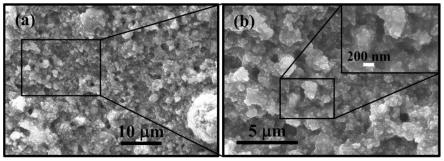
1.本发明属于功能涂层材料技术领域,具体涉及一种兼具光热除冰和长效防腐性能的超疏水涂层及制备方法。
背景技术:2.表面结冰是一种常见的自然现象,然而表面结冰通常会对基础设施和工业设备造成严重损坏。特别是在电力运输、航空运载、风力涡轮机和远洋船舶等领域产生极大影响,进而导致一些能源消耗、紧急情况、安全隐患和财产损失。传统的机械除冰、电热除冰和化学除冰方法存在操作危险、费用巨大、危害环境等问题。因此,研制具有高效防除冰性能的功能涂层材料具有重要意义。
3.超疏水涂层用于表面防除冰已被科技工作者广泛报道,涂层表面优异的界面非润湿特性可以使水滴在重力作用下迅速滚落,避免冻结。此外,涂层表面微-纳米多级结构中储存的空气能够降低传热效率,并减少水滴与涂层表面的接触面积,从而实现延长结冰时间,减弱冰粘附强度的效果。然而,在极端环境下超疏水涂层表面仍然会因为水分逐渐凝结和积累而渐渐结霜,最后完全结冰;此时表面微-纳米多级结构的存在反而增加了冰与涂层的接触面积和冰粘附强度。此外,涂层表面微-纳米多级结构在多次机械除冰循环后易破碎剥落,这依然限制了超疏水涂层材料在防除冰工业领域的实际应用。针对上述问题,设计制备具有光热性能的超疏水防除冰涂层逐渐成为研究热点。
4.目前,现有技术中关于制备具有光热性能超疏水防除冰涂层的技术主要包括:
5.专利cn112852289b公开了一种具有光热效应的超疏水防除冰涂层及其制备方法,所述方法主要包括:首先,将从墨囊中获取的黑色素纳米颗粒与聚二甲基硅氧烷共混并喷涂在基体上制备光热涂层;其次,将功能化处理的纳米二氧化硅颗粒分散液喷涂在光热涂层表面;最终得到超疏水防除冰涂层。该两步喷涂法制备的超疏水涂层润湿特性易失效,进而影响涂层的整体防冰性能。
6.专利申请cn114058224a公开了一种光热响应超疏水防冰涂层及其制备方法,所述方法将微米级与纳米级颗粒相复合分散在溶剂中得到均匀溶液,利用喷枪将其喷涂在涂敷有硅橡胶基板表面,并经过加热氟化处理得到光热响应超疏水防冰涂层。由于所述方法采用低表面能氟化物附着技术,该涂层材料并非整体低表面能,因此,所述方法制备得到的光热除冰超疏水涂层浸润性未呈现出对非机械损伤的可治愈性能。
7.马等人利用碳纳米管-纳米二氧化硅颗粒与树脂基体混合制备了具有主动光热除冰性能的耐久性超疏水涂层(chem.eng.j.2021,423,130238);张等人将预处理碳化钛颗粒和碳纳米管悬浮液喷涂到乙烯醋酸酯表面获得了一种被动防冰和主动光热除冰的超疏水涂层(acsappl.mater.interfaces,2018,10,36505-36511);由于碳纳米管与聚合物基体界面的相互作用相对较弱,且长径比大,导致其在涂层内易发生团聚现象,对涂层的机械稳定性和光热性能不利。同时,涂层填料成分中缺少阻碍腐蚀介质扩散渗透的物质,如应用到海洋腐蚀环境中,可能不具备长效腐蚀防护能力。在一些极端气候环境下,如极地科考船,具
有优异防除冰和腐蚀防护耦合性能逐渐成为功能涂层材料的发展方向。
技术实现要素:8.为了克服现有技术中具有光热性能的超疏水涂层存在的化学-机械性能稳定差、长效腐蚀防护性能差、光热除冰性能低、不具备非机械损伤的可治愈性等缺陷,本发明的目的之一在于提供一种兼具光热除冰和长效防腐性能的超疏水涂层。
9.本发明的目的之二在于提供一种兼具光热除冰和长效防腐性能的超疏水涂层的制备方法。
10.为实现本发明的目的,提供以下技术方案。
11.一种兼具光热除冰和长效防腐性能的超疏水涂层,以所述涂层原料组成成分的总体质量为100%计,其中,各原料组分及其质量百分数如下:
[0012][0013][0014]
所述功能化sio2纳米颗粒为十八烷基修饰的sio2纳米颗粒;
[0015]
所述功能化tic纳米颗粒为十八烷基修饰的tic纳米颗粒;
[0016]
所述功能化go为十八烷基修饰的氧化石墨烯;
[0017]
所述有机溶剂为乙酸乙酯;
[0018]
优选的,所述功能化sio2纳米颗粒采用如下方法制备:将sio2纳米颗粒均匀分散在无水乙醇中,再滴入三氯十八烷基硅烷(ots),加热、搅拌至得到均匀的溶液;将所述溶液干燥得到固体颗粒,并将所述固体颗粒清洗干燥,得到功能化sio2纳米颗粒;
