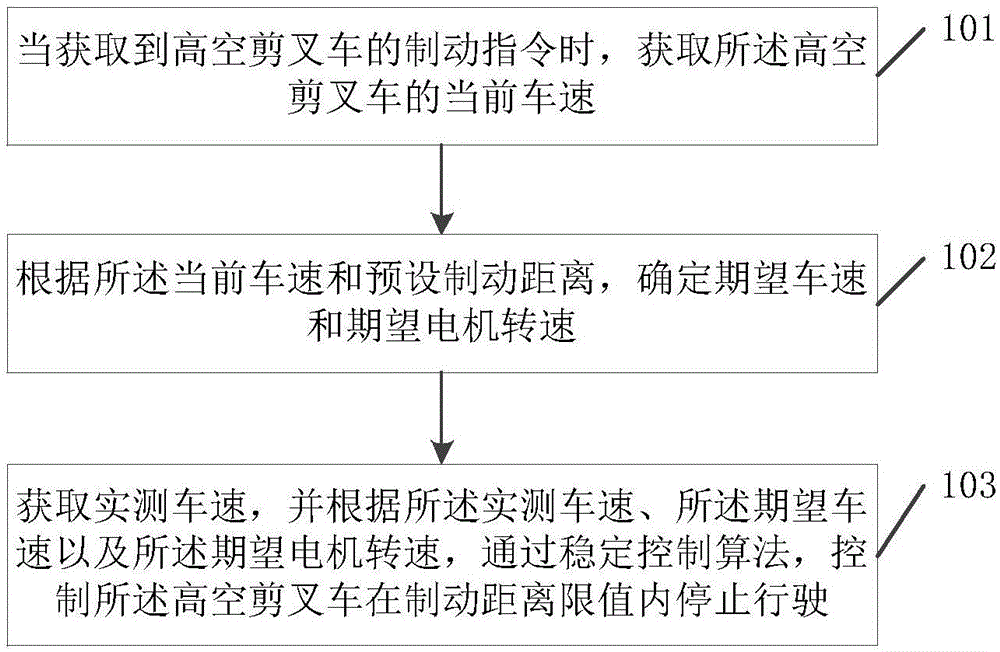
本发明涉及车辆制动
技术领域:
,具体地,涉及一种高空剪叉车制动控制方法、装置及高空剪叉车。
背景技术:
:高空剪叉车因其结构限制,其运动轮没有刹车片制动系统,停车制动主要依靠电机减速来实现。制动时,控制器开启延迟计时并控制电机逐步减速,当延迟时间到了后立即切断电机电源,从而实现制动过程。但是由于其底盘配重较大,故在停车制动过程中会因惯性较大而存在抖动现象,尤其当工作平台上升至最高点时,会对作业中操作人员的安全性造成较大的危害。技术实现要素:本发明的目的是提供一种高空剪叉车制动控制方法、装置及高空剪叉车,解决了现有技术中高空剪叉车制动过程中因惯性较大而存在抖动现象的问题,实现了车辆平稳制动,消除惯性抖动。为了实现上述目的,本发明实施例提供一种高空剪叉车制动控制方法,所述方法包括:当获取到高空剪叉车的制动指令时,获取所述高空剪叉车的当前车速;根据所述当前车速和预设制动距离,确定期望车速和期望电机转速;获取实测车速,并根据所述实测车速、所述期望车速以及所述期望电机转速,通过稳定控制算法,控制所述高空剪叉车在制动距离限值内停止行驶。进一步地,所述当获取到高空剪叉车的制动指令时,获取所述高空剪叉车的当前车速包括:当获取到高空剪叉车的制动指令时,获取所述高空剪叉车的当前电机转速;根据得到所述当前车速v0,其中,nm为所述当前电机转速,r为所述高空剪叉车的车轮半径,i为所述高空剪叉车的减速器传动比。进一步地,所述根据所述当前车速和预设制动距离,确定期望车速和期望电机转速包括:根据所述当前车速和预设制动距离,确定制动时间;将所述制动时间按照预设采样周期进行划分,并根据得到tk时刻的期望车速vtk(k),根据得到tk时刻的期望电机转速ntk(k),其中,v0为所述当前车速,s为所述预设制动距离,tk为从接收到所述制动指令的时刻至所述制动时间的范围内的第k个采样周期的时刻,r为所述高空剪叉车的车轮半径,i为所述高空剪叉车的减速器传动比。进一步地,所述获取实测车速,并根据所述实测车速、所述期望车速以及所述期望电机转速,通过稳定控制算法,控制所述高空剪叉车在制动距离限值内停止行驶包括:获取实测电机转速,并根据所述实测电机转速确定实测车速;将第k个采样周期的所述实测车速和所述期望车速之间的差值确定为第k个采样周期的车速差值;根据所述第k个采样周期的车速差值、所述期望电机转速以及稳定控制算法,得到第k个采样周期的电机转速调整值;根据所述电机转速调整值控制所述高空剪叉车的电机运转,直到控制所述高空剪叉车在制动距离限值内停止行驶。进一步地,所述根据所述第k个采样周期的车速差值、所述期望电机转速以及稳定控制算法,得到第k个采样周期的电机转速调整值包括:根据得到第k个采样周期的电机转速调整值nmc(k),其中,x(k)为第k个采样周期的车速差值,x(k-1)为第k-1个采样周期的车速差值,ntk(k)为第k个采样周期的期望电机转速,ni(k)为第k个采样周期的积分控制项,a1(k)、a2(k)和β0(k)为第k个采样周期的系数,l1和l2为固定系数,其中,第k个采样周期的积分控制项通过ni(k)=ni(k-1)+kix(k)得到,其中,ki为积分控制参数,其中,系数a1(k)、a2(k)和β0(k)通过下述辨识公式得到:其中,φ(k)=[x(k-1),x(k-2),nmc(k-1)]t,λ1与λ2为设定参数,且0<λ1<1,0<λ2<4。相应地,本发明实施例还提供一种高空剪叉车制动控制装置,所述装置包括:获取单元,用于获取高空剪叉车的制动指令,并当获取到所述制动指令时,获取所述高空剪叉车的当前车速;确定单元,用于根据所述当前车速和预设制动距离,确定期望车速和期望电机转速;所述获取单元还用于获取实测车速;处理单元,用于根据所述实测车速、所述期望车速以及所述期望电机转速,通过稳定控制算法,控制所述高空剪叉车在制动距离限值内停止行驶。