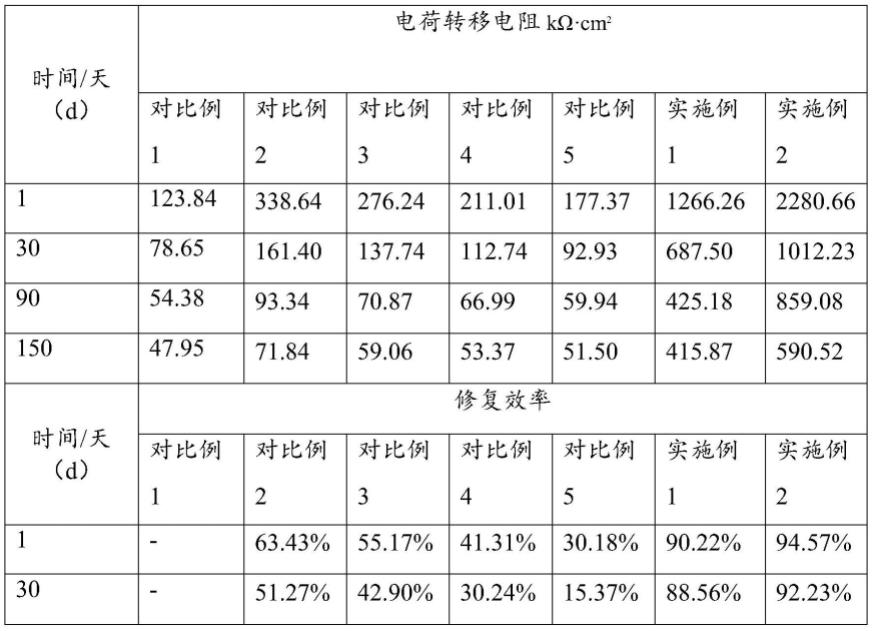
1.本发明涉及聚脲涂料技术领域,尤其涉及一种光伏屋面用自修复聚脲涂料及其制备方法。
背景技术:2.光伏组件的技术已然成熟,但制约光伏建设应用的漏水问题常常被忽视。光伏组件防水屋顶常规做法包括打胶,铝箔胶带粘接,彩钢瓦衬底,定制导流支架,定制组件边框,bi pv专用构件等。若只靠彩钢瓦的自防水形式,很容易因为涂层厚度不够,在紫外线、雨水、风震、音震等作用下,容易使垫圈老化脆硬开裂,铆钉松动,锈蚀扩大;而且酸性、碱性、强氧气体腐蚀钢结构,也加速钢结构的锈蚀、穿孔。彩钢瓦一旦漏水,建筑物施工时必须将光伏组件拆除后才能维修翻新,由此,建筑物的翻新成本和难度大大增加。
3.光伏组件的设计使用寿命通常为25年,钢结构的使用寿命与光伏组件 25年的使用寿命并不匹配,而且既有建筑光伏改造过程中是不涉及与防水层的衔接。
4.如中国专利cn201810669687.6公开了一种高强度单层屋面防水卷材及其制备方法。该专利中指出高强度单层屋面防水卷材尺寸稳定性强,外观平直度好、具有良好的耐热性和阻燃性,长期暴露下使用寿命高,具有良好的高低温环境耐候性能,同时兼具优异的拉伸强力和抗撕裂性;cn201620323643.4 的实用新型也公开了一种防水耐候聚脲涂层,其由底漆层、设于底漆层上的修补腻子层、设于修补腻子层上的面漆层组成。该涂层无溶剂,无污染,施工方便,涂层连续、致密、无接缝,具有优异的理化性能和稳定性,不易变色,可广泛用于旧屋面防水翻新工程。但是,防水卷材应用于屋面防水一般采用机械固定和热风焊接固定,接缝易出现渗漏,现场异型结构需要裁切。聚脲涂层虽然具有优异的理化性能和稳定性,应用于屋面光伏防水有连续、致密、无接缝的优势,但是光伏设备自重大,屋面承重较高,屋面型变量大,人员检修频繁,踩踏走动频繁等都加重了光伏屋面表面被机械损伤导致涂层破损的风险,一旦屋面出现破损渗漏,修复又成为难题。
5.因此,实现光伏与建筑的深度融合,从根本上解决光伏屋面的防水问题具有重要意义。
技术实现要素:6.有鉴于此,本发明所要解决的技术问题在于提供了一种光伏屋面用自修复聚脲涂料及其制备方法,本发明提供的自修复聚脲涂料通过涂层的自修复可为光伏屋面的可持续、安全持久提供保护。
7.与现有技术相比,本发明提供的一种光伏屋面用自修复聚脲涂料,包括:含有自修复微胶囊的聚脲材料a和胺基固化剂b;所述自修复微胶囊从内向外依次包括:钴/铬金属层、固化剂层、异氰酸酯预聚物层;其中,通过选择所述第一异氰酸酯为特定的多异氰酸酯;并使所述含有自修复微胶囊的聚脲材料a中的nco含量控制在2.0wt%~5.0wt%;实验结果表明,本发明得到的自修复聚脲涂料能够在屋面太阳能暴露下,即,微胶囊破损和太阳能量
都具备的条件下,自修复涂层会启动修复过程,实现了屋面的自修复,且能够避免了生产和施工过程中微胶囊破裂,造成微胶囊提前失效。
具体实施方式
8.本发明提供了一种光伏屋面用自修复聚脲涂料,包括:含有自修复微胶囊的聚脲材料a和胺基固化剂b;
9.所述自修复微胶囊从内向外依次包括:钴/铬金属层、固化剂层、异氰酸酯预聚物层;其中,所述异氰酸酯预聚物层的异氰酸酯为第一多异氰酸酯;
10.所述含有自修复微胶囊的聚脲材料中的nco含量为2.0wt%~5.0wt%。
