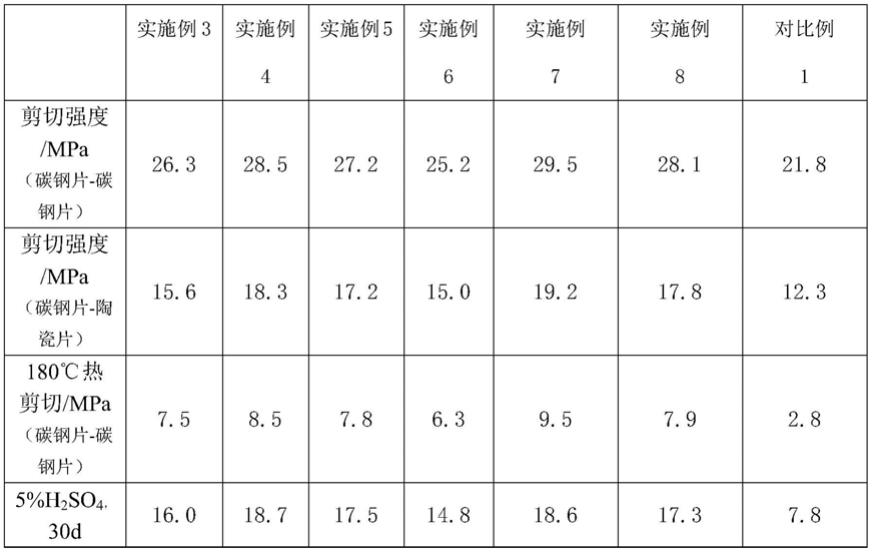
1.本发明是一种陶瓷材料用胶黏剂及制备方法,属胶粘剂领域,具体涉及一种陶瓷材料用胶黏剂的制备。
背景技术:2.近年来,随着陶瓷材料的大规模研究开发,陶瓷的连接技术显得尤为重要,实现陶瓷与陶瓷或陶瓷与金属的连接可进一步扩大陶瓷的应用范围。陶瓷具有耐高温、耐腐蚀、高强度等基本属性,但又存在脆性大(塑韧性极差)、难加工等弱点,因而急需一种性能优异的陶瓷胶接用耐高温胶粘剂,用于陶瓷与金属或其他材质的连接,减少机械加工对陶瓷的破坏性。基于陶瓷表面极性差、多孔性与光滑等特点,要求胶粘剂的极性强、渗透性能好、致密性高、粘结力强;同时考虑到陶瓷的高脆性、刚性,要求胶粘剂的强度高、硬性大、不易变形;为了保证陶瓷的高温应用,胶粘剂必须具有良好的热冲击性。采用环氧胶粘剂进行粘接来实现耐磨陶瓷与设备金属件之间的连接是一种行之有效的连接方式,现已推广至电力、冶金、矿山、水泥等行业并已经得到了广泛的应用与认可,具有非常大的应用价值。
3.专利号为cn201110324359.0的专利公开了一种环氧耐磨陶瓷片粘接胶及其制备方法,其采用8240酚醛环氧树脂、自制增韧剂和低粘度固化剂制备了一种陶瓷片胶粘剂,该粘结剂对于碳钢具有较好的粘接效果,但是对于陶瓷片的粘接强度不够大(陶瓷与碳钢的剪切强度<14mpa),其工作温度<160℃。
技术实现要素:4.本发明的目的是提供一种陶瓷材料用胶黏剂及制备方法,以克服现有技术上的上述不足.
