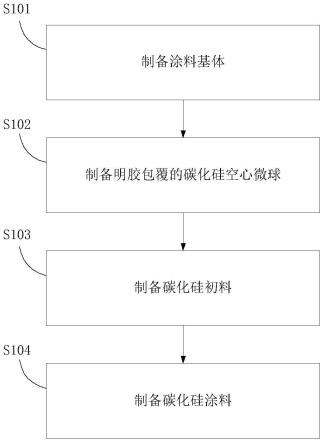
1.本发明涉及散热涂料技术领域,具体是涉及一种高传导热、高热辐射的碳化硅涂料及其制备方法。
背景技术:2.导热涂料是一种用于高温设备的高效导热节能环保产品,可直接涂覆在各种高温导热体的表面,提高导热体的导热能力,如涂刷蒸汽锅炉水冷壁管的表面,形成一层坚硬的陶瓷釉面硬壳,起到保护炉体、延长炉龄、增强水冷壁导热、从而起到节约燃料的作用。
3.导热涂料分为150℃以下低温型和耐高温1800℃两种类型;导热涂料含有多种红外辐射材料,在远红外、中红外、近红外各波段均有很高的红外辐射光谱发射率和优良的技术特性,涂覆于导热体表面可获得显著节能效果,具有提高辐射传热能力,减少散热损失。
4.导热涂料的涂层结构致密,具有很好的耐磨性、耐腐蚀性,可以有效的保护基体,针对在燃烧室换热管、换热片、导热管、高温模具、发热器、散热片、焦炉上升烟管等设备器件上导热防腐,为了提高以上设备器件的导热效果,现需要一种能够显著提升内外的热交换效率又能避免材料腐蚀的新型涂料。
技术实现要素:5.为解决上述技术问题,本发明提供了一种高传导热、高热辐射的碳化硅涂料及其制备方法。
6.本发明的技术方案是:一种高传导热、高热辐射的碳化硅涂料,按质量份数计包括10~30份改性碳化硅粉体、5~15份明胶包覆的碳化硅空心微球、5~8份无机粉体、2~5份金属氧化物、0.2~0.5份阻聚剂、0.2~0.5份流平剂、0.5~1份分散剂和30~50份无机树脂;
7.其中,所述改性碳化硅粉体为碳化硅粉体通过水解聚马来酸酐和硅烷偶联剂联合进行改性处理得到的,
8.所述明胶包覆的碳化硅空心微球是将碳化硅空心微球经过明胶包覆处理得到的;
9.所述明胶包覆处理的方法为:将碳化硅空心微球通过质量浓度为8~10%的hcl溶液浸泡5~10min,随后将碳化硅空心微球冲洗至中性,然后放置在明胶中,搅拌均匀后再静置10~30min,利用明胶对碳化硅空心微球进行包覆处理,然后取出,即得所述明胶包覆的碳化硅空心微球。
10.进一步地,所述改性碳化硅粉体的改性处理的方法包括以下步骤:
11.1)将水解马来酸酐和硅烷偶联剂按照质量比3~8:2进行混合,得到改性液;
12.2)将碳化硅颗粒填铺在滤网仓中,并浸没在步骤1)所得到的改性液中,并不断搅拌滤网仓中的碳化硅颗粒,在搅拌期间加入氨水使改性液的ph值在碱性范围内,
13.3)通过滤网仓从改性液中升出,使碳化硅颗粒每间隔x秒脱离改性液y秒,并同时采用200~500rad/s的辐射剂量对滤网仓中的碳化硅颗粒辐照n秒,随后滤网仓再次浸没在
改性液中并不断搅拌滤网仓中的碳化硅颗粒,
14.4)重复步骤3)处理5~8次,随后将滤网仓脱离改性液,静置后将滤网仓中的碳化硅颗粒研磨成粉,干燥处理后得到改性碳化硅粉体;
15.本发明通过对碳化硅进行改性处理,通过水解马来酸酐和硅烷偶联剂联合改性处理,可以有效的促进无机树脂与改性碳化硅粉体的包裹粘附,从而强化碳化硅涂料与涂覆面的结合效果,并且通过对碳化硅进行改性处理,利用间歇式的辐射处理可以促进改性液对碳化硅颗粒进行改性处理,从而显著降低碳化硅粉体团聚现象,进而提高碳化硅涂料的导热性能。
16.更进一步地,所述步骤3)中,x的取值范围为30~50s,y的取值范围为15~21s,n的取值范围与x、y相关,具体为:
[0017][0018]
其中,x表示滤网仓脱离改性液的间隔时长;y表示滤网仓脱离改性液的时长;n表示滤网仓中碳化硅颗粒激光辐照时长;j表示常量,当辐射剂量<340rad/s时,取j=3,当辐射剂量≥340rad/s时,取j=5;
[0019]
通过上述x、y、n时长取值范围的限定,从而可根据实际生产情况对步骤3)的改性处理进行精确调控,从而避免因辐照等参数影响改性碳化硅粉体所制备的碳化硅涂料导热效果。
