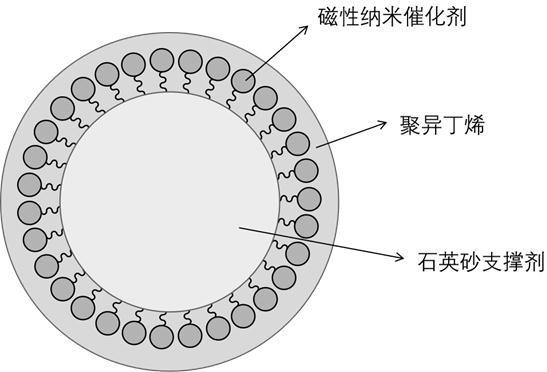
1.本发明涉及功能化支撑剂制备技术领域,具体涉及一种磁性纳米催化型支撑剂及其制备方法和应用。
背景技术:2.压裂技术是目前非常规油气藏增产改造的核心技术。压裂是人为地使地层产生裂缝,使油井产量增加,对改善油层流动状况可起到重要的作用,是油气田稳产增产的重要技术手段。压裂技术主要可以分为爆炸压裂、高能核爆压裂、酸化压裂、水力压裂、无水压裂等几个发展阶段。基于安全性,经济性以及环保等方面的考虑,目前水力压裂技术应用最为广泛。
3.支撑剂在水力压裂中具有十分重要的作用,关系着支撑裂缝的导流效果甚至是整个水力压裂施工的成败。只有获得有效支撑的裂缝,才是油气产生过程中重要的流体通道。随着对压裂工艺要求的提高和现场不断出现的复杂施工问题,大量的不同功能化的支撑剂研究不断涌现,在完成传统支撑导流作用的同时,为一大类压裂作业中出现的工程问题提供了新思路和新方案,成为目前石油化工领域的热点研究内容。
4.支撑剂是一种细小的颗粒状固体材料,其主要功能是在压裂后维持已形成的裂缝。没有支撑的裂缝容易闭合,潜在的油气流动会受到限制。支撑剂通常分为天然石英砂、陶粒和覆膜型支撑剂等。
5.由于地质条件的多样性,简单的支撑剂无法满足不断涌现的压裂施工的多样化需要。为克服油藏内部的技术挑战,满足各种地质条件下的生产需要,从普通支撑剂中衍生出了一系列更具特色的功能化支撑剂。
6.尽管水力压裂技术正在不断进步,但页岩油由于其高粘度在储层流动性较差,导致压裂后原油的开采问题仍然重要。
7.随着技术的进步,降粘技术在油田的应用范围不断扩大,迄今为止,研究者已经发展了许多降粘技术,依赖于热量、微声波、磁力或稀油驱的物理方法已应用于页岩油储量开采,这可以改善原油的流动性,提高页岩油的开采效率。但许多情况下,这些物理方法对降低原油粘度和提高原油质量的影响非常有限。因此,国内外学者开始致力于催化剂降粘技术的研究,并实现永久的原油降粘。
技术实现要素:8.为了解决上述技术问题,本发明的目的是提供一种磁性纳米催化型支撑剂及其制备方法和应用,将磁性纳米催化剂与传统支撑剂-石英砂相结合,制得了新型的磁性纳米催化剂功能化的支撑剂,并且实现了在实际应用中的可控释放,解决了现有页岩储层中存在的原油粘度高、流动性差和难以开采等问题。
9.本发明解决上述技术问题的技术方案如下:提供一种磁性纳米催化型支撑剂的制备方法,包括以下步骤:
(1)将六水三氯化铁在氮气气氛中水浴加热搅拌,然后加入四水氯化亚铁搅拌,混匀后加入氨水,再加入柠檬酸三钠溶液持续反应,将反应溶液转移至锥形瓶内并放置在磁铁上,待上清液澄清时托住磁铁倒出上清液,加入酒精超声洗涤,接着将锥形瓶放置在磁铁上,待上清液澄清时托住磁铁倒出上清液,重复洗涤,得固体成分;(2)将步骤(1)所得固体成分在超声搅拌下悬浮于柠檬酸中,沉淀干燥,得羧基修饰的磁性纳米颗粒;将支撑剂分散在乙醇中超声分散处理,加入氨水,再滴加正硅酸乙酯和3-氨丙基三乙氧基硅烷搅拌反应,最后依次经离心、洗涤和干燥,得氨基修饰的支撑剂;(3)将步骤(2)所得氨基修饰的支撑剂添加到羧基修饰的磁性纳米颗粒溶液中,超声处理至形成均质溶液,然后加入n-羟基琥珀酰亚胺溶液和1-乙基-(3-二甲基氨基丙基)碳二亚胺盐酸盐溶液继续搅拌,磁分离,再用去离子水和无水乙醇洗涤去除非磁性颗粒,干燥,得复合产物;最后将包覆聚合物分散在正己烷中,加入复合产物并搅拌,干燥,得磁性纳米催化型支撑剂。
10.进一步,步骤(1)中,在80℃和300r/min条件下水浴加热,并通入氮气15min,加入四水氯化亚铁在300r/min条件下搅拌5min,加入柠檬酸三钠溶液在ph=10条件下持续反应2h。