5.一种环氧耐磨陶瓷片粘接胶,包括a组分和b组分,所述a、b两组分的重量比为a:b=2:1,其中,
6.a组分由以下重量份的组分组成:
7.混合环氧树脂90~150份,自制增韧剂10~30份,稀释剂10~15份,氧化铝粉80~120份,重质碳酸钙20~40份,纤维状填料20~40,气相白炭黑15~30份,硅烷偶联剂3~5份;
8.b组分由以下重量份的组分组成:
9.陶瓷粘结剂用复配型固化剂40~60份,固化促进剂1~5份,氧化铝粉50~80份,重质碳酸钙30~50份,纤维状填料5~10份,气相白炭黑3~8份,硅烷偶联剂1~3份;
10.所述自制增韧剂为硅烷改性聚氨酯型增韧剂,合成方法为:在60~80℃条件下在反应釜中按照质量比为100:15~22.5的比例加入聚醚二元醇和4,4
’‑
二苯基甲烷二异氰酸酯,再加入0.01份的二月桂酸二级丁基锡反应3h后,循环水降温至料温≤30℃,然后逐滴加入的2~10份的氨基硅烷继续反应1h,得到粘稠状的透明物质,即为合成的硅烷改性聚氨酯型增韧剂;
11.所述混合环氧树脂是由多官能度环氧树脂ag-80和低粘度酚醛环氧树脂8240组成,其中ag-80环氧树脂用量为混合环氧树脂总重量的50~70%,8240低粘度酚醛环氧树脂用量为混合环氧树脂总重量的30~50%;混合环氧树脂在25℃时粘度为(20000-40000)mpa.s;所述的陶瓷粘结剂复配型固化剂是由三种固化剂按比例配制而成,其中三乙烯四胺含量为20~30%,氨基乙基哌嗪含量为10~20%,低粘度改性脂肪胺固化剂含量为50~70%。
12.所述的稀释剂是反应型环氧类稀释剂,包括乙二醇二缩水甘油醚、1,4-丁二醇二缩水甘油醚、1.6-己二醇二缩水甘油醚中的一种或多种的组合;
13.所述的环氧固化促进剂是一种液体叔胺类物质,特别的该促进剂为4,6-三(二甲氨基甲基)苯酚;
14.所述的纤维状填料为硫酸钙晶须或玻璃纤维。
15.本发明更优组份选择为:
16.a组分由以下重量份的组分组成优先如下:
17.混合环氧树脂100~140份,自制增韧剂15~25份,稀释剂10~15份,氧化铝粉80~100份,重质碳酸钙20~40份,纤维状填料20~40,气相白炭黑15~20份,硅烷偶联剂3~5份;
18.b组分由以下重量份的组分组成优先如下:
19.陶瓷粘结剂用复配型固化剂45~55份,固化促进剂3~5份,氧化铝粉50~80份,重质碳酸钙35~45份,纤维状填料7~10份,气相白炭黑3~8份,硅烷偶联剂2~3份。
20.本发明组成又为:
21.a组分由以下重量份的组分组成优先如下:
22.混合环氧树脂110~120份,自制增韧剂10~20份,稀释剂10~15份,氧化铝粉80~120份,重质碳酸钙20~40份,纤维状填料20~40,气相白炭黑20~25份,硅烷偶联剂3~5份;
23.b组分由以下重量份的组分组成优先如下:
24.陶瓷粘结剂用复配型固化剂50~55份,固化促进剂1~5份,氧化铝粉60~70份,重质碳酸钙30~50份,纤维状填料5~10份,气相白炭黑7~8份,硅烷偶联剂1~2份。
25.所述多官能度环氧树脂ag-80平均官能度4,50℃的粘度3000~7000mpa
·
s,环氧值≥0.8mol/100g;所述8240低粘度酚醛环氧树脂平均官能度2~3,25℃的粘度6000~7100mpa
·
s,环氧值为0.5mol/100g~0.6mol/100g。
26.所述的聚醚二元醇羟值为54.5mgkoh/g~57.5mgkoh/g。
27.所述的低粘度改性脂肪胺环氧固化剂为透明粘稠液体,25℃的粘度4500~7500mpa
·
s,胺值120~160mgkoh/g。
28.所述硫酸钙晶须长度为20~100um,直径为1~3um,玻璃纤维长度为100~500um,直径为11-13um。
