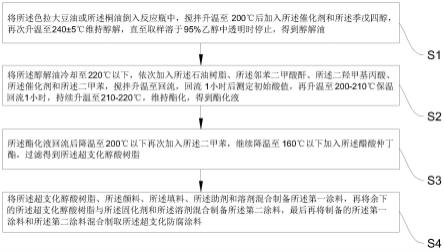
1.本发明涉及防腐涂料技术领域,尤其涉及一种超支化防腐涂料及其制备方法。
背景技术:2.涂料是人类生活生产中必需的功能材料,但传统的溶剂型涂料一般含有较高的挥发性有机化合物,会污染环境并对人体造成伤害。
3.随着国民环保意识增强,涂料市场对环保型和节能型涂料需求不断增长,涂料制造行业正在向水性涂料、高固体涂料和低挥发性有机化合物含量涂料等环保化与多功能化产品方向转变,从而实现新旧产能替代。
4.因此传统的线型聚合物涂料,不再满足现有的环保需求。
技术实现要素:5.本发明的目的在于提供一种超支化防腐涂料及其制备方法,旨在解决传统传统的线型聚合物涂料,不满足现有环保需求的问题。
6.为实现上述目的,第一方面,本发明提供了一种超支化防腐涂料,所述超支化防腐涂料由第一涂料和第二涂料混合而成,所述第一涂料成分和重量百分比为超支化树脂15-30%、颜料1-5%、填料40-70%、助剂0.5-5%和溶剂4-15%,所述第二涂料成分和重量百分比为固化剂10-100%和溶剂0-90%。
7.其中,所述超支化树脂原料成分和重量百分比为:色拉大豆油或桐油 35-50%、季戊四醇8-12%、二羟甲基丙酸3-5%、邻苯二甲酸酐15-20%、石油树脂0-20%、催化剂0.1%-0.6%和溶剂20%-25%。
8.其中,所述催化剂为氢氧化锂和对甲苯磺酸钠中的中的任意一种或两种。
9.其中,所述溶剂为二甲苯和醋酸仲丁酯中的中的任意一种或两种。
10.第二方面,本发明还提供了一种超支化防腐涂料制备方法,包括以下步骤:
11.将所述色拉大豆油或所述桐油倒入反应瓶中,搅拌升温至200℃后加入所述催化剂和所述季戊四醇,再次升温至240
±
5℃维持醇解,直至取样溶于95%乙醇中透明时停止,得到醇解油;
12.将所述醇解油冷却至220℃以下,依次加入所述石油树脂、所述邻苯二甲酸酐、所述二羟甲基丙酸、所述催化剂和所述二甲苯,搅拌升温至回流,回流1 小时后测定初始酸值,再升温至200-210℃保温回流1小时,持续升温至 210-220℃,维持酯化,得到酯化液;
13.所述酯化液回流后降温至200℃以下再次加入所述二甲苯,继续降温至 160℃以下加入所述醋酸仲丁酯,过滤得到所述超支化醇酸树脂;
14.将所述超支化醇酸树脂、所述颜料、所述填料、所述助剂和溶剂混合制备所述第一涂料,再将余下的所述超支化醇酸树脂与所述固化剂和所述溶剂混合制备所述第二涂料,最后再将制备的所述第一涂料和所述第二涂料混合制取所述超支化防腐涂料。
15.本发明的一种超支化防腐涂料,所述超支化防腐涂料由第一涂料和第二涂料混合
而成,所述第一涂料成分和重量百分比为超支化树脂15-30%、颜料1-5%、填料40-70%、助剂0.5-5%和溶剂4-15%,所述第二涂料成分和重量百分比为固化剂10-100%和溶剂0-90%,所述第一涂料与所述第二涂料分别包装,其混合比例根据施工需要确定,通常现场配制,本涂料具有高物理性能、耐冲击性大、柔韧性小和附着力强的特点,耐冲击性大于50cm,柔韧性小于等于1级,附着力在6mpa以上,拥有优异的耐性和防腐性能,耐盐雾性能在200h以上,且该涂料涂料施工性能好,满足各种钢结构涂装施工要求,并具有高固体和低挥发性有机化合物(voc)的特性,符合环保需求,适用期长,稳定性好,解决传统传统的线型聚合物涂料,不满足现有环保需求的问题。