11.按照本发明,所述自修复微胶囊中,所述固化剂层的固化剂为n,n'-(亚甲基二-4,1-环己胺二基)双-1,1',4,4'-四乙基酯和n,n'-(2-甲基-1,5-戊二醇)双
ꢀ‑
1,1',4,4'-四乙基酯中的一种或两种,更优选的,固化剂的型号为desmophennh 1220或desmophen nh 1420;所述固化剂层用固化剂与钴/铬金属层用钴盐和所述铬盐的质量比优选为(10~20):(5~10):(5~10);所述第一多异氰酸酯为甲苯-2,4-二异氰酸酯和甲苯-2,6-二异氰酸酯中的一种或两种;所述第一多异氰酸酯与所述钴盐和所述铬盐的质量比优选为(5~10):(5~10): (5~10)。
12.本发明中,所述含有自修复微胶囊的聚脲材料a由第一多元醇、第二多异氰酸酯和自修复微胶囊混合制备得到;所述第二多异氰酸酯为甲苯-2,4-二异氰酸酯和甲苯-2,6-二异氰酸酯中的一种或两种;所述第一多元醇优选为低不饱和度的聚氧化丙烯二醇、聚四氢呋喃醚二醇、聚己内酯二醇、聚酯二醇和聚碳酸酯二醇中的一种或几种;所述第一多元醇的平均分子量优选在 400-1500之间,其含水量优选≤0.5%,酸值优选≤0.8mg koh/g。所述第一多元醇的型号优选为ptmeg1000或ptmeg650所述第一多元醇和自修复微胶囊的质量比优选为(50~110):(10~30);更优选为(50~100):(10~30)。所述含有自修复微胶囊的聚脲材料中的nco含量优选为2.0wt%~3.5wt%,更优选为2.5wt%~3.0wt%。
13.按照本发明,所述胺基固化剂b优选包括以下组分:固化剂、第二多元醇、偶联剂、扩链剂、催化剂、除水剂和色浆。其中,所述固化剂优选为n,n'-(亚甲基二-4,1-环己胺二基)双-1,1',4,4'-四乙基酯和n,n'-(2-甲基-1,5-戊二醇)双
ꢀ‑
1,1',4,4'-四乙基酯中的一种或两种,更优选的,固化剂的型号为desmophennh 1220或desmophen nh 1420;所述第二多元醇优选为低不饱和度的聚氧化丙烯二醇、聚四氢呋喃醚二醇、聚己内酯二醇、聚酯二醇和聚碳酸酯二醇中的一种或几种;所述多元醇的平均分子量优选在400-1500之间,其含水量优选≤0.5%,酸值优选≤0.8mg koh/g;所述第二多元醇的型号优选为 ptmeg1000或ptmeg650;所述扩链剂优选为3,5-二甲硫基甲苯二胺(e-300)、 2,4-二氨基-3,5-二甲硫基氯苯(tx-2)、4,4
′‑
双仲丁氨基二苯基甲烷 (unilink4200)、n,n,-二烷基苯二胺、2,4-二氨基-3-甲硫基-5-丙基甲苯(tx-3)、 3,3
′‑
二甲基-4,4
′‑
二氨基二环己基甲烷、4,4,-双仲丁氨基二环己基甲烷、3, 3,-二甲基-4,4,-双仲丁氨基-二环己基甲烷、三甲基己二胺或氢化mda;所述偶联剂优选为硅烷偶联剂、硼酸酯偶联剂、铝酸酯偶联剂、硼酸酯偶联剂、双金属偶联剂和磷酸酯偶联剂中的一种或几种,所述的催化剂优选为异辛酸铋,异辛酸锌,三乙烯二胺,双吗啉基二乙基醚、硼酸四丁酯和硼酸四异丙酯中的一种或几种,所述的除水剂为分子筛,所述分子筛规格为3a或4a。本发明对所述的色浆没有特殊要求,行业通用聚氨酯色浆
