甲基苯胺,三乙烯四胺,双-(2-二甲基氨基乙基)醚,都会使强力胶的粘结强度降低,影响使用性能,且加速固化的效果也不够理想。本发明经大量研究发现,采用1,8-二氮杂双环[5.4.0]十一碳-7-烯代替现有的胺类物质,不仅能显著提升强力胶的固化速度,还不会降低强力胶的粘结性能,使强力胶固化后依然具有非常高的剪切强度、冲击强度和挠曲强度。
[0009]
在一些方式中,本发明提供的强力胶加速剂中也可以包含1,8-二氮杂双环[5.4.0]十一碳-7-烯(dbu)和其他胺类的混合物,只要在强力胶加速剂中含有dbu,都在本发明的保护范围内。
[0010]
进一步地,溶剂为正庚烷、正己烷或环戊烷中的任意一种或多种。
[0011]
1,8-二氮杂双环[5.4.0]十一碳-7-烯具有溶解性差的特点,因此需要选用合适的溶剂使其溶解,并且该溶剂需要有易挥发的特点,在涂覆木质基材表面后容易挥发,干燥后只留下1,8-二氮杂双环[5.4.0]十一碳-7-烯均匀覆盖在木质基材表面,之后再涂覆强力胶,加速强力胶固化,且不会影响强力胶的各项性能。
[0012]
进一步地,所述溶剂为正庚烷;按照质量百分比计算,所述1,8-二氮杂双环[5.4.0]十一碳-7-烯的质量占强力胶加速剂总质量的0.01~5.00%,所述正庚烷的质量占强力胶加速剂总质量的95.00~99.99%。
[0013]
进一步地,按照质量百分比计算,所述1,8-二氮杂双环[5.4.0]十一碳-7-烯的质量占强力胶加速剂总质量的0.5~1%,所述正庚烷的质量占强力胶加速剂总质量的99.00~99.50%。
[0014]
进一步地,按照质量百分比计算,所述1,8-二氮杂双环[5.4.0]十一碳-7-烯的质量占强力胶加速剂总质量的0.80%,所述正庚烷的质量占强力胶加速剂总质量的99.20%。
[0015]
另一方面,本发明提供了1,8-二氮杂双环[5.4.0]十一碳-7-烯用于制备强力胶加速剂的用途。
[0016]
进一步地,所述强力胶为氰基丙烯酸酯胶;所述加速剂中还包括溶剂,所述溶剂为正庚烷、正己烷或环戊烷中的任意一种或多种。
[0017]
进一步地,所述溶剂为正庚烷。
[0018]
进一步地,按照质量百分比计算,所述1,8-二氮杂双环[5.4.0]十一碳-7-烯的质量占强力胶加速剂总质量的0.01~5.00%,所述正庚烷的质量占强力胶加速剂总质量的95.00~99.99%。
[0019]
进一步地,按照质量百分比计算,所述1,8-二氮杂双环[5.4.0]十一碳-7-烯的质量占强力胶加速剂总质量的0.80%,所述正庚烷的质量占强力胶加速剂总质量的99.20%。
[0020]
再一方面,本发明提供了一种强力胶加速剂的制备方法,通过在正庚烷溶剂中加入适量dbu,搅拌均匀;适合的配方比为:1,8-二氮杂双环[5.4.0]十一碳-7-烯的质量占强力胶加速剂总质量的0.01~5.00%,其余为正庚烷。
[0021]
再一方面,本发明提供了一种强力胶加速剂的使用方法,先在基材表面预先涂覆一层强力胶加速剂,干燥后再涂覆强力胶。
[0022]
在一些方式中,所述基材为木质基材。
[0023]
在一些方式中,所述预先涂覆的强力胶加速剂的厚度为0.1~1mm。
[0024]
在一些方式中,所述干燥是指预先涂覆木质基材表面的强力胶加速剂干燥,此时其中的溶剂已完全挥发,剩余的1,8-二氮杂双环[5.4.0]十一碳-7-烯均匀覆盖木质基材表面。
