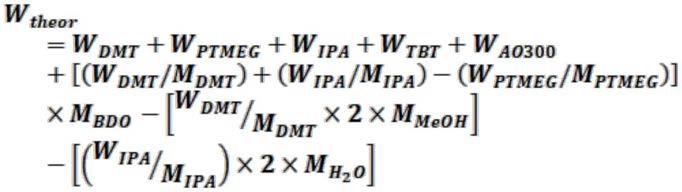
1.本发明关于高分子复合膜及包含其的热熔胶叠层,尤指一种聚酯复合膜及包含其的热熔胶叠层。
背景技术:2.因应时代变迁,消费者对于纺织品的机能性要求也逐渐提高,具有防水功能的机能布料成为纺织工业的重点发展课题之一。
3.防水机能布料的防水效果由耐水压值(又称防水系数)来评估。耐水压值是指布料表面可承受而不发生渗水的水压值,单位为毫米水柱高(mm h2o),耐水压值越高代表布料的防水效果越好。一般而言,耐水压值达1000mm h2o以上代表防水效果普通,耐水压值达3000mm h2o以上代表具有不错的防水效果,耐水压值达5000mm h2o以上则代表有良好的防水效果,此款防水机能布料可适用于小雨至中暴雨的天气。
4.现今,防水机能布料可由防水膜热压贴合于布料上所形成,或可将热熔胶膜热压贴合于二块布料的缝份上,以提升布料的防水效果。目前市面上所采用的防水膜或热熔胶膜多半由聚氨酯(polyurethane,pu)或热塑性聚氨酯(thermoplastic polyurethane,tpu)所制得,然而,此种材料的膜层与布料在经热压贴合时有受热裂解的问题,致使防水膜或热熔胶膜存有容易从布料上剥离的风险,也会劣化布料的防水效果。
5.因此,目前仍有待开发不同材料的防水膜或热熔胶膜,以解决现有技术存在的缺陷。
技术实现要素:6.有鉴于此,本发明其中一目的在于提供一种有别于以往的聚酯复合膜,此聚酯复合膜能良好地贴合于织物上,并且使贴合的织物获得良好的防水性。
7.为达成前述目的,本发明提供一种聚酯复合膜,其包括第一热塑性聚醚酯弹性体(thermoplastic polyether ester elastomer,tpee)膜及第二热塑性聚醚酯弹性体膜;其中,所述第一热塑性聚醚酯弹性体膜的材料包含第一热塑性聚醚酯弹性体树脂,所述第二热塑性聚醚酯弹性体膜的材料包含第二热塑性聚醚酯弹性体树脂,所述第二热塑性聚醚酯弹性体树脂的熔点大于所述第一热塑性聚醚酯弹性体树脂的熔点,且所述第一热塑性聚醚酯弹性体膜的熔化热焓(enthalpy of fusion,δhm)与所述第二热塑性聚醚酯弹性体膜的熔化热焓二者的绝对差值为5焦耳/克(j/g)至15j/g。
8.通过合并采用第一、第二热塑性聚醚酯弹性体膜,并且调控第二热塑性聚醚酯弹性体树脂的熔点大于第一热塑性聚醚酯弹性体树脂的熔点以及第一热塑性聚醚酯弹性体膜的熔化热焓与第二热塑性聚醚酯弹性体膜的熔化热焓二者的绝对差值为5j/g至15j/g,本发明的聚酯复合膜不仅能通过第一热塑性聚醚酯弹性体膜与织物贴合而获得良好的剥离强度(peel strength),且其第二热塑性聚醚酯弹性体膜经热压后仍可维持其膜层质量,不会受到热压高温影响而熔融,故能使贴合的织物获得良好的防水性。简言之,本发明的聚
酯复合膜应用于贴合织物上能同时兼具良好的剥离强度和防水性,适用于开发成防水机能衣物。
9.依据本发明,所述第一热塑性聚醚酯弹性体膜的熔化热焓与所述第二热塑性聚醚酯弹性体膜的熔化热焓二者的绝对差值可为5j/g、6j/g、7j/g、8j/g、9j/g、10j/g、11j/g、12j/g、13j/g、14j/g、15j/g;此外,其二者的绝对差值也可介于上述任二数值所构成的范围。于其中一实施态样,所述第一热塑性聚醚酯弹性体膜的熔化热焓与所述第二热塑性聚醚酯弹性体膜的熔化热焓二者的绝对差值可为6j/g至15j/g。
10.所述第一热塑性聚醚酯弹性体膜的熔化热焓可为1j/g、2j/g、3j/g、4j/g、5j/g、6j/g、7j/g、8j/g、9j/g、10j/g;此外,其熔化热焓也可介于上述任二数值所构成的范围。于其中一实施态样,所述第一热塑性聚醚酯弹性体膜的熔化热焓可为1j/g至10j/g;于另一实施态样,所述第一热塑性聚醚酯弹性体膜的熔化热焓可为3j/g至10j/g。