11.进一步,步骤(1)中,六水三氯化铁和四水氯化亚铁摩尔比为0.01:0.0058,六水三氯化铁和氨水的摩尔体积比为0.01mol:5.5ml。
12.进一步,步骤(1)中,氨水和柠檬酸三钠溶液浓度分别为25-30wt%和0.1-0.2mol/l。
13.进一步,步骤(1)中,氨水和柠檬酸三钠溶液浓度分别为28wt%和0.1mol/l。
14.进一步,步骤(2)中,支撑剂、乙醇、氨水、正硅酸乙酯和3-氨丙基三乙氧基硅烷质量体积比为100mg:200ml:15ml:100μl:1ml。
15.进一步,步骤(2)中,将固体成分在超声搅拌下悬浮于0.5 mol/l的柠檬酸中4h,将沉淀在50℃温度下干燥12h,其中,固体成分为5mg/ml。
16.进一步,步骤(2)中,支撑剂分散在乙醇中,在室温下超声分散处理60min,加入15 wt%氨水,再滴加正硅酸乙酯和3-氨丙基三乙氧基硅烷搅拌反应2h。
17.进一步,步骤(2)中,支撑剂为粒径20-40目的石英砂。
18.进一步,步骤(3)中,氨基修饰的支撑剂和羧基修饰的磁性纳米颗粒溶液质量体积比为0.042g:100ml,羧基修饰的磁性纳米颗粒溶液浓度为0.1mg/ml。
19.进一步,步骤(3)中,n-羟基琥珀酰亚胺溶液和1-乙基-(3-二甲基氨基丙基)碳二亚胺盐酸盐溶液体积比为5:5,浓度均为0.1mg/ml。
20.进一步,步骤(3)中,包覆聚合物和正己烷质量体积比为2.5g:250ml。
21.进一步,步骤(3)中,包覆聚合物浓度为2.5-15wt%。
22.进一步,步骤(3)中,包覆聚合物为聚异丁烯。
23.上述磁性纳米催化型支撑剂的制备方法制得的磁性纳米催化型支撑剂。
24.上述磁性纳米催化型支撑剂在制备压裂裂缝中催化原油裂解降粘的催化剂中的应用。
25.本发明具有以下有益效果:1、本发明将磁性纳米催化剂与传统支撑剂-石英砂相结合,制得了新型的磁性纳
米催化剂功能化的支撑剂,并且实现了在实际应用中的可控释放,解决了现有页岩储层中存在的原油粘度高、流动性差和难以开采等问题。所得磁性纳米催化型支撑剂具有节能、低污染、操作简单、对生态环境友好,以及可实现控制释放催化剂、使用温度范围广等优点,为催化剂的使用提供新方法,有利于井场的实际应用和推广。
26.2、本发明将传统的单一功能支撑剂发展为新型功能化支撑剂,不仅有针对性地解决稠油开采的关键技术问题,为支撑剂的设计和应用提供新的研究方法和思路,而且将进一步加强人们对纳米尺度粒子在地质条件下物化特性的认识,通过合成新型功能化支撑剂。本发明以石英砂为基体,将磁性纳米催化剂偶联到石英砂表面,并在石英砂的表面形成一层聚合物覆膜,进而实现催化剂在裂缝中的智能释放的目的。
27.3、本发明以磁性纳米催化剂为核心发展的功能型催化支撑剂,能够方便地用于油气井压裂裂缝中提高采收率工艺,利用重力分异作用实现页岩油催化剂在裂缝中的智能释放,达到提高原油流动性的目的,具有催化率高,对环境影响小,易在井场和施工现场推广等优点。形成系列产品后种类多样,能够满足分段压裂提高原油流动性问题的实际需要。
附图说明
28.图1为实施例1所得磁性纳米催化型支撑剂结构示意图;图2为实验例1所得磁性纳米催化剂的x射线衍射图谱;图3为实验例1所得磁性纳米催化剂的磁滞回线图;图4为实验例1所得磁性纳米催化剂的透射电镜图;图5为实验例1所得磁性纳米催化剂的粒径分布图;图6为实验例1所得磁性纳米催化剂的水合粒径分布图;图7为实验例1所得磁性纳米催化型支撑剂的显微影像图;图8为实验例1所得磁性纳米催化型支撑剂的导流能力曲线图。
具体实施方式