[0020]
更进一步地,所述硅烷偶联剂为γ-氨丙基三乙氧基硅烷、γ-(甲基丙烯酰氧)丙基三甲氧基硅烷中的任意一种。
[0021]
进一步地,所述无机粉体包括高导热石墨、石墨烯中的一种或多种任意比混合;通过添加高导热石墨、石墨烯或高导热石墨与石墨烯的混合物,能够为金属氧化物构建微观空间网络,从而配合金属氧化物进行填充和勾连,从而提高碳化硅涂料的耐用性。
[0022]
进一步地,所述金属氧化物包括三氧化铬、氧化铝、二氧化硅中的一种或多种任意比混合;通过添加三氧化铬、氧化铝或二氧化硅,能够对无机粉体所构建的微观空间网络进行填充和勾连,形成一个粉体颗粒微观导热结构内部网,从而提高碳化硅涂料的导热性能以及耐用性。
[0023]
进一步地,所述阻聚剂为对苯二酚、叔丁基邻苯二酚和环烷酸铜按照质量比2:1:1的混合物,所述流平剂为二丙酮醇、solvesso150中的任意一种,所述分散剂为十二烷基硫酸钠、脂肪酸聚乙二醇酯中的任意一种。
[0024]
本发明还提供了一种高传导热、高热辐射的碳化硅涂料的制备方法,包括以下步骤:
[0025]
s101、制备涂料基体
[0026]
按所述重量份将改性碳化硅粉体、阻聚剂依次加入至无机树脂中,并超声搅拌混合,混匀后得到涂料基体;
[0027]
s102、制备明胶包覆的碳化硅空心微球
[0028]
将碳化硅空心微球通过质量浓度为8~10%的hcl溶液浸泡5~10min,随后将碳化硅空心微球冲洗至中性,然后放置在明胶中,搅拌均匀后再静置10~30min,利用明胶对碳化硅空心微球进行包覆处理,然后取出,即得所述明胶包覆的碳化硅空心微球,待用;
[0029]
s103、制备碳化硅初料
[0030]
按所述重量份将无机粉体、金属氧化物和明胶包覆的碳化硅空心微球进行搅拌混合得到混合物,随后将所述混合物和涂料基体放入温度为5℃的低温水浴槽中,并施加电场强度为2
×
103~4
×
103v/m的静电场5~10min,期间不断搅拌,混匀后得到碳化硅初料;通过施加静电场作用,可以促进明胶的卷曲-螺旋转化,从而提高与无机粉体、金属氧化物的包覆结合,为后续碳化硅涂料的制备提供良好的初始条件;
[0031]
s104、制备碳化硅涂料
[0032]
将流平剂加入低温水浴槽中的碳化硅初料,随后以3~5℃升温速率进行升温至40~50℃,并超声搅拌混合,混匀后即得到所述高传导热、高热辐射的碳化硅涂料,通过上述升温速率进行搅拌混合,可以促进明胶包覆的碳化硅空心微球的明胶进行溶解,从而通过明胶包覆的碳化硅空心微球的搅拌混合提高无机粉体、金属氧化物与涂料基体的混合度,并且通过碳化硅空心微球还可以有效提高涂料的耐腐蚀以及热交换效率。
[0033]
本发明的有益效果是:
[0034]
(1)本发明的碳化硅涂料以改性碳化硅粉体和无机树脂构建的涂料基体,配合无机粉体以及金属氧化物强化导热性能,不仅可以提高碳化硅涂料的耐用性,而且有效提高了碳化硅涂料涂覆后管件内外的热交换效率。
[0035]
(2)本发明的碳化硅涂料通过对碳化硅进行改性处理,可以促进无机树脂与改性碳化硅粉体的包裹粘附效果,从而有效的强化碳化硅涂料与涂覆面的结合效果,并且可以有效的降低碳化硅粉体团聚,进而提高碳化硅涂料的导热性能。
附图说明
[0036]
图1是本发明碳化硅涂料制备方法的流程图。
具体实施方式
[0037]
下面结合具体实施方式来对本发明进行更进一步详细的说明,以更好地体现本发明的优势。
[0038]
实施例1
[0039]
一种高传导热、高热辐射的碳化硅涂料,按质量份数计包括18份改性碳化硅粉体、12份明胶包覆的碳化硅空心微球、7份无机粉体、4份金属氧化物、0.4份阻聚剂、0.4份流平剂、0.7份分散剂和43份无机树脂;