11.所述第二热塑性聚醚酯弹性体膜的熔化热焓可为5j/g、6j/g、7j/g、8j/g、9j/g、10j/g、11j/g、12j/g、13j/g、14j/g、15j/g、16j/g、17j/g、18j/g、19j/g、20j/g、21j/g、22j/g、23j/g、24j/g、25j/g;此外,其熔化热焓也可介于上述任二数值所构成的范围。于其中一实施态样,所述第二热塑性聚醚酯弹性体膜的熔化热焓可为5j/g至25j/g;于另一实施态样,所述第二热塑性聚醚酯弹性体膜的熔化热焓可为6j/g至25j/g。
12.依据本发明,所述第一热塑性聚醚酯弹性体膜中的第一热塑性聚醚酯弹性体树脂、所述第二热塑性聚醚酯弹性体膜中的第二热塑性聚醚酯弹性体树脂可由对苯二甲酸二甲酯(dimethyl terephthalate,dmt)、1,4-丁二醇(1,4-butanediol,bdo)、间苯二甲酸(m-phthalic acid,ipa)和聚四亚甲基醚二醇(poly(tetramethylene ether)glycol,ptmeg)共聚缩合而成,但并非仅限于此。举例而言,工艺中另可选择性添加1,3,5-三甲基-2,4,6-三(3,5-二叔丁基-4-羟苄)苯(1,3,5-trimethyl-2,4,6-tris(3,5-di-tert-butyl-4-hydroxybenzyl)benzene,ao330)抗氧化剂或者钛酸四丁酯(titanium butoxide,tbt)催化剂参与反应。
13.所述第一热塑性聚醚酯弹性体树脂的熔点可为90℃、95℃、100℃、105℃、110℃、115℃、120℃、125℃、130℃、135℃、140℃、145℃、150℃、155℃、160℃、164℃;此外,其熔点也可介于上述任二数值所构成的范围。于其中一实施态样,所述第一热塑性聚醚酯弹性体树脂的熔点可为90℃至164℃;于另一实施态样,所述第一热塑性聚醚酯弹性体树脂的熔点可为100℃至160℃。
14.所述第二热塑性聚醚酯弹性体树脂的熔点大于所述第一热塑性聚醚酯弹性体树脂的熔点,所述第二热塑性聚醚酯弹性体树脂的熔点可为165℃、170℃、175℃、180℃、185℃、190℃、195℃、200℃、205℃、210℃、215℃、220℃;此外,其熔点也可介于上述任二数值所构成的范围。于其中一实施态样,所述第二热塑性聚醚酯弹性体树脂的熔点可为165℃至220℃;于另一实施态样,所述第二热塑性聚醚酯弹性体树脂的熔点可为165℃至210℃。
15.所述第一或第二热塑性聚醚酯弹性体树脂的比重可为1.00、1.01、1.02、1.03、1.04、1.05、1.06、1.07、1.08、1.09、1.10、1.11、1.12、1.13、1.14、1.15;此外,其二者的比重也可各自独立地介于上述任二数值所构成的范围。于其中一实施态样,所述第一或第二热塑性聚醚酯弹性体树脂的比重可各自独立为1.00至1.15。
16.所述第一或第二热塑性聚醚酯弹性体树脂的邵氏硬度(shore hardness)可为15、
16、17、18、19、20、21、22、23、24、25、26、27、28、29、30、31、32、33、34、35、36、37、38、39、40、41、42、43、44、45;此外,其二者的邵氏硬度也可各自独立地介于上述任二数值所构成的范围。于其中一实施态样,所述第一或第二热塑性聚醚酯弹性体树脂的邵氏硬度可各自独立为15至45。于另一实施态样,所述第一热塑性聚醚酯弹性体树脂的邵氏硬度可为15至30。于又一实施态样,所述第二热塑性聚醚酯弹性体树脂的邵氏硬度可为25至45。于再一实施态样,所述第二热塑性聚醚酯弹性体树脂的邵氏硬度可大于所述第一热塑性聚醚酯弹性体树脂的邵氏硬度。
17.此外,本发明另一目的在于提供一种热熔胶叠层,其能良好地与织物一齐进行热压贴合获得足够的剥离强度,并且使贴合的织物获得良好的防水性。
18.为达成前述目的,本发明还提供一种热熔胶叠层,其包括如前所述的聚酯复合膜及离型膜,所述聚酯复合膜的第二热塑性聚醚酯弹性体膜夹置于所述聚酯复合膜的第一热塑性聚醚酯弹性体膜和所述离型膜之间。