29.所述的氧化铝粉,特别的其粒径为(20~60)um;所述的重质碳酸钙,特别的其粒径为(5~15)um。
30.所述的硅烷偶联剂在a组分中所用为环氧基硅烷偶联剂,b组分中所用为胺基硅烷偶联剂。
31.一种制备上述陶瓷材料用胶黏剂的制备方法,具体步骤如下:
32.制备a组分步骤为:
33.步骤一、将所述氧化铝粉、重质碳酸钙、纤维状填料、气相白炭黑预先在干燥机上于120℃干燥2小时,然后冷却至室温待用;
34.步骤二、所述ag-80、8240环氧树脂预先在80℃下预热5h;
35.步骤三、将行星分散釜加热至80℃,按比例先加入ag-80环氧树脂、8240低粘度酚醛环氧树脂、稀释剂于分散釜中,搅拌大约15min,保持真空度为-0.090~-0.095mpa;
36.步骤四、降温至40℃,按比例加入自制增韧剂、硅烷偶联剂搅拌大约10min,保持真空度为-0.090~-0.095mpa;
37.步骤五、然后按比例加入氧化铝粉、重质碳酸钙、纤维状填料,高速搅拌大约15min,保持真空度为-0.090~-0.095mpa;
38.步骤六、然后按比例加入气相白炭黑,高速搅拌大约5min,保持真空度为-0.090~-0.095mpa;
39.步骤七、降低搅拌速度缓慢降温至30℃,采用60目网过滤出料分装。
40.制备b组分步骤为:
41.步骤八、将所述氧化铝粉、重质碳酸钙、纤维状填料、气相白炭黑预先先在干燥机上于120℃干燥2小时,然后冷却至室温待用;
42.步骤九、将行星分散釜加热至50℃,按比例加入三乙烯四胺、氨基乙基哌嗪、改性脂肪胺、环氧促进剂、硅烷偶联剂于分散釜中搅拌大约10min,保持真空度为-0.090~-0.095mpa;
43.步骤十、然后按比例加入氧化铝粉、重质碳酸钙、纤维状填料高速搅拌大约10min,保持真空度为-0.090~-0.095mpa;
44.步骤十一、然后按比例加入气相白炭黑,高速搅拌大约10min,保持真空度为-0.090~-0.095mpa;
45.步骤十二、降低搅拌速度缓慢降温至30℃,采用60目网过滤出料分装。
46.有益效果
47.本发明提供陶瓷材料用胶黏剂具有很强的耐温性、粘接性以及耐介质性能;常温下对陶瓷片的剪切力在15mpa以上,180℃条件下对陶瓷片的剪切力在5mpa以上,并可满足短时间在250℃以下对陶瓷片的粘接使用要求,性能优于普通的环氧胶黏剂;同时产品有较好的耐硫酸介质的腐蚀性能,可满足气流冲刷过程中对酸性介质的耐腐蚀要求;在施工方面触变性优良,可立面涂抹不流淌,便于陶瓷片的粘接施工,可减少了陶瓷片在粘接过程中的因加工导致的应力损伤。主要可用于某型号航天器材耐热陶瓷片的粘接,也可以用于电力、化工设备等陶瓷材料的粘接。
具体实施方式
48.本发明提出了一种陶瓷材料用胶黏剂及其制备方法,其粘接强度(>18mpa)和较高耐热性能(<200℃)的陶瓷材料用胶黏剂和制备方法。通过自制的硅烷改性聚氨酯为增韧剂对环氧耐磨陶瓷片粘接胶进行增韧改性,提高高温下基材的附着力;采用耐温型混合环氧树脂与多种固化剂复配体系提高胶黏剂耐温性以及耐介质性,复配的固化剂为三乙烯
四胺、氨基乙基哌嗪和低粘度改性脂肪胺固化剂;添加纤维状填料提高胶黏剂抗剪切性能。
49.为了实现本发明的目的,提出一种环氧耐磨陶瓷片粘接胶,所述粘接胶包括a组分和b组分,所述a、b两组分的重量比为a:b=2:1,其中,
50.a组分由以下重量份的组分组成:
51.混合环氧树脂90~150份,自制增韧剂10~30份,稀释剂10~15份,氧化铝粉80~120份,重质碳酸钙20~40份,纤维状填料20~40,气相白炭黑15~30份,硅烷偶联剂3~5份。
52.b组分由以下重量份的组分组成:
53.陶瓷粘结剂用复配型固化剂40~60份,固化促进剂1~5份,氧化铝粉50~80份,重质碳酸钙30~50份,纤维状填料5~10份,气相白炭黑3~8份,硅烷偶联剂1~3份。