附图说明
16.为了更清楚地说明本发明实施例或现有技术中的技术方案,下面将对实施例或现有技术描述中所需要使用的附图作简单地介绍,显而易见地,下面描述中的附图仅仅是本发明的一些实施例,对于本领域普通技术人员来讲,在不付出创造性劳动的前提下,还可以根据这些附图获得其他的附图。
17.图1是本发明提供的一种超支化防腐涂料制备方法的流程图。
具体实施方式
18.下面详细描述本发明的实施例,所述实施例的示例在附图中示出,其中自始至终相同或类似的标号表示相同或类似的元件或具有相同或类似功能的元件。下面通过参考附图描述的实施例是示例性的,旨在用于解释本发明,而不能理解为对本发明的限制。
19.本发明结合以下实施例对一种超支化树脂的防腐涂料做进一步描述。可以理解的是,此处所描述的具体实施例仅仅用于解释相关发明,而非对该发明的限定。
20.本发明涉及一种超支化树脂的防腐涂料,其特征在于由所述第一涂料和所述第二涂料混合而成;所述第一涂料成分和重量百分比为超支化树脂15-30%、颜料1-5%、填料40-70%、助剂0.5-5%和溶剂4-15%,所述第二涂料成分和重量百分比为固化剂10-100%和溶剂0-90%。
21.所述第一涂料成分和重量百分比:
22.成分重量百分比(%)超支化树脂15-30颜料1-5填料40-70助剂0.5-5溶剂4-15
23.所述第二涂料成分和重量百分比:
24.成分重量百分比(%)固化剂10-100溶剂0-90
25.其中,所述的超支化树脂由色拉大豆油、季戊四醇、二羟甲基丙酸、邻苯二甲酸酐、石油树脂、氢氧化锂、对甲苯磺酸钠、二甲苯和醋酸仲丁酯等原料合成。
26.所述的颜料为钛白粉、炭黑、铁蓝、氧化铁红中的一种或几种的组合。
27.所述的填料为沉淀硫酸钡、重质碳酸钙、云母氧化铁灰、磷铁粉中的一种或几种的组合。
28.所述的助剂为流变改性蜡液、微化酰胺蜡粉、有机膨润土、流平剂、抗结皮剂、分散剂、润湿剂中的一种或几种的组合。
29.所述的溶剂为二甲苯、乙酸丁酯、环己酮、丙酮、乙醇中的一种或几种的组合。
30.所述的固化剂为hdi聚合物、tdi聚合物、硅烷偶联剂中的至少一种。
31.所述的超支化树脂,其原料成分和重量百分比为:色拉大豆油35-50%、季戊四醇8-12%、二羟甲基丙酸2-4%、邻苯二甲酸酐15-20%、石油树脂0-20%、催化剂0.1%-0.6%、溶剂20%-25%。
32.其中,所述的催化剂为氢氧化锂和对甲苯磺酸钠中的一种或两种。
33.所述的溶剂为二甲苯和醋酸仲丁酯中的一种或两种。
34.本发明提供一种超支化涂料的制备方法,步骤如下:
35.s1将所述色拉大豆油或所述桐油倒入反应瓶中,搅拌升温至200℃后加入所述催化剂和所述季戊四醇,再次升温至240
±
5℃维持醇解,直至取样溶于95%乙醇中透明时停止,得到醇解油;
36.具体的,将所述色拉大豆油倒入具有搅拌器、回流冷凝管、温度计的四口反应瓶中,搅拌升温至200℃加入所述催化剂和所述季戊四醇,再升温至240
±ꢀ
5℃维持醇解,直至取样能溶于10倍95%乙醇(v/v,25℃)中透明为止,得到所述醇解油。
37.s2将所述醇解油冷却至220℃以下,依次加入所述石油树脂、所述邻苯二甲酸酐、所述二羟甲基丙酸、所述催化剂和所述二甲苯,搅拌升温至回流,回流1小时后测定初始酸值,再升温至200-210℃保温回流1小时,持续升温至 210-220℃,维持酯化,得到酯化液;