19.在使用本发明的热熔胶叠层贴合织物时,可将热熔胶叠层的第一热塑性聚醚酯弹性体膜设置于织物上,由于所述第一热塑性聚醚酯弹性体膜中的第一热塑性聚醚酯弹性体树脂的熔点低于所述第二热塑性聚醚酯弹性体膜中的第二热塑性聚醚酯弹性体树脂的熔点,故进行热压工艺时仅需以介于第一、第二热塑性聚醚酯弹性体树脂的熔点的温度便能将第一热塑性聚醚酯弹性体膜熔融并且良好地贴合于织物上,且此热压温度不会破坏第二热塑性聚醚酯弹性体膜的膜层质量,故能同时确保贴合的织物的防水效果。
20.依据本发明,所述离型膜例如:聚乙烯(polyethylene,pe)离型膜、聚对苯二甲酸乙二酯(polyethylene terephthalate,pet)离型膜、定向拉伸聚丙烯薄膜(oriented polypropylene,opp)离型膜,但并非仅限于此。
21.本发明可适用的织物并无特别限制,例如一般针织布、梭织布或无纺布均可适用。此外,所述热熔胶叠层可大面积地热压贴合于织物上,形成一整块防水织物;或者,所述热熔胶叠层也可局部热压贴合于织物的缝份上,由此提升经车缝的织物的防水性,避免从缝份处发生渗水的问题。
附图说明
22.图1为制备聚酯复合膜和热熔胶叠层的流程示意图。
23.图2为聚酯复合膜的侧视示意图。
24.图3为热熔胶叠层的侧视示意图。
25.图4为试验例5中经热压的叠层的侧视示意图。
26.图5为试验例6中经热压的叠层的侧视示意图。
27.符号说明:
28.20:聚酯复合膜
29.21:第一热塑性聚醚酯弹性体膜
30.22:第二热塑性聚醚酯弹性体膜
31.30:热熔胶叠层
32.31:离型膜
33.41:梭织布
34.42:防水膜
35.51:第一梭织布
36.52:第二梭织布
37.53:防水膜
具体实施方式
38.以下,列举数种制备例和实施例说明聚酯复合膜及包含其的热熔胶叠层的实施方式,同时提供数种比较例作为对照,所属技术领域技术人员可通过下方实施例和比较例的内容轻易理解本发明能达到的优点及效果。应当理解的是,本说明书所列举的实施例仅用于示范性说明本发明的实施方式,并非用于局限本发明的范围,所属技术领域技术人员可以根据通常知识在不悖离本发明的精神下进行各种修饰、变更,以实施或应用本发明的内容。
39.《热塑性聚醚酯弹性体树脂》
40.制备例1:tpee树脂粒
41.首先,根据下表1所示的重量,分别秤取10公斤的对苯二甲酸二甲酯(dmt)、10公斤的1,4-丁二醇(bdo)、3.43公斤的间苯二甲酸(ipa)、22公斤的聚四亚甲基醚二醇(ptmeg,其数均分子量为1000,于下表1中以“ptmeg1000”表示)、70克的1,3,5-三甲基-2,4,6-三(3,5-二叔丁基-4-羟苄)苯(ao330),将其等添加于3公升的反应釜中,并且加入70克的钛酸四丁酯(tbt)。此后,将反应釜加热片的温度设定在210℃至230℃,以进行酯化反应。
42.酯化反应过程中会产生副产物甲醇(meoh,沸点64.7℃)、水(h2o,沸点100℃),在220℃至225℃的反应釜中甲醇和水会沸腾,并在与反应釜相连的冷凝管中重新凝结,收集于冷凝收集槽中。当冷凝管顶部的温度降至40℃以下视为酯化反应结束,立即进入聚缩合阶段。
43.于聚缩合阶段,将反应釜温度升至240℃至250℃,并且开启真空泵使反应釜的内压力达1毫巴(mbar)以下,之后维持反应釜温度与压力约200分钟,待反应釜内共聚物的熔融指数达15克/10分钟(g/10min)至20g/10min,视为反应完成,即可旋开釜底阀进行后续拉条、切粒工艺。于此,所述熔融指数是指共聚物于190℃、负荷2.16公斤的测试条件下,在10分钟内通过直径约2.095毫米的标准口模的重量。
44.最后,在釜底阀出口处准备水中切粒设备,其切刀转速设定为2000转速/分钟(rpm)、模头温度设定为230℃、切粒水温设定为10℃,并以齿轮泵出料量设定为50公斤/小时(kg/hr)进行切粒,切粒后粒子形成直径约3毫米(mm)的圆粒,经冷却水道内冷却并结晶,之后再经由脱水机去除水分后得到产物(即,tpee树脂粒)。
