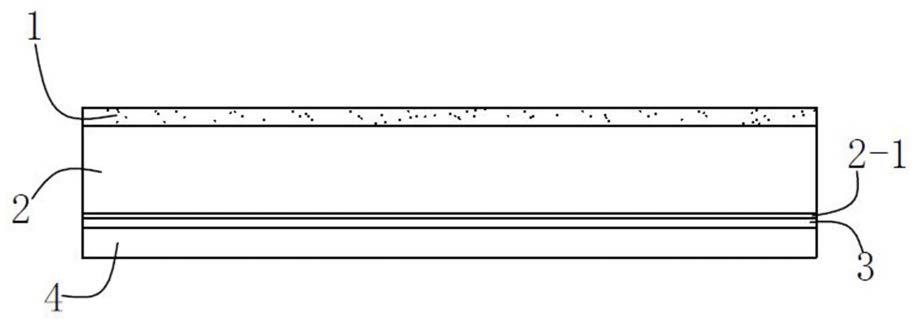
1.本实用新型涉及一种汽车用的保护膜,特别是一种汽车漆面保护膜。
背景技术:2.汽车漆面保护膜,也被称为“隐形车衣”,是贴在汽车车身表面的一层透明保护膜,能够有效的防止刮蹭和沙粒的击打,还隔绝了车漆与空气的接触,可以防止酸雨,昆虫,鸟粪等对车身漆面的腐蚀。主要目的在于撕除之后,汽车的原厂车漆仍能光亮如新。
3.现有汽车漆面保护膜一般为三层结构,依次为修复涂层、热塑性聚氨酯基材层和压敏胶层。修复涂层处于产品的最外层,起到划痕修复、阻隔脏污及紫外防护等保护作用。
4.为保证汽车漆面保护膜在汽车车身上的粘贴强度,现汽车漆面保护膜产品中常采用的压敏胶粘力较大,导致汽车漆面保护膜粘贴于车身上之后,剥离的过程中常会发生胶粘剂残余物残留在车身漆面上的情况。另外,采用稀释剂或溶剂来剥除留在车身上的压敏胶残余物,会对车身漆面造成不同程度上的损伤。
5.对此,申请人提出本实用新型产品。
技术实现要素:6.本实用新型的目的是为了解决上述现有技术的不足而提供一种基材与压敏胶之间具备高粘接强度的汽车漆面保护膜。
7.为了实现上述目的,本实用新型所设计的一种汽车漆面保护膜,包括依次复合的修复涂层、热塑性聚氨酯基材层、压敏胶层和离型膜层,所述热塑性聚氨酯基材层上指向压敏胶层的单侧表面形成线型的凸起部,且呈纵横交错的网格状分布,所述压敏胶层的厚度与凸起部的凸起高度的比值为2~3.5∶1。
8.上述汽车漆面保护膜因基材表面的线型的凸起部,压敏胶液在该表面进行涂布、固化后,两者的粘接强度能够得到进一步的大幅提高,进而使用中在将上述汽车漆面保护膜从车身漆面上剥离时,基材与压敏胶两者的整体性会更好,就不易发生胶粘剂残余物残留在车身漆面上的情况。
9.优选的,所述凸起部的凸起高度为3μm~15μm,且凸起宽度10μm~50μm;所述压敏胶层为丙烯酸压敏胶层或聚氨酯压敏胶层,厚度为6μm~50μm,可见光透过率可以控制在90%以上。
10.上述优选方案中将所述凸起部的凸起高度限制在15μm以下,同时又将凸起宽度限制在50μm以下,此尺寸大小的凸起部经过压敏胶覆盖后肉眼无法直接观察到,即不会影响到保护膜整体的外观,进而就避免了因凸起部可能会给保护膜使用造成的负面影响,例如外观不被市场所接受。
11.优选的,所述修复涂层为聚氨酯涂层,厚度为5μm~25μm,产生微小划痕后,在加热条件下可以自我修复,并且能够在所述聚氨酯涂层内再添加紫外线吸收剂和纳米陶瓷粉末,起到阻隔紫外线,防止车漆老化和提升涂层硬度的功能。
12.上述紫外线吸收剂优选稳定性好的锐钛矿型纳米tio2粉末和金红石型纳米tio2粉末中的至少一种。更优选锐钛矿型纳米tio2粉末和金红石型纳米tio2粉末的混合物,锐钛矿型纳米tio2粉末和金红石型纳米tio2粉末对紫外线具有较强的吸收和散射作用,紫外光透过率低,且随着时间延长也比较稳定。因此添加锐钛矿型纳米tio2粉末和金红石型纳米tio2粉末能更有效的提高涂层抗uv老化性能。