29.以下对本发明的原理和特征进行描述,所举实例只用于解释本发明,并非用于限定本发明的范围。实施例中未注明具体条件者,按照常规条件或制造商建议的条件进行。所用试剂或仪器未注明生产厂商者,均为可以通过市售购买获得的常规产品。
30.实施例1一种磁性纳米催化型支撑剂的制备方法,其特征在于,包括以下步骤:(1)将2.703 g六水三氯化铁在80℃和300r/min条件下水浴加热,并通入氮气15min,然后加入1.15 g四水氯化亚铁在300r/min条件下搅拌5min,混匀后加入5.5 ml浓度为28wt%的氨水,再加入0.1mol/l的柠檬酸三钠溶液在ph=10条件下持续反应2h,将反应溶液转移至锥形瓶内并放置在磁铁上,待上清液澄清时托住磁铁倒出上清液,加入酒精超声洗涤,接着将锥形瓶放置在磁铁上,待上清液澄清时托住磁铁倒出上清液,重复洗涤,得固体成分;(2)将步骤(1)所得固体成分在超声搅拌下悬浮于0.5 mol/l的柠檬酸中4h,将沉淀在50℃温度下干燥12h,得羧基修饰的磁性纳米颗粒;将100 mg支撑剂(石英砂)分散在200 ml乙醇中,在室温下超声分散处理60min,加入15 ml 浓度为15 wt%的氨水,再滴加100
μl正硅酸乙酯和1ml 3-氨丙基三乙氧基硅烷搅拌反应2h,最后依次经离心、洗涤和干燥,得氨基修饰的支撑剂;(3)将0.042 g步骤(2)所得氨基修饰的支撑剂添加到100 ml羧基修饰的磁性纳米颗粒溶液(0.1mg/ml)中,超声处理至形成均质溶液,然后加入5 ml n-羟基琥珀酰亚胺溶液(0.1mg/ml)和5 ml 1-乙基-(3-二甲基氨基丙基)碳二亚胺盐酸盐溶液(0.1mg/ml)继续搅拌2h,磁分离,再用去离子水和无水乙醇洗涤去除非磁性颗粒,在60℃下干燥8h,得复合产物;最后将2.5g聚异丁烯分散在250 ml正己烷中,加入复合产物并搅拌,在60℃下干燥8h,得磁性纳米催化型支撑剂,其结构示意图如图1所示。
31.实验例1将实施例1所得磁性纳米催化剂(步骤(1)所得固体成分)研磨成细小粉末状固体,取出30 mg粉末作为xrd测试样品均匀平铺在载玻片上并盖片,放入型号为smartlab 9kw的x射线多晶衍射仪,在室温下进行连续扫描测试,其结果如图2所示。
32.由图2可知,磁性纳米催化剂的x射线衍射结果图谱出现明显的8个峰,在2θ= 21.2
°
、35.1
°
、41.4
°
、43.3
°
、50.4
°
、62.9
°
、67.2
°
、74.1
°
的衍射峰分别对应fe3o4粒子的(111)、(220)、(311)、(222)、(400)、(422)、(511)和(440)晶面,与标准谱图(pdf#19-0629)基本吻合,且具有反尖晶石结构。
33.将实施例1所得磁性纳米催化剂研磨成细小的粉末,再称量至少40 mg作为磁性测试样品。采用仪器型号为lakeshore 7400的振动样品磁强计,在最大磁场强度为1t的室温环境下进行磁性性质测试,并且将测得的数据进行整理、绘制磁场强度与磁性的关系曲线图,其结果如图3所示。
34.由图3可知,磁性纳米催化剂在磁场条件下表现出明显的磁性,当施加了反向磁场是也能表现出反向饱和的趋势。
35.将少量实施例1所得磁性纳米催化剂分散于去离子水中,取5-10ml样品进行超声分散至少0.5小时,再将液体样品滴在铜网上,置于型号为jem 2100 f的透射电子显微镜上测试,设置测试电压为200 kv,标尺为100 nm,待水蒸发后用高倍电子显微镜观察纳米粒子的形貌和粒径分布图,其结果如图4-5所示。
36.由图4-5可知,磁性纳米催化剂呈现较为均匀的球形形貌,分散性较好,颗粒粒径分布在8-14 nm之间。