45.制备例2至12:tpee树脂粒
46.制备例2至12的tpee树脂粒的工艺大致上与制备例1雷同,其差异仅在于如下表1所示的dmt、bdo、ipa、ao300、tbt等原料的重量、ptmeg的数均分子量及重量。
47.于此,各制备例所选用的聚四亚甲基醚二醇的数均分子量略有差异。如前所述,数均分子量为1000的聚四亚甲基醚二醇于下表1中以“ptmeg1000”表示,而数均分子量为2000的聚四亚甲基醚二醇则以“ptmeg2000”表示。
48.上述制备例1至12的tpee树脂粒的理论产物重(w
theor
)可经由下方算式求得:
[0049][0050]
于上式中,
[0051]wtheor
:理论产物重
[0052]wdmt
:dmt重量;
[0053]wptmeg
:ptmeg重量;
[0054]wipa
:ipa重量;
[0055]wtbt
:tbt重量;
[0056]wao300
:ao300重量;
[0057]mdmt
:dmt分子量:194g/mol;
[0058]mipa
:ipa分子量:166g/mol;
[0059]mptmeg
:ptmeg分子量;
[0060]mbdo
:bdo分子量:90g/mol;
[0061]mmeoh
:meoh分子量:32g/mol;
[0062]mh2o
:h2o分子量:18g/mol。
[0063]
此外,ptmeg和ipa的重量比例则可经由下方算式求得:
[0064]
ptmeg用量比例(%)=(w
ptmeg
/w
theor
)
×
100%
[0065]
ipa用量比例(%)=(w
ipa
/w
theor
)
×
100%
[0066]
根据上述算式所求得的制备例1至12的tpee树脂粒的理论产物重、ptmeg的重量比例以及ipa的重量比例如下表1所示。
[0067]
除了前述制备例所例示的实施方式外,所属技术领域技术人员可在不悖离本发明的精神下调整、修饰、变更上述工艺,获得可适用于本发明的tpee树脂粒。例如,可视需求调整各种原料的重量,或于工艺中可视需求调整催化剂的添加时机;举例而言,可于聚缩合阶段另行添加催化剂以加速反应的进行,即,催化剂的添加时机并不限于仅能在最初的酯化反应阶段中添加。
[0068]
试验例1:熔点
[0069]
本试验例以前述制备例1至12的tpee树脂粒为待测样品,取10毫克的待测样品置于铝盘内,并连同空白铝盘置入示差扫描卡计(dsc)(厂商:ta instrument,型号:q-2000)中,以每分钟10℃的升温速率从室温加热至出现熔融峰,并纪录各制备例的tpee树脂粒的熔点,其结果如表2所示。
[0070]
试验例2:比重
[0071]
本试验例以前述制备例1至12的tpee树脂粒为待测样品,依照iso1183的标准方法测量其比重。
[0072]
具体而言,使用天平在空气中秤量各待测样品的重量(a,单位:克),取至小数点第四位;将小钢丝在天平上挂勾垂浸入装满水的烧杯中,并将小钢丝在水中的重量归零;接着,以小钢丝勾住待测样品,由天平上挂勾垂浸入装满水的烧杯中,并使待测样品完全浸入
水中,并小心去除附着在待测样品的气泡;秤取浸在水中的样品重(b,单位:克),取至小数点第四位;最后,根据a/(a-b)求得各待测样品的比重。如下表2所示,制备例1至12的tpee树脂粒的比重为1.00至1.15。
[0073][0074]
表2:制备例1至12的tpee树脂粒的熔点、比重及邵氏硬度
[0075] 熔点(℃)比重邵氏硬度
pe11101.102320pe21401.092128pe31521.044323pe41671.068626pe51851.082530pe61901.107833pe72071.133540pe8941.080418pe91011.113319pe101181.093919pe111261.101621pe121601.058120
[0076]
试验例3:邵氏硬度
[0077]
