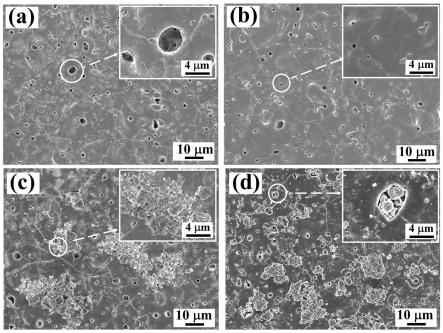
1.本发明属于镁合金表面处理技术领域,具体涉及一种低孔隙率低厚度镁合金复合涂层及其制备方法和应用。
背景技术:2.镁合金具有高强度重量比、可生物降解性能好、阻尼能力强等优点,被广泛应用于运输和医疗器械等领域。如果用镁合金代替钢或铝合金,每辆车的总重量将减少约15%,从而导致燃料利用率减少,温室气体排放显著减少。然而,由于镁合金的化学活性较高,很容易被腐蚀,因此在取代钢或铝方面并不能发挥预期的作用。因此,为了提高镁合金在腐蚀环境中的长期耐腐蚀性能,对其进行表面处理是一种简便且有效的途径。
3.对镁合金表面进行表面处理的方式有很多,其中,等离子体电解氧化(peo)(也叫微弧氧化)是一种对环境友好的处理方式,具有制备工艺简单、成本低以及与镁合金结合力强等优点,但因其特殊的制备过程,peo涂层的表面常存在一些微孔和微裂纹,导致外界腐蚀性物质通过微孔或微裂纹进入而腐蚀镁合金,极大地影响了peo涂层的长期耐腐蚀性能。
4.为解决上述问题,有研究者在peo涂层上结合有机涂层或其它涂层用于封闭peo涂层的微孔和微裂纹,但是,这种方法显著增加了涂层的厚度,一定程度上限制了其在微型仪器防腐、精密仪器防腐等方向中的应用。如公开号为cn103085379a的专利公开了一种镁合金表面微弧氧化纳米自组装金属陶瓷涂层及制备方法,在镁合金基体表面形成微弧氧化陶瓷涂层后再在该陶瓷层表面依次覆盖自组装纳米膜和无机金属陶瓷涂层,实现对微弧氧化膜的微孔的封闭处理,但其中自组装纳米膜厚度为0.1-10μm,无机金属陶瓷涂层厚度为10-50μm,大大增加了整体涂层的厚度。
5.因此,亟需开发一种即可减少镁合金表面peo涂层的微孔或微裂纹、又不额外增加涂层厚度的方法,以进一步扩大镁合金的应用范围。
技术实现要素:6.针对现有技术中在减少镁合金表面peo涂层的微孔或微裂纹时易增加涂层厚度的问题,本发明提出一种低孔隙率低厚度镁合金复合涂层及其制备方法和应用。
7.为了达到上述目的,本发明的技术方案是这样实现的:一种低孔隙率低厚度镁合金复合涂层的制备方法,步骤如下:(1)镁合金预处理;(2)将步骤(1)预处理的镁合金放入等离子体电解氧化涂层电解液,以预处理的镁合金为阳极、不锈钢电极为阴极进行等离子体电解氧化处理,得到等离子体电解氧化涂层peo;(3)在丙酮存在的条件下,将1-甲基咪唑和溴十一酸反应,得到[mcim]br,然后在蒸馏水存在的条件下,将 [mcim]br和双三氟甲基磺酰亚胺锂反应,得到[mcim][ntf2];(4)在无水乙醇和乙二醇存在的条件下,将硅酸钠、六水合硝酸镁和氢氧化钠反
应,得到硅酸镁纳米管msnts;(5)在二氯甲烷存在的条件下,将硅酸镁纳米管msnts与[mcim][ntf2]反应,得到msnts@[mcim][ntf2]材料;(6)将步骤(2)中的peo进行真空处理,再加入步骤(5)中的msnts@[mcim][ntf2]的无水乙醇溶液,继续真空处理,得到peo/msnts@[mcim][ntf2]复合涂层。
[0008]
优选地,所述步骤(1)中镁合金预处理具体为:将镁合金依次用240目、600目、1500目和3000目砂纸进行打磨,然后用金刚石抛光膏进行抛光处理,最后依次用蒸馏水和无水乙醇清洗,得到预处理的镁合金。
[0009]