即可,其颜色包括:红、黄、蓝、绿、白、黑色浆,其含水量≤0.5%;所述固化剂、多元醇、偶联剂、扩链剂、催化剂、除水剂和色浆的质量比优选为(30~60):(20~50):(1~2): (20~40):(0~1):(1~5):(1~5)。
14.本发明还提供了一种光伏屋面用自修复聚脲涂料的制备方法,包括:
15.1)将固化剂、溶剂、表面活性剂混合,得到固化剂乳化液;
16.将固化剂乳化液与铬盐、钴盐混合,焙烧得到钴/铬包裹固化剂微球;
17.将第一多异氰酸酯、多元醇、溶剂和表面活性剂混合反应得到预聚物乳化液;
18.将钴/铬包裹固化剂微球与预聚物乳化液混合反应,得到自修复微胶囊;
19.2)将第一多元醇、自修复微胶囊和多异氰酸酯1混合反应,得到含有自修复微胶囊的聚脲材料a;
20.所述含有自修复微胶囊的聚脲材料中的nco含量为2.0wt%~5.0wt%;
21.3)将含有自修复微胶囊的聚脲材料a和胺基固化剂b混合得到光伏屋面用自修复聚脲涂料。
22.按照本发明,将固化剂、溶剂、表面活性剂混合,得到固化剂乳化液;其中,其中,所述溶剂优选乙醇,所述表面活性剂优选为n-十二烷基二甲胺;所述固化剂、溶剂和表面活性剂的质量比优选为(10~20):100:(0.1~0.2);本发明对混合的方式没有特殊要求,本领域公知的混合方式即可,本发明优选在室温条件下7000转/分高速剪切混合。
23.按照本发明,将固化剂乳化液与铬盐、钴盐混合,焙烧得到钴/铬包裹固化剂微球;其中,所述铬盐为硝酸铬,其纯度优选≥98%;所述钴盐为硝酸钴,其纯度优选≥98%;所述固化剂、钴盐和铬盐的质量比优选为(10~20):(5~10): (5~10),本发明所述混合的方式没有特殊要求,优选常温磁力搅拌即可;所述焙烧的温度优选为500~800℃。
24.按照本发明,将第一多异氰酸酯、多元醇、溶剂和表面活性剂混合反应得到预聚物乳化液;其中,所述第一多异氰酸酯、多元醇的选择与前述涂料中成分的限定相同,所述溶剂优选为正己烷;所以表面活性剂优选为n-十二烷基二甲胺;所以第一多异氰酸酯、多元醇、溶剂和表面活性剂的质量比为 (5~10):(5~10):100:(0.1~0.2);本发明对混合的方式没有特殊要求,本领域公知的混合方式即可,本发明优选在室温条件下7000转/分高速剪切混合。
25.按照本发明,将钴/铬包裹固化剂微球与预聚物乳化液混合反应,得到自修复微胶囊;本发明所述混合的方式没有特殊要求,优选常温磁力搅拌即可;本发明还将混合反应得到的产物在60~80℃条件先干燥12小时。
26.按照本发明,将第一多元醇、自修复微胶囊和第二多异氰酸酯混合反应,得到含有自修复微胶囊的聚脲材料a;本发明中,所述第二多异氰酸酯优选为甲苯-2,4-二异氰酸酯和甲苯-2,6-二异氰酸酯中的一种或两种;所述第一多元醇与前述产品限定中的优选相同;所述第一多元醇与自修复微胶囊的质量比优选为(50~110):(10~30),更优选为(50~100):(10~30);本发明中,优选先将第一多元醇搅拌加热至95~105℃,加入自修复微胶囊,脱水5~ 7h,解除真空,降温至50℃以下,再加入多第二异氰酸酯,测定-nco值后出料,得到聚脲材料a;其中,所述第二多异氰酸酯的用量根据-nco值进行调整;所述含有自修复微胶囊的聚脲材料中的nco含量优选为2.0wt%~3.5wt%,更优选为2.5wt%~3.0wt%。