37.用去离子水将实施例1所得磁性纳米催化剂稀释成透明状的样品,超声半小时后取少量液体样品装样,放入预热15 min 后的nanobrook omni激光粒度仪中,其结果如图6所示。
38.由图6可知,磁性纳米催化剂的流体动力学直径为113. 45nm。
39.实验例2将实施例1所得磁性纳米催化剂配成浓度为300 mg/l的溶液,取500 ml溶液在55 ℃、65 ℃、75 ℃、85 ℃和95 ℃条件下,密封保存48 h,观察催化剂是否发生沉淀或凝析现象,并且测定催化剂的浓度保留率,其结果见表1。
40.表1磁性纳米催化剂的耐温性评价结果
由表1可知,在55 ℃-95 ℃温度条件下,磁性纳米催化剂的质量浓度保留率在95 %以上,表明磁性纳米催化剂具有良好的热稳定性。
41.将岩心研磨成粉,过筛后保留60/80目的粉末用于吸附实验。再将浓度为300 mg/l的500 ml磁性纳米催化剂溶液分别与岩心混合,静置48 h后测量他们之间的吸附损失量。同时,为模拟在地层不同温度环境下岩石与催化剂的吸附性,在55 ℃、65 ℃、75 ℃、85 ℃、95 ℃下进行多组吸附性实验,测定试验前后溶液中催化剂质量浓度的变化,其结果见表2。
42.表2磁性纳米催化剂与岩石的吸附评价结果由表2可知,经48 h与岩石的吸附实验后的实验数据可知,在地层温度(55-95 ℃)下,磁性纳米催化剂的吸附损失率很小(只有3 %左右)。
43.利用质量浓度为0.33 %的胍胶溶液作为压裂液体系,采用四硼酸钠为交联剂(交联比100:0.6),选用过硫酸铵为破胶剂。选用型号为haake mars
ꢀⅲ
的流变仪对压裂液进行粘度测试,将剪切速率设置为170 s-1
对压裂液连续剪切,从而测定其粘度。由空白组粘度可知,室温下压裂液基液的粘度为41.75 mpa
∙
s;当采用100:0.6的交联比添加交联剂后持续搅拌,胍胶溶液发生交联反应,粘度急剧增大,能用玻璃棒进行挑挂,测定粘度为927.66 mpa
∙
s;加入破胶剂后,在70 ℃的水浴环境下稳定破胶2 h后,粘度测定为5.08 mpa
∙
s。设计催化剂浓度为60 mg/l、90 mg/l、120 mg/l加入压裂液中,探究不同催化剂浓度对压裂液的影响,评价其分别对压裂液粘度的影响,其结果见表3。
44.表3磁性纳米催化剂对压裂液粘度的影响由表3可知,与空白组对比,加入浓度分别为60、90、120 mg/l的磁性纳米催化剂后,压裂液基液的粘度增大,但不影响其在注入阶段的流动性能。
45.选用塔河稠油为原油进行磁性纳米催化剂的降粘评价,取适量原油与磁性催化剂混合均匀,将混合好的反应物加入高压反应釜中,用n2置换体系为惰性气体氛围,并升温至反应温度,启动搅拌,恒温一段时间后,停止加热冷却至室温。反应结束后放空釜内气体,使用粘度计测量降粘后的油样在240 ℃下的粘度,其结果见表4。
46.表4原油催化后的粘度及降粘率
由表4可知,加入磁性纳米催化剂后原油粘度降低了85.65%,说明磁性纳米催化剂具有较好的降粘效果。
47.实验例3(1)圆度、球度根据国内行业标准sy/t 5108-2014第7节要求,在满足颗粒尺寸的样品中随机挑选1-2 g支撑剂。选用leica dm2700p型号的光学显微镜进行支撑剂圆度和球度的测试,将支撑剂平铺在载玻片上,根据不同支撑剂尺寸选择合理倍数进行观察,其结果如图7所示。
48.由图7可知,磁性纳米催化型支撑剂的圆度和球度均满足压裂支撑剂的圆度和球度要求。
49.(2)密度在20 ℃下利用干燥的50 ml密度瓶来测定支撑剂的体积密度和视密度,所用测试液为煤油。经过测量和计算,天然石英砂的视密度为2.80 g/cm3,磁性纳米催化型支撑剂的视密度为2.72 g/cm3,两种支撑剂的视密度十分接近。