13.优选的,所述热塑性聚氨酯(tpu)基材层为脂肪族热塑性聚氨酯基材层,厚度为100μm~300μm。其表面硬度为80a~93a,可见光透过率能够达到90%以上,断裂伸长率能够达到300%以上,雾度能够控制在2%以下。
14.优选的,所述离型膜层为pet离型膜层,厚度为23μm~100μm。更优选为白色pet离型膜,雾度达到70%以上,离型力控制在20g/inch以内。
15.本实用新型得到的一种汽车漆面保护膜,相比较现有技术,其具备以下的优点:
16.1、本实用新型一种汽车漆面保护膜,其能够更为容易地粘贴至汽车车身上,以及再从汽车车身上完整剥离,整个过程中能够最大程度上避免发生“胶粘剂残余物残留在车身漆面上
”ꢀ
的情况。
17.2、本实用新型一种汽车漆面保护膜,其还具有更好的化学稳定性和热稳定性,因此延长了保护膜的使用寿命。
附图说明
18.图1是一种汽车漆面保护膜的层状结构示意图;
19.图2是热塑性聚氨酯基材层的表面结构示意图。
20.图中:修复涂层1、热塑性聚氨酯基材层2、凸起部2-1、压敏胶层3、离型膜层4。
具体实施方式
21.下面将结合本实用新型实施例中的附图,对本实用新型实施例中的技术方案进行清楚、完整地描述,显然,所描述的实施例仅仅是本实用新型一部分实施例,而不是全部的实施例。基于本实用新型中的实施例,本领域普通技术人员所获得的所有其他实施例,都属于本实用新型保护的范围。
22.实施例1:
23.如图1所示,作为本实用新型的一种实施方式,本实施例中提供的一种汽车漆面保护膜,包括依次复合的修复涂层1、热塑性聚氨酯基材层2、压敏胶层3和离型膜层4,所述热塑性聚氨酯基材层2上指向压敏胶层3的单侧表面形成线型的凸起部2-1,且呈纵横交错的网格状分布。
24.本实施例中所述修复涂层1的材质为聚氨酯,厚度为10μm,内含紫外线吸收剂和纳米陶瓷粉末,所述紫外线吸收剂选用锐钛矿型纳米tio2粉末和金红石型纳米tio2粉末的混合物,相对于聚氨酯100重量份,紫外线吸收剂和纳米陶瓷粉末2重量份,且锐钛矿型纳米tio2粉末、金红石型纳米tio2粉末与纳米陶瓷粉末的摩尔比为2∶2∶1。
25.本实施例中所述热塑性聚氨酯(tpu)基材层的材质为脂肪族热塑性聚氨酯,厚度为200μm。其表面的凸起部2-1的凸起高度为10μm,且凸起宽度为25μm;
26.本实施例中所述压敏胶层3的材质为丙烯酸压敏胶,厚度为25μm,可见光透过率在
90%以上。
27.本实施例中所述离型膜层4的材质为白色聚对苯二甲酸乙二醇酯(pet),厚度为55μm。
28.本实施例中一种汽车漆面保护膜的制备方法,如下:
29.a、修复涂层1的涂布液制备
30.将100份聚己内酯多元醇树脂、2份紫外线吸收剂和纳米陶瓷粉末混合物(锐钛矿型纳米tio2粉末、金红石型纳米tio2粉末与纳米陶瓷粉末的摩尔比为2∶2∶1)添加到150份乙酸乙酯中,最后添加20份异氰酸酯固化剂甲苯二异氰酸酯,充分搅拌30min,混合均匀以备用。
31.b、热塑性聚氨酯基材的制备