27.按照本发明,将含有自修复微胶囊的聚脲材料a和胺基固化剂b混合得到光伏屋面
用自修复聚脲涂料。本发明中,所述含有自修复微胶囊的聚脲材料a 和胺基固化剂b的异氰酸酯指数为1.05~1.10;所述胺基固化剂b优选由固化剂、第二多元醇、偶联剂、扩链剂、催化剂、除水剂和色浆混合制备得到。其中,所述固化剂优选为n,n'-(亚甲基二-4,1-环己胺二基)双-1,1',4,4'-四乙基酯和n,n'-(2-甲基-1,5-戊二醇)双-1,1',4,4'-四乙基酯中的一种或两种。;所述第二多元醇优选为低不饱和度的聚氧化丙烯二醇、聚四氢呋喃醚二醇、聚己内酯二醇、聚酯二醇和聚碳酸酯二醇中的一种或几种;所述多元醇的平均分子量优选在400-1500之间,其含水量优选≤0.5%,酸值优选≤0.8mg koh/g;所述扩链剂优选为3,5-二甲硫基甲苯二胺(e-300)、2,4-二氨基-3,5-二甲硫基氯苯 (tx-2)、4,4
′‑
双仲丁氨基二苯基甲烷(unilink4200)、n,n,-二烷基苯二胺、2,4
‑ꢀ
二氨基-3-甲硫基-5-丙基甲苯(tx-3)、3,3
′‑
二甲基-4,4
′‑
二氨基二环己基甲烷、4,4,-双仲丁氨基二环己基甲烷、3,3,-二甲基-4,4,-双仲丁氨基-二环己基甲烷、三甲基己二胺或氢化mda;所述偶联剂优选为硅烷偶联剂、硼酸酯偶联剂、铝酸酯偶联剂、硼酸酯偶联剂、双金属偶联剂和磷酸酯偶联剂中的一种或几种,所述的催化剂优选为异辛酸铋,异辛酸锌,三乙烯二胺,双吗啉基二乙基醚、硼酸四丁酯和硼酸四异丙酯中的一种或几种,所述的除水剂为分子筛,所述分子筛规格为3a或4a。本发明对所述的色浆没有特殊要求,行业通用聚氨酯色浆即可,其颜色包括:红、黄、蓝、绿、白、黑色浆,其含水量≤0.5%;所述固化剂、多元醇、偶联剂、扩链剂、催化剂、除水剂和色浆的质量比优选为(30~60):(20~50):(1~2):(20~40):(0~1):(1~5):(1~5)。本发明对混合制备的方法没有特殊要求,本领域公知的胺固化剂的混合方式均可。
28.本发明提供的光伏屋面用自修复聚脲涂料通过首先将固化剂与硝酸铬、硝酸钴反应,生成钴/铬金属包裹固化剂微球,继续滴加多异氰酸酯预聚物乳液,生成自修复微胶囊。然后自修复颗粒通过混合到聚脲涂料a中,然后与胺基固化剂一起喷涂到光伏屋面,结果发现,本技术通过控制自修复微胶囊外层材料的选择以及聚脲材料a中的-nco值,使得本声明提供的涂料只有在微胶囊破损和太阳能量都具备的条件下,涂料的自修复涂层才会发生作用,启动修复过程。这就避免了生产和施工过程中微胶囊破裂,造成微胶囊提前失效;使得得到的光伏屋面用自修复聚脲涂料具有更好的自修复可控性。
29.另外,本技术中低不饱和度的聚氧化丙烯二醇中的低不饱和度为本领域技术人员公知的低不饱和度。
30.下面将结合本发明实施例的技术方案进行清楚、完整地描述,显然,所描述的实施例仅仅是本发明一部分实施例,而不是全部的实施例。基于本发明中的实施例,本领域普通技术人员在没有做出创造性劳动前提下所获得的所有其他实施例,都属于本发明保护的范围。
31.需要指出的是,实施例中加料的份数均为重量份。
32.实施例1