[0019]
所述sio2纳米颗粒和无水乙醇质量比为1:25~1:15,进一步优选为1:20;
[0020]
所述ots与sio2纳米颗粒质量比为1:3~1:2,进一步优选为1:2.5;
[0021]
进一步优选的,所述加热温度为70℃~90℃;
[0022]
进一步优选的,所述干燥的温度为80℃~100℃,所述干燥的时间为4h~8h。
[0023]
优选的,所述功能化tic纳米颗粒采用如下方法制备:将tic纳米颗粒均匀分散于无水乙醇中,再滴入ots,加热、搅拌至得到均匀的溶液;将所述溶液干燥得到固体颗粒,并将所述固体颗粒清洗干燥,得到功能化tic纳米颗粒;
[0024]
所述tic纳米颗粒和无水乙醇的质量比为1:50~1:30,进一步优选为1:40;
[0025]
所述ots与tic纳米颗粒质量比为1:2~1:1,进一步优选为1:1.66;
[0026]
进一步优选的,所述加热温度为70℃~90℃;
[0027]
进一步优选的,所述干燥的温度为80℃~100℃,所述干燥的时间为4h~8h。
[0028]
优选地,所述功能化go采用如下方法制备:将go均匀分散在无水乙醇中,再滴入ots,加热、搅拌至得到均匀的溶液;将所述溶液干燥得到固体颗粒,并将所述固体颗粒清洗
干燥,得到的功能化go;
[0029]
所述go和无水乙醇的质量比为1:150~1:100,进一步优选为1:120;
[0030]
所述ots与go质量比为1:1~3:1,进一步优选为2:1;
[0031]
进一步优选的,所述加热温度为70℃~90℃;
[0032]
进一步优选的,所述干燥的温度为80℃~100℃,所述干燥的时间为4h~8h。
[0033]
优选的,所述功能化sio2纳米颗粒、功能化tic纳米颗粒和功能化go组成复合填料,所述复合填料与msr质量比为1:1.88~1:2.8,所述固化剂n75与msr的质量比为1:3.5;所述msr与有机溶剂乙酸乙酯的质量比为1:2。
[0034]
一种本发明所述兼具光热除冰和长效防腐性能的超疏水涂层的制备方法,所述方法步骤如下:
[0035]
(1)将msr完全溶解于有机溶剂中,分别加入功能化sio2纳米颗粒、功能化tic纳米颗粒和功能化go,超声分散均匀,然后加入固化剂n75,磁力搅拌至得到均匀溶液;
[0036]
优选的,所述磁力搅拌时间为2h~4h。
[0037]
(2)将步骤(1)配置的均匀溶液喷涂在镁合金基体上,加热固化,得到一种兼具光热除冰和长效防腐性能的超疏水涂层。
[0038]
具体为:将步骤(1)配置的均匀溶液倒入喷枪,喷涂在基体上,喷涂工艺参数为:喷枪的喷嘴直径为1.3mm;喷涂过程中基体与喷枪喷嘴的距离为15cm~20cm;喷涂时间为20s~40s。
[0039]
优选的,所述加热固化为梯度加热固化,第一阶段加热温度为70℃~90℃,加热时间1h~2h;第二阶段加热温度为100℃~140℃,加热时间4h~6h。
[0040]
优选的,所述喷涂为空气喷涂,喷涂压缩空气压力为0.6mpa~0.8mpa;
[0041]
优选的,对所述基体进行表面预处理,所述预处理为:先后依次经1000#和2000#的sic砂纸打磨至去掉基体表面氧化膜后超声清洗5min。
[0042]
本发明所述一种兼具光热除冰和长效防腐性能的超疏水涂层在近红外光照射过程中的光热除冰机理如下:在所述超疏水涂层表面滴上水滴,在低温环境中完全结冰后利用近红外光照射涂层表面,随着照射时间的延迟,完全冻结的冰逐渐融化成冰水混合物,最后完全融化成水,在融化过程中,由于马兰欧尼力作用,冰与超疏水涂层表面接触区域的空气层逐渐恢复,冰融化形成的液滴依然保持球型且容易滚落,所述涂层展现出良好的光热除冰性能。
[0043]
有益效果
[0044]
(1)本发明提供了一种兼具光热除冰和长效防腐性能的超疏水涂层,所述涂层添加了质量分数为9.0%~9.5%的功能化sio2纳米颗粒,所述功能化sio2纳米颗粒表面修饰有低表面能官能团(-ch3),功能化sio2纳米颗粒在涂层内充当骨架作用,显著提高了涂层表面粗糙度(ra),并且能够使涂层整体均为低表面能材料,适宜的ra和低表面能使得涂层呈现出良好的界面非润湿特性,其微液滴粘附力最低仅16.8
