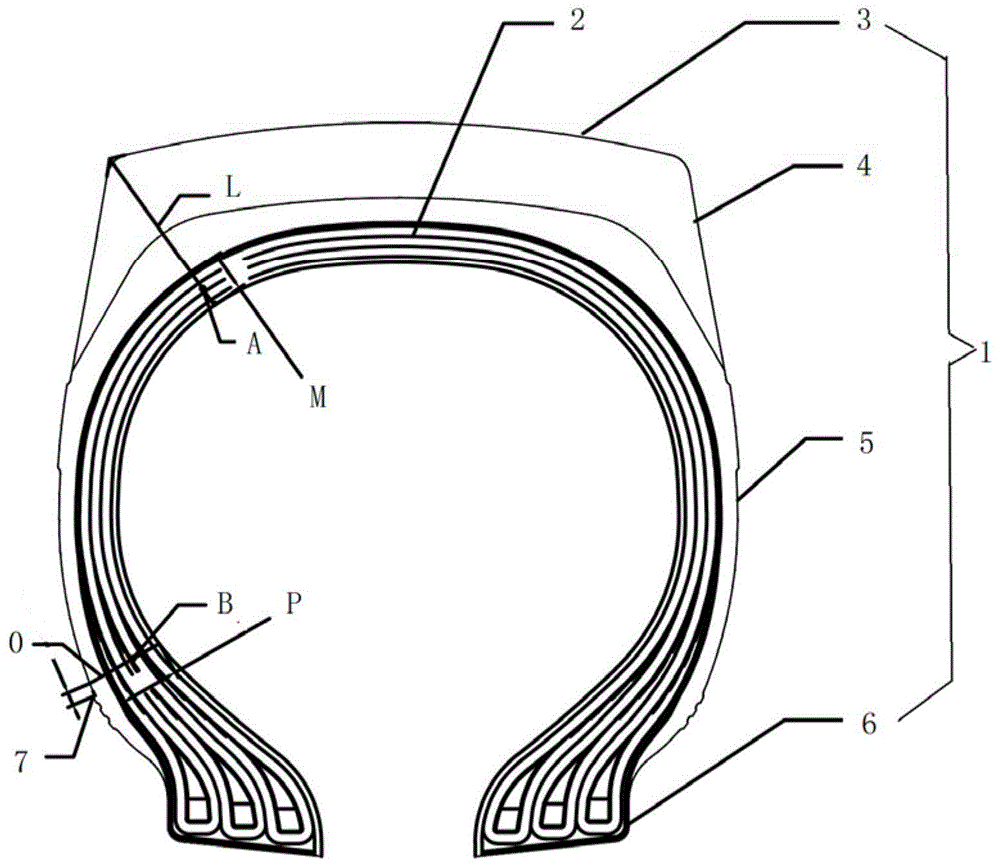
本发明属于轮胎设计
技术领域:
,具体地说涉及一种斜交港口胎。
背景技术:
:轮胎包括胎体,胎体上又根据位置分为胎冠、胎肩、胎侧和胎圈,传统斜交港口轮胎因为安装使用的需要,通常在胎肩和胎圈区域帘布层层数设置较多,使得胎肩和胎圈区域帘布层厚度较厚,在使用过程中帘布层内热量集中而且难以散发出去,随着温度提高,帘布层强度急剧降低,最后断裂出现热脱层,从而造成轮胎的早期损坏,影响轮胎的安全性能。因此,现有技术还有待于进一步发展和改进。技术实现要素:针对现有技术的种种不足,为了解决上述问题,现提出一种斜交港口胎。本发明提供如下技术方案:一种斜交港口胎,包括胎体以及设置在胎体内部的帘布层,所述胎体包括胎冠、胎肩、胎侧和胎圈,所述帘布层交叉排列设置有多层,所述胎侧外表面到帘布层的中间层之间设有散热孔。进一步的,所述胎体上设有轮辋装配线,所述轮辋装配线沿胎圈外周设置为环形。进一步的,所述散热孔包括胎肩散热孔和胎圈散热孔,所述胎肩散热孔设置于胎肩区域,所述胎圈散热孔设置于靠近所述轮辋装配线区域。进一步的,所述胎肩散热孔最深点的位置为:将胎冠外表面和胎肩外表面的交点向帘布层内表面作垂线得到线l,线l在帘布层上的厚度为线m,取线m的中点a为胎肩散热孔的最深点。进一步的,所述胎肩散热孔的钻孔路径为:以a为起点水平延伸至轮胎外轮廓得到交点q,则q和a连线即为胎肩散热孔的钻孔路径。进一步的,q到轮胎中心轴线的距离为c,所述胎肩散热孔的数量e=[2πc/50]。进一步的,所述胎圈散热孔最深点的位置为:以轮辋装配线为基准向外周偏移10mm为基准点,由基准点向帘布层内表面作垂线得到线o,线o在帘布层上的厚度为线p,取线p的中点b为胎圈散热孔的最深点。进一步的,所述胎圈散热孔的钻孔路径为:以b为起点水平延伸至轮胎外轮廓得到交点r,则r和b连线即为胎圈散热孔的钻孔路径。进一步的,r到轮胎中心轴线的距离为d,所述胎圈散热孔的数量f=[2πd/50]。进一步的,所述散热孔为用锥形钻头钻出的锥形散热孔。有益效果:本申请通过对斜交港口轮胎在胎肩和胎圈附近温度集中的区域进行均匀地钻孔处理,在保证原有轮胎结构及生产工艺不变的情况下,可以大大提高斜交港口轮胎胎肩和胎圈区域的散热速度,避免热量的集中,从而减少热脱层情况的出现,提高了斜交港口轮胎的使用寿命及安全使用性。附图说明图1是本发明具体实施例中一种斜交港口胎剖视结构示意图;图2是本发明具体实施例中一种斜交港口胎打孔位置示意图。具体实施方式为了使本领域的人员更好地理解本发明的技术方案,下面结合本发明的附图,对本发明的技术方案进行清楚、完整的描述,基于本申请中的实施例,本领域普通技术人员在没有做出创造性劳动的前提下所获得的其它类同实施例,都应当属于本申请保护的范围。此外,以下实施例中提到的方向用词,例如“上”“下”“左”“右”等仅是参考附图的方向,因此,使用的方向用词是用来说明而非限制本发明创造。