38.具体的,将所述醇解油冷却至220℃以下,停止搅拌依次加入所述石油树脂、所述邻苯二甲酸酐、所述二羟甲基丙酸、所述催化剂和部分所述二甲苯,搅拌升温至回流,回流1小时后测定初始酸值,并升温至200-210℃保温回流1小时,持续升温至210-220℃,维持酯化,得到所述酯化液。
39.s3所述酯化液回流后降温至200℃以下再次加入所述二甲苯,继续降温至 160℃以下加入所述醋酸仲丁酯,过滤得到所述超支化醇酸树脂;
40.具体的,所述酯化液酯化回流1、3、5小时分别取样测酸值,5小时后勤取样测酸值及粘度,待固体酸值≤22mgkoh/g,粘度≥28s(格式管粘度计)后,降温至200℃以下加入剩余的二甲苯,继续降温至160℃以下加入醋酸仲丁酯,过滤得到所述超支化醇酸树脂。
41.s4将所述超支化醇酸树脂、所述颜料、所述填料、所述助剂和溶剂混合制备所述第一涂料,再将余下的所述超支化醇酸树脂与所述固化剂和所述溶剂混合制备所述第二涂料,最后再将制备的所述第一涂料和所述第二涂料混合制取所述超支化防腐涂料。
42.具体的,将所述超支化树脂、基材润湿剂、附着力促进剂、所述颜料、所述填料和所述溶剂投入搅拌釜中,以500转/分搅拌10分钟后,放入研磨机研磨制得漆浆,将所述漆浆、流平剂、所述催化剂、抗结皮剂和所述溶剂将入搅拌釜中,以500转/分搅拌10分钟后过滤包装得到所述第一涂料;将生产的异氰酸酯类固化剂tdi三聚体,即所述超支化醇酸树脂用溶剂稀释后,过滤包装制得所述第二涂料,再将所述第一涂料与所述第二涂料分别包装,制备
所述超支化防腐涂料,将所述第一涂料与所述第二涂料按混合比例现场混合配置,混合比例根据施工需要确定,通常现场配制。
43.本发明的超支化防腐涂料根据实际使用场合的需要,还可以添加如下组分,如附着力促进剂、基材润湿剂或流平剂等,以获得更优的使用性能:
44.其中附着力促进剂是:甲基硅氧烷类,如z-6040、bfk-d等;其重量百分比为0.3~3%;
45.其中基材润湿剂是:氟改性有机硅氧烷类润湿剂,如wet245、byk345等;其重量百分比为0.1~1%;
46.其中流平剂是:有机硅类流平剂,如tego450,含氟类流平剂,如efka3600、 efka3777等的任一种,或两种以各自大于百分之零的比例混合;其重量百分比为0.2~1%。
47.所述第一涂料与所述第二涂料分别包装,在施工现场混合均匀,其混合比例根据施工需要确定,通常再进行配制,基本不受限制;本发明优选两组分的质量比a:b=m:n,m、n为自然数,如8:1、10:1、12:1、20:1等。
48.实施例1
49.超支化树脂a:称取豆油1389kg入釜,开动搅拌和热油升温至200℃加入氢氧化锂0.24kg和季戊四醇336kg,再升温至240
±
5℃维持醇解,直至取样能溶于10倍95%乙醇(v/v,25℃)中透明为止。将醇解物冷却至220℃以下,停止搅拌依次加入邻苯二甲酸酐600kg、二羟甲基丙酸60kg、对甲苯磺酸钠15kg 和105kg二甲苯,搅拌升温至回流,回流1小时后测定初始酸值为140mg koh/g,升温至200-210℃保温回流1小时,持续升温至210-220℃,维持酯化。酯化回流8h后,降温至200℃以下加入二甲苯285kg,继续降温至160℃以下加入醋酸仲丁酯210kg,过滤得到超支化树脂a。
50.实施例2
51.超支化树脂b:称取豆油1074kg入釜,开动搅拌和热油升温至200℃加入氢氧化锂0.24kg和季戊四醇267kg,再升温至240