本试验例以前述制备例1至12的tpee树脂粒为分析对象,依照iso868的标准方法,使用硬度测试仪(厂牌:德国bareiss,型号:digi test ii)测量得到邵氏硬度。
[0078]
具体而言,将各制备例的tpee树脂粒经射出成型制得厚度至少4毫米以上的试片;开启硬度测试仪,并确认砝码及探针已装设定位;进入func页面选择std.pv模式;再将试片放置于平台上,目标量测点需距离试片边界至少9毫米以上;按下开启键进行量测,等待3秒后仪器上显示的数值即为tpee树脂粒的邵氏硬度。如上表2所示,制备例1至12的tpee树脂粒的邵氏硬度为15至45。
[0079]
《聚酯复合膜和热熔胶叠层》
[0080]
请参阅图1所示,本发明混合采用二种不同特性的tpee树脂(第一、第二tpee树脂)分别形成二种不同特性的tpee膜(第一、第二tpee树脂膜),通过控制二种tpee树脂之间的熔点和控制二层tpee膜之间的熔化热焓的绝对差值,获得期望的聚酯复合膜和热熔胶叠层。所述聚酯复合膜和热熔胶叠层的实施方式说明如后。
[0081]
实施例1
[0082]
实施例1采用前述制备例1的tpee树脂粒作为第一tpee树脂,另采用前述制备例6的tpee树脂粒作为第二tpee树脂,并经由下述方法制成第一tpee膜和第二tpee膜,即可获得聚酯复合膜和热熔胶叠层。
[0083]
如图1所示,取20公斤至25公斤的第二tpee树脂(高熔点tpee树脂粒)置入结晶干燥槽,将温度设定在100℃至120℃下结晶干燥至少4小时至8小时,以干燥空气将高熔点tpee树脂粒输送至计量挤压机中;将挤压机速度设定为10rpm至50rpm,挤压螺杆各区温度设定为150℃至230℃,使高熔点tpee树脂粒经挤压机的加热温度与螺杆搅动剪力摩擦热,熔化成为高熔点tpee熔融浆体,后经挤压模头各区温度设定在190℃至230℃的持温下,挤出流延成型。
[0084]
此时,淋模机一侧置入连续式pet离型膜,其离型力为250g至1500g,当高熔点tpee熔融浆体经挤压模头流延出后,离型膜穿过压力辊与冷却辊之间,所述压合区位于模具下方承接高熔点tpee熔融浆体压合成型一高熔点tpee膜,此高熔点tpee膜再经一至数组熟成辊轮组延伸,熟成辊轮温度为5℃至30℃、速度为1rpm至10rpm,最后经收卷辊轮以1rpm至
10rpm的速度将离型膜和其上的高熔点tpee膜(即,第二tpee膜)收卷成型。
[0085]
取20公斤至25公斤的第一tpee树脂(低熔点tpee树脂粒)置入结晶干燥槽,将温度设定在60℃至120℃下结晶干燥至少4小时至8小时,以干燥空气将低熔点tpee树脂粒输送至计量挤压机中;将挤压机速度设定为10rpm至50rpm,挤压螺杆各区温度设定为100℃至210℃,使低熔点tpee树脂粒经挤压机的加热温度与螺杆搅动剪力摩擦热熔化成为低熔点tpee熔融浆体,后经挤压模头各区温度设定在140℃至210℃的持温下,挤出流延成型。
[0086]
此时,淋模机一侧置入前述连续式离型膜和高熔点tpee膜,当低熔点tpee熔融浆体经挤压模头流延出后,前述离型膜和高熔点tpee膜穿过压力辊与冷却辊之间,所述压合区位于模具下方承接低熔点tpee熔融浆体压合成型一低熔点tpee膜(即,第一tpee膜),此低熔点tpee膜再经一至数组熟成辊轮组延伸,熟成辊轮温度为5℃至30℃、速度为1rpm至10rpm,最后经收卷辊轮以1rpm至10rpm的速度将离型膜和高熔点tpee膜、低熔点tpee膜一齐收卷成型,得到形成于离型膜上的聚酯复合膜。所述离型膜和聚酯复合膜即构成热熔胶叠层。
[0087]
如图2所示,聚酯复合膜20包括第一热塑性聚醚酯弹性体膜21及设置在所述第一热塑性聚醚酯弹性体膜21上的第二热塑性聚醚酯弹性体膜22;所述第一热塑性聚醚酯弹性体膜21的材料包含第一热塑性聚醚酯弹性体树脂,所述第二热塑性聚醚酯弹性体膜22的材料包含第二热塑性聚醚酯弹性体树脂。
[0088]