±
0.6μn,水滴接触角(cas)最高可达为161.9
°
,滑动角(sas)最低仅为4.2
°
。
[0045]
(2)本发明提供了一种兼具光热除冰和长效防腐性能的超疏水涂层,所述涂层表现出良好的近红外光(808nm,2w)光热转换能力,随着功能化tic纳米颗粒含量的增加,涂层光热效率之间存在差异,会逐渐提高,在近红外光照射100s以后,照射区域温度能够达到65
℃以上,可以满足光热除冰所需的温度要求;此外,在融化过程中,由于马兰欧尼力作用,冰与超疏水涂层表面接触区域的空气层逐渐恢复,冰融化形成的液滴依然保持球型,且易于滚落,涂层展现出良好的光热除冰性能。
[0046]
(3)本发明提供了一种兼具光热除冰和长效防腐性能的超疏水涂层,所述涂层表现出优异的长效防腐性能;防腐机理可归纳如下:首先,超疏水涂层表面微-纳米多级结构可储存大量空气并在一定时间内稳定存在,大大减少了腐蚀介质与涂层的接触面积;经cassie-baxter公式计算得,涂层表面与腐蚀介质的接触面积平均值仅为2.8%;其次,所述涂层通过调控环氧改性有机硅树脂(msr)与复合填料(sio2、tic和go)之间的重量比获得均匀致密的涂层,可以在一定时间内更好地阻止腐蚀介质渗入侵蚀镁合金基体,起到了腐蚀屏障作用;最后,随着浸泡时间的延长,所述涂层的复合填料中非渗透性的功能化go会导致腐蚀介质扩散路径变得复杂,从而实现长效防腐性能。
[0047]
(4)本发明提供了一种兼具光热除冰和长效防腐性能的超疏水涂层,涂层具有良好的机械-化学稳定性;由于涂层整体的低表面能特性,经摩擦后暴露出来的粗糙结构依然能够满足实现超疏水特性的需要;同时所选环氧改性有机硅树脂和复合填料均是耐磨材料;超疏水涂层表面会储存一定的空气层可以降低侵蚀介质与涂层的接触面积;所述涂层的机械稳定性通过砂纸摩擦循环试验测试,当摩擦距离达到60米,涂层仍然保持着超疏水特性;另外,所述涂层中添加的环氧改性有机硅树脂和复合填料有一定的抵抗酸、碱和盐雾的能力;所述涂层样品在强酸(ph=1)或强碱(ph=14)腐蚀介质中浸泡16h表面润湿性无明显波动,在nacl溶液(3.5wt.%)中浸泡7天,超疏水特性的变化可以忽略不计,具有优异的化学稳定性。
[0048]
(5)本发明提供了一种兼具光热除冰和长效防腐性能的超疏水涂层,由于所述涂层中添加的环氧改性有机硅树脂在n75固化剂固化后较稳定,不会在高低温变换条件下发生破坏,因此所述涂层能够抵抗较大的高低温循环测试(-196℃和200℃),经过10次交替循环测试后,涂层依然保持超疏水特性,且未发生开裂和降解。
[0049]
(6)本发明提供了一种兼具光热除冰和长效防腐性能的超疏水涂层,所述涂层中添加了表面修饰有低表面能官能团(-ch3)的功能化sio2纳米颗粒,加热后低表面能疏水碳氢链向涂层表面迁移积,因此涂层具有优异的非机械损伤(o2等离子刻蚀)可治愈性能。
[0050]
(7)本发明提供了一种兼具光热除冰和长效防腐性能的超疏水涂层的制备方法,所述方法工艺操作简单可控、设备价格及原料成本低廉,适合大规模工业生产和商业推广。
附图说明
[0051]
图1为实施例2制备获得的兼具光热除冰和长效防腐性能的超疏水涂层水滴接触角(cas)和滚动角(sas)测试图。
[0052]
图2为实施例2制备获得的兼具光热除冰和长效防腐性能的超疏水涂层表面微观形貌。
[0053]
图3为实施例3制备获得的兼具光热除冰和长效防腐性能的超疏水涂层在在1000#砂纸上100g砝码重量下经过总距离60米摩擦后表面疏水性。
[0054]
图4为实施例3制备获得的兼具光热除冰和长效防腐性能的超疏水涂层分别在强酸(ph=1)、强碱(ph=14)浸泡16h和3.5wt.%nacl溶液浸泡7天条件下表面润湿性变化。
[0055]
图5为实施例3制备获得的兼具光热除冰和长效防腐性能的超疏水涂层高-低温交替循环测试次数及疏水性变化。
[0056]
图6为实施例4制备获得的兼具光热除冰和长效防腐性能的超疏水涂层的抵抗非机械损伤可治愈循环次数。
[0057]
