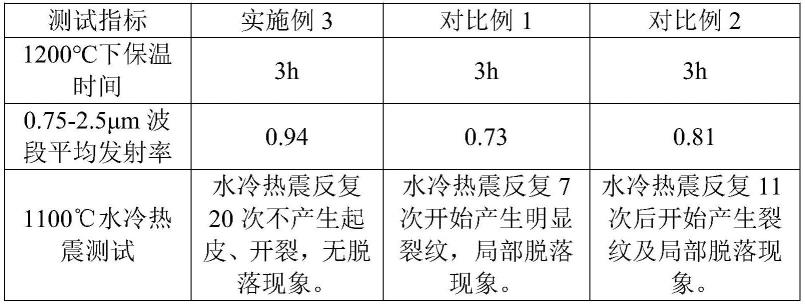
1.本发明涉及一种红外辐射涂料及其制备方法和涂层领域,尤其是涉及一种基于铜冶炼渣的高发射率红外辐射涂料及其制备方法和涂层。
背景技术:2.铜冶炼一般是指从铜精矿到精炼铜的形成过程,其中火法炼铜是主流工艺。在火法炼铜过程中每生产1吨铜会排出2~3吨的铜渣,我国每年产生约2000万吨铜渣。铜渣中主要物相是磁铁矿(fe3o4)、铁橄榄石(2feo
·
sio2)及脉石组成的无定形玻璃体。闪速炉渣中fe3o4的含量较高,渣含铜量约为1%-3%,部分渣中含cu达4.5%。
3.目前,铜冶炼渣一般经浮选回收铜后,获得渣精矿和尾矿,渣精矿含cu 30%左右,一般返回配料系统;尾矿含cu 0.4%左右,铁品位为52%,主要成分为铁氧化物,可用作铁精矿的原料,或作水泥生产的掺合料。但根据炼铁要求,当含铜高的尾矿作铁精矿的原料时,必须使尾矿含铜降至0.2%左右。因此,这就直接制约了含铜高的尾矿合理利用的范围,使得相当多的含铜高的尾矿不得不采取堆放方法处理。总体来说,我国铜冶炼渣直接利用率非常低,部分处理方式尾矿量仍然比较大;铜渣尾矿的无序堆放,不仅侵占了大量的土地资源,而且铜渣含有cd、pb和as等重金属元素还会造成严重的环境污染问题。
4.另一方面,我国冶金、建材等高温行业能消巨大,其中工业窑炉能耗占全国总能耗的25%左右。因而,窑炉节能也是目前研究及生产应用的热点。在大于800℃的高温环境下,热量的传递以辐射传热为主;强化辐射传热能够大幅提升窑炉热效率,实现窑炉节能。现有的工业窑炉大多数工作温度在800~1400℃,在现有的工业窑炉炉壁表面涂覆高发射率红外辐射涂层是重要的途径,尤其是将红外辐射涂层在0.75~5μm波段的红外发射率提高至0.85以上,节能效果更明显。
5.中国专利cn 1038296 a一种远红外辐射涂料的制造方法,采用20-70%铜渣为原料制得的远红外辐射涂料;其中实施例1采用30%铜渣,全波段辐射率为0.9;实施例2采用30%铜渣,尽管全波段辐射率可达0.92,但其涂覆在金属材料表面。一般,远红外涂层重点关注8μm以上远红外波段的发射率。由于专利技术中信息有限,不能明确上述专利技术中全发射率是否包含在高温使用中起主导作用的0.75~5μm的近红外波段;另外,其在超过800℃的窑炉中使用效果也不明确。
6.此外,2019年北京科技大学张剑博士学位论文《尖晶石型铁氧体材料红外辐射性能强化基础研究》中表明,在室温条件下fe3o4是一种在3-5μm波段具有高红外发射率的材料,但是fe3o4在高温下并不稳定,在温度高于600℃时,fe3o4会氧化转变为fe2o3,而fe2o3的发射率在3-5μm仅为0.6左右。直接采用fe3o4材料用于制备红外辐射涂层很难在800~1400℃工业窑炉中长期使用。
技术实现要素:7.发明目的:为了解决现有技术中所存在的问题,本发明提出了一种高成本低廉的基于铜冶炼渣的高发射率红外辐射涂料及其制备方法和涂层,制备的涂层不仅在0.75-5μm波段具有高红外发射率,耐高温性强,能够在800-1400℃环境中长期使用。
8.技术方案:为达以上目的,本发明采取以下技术方案:一种基于铜冶炼渣的高发射率红外辐射涂料,以重量计算包括如下制备原料:铜冶炼渣细粉58~80份,改性铁鳞细粉12~27份,氧化铝微粉3~8份,钠硅玻璃粉2~5份,广西白泥1~3份,钠水玻璃粉0.5~1.5份,木质素磺酸铵0.5~1份。
9.更进一步的,所述铜冶炼渣细粉为采用火法炼铜工艺制备粗铜过程中产生的残渣磨至粒径<74μm得到的细粉;其tfe含量≥40%;cuo含量≥0.2%。