[0040]
其中,所述明胶包覆的碳化硅空心微球是将碳化硅空心微球经过明胶包覆处理得到的;
[0041]
所述明胶包覆处理的方法为:将碳化硅空心微球通过质量浓度为10%的hcl溶液浸泡7min,随后将碳化硅空心微球冲洗至中性,然后放置在明胶中,搅拌均匀后再静置25min,利用明胶对碳化硅空心微球进行包覆处理,然后取出,即得所述明胶包覆的碳化硅空心微球;
[0042]
所述改性碳化硅粉体为碳化硅粉体通过水解聚马来酸酐和硅烷偶联剂联合改性处理得到的,所述改性碳化硅粉体的改性处理的方法包括以下步骤:
[0043]
1)将水解马来酸酐和硅烷偶联剂按照质量比7:2进行混合,得到改性液,所述硅烷
偶联剂为γ-氨丙基三乙氧基硅烷;
[0044]
2)将碳化硅颗粒填铺在滤网仓中,并浸没在步骤1)所得到的改性液中,并不断搅拌滤网仓中的碳化硅颗粒,在搅拌期间加入氨水使改性液的ph值=9,
[0045]
3)通过滤网仓从改性液中升出,使碳化硅颗粒每间隔x秒脱离改性液y秒,并同时采用210rad/s的辐射剂量对滤网仓中的碳化硅颗粒辐照n秒,随后滤网仓再次浸没在改性液中并不断搅拌滤网仓中的碳化硅颗粒,
[0046]
其中,x的取值范围为45s,y的取值范围为18s,n的取值范围与x、y相关,具体为:
[0047][0048]
其中,x表示滤网仓脱离改性液的间隔时长;y表示滤网仓脱离改性液的时长;n表示滤网仓中碳化硅颗粒激光辐照时长;j表示常量,当辐射剂量<340rad/s时,取j=3,当辐射剂量≥340rad/s时,取j=5;
[0049]
由公式(1)计算得,n为9s;
[0050]
通过上述x、y、n时长取值范围的限定,从而可根据实际生产情况对步骤3)的改性处理进行精确调控,从而避免因辐照等参数影响改性碳化硅粉体所制备的碳化硅涂料导热效果;
[0051]
4)重复步骤3)处理6次,随后将滤网仓脱离改性液,静置后将滤网仓中的碳化硅颗粒研磨成粉,干燥处理后得到改性碳化硅粉体;
[0052]
通过对碳化硅进行改性处理,通过水解马来酸酐和硅烷偶联剂联合改性处理,可以有效的促进无机树脂与改性碳化硅粉体的包裹粘附,从而强化碳化硅涂料与涂覆面的结合效果,并且通过对碳化硅进行改性处理,利用间歇式的辐射处理可以促进改性液对碳化硅颗粒进行改性处理,从而显著降低碳化硅粉体团聚现象,进而提高碳化硅涂料的导热性能;
[0053]
所述无机粉体包括高导热石墨、石墨烯按照质量比5:2混合;通过添加高导热石墨与石墨烯的混合物,能够为金属氧化物构建微观空间网络,从而配合金属氧化物进行填充和勾连,从而提高碳化硅涂料的耐用性;
[0054]
所述金属氧化物包括氧化铝、二氧化硅按照质量比1:2混合;通过添加金属氧化物,能够对无机粉体所构建的微观空间网络进行填充和勾连,形成一个粉体颗粒微观导热结构内部网,从而提高碳化硅涂料的导热性能以及耐用性;
[0055]
所述阻聚剂为对苯二酚、叔丁基邻苯二酚和环烷酸铜按照质量比2:1:1的混合物,所述流平剂为二丙酮醇,所述分散剂为十二烷基硫酸钠;
[0056]
上述高传导热、高热辐射的碳化硅涂料的制备方法,包括以下步骤:
[0057]
s101、制备涂料基体
[0058]
按所述重量份将改性碳化硅粉体、阻聚剂依次加入至无机树脂中,并超声搅拌混合,混匀后得到涂料基体;
[0059]
s102、制备明胶包覆的碳化硅空心微球
[0060]
将碳化硅空心微球通过质量浓度为10%的hcl溶液浸泡7min,随后将碳化硅空心微球冲洗至中性,然后放置在明胶中,搅拌均匀后再静置25min,利用明胶对碳化硅空心微球进行包覆处理,然后取出,即得所述明胶包覆的碳化硅空心微球,待用;
[0061]
s103、制备碳化硅初料
[0062]