33.(1)聚脲材料a组分的合成:
34.将10份固化剂(desmophen nh 1220)置于100份乙醇中,加入0.1 份n-十二烷基二甲胺,在室温条件下7000转/分高速剪切搅拌得到固化剂乳化液,继续加入5份硝酸铬、5份硝酸钴,在室温条件下磁力搅拌2小时,之后500℃焙烧,得到钴/铬包裹固化剂微球。
35.取5份甲苯-2,4-二异氰酸酯与5份甲苯-2,6-二异氰酸酯置于100份正己烷中,加入0.1份n-十二烷基二甲胺,在室温条件下7000转/分高速剪切搅拌得到预聚物乳化液。将
上述制备好的钴/铬包裹固化剂微球加入到此预聚物乳化液中,在室温条件下磁力搅拌2小时,反应完成通过离心收集得到沉淀,用水洗涤三次,然后在真空干燥箱中60℃干燥12h,获得自修复微胶囊。
36.100份ptmeg1000搅拌加热至95℃,在真空-0.1mpa下,加入上述10 份自修复微胶囊,脱水5~7h,解除真空,降温至50℃以下,再加入甲苯-2,4
‑ꢀ
二异氰酸酯,在90℃下反应3h,测定-nco值3.0%后出料。
37.(2)b组分的制备
38.按配方顺序称量各组分,将30份n,n'-(亚甲基二-4,1-环己胺二基)双
ꢀ‑
1,1',4,4'-四乙基酯,20份ptmeg1000,2份硅烷偶联剂a171,35份扩链剂e100, 0.1份催化剂异辛酸铋、5份3a分子筛,1份色浆,依次投入高速分散机储料罐中,室温搅拌15~30min,然后经砂磨机研磨至细度合格后用200目铜滤网过滤包装,制得b组分。
39.将体积比为1:1的a组分和b组分,通过喷涂机混合均匀并喷涂于钢板表面,涂层置于温度为(25
±
2)℃、湿度为(50
±
5)%的环境中,养护7天后,测试性能如下:拉伸强度21mpa,断裂伸长率450%,材料修复率见表1。
40.实施例2
41.(1)聚脲材料a组分的合成:
42.将20份desmophen nh 1420置于100份乙醇中,加入0.1份n-十二烷基二甲胺,在室温条件下7000转/分高速剪切搅拌得到固化剂乳化液,继续加入10份硝酸铬、10份硝酸钴,在室温条件下磁力搅拌2小时,之后500℃焙烧,得到钴/铬包裹固化剂微球。
43.取5份甲苯-2,4-二异氰酸酯与5份甲苯-2,6-二异氰酸酯置于100份正己烷中,加入0.1份n-十二烷基二甲胺,在室温条件下7000转/分高速剪切搅拌得到预聚物乳化液。将上述制备好的钴/铬包裹固化剂微球加入到此预聚物乳化液中,在室温条件下磁力搅拌2小时,反应完成通过离心收集得到沉淀,用水洗涤三次,然后在真空干燥箱中60℃干燥12h,获得自修复微胶囊。
44.将150份ptmeg1000搅拌加热至95℃,在真空-0.1mpa下,加入上述 30份自修复微胶囊,脱水5h,解除真空,降温至50℃以下加入200份甲苯-2,4
‑ꢀ
二异氰酸酯,在90℃下反应4h,反应结束后,测定-nco值为3.5%后出料,包装。
45.(2)b组分的制备:
46.按配方顺序称量各组分,将50份n,n'-(亚甲基二-4,1-环己胺二基)双
ꢀ‑
1,1',4,4'-四乙基酯,20份ptmeg650,1份硼酸酯偶联剂kr-tts,20份扩链剂unilink4200,1份4a分子筛,4份色浆,依次投入高速分散机储料罐中,室温搅拌15min,然后经砂磨机研磨,过滤包装,制得b组分。