10.本发明选用铜冶炼渣为主要红外辐射涂料原料,一方面是利用铜冶炼渣中主要物相磁铁矿(fe3o4)作为红外辐射的功能基元;另一方面,渣中无定形玻璃体可以较好包裹fe3o4,从而大幅减少fe3o4的氧化,从而确保所制备的红外辐射涂层在3-5μm波段具有高红外发射率。
11.更进一步的,所述改性铁鳞细粉是以重量计算将8~18份的铁鳞细粉、3~6份的氧化镁细粉和1~2份的废铜粉混合均匀后于50~100mpa条件下压制成坯,再在1000~1400℃条件下保温3~6h,随炉自然冷却后破碎、筛分至粒径<74μm得到的细粉。
12.更进一步的,所述铁鳞细粉中tfe含量≥70%,平均粒径小于45μm。
13.铁鳞中主要组分为feo、fe2o3及fe3o4。当铁鳞、氧化镁和废铜粉在1000~1400℃高温热处理时,feo和fe2o3与氧化镁发生反应生成feo-mgo固溶体和镁铁尖晶石;废铜粉在该温度比feo更容易氧化,一方面可以减少铁鳞中feo的氧化,另一方面生成的cuo可以进一步与fe2o3反应生成铜铁尖晶石。由于fe
2+
、mg
2+
及cu
2+
尺寸相差不大,这使得很可能出现三种离子相互取代的现象,从而得到非标准组成的fe3o4、镁铁尖晶石和铜铁尖晶石的混合尖晶石;这种混合尖晶石中存在大量的晶格畸变或缺陷,这些晶格畸变与缺陷在高温时促进晶格振动增强和瞬时偶极矩的变化,从而大幅度提升改性铁鳞在在0.75~2.5μm波段的红外发射率。由于mgo吸收40%的feo后形成的feo-mgo固溶体熔点仍高达2000℃以及镁铁尖晶石熔点达1720℃,而fe3o4熔点仅为1595℃,改性铁鳞具有更高的使用温度。本发明选用改性铁鳞细粉作为红外辐射涂料的原料,一方面可以提高红外辐射涂层在0.75~2.5μm波段的红外发射率,另一方面也可以提高以铜冶炼渣为主红外辐射涂层的使用温度。
14.此外,当以铜冶炼渣为主的红外辐射涂层在800~1400℃高温环境使用时,fe3o4、镁铁尖晶石和铜铁尖晶石等组成混合尖晶石中fe
2+
、mg
2+
及cu
2+
还会进一步互扩散,甚至铜冶炼渣中的cu
2+
或zn
2+
也可能参与这种扩散,从而使尖晶石的复杂程度进一步增加,从而确保以铜冶炼渣为主的红外辐射涂层在0.75~2.5μm波段保持高的红外发射率。
15.更进一步的,所述氧化镁细粉中mgo含量≥96%,平均粒径小于45μm。
16.更进一步的,所述废铜粉中cu含量≥90%,平均粒径小于45μm。
17.更进一步的,所述钠硅玻璃粉的平均粒径小于45μm;所述氧化铝微粉的平均粒径小于3μm。
18.本发明还公开了上述基于铜冶炼渣的高发射率红外辐射涂料的制备方法,包括如下步骤:将制备原料按配方混合得到混合原料,再按混合原料与去离子水为100∶(48~75)
的重量比向所述混合原料中加入去离子水,在行星球磨机中球磨0.5~3h,制得基于铜冶炼渣的高发射率红外辐射涂料。
19.更进一步的,所述行星球磨机中的磨球为刚玉球,球料比为(2~4)∶1。
20.本发明还公开了上述涂料制备的涂层,将涂料涂覆至工业窑炉耐火材料表面,自然干燥12~24h,于800~1400℃条件下热处理2~4h或随工业窑炉升温至800~1400℃,制得基于铜冶炼渣的高发射率红外辐射涂层。
21.有益效果:
22.(1)本发明采用大量铜冶炼渣为原料,属于固体废弃物,不仅可以降低高发射率红外辐射涂层的生产成本,而且为这种固废的高附加值利用提供了新的途径。