优选地,所述步骤(2)中等离子体电解氧化电解液的成分为硅酸钠12-18g/l,氢氧化钾8-12g/l和氟化钾3-8g/l;等离子体电解氧化处理的条件为处理时间5-25min、处理温度30-50℃、电压260-350v、电流40-70ma
·
cm-2
、占空比20-30%、频率450-600hz。
[0010]
优选地,所述步骤(3)中1-甲基咪唑和溴十一酸在20-60℃条件下反应12-48h,其中1-甲基咪唑和溴十一酸的摩尔比为1:1;[mcim]br和双三氟甲基磺酰亚胺锂在20-60℃条件下反应8-20h,其中[mcim]br和双三氟甲基磺酰亚胺锂的摩尔比为1:1.2。
[0011]
优选地,所述步骤(4)中硅酸钠、六水合硝酸镁和氢氧化钠反应具体为:将硅酸钠、六水合硝酸镁和氢氧化钠混合后在室温下搅拌0.5-3h,再将所得溶液转移到聚四氟乙烯水热高压釜中,在120-300℃条件下反应12-48h,其中硅酸钠、六水合硝酸镁和氢氧化钠的摩尔比为1:1:25。
[0012]
优选地,所述步骤(5)中将硅酸镁纳米管msnts与[mcim][ntf2]在室温条件下反应12-48h,其中[mcim][ntf2]和msnts的质量比为45:1。
[0013]
优选地,所述步骤(6)中真空处理的时间为0.5-3h;继续真空处理的时间为0.5-1.5h。
[0014]
虽然直接将缓蚀剂封装在peo涂层中也可赋予涂层一定的自愈性能,但在长时间浸泡的海洋环境下,缓蚀剂容易提前泄露,导致其不能很好地发挥自愈性能。为此,本发明采用接枝的方法,将缓蚀剂mn接枝在msnts上,再将其封装在peo涂层中,可有效解决缓蚀剂提前泄露的问题,不仅能更好地发挥缓蚀剂的自愈性能,同时也不额外增加涂层的厚度,还降低了涂层的孔隙率,提高了涂层整体的致密程度。
[0015]
本发明还包括利用上述方法制备的低孔隙率低厚度镁合金复合涂层,所述低孔隙率低厚度镁合金复合涂层的孔隙率为0.35%、腐蚀电流密度为3.05
×
10-10a·
cm-2
,未额外增加等离子体电解氧化涂层的厚度。
[0016]
本发明还包括上述低孔隙率低厚度镁合金复合涂层在镁合金表面防腐中的应用。
[0017]
本发明还包括上述低孔隙率低厚度镁合金复合涂层在液态环境下镁合金表面防腐中的应用。
[0018]
本发明的有益效果:1、本发明通过将特定的缓蚀剂与硅酸镁纳米管接枝后对等离子体电解氧化(peo)涂层进行封孔处理,得到一种低孔隙率低厚度镁合金复合涂层,该复合涂层的表面均匀平整,原peo涂层表面的微孔被均匀填充,复合涂层表面的孔隙率为0.35%、腐蚀电流密度为3.05
×
10-10a·
cm-2
,且未额外增加peo涂层的厚度,如以厚度为9.8
ꢀµ
m的peo涂层为基础进一步制得的该复合涂层,其厚度依然为9.8
ꢀµ
m。
[0019]
2、本发明通过将特定的缓蚀剂接枝在硅酸镁纳米管表面再封装到peo涂层中,不仅阻止了腐蚀介质经peo涂层的孔洞进入膜层内部而造成膜层腐蚀,还有效避免了缓蚀剂直接封装在peo涂层中提前泄露的问题,在镁合金用于海洋等液态环境时,镁合金表面涂层中的缓蚀剂不易在液体介质的侵蚀下提前泄露,而是持续保留在涂层中发挥其耐腐蚀、自修复等的作用,因而该复合涂层具备优异的自修复性能,提高了镁合金在液态环境下的长期防腐性能。
[0020]
3、本发明是将缓蚀剂与硅酸镁纳米管接枝后直接封装到等离子体电解氧化(peo)涂层的微孔中,在填充peo涂层表面微孔的同时,并不额外增加涂层的厚度,本发明复合涂层的厚度与peo涂层的厚度一致,避免了常规技术中封孔peo涂层后整体涂层过厚而导致的材料过度浪费、与peo涂层的结合力不强以及不满足轻质量要求,一定程度上拓展了该复合涂层在微型仪器防腐、精密仪器防腐等方向中的应用。