[0025]
在一些方式中,所述预先涂覆木质基材表面的强力胶加速剂干燥时间为5~10s。
[0026]
再一方面,本发明提供了一种强力胶加速剂用于加速强力胶固化并保持粘结性能的用途,所述强力胶加速剂如上所述;所述强力胶为氰基丙烯酸酯胶。
[0027]
进一步地,所述强力胶加速剂能保持强力胶粘结性能降低粘结性能,是指强力胶固化后依然具有非常高的剪切强度、冲击强度和挠曲强度,具有非常好的耐湿热老化性能,胶层不会发脆。
[0028]
综上所述,本发明提供了一种新型强力胶加速剂,主要具备以下有益效果:
[0029]
1、显著提升强力胶在木质基材界面的固化速度;
[0030]
2、不会影响强力胶本身的性能,不会降低粘结性能;
[0031]
3、强力胶固化后依然具有非常高的剪切强度、冲击强度、挠曲强度,具有非常好的耐湿热老化性能,胶层不会发脆。
具体实施方式
[0032]
下面结合实施例对本发明作进一步详细描述,需要指出的是,以下所述实施例旨在便于对本发明的理解,而对其不起任何限定作用。
[0033]
以下实施例中的强力胶为圣戈班汇杰新材料有限公司生产的,型号tek 793的强力胶,其组成成分质量比为:氰基丙烯酸乙酯90~100%,对苯二酚<0.1%,超细pmma0~10%。
[0034]
实施例1本发明提供的强力胶加速剂的制备和使用
[0035]
本实施例提供的强力胶加速剂配方采用1,8-二氮杂双环[5.4.0]十一碳-7-烯(dbu,购自上海阿拉丁生化科技股份有限公司)作为胺类加速固化剂,正庚烷作为溶剂,其步骤为向正庚烷溶剂中加入1,8-二氮杂双环[5.4.0]十一碳-7-烯,然后搅拌均匀,适合的配方比为1,8-二氮杂双环[5.4.0]十一碳-7-烯0.8%,其余为正庚烷。
[0036]
强力胶加速剂的使用方法为:先在木质基材(如榉木板)表面预先涂覆一层厚度约0.1~1mm的强力胶加速剂,待5~10s左右后干燥,然后涂覆强力胶。
[0037]
实施例2不同胺类物质对强力胶固化效果的影响
[0038]
本实施例按照实施例1提供的方法制备强力胶加速剂,其中的胺类物质分别采用1,8-二氮杂双环[5.4.0]十一碳-7-烯、n,n-二甲基苯胺、三乙烯四胺、双-(2-二甲基氨基乙基)醚、三乙胺,溶剂为正庚烷,其中胺类物质含量为0.8%,其余为正庚烷,制备得到5种不同的强力胶加速剂,将这5种强力胶加速剂分别先在木质基材或塑料基材表面涂覆,干燥后再涂覆强力胶,考察强力胶的固化时间,及固化后强力胶的剪切强度、冲击强度、挠曲强度和耐湿热老化性能。其中固化时间的检测方法参照hg/t 2492-2018;剪切强度的测试方法参照标准gb/t 7124;冲击强度的测试方法为:由两个端面为正方形的金属长条对接胶接成试样,试样端面胶接处错位小于0.1mm,胶接面平整,且与试样纵轴方向垂直,将试样放在摆锤式冲击试验机上,摆锤端面与试样轴线垂直,松开摆锤自由下落,记录试样破坏时所消耗的能a(j),计算冲击强度,冲击强度=a/bdl,其中b为试样宽度,d为试样厚度,l为支点间距离;挠曲强度的测试方法为通过挠曲万能试验机测试;耐湿热老化性能的测试方法为将完全固化后的胶接件置于85℃、湿度85%的试验箱中,7天后取出,冷却后测定剪切强度,并计算湿热老化后的剪切强度与老化前的剪切强度之间的比值;结果如表1所示。