按所述重量份将无机粉体、金属氧化物和明胶包覆的碳化硅空心微球进行搅拌混合得到混合物,随后将所述混合物和涂料基体放入温度为5℃的低温水浴槽中,并施加电场强度为3.5
×
103v/m的静电场8min,期间不断搅拌,混匀后得到碳化硅初料;通过施加静电场作用,可以促进明胶的卷曲-螺旋转化,从而提高与无机粉体、金属氧化物的包覆结合,为后续碳化硅涂料的制备提供良好的初始条件;
[0063]
s104、制备碳化硅涂料
[0064]
将流平剂加入低温水浴槽中的碳化硅初料,随后以4℃升温速率进行升温至40℃,并超声搅拌混合,混匀后即得到所述高传导热、高热辐射的碳化硅涂料,通过上述升温速率进行搅拌混合,可以促进明胶包覆的碳化硅空心微球的明胶进行溶解,从而通过明胶包覆的碳化硅空心微球的搅拌混合提高无机粉体、金属氧化物与涂料基体的混合度,并且通过碳化硅空心微球还可以有效提高涂料的耐腐蚀以及热交换效率。
[0065]
实施例2
[0066]
本实施例与实施例1基本相同,与其不同之处在于,一种高传导热、高热辐射的碳化硅涂料,按质量份数计包括10份改性碳化硅粉体、5份明胶包覆的碳化硅空心微球、5份无机粉体、2份金属氧化物、0.2份阻聚剂、0.2份流平剂、0.5份分散剂和30份无机树脂。
[0067]
实施例3
[0068]
本实施例与实施例1基本相同,与其不同之处在于,一种高传导热、高热辐射的碳化硅涂料,按质量份数计包括30份改性碳化硅粉体、15份明胶包覆的碳化硅空心微球、8份无机粉体、5份金属氧化物、0.5份阻聚剂、0.5份流平剂、1份分散剂和50份无机树脂。
[0069]
实施例4
[0070]
本实施例与实施例1基本相同,与其不同之处在于,1)将水解马来酸酐和硅烷偶联剂按照质量比3:2进行混合,得到改性液,所述硅烷偶联剂为γ-氨丙基三乙氧基硅烷。
[0071]
实施例5
[0072]
本实施例与实施例1基本相同,与其不同之处在于,1)将水解马来酸酐和硅烷偶联剂按照质量比8:2进行混合,得到改性液,所述硅烷偶联剂为γ-氨丙基三乙氧基硅烷。
[0073]
实施例6
[0074]
本实施例与实施例1基本相同,与其不同之处在于,3)通过滤网仓从改性液中升出,使碳化硅颗粒每间隔x秒脱离改性液y秒,并同时采用200rad/s的辐射剂量对滤网仓中的碳化硅颗粒辐照n秒,随后滤网仓再次浸没在改性液中并不断搅拌滤网仓中的碳化硅颗粒,
[0075]
其中,x的取值范围为30s,y的取值范围为15s,n的取值范围与x、y相关,具体为:
[0076][0077]
其中,x表示滤网仓脱离改性液的间隔时长;y表示滤网仓脱离改性液的时长;n表示滤网仓中碳化硅颗粒激光辐照时长;j表示常量(当辐射剂量<340rad/s时,取j=3,当辐射剂量≥340rad/s时,取j=5);
[0078]
由公式(1)计算得,n为5s。
[0079]
实施例7
[0080]
本实施例与实施例1基本相同,与其不同之处在于,3)通过滤网仓从改性液中升出,使碳化硅颗粒每间隔x秒脱离改性液y秒,并同时采用500rad/s的辐射剂量对滤网仓中的碳化硅颗粒辐照n秒,随后滤网仓再次浸没在改性液中并不断搅拌滤网仓中的碳化硅颗粒,
[0081]
其中,x的取值范围为50s,y的取值范围为21s,n的取值范围与x、y相关,具体为:
[0082][0083]
其中,x表示滤网仓脱离改性液的间隔时长;y表示滤网仓脱离改性液的时长;n表示滤网仓中碳化硅颗粒激光辐照时长;j表示常量(当辐射剂量<340rad/s时,取j=3,当辐射剂量≥340rad/s时,取j=5);
[0084]
由公式(1)计算得,n为5.8s。
[0085]
实施例8
[0086]