进一步地,所述获取单元还包括:指令接收模块,用于获取高空剪叉车的制动指令;电机转速传感器,用于当所述指令接收模块获取到所述制动指令时,获取所述高空剪叉车的当前电机转速;计算模块,用于根据得到所述当前车速v0,其中,nm为所述当前电机转速,r为所述高空剪叉车的车轮半径,i为所述高空剪叉车的减速器传动比。进一步地,所述确定单元还用于根据所述当前车速和预设制动距离,确定制动时间;将所述制动时间按照预设采样周期进行划分,并根据得到tk时刻的期望车速vtk(k),根据得到tk时刻的期望电机转速ntk(k),其中,v0为所述当前车速,s为所述预设制动距离,tk为从接收到所述制动指令的时刻至所述制动时间的范围内的第k个采样周期的时刻,r为所述高空剪叉车的车轮半径,i为所述高空剪叉车的减速器传动比。进一步地,所述获取单元还用于获取实测电机转速;所述处理单元还用于根据所述实测电机转速确定实测车速;将第k个采样周期的所述实测车速和所述期望车速之间的差值确定为第k个采样周期的车速差值;根据所述第k个采样周期的车速差值、所述期望电机转速以及稳定控制算法,得到第k个采样周期的电机转速调整值;根据所述电机转速调整值控制所述高空剪叉车的电机运转,直到控制所述高空剪叉车在制动距离限值内停止行驶。进一步地,所述处理单元还用于根据得到第k个采样周期的电机转速调整值nmc(k),其中,x(k)为第k个采样周期的车速差值,x(k-1)为第k-1个采样周期的车速差值,ntk(k)为第k个采样周期的期望电机转速,ni(k)为第k个采样周期的积分控制项,a1(k)、a2(k)和β0(k)为第k个采样周期的系数,l1和l2为固定系数,其中,第k个采样周期的积分控制项通过ni(k)=ni(k-1)+kix(k)得到,其中,ki为积分控制参数,其中,系数a1(k)、a2(k)和β0(k)通过下述辨识公式得到:其中,φ(k)=[x(k-1),x(k-2),nmc(k-1)]t,λ1与λ2为设定参数,且0<λ1<1,0<λ2<4。相应地,本发明实施例还提供一种高空剪叉车,所述高空剪叉车包括如上所述的高空剪叉车制动控制装置。通过上述技术方案,利用获取到制动指令时的当前车速,得到在预设制动距离内的每个采用周期对应的期望电机转速和期望车速,利用期望电机转速、期望车速与实测车速,自动调整实测电机转速,使其趋近于期望电机转速,区别于现有技术中设置预估值的延迟时间,在本发明实施例中只需要根据车辆实际运行情况自动调整控制参数即可。本发明实施例解决了现有技术中高空剪叉车制动过程中因惯性较大而存在抖动现象的问题,避免了后期大量人工调试工作,提高了生产效率,且通过实测车速和电机转速能很好的契合各种工况,实现了车辆平稳制动,消除惯性抖动。本发明的其它特征和优点将在随后的具体实施方式部分予以详细说明。附图说明附图是用来提供对本发明的进一步理解,并且构成说明书的一部分,与下面的具体实施方式一起用于解释本发明,但并不构成对本发明的限制。在附图中:图1是本发明实施例提供的一种高空剪叉车制动控制方法的流程示意图;图2是本发明实施例提供的车速控制回路示意图;图3是本发明实施例提供的车速仿真结果示意图;图4是本发明实施例提供的行驶距离变化曲线仿真示意图;图5是本发明实施例提供的一种高空剪叉车制动控制装置的结构示意图;图6是本发明实施例提供的另一种高空剪叉车制动控制装置的结构示意图。具体实施方式以下结合附图对本发明的具体实施方式进行详细说明。应当理解的是,此处所描述的具体实施方式仅用于说明和解释本发明,并不用于限制本发明。图1是本发明实施例提供的一种高空剪叉车制动控制方法的流程示意图。