[0039]
表1、不同胺类物质对强力胶固化效果的影响
[0040][0041][0042]
由表1可以看出,相比其他胺类物质,dbu制备的加速剂,能更快促进强力胶在各种木质基材表面的固化;更重要的是,其它胺类物质制备的加速剂,或多或少都会影响强力胶在固化后的粘结性能,而dbu对固化后的强力胶的剪切强度、冲击强度、挠曲强度、耐湿热老化性能都达到最高,可见在木质基材表面涂覆dbu几乎不会对强力胶的各项性能产生影响。
[0043]
另外,强力胶在聚氯乙烯塑料表面的固化速度较快,基本无需添加加速剂,不过即使添加也不会有任何影响,固化速度还稍有提高。
[0044]
实施例3不同溶剂对强力胶固化效果的影响
[0045]
本实施例按照实施例1提供的方法,采用1,8-二氮杂双环[5.4.0]十一碳-7-烯,并分别选用不同的溶剂,其中1,8-二氮杂双环[5.4.0]十一碳-7-烯含量为0.8%,其余为溶剂,制备得到3种不同的强力胶加速剂,将这3种强力胶加速剂分别先在木质基材或塑料基材表面涂覆,干燥后再涂覆强力胶,考察强力胶的固化时间,及固化后强力胶的剪切强度、冲击强度、挠曲强度和耐湿热老化性能,检测方法如实施例2所示,并以不使用加速剂直接涂覆强力胶作为空白对照,结果如表2所示。
[0046]
表2、不同溶剂对强力胶固化效果的影响
[0047][0048]
由表2可以看出,采用不同溶剂溶解dbu制备的加速剂,对强力胶的固化时间稍有影响,差别不是很明显,但是对强力胶固化后的剪切强度、冲击强度、挠曲强度和耐湿热老化性能却存在一定的影响,其中最优选为正庚烷,固化后的强力胶的剪切强度、冲击强度、挠曲强度、耐湿热老化性能都达到最高,固化时间也较短,其原因可能是因为正庚烷既能帮助1,8-二氮杂双环[5.4.0]十一碳-7-烯均匀涂覆,涂覆后还能迅速挥发,不会对1,8-二氮
杂双环[5.4.0]十一碳-7-烯和强力胶产生任何影响,而其他溶剂或多或少会存在残留,甚至会影响强力胶的粘结性能。
[0049]
实施例4dbu及其溶剂的不同配比关系对强力胶固化效果的影响
[0050]
本实施例按照实施例1提供的方法,采用1,8-二氮杂双环[5.4.0]十一碳-7-烯,和正庚烷配制强力胶加速剂,其中1,8-二氮杂双环[5.4.0]十一碳-7-烯与正庚烷分别采用如表3所示的不同质量比例关系,制备得到的强力胶加速剂分别先在木质基材表面涂覆,干燥后再涂覆强力胶,考察强力胶的固化时间,及固化后强力胶的剪切强度、冲击强度、挠曲强度和耐湿热老化性能,检测方法如实施例3所示,并以不使用加速剂直接涂覆强力胶作为空白对照,结果如表3所示。
[0051]
表3、不同溶剂对强力胶固化效果的影响
[0052][0053]
由表3可以看出,随着dbu含量的上升,强力胶的固化速度迅速加快,但当dbu占比在0.8%以后,固化时间不再继续缩短,可见dbu占比0.8%已完全足够,且能满足市场需求,继续上升比例只会增大成本;另外当dbu占比达到5%时,固化后的强力胶剪切强度、冲击强度、挠曲强度和耐湿热老化性能出现下降趋势。
[0054]
虽然本发明披露如上,但本发明并非限定于此。任何本领域技术人员,在不脱离本发明的精神和范围内,均可作各种更动与修改,因此本发明的保护范围应当以权利要求所限定的范围为准。