±
5℃维持醇解,直至取样能溶于10倍95%乙醇(v/v,25℃)中透明为止。将醇解物冷却至220℃以下,停止搅拌依次加入石油树脂513kg、邻苯二甲酸酐471kg、二羟甲基丙酸60kg、对甲苯磺酸钠15kg和105kg二甲苯,搅拌升温至回流,回流1小时后测定初始酸值为135mg koh/g,升温至200-210℃保温回流1小时,持续升温至210-220℃,维持酯化。酯化回流8h后,降温至200℃以下加入二甲苯285kg,继续降温至 160℃以下加入醋酸仲丁酯210kg,过滤得到超支化树脂b。
52.对比例1
53.常规醇酸树脂:称取豆油1074kg入釜,开动搅拌和热油升温至200℃加入氢氧化锂0.24kg和季戊四醇327kg,再升温至240
±
5℃维持醇解,直至取样能溶于10倍95%乙醇(v/v,25℃)中透明为止。将醇解物冷却至220℃以下,停止搅拌依次加入石油树脂528kg、邻苯二甲酸酐471kg和105kg二甲苯,搅拌升温至回流,回流1小时后测定初始酸值为130mg koh/g,升温至200-210℃保温回流1小时,持续升温至210-220℃,维持酯化。酯化回流8后,降温至200℃以下加入二甲苯285kg,继续降温至160℃以下加入醋酸仲丁酯210kg,过滤得到常规醇酸树脂。
54.按照测试标准,对实施例1、实施例2和对比例1进行酸值、粘度、固含测试,数据如表1所示。
55.表1实施例1、实施例2、对比例1的测试结果
56.项目实施例1实施例2对比例1固体酸值/mgkoh/g20.519.811.4粘度(格式管粘度计)/s293038不挥发分/%80.480.179.8
57.实施例3
58.所述第一涂料:称取作为超支化防腐涂料的超支化树脂a220.5kg,二甲苯 121kg,混合并搅拌均匀。在搅拌的状态下,依次加入,作为防沉剂的微化酰胺蜡粉1.96kg和有机膨润土5.88kg,作为颜料的铁蓝0.49kg、炭黑2.94kg和钛白粉39.2kg,作为填料的磷铁微粉588kg,搅拌混合均匀,用砂磨机分散至细度50μm以下转入调漆缸中。加入作为流平剂的硅油液1kg,作为抗结皮剂的丁酮肟3kg,补足剩余的二甲苯16kg。搅拌分散30min,检验合格后过滤包装。
59.所述第二涂料:自生产的异氰酸酯类固化剂的tdi三聚固化剂,不需额外溶剂稀释,直接包装备用。
60.所述第一涂料与所述第二涂料按质量比a:b=12:1混合,搅拌均匀使用。
61.实施例4
62.所述第一涂料:称取作为超支化防腐涂料的超支化树脂b 220.5kg,二甲苯 121kg,混合并搅拌均匀。在搅拌的状态下,依次加入,作为防沉剂的微化酰胺蜡粉1.96kg和有机膨润土5.88kg,作为颜料的铁蓝0.49kg、炭黑2.94kg和钛白粉39.2kg,作为填料的磷铁微粉588kg,搅拌混合均匀,用砂磨机分散至细度 50μm以下转入调漆缸中。加入作为流平剂的硅油液1kg,作为抗结皮剂的丁酮肟3kg,补足剩余的二甲苯16kg。搅拌分散30min,检验合格后过滤包装。
63.所述第二涂料:自生产的异氰酸酯类固化剂的tdi三聚固化剂,不需额外溶剂稀释,直接包装备用。
64.所述第一涂料与所述第二涂料按质量比a:b=12:1混合,搅拌均匀使用。
65.对比例2