图7为对比例制备获得的纯树脂涂层、实施例1和实施例3制备获得的涂层在808nm近红外光照射300s过程中表面温度变化。
[0058]
图8为镁合金基体电化学阻抗谱以及实施例4制备获得的兼具光热除冰和长效防腐性能的超疏水涂层在3.5wt.%nacl溶液中浸泡0天、14天和21天后的电化学阻抗谱。
具体实施方式
[0059]
下面结合附图和具体实施例来详述本发明,但不作为对本发明专利的限定。
[0060]
环氧改性有机硅树脂牌号:sh-023-7,湖北新四海化工有限公司;
[0061]
固化剂n75:黏度(25℃)/mpa
·
s100-150,济南裕才化工有限公司,工业级;
[0062]
涂层表面与腐蚀介质的接触面积采用cassie-baxter公式计算:
[0063]
cosθs=f
1 cosθ
0-f2[0064]
其中,f1为固-液的接触面积分数,f2为气-液的接触面积分数,f1+f2=1;θs为涂层表面cas,θ0为镁合金基体cas。
[0065]
对以下实施例中制备得到的兼具光热除冰和长效防腐性能的超疏水涂层进行检测如下:
[0066]
(1)表面微液滴粘附力和疏水性定量表征:高灵敏度微机电平衡系统,型号:dcat11;接触角测量仪,型号:dsa255。
[0067]
(2)微观形貌表征:场发射扫描电子显微镜,型号:jsm-7610f,japan。
[0068]
(3)抗高-低温交替循环测试:将所述涂层在液氮(-196℃)浸泡10min,接着取出样品恢复室温,在加热板(200℃下)加热10min,为1次高低温循环测试,并记录涂层表面变化。
[0069]
(4)机械稳定性测试:将超疏水涂层样品放置在1000#砂纸上,在100g砝码载荷下往返摩擦,一次往返总摩擦距离20cm,每摩擦5m测量涂层表面cas和sas,并测量涂层经总摩擦距离60m后表面微观形貌。
[0070]
(5)化学稳定性测试:石蜡密封超疏水涂层样品,分别浸泡在强酸溶液(ph=1)和强碱溶液(ph=14)中,每隔2个小时记录表面的润湿性;涂层样品浸泡在nacl溶液(3.5wt.%)中,每隔1天记录表面润湿性变化。
[0071]
(6)可治愈性能表征:o2等离子刻蚀机,型号:dienerelectronic,germany。
[0072]
(7)光热性能测试:红外热像仪,型号:sc7300m,flir;测量在波长为808nm、功率为2w的近红外光垂直照射300s过程中涂层表面的温度变化,红外热像仪和涂层位置间距为15cm,环境温度为室温。
[0073]
(8)电化学阻抗谱测试:电化学工作站,型号:gamry reference600;将光热除冰和长效防腐超疏水涂层样品在3.5wt%nacl溶液中浸泡0天、14天和21天,测试所述涂层样品及镁合金基体电化学阻抗谱。
[0074]
实施例1
[0075]
一种兼具光热除冰和长效防腐性能的超疏水涂层,以所述涂层原料组成成分的总
质量为100%计,其中,各原料组分及其质量百分数如下:
[0076][0077]
所述功能化sio2纳米颗粒采用如下方法制备:将5.0g sio2纳米颗粒均匀分散在100g无水乙醇中,再滴入2.0g ots,80℃加热、搅拌至得到均匀的溶液;将所述溶液放入鼓风干燥箱中80℃干燥8h得到固体颗粒,并将所述固体颗粒清洗干燥,得到功能化sio2纳米颗粒;其中,所述sio2纳米颗粒和无水乙醇的质量比为1:20,所述ots与sio2纳米颗粒质量比为1:2.5。
[0078]
所述功能化tic纳米颗粒采用如下方法制备:将2.5g tic纳米颗粒均匀分散于100g无水乙醇中,再滴入1.5g ots,80℃加热、搅拌至得到均匀的溶液;将所述溶液放入鼓风干燥箱中90℃干燥6h得到固体颗粒,并将所述固体颗粒清洗干燥,得到功能化tic纳米颗粒;其中,所述tic纳米颗粒和无水乙醇的质量比为1:40,所述ots与tic纳米颗粒质量比为1:1.66。
[0079]
所述功能化go采用如下方法制备:将0.5g go均匀分散在60g无水乙醇中,再滴入1.0g ots,80℃加热、搅拌至得到均匀的溶液;将所述溶液放入鼓风干燥箱中90℃干燥6h得到固体颗粒,并将所述固体颗粒清洗干燥,得到的功能化go;其中,所述go和无水乙醇的质量比为1:120,所述ots与go质量比为2:1;