本实施例与实施例1基本相同,与其不同之处在于,4)重复步骤3)处理5次,随后将滤网仓脱离改性液,静置后将滤网仓中的碳化硅颗粒研磨成粉,干燥处理后得到改性碳化硅粉体。
[0087]
实施例9
[0088]
本实施例与实施例1基本相同,与其不同之处在于,4)重复步骤3)处理8次,随后将滤网仓脱离改性液,静置后将滤网仓中的碳化硅颗粒研磨成粉,干燥处理后得到改性碳化硅粉体。
[0089]
实施例10
[0090]
本实施例与实施例1基本相同,与其不同之处在于,如图1所示,上述高传导热、高热辐射的碳化硅涂料的制备方法,包括以下步骤:
[0091]
s101、制备涂料基体
[0092]
将改性碳化硅粉体、阻聚剂依次加入至无机树脂中,并超声搅拌混合,混匀后得到涂料基体;
[0093]
s102、制备明胶包覆的碳化硅空心微球
[0094]
将碳化硅空心微球通过质量浓度为10%的hcl溶液浸泡7min,随后将碳化硅空心微球冲洗至中性,然后放置在明胶中,搅拌均匀后再静置25min,利用明胶对碳化硅空心微球进行包覆处理,然后取出,即得所述明胶包覆的碳化硅空心微球,待用;
[0095]
s103、制备碳化硅初料
[0096]
将无机粉体、金属氧化物和碳化硅空心微球进行搅拌混合得到混合物,随后将所述混合物和涂料基体放入温度为5℃的低温水浴槽中,并施加电场强度为2
×
103v/m的静电场8min,期间不断搅拌,混匀后得到碳化硅初料;
[0097]
s104、制备碳化硅涂料
[0098]
将流平剂加入低温水浴槽中的碳化硅初料,随后以3℃升温速率进行升温至40℃,并超声搅拌混合,混匀后得到碳化硅涂料。
[0099]
实施例11
[0100]
本实施例与实施例1基本相同,与其不同之处在于,如图1所示,上述高传导热、高热辐射的碳化硅涂料的制备方法,包括以下步骤:
[0101]
s101、制备涂料基体
[0102]
将改性碳化硅粉体、阻聚剂依次加入至无机树脂中,并超声搅拌混合,混匀后得到涂料基体;
[0103]
s102、制备明胶包覆的碳化硅空心微球
[0104]
将碳化硅空心微球通过质量浓度为10%的hcl溶液浸泡7min,随后将碳化硅空心微球冲洗至中性,然后放置在明胶中,搅拌均匀后再静置25min,利用明胶对碳化硅空心微球进行包覆处理,然后取出,即得所述明胶包覆的碳化硅空心微球,待用;
[0105]
s103、制备碳化硅初料
[0106]
将无机粉体、金属氧化物和碳化硅空心微球进行搅拌混合得到混合物,随后将所述混合物和涂料基体放入温度为5℃的低温水浴槽中,并施加电场强度为4
×
103v/m的静电场8min,期间不断搅拌,混匀后得到碳化硅初料;
[0107]
s104、制备碳化硅涂料
[0108]
将流平剂加入低温水浴槽中的碳化硅初料,随后以5℃升温速率进行升温至50℃,并超声搅拌混合,混匀后得到碳化硅涂料。
[0109]
实验例
[0110]
分别通过实施例1-11所制备的碳化硅涂料作为实验样本,以涂层传导系数对实施例1-11的碳化硅涂料进行实验对比,具体如下:
[0111]
1)探究一 不同碳化硅涂料配比对涂料导热系数的影响
[0112]
以实施例1和2、3进行对比,分别测定各实施例的碳化硅涂料固化好的涂层传导系数(70℃),结果如下表1所示:
[0113]
表1实施例1、2、3的碳化硅涂料的导热系数表
[0114] 实施例1实施例2实施例3涂层传导系数(70℃)104w/(m.k)96w/(m.k)99w/(m.k)
[0115]
由上表1结果可以看出,实施例1、2、3的碳化硅涂料各物质配比不同,对所制备的碳化硅涂料的涂层传导系数(70℃)有一定影响,其中,以实施例1所制备的碳化硅涂料的导热系数最高。
[0116]
2)探究二 不同碳化硅改性处理对涂料导热系数的影响
[0117]