[0021]
4、本发明的低孔隙率低厚度镁合金复合涂层的制备方法操作简便,所得复合涂层具有较低的孔隙率、厚度和腐蚀电流密度,且具备优异的自修复性能,为提高镁合金涂层的功能化应用提供了一种新的、简单的途径,具有较好的应用前景。
附图说明
[0022]
为了更清楚地说明本发明实施例或现有技术中的技术方案,下面将对实施例或现有技术描述中所需要使用的附图作简单地介绍,显而易见地,下面描述中的附图仅仅是本发明的一些实施例,对于本领域普通技术人员来讲,在不付出创造性劳动的前提下,还可以根据这些附图获得其他的附图。
[0023]
图1为硅酸镁纳米管(msnts)和[mcim][ntf2]的接枝反应示意图。
[0024]
图2为镁合金表面不同涂层的sem图,其中,(a)为peo涂层,(b)为peo/mn复合涂层,(c)为peo/msnts复合涂层,(d)为实施例1的peo/msnts@mn复合涂层。
[0025]
图3为不同涂层的截面sem图及能谱图,其中,(a)为peo涂层的截面sem图,(b)为peo涂层的能谱图,(c)为实施例1的peo/msnts@mn复合涂层的截面sem图,(d)为实施例1的peo/msnts@mn复合涂层的能谱图。
[0026]
图4为镁合金表面不同涂层的孔隙率对比分析图,其中(a)为peo涂层,(b)为peo/mn复合涂层,(c)为peo/msnts复合涂层,(d)为实施例1的peo/msnts@mn复合涂层,(e)为各涂层的孔隙率数值对比。
[0027]
图5为az31b镁合金、peo涂层、peo/mn复合涂层、peo/msnts复合涂层和实施例1的peo/msnts@mn复合涂层在3.5 wt.% nacl溶液中的动电位极化曲线。
[0028]
图6为az31b镁合金、peo涂层、peo/mn复合涂层、peo/msnts复合涂层和实施例1的peo/msnts@mn复合涂层的自愈性能测试图。
具体实施方式
[0029]
下面将结合本发明实施例中的附图,对本发明实施例中的技术方案进行清楚、完整地描述,显然,所描述的实施例仅仅是本发明一部分实施例,而不是全部的实施例。基于本发明中的实施例,本领域普通技术人员在没有付出创造性劳动前提下所获得的所有其他实施例,都属于本发明保护的范围。
[0030]
本发明的实施例中所使用的实验方法如无特殊说明,均为常规方法。
[0031]
本发明的实施例中所用的材料、试剂等,如无特殊说明,均可从商业途径得到。
[0032]
本发明所合成的羟基化硅酸镁纳米管(msnts),其管上自带羟基;所合成的[mcim][ntf2]缓蚀剂,其阳离子带羧基基团;如图1所示,在二氯甲烷试剂存在的情况下,[mcim][ntf2]缓蚀剂可以接枝在羟基化硅酸镁纳米管上。
[0033]
实施例1本实施例提供一种低孔隙率低厚度镁合金复合涂层的制备方法,步骤如下:(1)镁合金的预处理本实施例以az31b镁合金作为基材,其规格为1.5cm
×
1.5cm
×
0.6cm。每次实验前,使用环氧树脂对az31b镁合金样品进行涂敷,仅保留一个1.5cm
×
1.5cm的工作面,将az31b镁合金样品的工作面依次用240目、600目、1500目和3000目砂纸打磨,然后用w3.5金刚石抛光膏(veiyee,型号:pg)进行抛光,最后依次用蒸馏水和无水乙醇超声清洗10min,得到预处理后的镁合金。