[0080]
所述功能化sio2纳米颗粒、功能化tic纳米颗粒和功能化go组成复合填料,所述复合填料与msr质量比为1:2.8,所述固化剂n75与msr的质量比为1:5;所述msr与有机溶剂乙酸乙酯的质量比为1:1.6。
[0081]
一种本实施例所述兼具光热除冰和长效防腐性能的超疏水涂层的制备方法,所述方法步骤如下:
[0082]
(1)将5g msr加入8g乙酸乙酯中超声至完全溶解,分别加入1.5g功能化sio2纳米颗粒、0.3g功能化tic和0.015g功能化go,超声分散均匀;然后加入1.0g固化剂n75,磁力搅拌3h,得到msr@sio2+tic+go均匀溶液。
[0083]
(2)将步骤(1)配制的msr@sio2+tic+go均匀溶液喷涂在镁合金基体上,梯度加热固化,得到一种兼具光热除冰和长效防腐性能的超疏水涂层。
[0084]
具体为:将步骤(1)配制的msr@sio2+tic+go均匀溶液倒入喷枪喷壶中,采用空气压缩喷涂技术喷涂在镁合金基体上,梯度加热固化,第一阶段加热温度为80℃,加热时间为2h,第二阶段加热温度为120℃,加热时间为4h,得到一种兼具光热除冰和长效防腐性能的超疏水涂层。
[0085]
喷涂工艺参数:喷枪的喷嘴直径为1.3mm;喷涂压缩空气压力为0.8mpa;喷涂过程中基体与喷枪喷嘴的距离为15cm;喷涂时间为20s。
[0086]
所述基体进行表面预处理,先后依次经1000#和2000#的sic砂纸打磨至去掉基体表面氧化膜后超声清洗5min。
[0087]
实施例2
[0088]
一种兼具光热除冰和长效防腐性能的超疏水涂层,以所述涂层原料组成成分的总质量为100%计,其中,各原料组分及其质量百分数如下:
[0089][0090]
所述功能化sio2纳米颗粒采用如下方法制备:将5.0g sio2纳米颗粒均匀分散在100g无水乙醇中,再滴入2.0g ots,80℃加热、搅拌至得到均匀的溶液;将所述溶液放入鼓风干燥箱中90℃干燥6h得到固体颗粒,并将所述固体颗粒清洗干燥,得到功能化sio2纳米颗粒;其中,所述sio2纳米颗粒和无水乙醇的质量比为1:20,所述ots与sio2纳米颗粒质量比为1:2.5。
[0091]
所述功能化tic纳米颗粒采用如下方法制备:将2.5g tic纳米颗粒均匀分散于100g无水乙醇中,再滴入1.5g ots,80℃加热、搅拌至得到均匀的溶液;将所述溶液放入鼓风干燥箱中100℃干燥6h得到固体颗粒,并将所述固体颗粒清洗干燥,得到功能化tic纳米颗粒;其中,所述tic纳米颗粒和无水乙醇的质量比为1:40,所述ots与tic纳米颗粒质量比为1:1.66。
[0092]
所述功能化go采用如下方法制备:将0.5g go均匀分散在60g无水乙醇中,再滴入1.0g ots,80℃加热、搅拌至得到均匀的溶液;将所述溶液放入鼓风干燥箱中90℃干燥6h得到固体颗粒,并将所述固体颗粒清洗干燥,得到的功能化go;其中,所述go和无水乙醇的质量比为1:120,所述ots与go质量比为2:1。
[0093]
所述功能化sio2纳米颗粒、功能化tic纳米颗粒和功能化go组成复合填料,所述复合填料与msr质量比为1:2.5,所述固化剂n75与msr的质量比为1:4;所述msr与有机溶剂乙酸乙酯的质量比为1:1.67。
[0094]
一种本实施例所述兼具光热除冰和长效防腐性能的超疏水涂层的制备方法,所述方法步骤如下:
[0095]
(1)将6g msr加入10g乙酸乙酯中超声至完全溶解,分别加入1.8g功能化sio2纳米颗粒、0.6g功能化tic和0.03g功能化go,超声分散均匀;随后加入1.5g固化剂n75,磁力搅拌3h,得到msr@sio2+tic+go均匀溶液。
[0096]
(2)将步骤(1)配制的msr@sio2+tic+go均匀溶液喷涂在镁合金基体上,梯度加热固化,得到一种兼具光热除冰和长效防腐性能的超疏水涂层。
[0097]
具体为:将步骤(1)制备的msr@sio2+tic+go均匀溶液倒入喷枪喷壶中,采用空气压缩喷涂技术喷涂在基体上,梯度加热固化,第一阶段加热温度为80℃,加热时间为2h,第