如图1-2所示,一种斜交港口胎,包括胎体1以及设置在胎体1内部的帘布层2,帘布层的中间层之间设有散热孔胎体1包括胎冠3、胎肩4、胎侧5和胎圈6,帘布层的中间层之间设有散热孔帘布层2交叉排列设置有多层,帘布层的中间层之间设有散热孔胎侧5外表面到帘布层2中间层之间设有散热孔。轮胎的胎肩4及胎圈6区域是轮胎使用过程中的产热高发区,通过在轮胎的胎肩4及胎圈6区域钻孔至胎体1帘线内部,从而使积攒在帘布层2内部的热量在使用过程中沿所钻孔散发出来,避免帘布层2的热脱层现象,通过改善后,在原有生产工艺不变的前提下,轮胎的使用寿命及其耐久小时数均有大幅度提高。进一步的,帘布层的中间层之间设有散热孔胎体1上设有轮辋装配线7,帘布层的中间层之间设有散热孔轮辋装配线7沿胎圈6外周设置为环形。轮辋装配线7突出于胎侧5设置,其位置通常是按照统一标准固定设置的,凸出设置便于直接观察安装是否到位,同时,由于帘布层2设置于轮胎内部,除设计图外很难对其使用状态的最厚位置进行判断,轮辋装配线7方便辅助确定帘布层2的最厚位置,方便使用者钻孔时进行参照。进一步的,帘布层的中间层之间设有散热孔散热孔包括胎肩散热孔和胎圈散热孔,帘布层的中间层之间设有散热孔胎肩散热孔设置于胎肩4区域,帘布层的中间层之间设有散热孔胎圈散热孔设置于靠近帘布层的中间层之间设有散热孔轮辋装配线7区域。仅在帘布层2到轮胎外表面最厚位置处设置散热孔,极大的减少了散热孔的设置数量,保证轮胎整体的结构强度和耐用性,同时又尽可能的将产生的热量沿散热孔散发出去,避免帘布层2因过热导致的强度降低、断裂脱层现象。进一步的,帘布层的中间层之间设有散热孔胎肩散热孔最深点的位置为:将胎冠3外表面和胎肩4外表面的交点向帘布层2内表面作垂线得到线l,线l在帘布层2上的厚度为线m,取线m的中点a为胎肩散热孔的最深点。在胎肩4附近帘布层2厚度较为均一,并没有太大的厚度差,因此影响散热的因素主要在胎体1上,由于轮胎结构设计要求,使得胎肩4与胎冠3交汇处呈近似直角形状,而内部帘布层2需要配合内胎设计为弧形,这就使得胎肩4与胎冠3交汇处到内胎的距离最长,因而成为阻碍散热的最厚区域之一,因此需要在最厚距离上设置散热孔来进行散热,而为了保证帘布层2的结构强度,避免散热孔对内胎造成影响,因此选取帘布层2的中间位置作为散热孔的最深点。进一步的,帘布层的中间层之间设有散热孔胎肩散热孔的钻孔路径为:以a为起点水平延伸至轮胎外轮廓得到交点q,则q和a连线即为胎肩散热孔的钻孔路径。钻孔路径由水平方向向预先确定的最厚中心点a处延伸,一方面是由于水平方向有利于施工人员掌握钻孔角度,避免钻孔角度误差,另一方面使得外部散热孔处于胎侧5位置,避免行车过程中周围环境中的石子等杂质卡入散热孔中,阻碍散热的正常进行,同时,不破坏轮胎结构强度,使得胎冠3、胎肩4等易磨损部位保持完成,延长轮胎的使用寿命。进一步的,q到轮胎中心轴线的距离为c,帘布层的中间层之间设有散热孔胎肩散热孔的数量e=[2πc/50]。该公式为取整函数等式,打孔需要对胎肩散热孔数量e取整数,以轮胎中心轴线为中心轴沿胎侧5周向均匀分布,以中心轴为对称中心均匀的分布散热孔,有利于均匀的释放使用过程中的应力,避免散热孔对轮胎整体结构强度产生影响。