47.将体积比为1:1的a组分和b组分,通过喷涂机混合均匀并喷涂于钢板表面,涂层置于温度为(25
±
2)℃、湿度为(50
±
5)%的环境中,养护7天后,测试性能如下:拉伸强度20mpa,断裂伸长率500%,材料修复率见表1。
48.对比例1
49.(参考实施例1,没有加入自修复胶囊)
50.(1)聚脲材料a组分的合成:
51.100份ptmeg1000搅拌加热至95℃,在真空-0.1mpa下,脱水5~7h,解除真空,降温
至50℃以下,再加入甲苯-2,4-二异氰酸酯,在90℃下反应3h,测定-nco值3.0%后出料。
52.(2)b组分的制备
53.按配方顺序称量各组分,将30份端氨基聚醚d2000,20份ptmeg1000,2 份硅烷偶联剂a171,35份扩链剂e100,0.1份催化剂异辛酸铋、5份3a分子筛,1份色浆,依次投入高速分散机储料罐中,室温搅拌15~30min,然后经砂磨机研磨至细度合格后用200目铜滤网过滤包装,制得b组分。
54.将体积比为1:1的a组分和b组分,通过喷涂机混合均匀并喷涂于钢板表面,涂层置于温度为(25
±
2)℃、湿度为(50
±
5)%的环境中,养护7天后,测试性能如下:拉伸强度20mpa,断裂伸长率430%。
55.对比例2:
56.(参考实施例1,更换微胶囊中的异氰酸酯为脂肪族异氰酸酯异佛尔酮二异氰酸酯ipdi)
57.(1)聚脲材料a组分的合成:
58.将10份desmophen nh 1220置于100份乙醇中,加入0.1份n-十二烷基二甲胺,在室温条件下7000转/分高速剪切搅拌得到固化剂乳化液,继续加入5份硝酸铬、5份硝酸钴,在室温条件下磁力搅拌2小时,之后500℃焙烧,得到钴/铬包裹固化剂微球。
59.取10份异佛尔酮二异氰酸酯置于100份正己烷中,加入0.1份n-十二烷基二甲胺,在室温条件下7000转/分高速剪切搅拌得到预聚物乳化液。将上述制备好的钴/铬包裹固化剂微球加入到此预聚物乳化液中,在室温条件下磁力搅拌2小时,反应完成通过离心收集得到沉淀,用水洗涤三次,然后在真空干燥箱中60℃干燥12h,获得自修复微胶囊。
60.100份ptmeg1000搅拌加热至95℃,在真空-0.1mpa下,加入上述10 份自修复微胶囊,脱水5~7h,解除真空,降温至50℃以下,再加入甲苯-2,4
‑ꢀ
二异氰酸酯,在90℃下反应3h,测定-nco值3.0%后出料。
61.(2)b组分的制备
62.按配方顺序称量各组分,将30份n,n
’‑
(亚甲基二-4,1-环己胺二基)双
ꢀ‑
1,1’,4,4
’‑
四乙基酯,20份ptmeg1000,2份硅烷偶联剂a171,35份扩链剂e100,0.1份催化剂异辛酸铋、5份3a分子筛,1份色浆,依次投入高速分散机储料罐中,室温搅拌15~30min,然后经砂磨机研磨至细度合格后用 200目铜滤网过滤包装,制得b组分。
63.将体积比为1:1的a组分和b组分,通过喷涂机混合均匀并喷涂于钢板表面,涂层置于温度为(25
±
2)℃、湿度为(50
±
5)%的环境中,养护7天后,测试性能如下:拉伸强度20mpa,断裂伸长率400%,材料修复率见表1,可见,改变微胶囊中异氰酸酯的种类,其修复率明显降低。
64.对比例3:
65.(参考实施例1,更换微胶囊异氰酸酯为二苯基甲烷-4,4'-二异氰酸酯 (mdi))
66.(1)聚脲材料a组分的合成:
67.将10份desmophen nh 1220置于100份乙醇中,加入0.1份n-十二烷基二甲胺,在室温条件下7000转/分高速剪切搅拌得到固化剂乳化液,继续加入5份硝酸铬、5份硝酸钴,在室温条件下磁力搅拌2小时,之后500℃焙烧,得到钴/铬包裹固化剂微球。
68.取10份二苯基甲烷-4,4'-二异氰酸酯置于100份正己烷中,加入0.1份n
‑ꢀ
十二烷
基二甲胺,在室温条件下7000转/分高速剪切搅拌得到预聚物乳化液。将上述制备好的钴/铬包裹固化剂微球加入到此预聚物乳化液中,在室温条件下磁力搅拌2小时,反应完成通过离心收集得到沉淀,用水洗涤三次,然后在真空干燥箱中60℃干燥12h,获得自修复微胶囊。
69.100份ptmeg1000搅拌加热至95℃,在真空-0.1mpa下,加入上述10 份自修复微胶囊,脱水5~7h,解除真空,降温至50℃以下,再加入甲苯-2,4
‑ꢀ
二异氰酸酯,在90℃下反应3h,测定-nco值3.0%后出料。
70.(2)b组分的制备
71.按配方顺序称量各组分,将30份n,n
’‑
(亚甲基二-4,1-环己胺二基)双
ꢀ‑
1,1’,4,4
’‑
四乙基酯,20份ptmeg1000,2份硅烷偶联剂a171,35份扩链剂e100,0.1份催化剂异辛酸铋、5份3a分子筛,1份色浆,依次投入高速分散机储料罐中,室温搅拌15~30min,然后经砂磨机研磨至细度合格后用 200目铜滤网过滤包装,制得b组分。
72.将体积比为1:1的a组分和b组分,通过喷涂机混合均匀并喷涂于钢板表面,涂层置于温度为(25
±
2)℃、湿度为(50
±
5)%的环境中,养护7天后,测试性能如下:拉伸强度21mpa,断裂伸长率420%,材料修复率见表1,可见,改变微胶囊中异氰酸酯的种类,其修复率明显降低。
73.对比例4
74.(参考实施例1,a组分nco值在8%)
75.(1)聚脲材料a组分的合成:
76.将10份desmophen nh 1220置于100份乙醇中,加入0.1份n-十二烷基二甲胺,在室温条件下7000转/分高速剪切搅拌得到固化剂乳化液,继续加入5份硝酸铬、5份硝酸钴,在室温条件下磁力搅拌2小时,之后500℃焙烧,得到钴/铬包裹固化剂微球。
77.取5份甲苯-2,4-二异氰酸酯与5份甲苯-2,6-二异氰酸酯置于100份正己烷中,加入0.1份n-十二烷基二甲胺,在室温条件下7000转/分高速剪切搅拌得到预聚物乳化液。将上述制备好的钴/铬包裹固化剂微球加入到此预聚物乳化液中,在室温条件下磁力搅拌2小时,反应完成通过离心收集得到沉淀,用水洗涤三次,然后在真空干燥箱中60℃干燥12h,获得自修复微胶囊。
78.100份ptmeg1000搅拌加热至95℃,在真空-0.1mpa下,加入上述10 份自修复微胶囊,脱水5~7h,解除真空,降温至50℃以下,再加入甲苯-2,4
‑ꢀ
二异氰酸酯,在90℃下反应3h,测定-nco值8.0%后出料。
79.(2)b组分的制备
80.按配方顺序称量各组分,将30份n,n
’‑
(亚甲基二-4,1-环己胺二基)双
ꢀ‑
1,1’,4,4
’‑