以实施例1和4、5进行对比,同时以实施例1为例,采用与水解马来酸酐相同质量的硅烷偶联剂替换水解马来酸酐,作为对照例1,分别测定各实施例以及对照例1的碳化硅涂料固化好的涂层传导系数(70℃),结果如下表2所示:
[0118]
表2实施例1、4、5的碳化硅涂料的导热系数表
[0119][0120]
由上表2结果可以看出,实施例1、4、5的改性液中水解马来酸酐和硅烷偶联剂配比不同,对所制备的碳化硅涂料的涂层传导系数(70℃)有一定影响;其中,以实施例1所制备的碳化硅涂料的导热系数最高;
[0121]
由上表2结果可以看出,实施例1采用水解马来酸酐和硅烷偶联剂联合改性处理碳化硅,对照例1采用硅烷偶联剂改性处理碳化硅,所制备的碳化硅涂料的导热系数有一定差
别,其中,以实施例1所制备的碳化硅涂料的导热系数更高。
[0122]
3)探究三 不同碳化硅改性处理的辐照参数对涂料导热系数的影响
[0123]
以实施例1和6、7进行对比,分别测定各实施例的碳化硅涂料固化好的涂层传导系数(70℃),结果如下表3所示:
[0124]
表3实施例1、6、7的碳化硅涂料的导热系数表
[0125] 实施例1实施例6实施例7涂层传导系数(70℃)104w/(m.k)104w/(m.k)103w/(m.k)
[0126]
由上表3结果可以看出,实施例1、6、7采用了不同辐照参数,但实施例1、6、7所制备的碳化硅涂料的涂层传导系数(70℃)基本相同,因此,通过x、y、n的取值选择,可以根据实际生产条件进行适应调整,从而获取性能稳定的碳化硅涂料;
[0127]
同时,为了进一步探究通过x、y、n的取值选择对改性碳化硅粉体以及所制备碳化硅涂料的影响,以实施例1为例,分别设定n为7s,11s作为对照例2、对照例3,且其余参数均不变,分别测定各碳化硅涂料固化好的涂层传导系数(70℃),结果如下表4所示:
[0128] 实施例1对照例2对照例3涂层传导系数(70℃)104w/(m.k)97w/(m.k)100w/(m.k)
[0129]
由上表4结果可以看出,对照例2和对照例3与实施例1仅是滤网仓中碳化硅颗粒激光辐照时长的不同,但实施例1、对照例2、对照例3所制备的碳化硅涂料的涂层传导系数(70℃)不同,其中,以实施例1所制备的碳化硅涂料的导热系数最高。
[0130]
4)探究四 不同碳化硅改性处理的处理次数对涂料导热系数的影响
[0131]
以实施例1和8、9进行对比,分别测定各实施例的碳化硅涂料固化好的涂层传导系数(70℃),结果如下表5所示:
[0132]
表5实施例1、8、9的碳化硅涂料的导热系数表
[0133] 实施例1实施例8实施例9涂层传导系数(70℃)104w/(m.k)99w/(m.k)103w/(m.k)
[0134]
由上表5结果可以看出,实施例1、8、9采用了不同步骤3)重复处理次数,对所制备的碳化硅涂料的涂层传导系数(70℃)有一定影响,其中,以实施例1所制备的碳化硅涂料的导热系数最高。
[0135]
5)探究五 不同碳化硅涂料制备方法对涂料导热系数的影响
[0136]
以实施例1和10、11进行对比,分别测定各实施例的碳化硅涂料固化好的涂层传导系数(70℃),结果如下表6所示:
[0137]
表6实施例1、10、11的碳化硅涂料的导热系数表
[0138] 实施例1实施例10实施例11涂层传导系数(70℃)104w/(m.k)94w/(m.k)104w/(m.k)
[0139]
由上表6结果可以看出,实施例1、10、11采用了不同制备方法,对所制备的碳化硅涂料的涂层传导系数(70℃)有一定影响,其中,以实施例1和实施例11所制备的碳化硅涂料的导热系数最高,考虑到生产成本等因素,实施例11与实施例1导热系数差别不大,实施例1所制备的碳化硅涂料的经济性更好。