[0034]
(2)等离子体电解氧化涂层(peo)的制备采用脉冲双极性电源(ys9000ddb-70020,上海),将不锈钢电极作为阴极、将步骤(1)预处理后的镁合金样品作为阳极放入等离子体电解氧化电解液中,进行等离子体电解氧化处理15min,将处理后的样品用蒸馏水超声清洗10min,然后室温下干燥,即得等离子体电解氧化涂层(peo)。
[0035]
其中,等离子体电解氧化电解液采用硅酸盐电解液,配制过程为:称取15g硅酸钠、10g氢氧化钾和5g氟化钾于烧杯中,加入1l蒸馏水,搅拌溶解,即得等离子体电解氧化电解液。等离子体电解氧化处理的参数为:电压为300v,电流为50ma/cm2,占空比为20%,频率为500hz,整个等离子体电解氧化过程中等离子体电解氧化电解液的温度大约为40℃,全程使用磁子对电解液进行搅拌,避免电解液局部温度过高。
[0036]
(3)1-甲基-3-(羧基十一烷基)咪唑双(三氟甲基磺酰基)酰亚胺(即[mcim][ntf2],简称mn)缓蚀剂的制备称取0.82g的1-甲基咪唑和2.65g的溴十一酸于100ml的圆底烧瓶中,向圆底烧瓶中加入40ml丙酮,在40℃条件下反应24小时。反应结束后,用乙酸乙酯洗涤粗反应混合物,过滤得到纯化合物[mcim]br(白色固体化合物)。然后,取3.46g的[mcim]br和3.16g的双三氟甲基磺酰亚胺锂于100ml的圆底烧瓶中,向圆底烧瓶中加入40ml蒸馏水使其溶解,在40℃条件下反应10小时,反应结束后用蒸馏水对其进行洗涤,得到淡黄色液体样的1-甲基-3-(羧基十一烷基)咪唑双(三氟甲基磺酰基)酰亚胺,命名为[mcim][ntf2],简称mn。
[0037]
(4)硅酸镁纳米管(即msnts)的制备采用水热法制备硅酸镁纳米管(msnts)。称取0.305g的硅酸钠、0.64g的六水合硝酸镁和0.2g的氢氧化钠溶解在60ml的无水乙醇和乙二醇(体积比5:1)的混合物中,以400rpm在室温下搅拌1h。然后,将所得溶液转移到聚四氟乙烯(ptfe)水热高压釜中,并在210℃下反应24h,反应结束后,通过离心(10000rpm,5min)收集产物,用无水乙醇洗涤3次,最后在60℃下干燥24h,即得硅酸镁纳米管(msnts)。
[0038]
(5)msnts@mn接枝材料的制备称取0.3g msnts加入到50ml二氯甲烷溶液中,超声处理20min;然后,向该溶液中
加入1.35g[mcim][ntf2],在室温下搅拌24h;通过离心(10000rpm,5min)回收沉淀,用无水乙醇溶液洗涤几次,最后在60℃条件下真空干燥24h,即得到msnts@mn接枝材料。
[0039]
(6)peo/msnts@mn复合涂层的制备将步骤(2)具有等离子体电解氧化涂层的样品放入抽滤瓶中,使用循环水真空泵真空处理2h,随后,将300mg的msnts@mn溶于无水乙醇溶液,并加入到真空过滤瓶中进行真空处理60min,然后取出干燥,得到peo/msnts@mn复合涂层,即为本发明的低孔隙率低厚度镁合金复合涂层。
[0040]
实施例2一种低孔隙率低厚度镁合金复合涂层及其制备方法,步骤如下:步骤(1)-(4)同实施例1;(5)msnts@mn接枝材料的制备称取0.3g msnts加入到50ml二氯甲烷溶液中,超声处理20min;然后,向该溶液中加入1.35g[mcim][ntf2],在室温下搅拌24h;通过离心(10000rpm,5min)回收沉淀,用无水乙醇溶液洗涤几次,最后在60℃条件下真空干燥24h,即得到msnts@mn接枝材料。