66.所述第一涂料:称取作为常规防腐涂料的常规醇酸树脂220.5kg,二甲苯 121kg,混合并搅拌均匀。在搅拌的状态下,依次加入,作为防沉剂的微化酰胺蜡粉1.96kg和有机膨润土5.88kg,作为颜料的铁蓝0.49kg、炭黑2.94kg和钛白粉39.2kg,作为填料的磷铁微粉588kg,搅拌混合均匀,用砂磨机分散至细度 50μm以下转入调漆缸中。加入作为流平剂的硅油液1kg,作为抗结皮剂的丁酮肟3kg,补足剩余的二甲苯16kg。搅拌分散30min,检验合格后过滤包装。
67.所述第二涂料:自生产的异氰酸酯类固化剂的tdi三聚固化剂,不需额外溶剂稀释,直接包装备用。
68.所述第一涂料与所述第二涂料按质量比a:b=12:1混合,搅拌均匀使用。
69.实施例5
70.所述第一涂料:称取作为超支化防腐涂料的超支化树脂a220.5kg,二甲苯 139kg,混合并搅拌均匀。在搅拌的状态下,依次加入,作为防沉剂的微化酰胺蜡粉1.96kg和有机膨润土5.88kg,作为颜料的氧化铁红1.96kg、炭黑2.94kg和钛白粉39.2kg,作为填料的磷铁微
粉98kg和重质碳酸钙470kg,搅拌混合均匀,用砂磨机分散至细度50μm以下转入调漆缸中。加入作为流平剂的硅油液1kg,作为抗结皮剂的丁酮肟3kg,补足剩余的二甲苯16kg。搅拌分散30min,检验合格后过滤包装。
71.所述第二涂料:自生产的异氰酸酯类固化剂的tdi三聚固化剂,不需额外溶剂稀释,直接包装备用。
72.所述第一涂料与所述第二涂料按质量比a:b=12:1混合,搅拌均匀使用。
73.实施例6
74.所述第一涂料:称取作为超支化防腐涂料的超支化树脂b 220.5kg,二甲苯 139kg,混合并搅拌均匀。在搅拌的状态下,依次加入,作为防沉剂的微化酰胺蜡粉1.96kg和有机膨润土5.88kg,作为颜料的氧化铁红1.96kg、炭黑2.94kg和钛白粉39.2kg,作为填料的磷铁微粉98kg和重质碳酸钙470kg,搅拌混合均匀,用砂磨机分散至细度50μm以下转入调漆缸中。加入作为流平剂的硅油液1kg,作为抗结皮剂的丁酮肟3kg,补足剩余的二甲苯16kg。搅拌分散30min,检验合格后过滤包装。
75.所述第二涂料:自生产的异氰酸酯类固化剂的tdi三聚固化剂,不需额外溶剂稀释,直接包装备用。
76.所述第一涂料与所述第二涂料按质量比a:b=12:1混合,搅拌均匀使用。
77.对比例3
78.所述第一涂料:称取作为超支化防腐涂料的常规醇酸树脂220.5kg,二甲苯 139kg,混合并搅拌均匀。在搅拌的状态下,依次加入,作为防沉剂的微化酰胺蜡粉1.96kg和有机膨润土5.88kg,作为颜料的氧化铁红1.96kg、炭黑2.94kg和钛白粉39.2kg,作为填料的磷铁微粉98kg和重质碳酸钙470kg,搅拌混合均匀,用砂磨机分散至细度50μm以下转入调漆缸中。加入作为流平剂的硅油液1kg,作为抗结皮剂的丁酮肟3kg,补足剩余的二甲苯16kg。搅拌分散30min,检验合格后过滤包装。
79.所述第二涂料:自生产的异氰酸酯类固化剂的tdi三聚固化剂,不需额外溶剂稀释,直接包装备用。
80.所述第一涂料与所述第二涂料按质量比a:b=12:1混合,搅拌均匀使用。
81.本发明超支化防腐涂料,产品按gb/t3186之规定取样,引hg/t3668-2009 中ⅱ型3类有机富锌底漆标准(锌含量项目除外)如表2,对漆料进行检测。
82.表2hg/t3668-2009中ⅱ型3类技术指标
[0083][0084]
依据以上标准,对实施例3-6、对比例2-3样品进行检验,检验结果如表3 所示。