50.(3)酸溶解度
①
将待评价的支撑剂置于105 ℃烘箱内烘干至恒重,然后在干燥器内冷却。用精密天平称出取5 g石英砂和磁性纳米催化型支撑剂(精确到0.001g)分别放入称量样品盘内,记录样品的质量ms。
51.②
将漏斗和过滤纸置于105 ℃的烘箱内烘干至少1 h,直至达到恒定质量并记录下质量mf。
52.③
在容量为150 ml的聚乙烯烧杯中加入100 ml混合酸液,将称量好的支撑剂加入其中,并用聚乙烯盖盘盖住杯口,以防酸液挥发。用加热到66 ℃的水浴锅加热半小时,在此期间切勿搅拌。
53.④
待样品加热完成后,将样品和混合酸液从烧杯中移至铺上过滤纸的漏斗中,通过预称量的过滤漏斗过滤样品,确保全部颗粒均由烧杯中移入漏斗内。再将漏斗装置接上真空泵,使其加速过滤,并在1 min内去除酸液。
54.⑤
用20 ml的蒸馏水清洗过滤设备中的样品3次,至ph值为中性。
55.⑥
将过滤器和余留样品烘干置于105 ℃的烘箱中烘干1h,直至达到恒定质量,称出过滤器和样品的质量并记录质量m
fs
。
56.酸溶解度计算公式:
式中:s-酸溶解度,以百分数表示;m
s-样品质量,单位为克(g);m
f-过滤器的质量,单位为克(g);m
fs-包括支撑剂在内的过滤器质量,单位为克(g)。
57.通过实验,获得石英砂与磁性纳米催化型支撑剂的酸溶解度评价数据,结果如表5所示。
58.表5石英砂与磁性纳米催化型支撑剂的酸溶解度支撑剂名称ms(g)mf(g)mfs(g)s(%)石英砂540.341545.10214.79磁性纳米催化型支撑剂540.341545.21312.57由表5可知,石英砂在混合酸中的酸溶解度为4.79%,而磁性纳米催化型支撑剂的酸溶解度为2.57%,均符合行业标准(《5.0%)。
59.(4)浊度选用型号为wgz-1a的数显浊度仪。样品制作步骤为:分别称量30 g天然石英砂和磁性纳米催化型支撑剂于250 ml广口瓶内,再向广口瓶内倾倒100 ml去离子水,静置30分钟,用手水平往复摇动半分钟(60次),但不能搅动,静置5分钟后即可用浊度仪测量,结果如表6所示。
60.表6石英砂与磁性纳米催化型支撑剂的浊度支撑剂种类石英砂磁性纳米催化型支撑剂浊度(ntu)2527由表6可知,天然石英砂的浊度为25 ntu,磁性纳米催化型支撑剂的浊度为26 ntu,均符合行业标准(《100 ntu)。
61.(5)导流能力参照石油天然气行业标准sy/t 6302 2019《压裂支撑剂导流能力测试方法》对上述两种支撑剂进行短期导流能力测试,其结果如图8所示。
62.由图8可知,石英砂和磁性纳米催化型支撑剂都随闭合压力的增大而减小,这是因为闭合压力越大,两种支撑剂就因为承压而被压得更实,从而导致支撑剂颗粒之间的缝隙减小,导流能力下降。在相同压力下,磁性纳米催化型支撑剂的导流能力大于石英砂,这可能是因为磁性纳米催化型支撑剂的圆度和球度大于石英砂支撑剂,因此,其导流能力大于石英砂支撑剂。
63.(6)破碎率根据行业标准sy/t 5108-2014的第11项评价准则,对磁性纳米催化型支撑剂和石英砂支撑剂进行破碎率评价。
64.经过评价,磁性纳米催化型支撑剂在压力为14 mpa的情况下的破碎率为2.4 %,在压力为28 mpa的情况下的破碎率为8.2 %;石英砂支撑剂在14 mpa压力下的破碎率为2.1 %,在压力为28 mpa的情况下的破碎率为8.1 %。两种支撑剂在相同压力下的破碎率接近。
65.以上所述仅为本发明的较佳实施例,并不用以限制本发明,凡在本发明的精神和原则之内,所作的任何修改、等同替换、改进等,均应包含在本发明的保护范围之内。