二阶段加热温度为120℃,加热时间为4h,最终得到兼具光热除冰和长效防腐性能的超疏水涂层。
[0098]
喷涂工艺参数:喷枪的喷嘴直径为1.3mm;压缩空气压力为0.6mpa;喷涂过程中基体与喷枪喷嘴的距离为20cm;喷涂时间为30s。
[0099]
所述基体进行表面预处理,先后依次经1000#和2000#的sic砂纸打磨至去掉基体表面氧化膜后超声清洗5min。
[0100]
实施例3
[0101]
一种兼具光热除冰和长效防腐性能的超疏水涂层,以所述涂层原料组成成分的总质量为100%计,其中,各原料组分及其质量百分数如下:
[0102][0103]
所述功能化sio2纳米颗粒采用如下方法制备:将5.0g sio2纳米颗粒均匀分散在100g无水乙醇中,再滴入2.0g ots,80℃加热、搅拌至得到均匀的溶液;将所述溶液放入鼓风干燥箱中100℃干燥4h得到固体颗粒,并将所述固体颗粒清洗干燥,得到功能化sio2纳米颗粒;其中,所述sio2纳米颗粒和无水乙醇的质量比为1:20,所述ots与sio2纳米颗粒质量比为1:2.5。
[0104]
所述功能化tic纳米颗粒采用如下方法制备:将2.5g tic纳米颗粒均匀分散于100g无水乙醇中,再滴入1.5g ots,80℃加热、搅拌至得到均匀的溶液;将所述溶液放入鼓风干燥箱中90℃干燥6h得到固体颗粒,并将所述固体颗粒清洗干燥,得到功能化tic纳米颗粒;其中,所述tic纳米颗粒和无水乙醇的质量比为1:40,所述ots与tic纳米颗粒质量比为1:1.66。
[0105]
所述功能化go采用如下方法制备:将0.5g go均匀分散在60g无水乙醇中,再滴入1.0g ots,80℃加热、搅拌至得到均匀的溶液;将所述溶液放入鼓风干燥箱中90℃干燥8h得到固体颗粒,并将所述固体颗粒清洗干燥,得到的功能化go;其中,所述go和无水乙醇的质量比为1:120,所述ots与go质量比为2:1。
[0106]
所述功能化sio2纳米颗粒、功能化tic纳米颗粒和功能化go组成复合填料,所述复合填料与msr质量比为1:2,所述固化剂n75与msr的质量比为1:4;所述msr与有机溶剂乙酸乙酯的质量比为1:2。
[0107]
一种本实施例所述兼具光热除冰和长效防腐性能的超疏水涂层的制备方法,所述方法步骤如下:
[0108]
(1)将6g msr加入12g中超声至完全溶解,分别加入2.1g功能化sio2纳米颗粒、0.9g功能化tic和0.03g功能化go,超声分散均匀;随后加入1.5g固化剂n75,磁力搅拌3h,得到msr@sio2+tic+go均匀溶液。
[0109]
(2)将步骤(1)配制的msr@sio2+tic+go均匀溶液喷涂在镁合金基体上,梯度加热固化,得到一种兼具光热除冰和长效防腐性能的超疏水涂层。
[0110]
具体为:将步骤(1)制备的msr@sio2+tic+go均匀溶液倒入喷枪喷壶中,采用空气压缩喷涂技术喷涂在基体上,梯度加热固化,第一阶段加热温度为80℃,加热时间为2h,第二阶段加热温度为120℃,加热时间为4h,最终得到兼具光热除冰和长效防腐性能的超疏水涂层。
[0111]
喷涂工艺参数:喷枪的喷嘴直径为1.3mm;压缩空气压力为0.6mpa;喷涂过程中基体与喷枪喷嘴的距离为20cm;喷涂时间为40s。
[0112]
所述基体进行表面预处理,先后依次经1000#和2000#的sic砂纸打磨至去掉基体表面氧化膜后超声清洗5min。
[0113]
实施例4
[0114]
一种兼具光热除冰和长效防腐性能的超疏水涂层,以所述涂层原料组成成分的总质量为100%计,其中,各原料组分及其质量百分数如下:
[0115][0116]
所述功能化sio2纳米颗粒采用如下方法制备:将5.0g sio2纳米颗粒均匀分散在100g无水乙醇中,再滴入2.0g ots,80℃加热、搅拌至得到均匀的溶液;将所述溶液放入鼓风干燥箱中90℃干燥6h得到固体颗粒,并将所述固体颗粒清洗干燥,得到功能化sio2纳米颗粒;其中,所述sio2纳米颗粒和无水乙醇的质量比为1:20,所述ots与sio2纳米颗粒质量比为1:2.5。
[0117]