如图1所示,所述方法包括如下步骤:步骤101,当获取到高空剪叉车的制动指令时,获取所述高空剪叉车的当前车速;步骤102,根据所述当前车速和预设制动距离,确定期望车速和期望电机转速;步骤103,获取实测车速,并根据所述实测车速、所述期望车速以及所述期望电机转速,通过稳定控制算法,控制所述高空剪叉车在制动距离限值内停止行驶。其中,在获取到高空剪叉车的制动指令时,可根据如图2所示的车速控制回路示意图,来控制车辆制动后的电机转速。如图2所示,通过将实测车速、期望车速与期望电机转速代入稳定控制算法中,从而得到控制电机运转的电机转速调整值,使得实测车速近似于期望车速,从而保证所述高空剪叉车在制动距离限值内停止行驶。在实施本发明实施例的过程中,需要将制动时间按照预设采样周期进行划分,然后在每个预设采样周期内通过对电机转速的调整,达到对实测车速的调整,具体实现方式如下所述。其中,在获取到高空剪叉车的制动指令时,可利用例如电机转速传感器获取其当前电机转速,然后根据公式(1),得到与所述当前电机转速对应的当前车速v0:其中,nm为所述当前电机转速,r为所述高空剪叉车的车轮半径,i为所述高空剪叉车的减速器传动比。然后,根据所述当前车速和预设制动距离,确定制动时间。例如,通过公式(2)确定:其中,tn为制动时间。由公式(2)得到所述制动时间,其中,制动距离限值为0.5m,因为在后续调整电机转速的过程中,实际制动距离会有所增加,因此可将所述预设制动距离设置值小于所述制动距离限值,为0.4m。若当前车速v0=1.0m/s,则确定制动时间为0.8s。将该制动时间按照预设采样周期进行划分,所述预设采样周期为ts=0.01s,则得到的周期个数为80。另外,针对接收到制动指令时,获取的所述当前车速的不同,在确定期望车速和期望电机转速时,采用不同的公式进行计算,如公式(3)和公式(4)所示:其中,v0为所述当前车速,s为所述预设制动距离,tk为从接收到所述制动指令的时刻至所述制动时间的时间范围内的第k个采样周期的时刻,r为所述高空剪叉车的车轮半径,i为所述高空剪叉车的减速器传动比。根据公式(3)和公式(4)分别得到在当前车速在小于0.5m/s,大于等于0.5m/s且小于等于2m/s,以及大于2m/s三种不同范围下对应的tk时刻的期望车速vtk(k)以及tk时刻的期望电机转速ntk(k)。然后,获取制动后高空剪叉车的实测电机转速,并根据公式(1)得到所述实测电机转速对应的实测车速。在获取到第k个采样周期的实测车速、期望车速以及期望电机转速之后,通过稳定控制算法,得到第k个采样周期的电机转速调整值,并根据所述电机转速调整值控制所述高空剪叉车的电机运转,直到控制所述高空剪叉车在制动距离限值内停止行驶。首先,为了使得高空剪叉车在不同的工况条件下都能具有较好的制动性能,本发明实施例中的稳定控制算法采用全系数自适应控制方法,即将第k个采样周期的所述实测车速和所述期望车速之间的差值确定为第k个采样周期的车速差值,然后将第k个采样周期的车速差值与所述期望电机转速代入公式(5)中。其中,nmc(k)为第k个采样周期的电机转速调整值,x(k-1)为第k-1个采样周期的车速差值,ntk(k)为第k个采样周期的期望电机转速,ni(k)为第k个采样周期的积分控制项,a1(k)、a2(k)和β0(k)为第k个采样周期的系数,l1和l2为固定系数,例如,l1=0.382,l2=0.618。另外,第k个采样周期的积分控制项ni(k)通过公式(6)得到:ni(k)=ni(k-1)+kix(k)公式(6)其中,ki为积分控制参数。另外,系数a1(k)、a2(k)和β0(k)通过公式(7)得到:其中,φ(k)=[x(k-1),x(k-2),nmc(k-1)]t,λ1与λ2为设定参数,且0<λ1<1,0<λ2<4。