[0085]
表3实施例3-6、对比例2-3样品检验结果
[0086]
[0087][0088]
本发明不是富锌底漆,所以无锌含量检测标准。实施例3-6的检验结果均达到或超过hg/t3668-2009中ⅱ型3类标准,而对比例2和对比例3由于树脂的粘度较高,施工性和漆膜外观不达标。
[0089]
本发明按照gb/t 1731-1993的规定对实施例3-6,对比例2-3做柔韧性测试。
[0090]
表4实施例3-6,对比例2-3样品柔韧性的测试结果
[0091]
项目实施例3实施例4实施例5实施例6对比例2对比例3柔韧性/级1级1级1级1级1级1级
[0092]
从表4中可看出,本发明超支化防腐涂料实施例3-6的柔韧性均能达到1 级,而对比例2和对比例3的树脂脆性大,柔韧性只能达到2级。
[0093]
本发明按照按gb/t 1733-1993中甲法的规定做耐水性测试,按照gb/t9274-1988甲法的规定做耐盐水性测试,其中盐水的浓度为3%nacl。
[0094]
表5实施例3-6,对比例2-3样品耐性的测试结果
[0095]
项目实施例3实施例4实施例5实施例6对比例2对比例3耐水性/h587556467502489453耐盐水性/h379432374359348363
[0096]
从表5中可看出,本发明超支化防腐涂料实施例3-6的耐水性超过400h,耐盐水性超过300h。
[0097]
本发明超支化防腐涂料按照按gb/t 23985-2009中的规定做voc含量的测定。
[0098]
表6实施例3-6,对比例2-3样品voc含量的测试结果
[0099]
项目实施例3实施例4实施例5实施例6对比例2对比例3voc含量/(g/l)380.2381.5381.5365.6428.5397.8
[0100]
从表6中可看出,本发明超支化防腐涂料实施例3-6的voc含量均小于 400g/l。
[0101]
本发明超支化防腐涂料按照按gb/t 6753.4-1998中的规定做粘度的测定。
[0102]
表7实施例3-6,对比例2-3样品粘度的测试结果
[0103]
项目实施例3实施例4实施例5实施例6对比例2对比例3粘度(iso6号)/s8695107112153164
[0104]
从表7中可看出,本发明超支化防腐涂料实施例3-6的粘度小于120s,而对比例2和对比例3的粘度较大。
[0105]
本发明超支化防腐涂料施工参考:
[0106]
(1)喷涂前,请务必做好工件清洗等前处理工序,要保持工件无油无锈、干净干燥。请将a组分和b组分按规定比例混合后搅拌均匀,用超支化防腐涂料专用稀释剂作为稀释剂,稀释比例约为原漆的10-20%,调整施工粘度为 25-35s,放置10min后涂装。
[0107]
(2)涂装方法采用高压无气喷涂机喷涂施工,喷涂压力:0.4-0.8mpa枪距: 0.2-0.4m多次喷涂厚度为70-100μm。
[0108]
(3)施工过程中,若漆液有粗粒可用120目滤布进过滤。
[0109]
本发明的超支化防腐涂料固化条件为常温自然固化,固化温度在5℃以上,能满足实际需要,实现本发明目的。
[0110]
以上所揭露的仅为本发明一种超支化防腐涂料及其制备方法较佳实施例而已,当然不能以此来限定本发明之权利范围,本领域普通技术人员可以理解实现上述实施例的全部或部分流程,并依本发明权利要求所作的等同变化,仍属于发明所涵盖的范围。