所述功能化tic纳米颗粒采用如下方法制备:将2.5g tic纳米颗粒均匀分散于100g无水乙醇中,再滴入1.5g ots,80℃加热、搅拌至得到均匀的溶液;将所述溶液放入鼓风干燥箱中90℃干燥6h得到固体颗粒,并将所述固体颗粒清洗干燥,得到功能化tic纳米颗粒;其中,所述tic纳米颗粒和无水乙醇的质量比为1:40,所述ots与tic纳米颗粒质量比为1:1.66。
[0118]
所述功能化go采用如下方法制备:将0.5g go均匀分散在60g无水乙醇中,再滴入1.0g ots,80℃加热、搅拌至得到均匀的溶液;将所述溶液放入鼓风干燥箱中90℃干燥6h得到固体颗粒,并将所述固体颗粒清洗干燥,得到的功能化go;其中,所述go和无水乙醇的质量比为1:120,所述ots与go质量比为2:1。
[0119]
所述功能化sio2纳米颗粒、功能化tic纳米颗粒和功能化go组成复合填料,所述复合填料与msr质量比为1:1.88,所述固化剂n75与msr的质量比为1:3.5;所述msr与有机溶剂乙酸乙酯的质量比为1:2。
[0120]
一种本实施例所述兼具光热除冰和长效防腐性能的超疏水涂层的制备方法,所述
方法步骤如下:
[0121]
(1)将7g msr加入14g乙酸乙酯中超声至完全溶解,分别加入2.5g功能化sio2纳米颗粒、1.2g功能化tic和0.03g功能化go,超声搅拌均匀;随后加入2g固化剂n75,磁力搅拌3h,得到msr@sio2+tic+go均匀溶液。
[0122]
(2)将步骤(1)配制的msr@sio2+tic+go均匀溶液喷涂在镁合金基体上,梯度加热固化,得到一种兼具光热除冰和长效防腐性能的超疏水涂层。
[0123]
具体为:将步骤(1)配置的msr@sio2+tic+go均匀溶液倒入喷枪喷壶中,采用空气压缩喷涂技术喷涂在基体上,梯度加热固化,第一阶段加热温度为80℃,加热时间为2h,第二阶段加热温度为120℃,加热时间为4h,最终得到兼具光热除冰和长效防腐性能的超疏水涂层。
[0124]
喷涂工艺参数:喷枪的喷嘴直径为1.3mm;压缩空气压力为0.8mpa;喷涂过程中基体与喷枪喷嘴的距离为20cm;喷涂时间为30s。
[0125]
所述基体进行表面预处理,先后依次经1000#和2000#的sic砂纸打磨至去掉基体表面氧化膜后超声清洗5min。
[0126]
对比例
[0127]
对比例仅在实施例1的基础上,去掉功能化复合填料,得到纯树脂涂层。
[0128]
实施例1~4和对比例的表征及结果如下:
[0129]
(1)涂层表面微液滴粘附力和疏水性定量表征:
[0130]
对实施例2制备获得的兼具光热除冰和长效防腐性能的超疏水涂层微液滴粘附力和疏水性进行表征,结果如图1所示,其微液滴粘附力约为16.8
±
0.6μn,cas为161.9
°
,sas为4.2
°
。
[0131]
实施例1超疏水涂层微液滴粘附力约为18.4
±
0.5μn,cas为161.5
°
,sas为4.5
°
。
[0132]
实施例3超疏水涂层微液滴粘附力约为17.5
±
0.6μn,cas为160.9
°
,sas为4.6
°
。
[0133]
实施例4超疏水涂层微液滴粘附力约为17.7
±
0.5μn,cas为161.2
°
,sas为4.8
°
。
[0134]
说明实施例1~4制备的涂层具有良好的超疏水低粘附性能。
[0135]
(2)涂层微观形貌表征:
[0136]
实施例2制备获得的兼具光热除冰和长效防腐性能的超疏水涂层表面形貌为均匀致密的微-纳米多级结构,结果如图2所示,其中图(a)的标尺10μm,图(b)的标尺为5μm。
[0137]
实施例1、3、4涂层表面形貌观察结果与实施例2接近,均为微-纳多级结构。
[0138]
(3)机械稳定性测试:
[0139]
实施例3制备获得的兼具光热除冰和长效防腐性能的超疏水涂层在1000#砂纸上100g砝码重量下经过总距离60m摩擦后表面疏水性如图3所示,位于上方的曲线为接触角(cas)测试结果,位于下方的曲线为滚动角(sas)测试结果,结果表明:总摩擦距离达60m后,涂层表面依然保持超疏水特性,即cas在160
°
左右波动,sas在5
°
左右波动,所述涂层具有良好的摩擦机械稳定性。
[0140]
实施例1、2、4制备获得的兼具光热除冰和长效防腐性能的超疏水涂层经过60m摩擦后,水滴cas均在160