通过上述实施例,利用获取到制动指令时的当前车速,得到在预设制动距离内的每个采用周期对应的期望电机转速和期望车速,利用期望电机转速、期望车速与实测车速,自动调整实测电机转速,使其趋近于期望电机转速,区别于现有技术中设置预估值的延迟时间,在本发明实施例中只需要根据车辆实际运行情况自动调整控制参数即可。本发明实施例解决了现有技术中高空剪叉车制动过程中因惯性较大而存在抖动现象的问题,避免了后期大量人工调试工作,提高了生产效率,且通过实测车速和电机转速能很好的契合各种工况,实现了车辆平稳制动,消除惯性抖动。为了更好地理解本发明实施例,下面通过一示例来描述本发明实施例的实现过程。其中,以获取到高空剪叉车的制动指令时所述当前车速为1.0m/s,预设采样周期为ts=0.01s,预设制动距离为0.4m为例。其中,当所述当前车速为1.0m/s时,对应公式(3)中得到的期望车速为对应公式(4)中得到的期望电机转速为另外,为了保证辨识公式(7)得到的系数a1(k)、a2(k)和β0(k)为收敛状态,可在所述高空剪叉车开始行驶时,即确定上述三者的数值,而公式(7)中相关的期望车速和期望电机转速可为预设固定值。由此得到如表1所示对应于采样周期k的系数a1(k)、a2(k)和β0(k)。表1采样周期数ka1(k)a2(k)β0(k)01.8125-0.84930.0110201.8126-0.84920.0127501.8134-0.84850.01651001.8139-0.84800.01882001.8144-0.84750.02043001.8144-0.84750.02044001.8144-0.84750.02045001.8144-0.84750.02046001.8215-0.84020.01757001.8221-0.83960.01478001.8221-0.83960.01479001.8221-0.83960.0147如表1所示,在车辆开始行驶时,设置系数a1(k)、a2(k)和β0(k)的初始值分别为α1(0)=1.8125,α2(0)=-0.8493,β0(0)=0.0110,然后结合利用本发明实施例的车速仿真结果图3所示,当期望车速值设置为1m/s时,在该期望车速自动调整实测车速的情况下,其中的系数a1(k)、a2(k)和β0(k)也趋于收敛,例如,当车辆开始行驶的第2s至第5s,即对应于第200个采样周期至第500个采样周期中,系数a1(k)、a2(k)和β0(k)的值均没有变化。在车辆行驶至第5s时获取到制动指令,则当前车速为1m/s,预设制动距离为0.4m,所需的制动时间为0.8s,对应的采用周期为80个。由表1所示的系数a1(k)、a2(k)和β0(k)的值可知,在车辆开始行驶的第500个采样周期至第600个采样周期的系数α1(k)取值范围1.8144至1.8215对应于车辆制动过程中的系数α1(k)的取值范围,α2(k)的取值范围-0.8475至-0.8402对应于车辆制动过程中的系数α2(k)的取值范围,β0(k)的取值范围0.0204至0.0175对应于车辆制动过程中的系数β0(k)的取值范围。因此,可在获取到制动指令之后,开始根据所述电机转速调整值控制所述高空剪叉车的电机运转时,将上述系数a1(k)、a2(k)和β0(k)的初始值分别设置为1.8144、-0.8475和0.0204。另外,公式(6)中的系数ki为0.5,公式(7)中的λ1=0.05,λ2=0.01。最终通过仿真得到高空剪叉车的行驶距离变化曲线如图4所示。如图4所示,其实际制动距离为0.48m,满足实际制动距离小于制动距离限值0.5m的要求。通过本发明实施例,在减速的过程中不再根据预估的延迟时间进行制动,而是根据采集的电机转速通过控制回路和参数辨识计算得出电机转速调整值,从而自动调整电机转速,保证车辆在制动距离限值内停止行驶,通过采用全系数自适应控制方法提高停车制动过程对不同路面工况和载荷工况的适应能力,而且也减少了现有技术中需要不断调整延迟时间的调试工作,提高了制动过程的鲁棒性,实现对停车制动过程的平稳控制,消除惯性抖动。