32.材料准备:包括按重量份组成的下列成分:异佛尔酮二异氰酸酯(ipdi)为80份、聚四氢呋喃醚二醇为20份、聚己内酯二醇为10份和扩链剂为5份。其中,扩链剂为六氟双酚a。
33.制备方法采用以下步骤:
34.s1.在110~120℃、0.1mpa条件下,将聚四氢呋喃醚二醇真空脱水1.5h~2h;
35.s2.取脱水后适量的聚四氢呋喃醚二醇、异佛尔酮二异氰酸酯(ipdi)和聚己内酯二醇加入到装有机械搅拌、冷凝回流装置、温度计的四口烧瓶中,升温至70℃,抽真空,充入氮气保护,持续反应1.5h~2h后,加入溶剂二甲基甲酰胺(dmf)调节固含量为60wt%,以降低体系粘度,促使反应充分进行;
36.s3.待测定预聚体中异氰酸酯基质量分数稳定后,逐渐升温至100℃,加入扩链剂,剧烈搅拌反应2h,真空脱气,将粘稠的产物趁热倒入铺有一层表面光滑的聚四氟乙烯薄膜的模具中,所述模具为40*40cm的玻璃板刻有深度为200μm的凹槽,要求所述聚四氟乙烯薄膜的表面预先形成线型的凹槽部,且呈纵横交错的网格状分布,所述凹槽部的槽深为10μm,槽宽为25μm,用辊压棒进行均匀辊压后,置于70℃烘箱中烘5天成膜,再常温下放置24h后即可得到热塑性聚氨酯薄膜,完成制备。
37.c、压敏胶层3的涂布
38.将压敏胶涂布液涂布在200μm tpu基材的一侧表面(凸起部2-1所在的表面)上,干燥条件110℃,2min,形成干胶25μm厚的压敏胶层3。然后将55μm白色pet离型膜复合在上述压敏胶层3上。
39.d、修复涂层1的涂布
40.在步骤c中tpu基材的另一侧表面涂布修复涂层1,固化条件120℃,2min,干燥后厚度为10μm,至此得到保护膜半成品。
41.e、熟化
42.将步骤d中的半成品放入50℃熟化室中,经过72h,即可得到保护膜。
43.实施例2:
44.作为本实用新型的第二种实施方式,本实施例中一种汽车漆面保护膜,其层状结构与实施例1相一致。
45.但是,本实施例中所述修复涂层1的材质为聚氨酯,厚度却为5μm,其同样内含紫外线吸收剂和纳米陶瓷粉末,所述紫外线吸收剂选用锐钛矿型纳米tio2粉末和金红石型纳米tio2粉末的混合物,相对于聚氨酯100重量份,紫外线吸收剂和纳米陶瓷粉末2重量份,且锐
钛矿型纳米tio2粉末、金红石型纳米tio2粉末与纳米陶瓷粉末的摩尔比为2∶2∶1。
46.本实施例中所述热塑性聚氨酯(tpu)基材层的材质为脂肪族热塑性聚氨酯,厚度却为100μm。其表面的凸起部2-1的凸起高度为3μm,且凸起宽度为10μm;
47.本实施例中所述压敏胶层3的材质为丙烯酸压敏胶,厚度却为6μm,可见光透过率在90%以上。
48.本实施例中所述离型膜层4的材质为白色聚对苯二甲酸乙二醇酯(pet),厚度却为23μm。
49.本实施例中一种汽车漆面保护膜的制备方法,其基本步骤与实施例1相一致。
50.但是,本实施例所提供一种汽车漆面保护膜的制备方法,其步骤b中所述模具为40*40cm的玻璃板刻有深度为100μm的凹槽,同样要求所述聚四氟乙烯薄膜的表面预先形成线型的凹槽部,且呈纵横交错的网格状分布,所述凹槽部的槽深为3μm,槽宽为10μm。