°
左右;水滴sas均低于6
°
。
[0141]
(4)化学稳定性测试:
[0142]
对实施例3制备获得的兼具光热除冰和长效防腐性能的超疏水涂层进行化学稳定
性测试,所述涂层分别浸泡在强酸、强碱和nacl溶液中,每隔一段时间分别记录涂层表面的润湿性,以上3种测试结果如图4所示,图4(a)~(c)中位于上方的曲线均为接触角(cas)测试结果,位于下方的曲线均为滚动角(sas)测试结果,所述涂层表面水滴cas均高于160
°
,且sas小于8
°
,可以得出所述兼具光热除冰和长效防腐性能的超疏水涂层具有较好的化学稳定性。
[0143]
实施例1、2、4制备获得的兼具光热除冰和长效防腐性能的超疏水涂层经过化学稳定性测试后,水滴cas同样均在160
°
左右;水滴sas均低于6
°
。
[0144]
(5)抗高-低温交替循环测试:
[0145]
对实施例3制备获得的兼具光热除冰和长效防腐性能的超疏水涂层进行抗高-低温交替循环试验,结果如图5所示,所述涂层能够抵抗较大的高低温循环测试(-196℃和200℃),经过10次交替循环测试后,涂层表面依然保持超疏水自清洁特性,cas维持在160
°
左右,且sas在6
°
左右。
[0146]
实施例1、2、4制备的兼具光热除冰和长效防腐性能的超疏水涂层样品经过同样的抗高-低温交替循环试验,均保持初始超疏水自清洁特性。
[0147]
(6)非机械损伤可治愈能力测试:对实施例4制备获得的兼具光热除冰和长效防腐性能的超疏水涂层进行o2等离子刻蚀,结果如图6所示,刻蚀后超疏水涂层表面变为超亲水状态,微液滴能够在极短时间将表面完全润湿,cas为0
°
;当刻蚀后样品经高温处理(150℃,10min),涂层恢复超润湿性能,cas高于160
°
,此可治愈循环次数为14次,说明所述涂层具有良好的非机械损伤可治愈性能。
[0148]
实施例1~3制备的兼具光热除冰和长效防腐性能的超疏水涂层同样表现出良好的非机械损伤可治愈循环性能,润湿性恢复后涂层cas接近160
°
。
[0149]
(7)光热性能测试:
[0150]
采用波长为808nm、功率为2w的近红外光垂直照射纯树脂涂层和实施例1、3制备的涂层,并测量300s过程中不同涂层表面的温度变化,二者位置间距为15cm,环境温度为室温,结果如图7所示。测试结果表明:纯树脂涂层表面温度几乎未发生变化,然而实施例1制备的涂层的在近红外光照射100s后温度接近57℃,实施例3制备的涂层在近红外光照射100s后温度可达65℃以上,并随后保持稳定,实施例2、4所述涂层在近红外光照射100s后与实施例3接近。实施例1~4所述涂层与对比例所述纯树脂涂层相比,光热性能显著提升。而且,实施例1~4所述涂层均表现出良好的光热除冰性能,在涂层表面滴上150μl水滴,在低温环境中完全结冰后利用近红外光照射涂层表面,随着照射时间的延长,完全冻结的冰逐渐融化成冰水混合物,最后完全融化,在融化过程中,由于马兰欧尼力作用,冰与超疏水涂层表面接触区域的空气层逐渐恢复,冰融化形成的液滴依然保持球型且容易滚落,涂层展现出良好的光热除冰性能。
[0151]
(8)电化学阻抗谱进行测试:
[0152]
实施例4制备获得的兼具光热除冰和长效防腐性能超疏水涂层及镁合金基体的电化学阻抗谱如图8所示。结果表明:实施例4制备的超疏水涂层的低频阻抗模量(|z|
0.01hz
)值高达8.9
×
108ω
·
cm2左右,比镁合金基体试样高5个数量级,这表明所述超疏水涂层具有超强的物理腐蚀屏蔽作用,耐腐蚀性优异。当涂层样品浸泡14天后,|z|
0.01hz
值略有下降至7.5
×
106ω
·
cm2左右,但仍保持在较高水平,即使所述涂层样品浸泡21天,其|z|
0.01hz
值也高于
镁合金基体1个数量级,测试结果证实了所述超疏水涂层对基体具有良好的长效腐蚀防护效果。
[0153]
实施例1~3制备获得的兼具光热除冰和长效防腐性能超疏水涂层电化学阻抗谱测试结果与实施例4相近,低频阻抗模量均比基底镁合金高5个数量级左右,这表明超疏水涂层具有超强的物理腐蚀屏蔽作用,耐腐蚀性优异;涂层样品浸泡21天,其低频阻抗模量值也高于镁合金1个数量级,表现良好的长效腐蚀防护效果。