54.所述混合环氧树脂是由多官能度环氧树脂ag-80和低粘度酚醛环氧树脂8240组成,其中ag-80环氧树脂用量为混合环氧树脂总重量的50~70%,8240低粘度酚醛环氧树脂用量为混合环氧树脂总重量的30~50%。所述多官能度环氧树脂ag-80平均官能度4,50℃的粘度3000~7000mpa
·
s,环氧值≥0.8mol/100g;所述8240低粘度酚醛环氧树脂平均官能度2~3,25℃的粘度6000~7100mpa
·
s,环氧值为(0.5~0.6)mol/100g;
55.所述自制增韧剂为硅烷改性聚氨酯型增韧剂,合成方法为在(60~80)℃条件下在反应釜中按照质量比为100:(15~22.5)的比例加入聚醚二元醇和4,4
’‑
二苯基甲烷二异氰酸酯,再加入0.01份的二月桂酸二级丁基锡反应3h后,循环水降温至料温≤30℃,然后逐滴加入的(2~10)份的氨基硅烷继续反应1h,可得到粘稠状的透明物质,即为合成的硅烷改性聚氨酯型增韧剂。所述的聚醚二元醇羟值为(54.5~57.5)mgkoh/g。
56.所述的陶瓷粘结剂复配型固化剂是由三种固化剂按比例配制而成,其中三乙烯四胺含量为20~30%,氨基乙基哌嗪含量为10~20%,低粘度改性脂肪胺固化剂含量为50~70%;其中低粘度改性脂肪胺环氧固化剂,外观为微黄色透明粘稠液体,25℃的粘度4500~7500mpa
·
s,胺值120~160mgkoh/g。
57.所述的稀释剂是反应型环氧类稀释剂,包括乙二醇二缩水甘油醚、1,4-丁二醇二缩水甘油醚、1.6-己二醇二缩水甘油醚中的一种或多种的组合;
58.所述的环氧固化促进剂是一种液体叔胺类物质,特别的该促进剂为4,6-三(二甲氨基甲基)苯酚;
59.所述的纤维状填料为硫酸钙晶须或玻璃纤维,特别的硫酸钙晶须长度为20~100um,直径为1~3um,玻璃纤维长度为100~500um,直径为11-13um;
60.所述的氧化铝粉,特别的其粒径为(20~60)um;所述的重质碳酸钙,特别的其粒径为(5~15)um。
61.所述的硅烷偶联剂a组分中所用为环氧基硅烷偶联剂,b组分中所用为胺基硅烷偶联剂。
62.本发明还提出一种制备上述陶瓷材料用胶黏剂的方法,具体步骤如下:
63.(1)将所述氧化铝粉、重质碳酸钙、纤维状填料、气相白炭黑预先在干燥机上于120℃干燥2小时,然后冷却至室温待用;
64.(2)所述ag-80、8240环氧树脂预先在80℃下预热5h;
65.(3)将行星分散釜加热至80℃,按比例先加入ag-80环氧树脂、8240低粘度酚醛环
氧树脂、稀释剂于分散釜中,搅拌大约15min,保持真空度为-0.090~-0.095mpa;
66.(4)降温至40℃,按比例加入自制增韧剂、硅烷偶联剂搅拌大约10min,保持真空度为-0.090~-0.095mpa;
67.(5)然后按比例加入氧化铝粉、重质碳酸钙、纤维状填料,高速搅拌大约15min,保持真空度为-0.090~-0.095mpa;
68.(6)然后按比例加入气相白炭黑,高速搅拌大约5min,保持真空度为-0.090~-0.095mpa;
69.(7)降低搅拌速度缓慢降温至30℃,采用60目网过滤出料分装。
70.制备b组分步骤为:
71.(1)将所述氧化铝粉、重质碳酸钙、纤维状填料、气相白炭黑预先先在干燥机上于120℃干燥2小时,然后冷却至室温待用;
72.(2)将行星分散釜加热至50℃,按比例加入三乙烯四胺、氨基乙基哌嗪、改性脂肪胺、环氧促进剂、硅烷偶联剂于分散釜中搅拌大约10min,保持真空度为-0.090~-0.095mpa;
73.(3)然后按比例加入氧化铝粉、重质碳酸钙、纤维状填料高速搅拌大约10min,保持真空度为-0.090~-0.095mpa;
74.(4)然后按比例加入气相白炭黑,高速搅拌大约10min,保持真空度为-0.090~-0.095mpa;