51.实施例3:
52.作为本实用新型的第三种实施方式,本实施例中一种汽车漆面保护膜,其层状结构与实施例1相一致。
53.但是,本实施例中所述修复涂层1的材质为聚氨酯,厚度却为25μm,其同样内含紫外线吸收剂和纳米陶瓷粉末,所述紫外线吸收剂选用锐钛矿型纳米tio2粉末和金红石型纳米tio2粉末的混合物,相对于聚氨酯100重量份,紫外线吸收剂和纳米陶瓷粉末2重量份,且锐钛矿型纳米tio2粉末、金红石型纳米tio2粉末与纳米陶瓷粉末的摩尔比为2∶2∶1。
54.本实施例中所述热塑性聚氨酯(tpu)基材层的材质为脂肪族热塑性聚氨酯,厚度却为300μm。其表面的凸起部2-1的凸起高度为15μm,且凸起宽度为50μm;
55.本实施例中所述压敏胶层3的材质为丙烯酸压敏胶,厚度却为50μm,可见光透过率在90%以上。
56.本实施例中所述离型膜层4的材质为白色聚对苯二甲酸乙二醇酯(pet),厚度却为100μm。
57.本实施例中一种汽车漆面保护膜的制备方法,其基本步骤与实施例1相一致。
58.但是,本实施例所提供一种汽车漆面保护膜的制备方法,其步骤b中所述模具为40*40cm的玻璃板刻有深度为300μm的凹槽,同样要求所述聚四氟乙烯薄膜的表面预先形成线型的凹槽部,且呈纵横交错的网格状分布,所述凹槽部的槽深为15μm,槽宽为50μm。
59.比较例1:
60.一种汽车漆面保护膜,包括依次复合的修复涂层1、热塑性聚氨酯基材层2、压敏胶层3和离型膜层4。
61.本比较例中所述修复涂层1的材质为聚氨酯,厚度为10μm,内含紫外线吸收剂和纳米陶瓷粉末,所述紫外线吸收剂选用锐钛矿型纳米tio2粉末和金红石型纳米tio2粉末的混合物,相对于聚氨酯100重量份,紫外线吸收剂和纳米陶瓷粉末2重量份,且锐钛矿型纳米tio2粉末、金红石型纳米tio2粉末与纳米陶瓷粉末的摩尔比为2∶2∶1。
62.本比较例中所述热塑性聚氨酯(tpu)基材层的材质为脂肪族热塑性聚氨酯,厚度为200μm。
63.本比较例中所述压敏胶层3的材质为丙烯酸压敏胶,厚度为25μm,可见光透过率在90%以上。
64.本比较例中所述离型膜层4的材质为白色聚对苯二甲酸乙二醇酯(pet),厚度为55μm。
65.本比较例中一种汽车漆面保护膜的制备方法,如下:
66.a、修复涂层1的涂布液制备
67.将100份聚己内酯多元醇树脂、2份紫外线吸收剂和纳米陶瓷粉末混合物(锐钛矿型纳米tio2粉末、金红石型纳米tio2粉末与纳米陶瓷粉末的摩尔比为2∶2∶1)添加到150份乙酸乙酯中,最后添加20份异氰酸酯固化剂甲苯二异氰酸酯,充分搅拌30min,混合均匀以备用。
68.b、热塑性聚氨酯基材的制备
69.材料准备:包括按重量份组成的下列成分:异佛尔酮二异氰酸酯(ipdi)为80份、聚四氢呋喃醚二醇为20份、聚己内酯二醇为10份和扩链剂为5份。其中,扩链剂为六氟双酚a。
70.制备方法采用以下步骤:
71.s1.在110~120℃、0.1mpa条件下,将聚四氢呋喃醚二醇真空脱水1.5h~2h;
72.s2.取脱水后适量的聚四氢呋喃醚二醇、异佛尔酮二异氰酸酯(ipdi)和聚己内酯二醇加入到装有机械搅拌、冷凝回流装置、温度计的四口烧瓶中,升温至70℃,抽真空,充入氮气保护,持续反应1.5h~2h后,加入溶剂二甲基甲酰胺(dmf)调节固含量为60wt%,以降低体系粘度,促使反应充分进行;
73.s3.待测定预聚体中异氰酸酯基质量分数稳定后,逐渐升温至100℃,加入扩链剂,剧烈搅拌反应2h,真空脱气,将粘稠的产物趁热倒入铺有一层表面光滑的聚四氟乙烯薄膜的模具中,所述模具为40*40cm的玻璃板刻有深度为200μm的凹槽,用辊压棒进行均匀辊压后,置于70℃烘箱中烘5天成膜,再常温下放置24h后即可得到热塑性聚氨酯薄膜,完成制备。
74.c、压敏胶层3的涂布
75.将压敏胶涂布液涂布在200μm tpu基材的一侧表面上,干燥条件110℃,2min,形成干胶25μm厚的压敏胶层3。然后将55μm白色pet离型膜复合在上述压敏胶层3上。
76.d、修复涂层1的涂布
77.在步骤c中tpu基材的另一侧表面涂布修复涂层1,固化条件120℃,2min,干燥后厚度为10μm,至此得到保护膜半成品。
78.e、熟化
79.将步骤d中的半成品放入50℃熟化室中,经过72h,即可得到保护膜。
80.比较例2:
81.本比较例中一种汽车漆面保护膜,其层状结构与比较例1相一致。
82.但是,本比较例中所述修复涂层1的材质为聚氨酯,厚度却为5μm,其同样内含紫外线吸收剂和纳米陶瓷粉末,所述紫外线吸收剂选用锐钛矿型纳米tio2粉末和金红石型纳米tio2粉末的混合物,相对于聚氨酯100重量份,紫外线吸收剂和纳米陶瓷粉末2重量份,且锐钛矿型纳米tio2粉末、金红石型纳米tio2粉末与纳米陶瓷粉末的摩尔比为2∶2∶1。
83.本比较例中所述热塑性聚氨酯(tpu)基材层的材质为脂肪族热塑性聚氨酯,厚度却为100μm。
84.本比较例中所述压敏胶层3的材质为丙烯酸压敏胶,厚度却为6μm,可见光透过率
在90%以上。
85.本比较例中所述离型膜层4的材质为白色聚对苯二甲酸乙二醇酯(pet),厚度却为23μm。
86.本比较例中一种汽车漆面保护膜的制备方法,其基本步骤与比较例1相一致。
87.胶粘剂残余物测试:
88.将实施例1~3和比较例1-2中的保护膜贴于汽车车身漆面样品上,用2公斤标准压辊来回滚压3次,然后在70℃温度,2公斤标准砝码的压力下老化20小时,然后在室温(23
±
2℃c,相对湿度50%)下冷却0.52小时,然后以300 mm/min进行180剥离,每组试样不少于3条,测试结果见下表1;
89.样品有无发现残胶的情况实施例1无实施例2无实施例3无比较例1有比较例2有
90.本实用新型不局限于上述最佳实施方式,任何人在本实用新型的启示下都可得出其他各种形式的产品,但不论在其形状或结构上作任何变化,凡是具有与本技术相同或相近似的技术方案,均落在本实用新型的保护范围之内。