相应的,图5是本发明实施例提供的一种高空剪叉车制动控制装置的结构示意图。如图5所示,所述装置50包括:获取单元51,用于获取制动指令,并当获取到制动指令时,获取高空剪叉车的当前车速;确定单元52,用于根据所述当前车速和预设制动距离,确定期望车速和期望电机转速;所述获取单元51还用于获取实测车速;处理单元53,用于根据所述实测车速、所述期望车速以及所述期望电机转速,通过稳定控制算法,控制所述高空剪叉车在制动距离限值内停止行驶。其中,如图6所示,所述获取单元51还包括:指令接收模块61,用于获取制动指令;电机转速传感器62,用于当所述指令接收模块获取到所述制动指令时,获取所述高空剪叉车的当前电机转速;计算模块63,用于根据得到所述当前车速v0,其中,nm为所述当前电机转速,r为所述高空剪叉车的车轮半径,i为所述高空剪叉车的减速器传动比。进一步地,所述确定单元还用于根据所述当前车速和预设制动距离,确定制动时间;将所述制动时间按照预设采样周期进行划分,并根据得到tk时刻的期望车速vtk(k),根据得到tk时刻的期望电机转速ntk(k),其中,v0为所述当前车速,s为所述预设制动距离,tk为从接收到所述制动指令的时刻至所述制动时间的范围内的第k个采样周期的时刻,r为所述高空剪叉车的车轮半径,i为所述高空剪叉车的减速器传动比。另外,所述获取单元还用于获取实测电机转速,即所述获取单元中的电机转速传感器还用于获取实测电机转速;所述处理单元还用于根据所述实测电机转速确定实测车速;将第k个采样周期的所述实测车速和所述期望车速之间的差值确定为第k个采样周期的车速差值;根据所述第k个采样周期的车速差值、所述期望电机转速以及稳定控制算法,得到第k个采样周期的电机转速调整值;根据所述电机转速调整值控制所述高空剪叉车的电机运转,直到控制所述高空剪叉车在制动距离限值内停止行驶。进一步地,所述处理单元还用于根据得到第k个采样周期的电机转速调整值nmc(k),其中,x(k)为第k个采样周期的车速差值,x(k-1)为第k-1个采样周期的车速差值,ntk(k)为第k个采样周期的期望电机转速,ni(k)为第k个采样周期的积分控制项,a1(k)、a2(k)和β0(k)为第k个采样周期的系数,l1和l2为固定系数,其中,第k个采样周期的积分控制项通过ni(k)=ni(k-1)+kix(k)得到,其中,ki为积分控制参数,其中,系数a1(k)、a2(k)和β0(k)通过下述辨识公式得到:其中,φ(k)=[x(k-1),x(k-2),nmc(k-1)]t,λ1与λ2为设定参数,且0<λ1<1,0<λ2<4。通过本发明实施例中的电机转速传感器即可获取到车辆的电机转速,从而得到对应的车速,并根据实测车速、期望车速以及期望电机转速,通过稳定控制算法,控制所述高空剪叉车在制动距离限值内停止行驶。本发明实施例中的电机转速传感器体积小,成本低,无需对整车结构做大幅度改动即可实现车辆平稳制动,消除惯性抖动。本装置操作过程,参见上述高空剪叉车制动控制方法的实现过程。相应地,本发明实施例还提供一种高空剪叉车,所述高空剪叉车包括上述实施例所述的高空剪叉车制动控制装置。以上结合附图详细描述了本发明的优选实施方式,但是,本发明并不限于上述实施方式中的具体细节,在本发明的技术构思范围内,可以对本发明的技术方案进行多种简单变型,这些简单变型均属于本发明的保护范围。另外需要说明的是,在上述具体实施方式中所描述的各个具体技术特征,在不矛盾的情况下,可以通过任何合适的方式进行组合。为了避免不必要的重复,本发明对各种可能的组合方式不再另行说明。此外,本发明的各种不同的实施方式之间也可以进行任意组合,只要其不违背本发明的思想,其同样应当视为本发明所公开的内容。当前第1页12