75.(5)降低搅拌速度缓慢降温至30℃,采用60目网过滤出料分装。
76.为使本发明的目的、技术方案和优点更加清楚明白,以下结合具体实施例,对本发明的技术方案进一步详细说明。
77.实施例1
78.自制增韧剂合成方法:
79.在60℃条件下在搪瓷反应釜中加入100份的聚醚二元醇dl-2000d和15份的4,4
’‑
二苯基甲烷二异氰酸酯,再加入0.01份的二月桂酸二级丁基锡反应3h,循环水降温至料温≤30℃,然后逐滴加入的2.5份的氨基硅烷继续反应1h至异氰酸酯根含量≤0.05%,可得到粘稠状的透明物质,即为合成的硅烷改性聚氨酯型增韧剂。
80.实施例2
81.自制增韧剂合成方法:
82.在60℃条件下在搪瓷反应釜中加入100份的聚四氢呋喃醚二醇和22.5份的4,4
’‑
二苯基甲烷二异氰酸酯,再加入0.01份的二月桂酸二级丁基锡反应3h,循环水降温至料温≤30℃,然后逐滴加入的9份的氨基硅烷继续反应1h至异氰酸酯根含量≤0.05%,可得到粘稠状的透明物质,即为合成的硅烷改性聚氨酯型增韧剂。
83.实施例3
84.a组分由以下重量份的组分组成:
85.ag-80环氧树脂45份,8240低粘度环氧树脂45份,自制增韧剂(实施例1)10份,1,4-丁二醇二缩水甘油醚10份,硅烷偶联剂3份,氧化铝粉80份,重质碳酸钙20份,硫酸钙晶须20份,气相白炭黑15份。
86.b组分由以下重量份的组分组成:
87.三乙烯四胺含量为8份,氨基乙基哌嗪含量为4份,低粘度改性脂肪胺固化剂含量为28份,环氧促进剂4份,硅烷偶联剂1份,氧化铝粉50份,重质碳酸钙30份,硫酸钙晶须5份,气相白炭黑3份。
88.实施例4
89.a组分由以下重量份的组分组成:
90.ag-80环氧树脂105份,8240低粘度环氧树脂45份,自制增韧剂(实施例1)30份,1,4-丁二醇二缩水甘油醚15份,硅烷偶联剂5份,氧化铝粉120份,重质碳酸钙40份,硫酸钙晶须40份,气相白炭黑20份。
91.b组分由以下重量份的组分组成:
92.三乙烯四胺含量为18份,氨基乙基哌嗪含量为12份,低粘度改性脂肪胺固化剂含量为30份,环氧促进剂5份,硅烷偶联剂3份,氧化铝粉80份,重质碳酸钙50份,硫酸钙晶须10份,气相白炭黑8份。
93.实施例5
94.ag-80环氧树脂72份,8240低粘度环氧树脂48份,自制增韧剂(实施例2)20份,1,6-己二醇二缩水甘油醚15份,硅烷偶联剂3份,氧化铝粉90份,重质碳酸钙25份,玻璃纤维25份,气相白炭黑20份。
95.b组分由以下重量份的组分组成:
96.三乙烯四胺含量为12份,氨基乙基哌嗪含量为5份,低粘度改性脂肪胺固化剂含量为25份,环氧促进剂2份,硅烷偶联剂2份,氧化铝粉60份,重质碳酸钙40份,玻璃纤维7份,气相白炭黑5.5份。
97.实施例6
98.ag-80环氧树脂84份,8240低粘度环氧树脂56份,自制增韧剂(实施例2)15份,1,6-己二醇二缩水甘油醚15份,硅烷偶联剂4份,氧化铝粉100份,重质碳酸钙35份,玻璃纤维35份,气相白炭黑25份。
99.b组分由以下重量份的组分组成:
100.三乙烯四胺含量为13份,氨基乙基哌嗪含量为9份,低粘度改性脂肪胺固化剂含量为38份,环氧促进剂4份,硅烷偶联剂2份,氧化铝粉70份,重质碳酸钙45份,玻璃纤维8份,气相白炭黑6.5份。
101.实施例7
102.ag-80环氧树脂65份,8240低粘度环氧树脂35份,自制增韧剂(实施例1)25份,1,6-己二醇二缩水甘油醚13份,硅烷偶联剂3.5份,氧化铝粉110份,重质碳酸钙30份,玻璃纤维30份,气相白炭黑15份。
103.b组分由以下重量份的组分组成:
104.三乙烯四胺含量为11份,氨基乙基哌嗪含量为6.5份,低粘度改性脂肪胺固化剂含量为32.5份,环氧促进剂1份,硅烷偶联剂2.5份,氧化铝粉65份,重质碳酸钙48份,玻璃纤维9份,气相白炭黑7份。