[0041]
(6)peo/msnts@mn复合涂层的制备将步骤(2)具有等离子体电解氧化涂层的样品放入抽滤瓶中,使用循环水真空泵真空处理0.5h,随后,将200mg的msnts@mn溶于无水乙醇溶液,并加入到真空过滤瓶中进行真空处理30min,然后取出干燥,得到peo/msnts@mn复合涂层,即为本发明的低孔隙率低厚度镁合金复合涂层。
[0042]
实施例3一种低孔隙率低厚度镁合金复合涂层及其制备方法,步骤如下:步骤(1)-(4)同实施例1;(5)msnts@mn接枝材料的制备称取0.3g msnts加入到50ml二氯甲烷溶液中,超声处理20min;然后,向该溶液中加入1.35g[mcim][ntf2],在室温下搅拌24h;通过离心(10000rpm,5min)回收沉淀,用无水乙醇溶液洗涤几次,最后在60℃条件下真空干燥24h,即得到msnts@mn接枝材料。
[0043]
(6)peo/msnts@mn复合涂层的制备将步骤(2)具有等离子体电解氧化涂层的样品放入抽滤瓶中,使用循环水真空泵真空处理3h,随后,将400mg的msnts@mn溶于无水乙醇溶液,并加入到真空过滤瓶中进行真空处理90min,然后取出干燥,得到peo/msnts@mn复合涂层,即为本发明的低孔隙率低厚度镁合金复合涂层。
[0044]
对比例1参照实施例1制备等离子体电解氧化涂层(peo)的步骤,制得peo涂层。
[0045]
对比例2参照实施例1的制备方法制得peo涂层和mn,然后将具有peo涂层的样品放入抽滤瓶中,使用循环水真空泵真空处理2h,随后,将2.0g的mn溶于无水乙醇溶液中,然后加入到真空过滤瓶中,真空处理60min后取出,经干燥,即得到peo/mn复合涂层。
[0046]
对比例3参照实施例1的制备方法制得peo涂层和msnts,然后将具有peo涂层的样品放入抽
滤瓶中,使用循环水真空泵真空处理2h,随后,将300mg的msnts溶于无水乙醇溶液中,然后加入到真空过滤瓶中,真空处理60min后取出,经干燥,即得到peo/msnts复合涂层。
[0047]
对比效果例为了验证本发明低孔隙率低厚度镁合金复合涂层的各项性能,将对比例1的peo涂层、对比例2的peo/mn复合涂层和对比例3的peo/msnts复合涂层,与实施例1的低孔隙率低厚度镁合金复合涂层(peo/msnts@mn复合涂层)进行对比。
[0048]
图2为在镁合金表面制备的不同涂层的sem图,其中(a)为peo涂层,(b)为peo/mn复合涂层,(c)为peo/msnts复合涂层,(d)为实施例1的peo/msnts@mn复合涂层。通过图2的sem表征表明,peo涂层的表面整体均匀平整,但可以很明显地看到其表面存在一定量的微孔,这是不可避免的(图2a);经[mcim][ntf2](即mn)缓蚀剂封孔处理后的peo/mn复合涂层的表面更光滑,涂层表面更加致密(图2b);经过msnts密封的peo/msnts复合涂层中,一些微分散的msnts进入peo涂层的微孔,另一些则聚集在表面,与纯peo涂层的表面相比,微孔隙部分消失,但是,由于msnt的体积较大,一些尺寸较小的微孔不能被msnt填充(图2c);但是,实施例1中经过msnts@mn材料密封的peo/msnts@mn复合涂层具有更好的封孔效果,更小尺寸的微孔均被密封(图2d)。
[0049]