如图3所示,热熔胶叠层30包括前述聚酯复合膜20及离型膜31,所述聚酯复合膜20设置在离型膜31上,具体而言,聚酯复合膜20的第二热塑性聚醚酯弹性体膜22夹置于所述聚酯复合膜20的第一热塑性聚醚酯弹性体膜21和所述离型膜31之间。
[0089]
实施例2至7、比较例1至3
[0090]
实施例2至7、比较例1至3大致上采用如同前述实施例1的方法制备聚酯复合膜和热熔胶叠层,其差异在于各实施例和比较例所采用的第一tpee树脂和第二tpee树脂的来源和熔点有所差异,其数据如表2至表4所示。
[0091]
如前所述,实施例2至7和比较例1至3的聚酯复合膜的结构也如图2所示,实施例2至7和比较例1至3的热熔胶叠层的结构也如图3所示。根据所采用的第一、第二tpee树脂的来源有所差异,实施例2至7和比较例1至3与实施例1的差异将于后方进一步说明。
[0092]
试验例4:熔化热焓
[0093]
本试验例以前述实施例1至7和比较例1至3的聚酯复合膜为分析对象,依照下述方法将各个分析对象拆分为两待测样品,再分别测定其等的熔化热焓。
[0094]
首先,取长度10公分、宽度4公分的聚酯复合膜,于25毫升的样品瓶中填装15毫升的丙酮,再将前述特定尺寸的聚酯复合膜浸泡于样品瓶中长达1天,取出浸泡后的聚酯复合膜,利用剪刀或美工刀等器具将聚酯复合膜中的第一tpee膜和第二tpee膜分离,即获得两待测样品(第一tpee膜和第二tpee膜)。
[0095]
接着,取10毫克的待测样品置于铝盘内,并连同空白铝盘置入示差扫描卡计(dsc)(厂商:ta instrument,型号:q-2000)中,以每分钟10℃的升温速率从室温加热至出现熔融峰,再以每分钟10℃的降温速率将其冷却至室温,将熔融峰与熔融起始、结束的两点连线所围面积计算得到各待测样品的熔化热焓,其结果如下表3所示。针对各聚酯复合膜进行分析,其第一tpee膜的熔化热焓于下表3中以
“△h1st”表示,第二tpee膜的熔化热焓于下表3中
以
“△h2nd”表示;各聚酯复合膜中第一tpee膜的熔化热焓与所述第二tpee膜的熔化热焓二者的绝对差值于下表3和表4中以“∣
△h2nd
-
△h1st
∣”表示。
[0096]
如表3及表4所示,实施例1至7的聚酯复合膜中第二tpee树脂的熔点均大于所述第一tpee树脂的熔点,且其∣
△h2nd
-
△h1st
∣为5j/g至15j/g。反观比较例1至3的聚酯复合膜,其第二tpee树脂的熔点虽大于所述第一tpee树脂的熔点,但∣
△h2nd
-
△h1st
∣均超出5j/g至15j/g的范围。具体来说,比较例1及3的聚酯复合膜中第一、第二tpee膜二者的熔化热焓十分接近,其∣
△h2nd
-
△h1st
∣均低于5j/g;而比较例2的聚酯复合膜中第一、第二tpee膜二者的熔化热焓则差异过大,∣
△h2nd
-
△h1st
∣超过15j/g。
[0097][0098]
《聚酯复合膜和热熔胶叠层的应用》
[0099]
本发明的聚酯复合膜和热熔胶叠层贴合于织物上能具有足够的剥离强度,故能良
好地与织物贴合,并且使织物具备良好的防水性。为验证本发明的聚酯复合膜或热熔胶叠层应用于织物上的效果,以下通过试验例5和试验例6评估其剥离强度和防水性,其试验结果合并说明如后。
[0100]
试验例5:剥离强度
[0101]
本试验例采用前述实施例1至7和比较例1至3的热熔胶叠层,将热熔胶叠层的离型膜剥除后设置在梭织布上,再经如下所述的热压、水洗、静置等处理步骤后获得待测样品;后依照iso2411的标准方法,使用拉伸试验机(厂商:instron,型号:3345)测得聚酯复合膜与梭织布之间的剥离强度。各待测样品的详细准备方法说明如后。
[0102]
首先,准备9块试验梭织布,各梭织布的长度至少200毫米、宽度至少75毫米,其表面覆盖有tpu防水膜;另取长度至少200毫米的聚酯复合膜(宽度不限),将其置放于梭织布上,所述聚酯复合膜的第一tpee膜朝向梭织布上的防水膜;再将热压机的单面热压温度设定在175℃、热压压力设定在3.0公斤/平方厘米(kg/cm2),以热压机持续热压聚酯复合膜和梭织布一段时间,获得经热压的叠层。于此,前述9块试验梭织布中有3块各自与聚酯复合膜热压20秒,另有3块试验梭织布各自与聚酯复合膜热压30秒,又有3块试验梭织布各自与聚酯复合膜热压40秒。所述聚酯复合膜留有100毫米的长度与梭织布热压贴合,未贴合的末端留供拉伸试验机的夹具夹持。接着,将经热压的叠层静置24小时,使聚酯复合膜熟成。