105.实施例8
106.ag-80环氧树脂71.5份,8240低粘度环氧树脂58.5份,自制增韧剂(实施例2)20份,1,6-己二醇二缩水甘油醚12份,硅烷偶联剂4.5份,氧化铝粉90份,重质碳酸钙36份,玻璃纤
维33份,气相白炭黑23份。
107.b组分由以下重量份的组分组成:
108.三乙烯四胺含量为16份,氨基乙基哌嗪含量为8.8份,低粘度改性脂肪胺固化剂含量为30.2份,环氧促进剂1.5份,硅烷偶联剂1.5份,氧化铝粉75份,重质碳酸钙35份,玻璃纤维6份,气相白炭黑4份。
109.对比例1
110.e-51环氧树脂40份,8240低粘度环氧树脂40份,ctbn增韧剂10份,稀释剂5份,氧化铝粉120份,石英粉5份,重质碳酸钙5份,气相白炭黑5份。
111.b组分由以下重量份的组分组成:
112.t31环氧固化剂80份,环氧促进剂4份,硅烷偶联剂4份,氧化铝粉120份,石英粉50份,重质碳酸钙60份,气相白炭黑10份。
113.上述实施例中具体生产工艺均按照以下工艺制得:
114.制备a组分步骤为:(1)将所述氧化铝粉、重质碳酸钙、纤维状填料、气相白炭黑预先在干燥机上于120℃干燥2小时,然后冷却至室温待用;(2)将ag-80、8240环氧树脂预先在80℃下预热5h;(3)将行星分散釜加热至80℃,按比例先加入ag-80环氧树脂、8240低粘度酚醛环氧树脂、稀释剂于分散釜中,搅拌大约15min,保持真空度为-0.090~-0.095mpa;(4)降温至40℃,按比例加入自制增韧剂、硅烷偶联剂搅拌大约10min,保持真空度为-0.090~-0.095mpa;(5)然后按比例加入氧化铝粉、重质碳酸钙、纤维状填料,高速搅拌大约15min,保持真空度为-0.090~-0.095mpa;(6)然后按比例加入气相白炭黑,高速搅拌大约5min,保持真空度为-0.090~-0.095mpa;
115.(7)降低搅拌速度缓慢降温至30℃,采用60目网过滤出料分装。
116.制备b组分步骤为:(1)将所述氧化铝粉、重质碳酸钙、纤维状填料、气相白炭黑预先先在干燥机上于120℃干燥2小时,然后冷却至室温待用;(2)将行星分散釜加热至50℃,按比例加入三乙烯四胺、氨基乙基哌嗪、改性脂肪胺、环氧促进剂、硅烷偶联剂于分散釜中搅拌大约10min,保持真空度为-0.090~-0.095mpa;(3)然后按比例加入氧化铝粉、重质碳酸钙、纤维状填料高速搅拌大约10min,保持真空度为-0.090~-0.095mpa;(4)然后按比例加入气相白炭黑,高速搅拌大约10min,保持真空度为-0.090~-0.095mpa;(5)降低搅拌速度缓慢降温至30℃,采用60目网过滤出料分装。
117.以上双组份胶黏剂按质量比为2:1进行混合调胶,在适用期内涂抹于陶瓷板与不锈钢板、铝板、铸铁件之间,胶层厚为(1-2)mm,经过23℃以上(1~2)d可以完成初步固化,满足运输和初步加工条件,1周后可以受力和介质浸泡。
118.以实施例3~6制备的陶瓷材料用胶黏剂测试其性能如下表所示:
[0119][0120][0121]
胶黏剂的剪切强度参照gb/t7124-2008的测试方法进行。通过实施例3~6可见该胶黏剂对碳钢和陶瓷均具有较好的粘接效果,尤其是在180℃高温环境下,该胶黏剂仍能保持较高的剪切强度,可满足某型号飞行器的高温环境下使用需要,而且在长期的硫酸介质的腐蚀下,对剪切强度影响不大,性能优于对比例。
[0122]
以上所述的具体实施例,对本发明的目的、技术方案和有益效果进行了进一步的详细说明,所应理解的是,以上所述仅为本发明的具体实施例而已,并不用于限制本发明,凡在本发明的精神和原则之内,所做的任何修改、等同替换、改进等,均应包含在本发明的保护范围之内。