四乙基酯,20份ptmeg1000,2份硅烷偶联剂a171,35份扩链剂e100,0.1份催化剂异辛酸铋、5份3a分子筛,1份色浆,依次投入高速分散机储料罐中,室温搅拌15~30min,然后经砂磨机研磨至细度合格后用 200目铜滤网过滤包装,制得b组分。
81.将体积比为1:1的a组分和b组分,通过喷涂机混合均匀并喷涂于钢板表面,涂层置于温度为(25
±
2)℃、湿度为(50
±
5)%的环境中,养护7天后,测试性能如下:拉伸强度21mpa,断裂伸长率450%,材料修复率见表1,可见,组分a中nco值为8%,其修复率明显降低。
82.对比例5
83.(参考实施例1,更换微胶囊固化剂,更换为端氨基聚醚d2000)
84.(1)聚脲材料a组分的合成:
85.将10份端氨基聚醚d2000置于100份乙醇中,加入0.1份n-十二烷基二甲胺,在室温条件下7000转/分高速剪切搅拌得到固化剂乳化液,继续加入5 份硝酸铬、5份硝酸钴,在室温条件下磁力搅拌2小时,之后500℃焙烧,得到钴/铬包裹固化剂微球。
86.取5份甲苯-2,4-二异氰酸酯与5份甲苯-2,6-二异氰酸酯置于100份正己烷中,加入0.1份n-十二烷基二甲胺,在室温条件下7000转/分高速剪切搅拌得到预聚物乳化液。将上述制备好的钴/铬包裹固化剂微球加入到此预聚物乳化液中,在室温条件下磁力搅拌2小时,反应完成通过离心收集得到沉淀,用水洗涤三次,然后在真空干燥箱中60℃干燥12h,获得自修复微胶囊。
87.100份ptmeg1000搅拌加热至95℃,在真空-0.1mpa下,加入上述10 份自修复微胶囊,脱水5~7h,解除真空,降温至50℃以下,再加入甲苯-2,4
‑ꢀ
二异氰酸酯,在90℃下反应3h,测定-nco值3.0%后出料。
88.(2)b组分的制备
89.按配方顺序称量各组分,将30份n,n'-(亚甲基二-4,1-环己胺二基)双
ꢀ‑
1,1',4,4'-四乙基酯,20份ptmeg1000,2份硅烷偶联剂a171,35份扩链剂e100, 0.1份催化剂异辛酸铋、5份3a分子筛,1份色浆,依次投入高速分散机储料罐中,室温搅拌15~30min,然后经砂磨机研磨至细度合格后用200目铜滤网过滤包装,制得b组分。
90.将体积比为1:1的a组分和b组分,通过喷涂机混合均匀并喷涂于钢板表面,涂层置于温度为(25
±
2)℃、湿度为(50
±
5)%的环境中,养护7天后,测试性能如下:拉伸强度21mpa,断裂伸长率450%,材料修复率见表1。从表1可以看出,选择固化剂为端氨基聚醚d2000,修复效果差。
91.采用电化学阻抗谱法(eis)对涂料的修复率进行检测,结果见表1;电化学阻抗谱法(eis)被广泛应用于涂层耐腐蚀性能和自愈性能研究中。eis可以在不同频率下对涂层电容、微孔电阻以及双电容层等信息进行实时、多次测量,且不会对涂层体系产生影响,故许多研究学者利用eis对涂层破坏的动力学过程进行研究。eis参数中的电荷转移电阻可以较为直接的反应涂层的自愈合过程,得出涂层的自修复效率。
92.表1
[0093][0094][0095]
以上实施例的说明只是用于帮助理解本发明的方法及其核心思想。应当指出,对于本技术领域的普通技术人员来说,在不脱离本发明原理的前提下,还可以对本发明进行若干改进和修饰,这些改进和修饰也落入本发明权利要求的保护范围内。