进一步的,帘布层的中间层之间设有散热孔胎圈散热孔最深点的位置为:以轮辋装配线7为基准向外周偏移10mm为基准点,由基准点向帘布层2内表面作垂线得到线o,线o在帘布层2上的厚度为线p,取线p的中点b为胎圈散热孔的最深点。对于胎圈6区域,由于帘布层2本身的设计特点,越靠近胎圈6位置其帘布层2越厚,但对于实际使用情况来说,在胎圈6位置由于轮胎与轮辋并非紧密粘合状态,行车过程中通过挤压会产生一定的缝隙,使胎圈6部分的帘布层2通过挤压缝隙进行散热,并且金属轮辋本身就具备很好的散热性能,其次,胎圈6部分在装配后大部分都处于轮辋内部,与外界并非直接相通,设置散热孔并没有太大的散热作用,因此,只需要考虑位于轮毂装配线之外的帘布层2是否需要设置散热孔。本申请选取以轮辋装配线7为基准向外周偏移10mm为基准点,主要目的是在维持轮胎的结构强度的基础上找到帘布层2的最厚位置,同样找到最厚位置后需要取帘布层2的中点位置作为散热孔的最深点,避免因钻孔导致孔对帘布层2本身结构产生的破坏。进一步的,帘布层的中间层之间设有散热孔胎圈散热孔的钻孔路径为:以b为起点水平延伸至轮胎外轮廓得到交点r,则r和b连线即为胎圈散热孔的钻孔路径。钻孔路径由水平方向向预先确定的最厚中心点b处延伸,一方面是由于水平方向有利于施工人员掌握钻孔角度,避免钻孔角度误差,另一方面由于胎圈散热孔距离轮辋装配线7较近,在轮胎的装配、维护过程中很容易由于拆装导致胎圈散热孔被扯坏,从而导致轮胎的结构强度下降,而水平设置则远离了轮辋装配线7,并且在胎侧5处钻孔,不破坏轮胎结构强度,使得靠近轮辋装配线7处易磨损部位保持完成,延长轮胎的使用寿命。进一步的,r到轮胎中心轴线的距离为d,帘布层的中间层之间设有散热孔胎圈散热孔的数量f=[2πd/50]。该公式为取整函数等式,打孔需要对胎圈散热孔数量f取整数,以轮胎中心轴线为中心轴沿胎侧5周向均匀分布,以中心轴为对称中心均匀的分布散热孔,有利于均匀的释放使用过程中的应力,避免散热孔对轮胎整体结构强度产生影响。进一步的,帘布层的中间层之间设有散热孔散热孔为用锥形钻头钻出的锥形散热孔。锥形散热孔有利于散热的快速进行,同时尽可能的降低散热孔对内部帘布层2结构强度的破坏程度,优选的,在外胎模具上雕刻确认的q点和r点的钻孔标记,钻孔标记与胎体1通过模具一次成型,节省后期钻孔所需的测量时间,用电钻夹持锥形钻头,按钻孔标记孔位置及测量深度钻至帘布层2内部即可,优选的,锥形钻头根部≤2mm。以18.00-25港口胎为实验对象,对其进行帘布层钻孔对比实验,包括耐久试验机对比实验和实际港口使用对比实验,其实验结果如下:实验条件帘布层未钻散热孔耐久时长/h帘布层钻散热孔耐久时长/h耐久试验机78118凯莱港39005600散热孔改善前和改善后耐久测量数据和港口使用数据对比表:改善前耐久累计时间84小时,累计里程427.47公里,改善后耐久累计时间120小时,累计里程598.61公里。改善后耐久小时数提升43%,耐久里程数提高40%。以上已将本发明做一详细说明,以上所述,仅为本发明之较佳实施例而已,当不能限定本发明实施范围,即凡依本申请范围所作均等变化与修饰,皆应仍属本发明涵盖范围内。当前第1页12