[0103]
如图4所示,经热压的叠层包含梭织布41、防水膜42和前述聚酯复合膜20,所述防水膜42形成在梭织布41上,而聚酯复合膜20通过第一热塑性聚醚酯弹性体膜21贴合在防水膜42上,即,第一热塑性聚醚酯弹性体膜21夹置于防水膜42和第二热塑性聚醚酯弹性体膜22之间。
[0104]
之后,将每块经热压的叠层分别置入水洗试验机,加入标准陪洗布使其总重量达到1.8公斤
±
0.1公斤,再添加66.0克
±
1克的1993aatcc标准洗涤剂溶解在18.0加仑
±
0.5加仑的水中,以60℃
±
3℃的水温、179rpm
±
2rpm的搅拌速度水洗12分钟,再以645rpm
±
15rpm的脱水速度甩干6分钟,依此方式反复进行水洗、脱干50次后,静置24小时,即获得待测样品。
[0105]
最后,以拉伸试验机的上夹具夹持待测样品的梭织布端,下夹具夹持待测样品的聚酯复合膜端(上、下夹具的夹持物可以互换),上、下夹具的尺寸为6英寸
×
2英寸,上、下夹具的夹距设定在50毫米;再将拉伸试验机中剥离夹具的拉伸行径速度设定在100毫米/分钟(mm/min)
±
10mm/min,并选择适当的应力荷重范围,定速拉伸至聚酯复合膜与梭织布剥离,剥离时检出的最大应力值即为聚酯复合膜与梭织布之间的剥离强度,单位:公斤重/厘米(kgf/cm)。将前述经热压20秒的3个待测样品所测得的剥离强度取平均值,其结果列于表4所示。同理,将前述经热压30秒的3个待测样品和前述经热压40秒的3个待测样品的剥离强度分别取平均值,其结果也列于表4所示。
[0106]
如表4所示,聚酯复合膜不论是历经20秒、30秒或40秒的热压时间,实施例1至7的聚酯复合膜与织物之间的剥离强度均显著大于比较例1至3的聚酯复合膜与织物之间的剥离强度,显示实施例1至7的聚酯复合膜能良好地与织物贴合,避免非预期的剥离情形发生。
[0107]
在历经20秒的热压时间,实施例1至7的聚酯复合膜与织物之间的剥离强度超过0.65kgf/cm;具体而言,实施例1至7的聚酯复合膜与织物之间的剥离强度为0.68kgf/cm至1.50kgf/cm。在历经30秒的热压时间,实施例1至7的聚酯复合膜与织物之间的剥离强度超
过0.68kgf/cm;具体而言,实施例1至7的聚酯复合膜与织物之间的剥离强度为0.70kgf/cm至1.75kgf/cm。在历经40秒的热压时间,实施例1至7的聚酯复合膜与织物之间的剥离强度超过0.72kgf/cm;具体而言,实施例1至7的聚酯复合膜与织物之间的剥离强度为0.85kgf/cm至2.00kgf/cm。
[0108]
试验例6:防水性
[0109]
本试验例采用前述实施例1至7和比较例1至3的热熔胶叠层,将热熔胶叠层的离型膜剥除后设置在经车缝的二块梭织布上,再经如下所述的热压、水洗、静置等处理步骤后获得待测样品;后依照iso811的标准方法,使用耐水压机(厂商:hezo,型号:322ad)测得经聚酯复合膜贴合的梭织布的耐水压性。各待测样品的详细准备方法说明如后。
[0110]
首先,取两块长度200毫米至225毫米、宽度200毫米至225毫米的试验梭织布,将二者以平缝方式对接车缝,车缝线折边压线,使车缝对接处能平贴,勿使缝份侧视时呈现三角凸面状况。此外,上方的梭织布表面覆盖有tpu防水膜。
[0111]
之后,剥除热熔胶叠层的离型膜,再将聚酯复合膜置放于两块梭织布的缝份上,所述聚酯复合膜的第一tpee膜朝向梭织布上的防水膜;将热压机的单面热压温度设定在175℃、热压压力设定在3.0kg/cm2,以热压机持续热压聚酯复合膜和二梭织布长达20秒、30秒或40秒,获得经热压的叠层。
[0112]