图3给出了peo涂层和实施例1中peo/msnts@mn复合涂层的截面sem图以及对应的能谱图。如图3所示,可观察到peo涂层的涂层厚度为9.8
ꢀµ
m,在填充本发明的msnts@mn后,涂层的厚度并没有改变,依然为9.8
ꢀµ
m,说明本发明的msnts@mn被很好地封装在peo涂层的微孔中;通过能谱数据可看到,出现了msnts@mn的特征元素:c元素、n元素和s元素,进一步说明msnts@mn材料的成功封装。由此表明,通过将缓蚀剂mn接枝在msnts的表面,再真空负载到peo涂层的微孔中,不仅可以封闭peo涂层的微孔,还可以控制涂层的厚度。
[0050]
利用image j软件对各涂层的孔隙率进行测量,将原始sem图像中的多孔区域转换为黑色,并将其他区域转换为白色,结果如图4所示,其中,(a)为peo涂层,(b)为peo/mn复合涂层,(c)为peo/msnts复合涂层,(d)为peo/msnts@mn复合涂层,(e)为各涂层的孔隙率数据对比。从图4可看出,对peo涂层进行后处理之后,peo涂层的孔隙率均有所降低,其中peo/msnts@mn的孔隙率最小,为0.35%,表明本发明msnts@mn的填充性能最好。
[0051]
使用电化学方法对az31b镁合金、peo涂层、peo/mn复合涂层、peo/msnts复合涂层和实施例1 peo/msnts@mn复合涂层在3.5wt.% nacl溶液(模拟液态海洋环境)中的耐蚀性进行测试,动电位极化曲线如图5所示。实施例1的peo/msnts@mn复合涂层的腐蚀电流密度为3.05
×
10-10a·
cm-2
,相比于az31b镁合金的腐蚀电流密度(1.17
×
10-5a·
cm-2
)降低了5个数量级,相比于peo涂层的腐蚀电流密度(1.06
×
10
−8a/cm2)降低了2个数量级,说明peo/msnts@mn复合涂层极大地提高了复合涂层的缓蚀效率,其在液态环境下的耐蚀性最好。
[0052]
图6给出了az31b镁合金、peo涂层、peo/mn复合涂层、peo/msnts复合涂层和实施例1 peo/msnts@mn复合涂层的自愈性能测试图。从图6中可直观的看出:在peo/msnts复合涂层样品中填充的msnts不具有自愈特性,其防腐性能的增强是由于部分孔隙被填充。peo/mn复合涂层样品中,[mcim][ntf2](即mn)缓蚀剂除对peo涂层孔隙有一定填充效果外,还可积极阻断腐蚀物质,对镁合金提供保护,但是,填充在peo涂层孔隙中的[mcim][ntf2]在初始浸泡阶段很容易泄漏,在长期浸泡过程中并没有发挥应有的自愈作用。但从实施例1 peo/msnts@mn复合涂层样品中可以看到,在3.5wt.% nacl溶液中浸泡14天后,样品的划痕处并
没有大面积的腐蚀现象,仅观察到轻微的腐蚀区域,表明本发明将[mcim][ntf2]接枝在msnts上,成功解决了在液态环境下使用时缓蚀剂[mcim][ntf2] 提前泄露的问题,该复合涂层具有优良的自愈性能。
[0053]
综上,一系列的对比结果表明本发明制备的peo/msnts@mn复合涂层不仅表面均匀平整、具有极低的孔隙率,还具备优异的自修复性能和较低的腐蚀电流密度,能够有效提高镁合金的长期耐蚀性能,且其中的缓蚀剂不易在液体介质的侵蚀下提前泄露,能较好地应用于海洋等液态环境。
[0054]
以上所述仅为本发明的较佳实施例而已,并不用以限制本发明,凡在本发明的精神和原则之内,所作的任何修改、等同替换、改进等,均应包含在本发明的保护范围之内。