23.(2)本发明采用氧化铝微粉、钠硅玻璃粉、广西白泥、钠水玻璃粉以及铜冶炼渣中的玻璃相共同组成结合系统,一方面能够确保红外辐射涂层在中低温度具有较好的结合能力,并且在800~1400℃产生液相不会流淌,既有效解决红外辐射涂层与工业窑炉的结合问题,又提升了红外辐射涂层的热震稳定性;另一方面,结合体系中适当的液相也会大幅减少fe3o4的氧化,从而确保其在800-1400℃环境中长期发挥红外辐射作用。
24.(3)本发明制备的红外辐射涂料很容易涂覆至工业窑炉耐火材料表面,使用高温红外发射率测试设备测试基于铜冶炼渣的红外辐射涂层0.75~2.5μm波段的平均发射率为0.85~0.94;基于铜冶炼渣的高发射率红外辐射涂层能够在800-1400℃环境中长期使用。
具体实施方式
25.实施例1:
26.一种基于铜冶炼渣的高发射率红外辐射涂料,以重量计算包括如下制备原料:铜冶炼渣细粉58份,改性铁鳞细粉12份,氧化铝微粉3份,钠硅玻璃粉5份,广西白泥1份,钠水玻璃粉1.5份,木质素磺酸铵0.5份。
27.其中所述铜冶炼渣细粉为采用火法炼铜工艺制备粗铜过程中产生的残渣磨至粒径<74μm得到的细粉;其tfe含量≥40%;cuo含量≥0.2%。
28.所述改性铁鳞细粉是以重量计算将8份的铁鳞细粉、3份的氧化镁细粉和1份的废铜粉混合均匀后于50mpa条件下压制成坯,再在1000℃条件下保温6h,随炉自然冷却后破碎、筛分至粒径<74μm得到的细粉;所述铁鳞细粉中tfe含量≥70%,平均粒径小于45μm。所述氧化镁细粉中mgo含量≥96%,平均粒径小于45μm。所述废铜粉中cu含量≥90%,平均粒径小于45μm;
29.所述钠硅玻璃粉的平均粒径小于45μm;所述氧化铝微粉的平均粒径小于3μm。
30.上述基于铜冶炼渣的高发射率红外辐射涂料的制备方法,包括如下步骤:将制备原料按配方混合得到混合原料,再按混合原料与去离子水为100∶48的重量比向所述混合原料中加入去离子水,在行星球磨机中球磨0.5h,制得基于铜冶炼渣的高发射率红外辐射涂料。所述行星球磨机中的磨球为刚玉球,球料比为2∶1。
31.将涂料涂覆至工业窑炉耐火材料表面,自然干燥12h,于800℃条件下热处理2h,制得基于铜冶炼渣的高发射率红外辐射涂层。
32.实施例2:
33.一种基于铜冶炼渣的高发射率红外辐射涂料,以重量计算包括如下制备原料:铜
冶炼渣细粉80份,改性铁鳞细粉27份,氧化铝微粉8份,钠硅玻璃粉2份,广西白泥3份,钠水玻璃粉0.5份,木质素磺酸铵1份。
34.其中所述铜冶炼渣细粉为采用火法炼铜工艺制备粗铜过程中产生的残渣磨至粒径<74μm得到的细粉;其tfe含量≥40%;cuo含量≥0.2%。
35.所述改性铁鳞细粉是以重量计算将18份的铁鳞细粉、6份的氧化镁细粉和2份的废铜粉混合均匀后于100mpa条件下压制成坯,再在1400℃条件下保温3h,随炉自然冷却后破碎、筛分至粒径<74μm得到的细粉;所述铁鳞细粉中tfe含量≥70%,平均粒径小于45μm。所述氧化镁细粉中mgo含量≥96%,平均粒径小于45μm。所述废铜粉中cu含量≥90%,平均粒径小于45μm;
36.所述钠硅玻璃粉的平均粒径小于45μm;所述氧化铝微粉的平均粒径小于3μm。
37.上述基于铜冶炼渣的高发射率红外辐射涂料的制备方法,包括如下步骤:将制备原料按配方混合得到混合原料,再按混合原料与去离子水为100∶75的重量比向所述混合原料中加入去离子水,在行星球磨机中球磨3h,制得基于铜冶炼渣的高发射率红外辐射涂料。所述行星球磨机中的磨球为刚玉球,球料比为4∶1。
38.将涂料涂覆至工业窑炉耐火材料表面,自然干燥24h,于1400℃条件下热处理3h,制得基于铜冶炼渣的高发射率红外辐射涂层。
39.实施例3:
40.一种基于铜冶炼渣的高发射率红外辐射涂料,以重量计算包括如下制备原料:铜冶炼渣细粉70份,改性铁鳞细粉20份,氧化铝微粉5份,钠硅玻璃粉3份,广西白泥2份,钠水玻璃粉1.0份,木质素磺酸铵0.8份。
41.其中所述铜冶炼渣细粉为采用火法炼铜工艺制备粗铜过程中产生的残渣磨至粒径<74μm得到的细粉;其tfe含量≥40%;cuo含量≥0.2%。
42.所述改性铁鳞细粉是以重量计算将12份的铁鳞细粉、5份的氧化镁细粉和2份的废铜粉混合均匀后于75mpa条件下压制成坯,再在1200℃条件下保温5h,随炉自然冷却后破碎、筛分至粒径<74μm得到的细粉;所述铁鳞细粉中tfe含量≥70%,平均粒径小于45μm。所述氧化镁细粉中mgo含量≥96%,平均粒径小于45μm。所述废铜粉中cu含量≥90%,平均粒径小于45μm;
43.所述钠硅玻璃粉的平均粒径小于45μm;所述氧化铝微粉的平均粒径小于3μm。
44.上述基于铜冶炼渣的高发射率红外辐射涂料的制备方法,包括如下步骤:将制备原料按配方混合得到混合原料,再按混合原料与去离子水为100∶60的重量比向所述混合原料中加入去离子水,在行星球磨机中球磨2h,制得基于铜冶炼渣的高发射率红外辐射涂料。所述行星球磨机中的磨球为刚玉球,球料比为3∶1。
45.将涂料涂覆至工业窑炉耐火材料表面,自然干燥20h,随工业窑炉升温至1200℃,制得基于铜冶炼渣的高发射率红外辐射涂层。
46.另设对比例1和2,
47.对比例1:
48.其他实施方式与实施例3相同,不同之处在于配方以重量计算包括如下制备原料:铜渣50份,氧化铁20份,硅溶胶30份。
49.其中铜渣为冶金工业矿渣,其平均粒径<74μm;氧化铁均为化学纯,平均粒径<45
μm,硅溶胶中sio2含量≥25%。
50.对比例2:
51.其他实施方式与实施例3相同,不同之处在于配方以重量计算包括如下制备原料:铜渣50份,fe3o4细粉20份,水玻璃溶液10份。
52.其中铜渣为冶金工业矿渣,其平均粒径<74μm;fe3o4细粉均为化学纯,平均粒径<45μm,水玻璃溶液的比重大于1.30g/cm3。
53.对实施例3以及对比例1~2制备而成的涂层,采用高温红外发射率测试设备进行测试:
54.测试结果如表1所示:
55.表1实施例3以及对比例1~2涂层性能测试结果
[0056][0057]
从表1的数据可以看出,在1200℃保温3h条件下,本发明制备的基于铜冶炼渣的高发射率红外辐射涂层,0.75~2.5μm波段的平均发射率为0.94;并且,该涂层经1100℃水冷热震测试反复20次后,不产生起皮、开裂以及脱落现象。而对比例1的涂层除铜渣外引入了氧化铁,氧化铁虽然在加热过程中可以小部分转化为fe3o4,其对0.75~2.5μm波段发射率的提升有限;并且选用常见硅溶胶作为结合剂,涂层与耐火材料基底的结合有限,7次热震后即出现裂纹和局部剥落。对比例2的涂层除铜渣外引入了fe3o4细粉,它能在一定程度上提升0.75~2.5μm波段的发射率;即使改用水玻璃作为结合剂,涂层水冷热震反复11次后也开始产生裂纹及局部脱落现象。本技术方案引入的改性铁鳞中在含有大量能够形成尖晶石的成分,能够形成混合尖晶石,如正尖晶石mgal2o4、mgcr2o4,反尖晶石mgfe2o4和fe3o4,其中存在大量的晶格畸变与晶格缺陷,这些晶格畸变与晶格缺陷在高温时促进晶格振动增强和瞬时偶极矩的变化,提升了涂层在0.75~2.5μm波段的红外辐射性能,其在该波段发射率能够达到0.94。并且,本技术方案涂层采用氧化铝微粉、钠硅玻璃粉、广西白泥2份为复合结合体系,可以较好解决涂层与基体结合问题,结合体系中适当的液相也会大幅减少fe3o4的氧化,从而确保其在800-1400℃环境中长期发挥红外辐射作用。