如图5所示,本试验例中经热压的叠层包含第一梭织布51、第二梭织布52、防水膜53和聚酯复合膜,所述第一梭织布51和第二梭织布52经车缝成型为一体;防水膜53形成在第一梭织布51和第二梭织布52上;而聚酯复合膜设置于缝份上(如图中虚线所示),即,聚酯复合膜通过第一热塑性聚醚酯弹性体膜21贴合在防水膜53上,聚酯复合膜的第一热塑性聚醚酯弹性体膜21夹置于防水膜53和第二热塑性聚醚酯弹性体膜22之间。
[0113]
之后,将经热压的叠层置入水洗试验机,加入标准陪洗布使其总重量达到1.8公斤
±
0.1公斤,再添加66.0克
±
1克的1993aatcc标准洗涤剂溶解在18.0加仑
±
0.5加仑的水中,以60℃
±
3℃的水温、179rpm
±
2rpm的搅拌速度水洗12分钟,再以645rpm
±
15rpm的脱水速度甩干6分钟,依此方式反复进行水洗、脱干50次后,静置24小时,即获得待测样品。
[0114]
最后,耐水压机的水柱水压以100
±
0.5毫米水柱高/分钟(mm h2o/min)增加,观察待测样品上贴合有聚酯复合膜的区域承受静水压头(hydrostatic head)的渗水情形,直到布面发生3处穿透水珠,停止增压并记录当下水压数值,即为聚酯复合膜的耐水压值,其结果如表4所示。或者,将耐水压机的水柱水压设定为固定值,例如设定静水压压力为5,000mmh2o持压120秒,观察待测样品上贴合有聚酯复合膜的区域承受静水压头的渗水情形,若少于3处水珠漏水,则记录此设定值为聚酯复合膜的耐水压值。
[0115]
如表4所示,实施例1至7的聚酯复合膜不论是经由20秒、30秒或40秒的热压时间贴合于织物上均可达到5,000mmh2o以上的耐水压效果,显示实施例1至7的聚酯复合膜均可使织物具备良好的防水性,能适用于抵挡于小雨至中暴雨的雨水;而比较例3的聚酯复合膜由于无法与织物之间获得足够的剥离强度,致使比较例3的聚酯复合膜在进行耐水压测试时无法支撑水重,故未能测得比较例3的耐水压结果。
[0116][0117]
实验结果讨论
[0118]
如表4所示,实施例1至7的聚酯复合膜因采用第一、第二tpee膜,且其聚酯复合膜
具备第二tpee树脂的熔点大于第一tpee树脂的熔点、以及所述第一tpee膜的熔化热焓与所述第二tpee膜的熔化热焓二者的绝对差值为5j/g至15j/g的技术特征,故采用实施例1至7的聚酯复合膜热压贴合于织物上不仅能通过第一tpee膜与织物贴合而获得良好的剥离强度,且其上方的第二tpee膜经热压后仍可维持其膜层质量,不会受到热压高温影响而熔融,故能确保贴合的织物获得高达5,000mmh2o以上的耐水压值,使贴覆有实施例1至7的聚酯复合膜的织物获得良好的防水性。
[0119]
反观比较例1至3,比较例1及2的聚酯复合膜热压贴合于织物上的剥离强度均较实施例1至7更低,易存在聚酯复合膜自织物上剥离的风险;尤其,比较例3的聚酯复合膜热压贴合于织物上的剥离强度甚至不足以承受耐水压测试所施予的水重,致使比较例3的聚酯复合膜无法良好地贴合于织物上提供所需的防水性。
[0120]
此外,由于第二tpee树脂的熔点大于第一tpee树脂的熔点,故实施例1至7的聚酯复合膜通过第一tpee膜热压贴合于织物上时,仅需耗费较低的热压温度(即,介于第一tpee树脂的熔点和第二tpee树脂的熔点之间的温度)便能将聚酯复合膜的第一tpee膜熔融并且良好地贴合于织物上,且第二tpee膜不会受到热压高温影响而熔融,故能使织物获得良好的防水性。
[0121]
综上所述,通过合并采用第一tpee膜和第二tpee膜,并且调控聚酯复合膜中第二tpee树脂的熔点大于第一tpee树脂的熔点以及第一tpee膜的熔化热焓与所述第二tpee膜的熔化热焓二者的绝对差值为5j/g至15j/g等技术手段,本发明的聚酯复合膜能良好地热压贴合于织物上获得足够的剥离强度,并且使贴合的织物获得良好的防水性。同理,包含前述聚酯复合膜的热熔胶叠层也能适用于织物贴合的用途,使其与织物之间获得足够的剥离强度,并且使贴合的织物获得良好的防水性。